The first trimester’s Collaborative Design Studio Project we focused on the conception, design, and execution of a vertical farming system. The system is intended for exhibition at Barcelona’s Ciutadella Park in February 2024, in an exhibition titled MÁQUINA CLIMÁTICA. The goal of the fabrication part of our project is to conceptualize and produce a plant container.
Container Design
In deliberate contrast to the precision and linearity of the wooden vertical shelf, the containers were designed with an organic aesthetic. The containers have a simple box shape, with rounded edges. Each container measures 100 x 50 cm, which is 4 containers on each shelf.
A crucial element of the design is the cut-out, strategically incorporated to conceal the irrigation and drainage pipes. This feature serves the dual purpose of hiding the infrastructure while ensuring easy access for maintenance and adjustments.
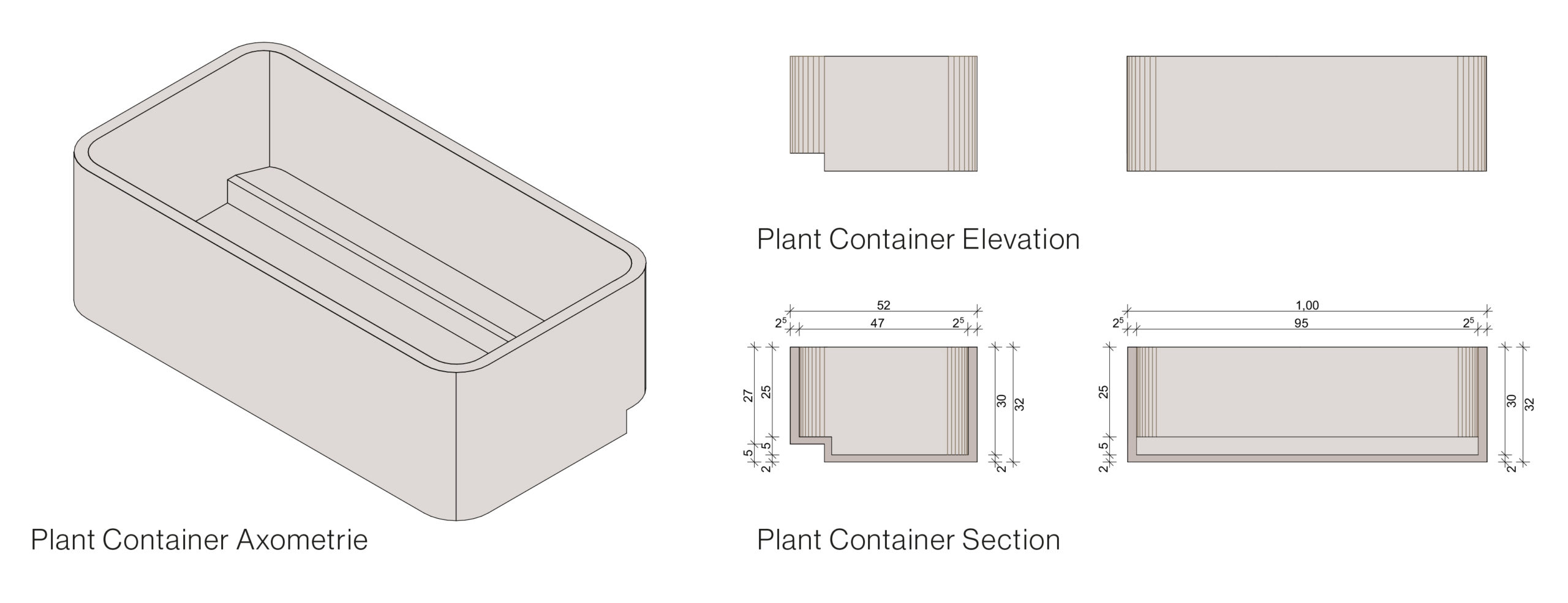
Three distinct materials were considered:
- containers utilizing recycled plastic
- containers combining wood and fabric covered with beeswax
- containers made of biobased sawdust mix material.
Biobased Material – Sawdust Mix
The design/material selected for in-depth exploration is the plant container crafted from bio-based materials.
The proposed composite bio-material comprises primarily sawdust obtained from trees cut down for the production of the exhibition’s furniture, along with additional binding agents such as pine resin, damar resin, or biopolymers like corn starch and agar agar. These materials are chosen based on their compatibility, availability, and ecological attributes. Pine and damar resins offer natural adhesive properties, while corn starch and agar agar contribute to the biodegradability and environmental sustainability of the composite.
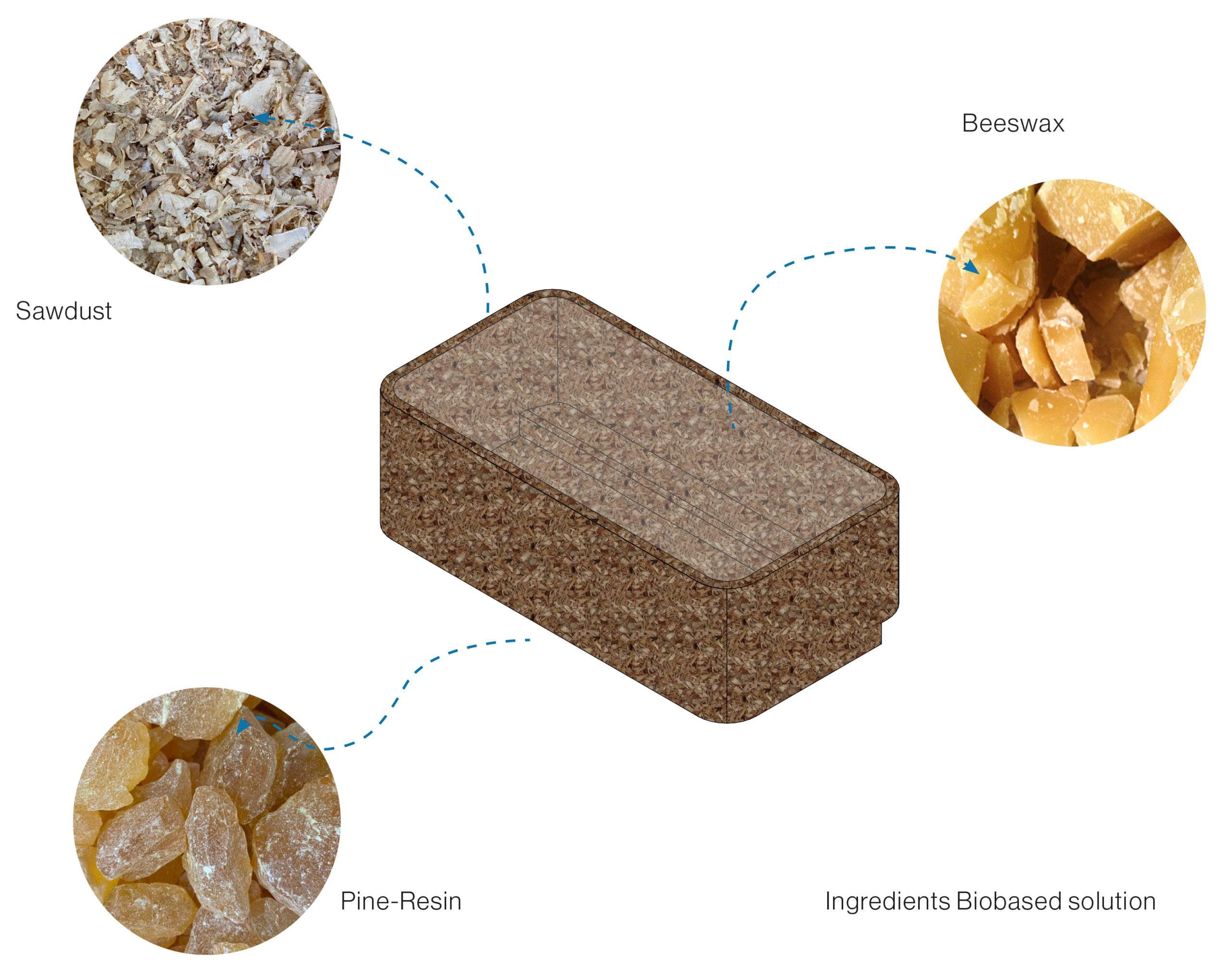
Selected Material Experiments
The experimental procedure involves blending sawdust with varying proportions of either pine resin, damar resin, or a mixture of corn starch, agar agar, water, and glycerol. These resulting mixtures were subjected to tests, including mechanical strength, water resistance, and decomposition rates. In the initial stage of the experiment, smaller quantities were produced to assess the mechanical composition. Through an exclusion process, the most suitable material was produced on a larger scale.
Six distinct mixtures were tested to determine their properties. The material components used in these mixtures are detailed in the next pages. The mixtures were tested using two different cooking methods: water-boiling and an electric cooking plate. These methods have distinct effects on the properties of the mixtures. The water-boiling method involves slow melting of the components and takes longer, typically between 30 minutes to 1 hour. Conversely, the direct heat method using the electric cooking plate melts the mixture rapidly but carries the risk of burning it and changing its color. The equipment for the water-boiling method includes a large pot with a gas cooking plate and a pan. The same pan is employed for the electric cooking plate in the direct heat method.
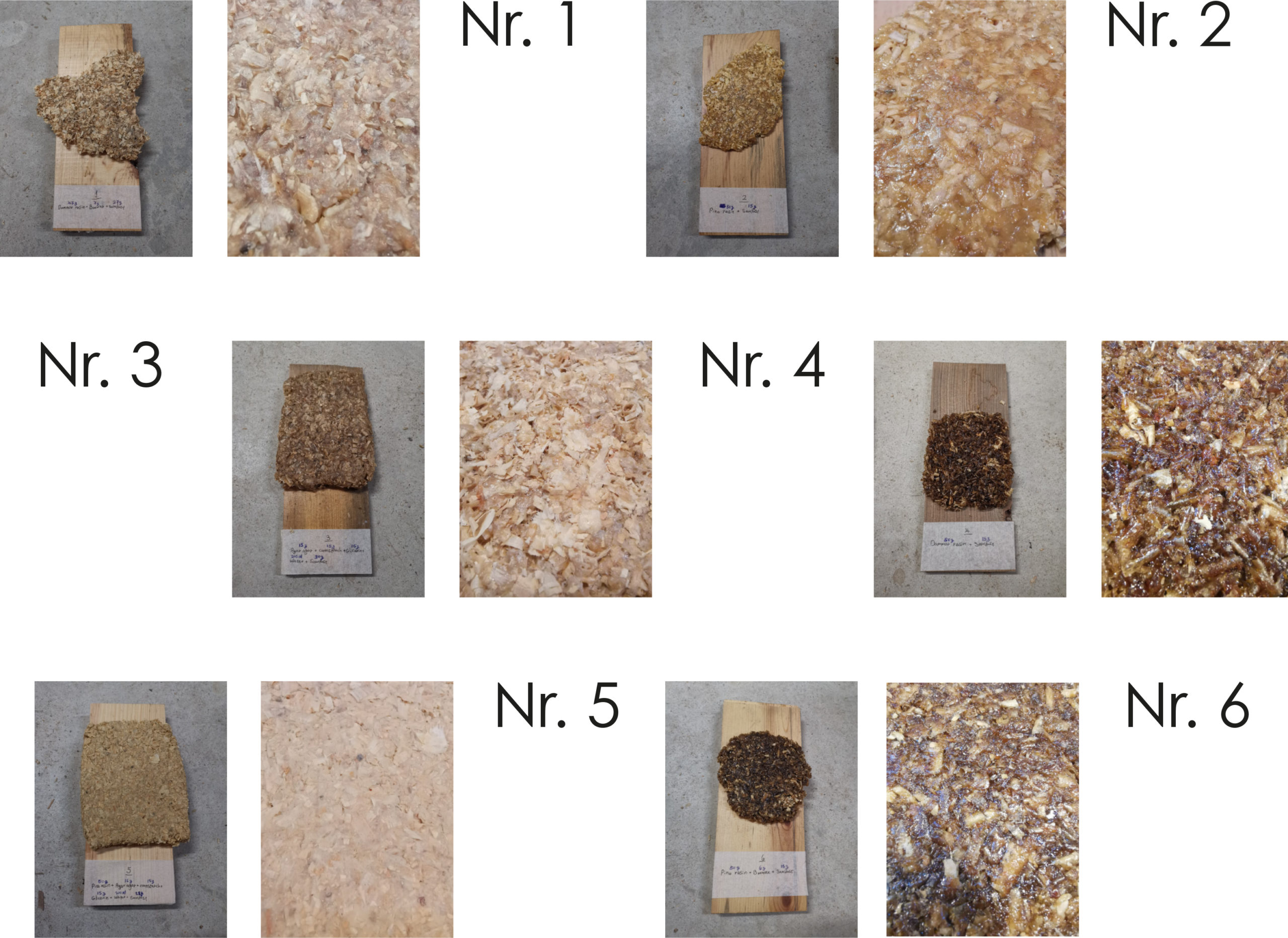
Processes Nr.1, Nr.2, Nr.4, Nr.6:
To expedite the melting process, the resin (either damar or pine) is ground into fine powder. This pulverized resin is then placed in a preheated pan, either boiled with water or heated directly. To prevent the formation of bubbles, the resin requires constant stirring. Once the resin reaches a more liquid state, various biomaterial components like beeswax, glycerol, water, agar-agar, and cornstarch can be added and thoroughly mixed. When the mixture takes on a golden, liquid color, sawdust can be added. To prevent the mixture from drying too rapidly, it needs to be swiftly poured into the mold. Before pouring the mixture, it’s advisable to treat the mold with wood glue and a lubricant like Vaseline or oil to prevent sticking.
Process Nr.3:
On the electric heat plate, carefully prepare a mixture of water, agar agar, and cornstarch, ensuring no bubbles form. Cook the mixture over low heat until it thickens, and then add glycerol. Once the mixture attains a gelatinous consistency, incorporate sawdust and mix thoroughly. After the sawdust is sufficiently mixed and soaked in, transfer the mixture to a mold. Note that this mixture is very adhesive and should not be used on previously treated wood coated with glue, as it will adhere.
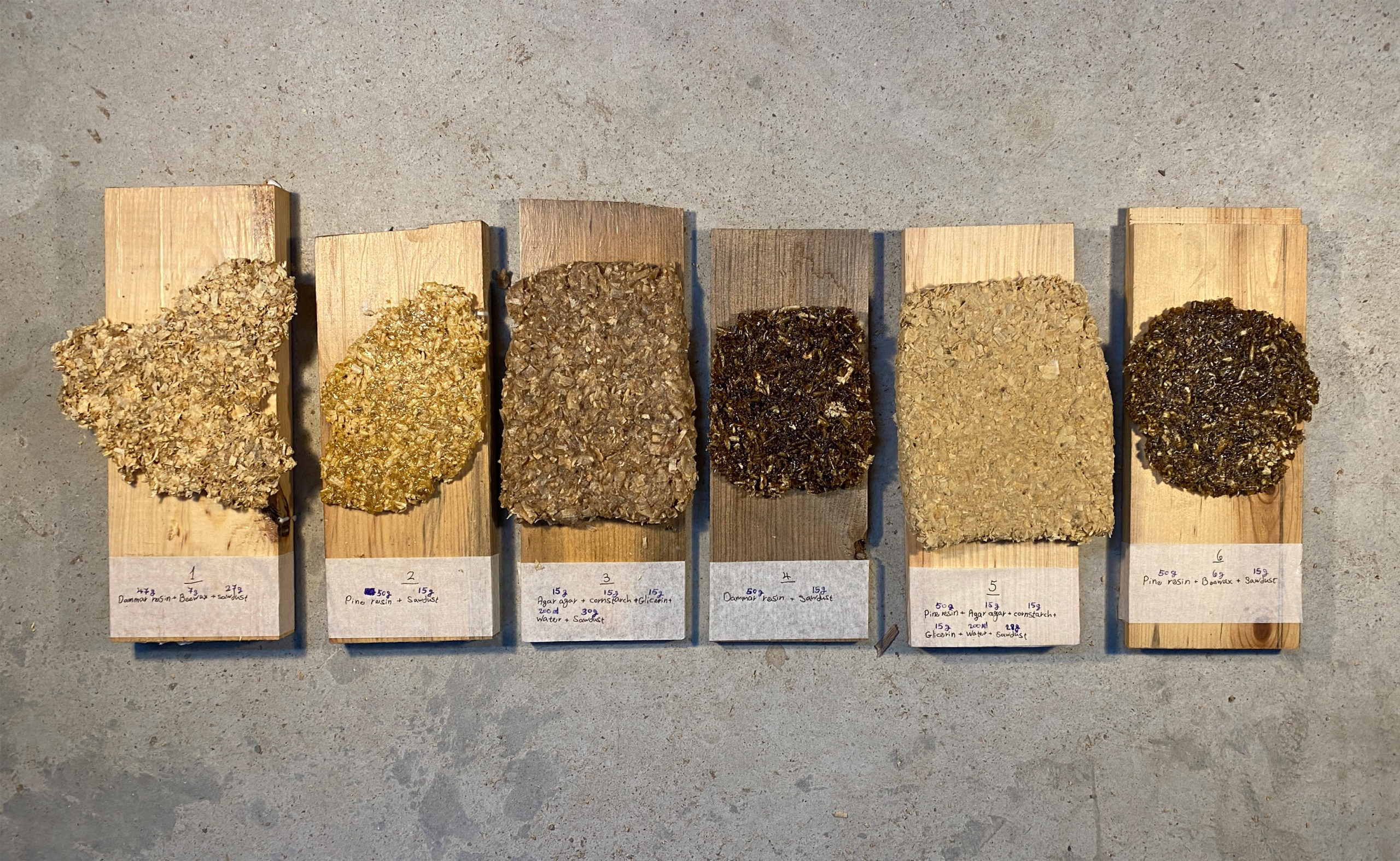
After careful observation and conducting numerous tests, we have identified Nr.6 as the most promising option for further exploration. An exciting discovery was the positive impact of beeswax on the mixture’s elasticity. We observed that incorporating this natural ingredient led to a slower drying process and increased flexibility, consequently reducing the risk of breakage during the transfer to the mold. Additionally, considering the economic and local availability of pine resin, we were very satisfied moving in this direction.
To assess the water resistance of the last two materials and determine the optimal method for manufacturing large-scale containers, we conducted experiments using small pots with plastic pots as molds. Nr.6 exhibited water resistance and a dough-like consistency, while Nr.5 was not waterproof and absorbed water.
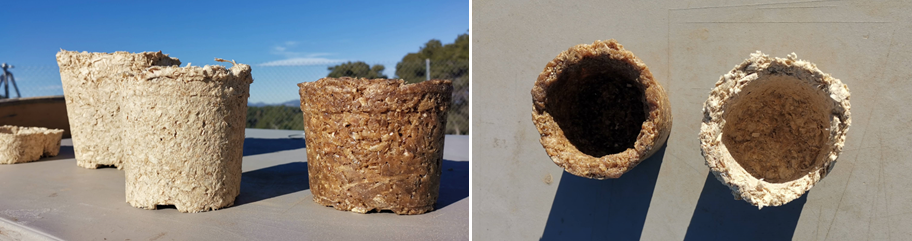
Mold for the Plant Container
The mold components were crafted from plywood with a design that allows for disassembly and reassembly. The mold consists of two sections: a large mold and a smaller one. The large mold is specifically designed for easy disassembly after use. L angles placed strategically on the edges facilitate the upward sliding of the side part and the sideways removal of the back part, preventing damage to the plant container. The front part is securely attached with hinges and can be opened horizontally. In contrast, the small mold is assembled using screws and is not intended for disassembly.
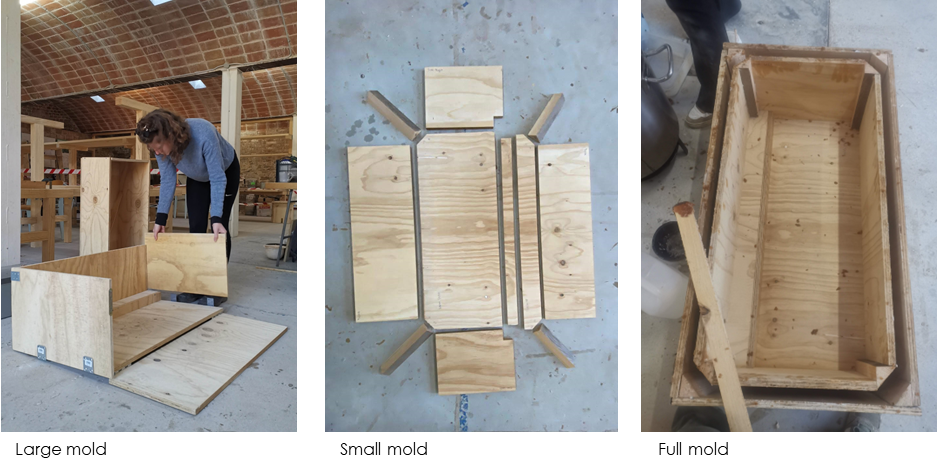
Production Process
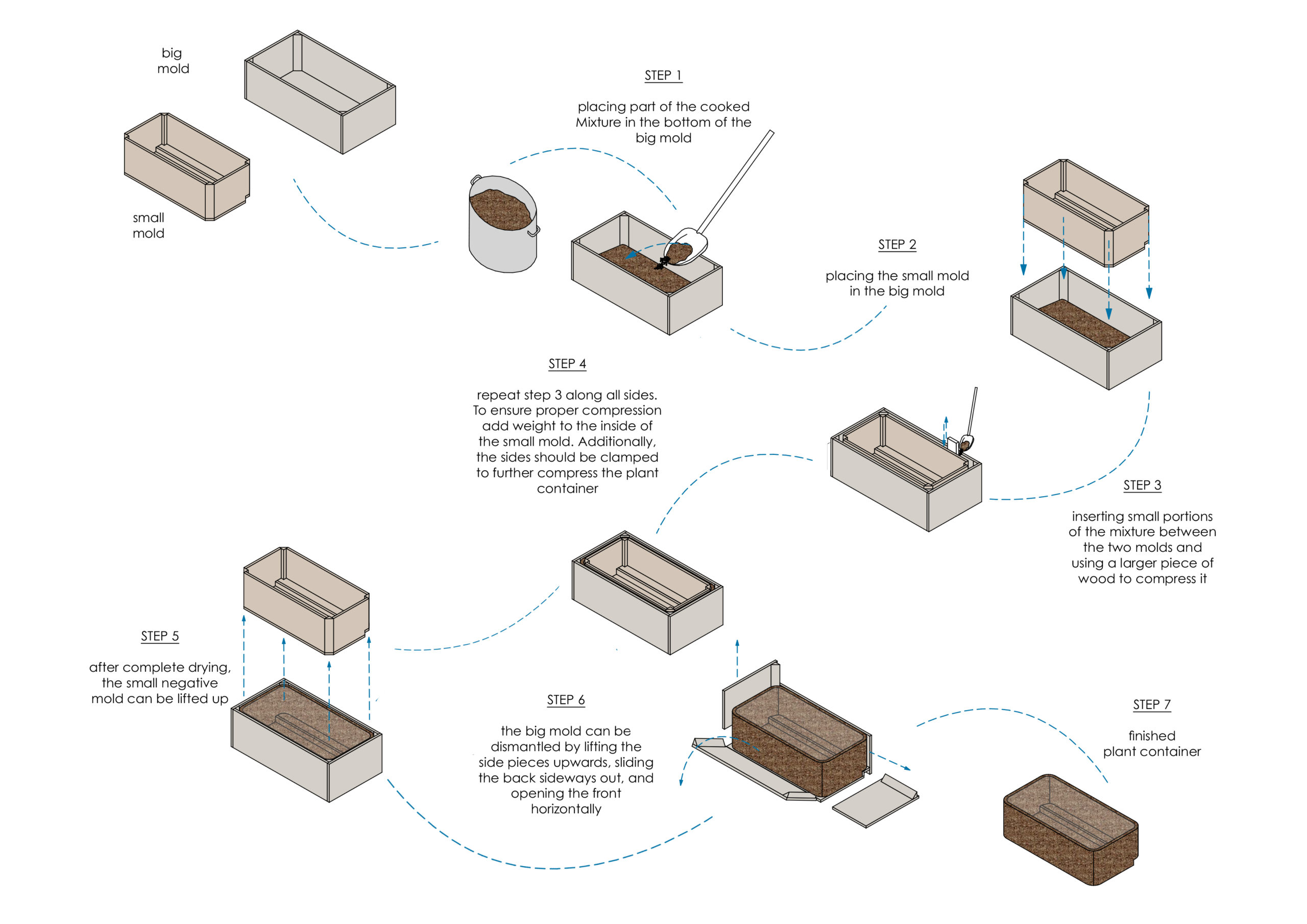
First full-scale production + conclusions
The creation of the initial large-scale prototype has offered crucial insights into necessary modifications for the design and production process of the plant containers.
Throughout this phase, it became evident that the wooden mold was unsuitable due to excessive material adherence, leading to breakage when attempting to remove the container. Alongside the time-consuming process of placing and compressing the material in the side parts, it’s recommended to redesign the mold with hinges for easy opening and closing, possibly using wood with a non-stick layer.
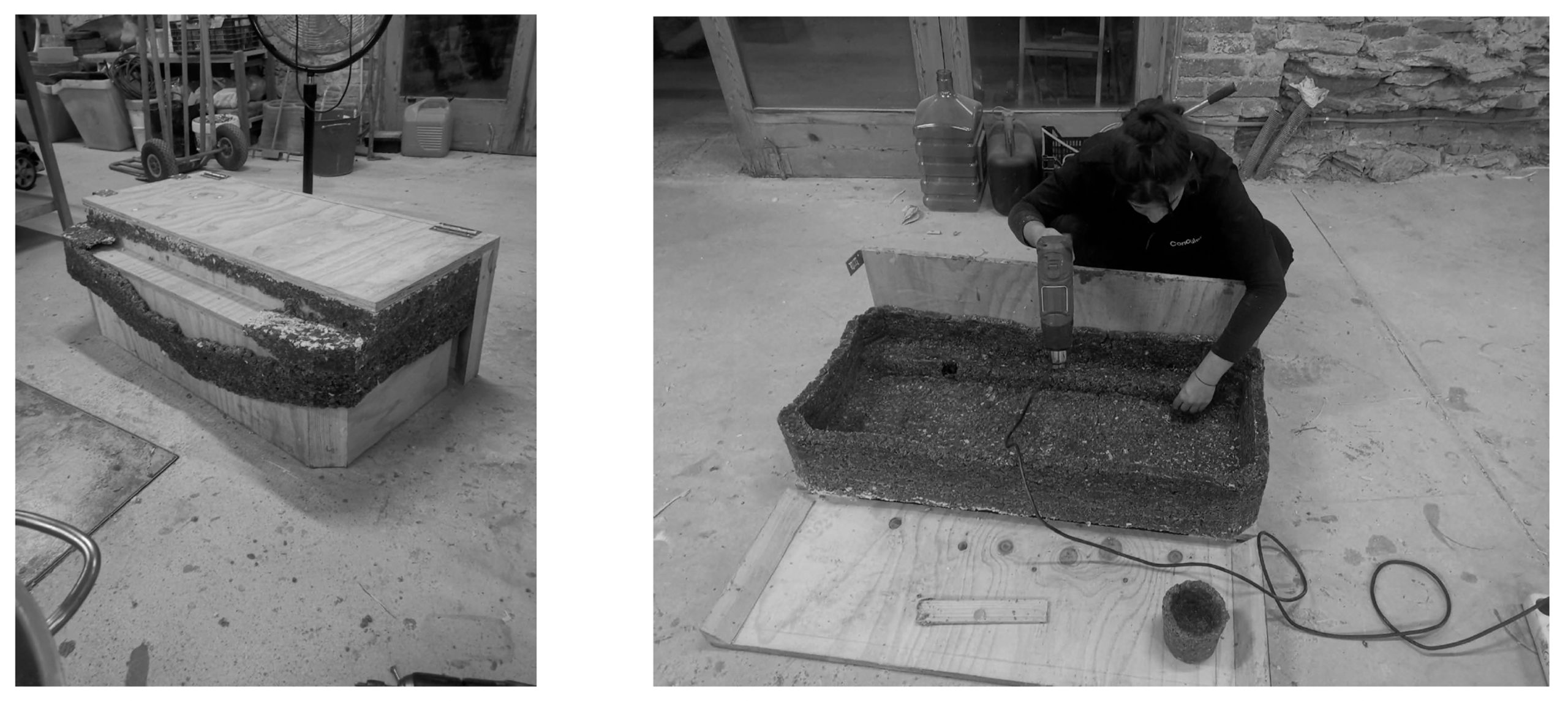
Furthermore, the container’s weight, nearly 11 kg, poses a potential issue as lifting might cause breakage at its weakest point, situated in the middle. Therefore, reconfiguring the plant container into two smaller units could offer a more viable solution.
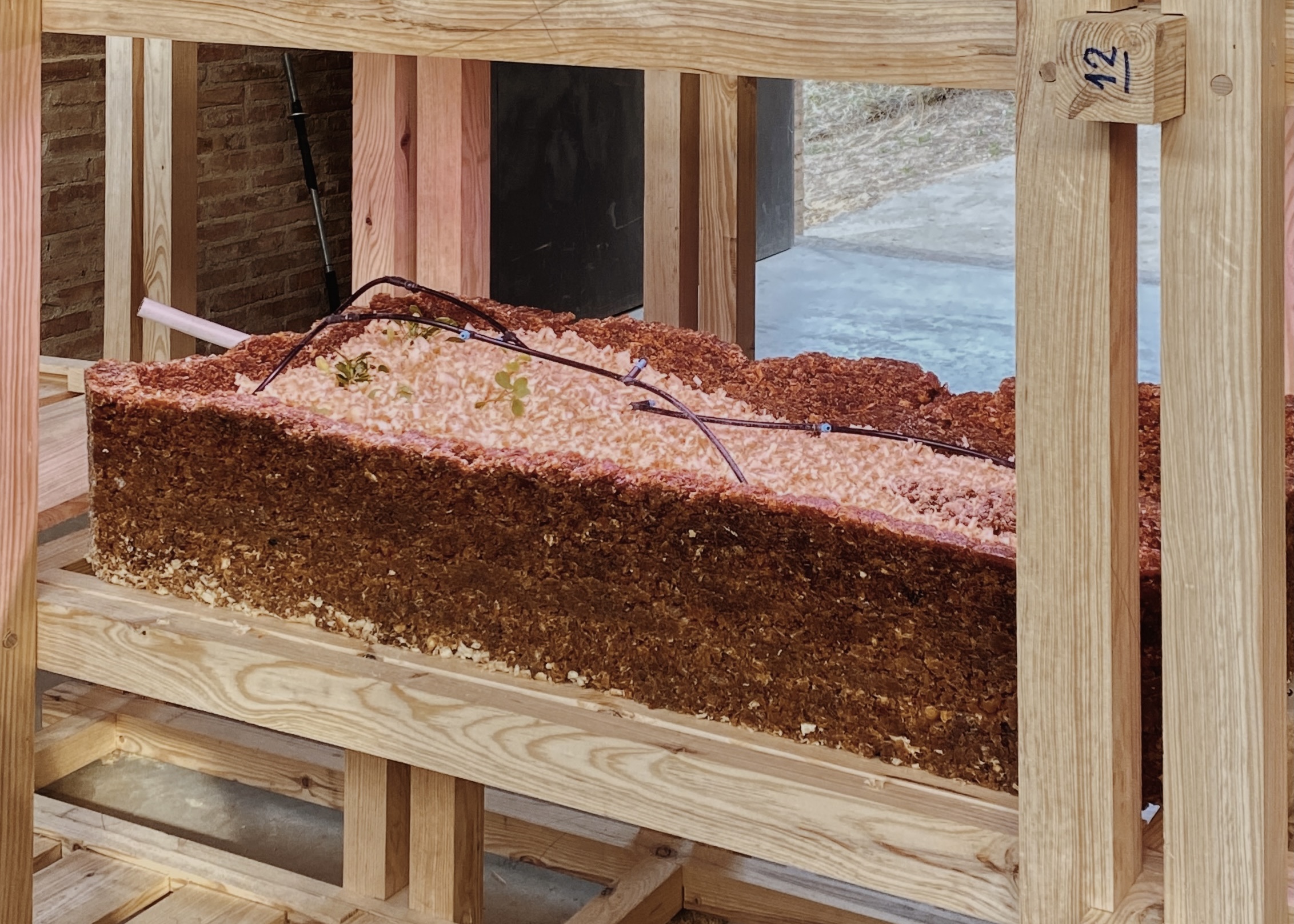