INTRODUCTION
As part of the Structural Design Essentials Workshop, our team explored alternative beam designs for Alejandro Aravena’s Quinta Monroy project. Using reclaimed timber, we designed and analyzed a castellated beam to support vertical growth. Both digital simulations with Karamba3D and physical tests were conducted to evaluate its structural performance and sustainability.
SKETCHES
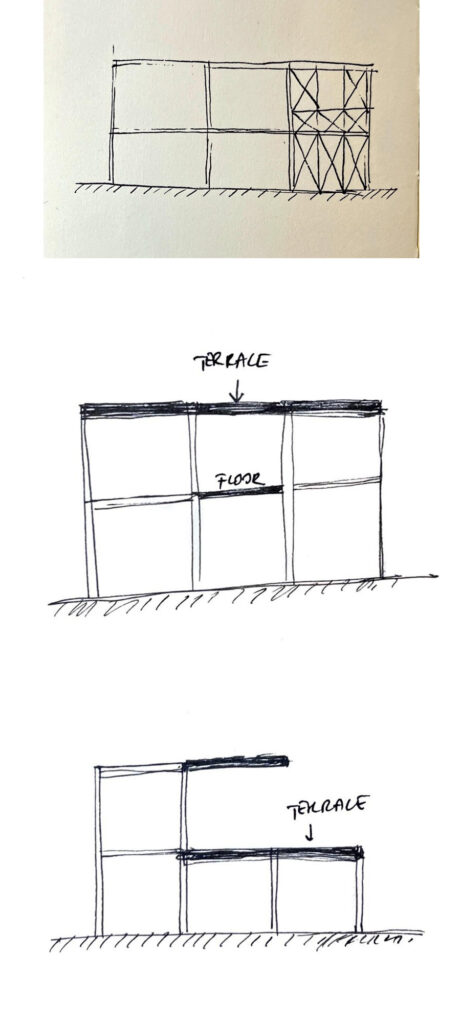
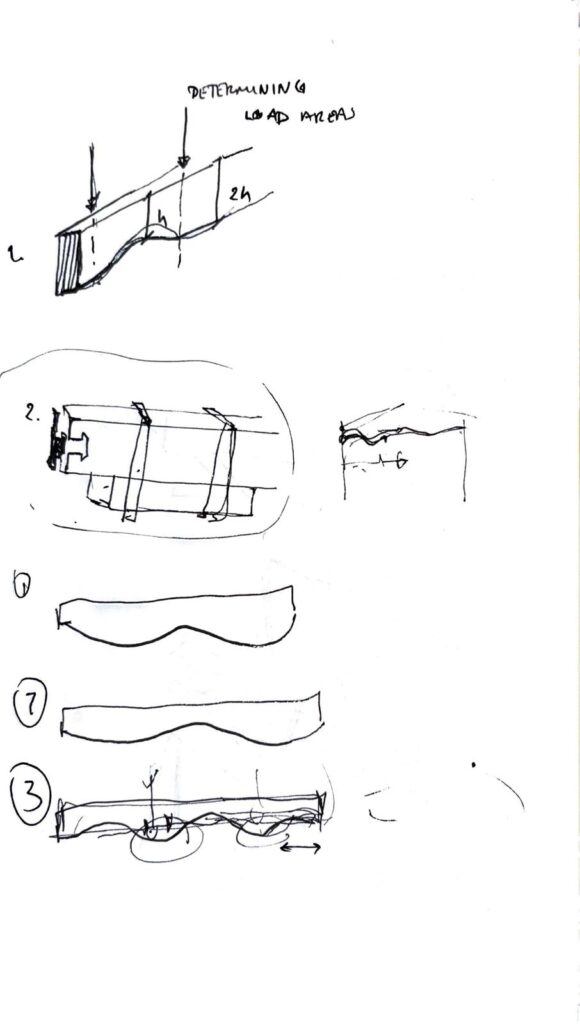
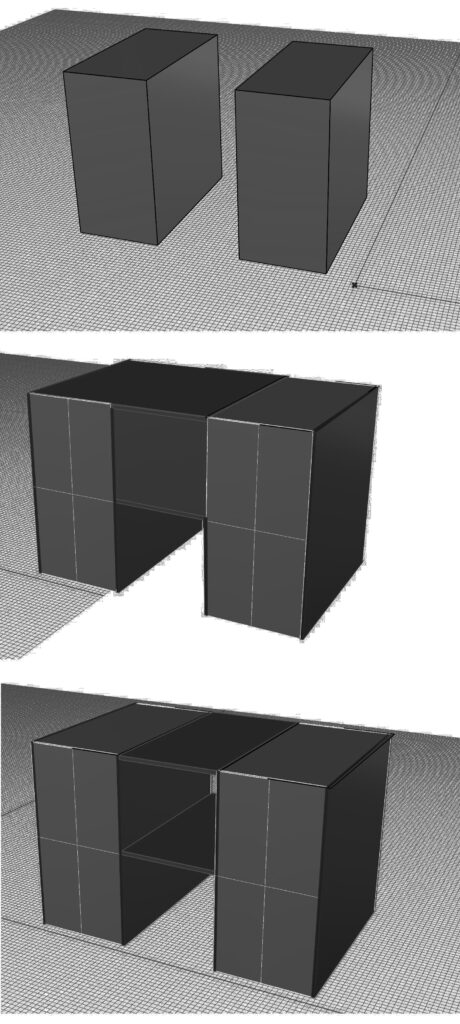
Quinta Monroy
Maximizing the life and usage of living spaces.
Variation 1 : Accessible Roof
Exploring ways to extend the usage of empty spaces with waste wood.
Variation 2 : Extended Common Areas
Diminishing existing walls and using the waste material as structure
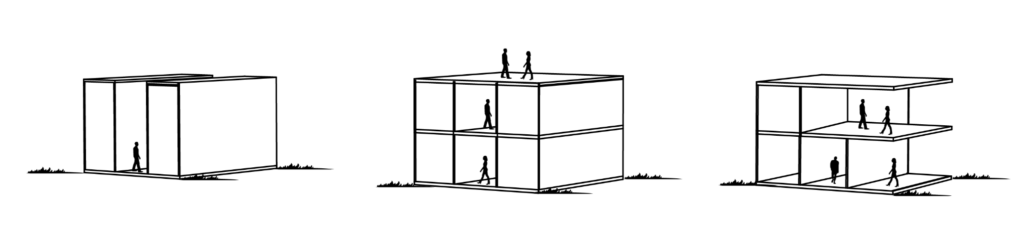
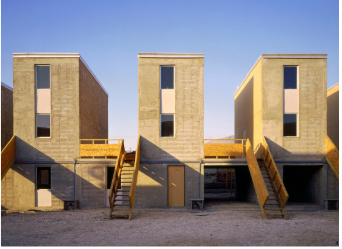
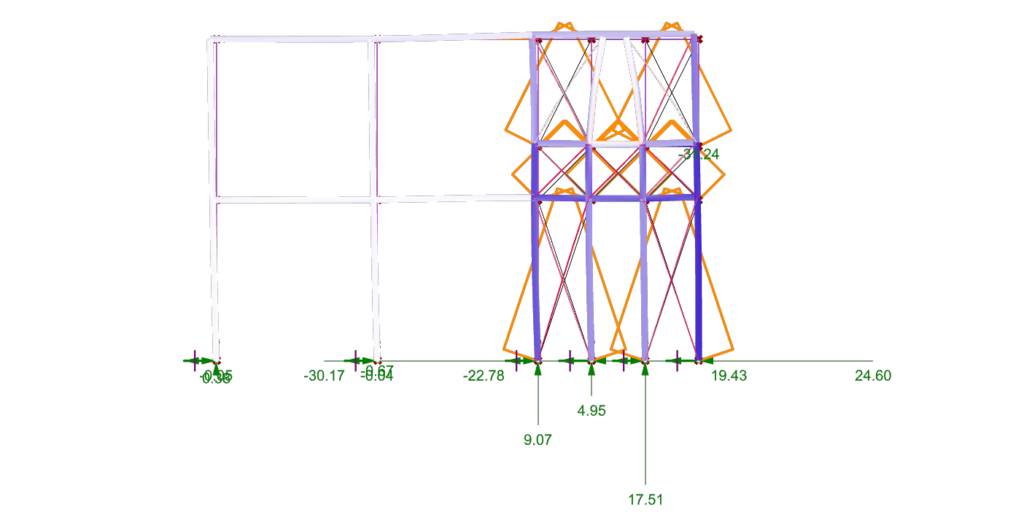
Quinta Monroy
Maximizing the life and usage of living spaces.
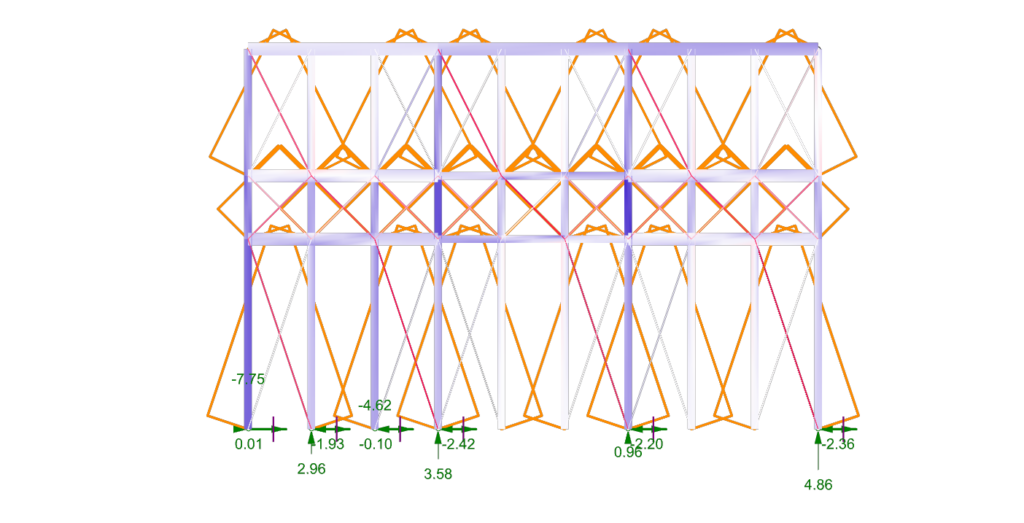
Deformation : 0
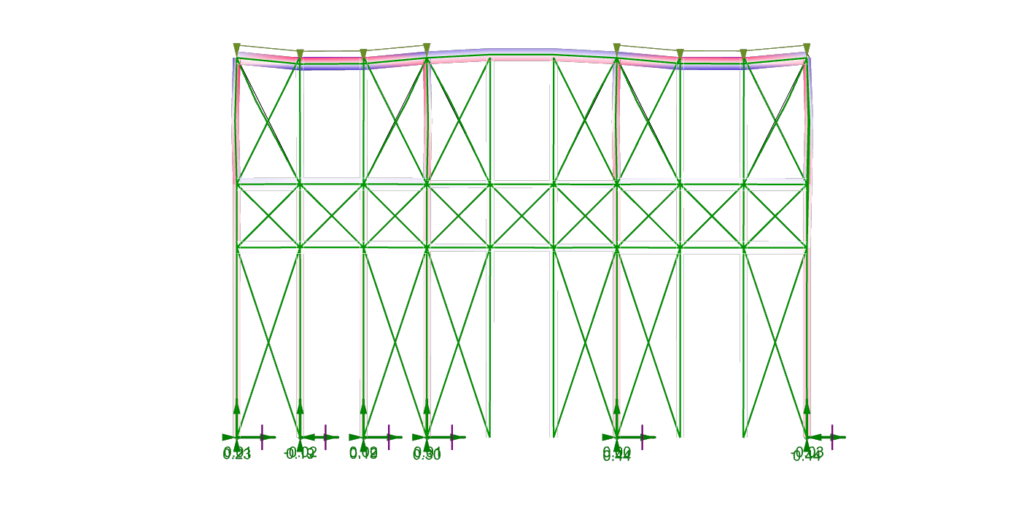
Deformation : 100
Displacements:
LCO: 0.130225
LC1: 1.775493
LC2: 0.028764
LC3: 0.120911
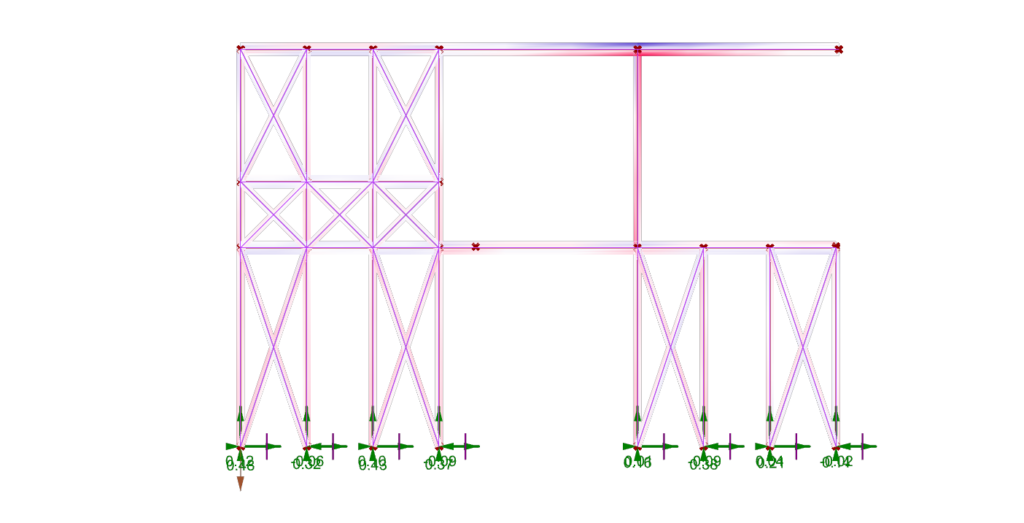
Deformation : 0
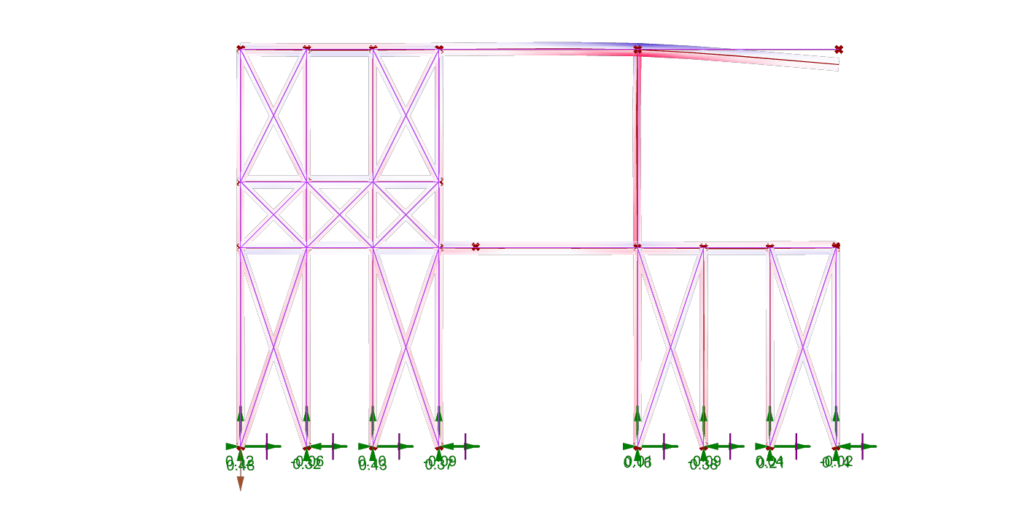
Deformation : 100
Displacements:
LCO: 0.229886
LC1: 0.780657
LC2: 0.116473
LC3: 0.084721
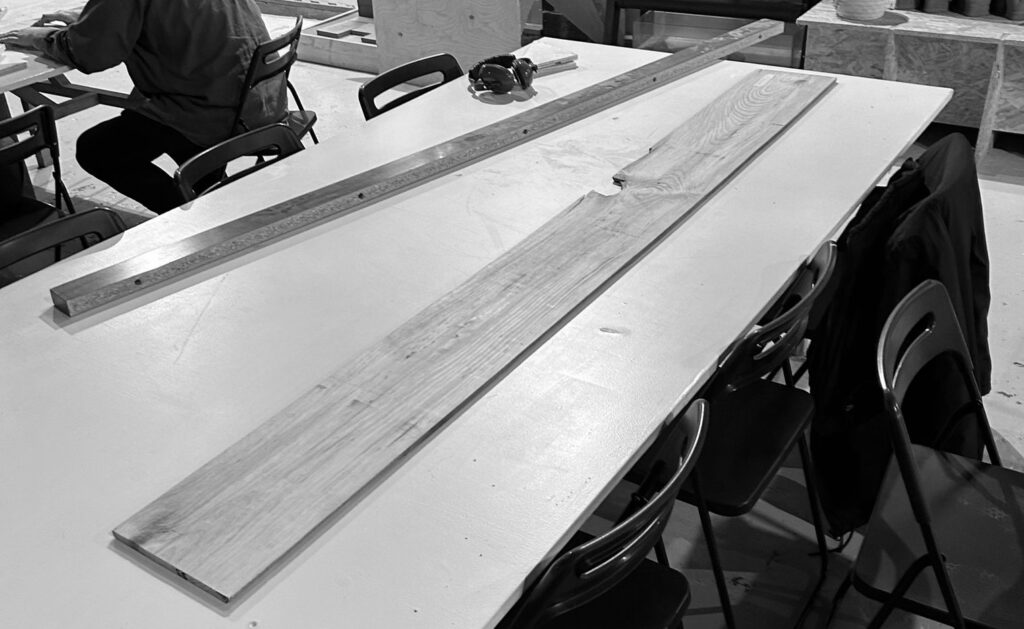
Dimensions: 213,5 x 22 cm
Material: Offcut Pine Plank
Variation 1 : Accessible Roof
Cross-section: O-Section
Domestic dwelling floor finish : 0.5 kN/m2
Variation 2 : Extended Common Areas
Cross-section: O-section
Domestic dwelling floor finish : 0.5 kN/m2
Roof finish load : 0.3 kN/m2
DESIGN STRATEGY
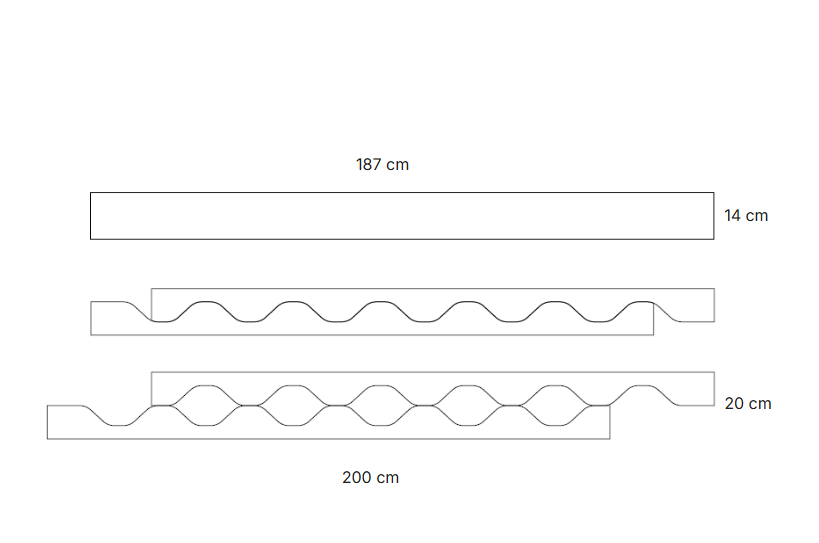
Taking a regular rectangular shape and using a castellated pattern to amplify its depth and strength. Being as lightweight as possible and without waste
DESIGN ITERATIONS
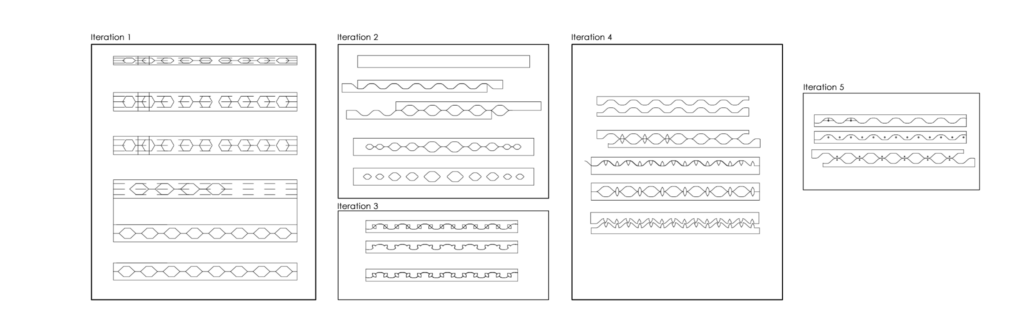
The main design principle was re-using a waste material on high efficiency. The design gives a chance to double the height to strengthen the beam.
Different type of connections are tried. Within in a limited time best option was using dowels (12 dowels) and a small connection piece.
The struggle was designing a without dowel option but the main aim was having it without dowels.
BEAM DIAGRAM
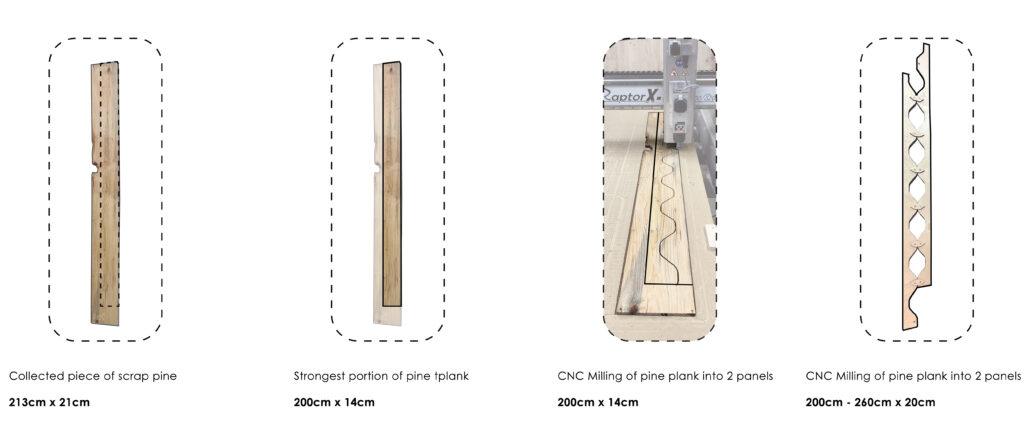
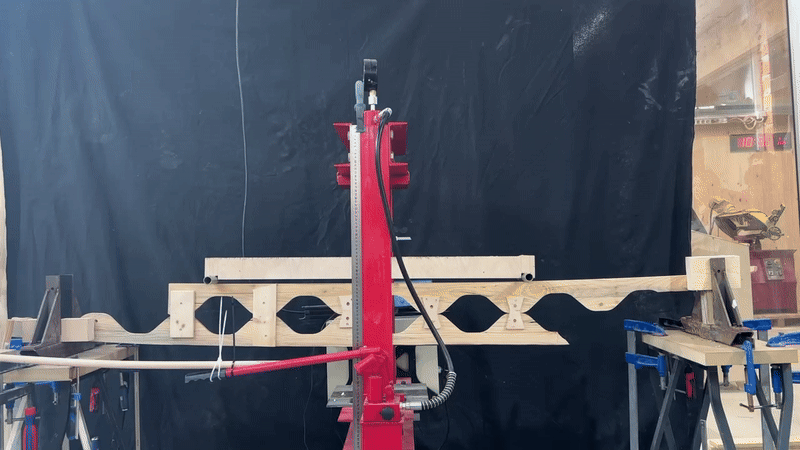
The chosen material was expected to be cracked, at first it cracked and at the end it buckled.
Deformation Graph
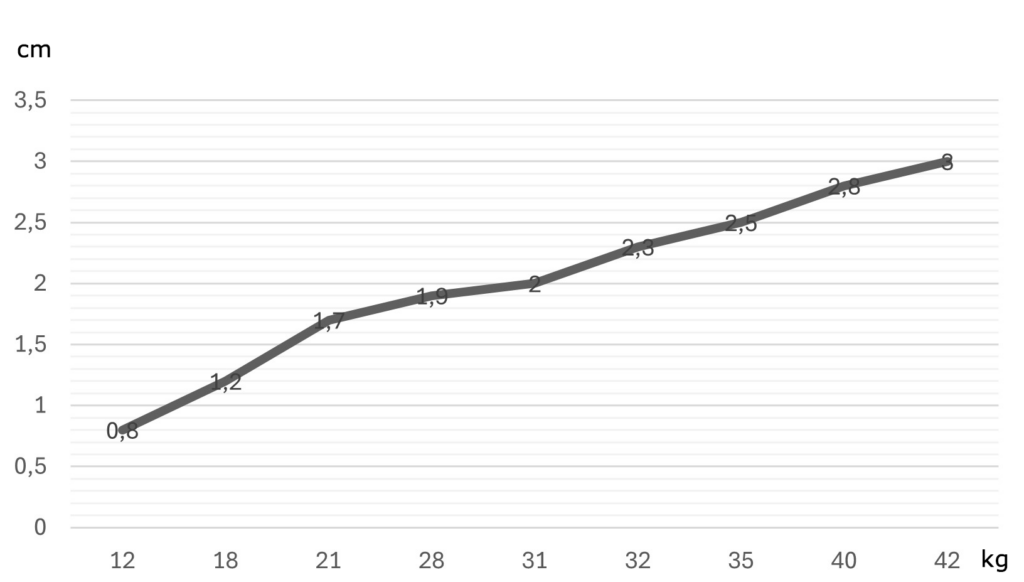
BEAM TEST
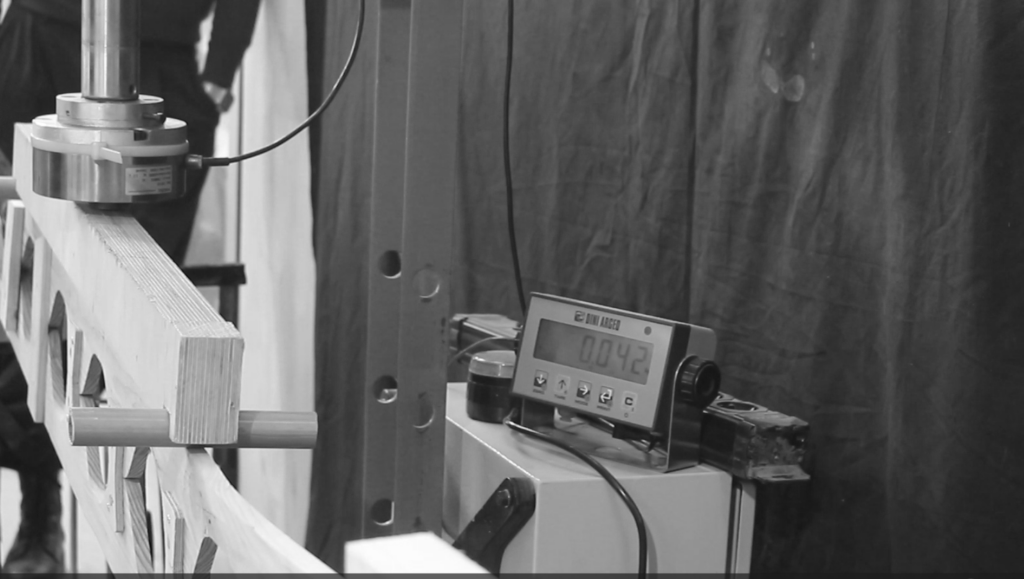
Max Deformation in Beam Test = 3cm
Max Load = 42kg
KARAMBA ANALYSIS
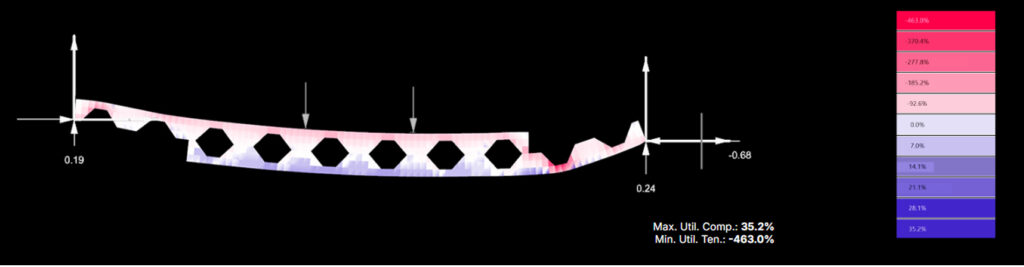
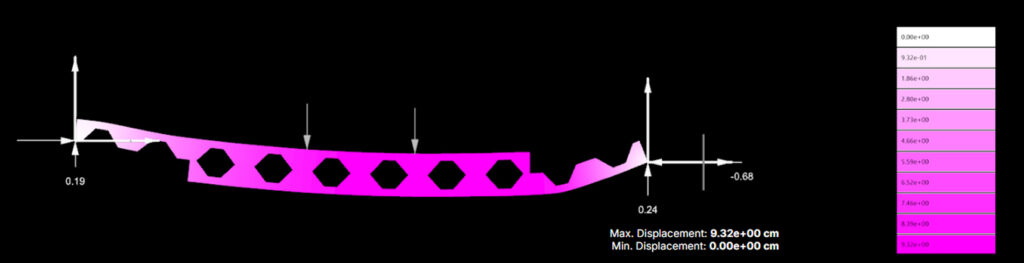
Max Deformation in Karamba = 72cm
Karamba analysis showed too much deformation and shear. Causing buckling and cracking at the ends.
Improvements:
Using a stronger wood
Less voids towards the ends of the beam
Fixing the joints of two pieces
2D utilisation comparison
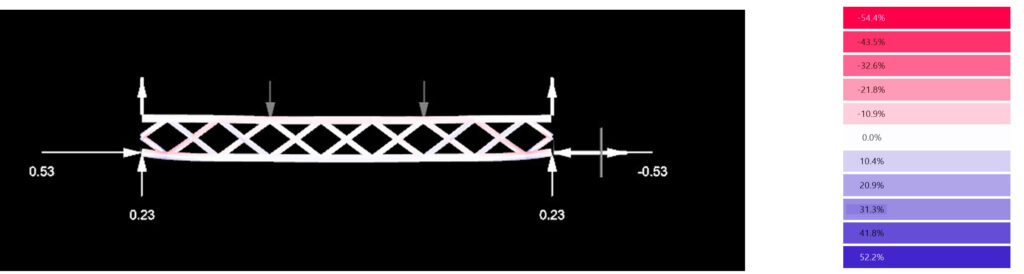
Max. Util. Comp.: 52.2%
Min. Util. Ten.: -54.4%
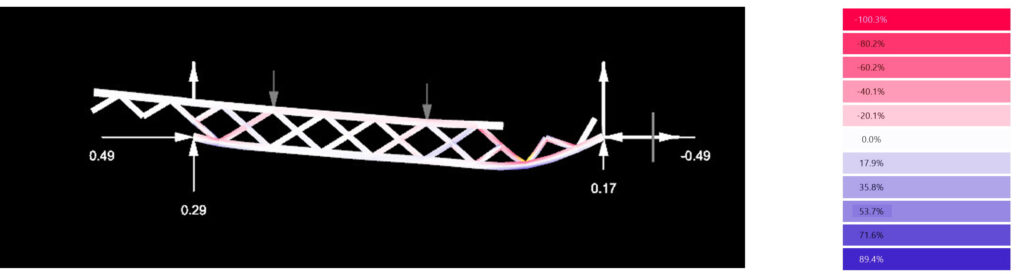
Max. Displacement: 2.98e-01 cm
Min. Displacement: 1.50e-02 cm
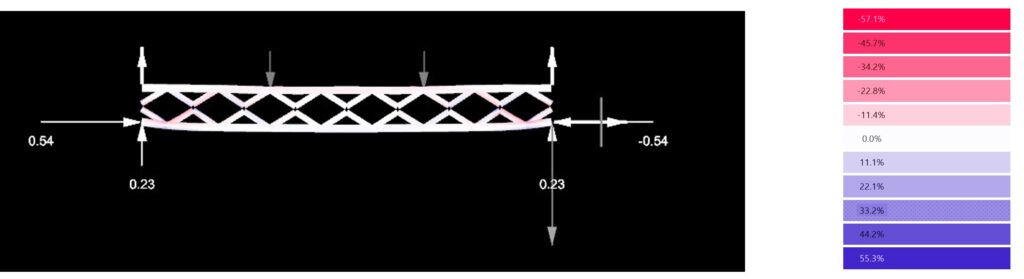
Max. Displacement: 6.76e-02 cm
Min. Displacement: 3.40e-03 cm
2D displacement comparison
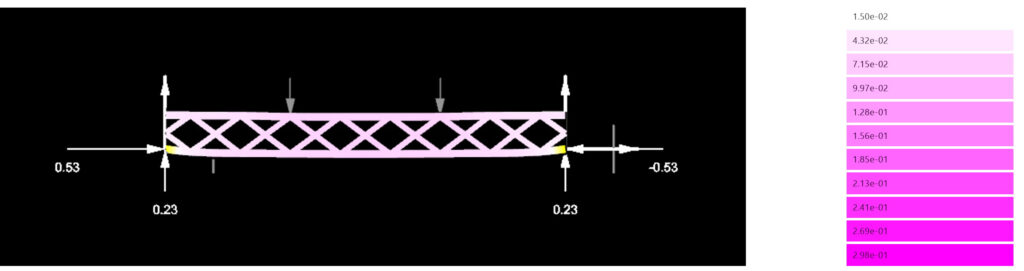
Max. Displacement: 6.18e-02 cm
Min. Displacement: 3.11e-03 cm
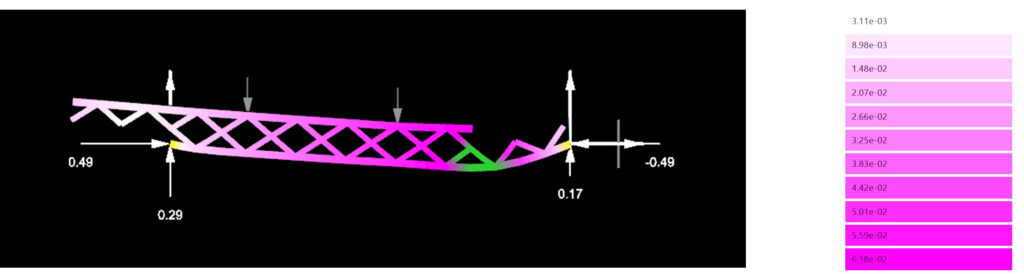
Max. Displacement: 2.98e-01 cm
Min. Displacement: 1.50e-02 cm
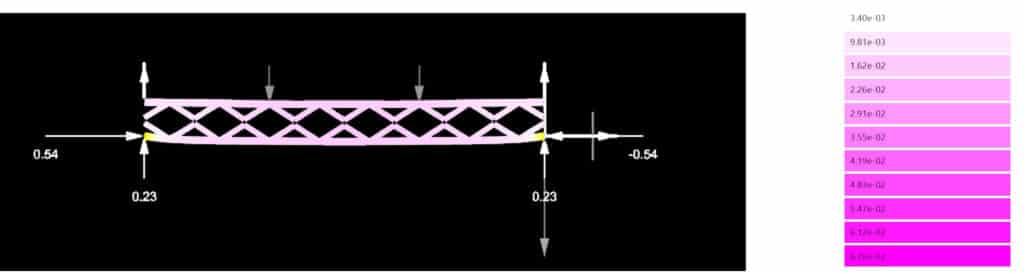
Max. Displacement: 6.76e-02 cm
Min. Displacement: 3.40e-03 cm
Implemented Beams into Existing Structure
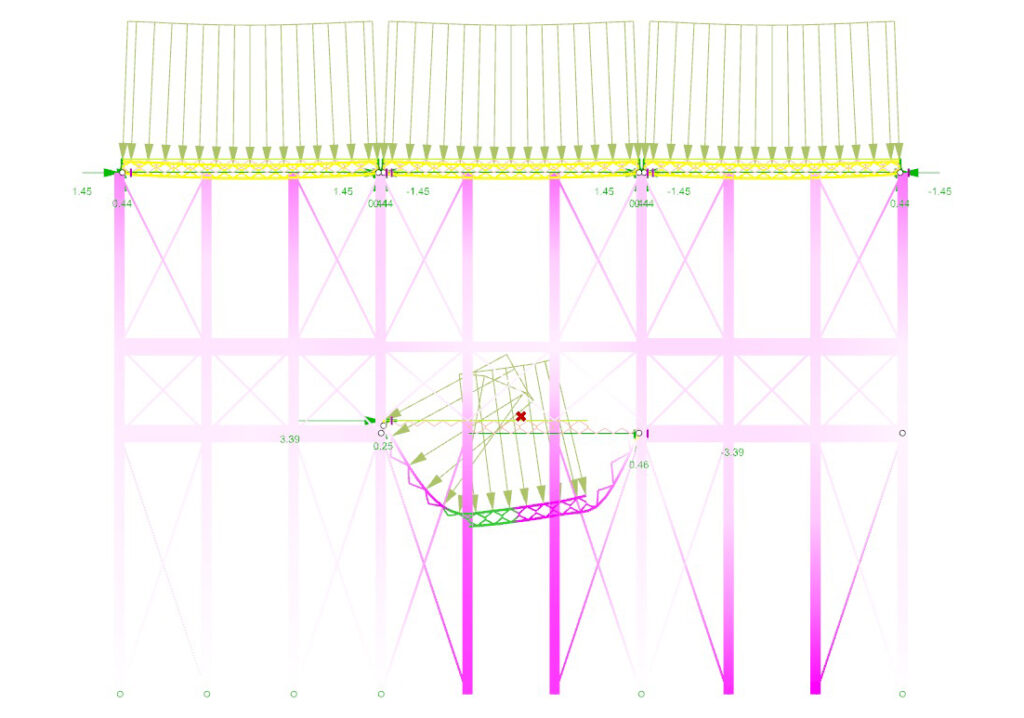
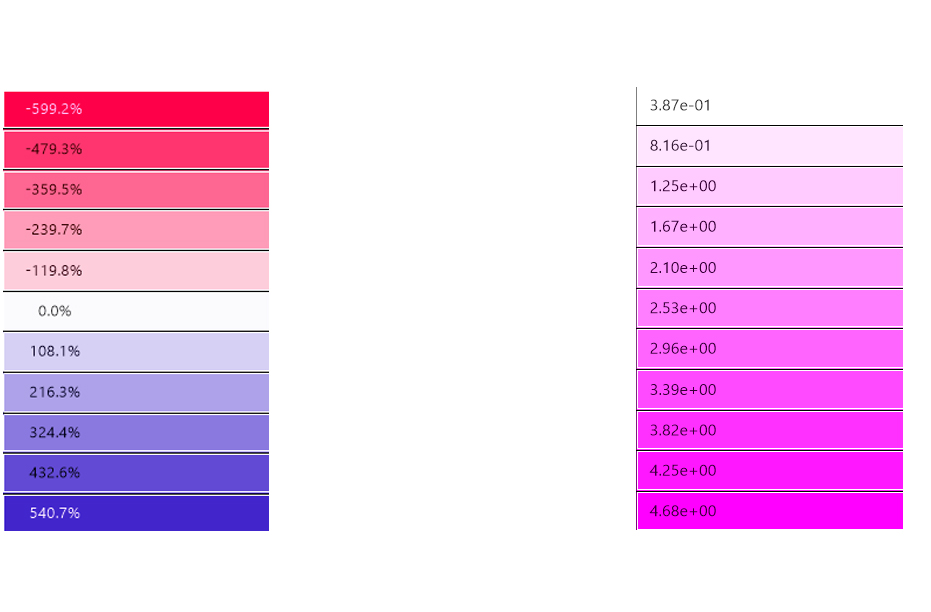
2D utilization analysis
2D displacement analysis
Snow load: 0.3 kN/m2
Span: 3m
h: span/20
Snow load: 0.3 kN/m2
Span: 3m
h: span/20
Max. Util. Comp.: 540.7%
Min. Util. Ten.: –599.2%
Max. Displacement: 4.68e+00 cm
Min. Displacement: 3.87e-01 cm
Solid timber beam
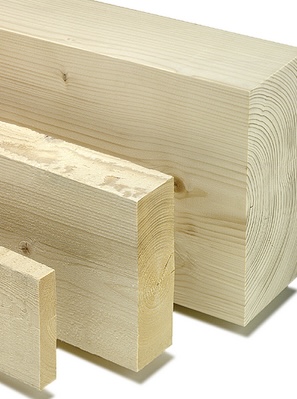
170x75mm deep C24 12.3kg for 2m
480 kg/m3 CO₂ Emission
Castellated RE-USE beam
200x9mm deep plywood 2kg for 2m
21.1744 kg/m3 CO₂ Emission
CNC MILLING
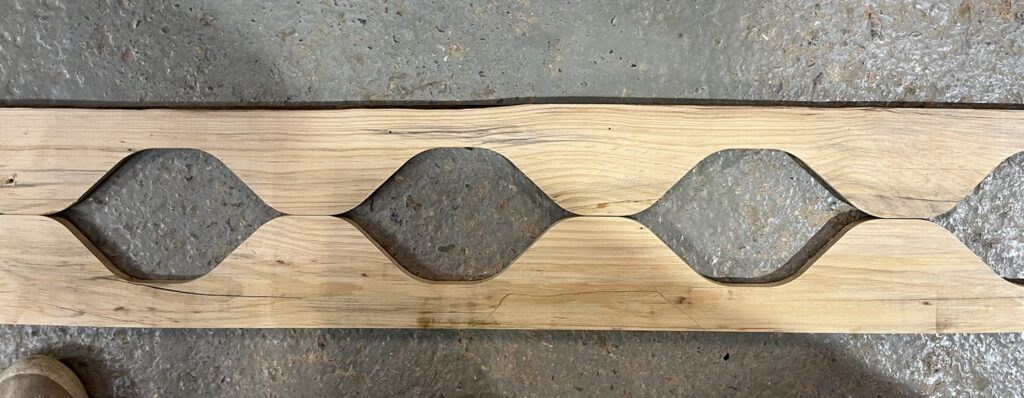
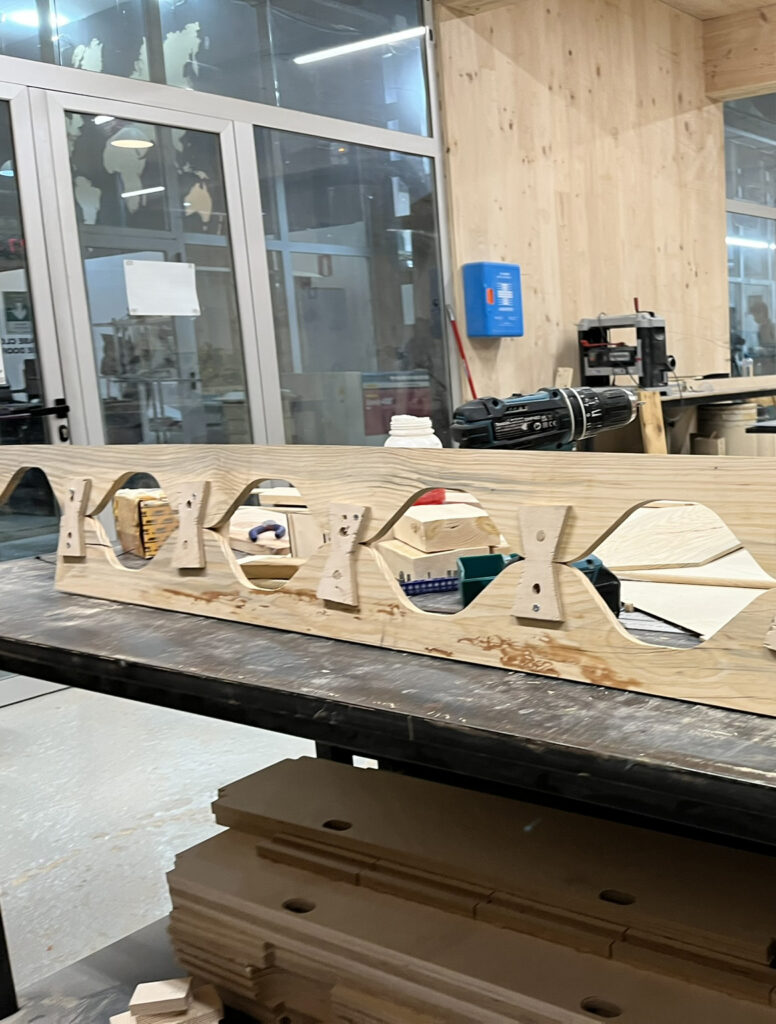