Fab.AR: Manual Fabrication assisted with Augmented Reality invites to explore the toolchain of Augmented Reality when applied to fabrication related scenarios, combining physical prototyping, material testing, computational design and augmented reality, in order to bridge the gap between the physical and digital realm and propose new ways for guided manual fabrication.
Syllabus
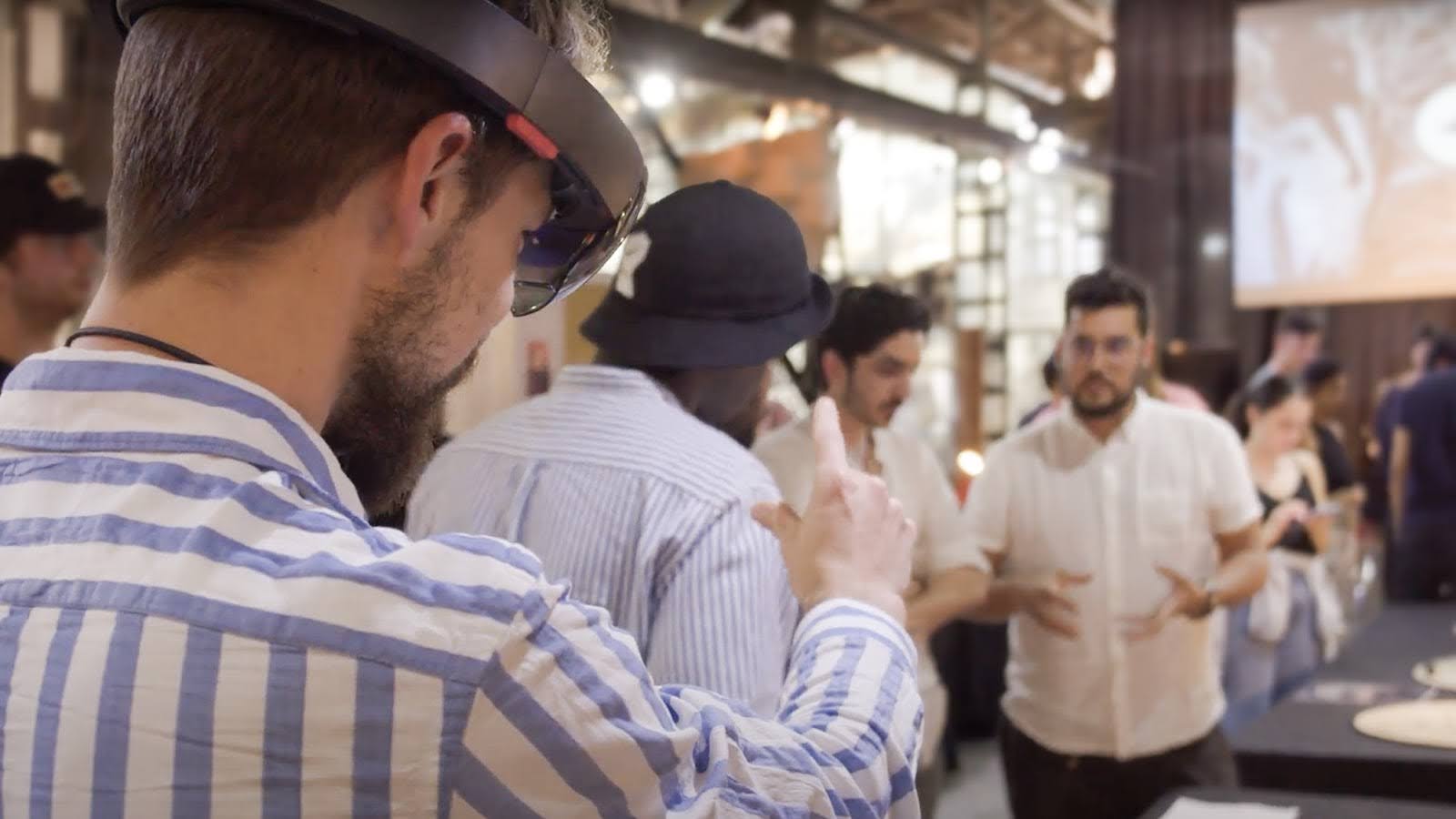
Credits: Fab.AR Seminar Final Presentations, 2022
Digital fabrication allows architects to achieve high precision and extreme variability of designs. Computational design tools further expand the ability to express complex geometries, simulate natural processes, and interface with fabrication machines. Architecture has been increasingly absorbing knowledge and tools from related fields, and architects and designers are pushed to consider even more facets for the projects, while keeping the core ideas reachable. However, from the design perspective, these technological advancements come with the common challenge of relative rigidity of control over the target definition or implementation. Additionally, the clients without the previous knowledge tend to see these design constraints as a black box. To reach the high precision of fabrication and assembly, a decision has to be made between a certain level of flexibility of manual fabrication and design tools, and level of complexity and precision of fabrication techniques.
To address these issues, students are invited to explore Mixed Reality (MR) applications in their workflows. The recent advancements in MR technologies have opened up possibilities to overlap digital information on top of physical spaces. Out of the full spectrum of MR technologies, Augmented Reality (AR) provides a vast range of possibilities at all stages of the creative process: from design to ideation, from visualisation to communication, from assistance in fabrication to assembly. Democratisation of the technology made it extremely accessible, leaving the stage of purely technological experiments or recreational applications – into fully integrated real-world use cases and practical tools. This unique ability to easily create custom interfaces and tools to facilitate our creative expression through MR will be the primary focus of this two-term seminar.
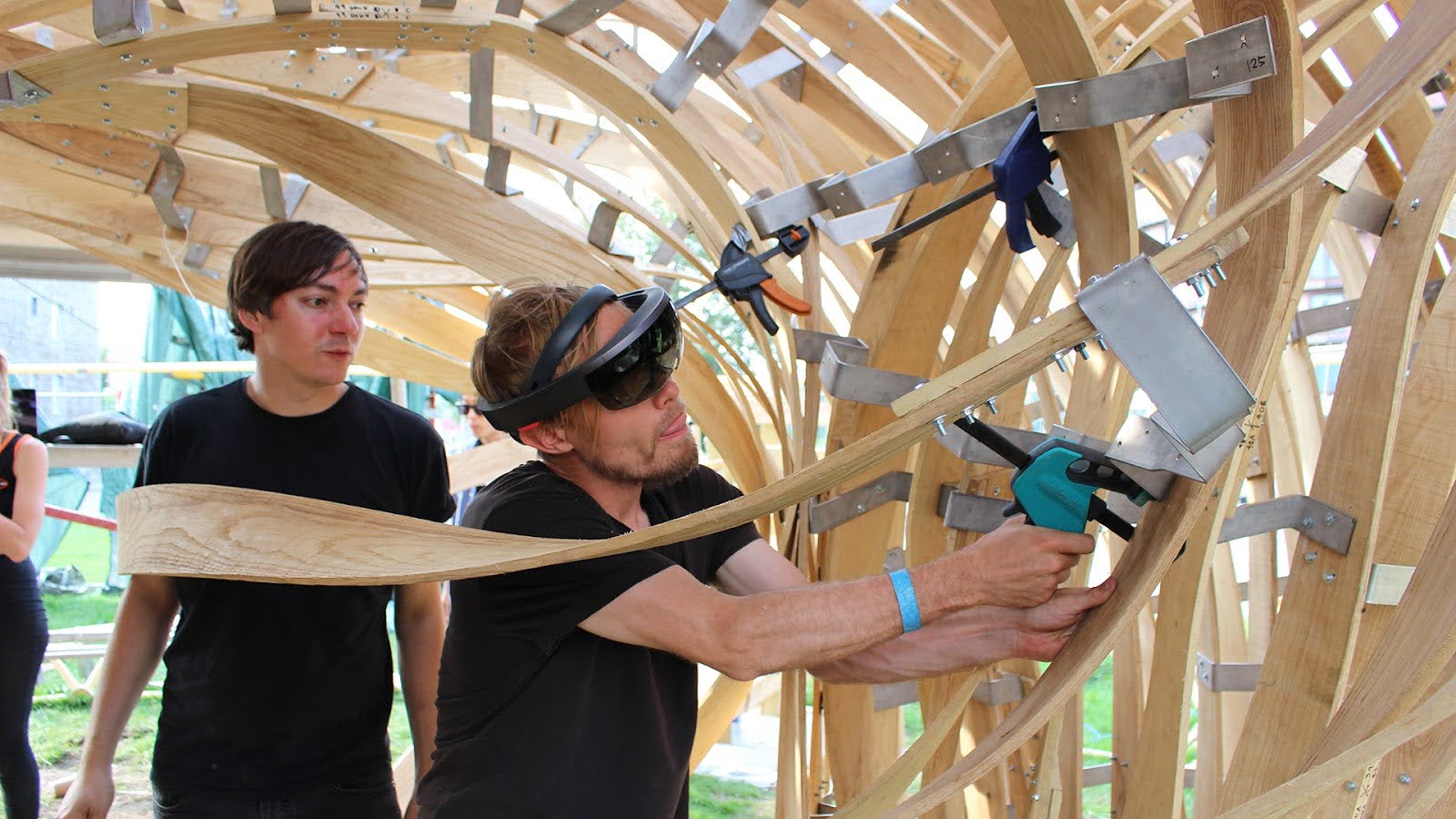
Credits: Steampunk Pavilion by Gwyllim Jahn & Cameron Newnham (Fologram), Soomeen Hahm Design & Igor Pantic, 2019
Within the seminar, students are invited to explore the toolchain of AR when applied to fabrication related scenarios, combining physical prototyping, material testing, and computational design, – developing new ways for assisted manual fabrication and assembly, and thus bridging the gap between the physical and digital aspects of the profession. To achieve this, students will develop bespoke digital tools and explore new possibilities for communication they can bring.
Around this core objective, within the first part of the course, students are invited to build up the base knowledge and experience of setting up such blended setups using Unity platform. The second part will act as a common ground to apply the learned tools within a workshop format, with a joint goal of a large-scale prototyping. Students are expected to design a group case study proposal, which would require the extra layer of information to be realised, and which would otherwise need disproportionally high-tech solutions.
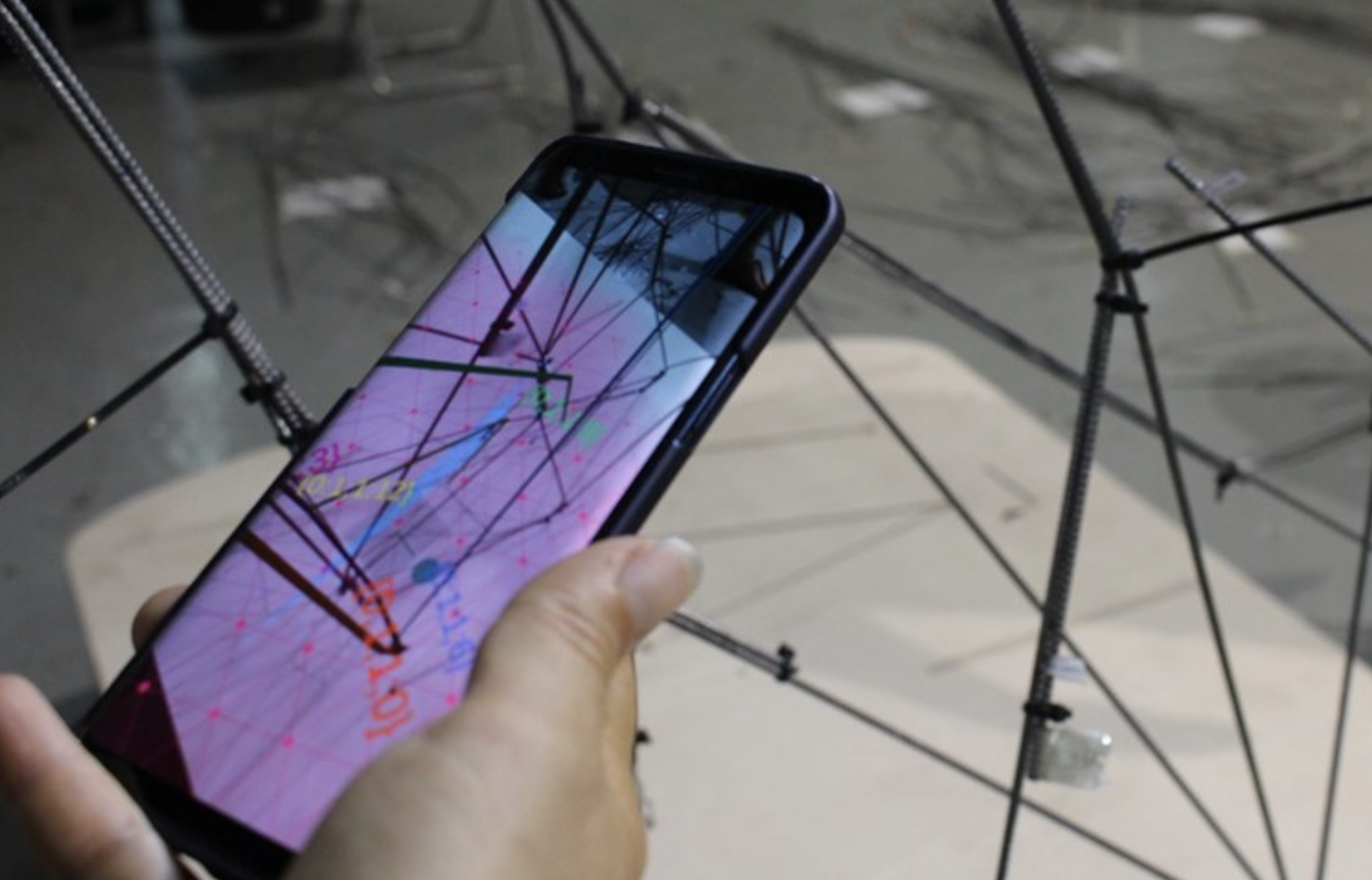
Credits: HoloFab by Ardeshir Talaei, Daniil Koshelyuk & Armin Akbari, 2018
Learning Objectives
At course completion the student will:
- Know how to work with Unity;
- Know how to create practical prototype interfaces in AR and MR applications;
- Be able to identify the most relevant toolset for a specific idea out of this spectrum;
- Be able to bridge the gap between the digital and the physical worlds;
- Experiment with fabrication-related applications of these technologies:
- Developing a workflow for assisted fabrication through the use of AR;
- Exploring a case study applying it to a materials system and fabrication/assembly technique that is guided via AR;
- Expanding the possibilities of a manual fabrication process by overlaying digital aspects of design in AR;
- Showcase the learnings by applying them to a large-scale prototype.
Faculty
Projects from this course
360 SPINX
360 SPINX – Introducing the leading-edge application merging groundbreaking fabrication methodologies with augmented reality (AR) technology to streamline the assembly of Kinetic, non-standardized building forms. This innovative tool leverages AR’s prowess to deliver meticulous instructions for diverse layers of kinetic structural reinforcement and service-related components. By seamlessly integrating AR guidance, it guarantees unparalleled accuracy and … Read more
BuildLens.XR
BuildLens.XR: An application that combines innovative fabrication techniques with augmented reality (AR) technology to simplify the construction of non-standardized building forms. By harnessing the capabilities of AR, this tool provides precise guidance for various layers of structural reinforcement and other service-related components, ensuring accuracy and efficiency throughout the fabrication process. With BuildLens.XR, users receive real-time … Read more
ARAS_Augmented Reality Aided Synthesis
Welcome to ARAS, your tool for creating complex architectural designs using AR and VR technologies. This Blog will guide you through its features, helping you bring your visions to life in an intuitive and immersive way. Let’s start creating with ARAS! Prototype Video
Fold.AR
Fold.AR: Unleash the magic of paper folding Discover intricate geometries in augmented reality. Explore the possibilities. Folding paper holds significant relevance in elevating the senses of space and design in architecture due to several factors as its versatility, adaptability, expressiveness, tactility, and cultural significant. In essence, folding paper serves as a powerful design tool in … Read more