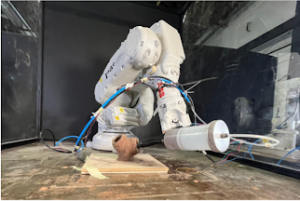
Buildings are currently responsible for 39% of global energy related carbon emissions: 28% from operational emissions, from energy needed to heat, cool and power them, and the remaining 11% from materials and construction (World Green Building Council, 2019) Modern buildings should operate with renewable energy and other technologies to ensure comfort while minimising the emission of carbon dioxide. Considering these significant reductions in operational energy, the focus is increasingly turning to embodied energy in the total sustainability assessment. In this context, additive construction offers tremendous potential, as it promises efficient material use (Dilenburger, 2022) and can provide new approaches to fabrication, beyond a single one, in a plethora of methods that respond to multi-layered skills in a building to answer various construction tasks and the individual local context.
The seminar invites students to explore new materials, additive processes and new fields of applications through robotic 3d printing taking advantage of the potential of the 6-axes of the robotic arm. The introduction of robotic arms in additive manufacturing enables scaling up of three dimensional (3D) and new path geometries. As a result, novel design potential is unlocked by having control over the layered configuration of paths in the object, and 3D printing becomes viable for architectural applications.
Building in this context, currently, the majority of large-scale 3D printing in architectural applications is carried out by cementitious printing and FDM printing with plastic materials. However, robotic printing explores the potential of using machines with five or more degrees of freedom by attaching the extruder or print base to a robotic arm opening the field of exploration to advanced possibilities and new biomaterials. Hence, the resulting flexibility in the geometry of paths can help tackle various disadvantages inherent to planar 3D Printing, such as the discretization artefacts, the need for additional support on overhanging parts, and the anisotropy of printed objects.
Therefore, a great field of exploration and new challenges come along with the novel possibilities. In the motion planning and fabrication process, collision, reachability, and smoothness constraints are crucial for the translation of a path geometry into fabrication commands. In addition, the design of path geometry presents another challenge to explore, as the slicing problem is no longer well-defined and requires additional constraints or requirements to narrow down the vast space of possible solutions. These can take the form of optimization objectives, user input, or a combination thereof. While various approaches have been proposed for the optimization of the paths’ geometry, not a lot of research has been developed on methodologies for enabling the user’s control over the print paths (Mitropoulou et al, 2022)
During the workshop, students will focus on the use of 3D Printing techniques with cork-based bio-composite materials from recycled stoppers, taking advantage of the great potential of this material and its innovative applications. Then, students will have the opportunity to develop a parametric system that exhibits a File-to-Factory workflow, capable of integrating fabrication constraints, robotic kinematics, assembly logics, and architectural goals. By the end of the seminar, students should propose an architectural system adapted to the robotic manufacturing of additive construction. The system will be evaluated on :
- Efficiency (ratio of used material vs waste)
- Stability (capacity to support self-load and external loads)
- Lightness (ratio of empty space vs material volume)
- Design (additional performance or strength)
Learning Objectives
The objective of the workshop is to prototype, fabricate and explore new possibilities in material through robotic additive manufacturing. With an overview of the state of the art in the syntax of additive manufacturing geometries and its influence on material capabilities. Discuss the practical implementation of custom end effectors, and brainstorm to later produce the most performative model with this technology. At course completion the student will learn:
- Have an overview of the possible robotic additive manufacturing processes available for architects and designers.
- Understand the basics of robotic kinematics, robotic simulation and robotic control.
- Communication between ABB arm robot and custom end effector
- How to calibrate/adjust end-effector tools and possible modifications of them
- Be capable of generating the robotic simulation and production files to produce a prototype.
- Be capable of integrating the limitations and opportunities of a specific robotics process into a final architecture design
- To think independently about novel robotic workflow concepts and implement them in small groups.