Our project represents the intersection of traditional ceramic craftsmanship and the precision of modern robotics, aiming to innovate within the field of ceramic glazing.
The Essence of Ceramics and Glazing
Ceramics, an integral part of human civilization, find their essence in the art of glazing. This process transforms simple clay objects into functional and decorative items by applying a pigment film and firing at high temperatures. Despite its long history, we’ve identified a niche for innovation within this traditional practice, particularly in the realm of 3D printed clay pieces.
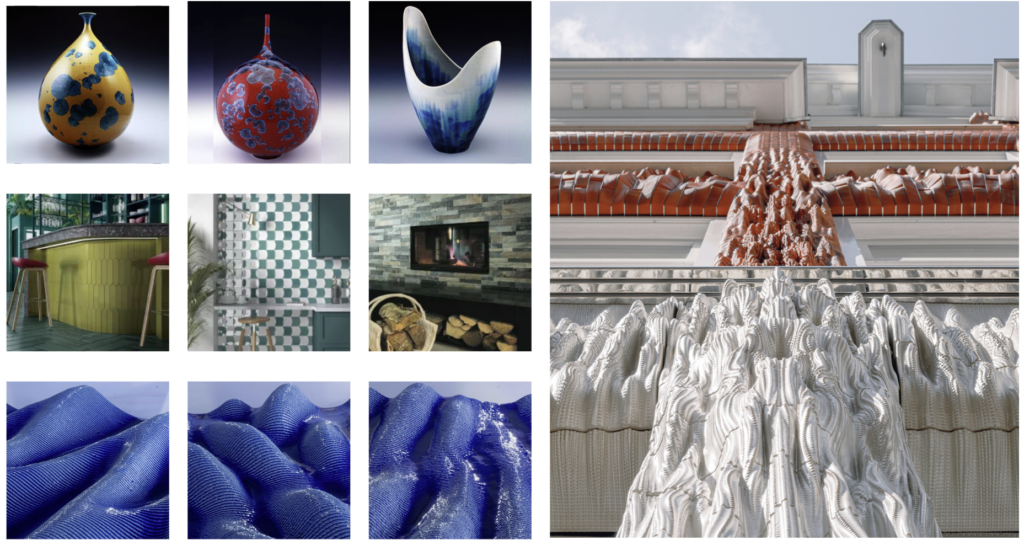
The benefits of glazing extend beyond merely the aesthetics; it renders the clay waterproof, antibacterial, and imparts additional properties like reflectiveness and heat insulation, thereby enhancing its appearance and utility.
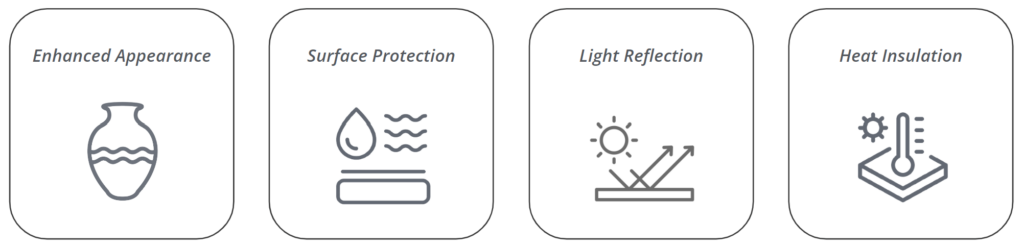
Due to these features, it we decided to further research and developed the core question driving our semester-long project has been: How can we develop a robotic system capable of precisely glazing 3D printed clay pieces? Glazing Virtuoso is our answer to this query, leveraging advanced technologies such as machine learning, vision systems, and robotics to achieve mass customization in ceramics that manual processes cannot match in efficiency or creativity.
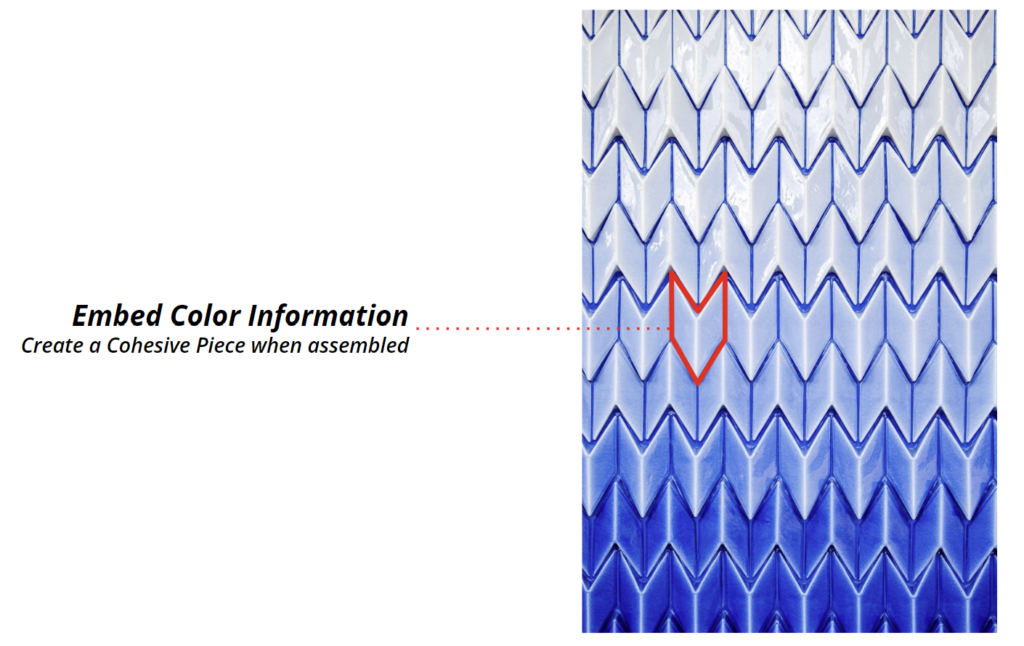
We want to create large assemblies, In each piece of a assembly we want to have embedded information about the glazing type and toolpaths and properties, creating a system that can quickly glaze multiple complex designs, without much human intervention. Trying to improve the workflow for large assemblies of 3d printed ceramic pieces.
Glazing Market Analysis
In the current glazing market, we’ve analyzed our positioning through a two-axis framework. The Y-axis contrasts low output with high output, while the X-axis compares automation to hand-painted techniques. High output signifies a reliance on rigid production line machines which, despite requiring considerable time and effort to set up, offer speed and high efficiency primarily for consumer products. Conversely, low output is characterized by artisan methods that, while time-intensive and demanding skilled labor, provide a greater degree of control and artistic freedom. Our system Glazing Virtuoso represents a synthesis of these dimensions, employing computer vision and robotics. This approach automates customization and upholds quality, positioning us uniquely between the extremes of high-output mechanization and the meticulous, hands-on artisanal process.
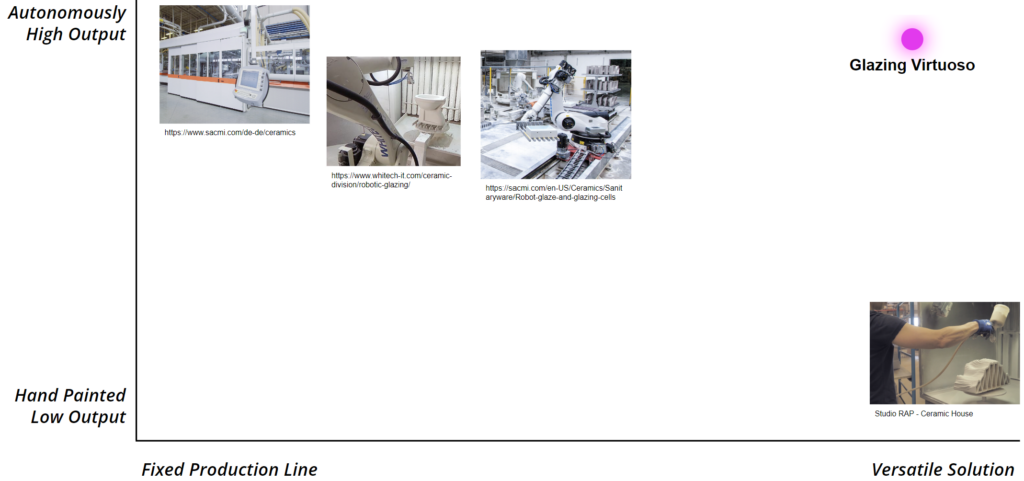
State of the Art
Dür Robotics stands at the forefront with their advanced painting robots designed for efficient integration into high-volume production lines, offering a glimpse into the future of automated manufacturing. Concurrently, Industrial Robotics introduces a user-friendly, no-code solution that appeals especially to artisans and small-scale manufacturers. This innovative approach simplifies the automation process, though it necessitates human input for each new task, blending traditional craftsmanship with modern technology. Meanwhile, OKIBO pushes the boundaries with its autonomous finishing robot, equipped with sophisticated autonomous path planning and 3D environmental scanning, aimed at revolutionizing painting in construction. However, despite its groundbreaking capabilities, the application of such mobile robotic solutions in the glazing sector encounters specific challenges that highlight the complex interplay between technological advancements and industry-specific requirements.
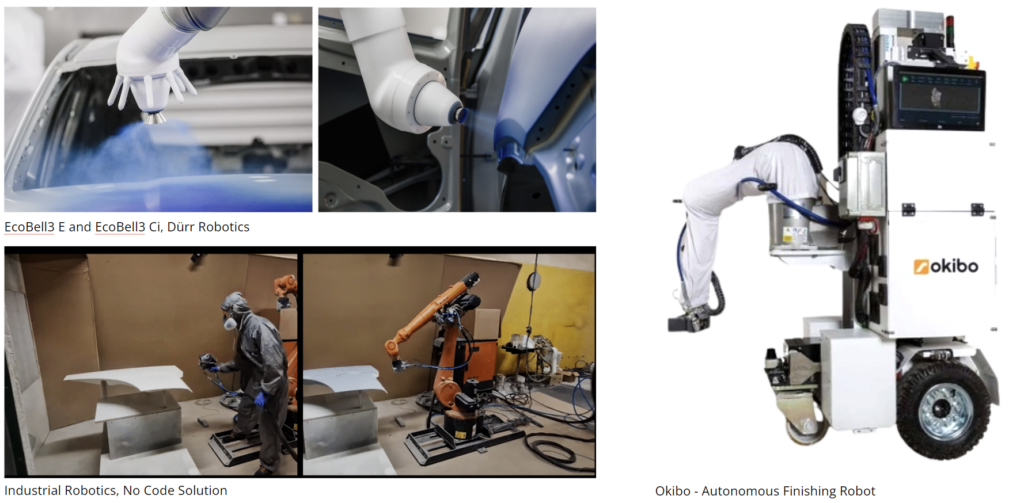
Target Workflow

- Design and 3D Printing: Initiate the process by designing a 3D model of a piece or an assembly of pieces. Once the design is finalized, proceed to 3D print the components, preparing them for the next phase of customization.
- Holistic Painting: Utilize the system to apply paint across multiple panels of the assembly, ensuring the design is integrated seamlessly across all components for a unified aesthetic.
- Toolpath Generation: With the design in place, employ the system to generate computerized toolpaths. These paths are crucial for the painting process and can be adjusted to achieve various effects, such as enhanced textures, depending on the desired outcome.
- Robot-Assisted Glazing: Position the printed piece in front of the robotic glazing system. The robot, equipped with vision technology, loads the predetermined toolpaths and proceeds to glaze the piece precisely as envisioned, applying paint with exceptional accuracy.
- Quality Evaluation and Adjustment: After glazing, the system uses vision technology to evaluate the finished piece against quality standards. This step not only ensures the piece meets the requisite criteria but also identifies any areas requiring improvement, allowing for the generation of new passes to correct quality mistakes, if necessary.
Actual Workflow
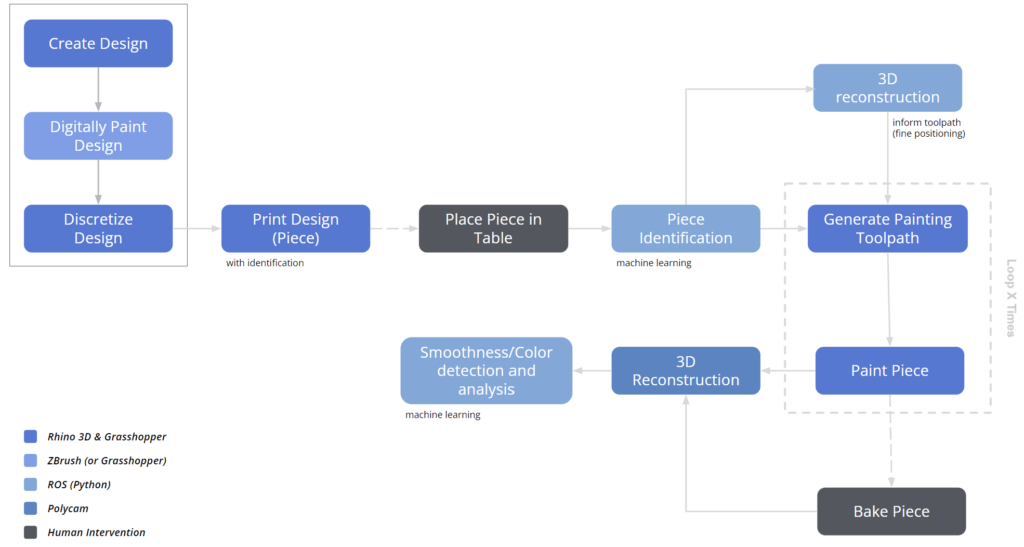
Piece Identification
We want to be able to utilize vision for Piece Identficiation. When the piece identification of the piece is recognized by the camera it should know what piece it is and how to paint it. This will embed information into the piece, which is useful for glazing now, but also for later, if a piece ever get damaged, the associated number can be used to reproduce the piece. For the Piece Identification we tested multiple methods. The one we found to be most effective was machine learning, it produced the best results with the least false recognitions.
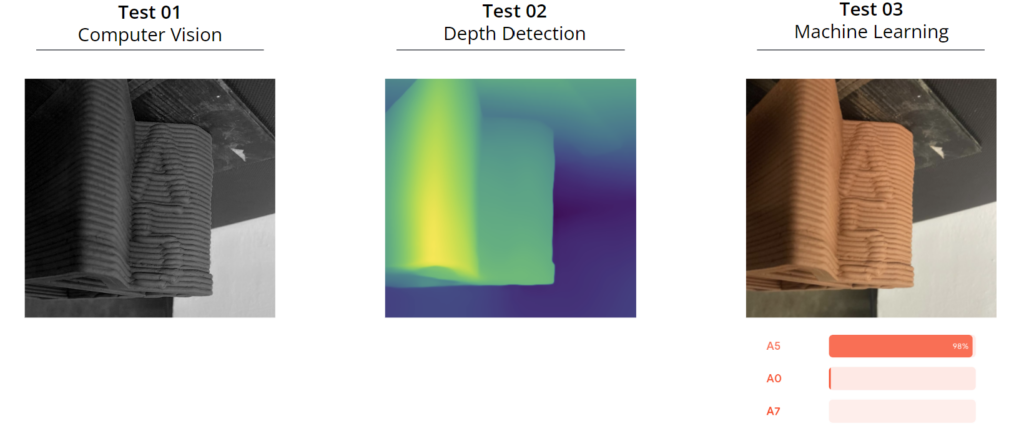
3D Reconstruction
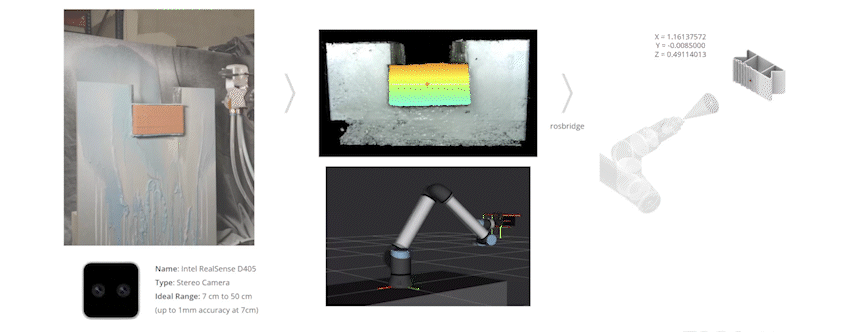
Hardware
For the hardware, the goal was straightforward: we needed a device capable of spraying a liquid with varying viscosities consistently. After some market research and industry insights, we concluded that the best tool for the job would be an air sprayer, with the market leader being xxx. However, we managed to find a nearly identical design that was much more affordable than the €1000 price tag. This sprayer can adjust the spray cone diameter and pressure. It requires feeding the paint to it and is controllable by operating a solenoid, which allows the sprayer to spray just air or a mixture of air and paint. The sprayer received a simple 3D-printed mount to attach it to the robot.
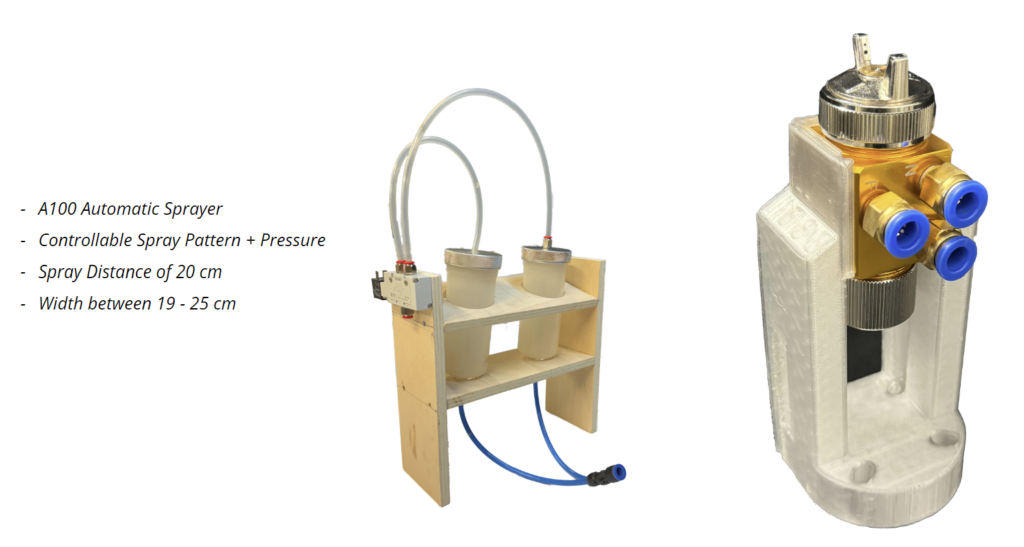
Design
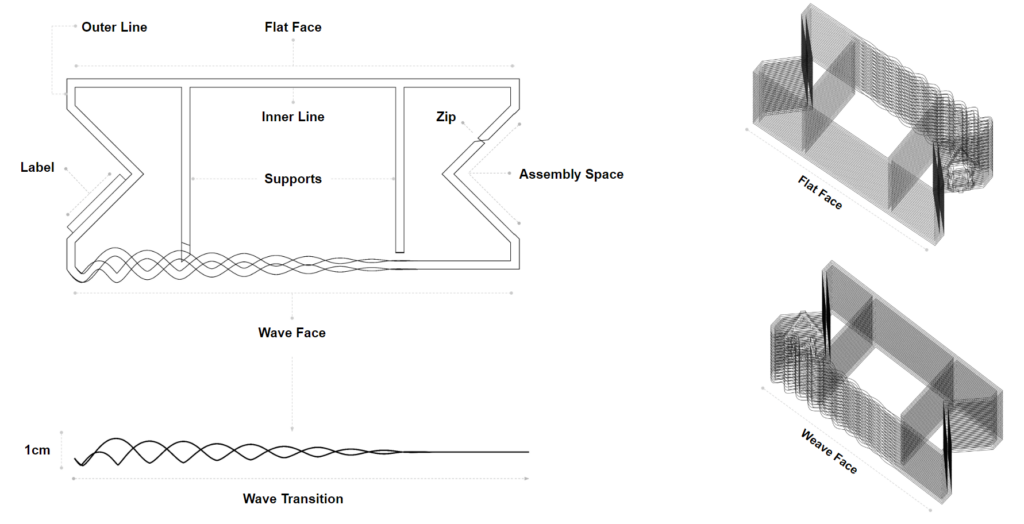
For the design we decided to create a Brick, which we 3D printed out of clay using a desktop extruder. We created the design as a benchmark to measure different variables. We are aiming to tackle large assemblies, which is why our piece assembles into a larger assembly. We have designed it to stack into two towers of five bricks each. the “Assembly Space” is used to align the brick in the spraying setup, the front wave pattern to evaluate how the pattern changes with varying amounts of glaze on it, and the label on the left is used to idenfiy the pieces in teh assembly.
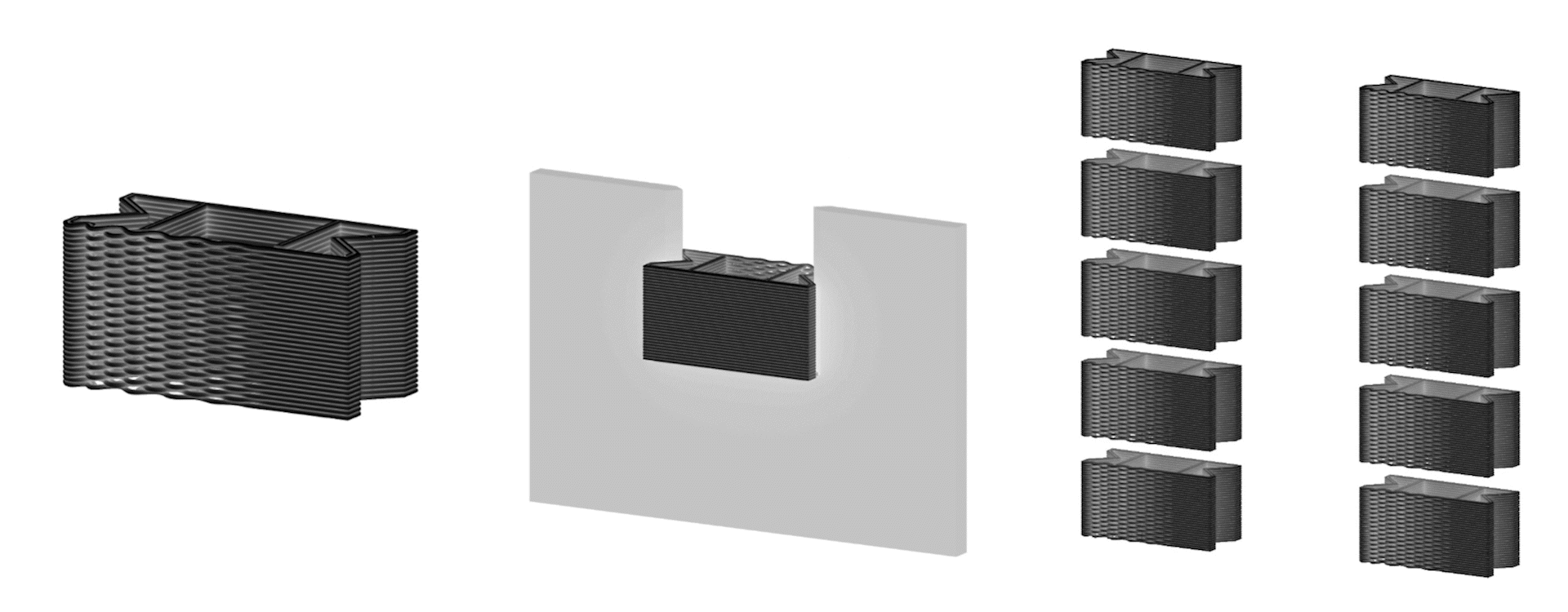
Below are the two Stacks we created. The front and the back are painted to utilize the most amount of surface area for testing our system. We have decided to conduct four tests, which we have highlighted below.
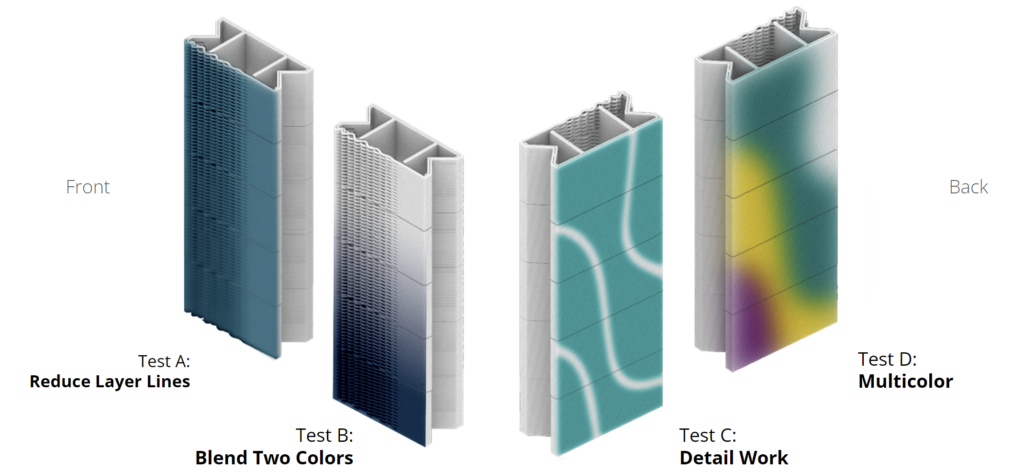
Test A: Reduce Layer Lines
In our first Test we aimed to see what will happen, the more paint we deposit on the piece. We created toolpaths for each brick with increasing amount of passes on each brick varying from two to ten passes.

We documented and compared the pieces from the design to the pre baked and post baked.
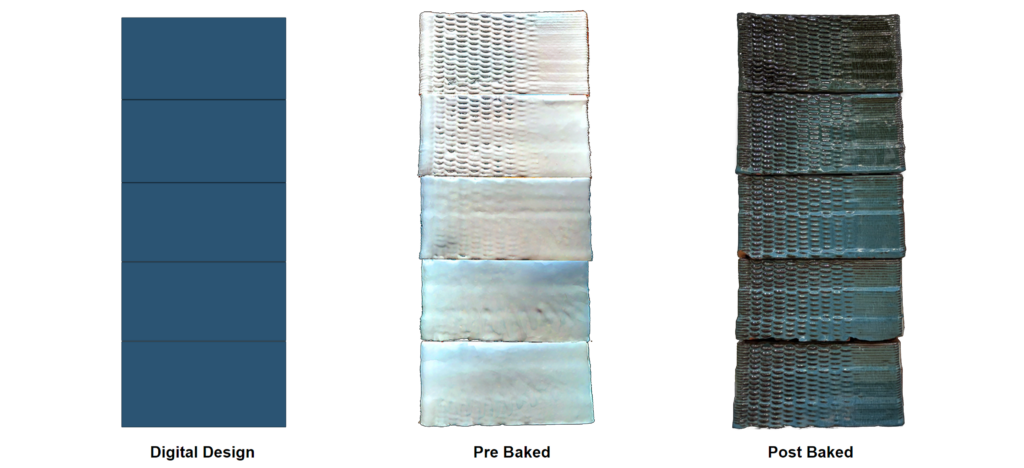
Test B: Blend Two Colors
For Test B we aim to blend two colors. We did this by painting the bricks blue with decreacing amount of glazing players from the top and vice versa with with white.
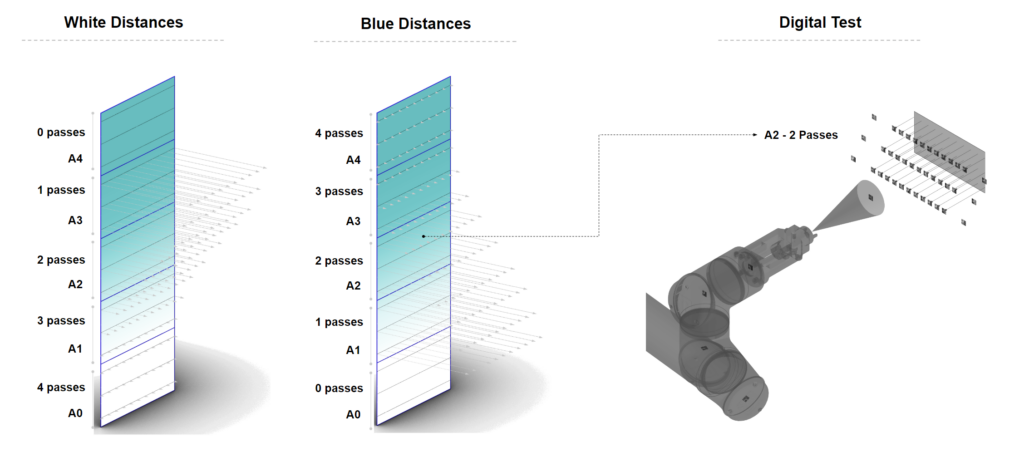
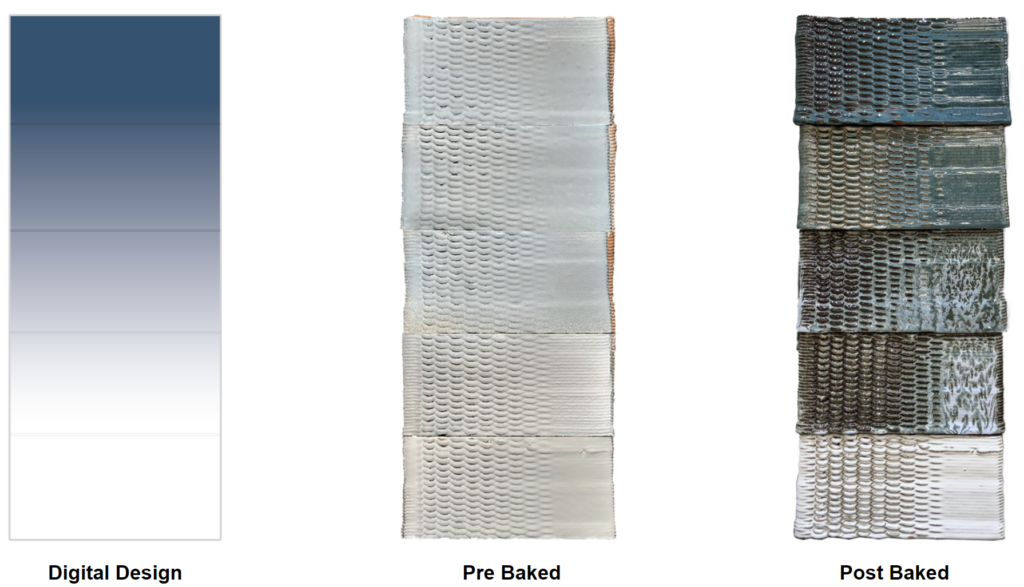
Test C: Detailed Linework
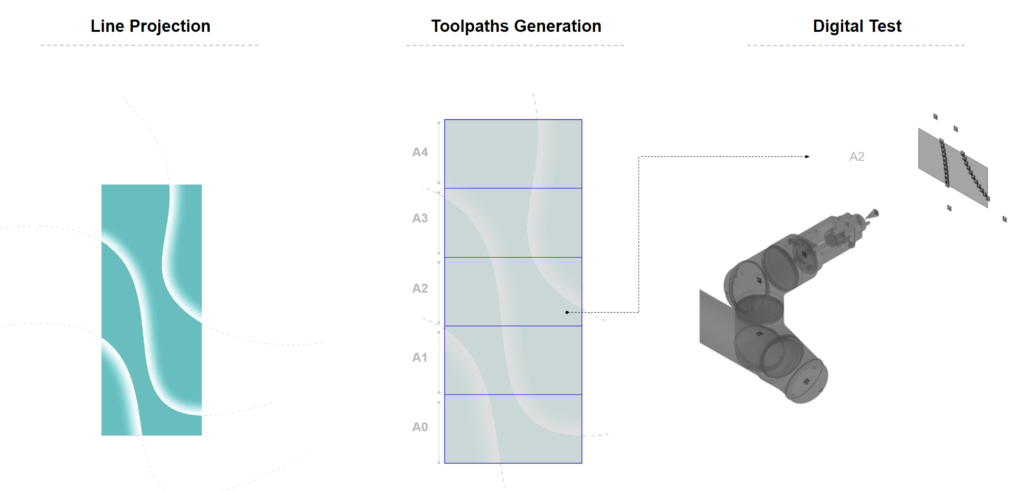
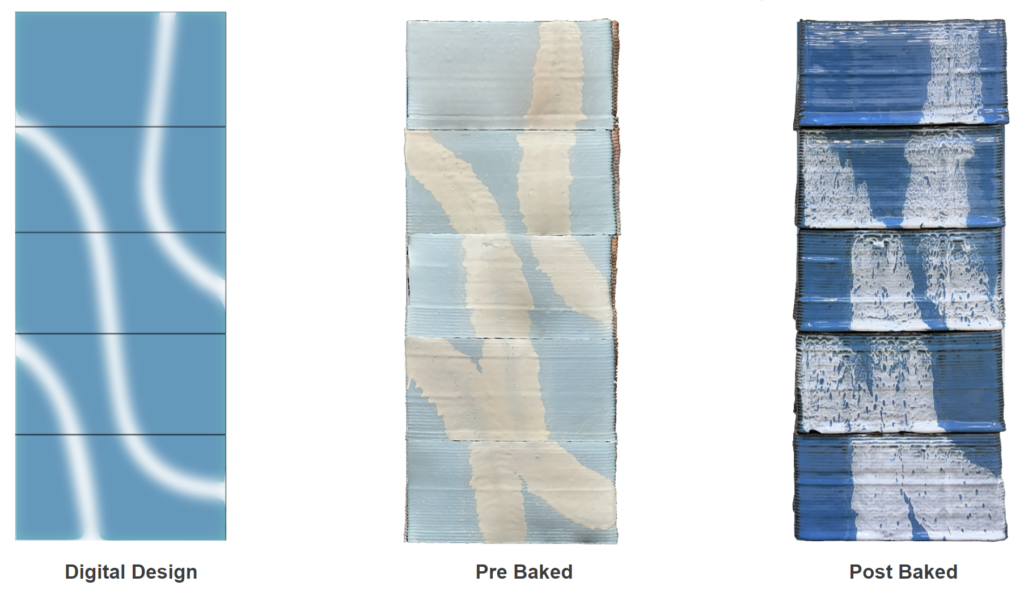
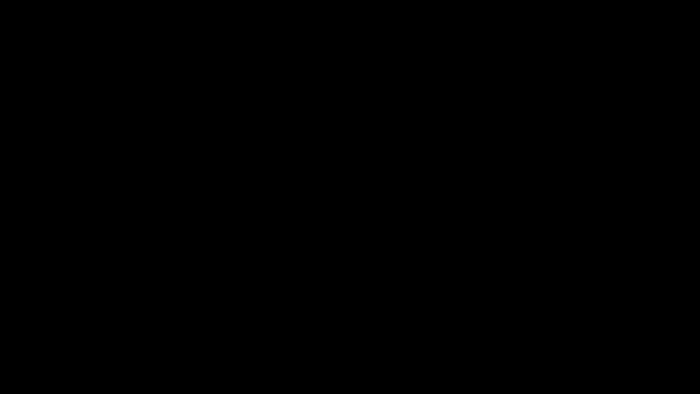
Test D: Multicolor
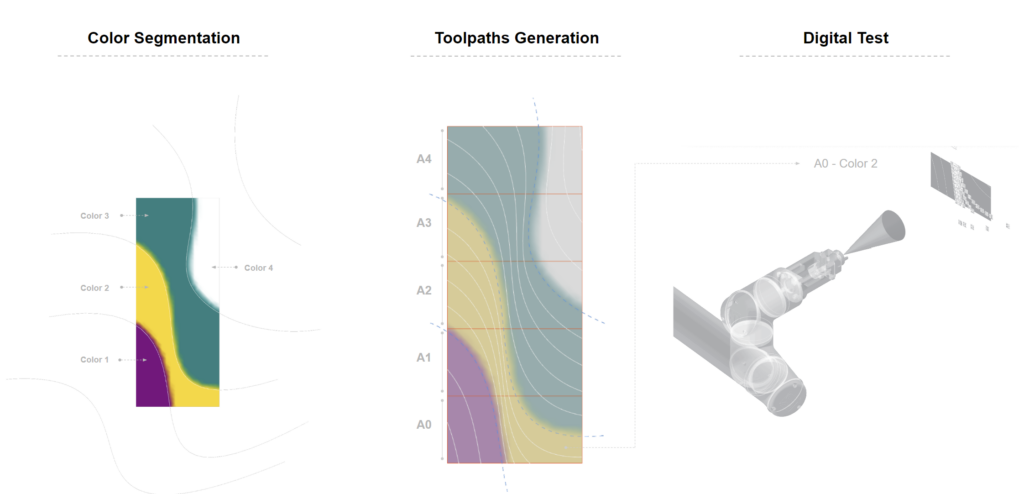
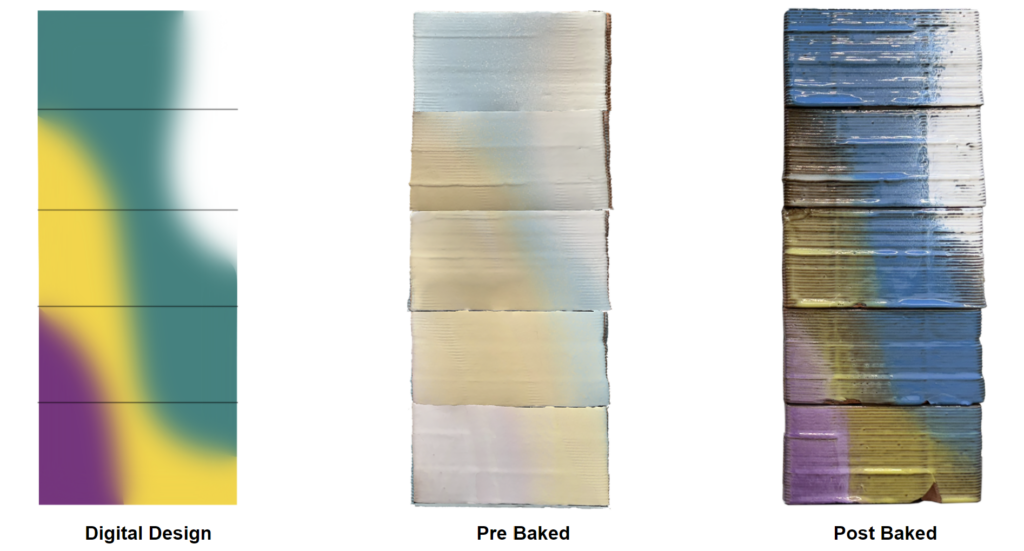
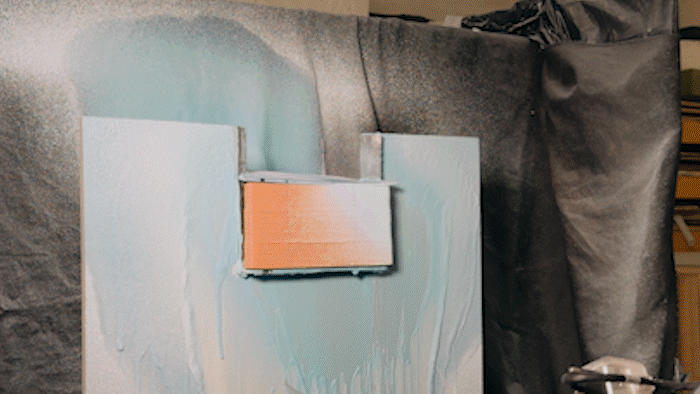