The aim of the research is to investigate the feasibility of using plywood in a hybrid bending active system. The system will integrate restraining elements for both bending actuation and stiffening of the structure, developing a method for scaling up active bending in lightweight construction.
Context_Framework
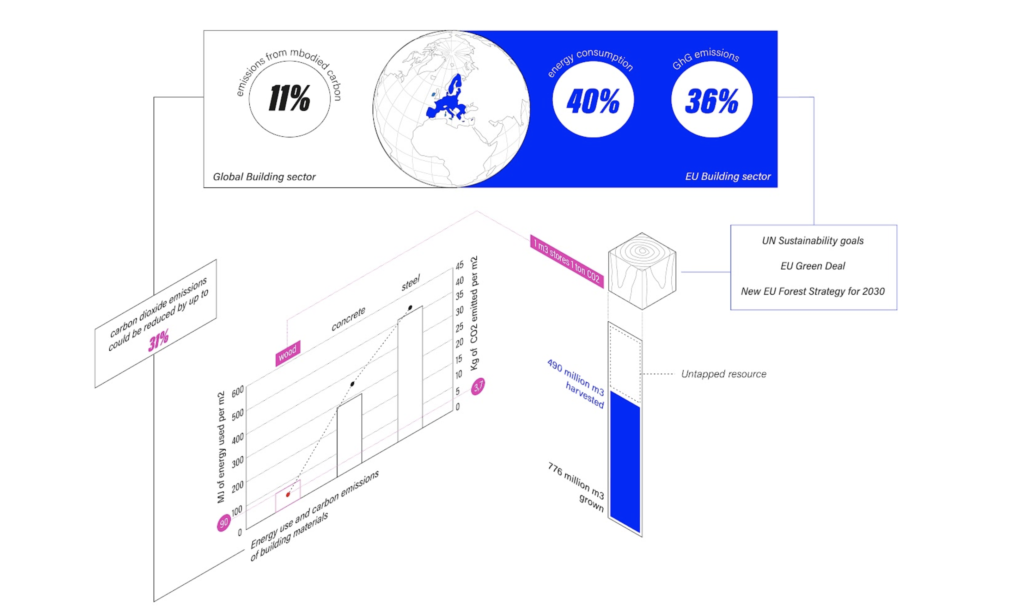
Context_Structural lumber
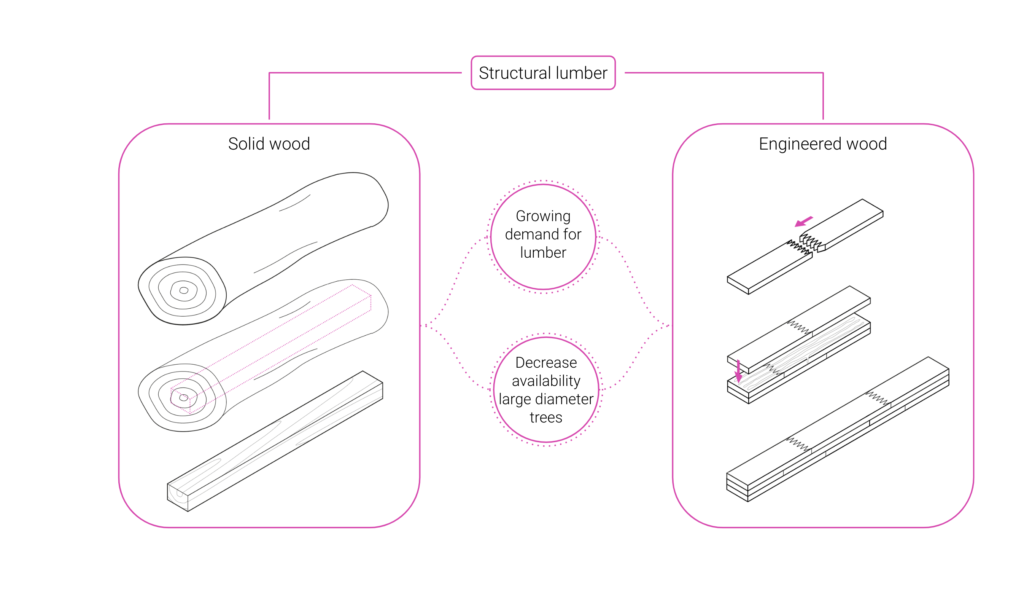
Context_Lightweight construction
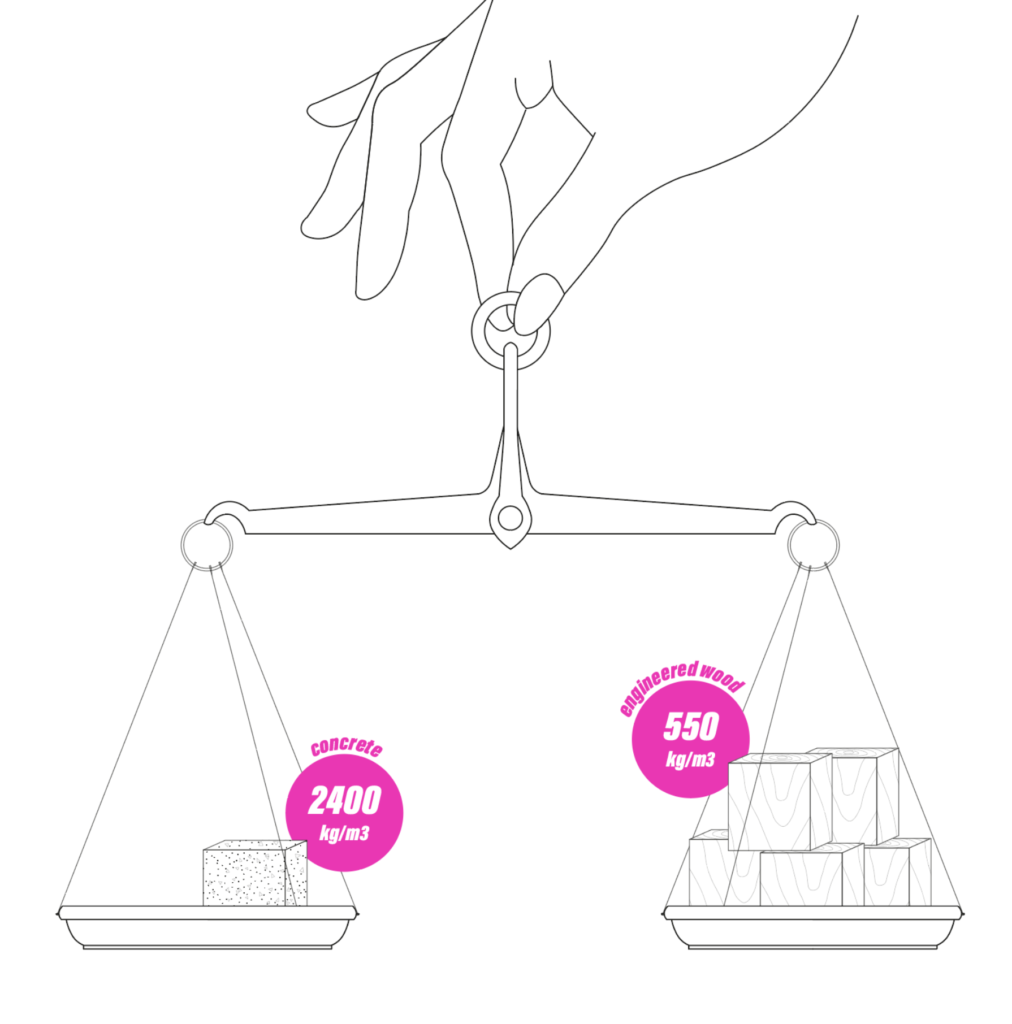
The investigation of lightweight structures and material efficiency can be traced back to the end of the 19th century with Antoni Gaudi through the implementation of form-finding strategies based on material and force through the hanging chain model to achieve structural efficiency.
These explorations led to an increasing interest in alternative lightweight construction principles around the 1950’s and brought the first development of shell structures, which possess strength and rigidity due to its geometry.
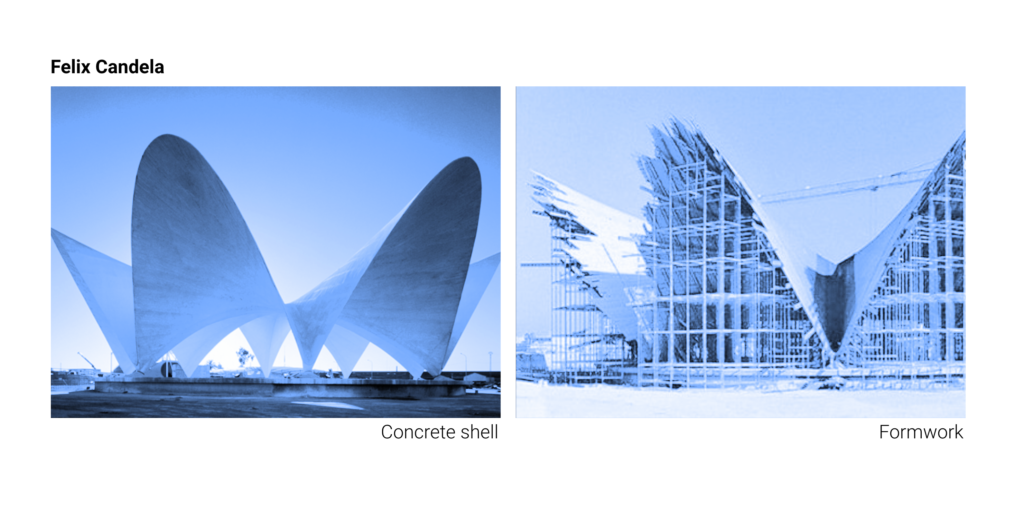
But also bending active systems gained interest. These are structural systems that include curved beam or shell elements that base their geometry on the elastic deformation from an initially straight configurations.
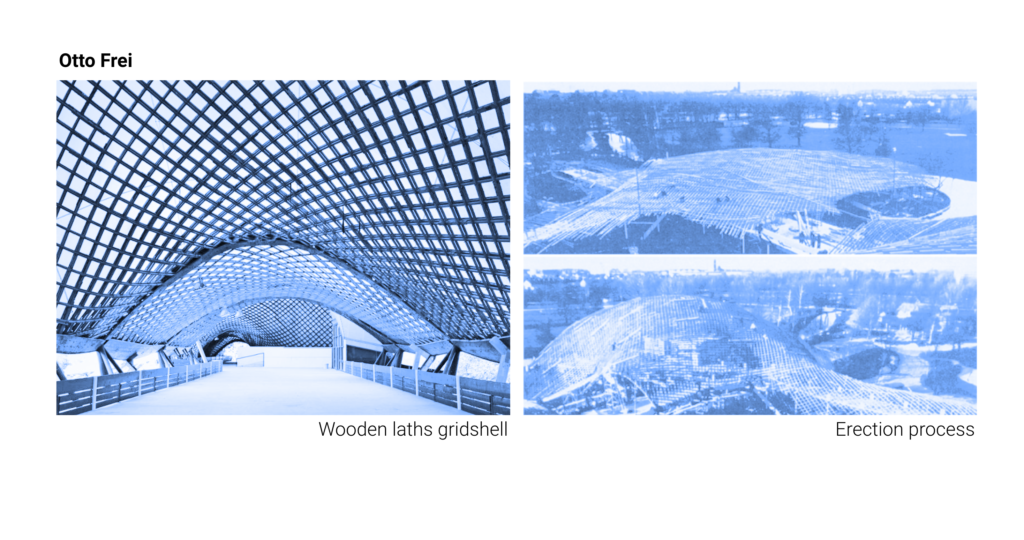
At the time it took enormous time and effort in form finding and engineering of bending active systems that it remained dormant. But recent advancements have given renewed interest in this approach to lightweight construction.
Bending active system_Active bending
Active bending exploits large deformation of material to achieve shape and stiffness from an initially planar element.
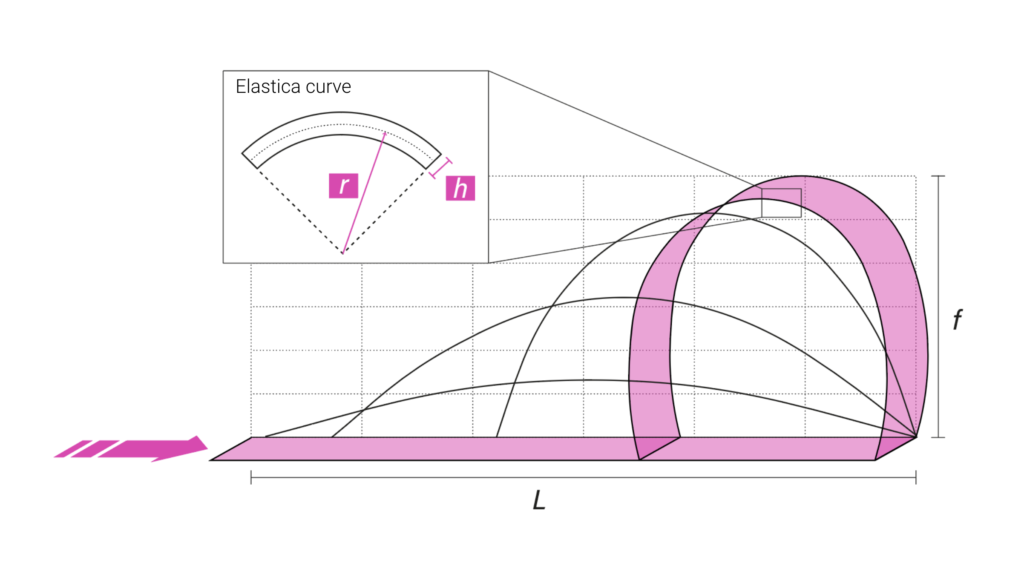
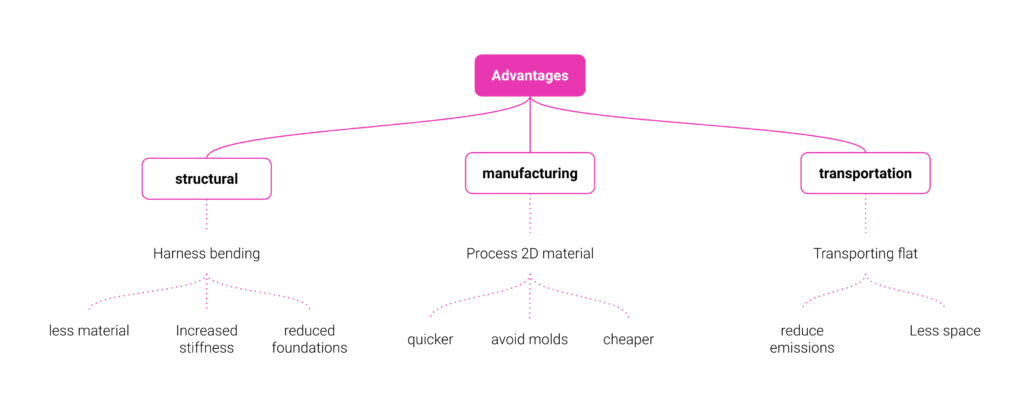
Context_History
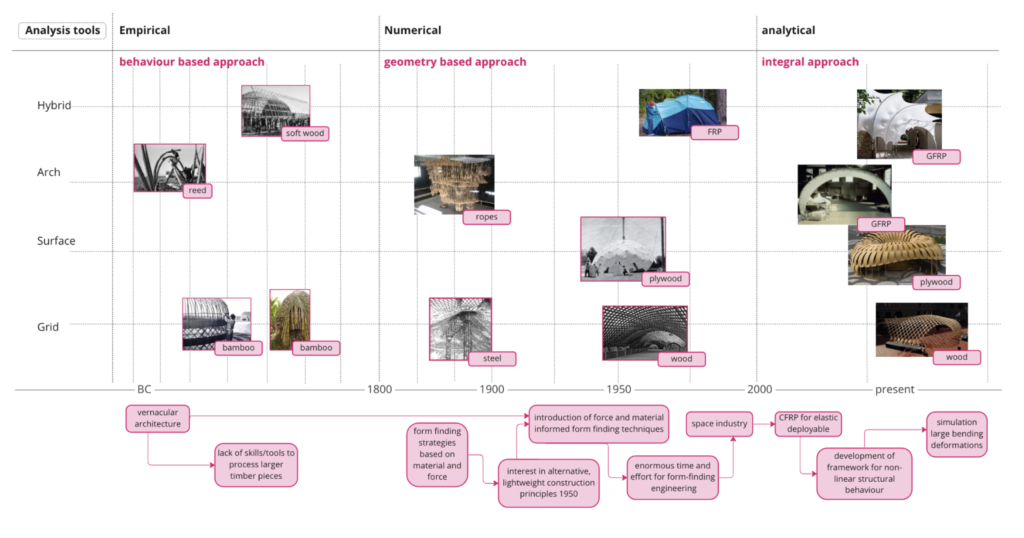
Context_Design approach
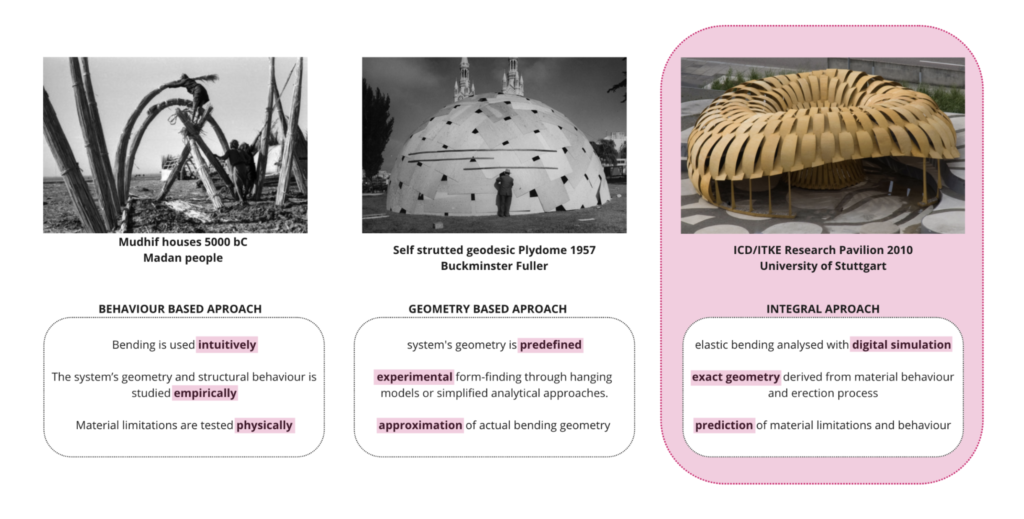
Material_Characteristics
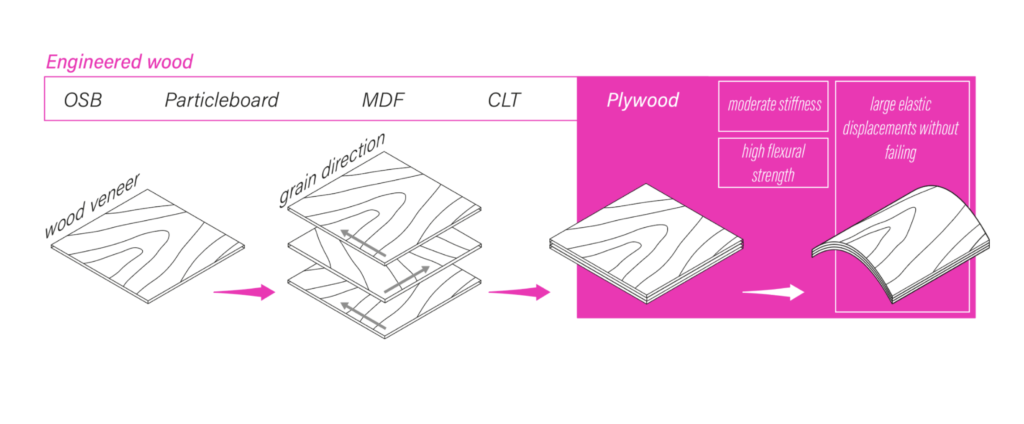
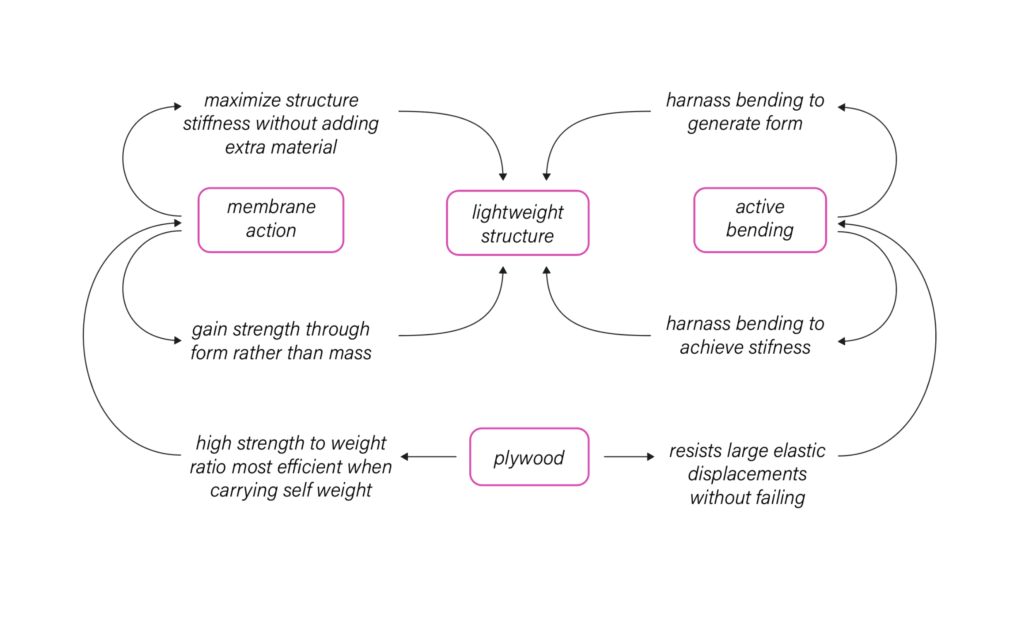
Precedents_Bending active structures
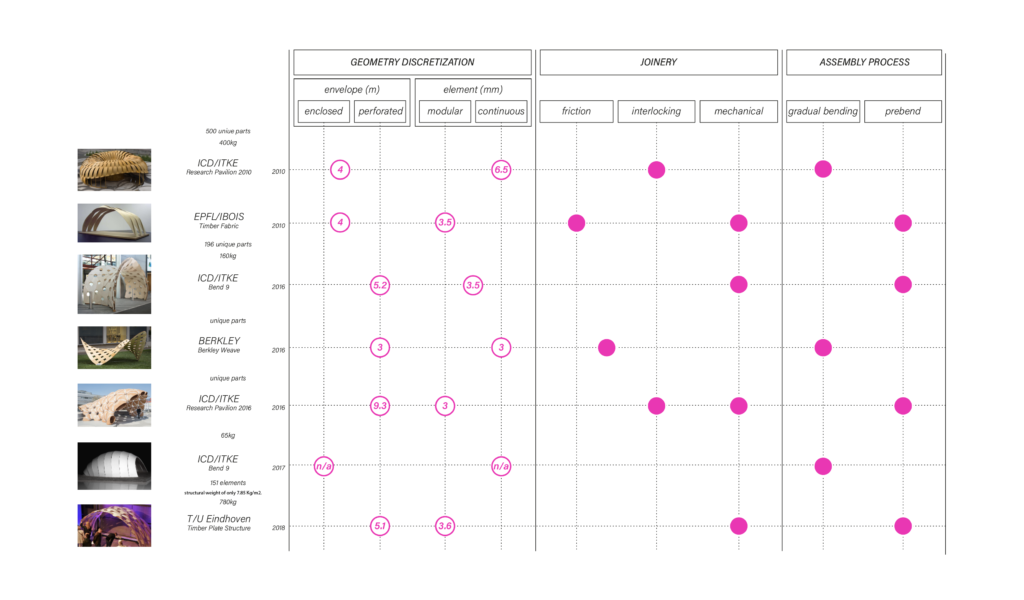
Detected challanges_Parameters
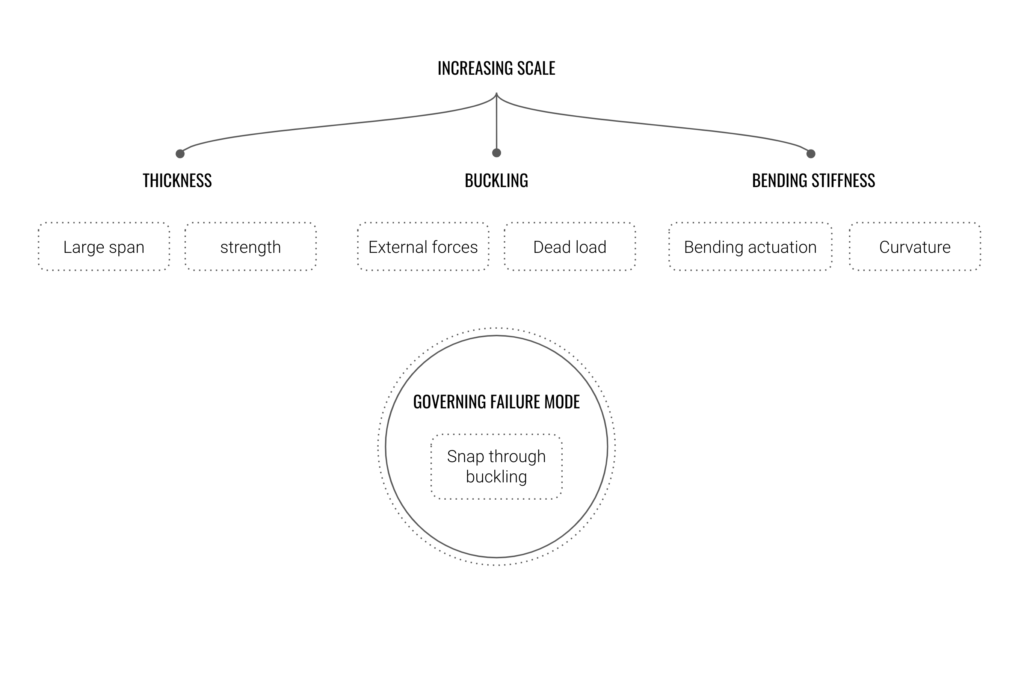
working with active bending comes down to a compromise between member strength and flexibility. Curved members must be slender enough to keep activation stresses low. However, too slender members may be prone to local buckling and may render a too flexible structure.
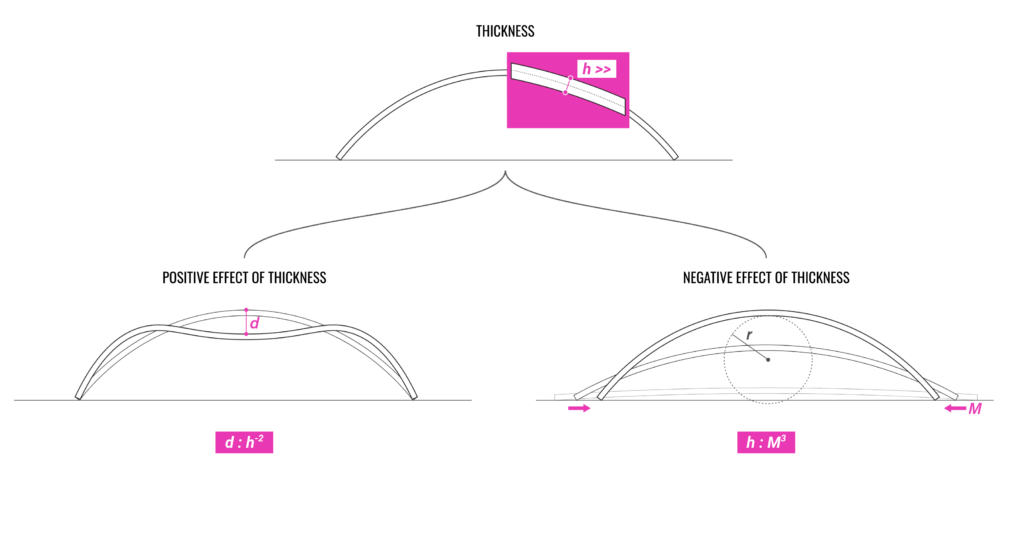
Statement_Investigate the feasibility of the use of plywood within a hybrid bending active system of cable stabilised elements for bending actuation and stiffening to respond to an increased scale and strength of actively bend wood for lightweight enclosed structures
Design parameters
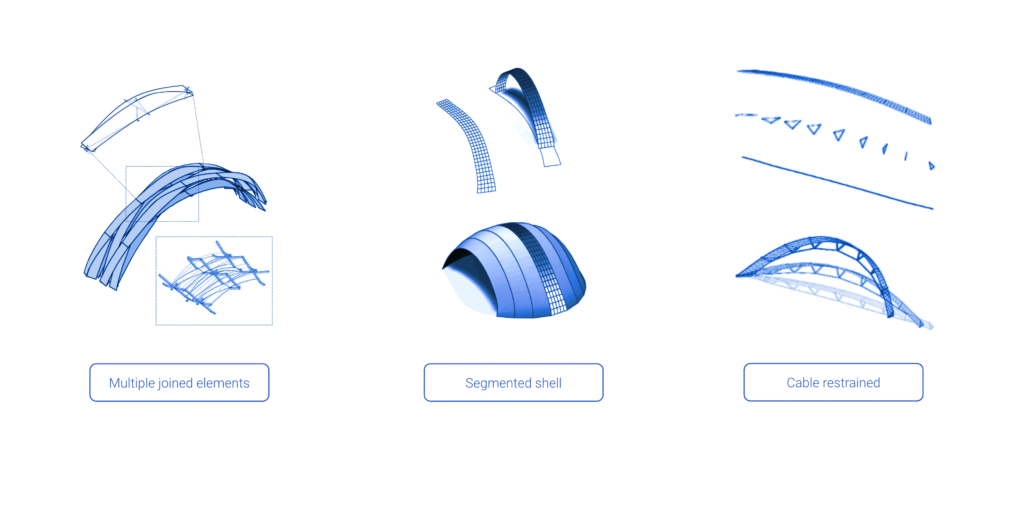
Hybrid system
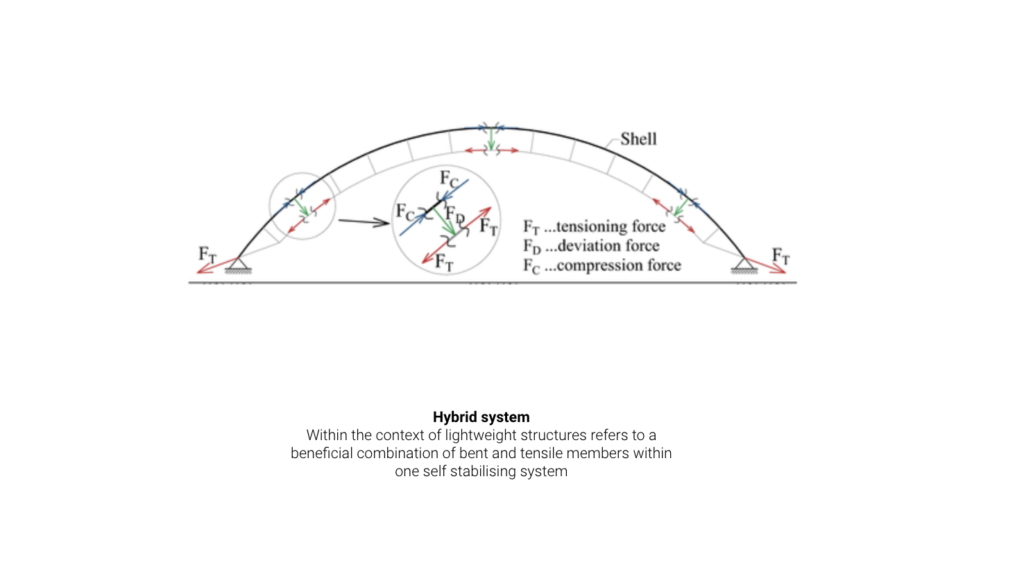
State of art_Hybrid bending active system
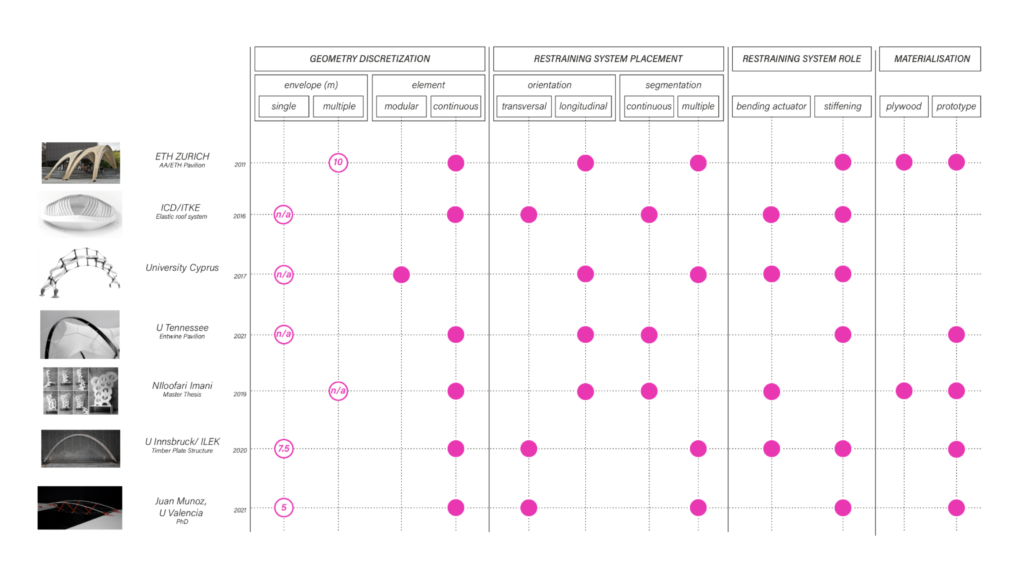
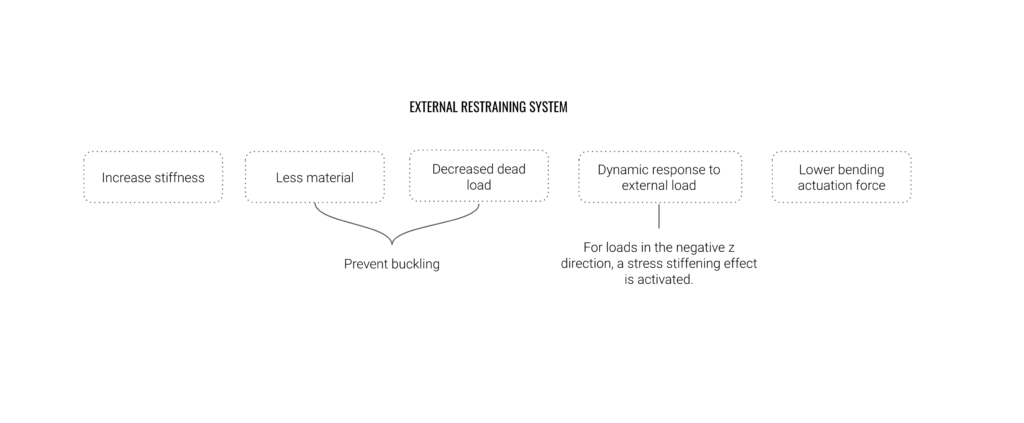
Restraining system_Design parameters
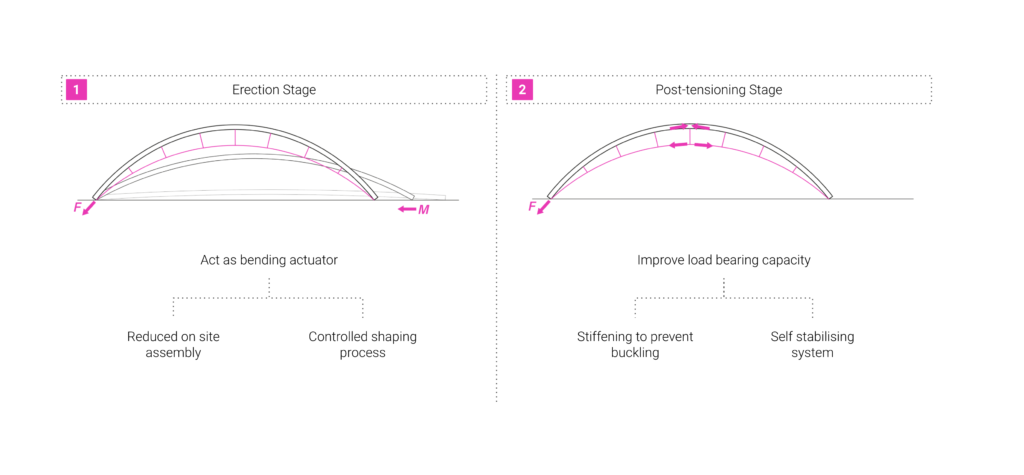
Physical experiments_Restraining system variations
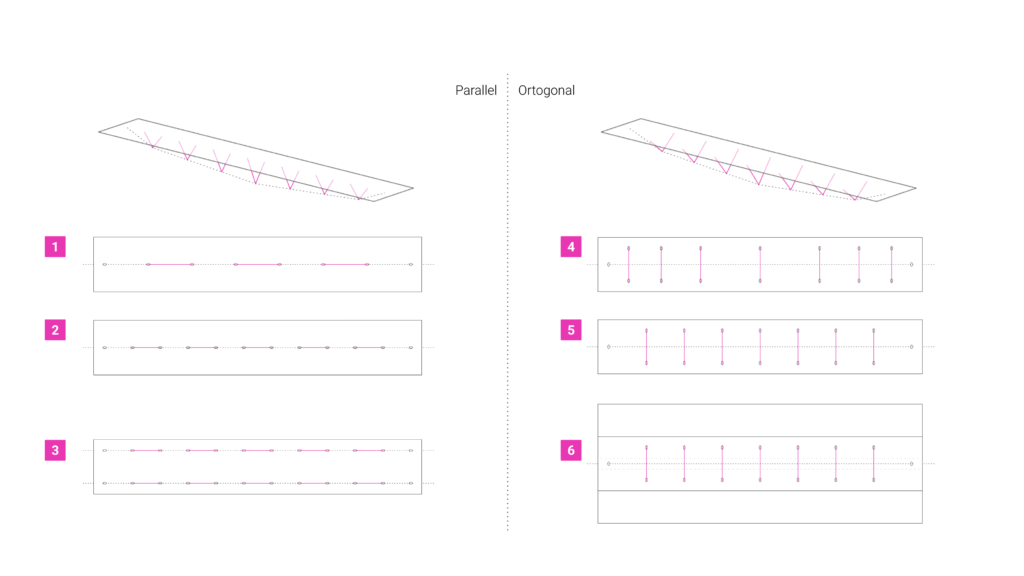
Physical experiments_Overview
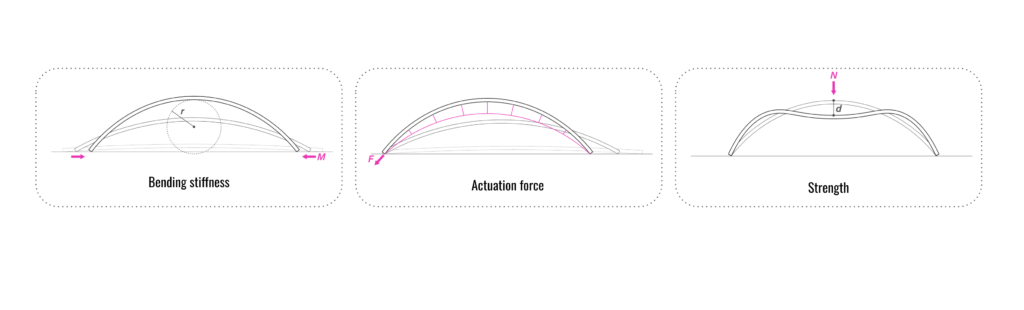
01 Experiment
How does the width to length ratio affect bending stiffness and actuation force?
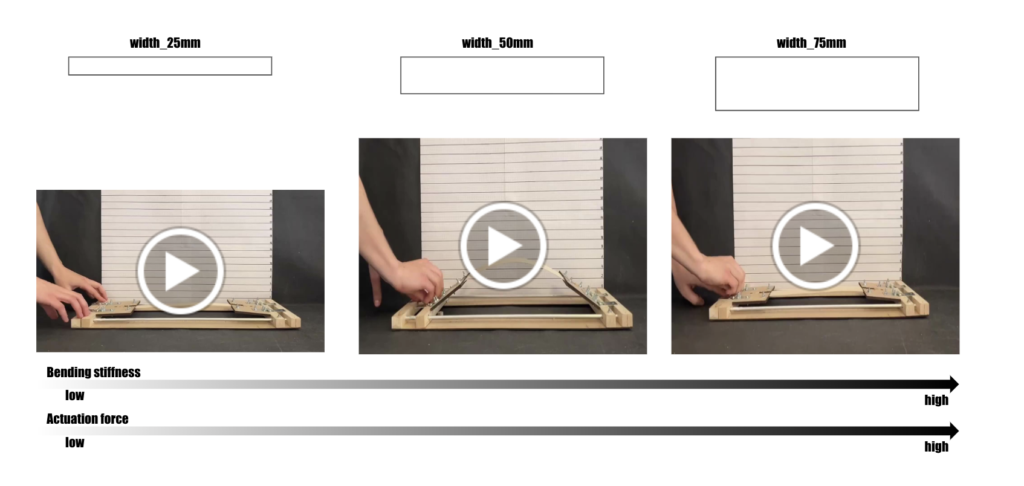
Conclusions
- proposal should take into account the amount of pieces that can be assembled without requiring to much force for the bending
- Take into account optimal width for defined length based on acceptable actuation force
02 Experiment
When keeping the angle constant, how does the width affect the strength?
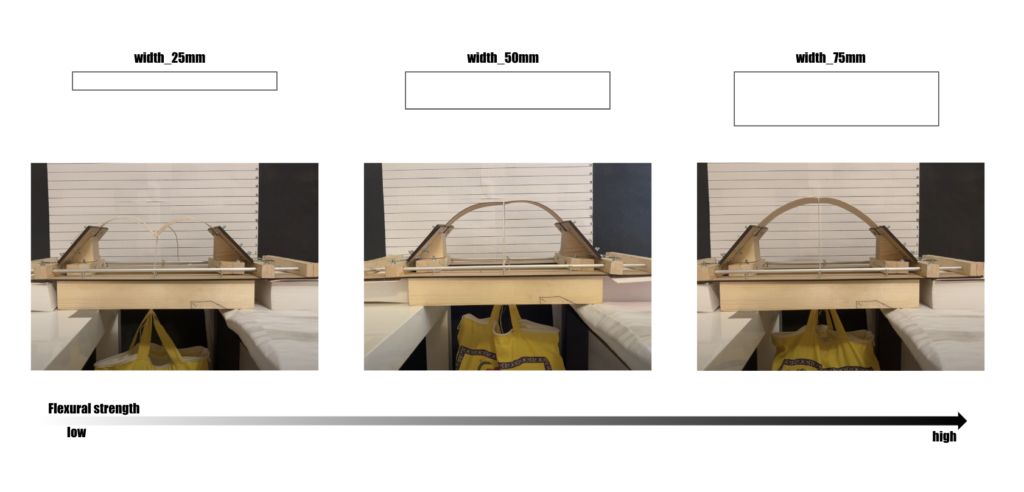
03 Experiment
How does the height to length ratio (f/L) affect the strength of the specimen?
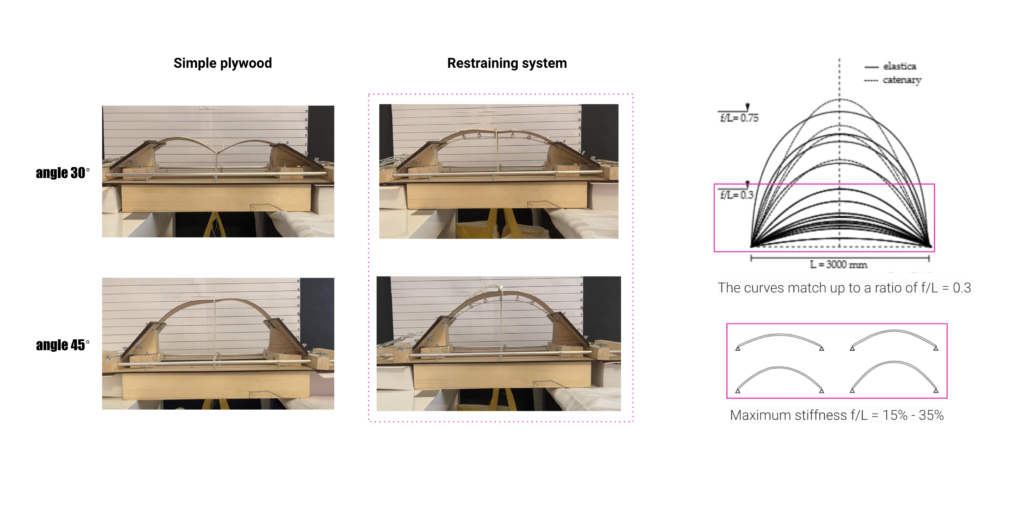
the addition of a restraining system increases the f/L ration within which the actively bend element has exhibits maximum stiffness.
04 Experiment
When keeping the angle and span constant, how does the restraining system affect the strength?
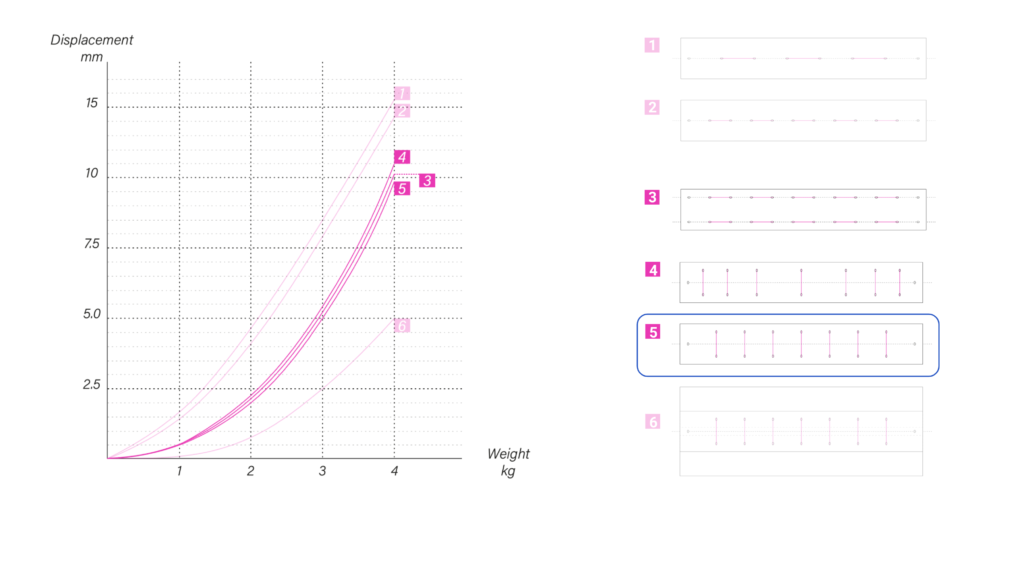
Digital explorations
Best performing physical models
Actuation method
Structural behaviour and analysis
Workflow
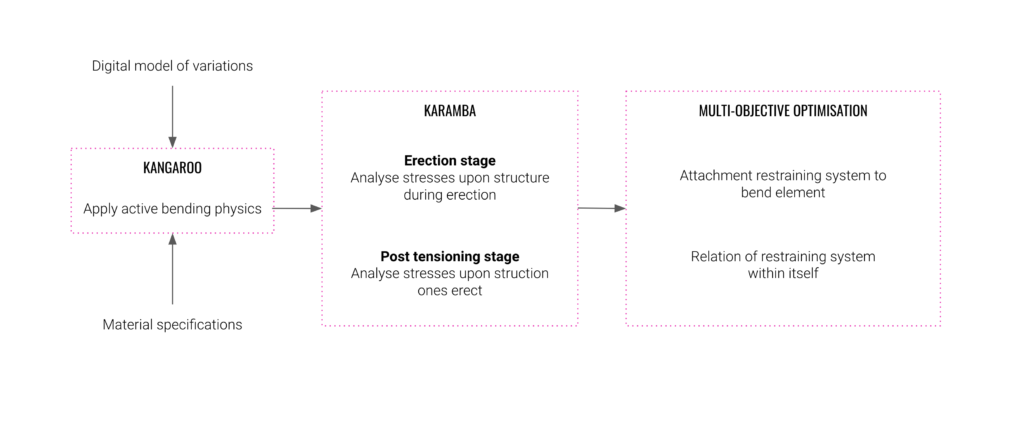
Application_Application parameters
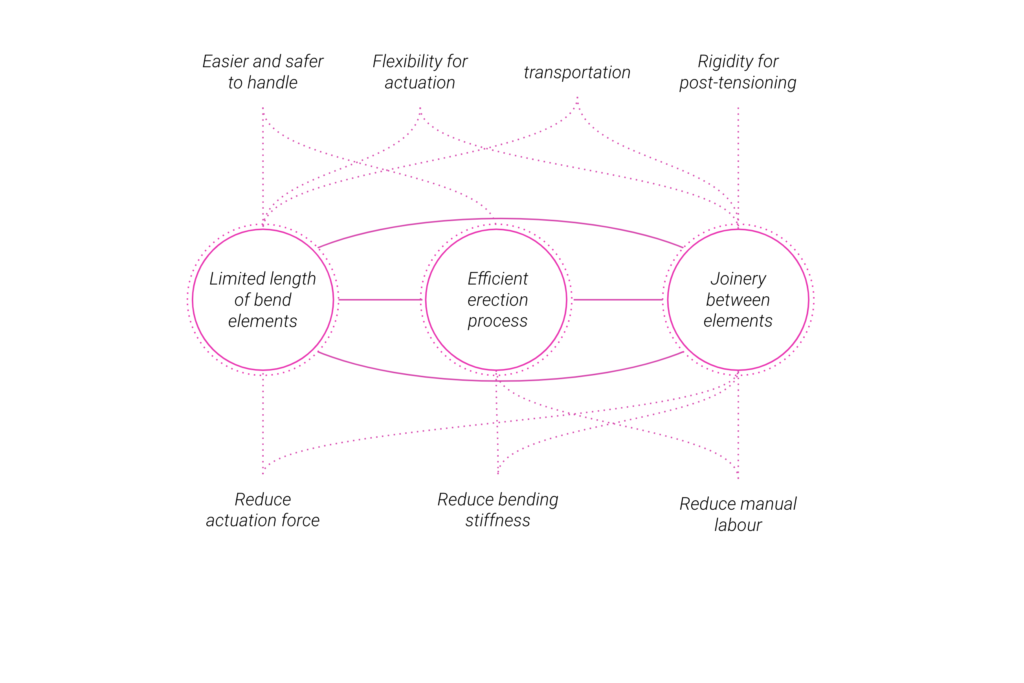
Joints_Multiple elements
Slot joint
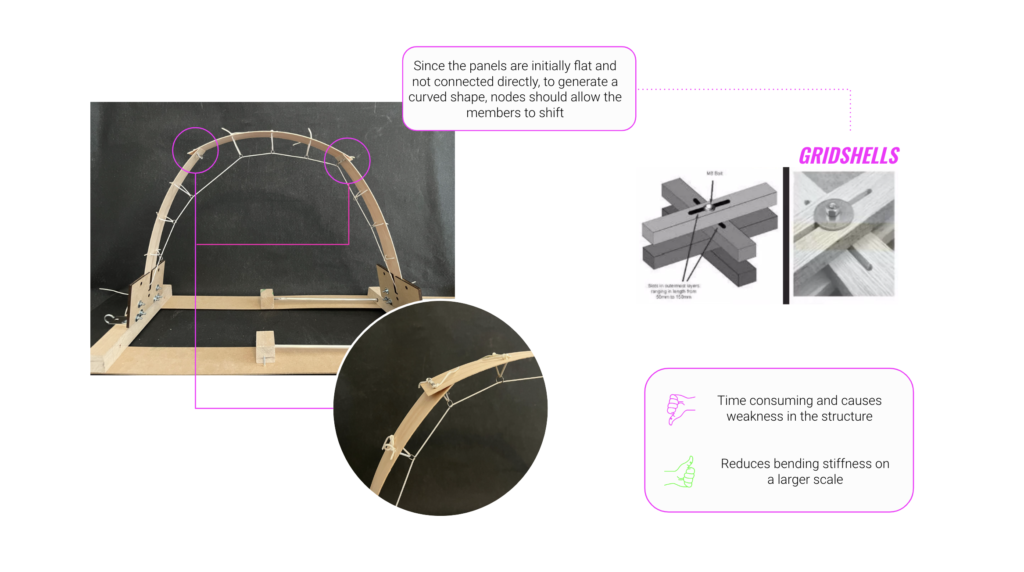
Kerfing
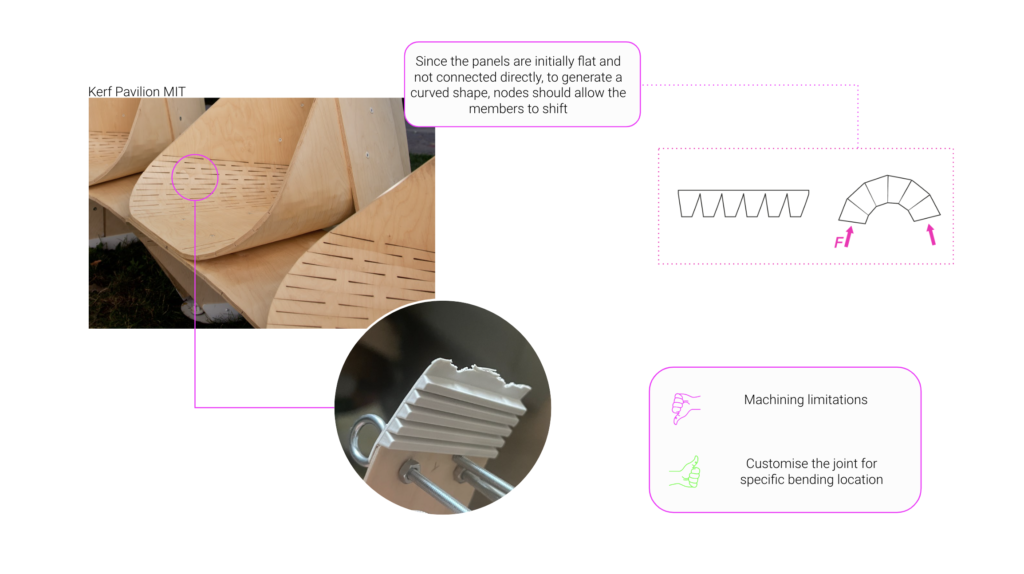
Friction
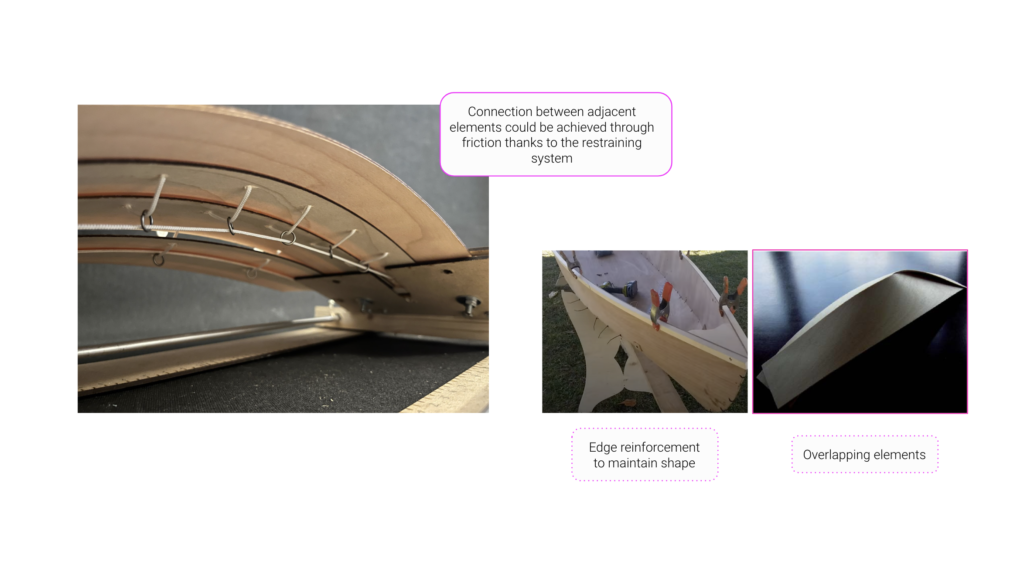
Summary
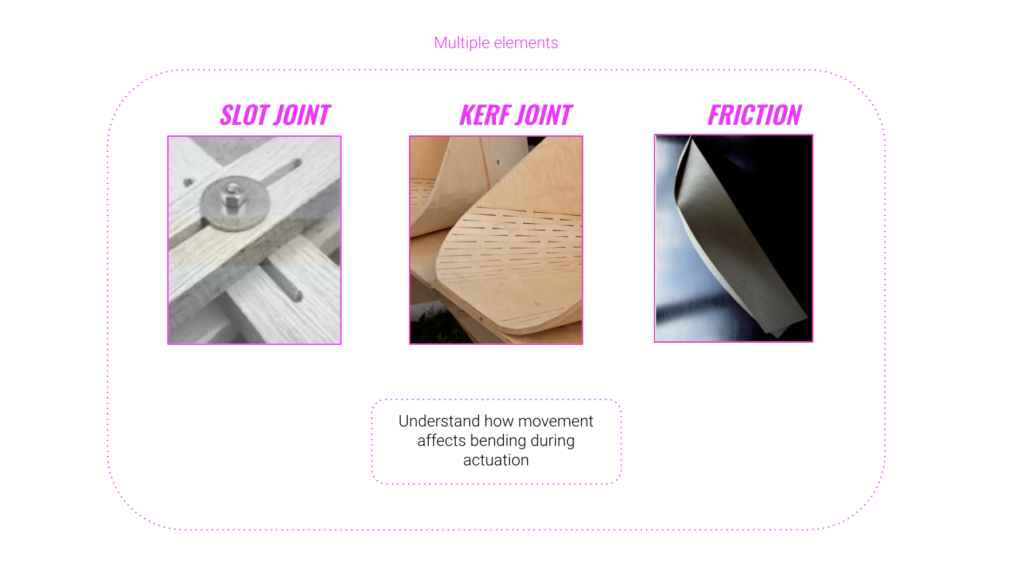
s