A metamorphosis
from textile waste to circular furnishing systems
Fast fashion generates over 92 million tonnes of textile waste per year, contributing to environmental pollution, while the construction industry is facing escalating costs and a massive carbon footprint.
Raising the question of how post-consumer textile waste can be transformed into panels suitable for various interiors without the use of extra binders, replacing common materials?
Neo-Textura creates a solution by upcycling textile waste into no-load-bearing panels in adaptable furnishing systems, addressing sustainability and circularity. Cellulose-rich textile composites fabricated from end-of-life garments bring durability, lightweightness and insulation needed to function effectively as interior elements, eliminating the need of synthetic binders. A dual methodology is employed: material composition research with heat pressed panels, and multiple complex component-based systems. Several elements were compared in a case study room, showing the most feasible designs and configurations. One representative element is fabricated at 1:1 scale, enabling examination of construction detailing, material requirements, and in-situ performance under real-world loading. This prototype also aids in the understanding of the complexity of a multi-company collaboration.
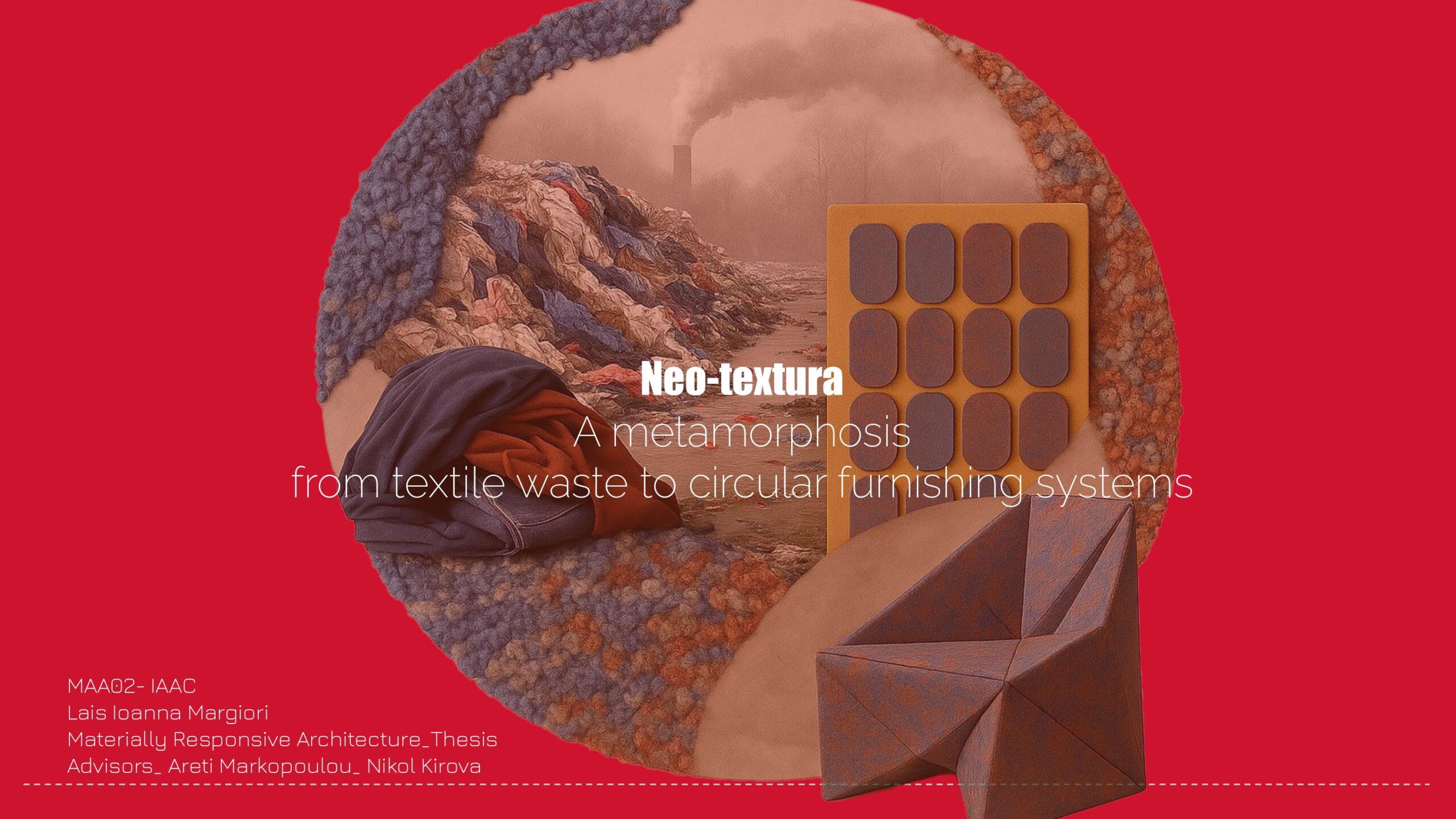
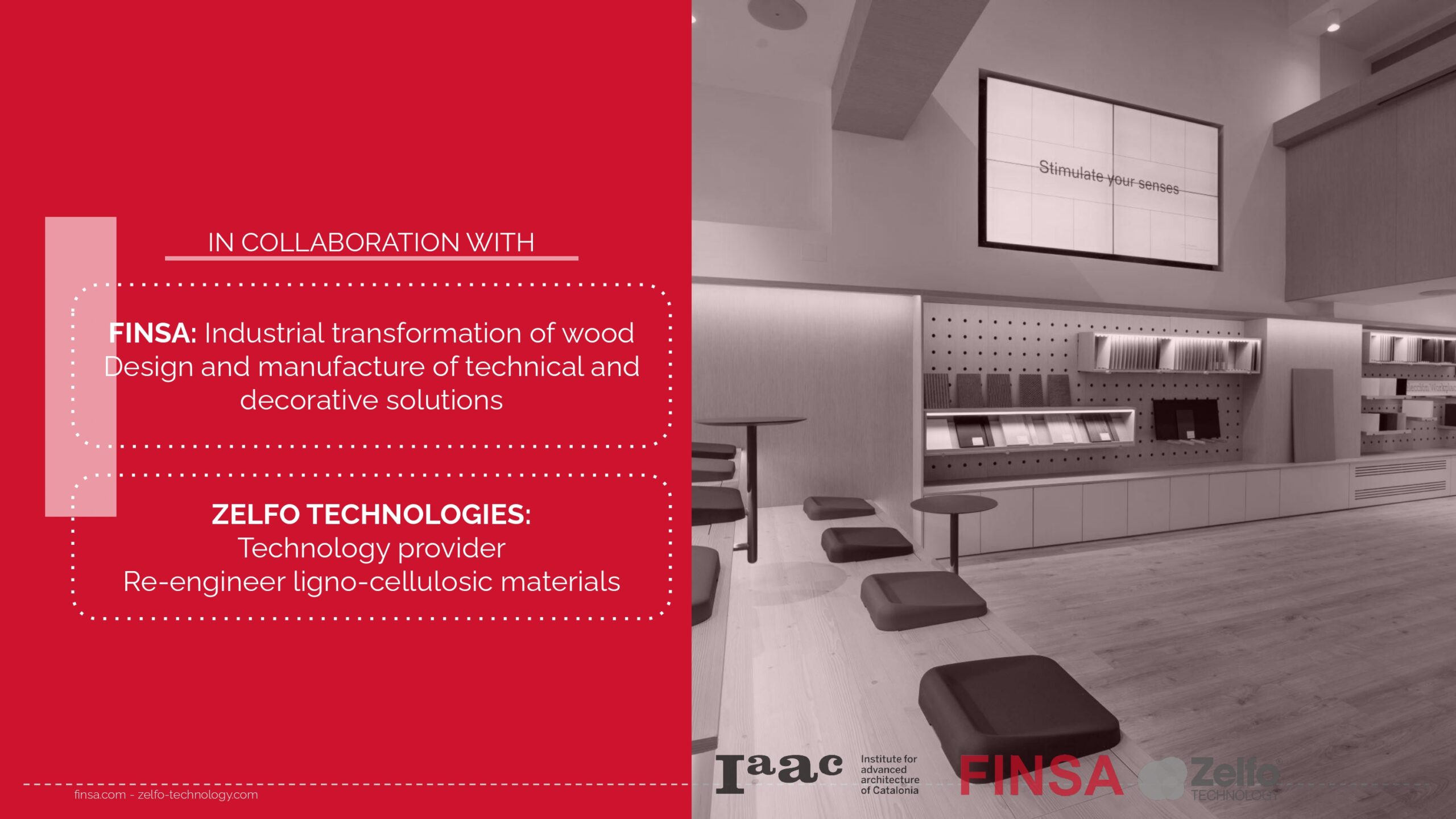
This thesis started as a collaboration between Finsa, a company focusing on industrial transformation of wood and their technology providers, zelfo technology.
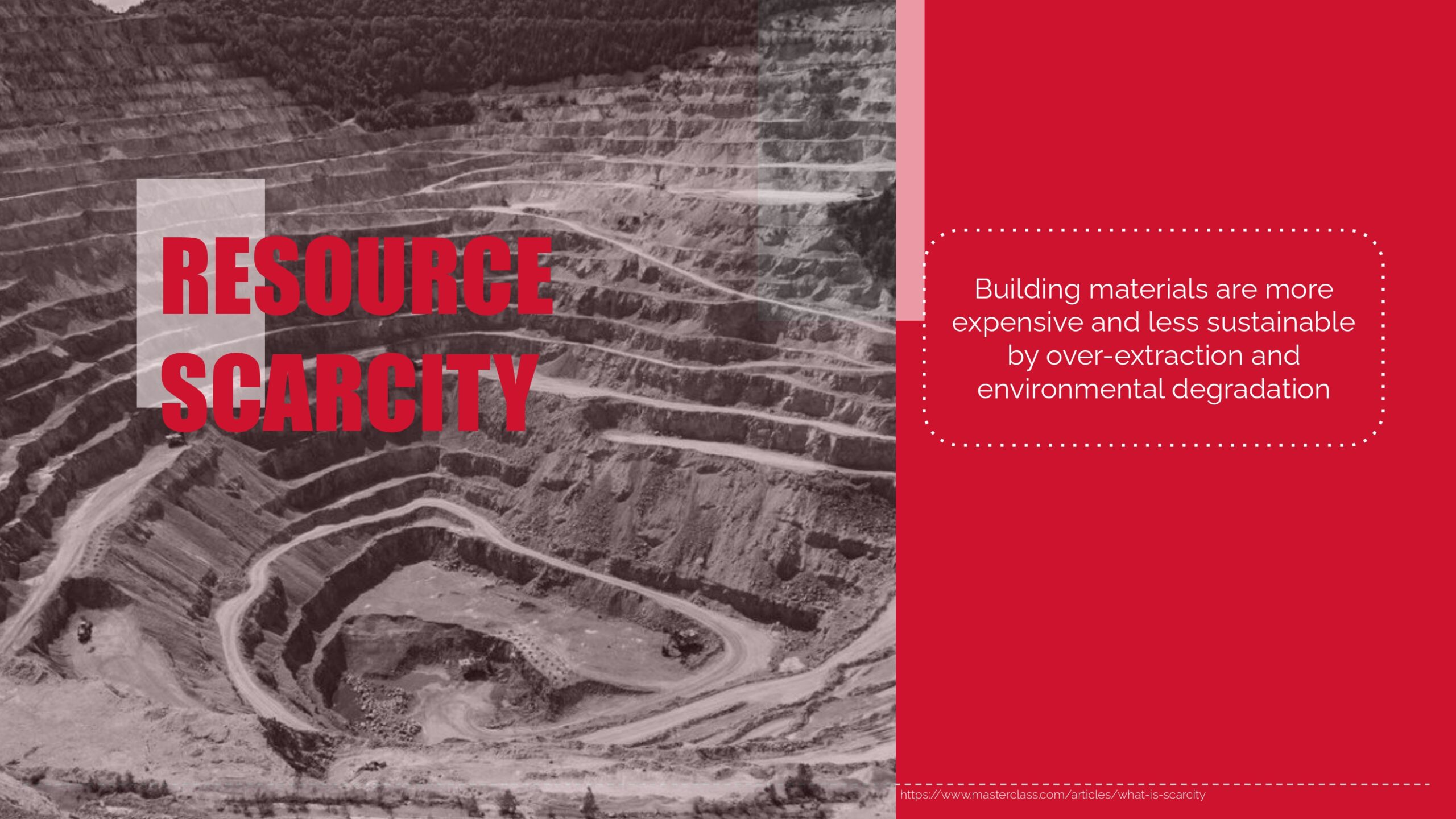
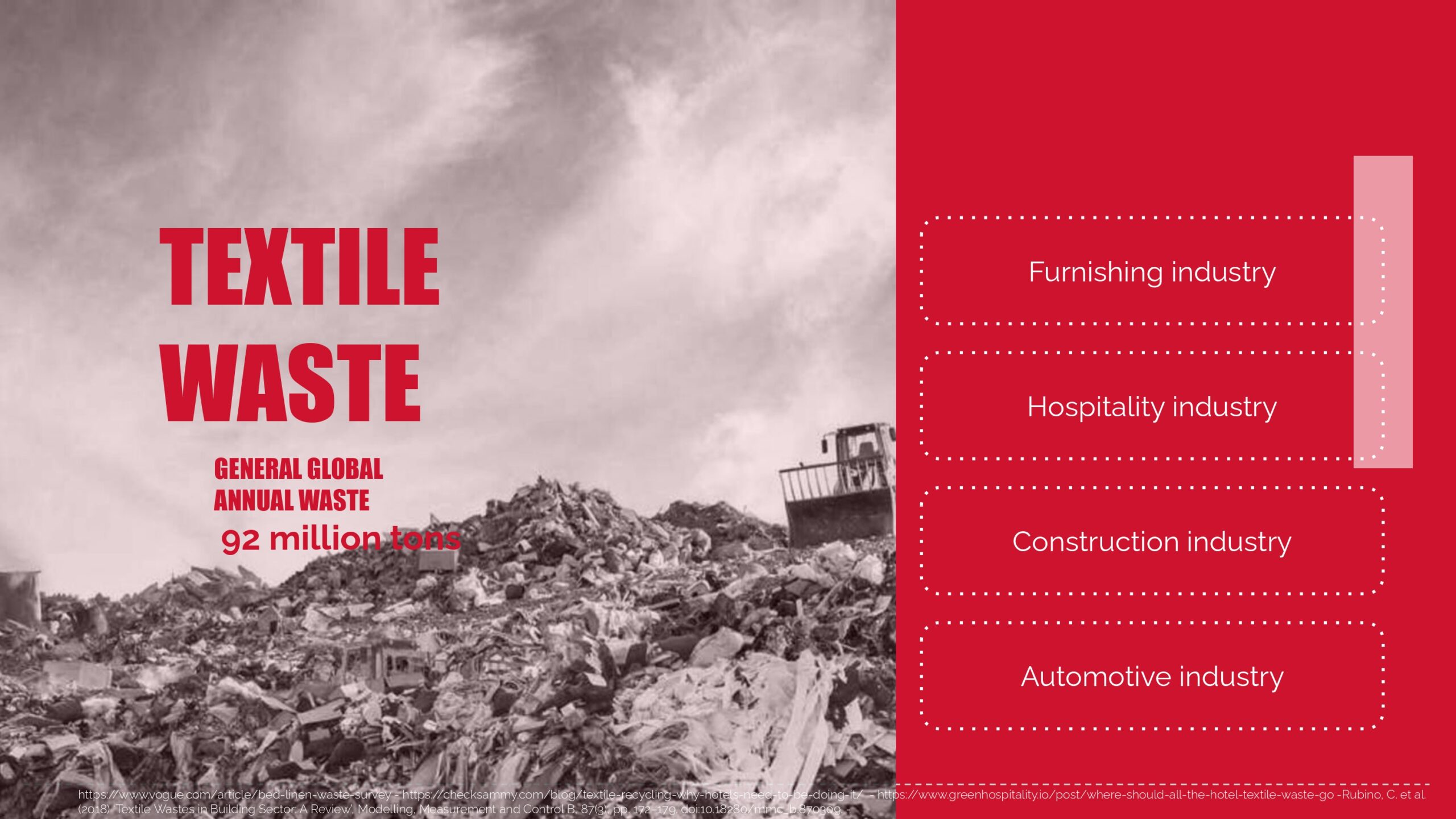
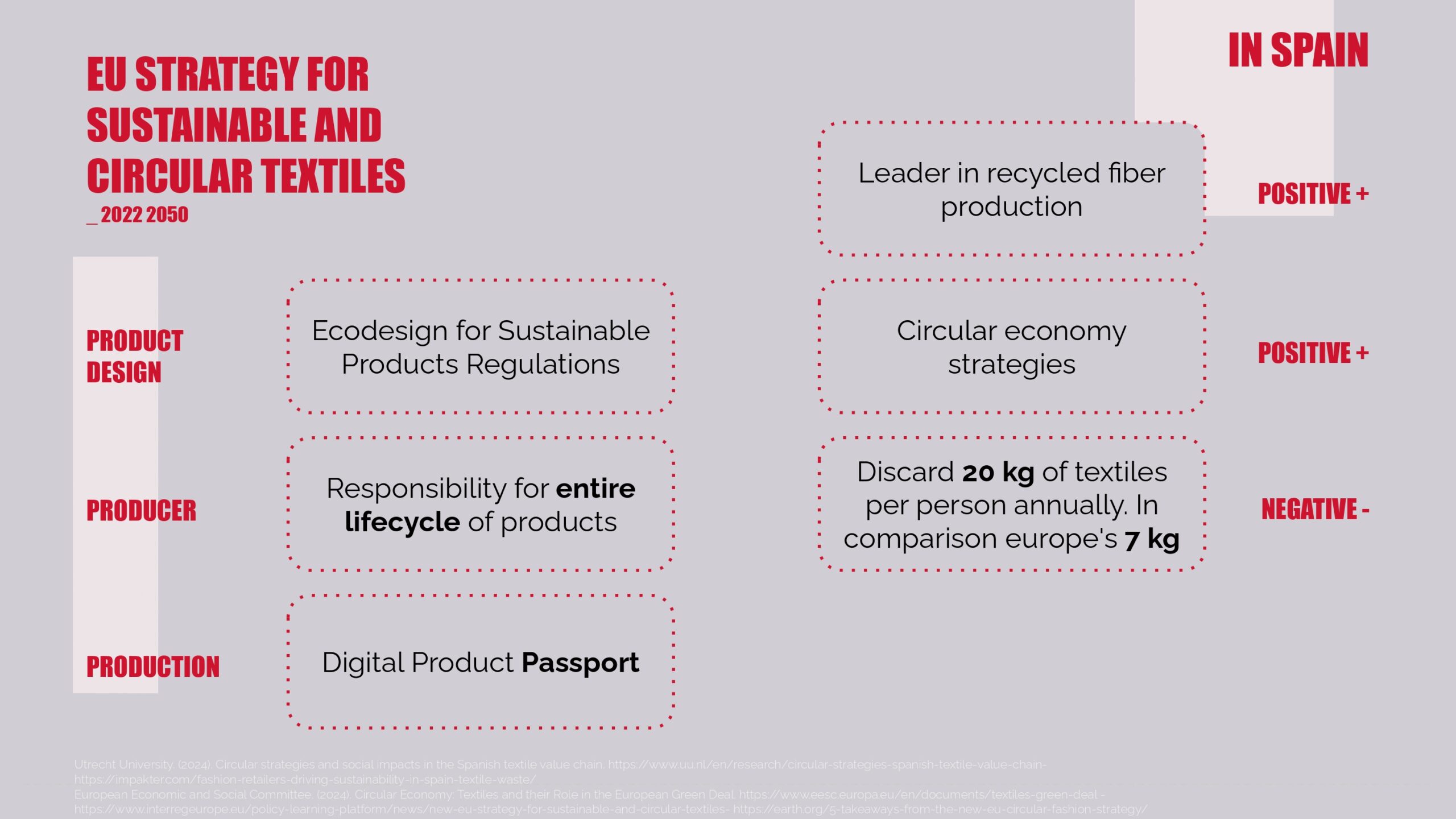
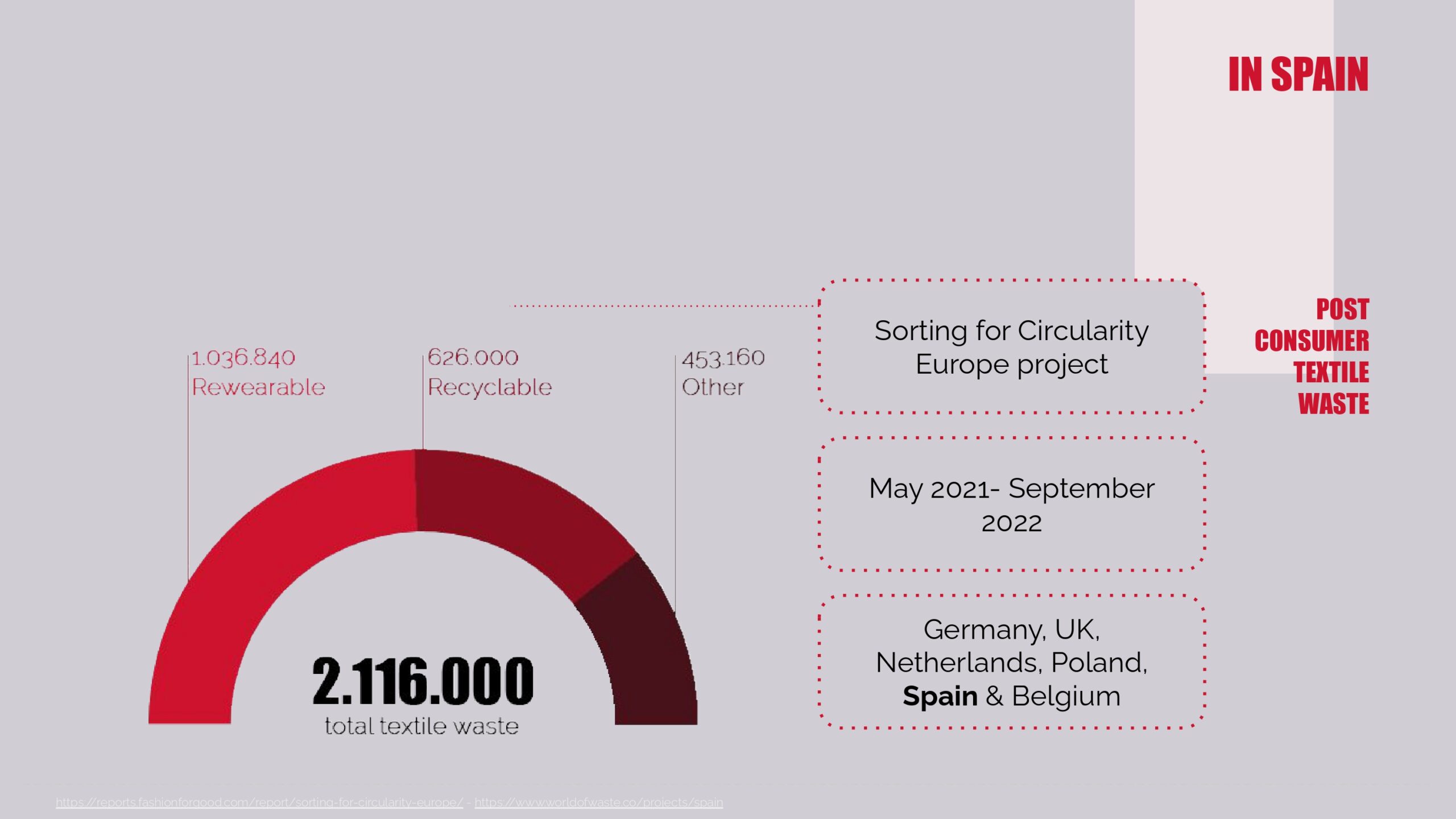
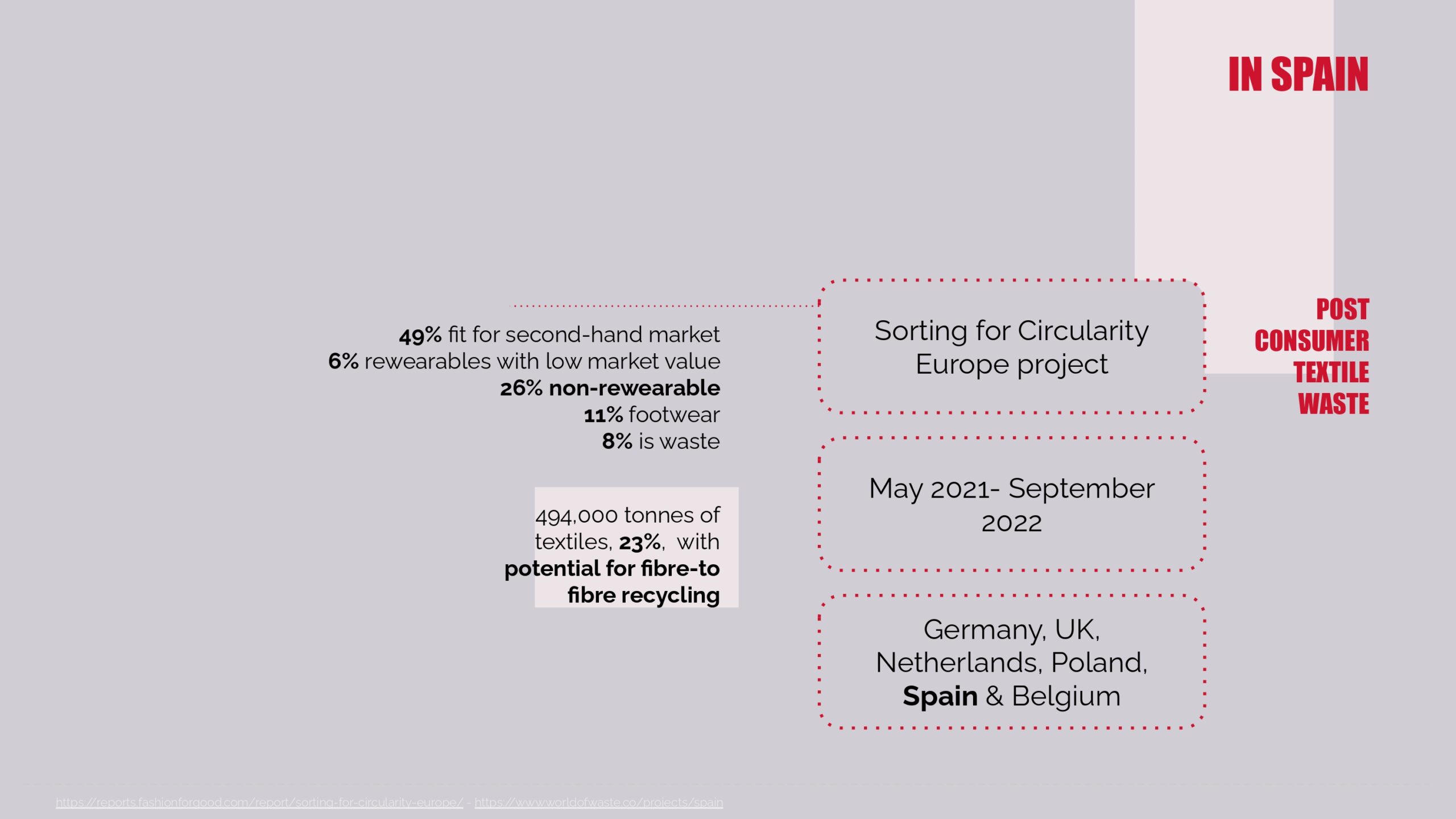
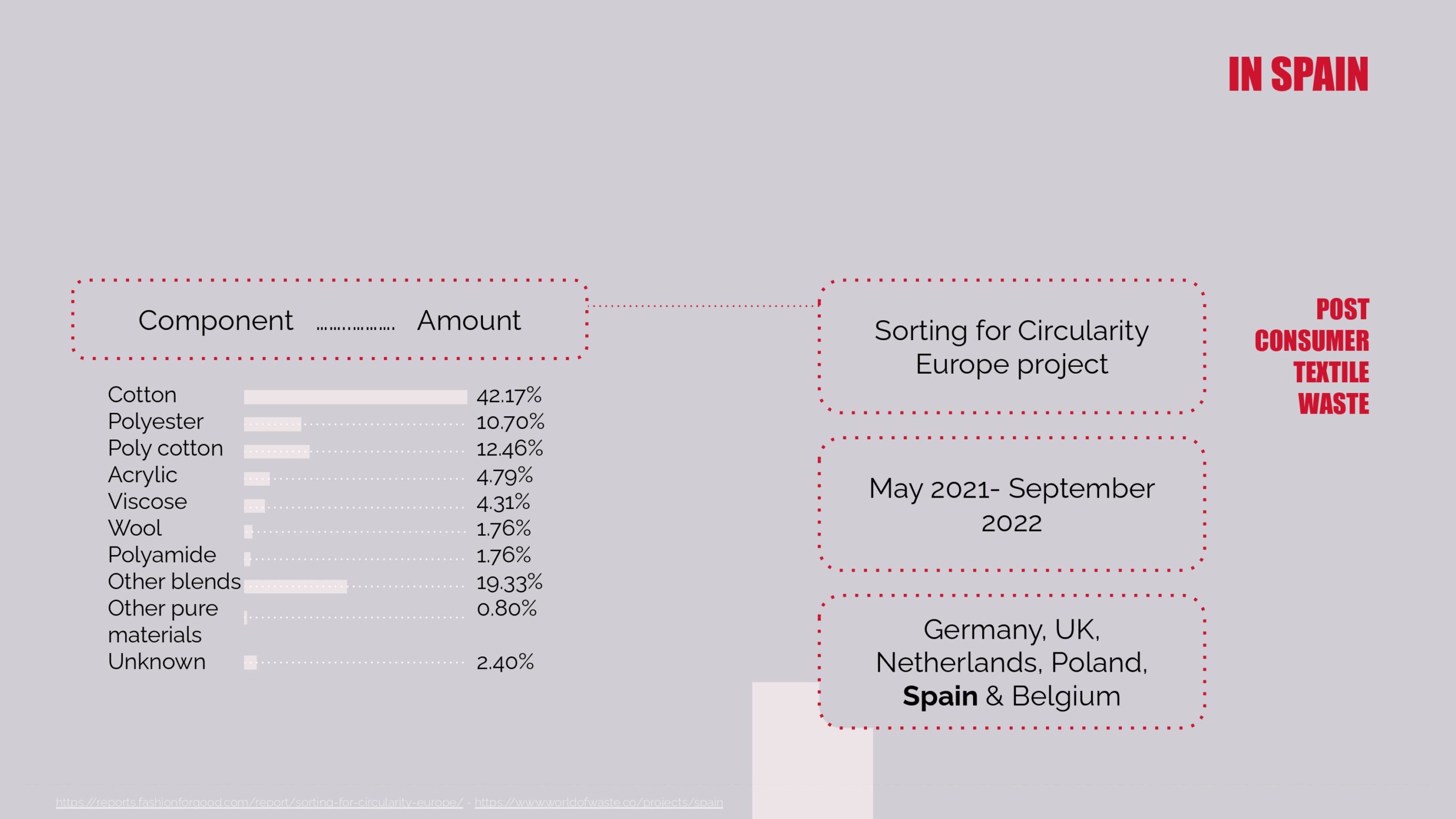
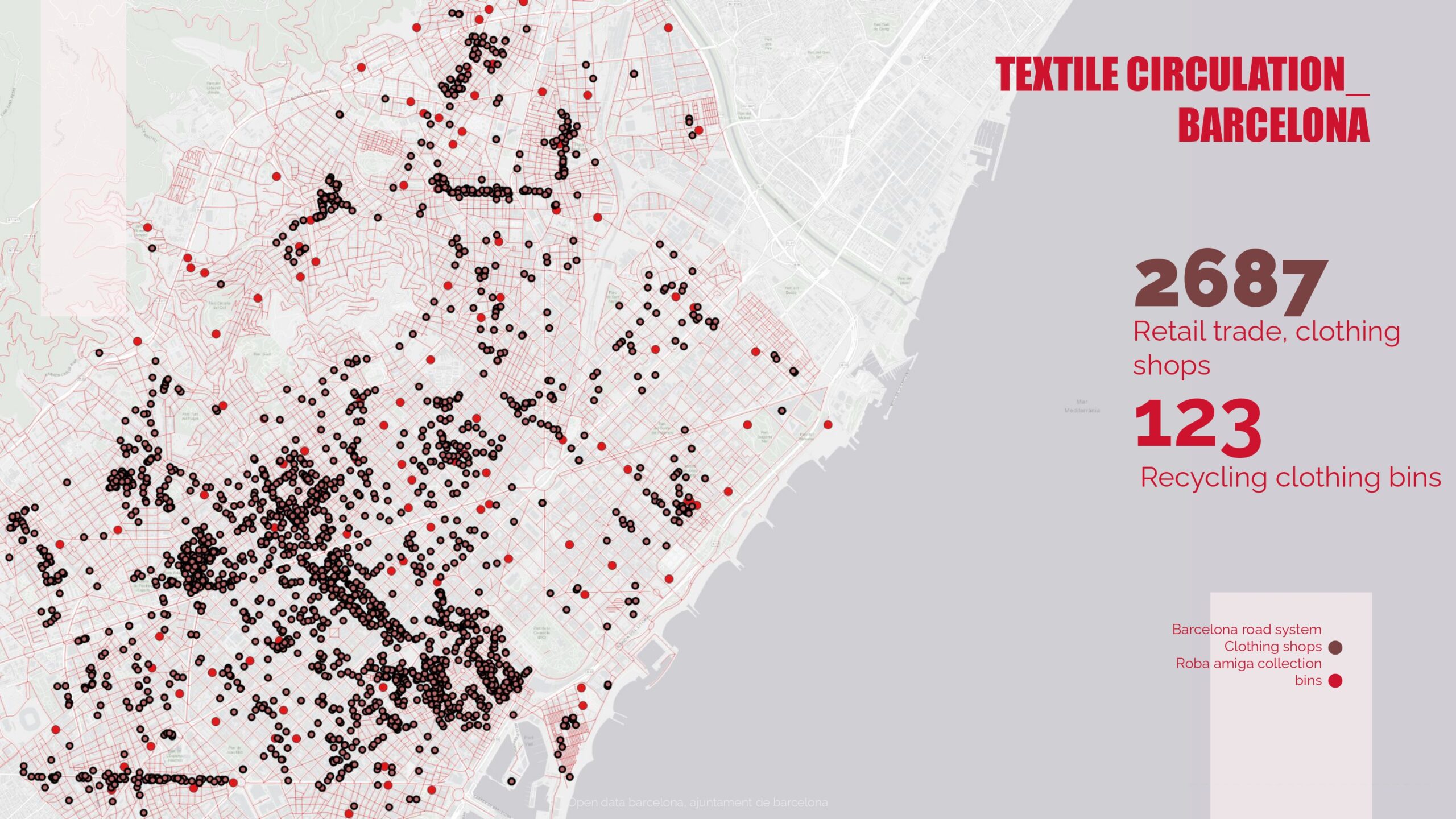
Zooming in Barcelona, the retail shops were mapped and in comparison to the recycling bins from the company that provided the waste clothes, Roba amiga. We were able to see the huge imbalance that Barcelona is trying to bridge, from shops to waste to gathering and reusing.
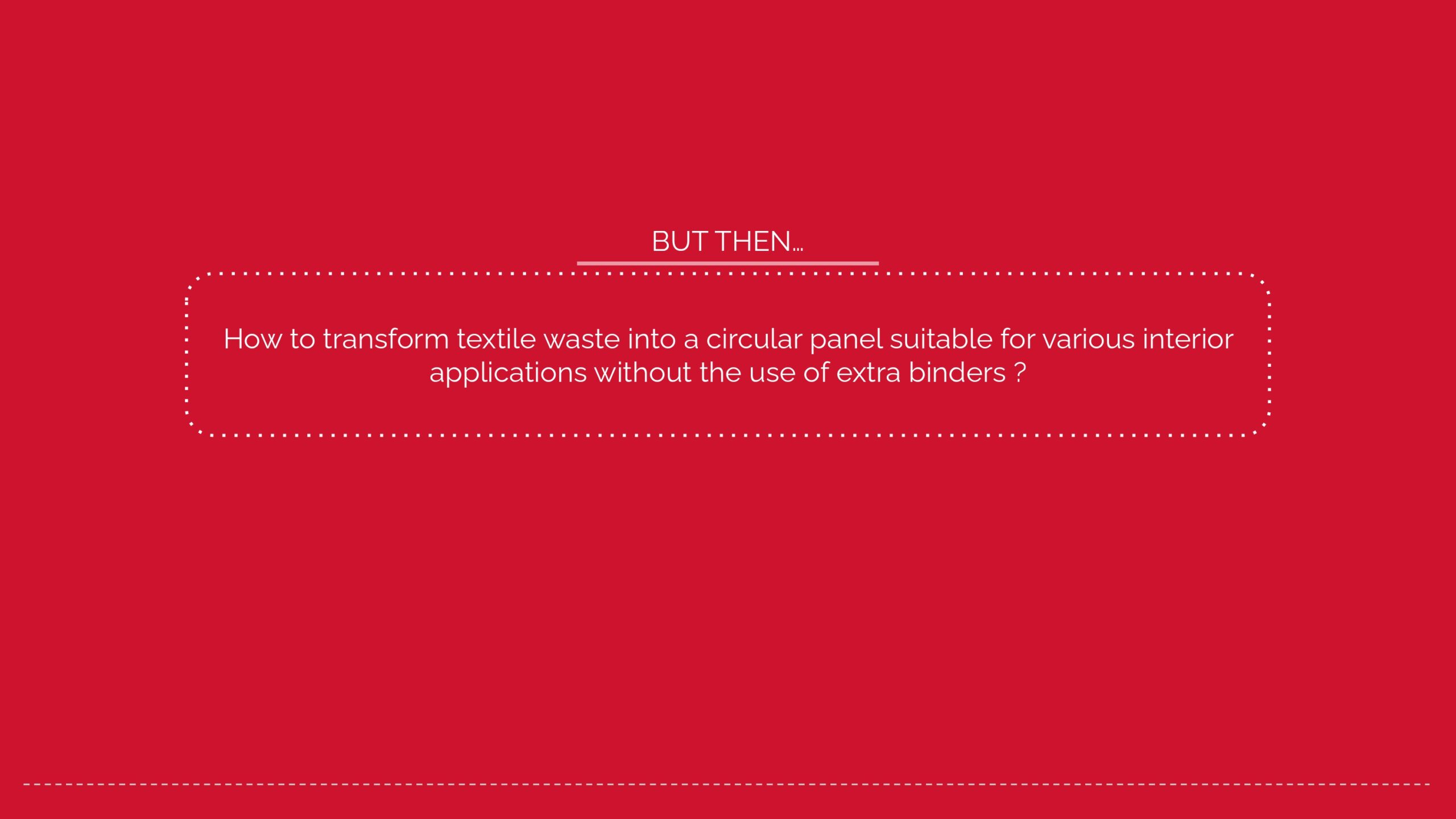
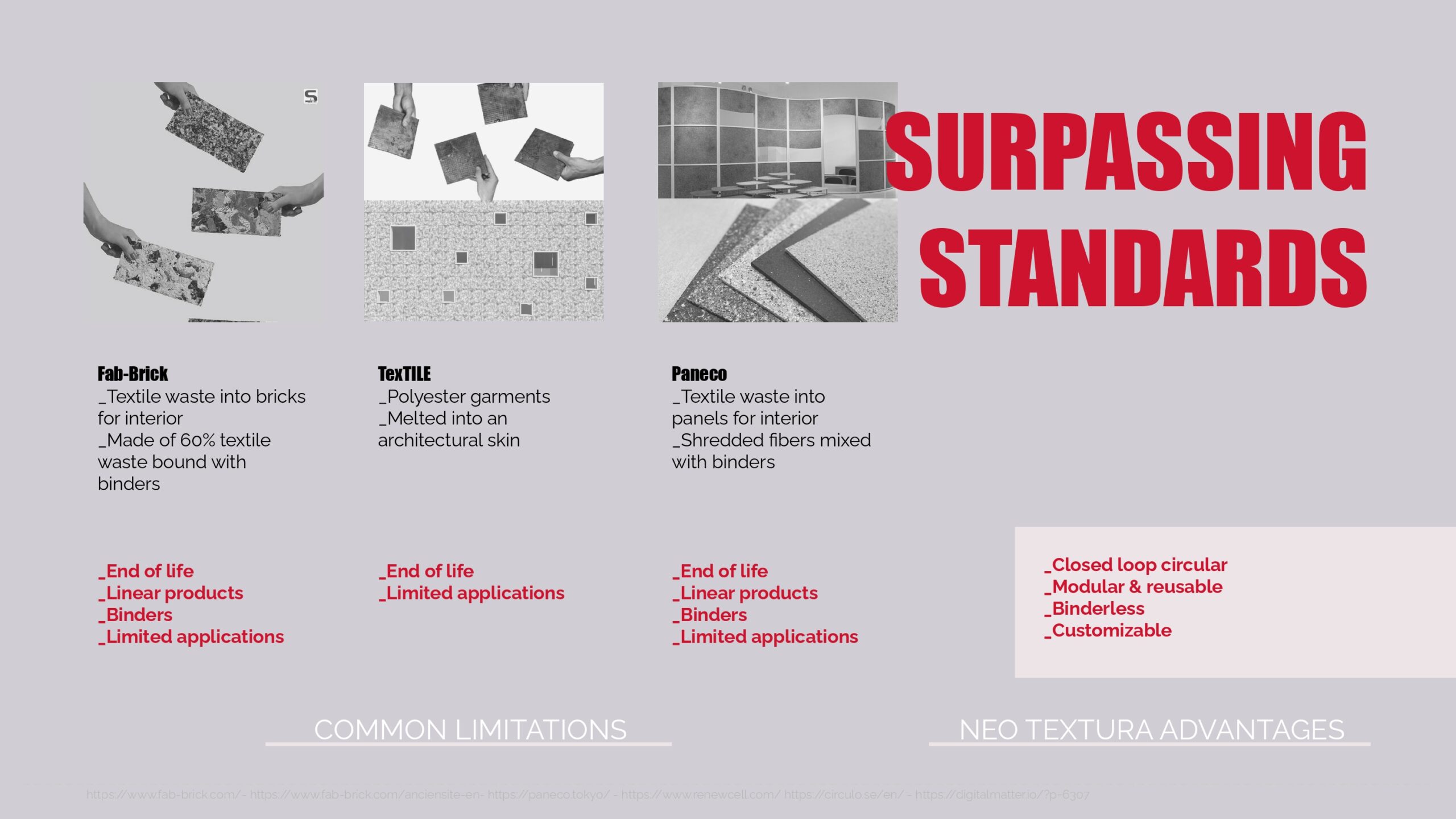
To answer the research question, it was important to find what is already happening, and how to surpass and deal with the problems they face, to surpass the end of life linear products, that contain binders, and the limited applications they possess. Concluding we needed a product circular, without extra binders, as modular and adaptable as it can be.
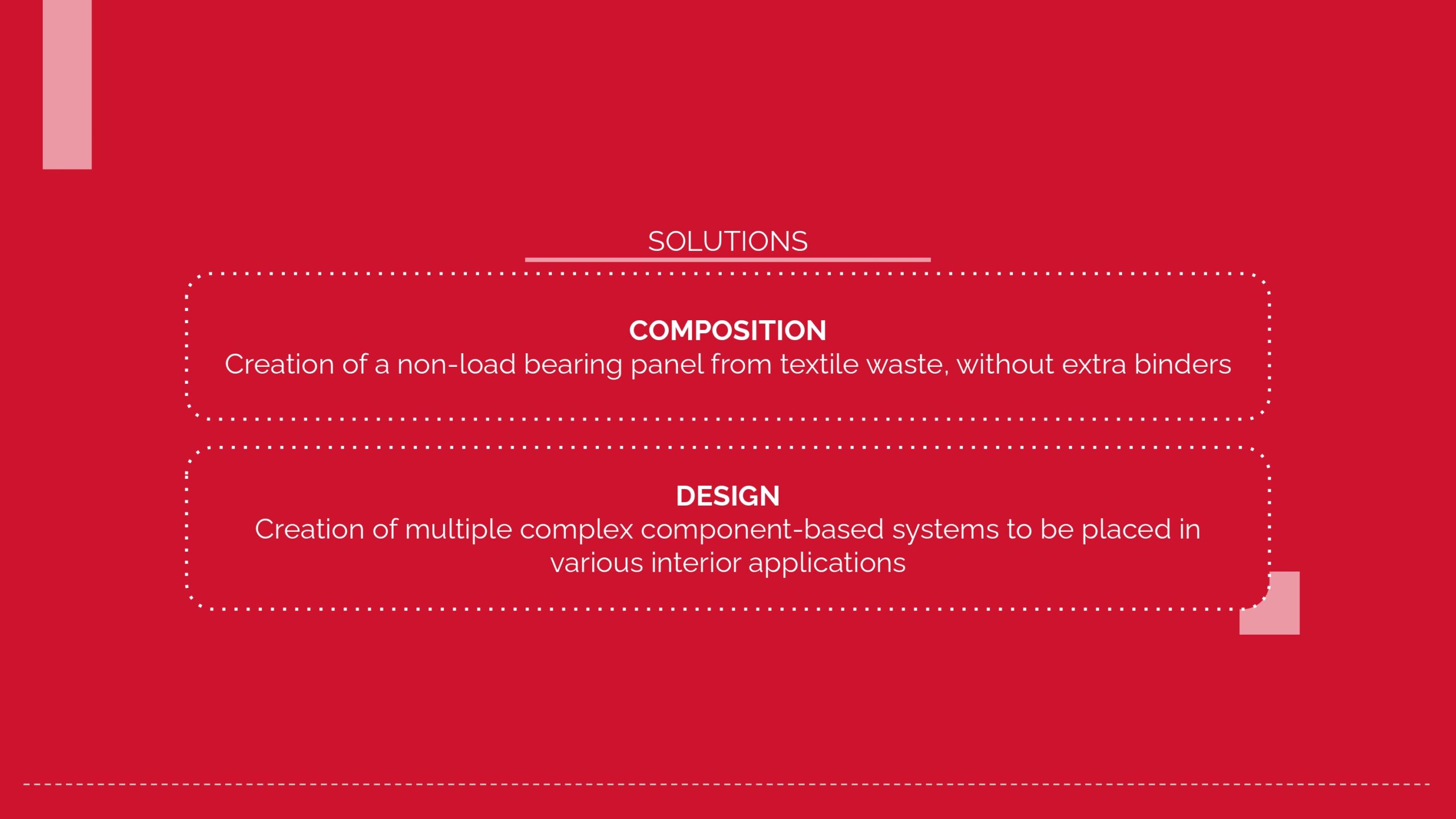
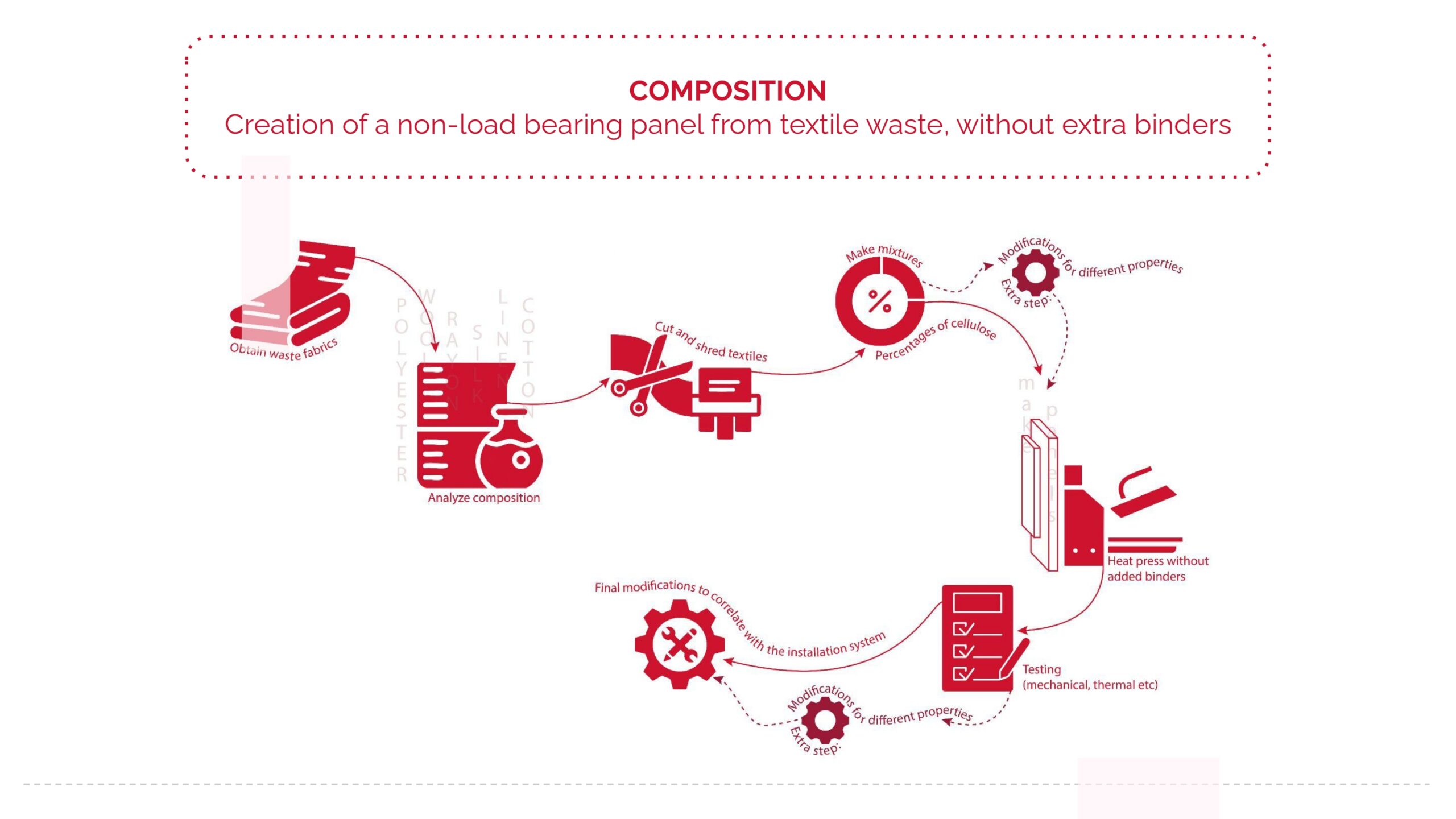
To start off, we are aiming to create a non-load bearing panel from textile waste, without extra binders, through a step by step process of obtaining the waste, analysing, shredding, creating the desired compositions, heat pressing and modifying for the desired system.
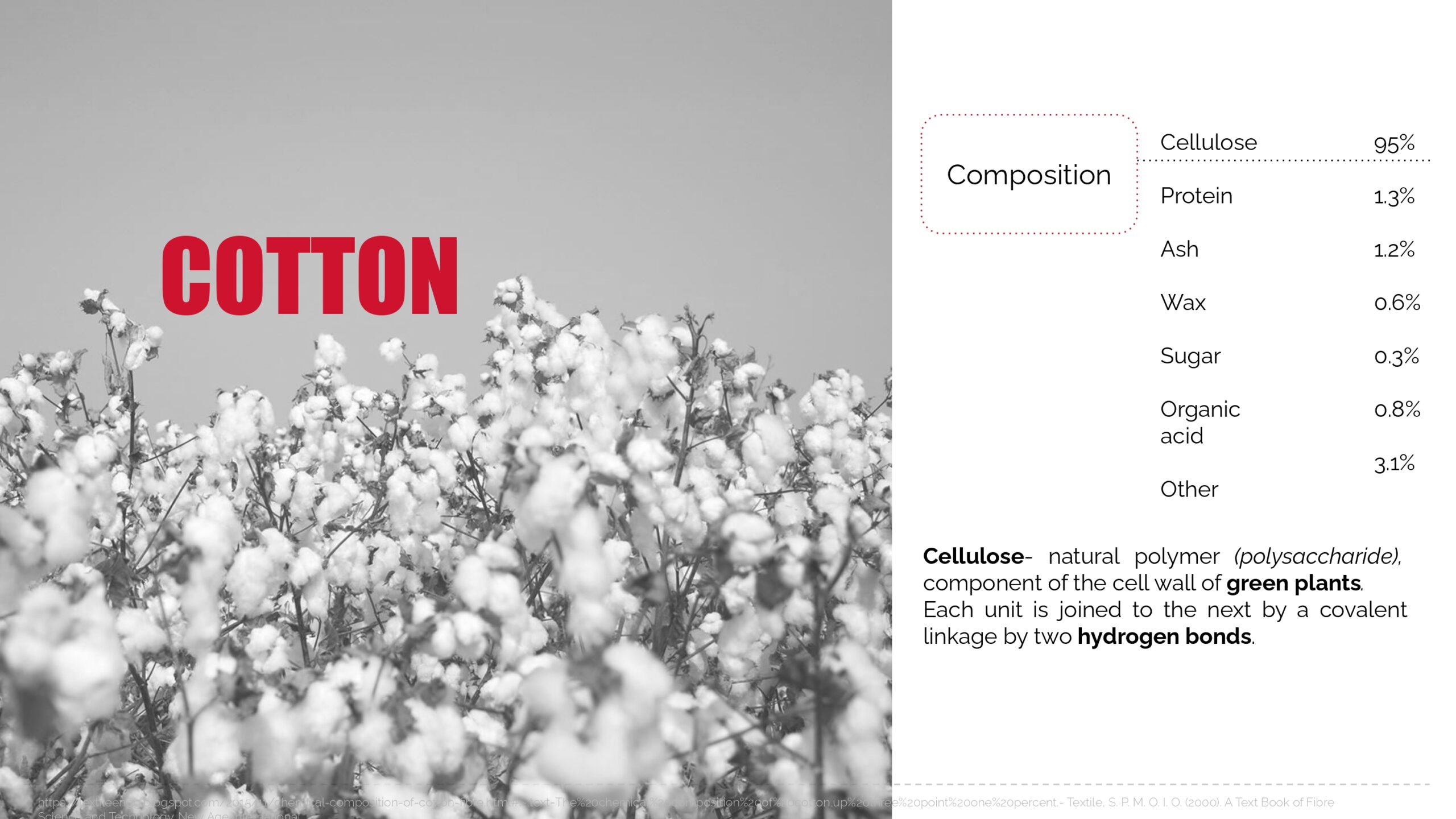
Mostly in these stages of the thesis we focused on cotton, a material in abundance with the highest cellulose percentages, meaning that heat and pressure activate cellulose own hydroxyl chemistry resulting in the self binding properties we are targeting.
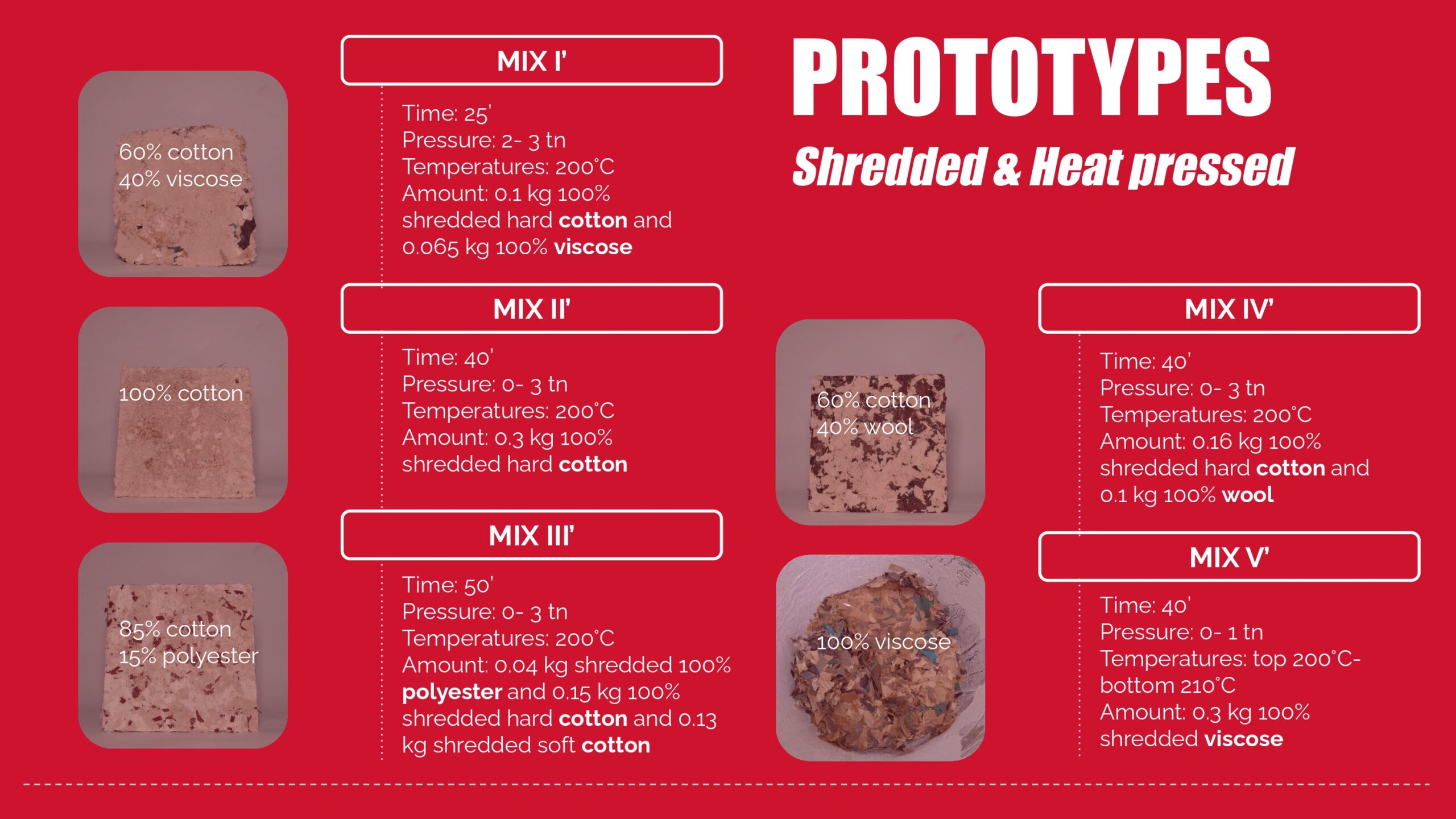
The tests were initiated by shredding and heat pressing a variety of compositions, with different times, pressures and amounts. As 100% cotton, or cotton with viscose or polyester and wool.
Fabrication steps at IaaC.
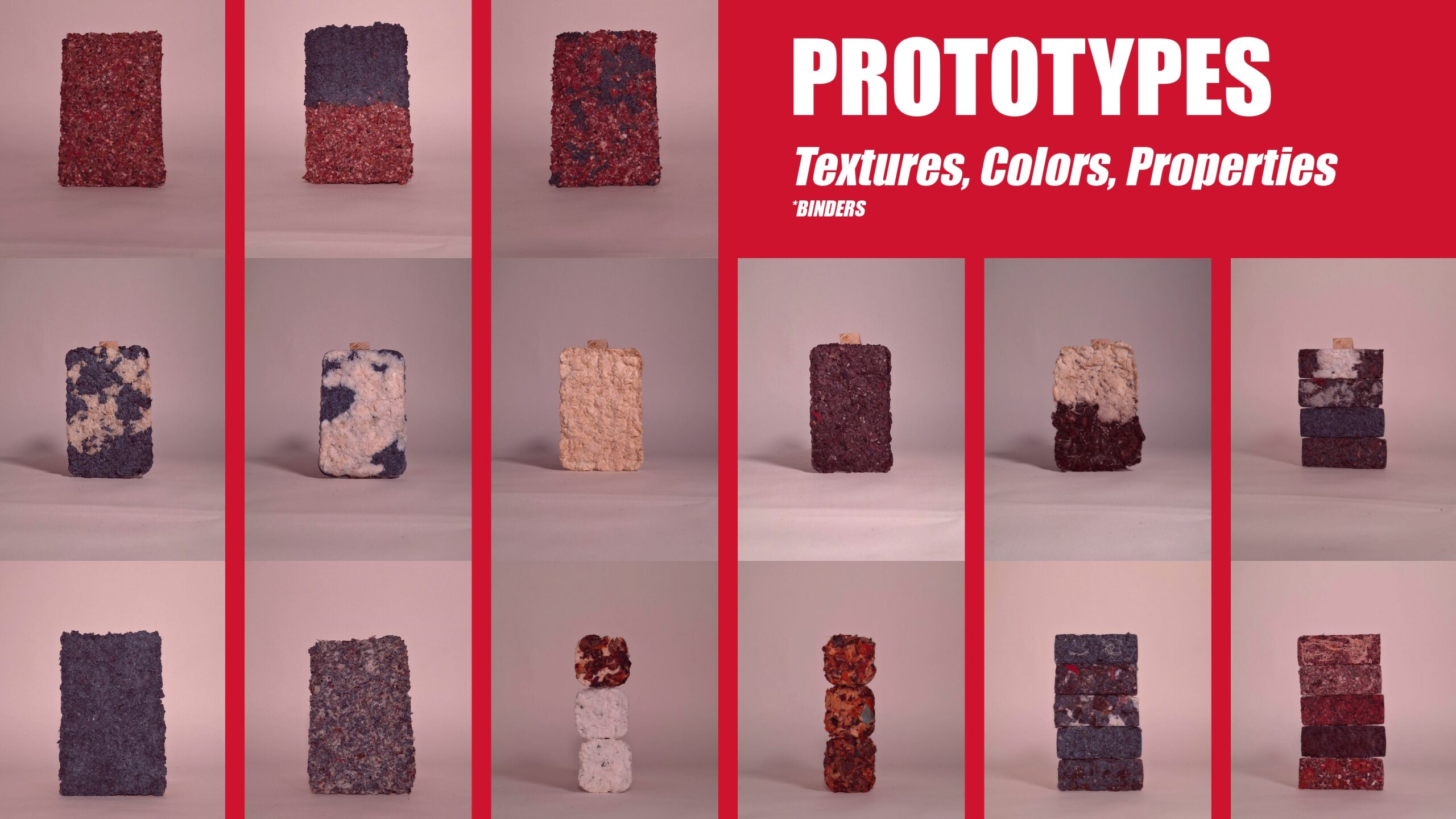
And another type of prototypes to see the textures, colors and the layerings we could achieve, using many types of materials, fabrication methods and compositions.
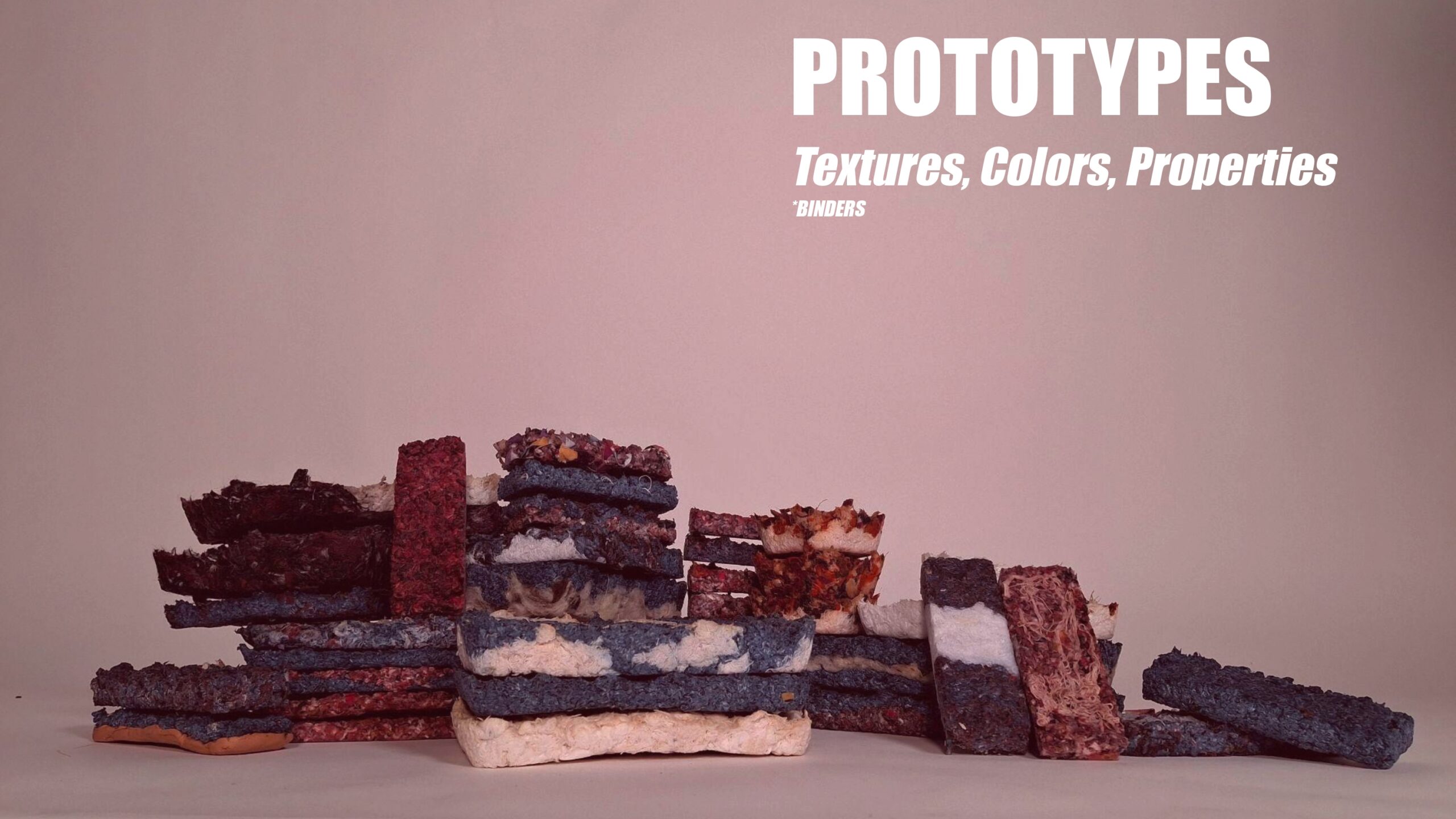
The fabrication steps, of obtaining cutting mixing and creating the prototypes.
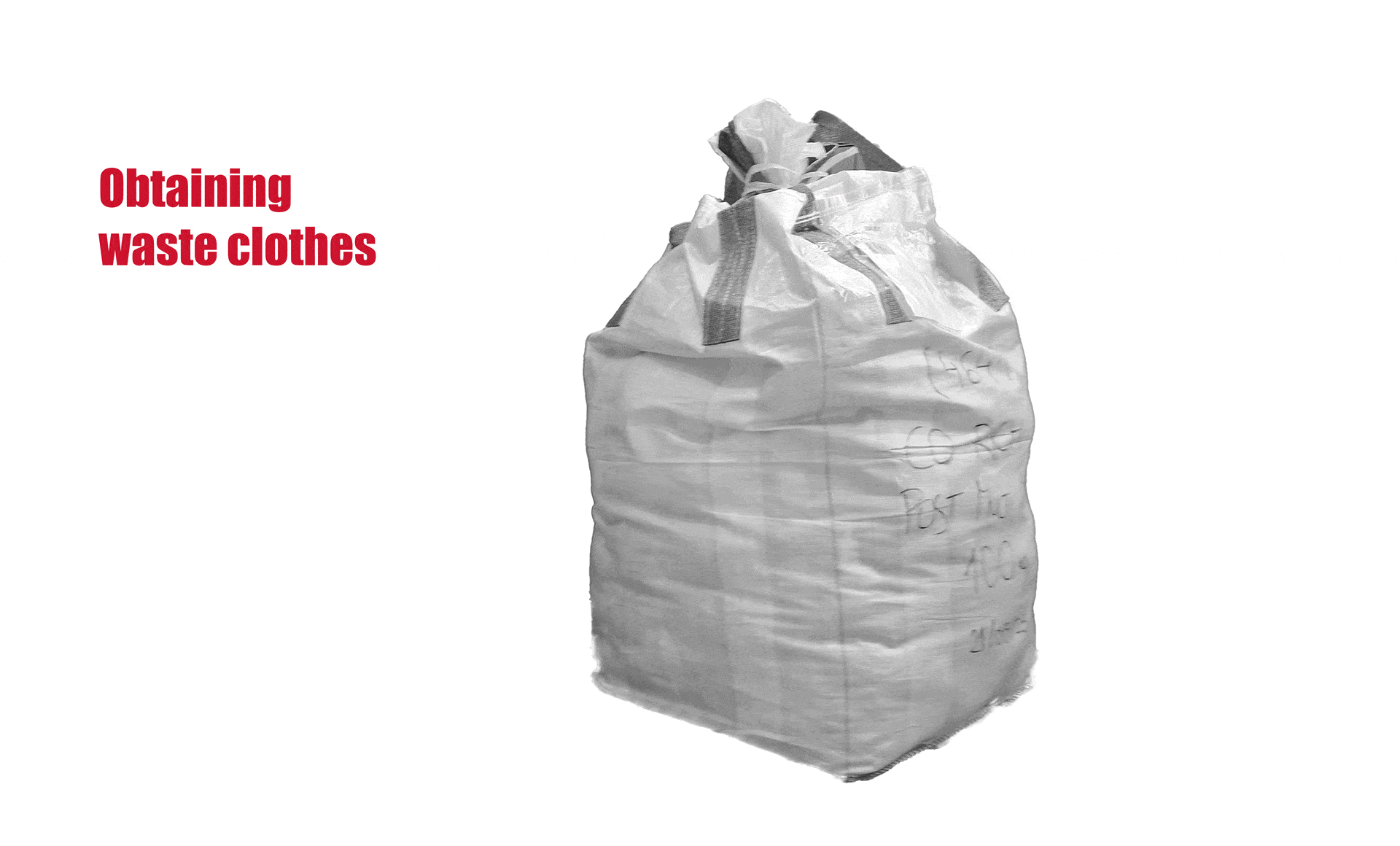
Finally, we continue with the industrial panels that zelfo technologies fabricated. They were able to use the cellulose based composites and their self binding properties to convert fibers to moldable materials.
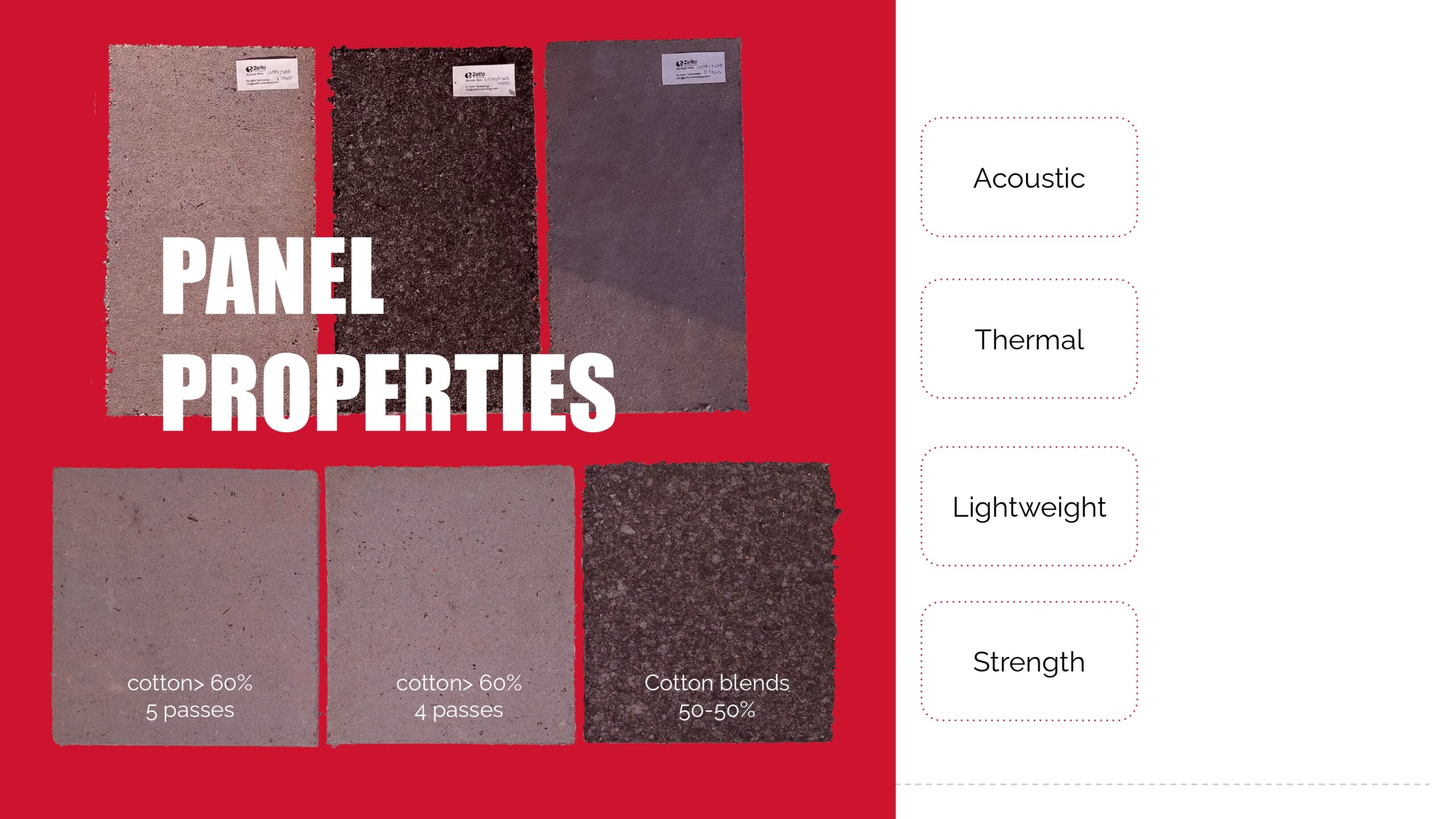
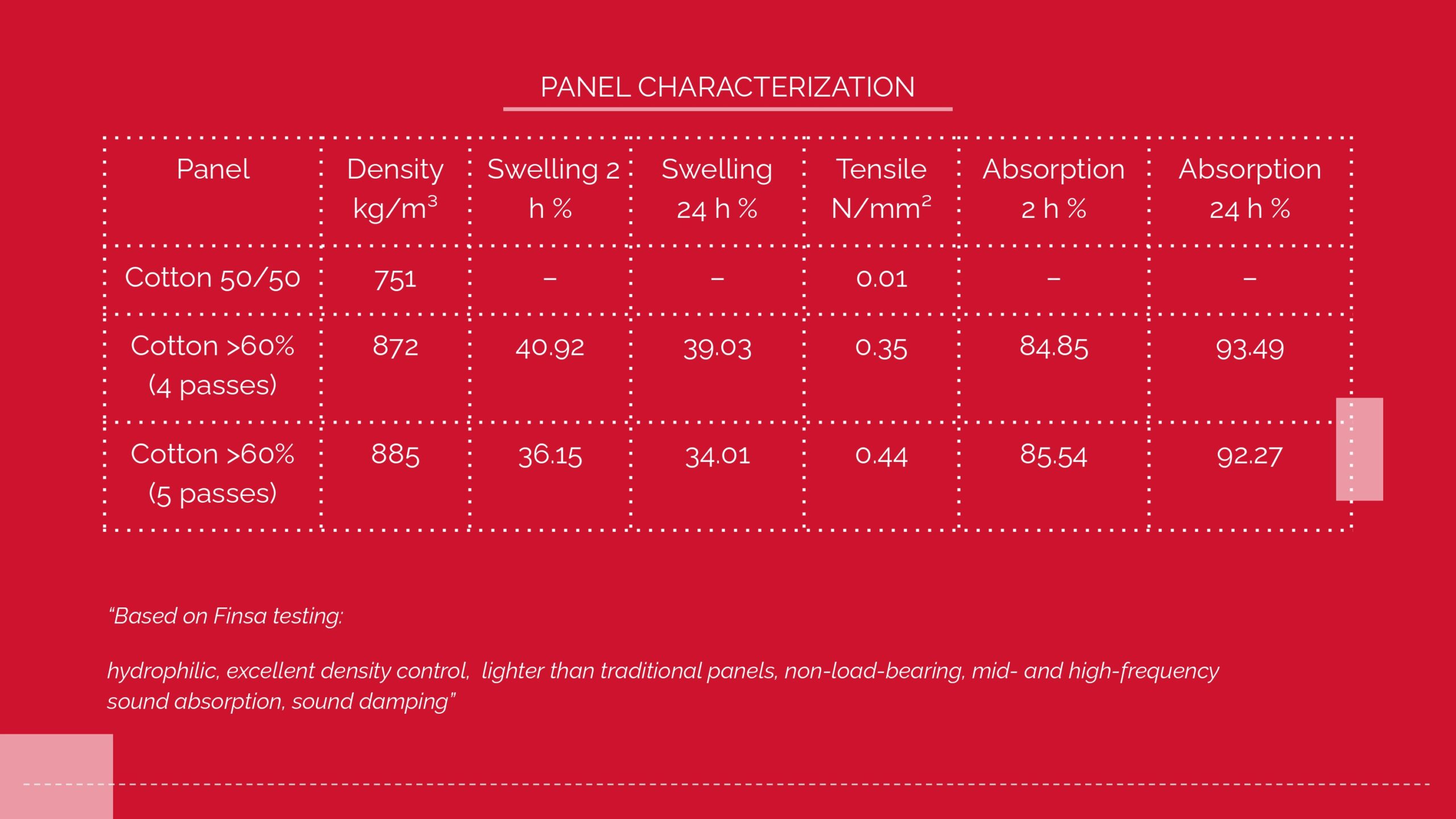
It was important to characterise the panels and with those initial tests we were able to conclude that the panels are hydrophilic, with excellent density control, lighter than traditional panels, non-load-bearing, but with mid- and high-frequency sound absorption, sound damping properties.
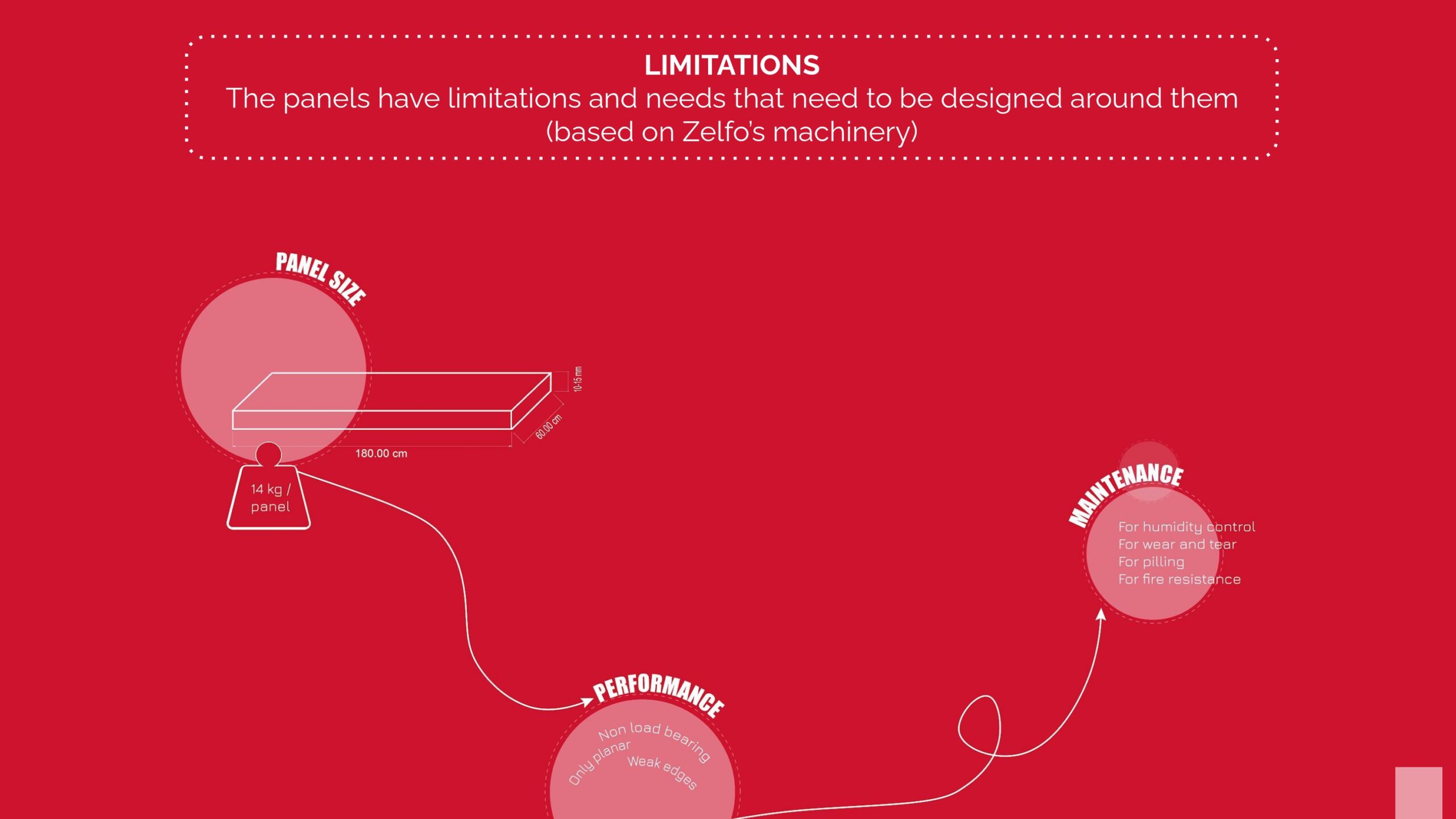
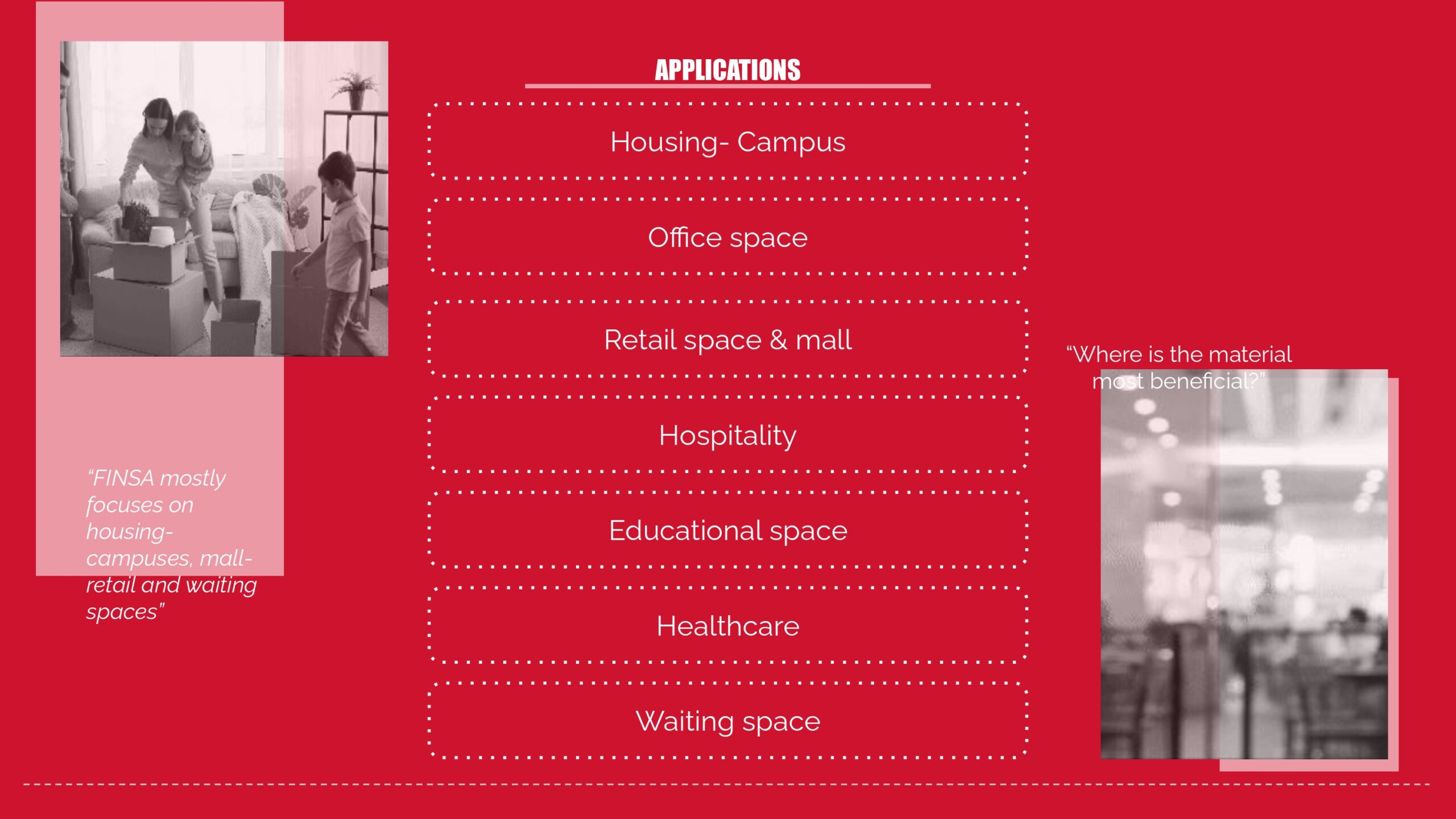
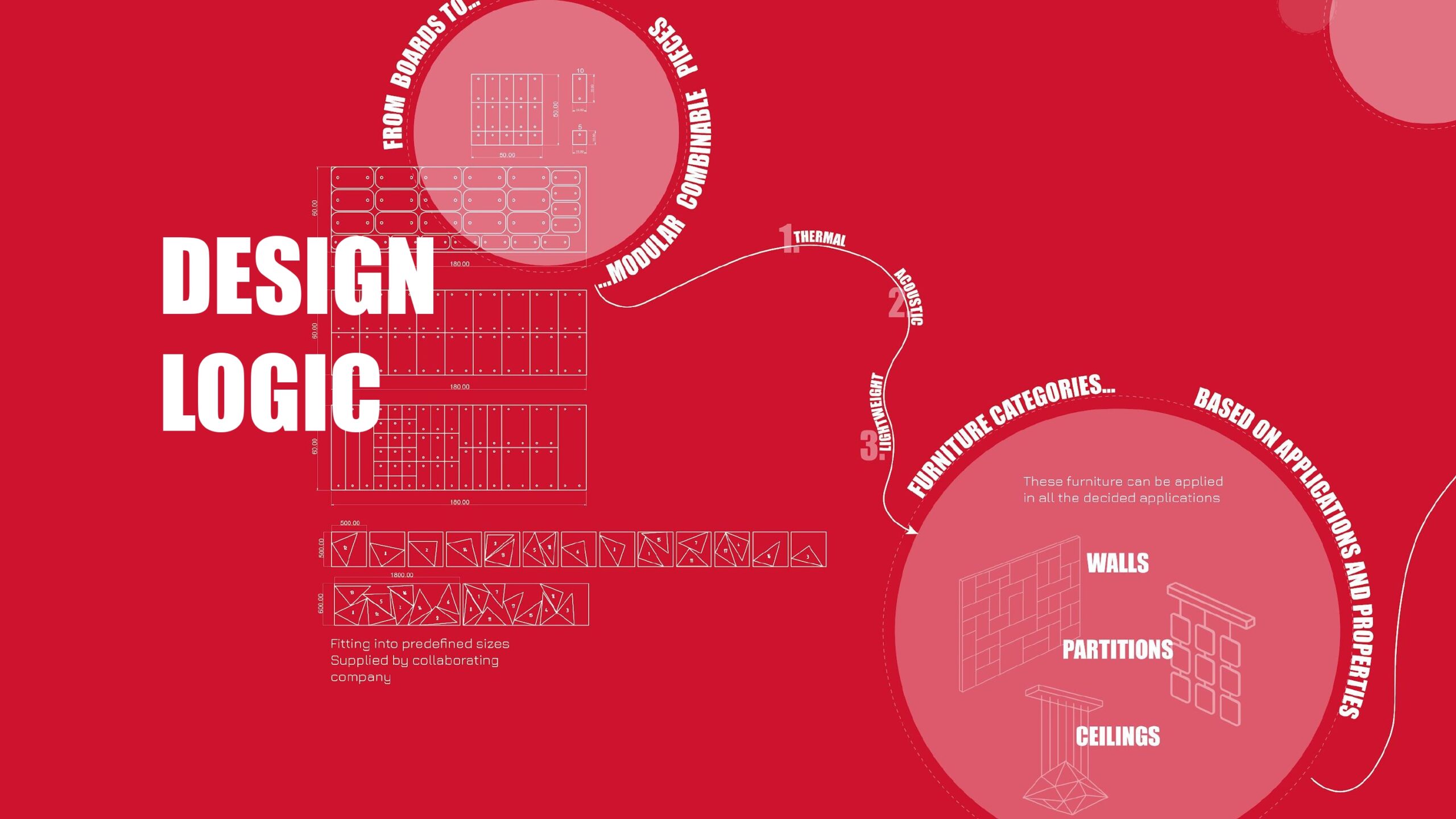

We needed a simple system so a variety of ideas was investigated form dowel system, to ball joints, and ropes, to fabrication tests to see how well we could cnc, engrave and use the panels.
Many designs had been made till we figured out the most appropriate ones.
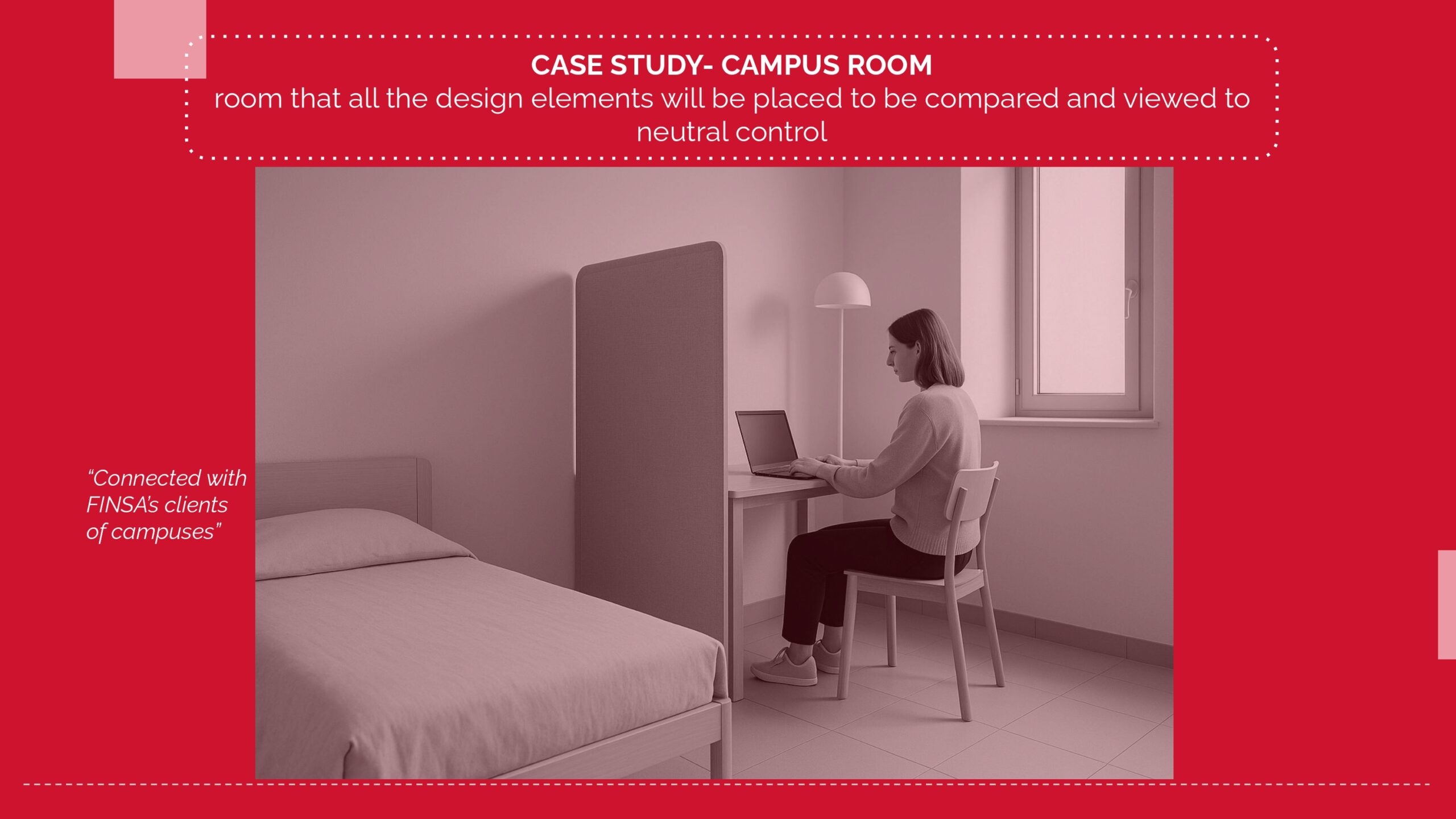
All the designs could of course be connected with a rope logic, making rigid, adjustable connections that way are mimicking the origins of garment stitching but also ensuring stability and adaptability.
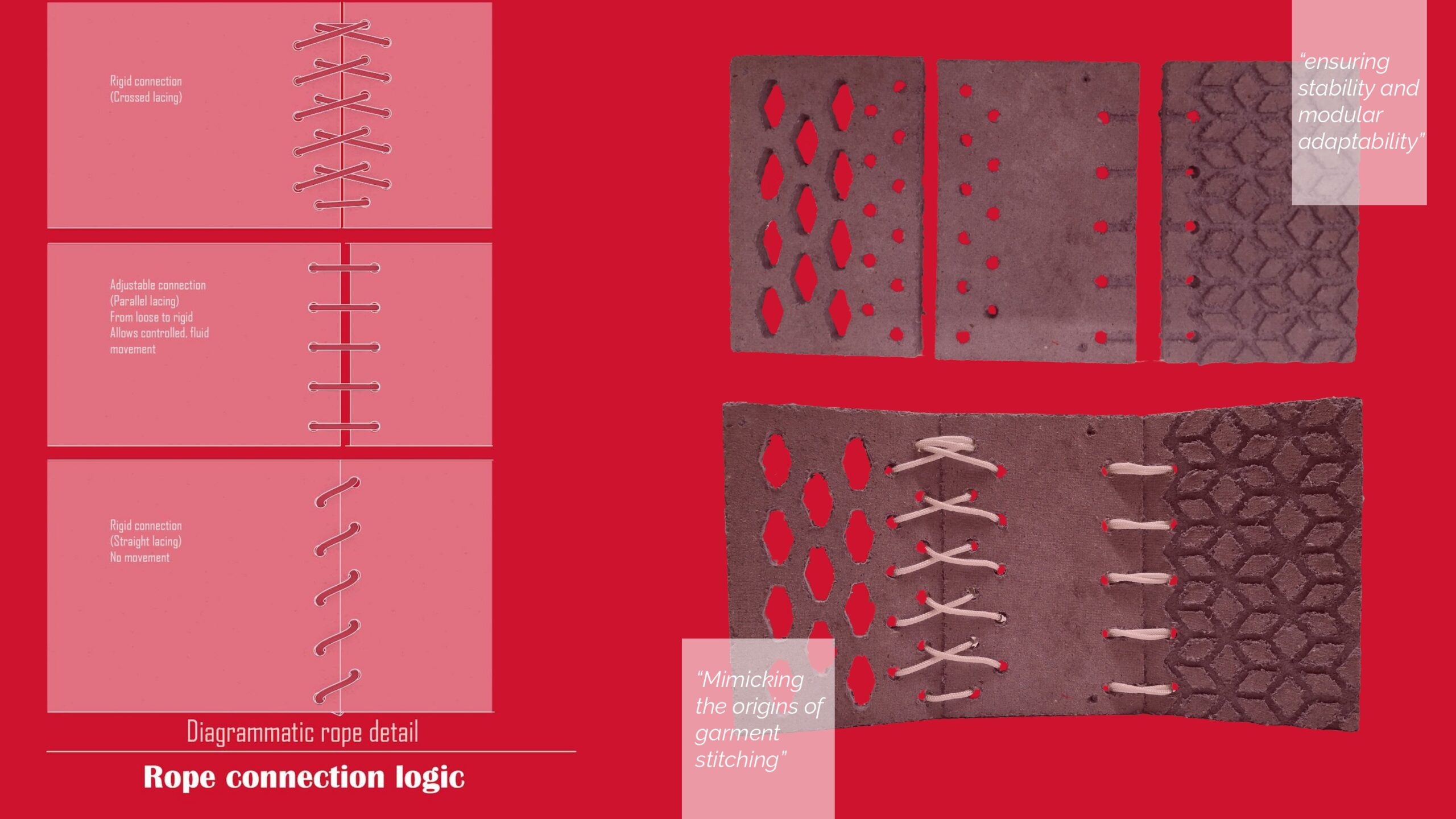
The elements were placed in a scaled down 3d printed room , to figure out all the positions and combinations.
But also we continued the 3d printing investigation looking for the most optimal connections.
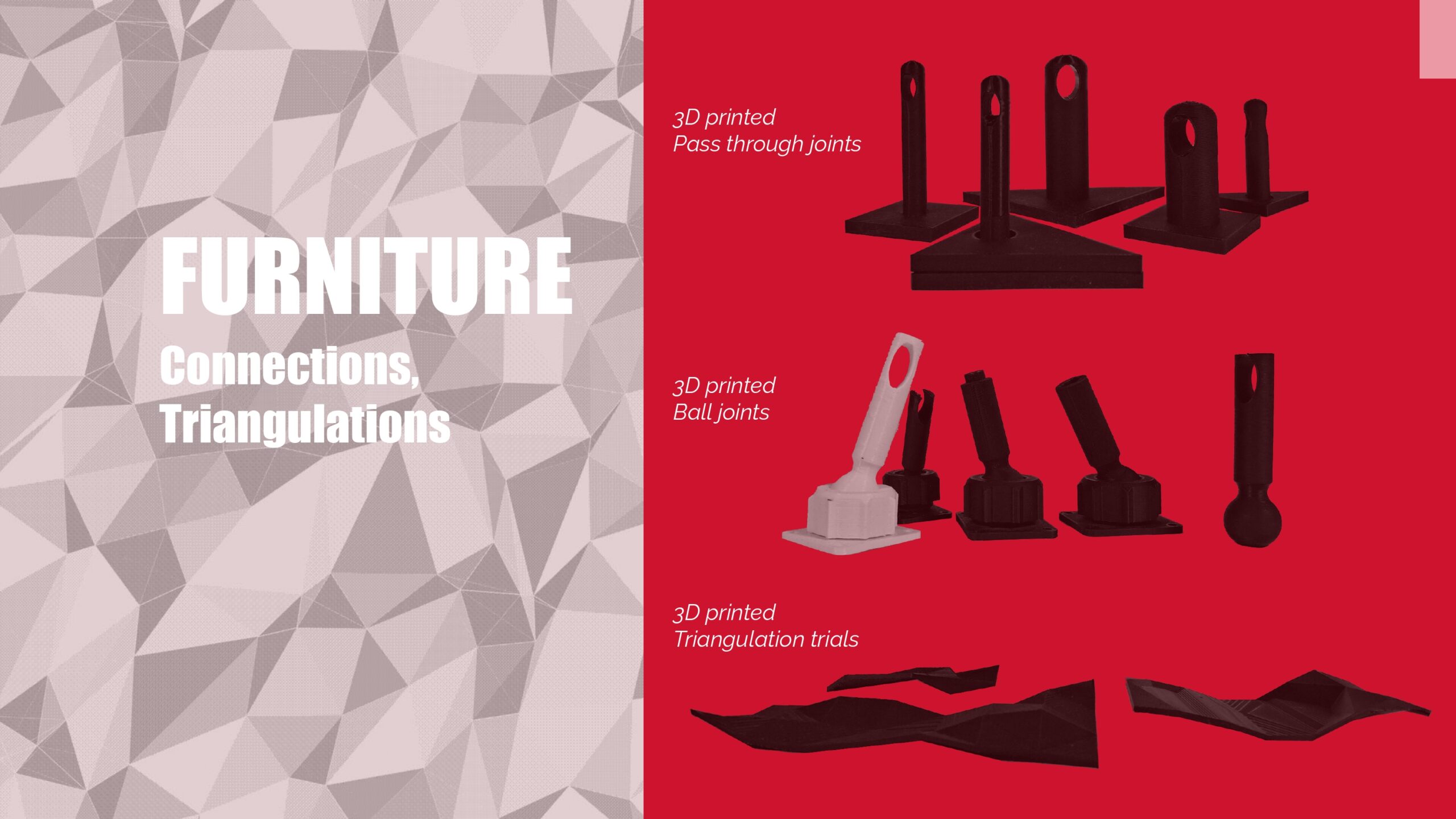
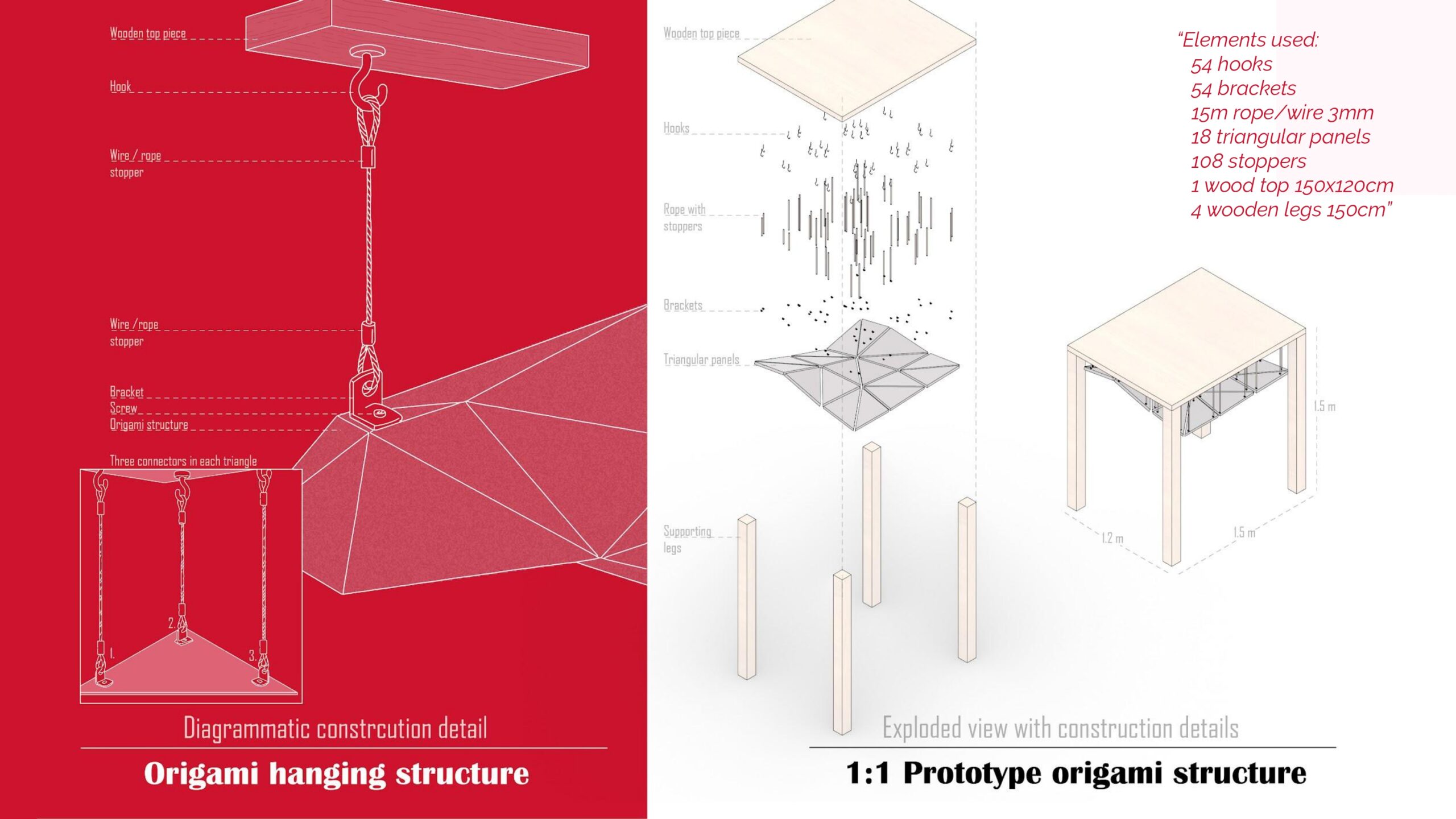
Finally, for the 1:1 scale prototype it was decided to recreate the folded hanging piece. To be places at IaaC, a secondary structure was made to hang the pieces. It must be understood that the parametric logic was kept and used in all the designs, as all spaces and needs are different, so the hanging pieces can be adjusted to satisfy different heights, geometries and more.
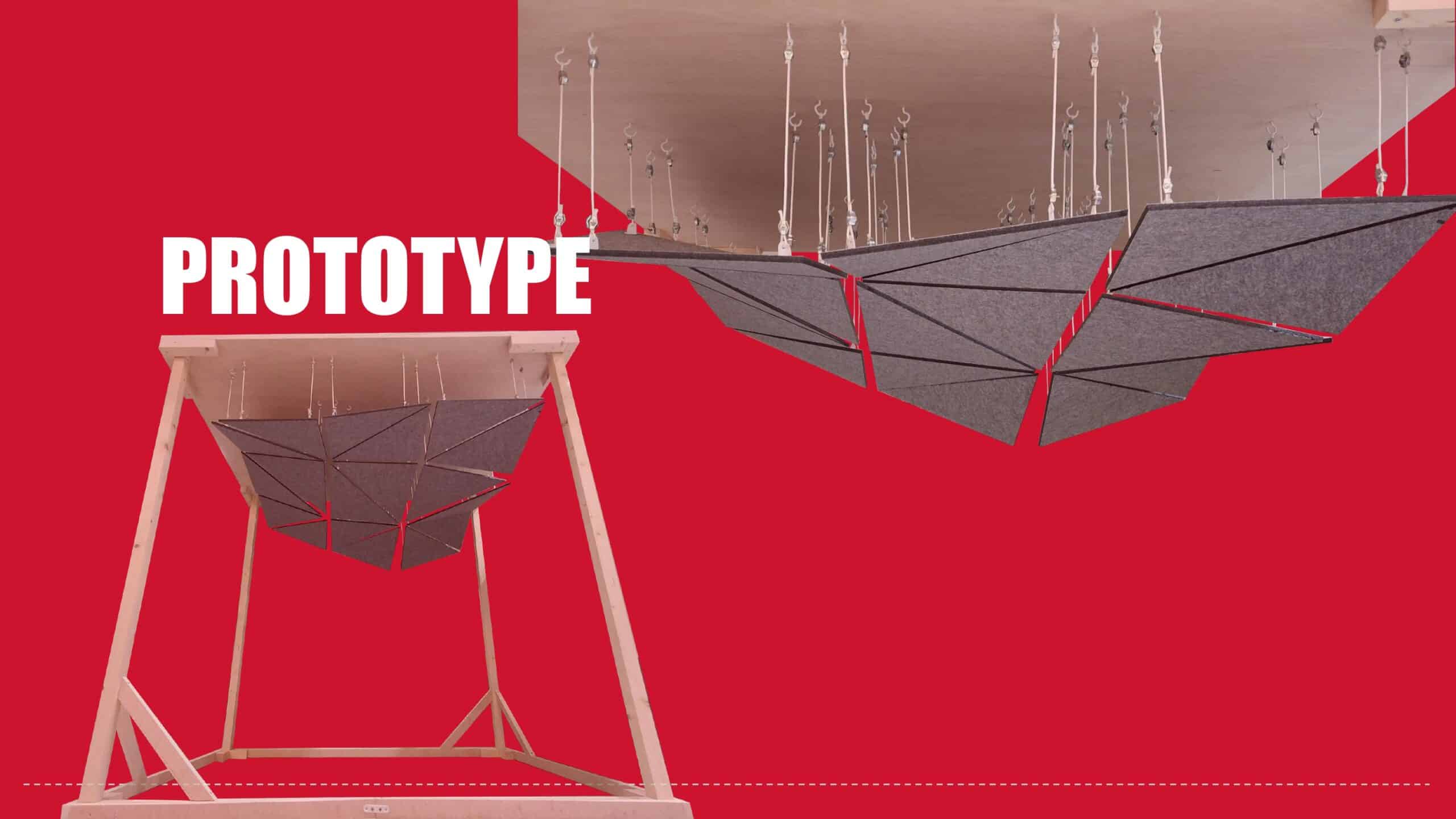
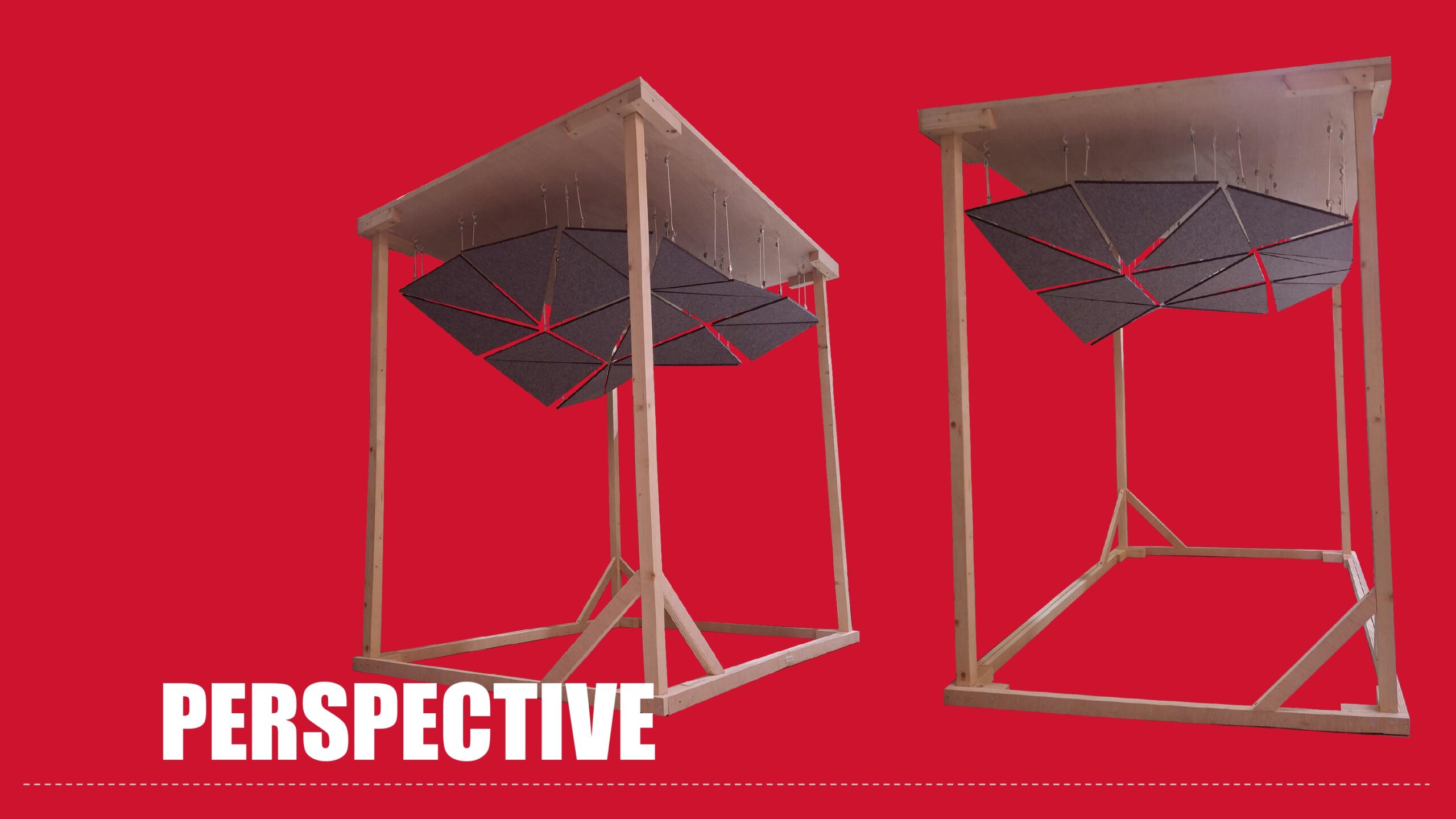
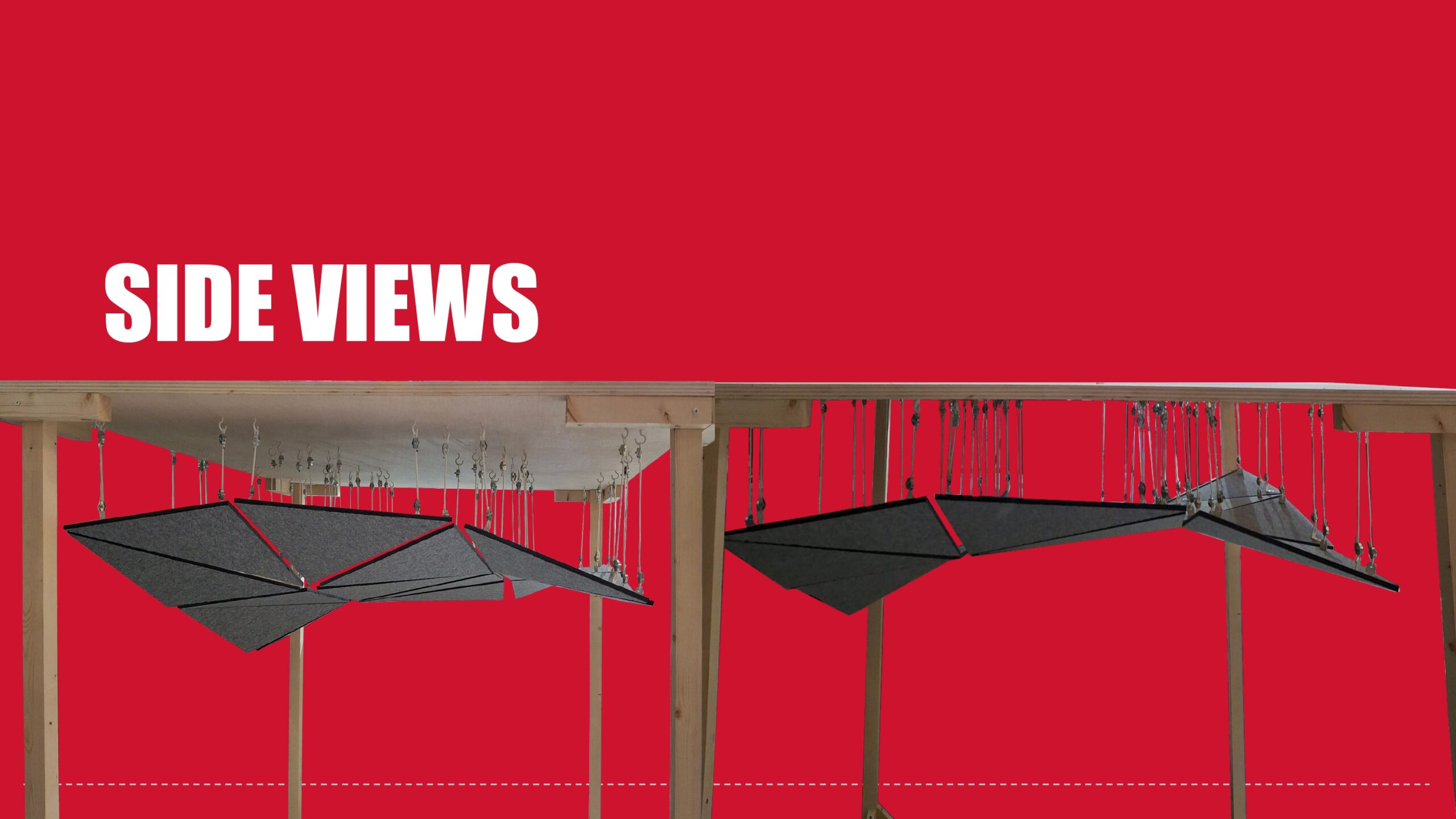
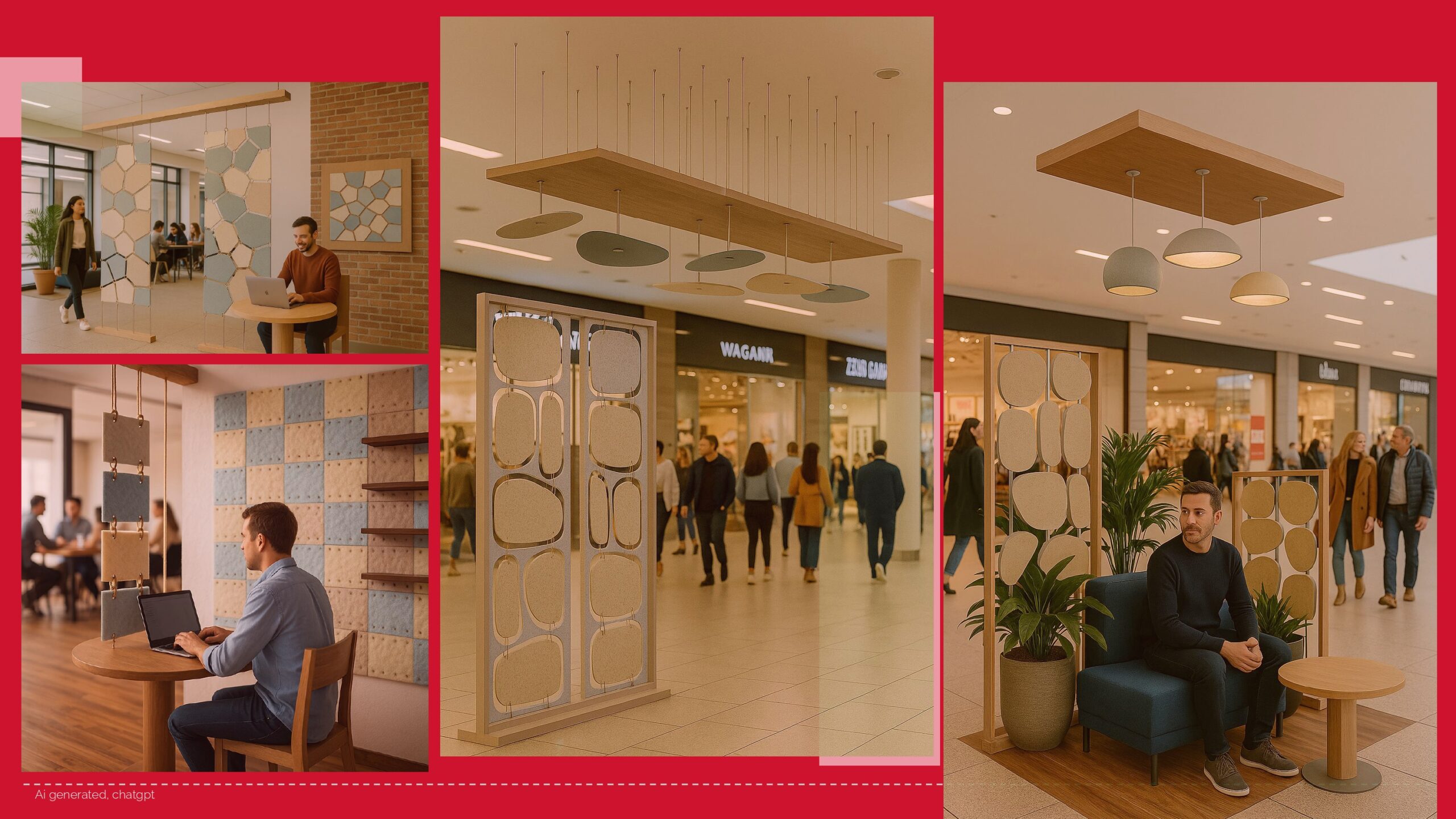
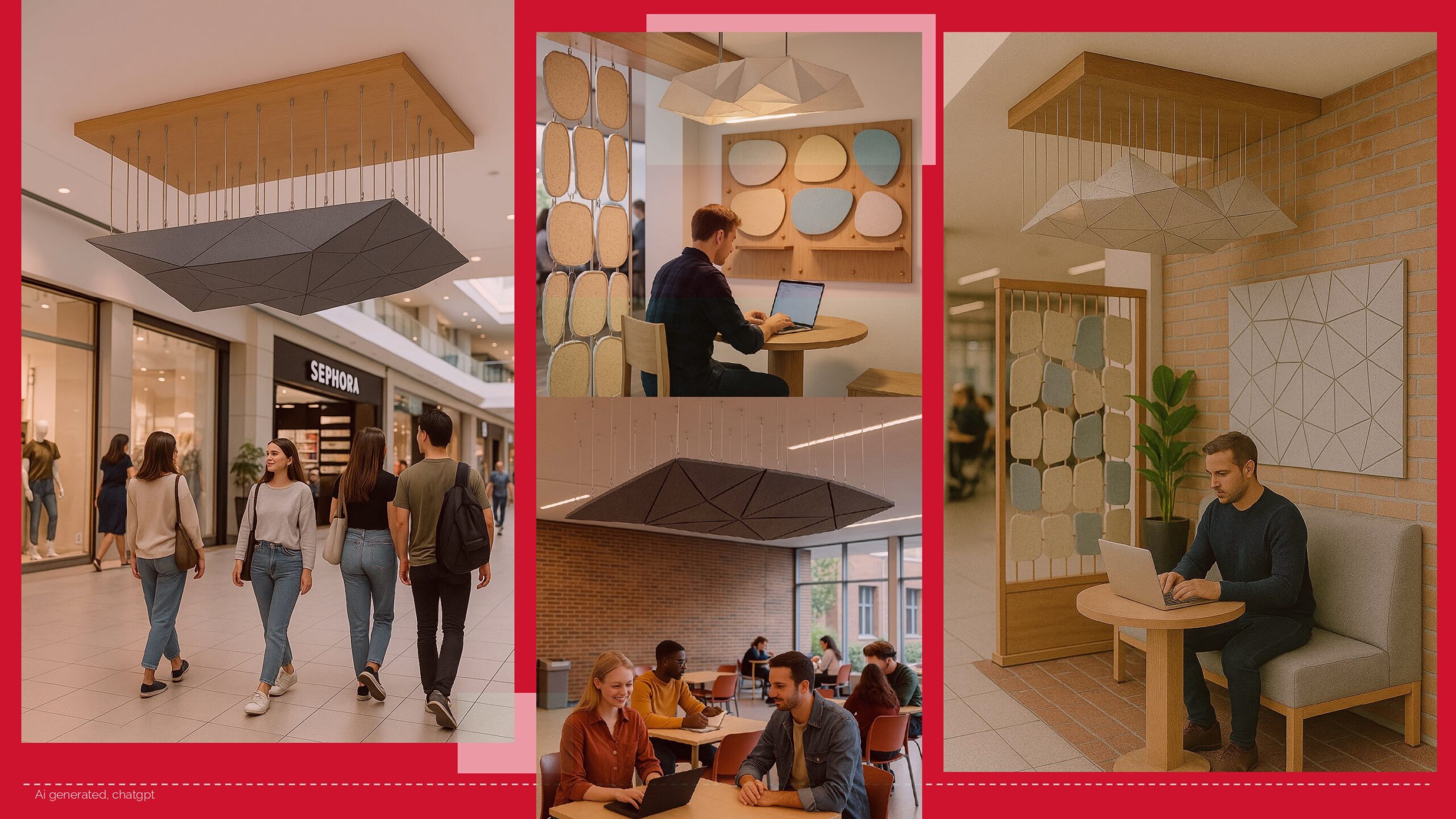
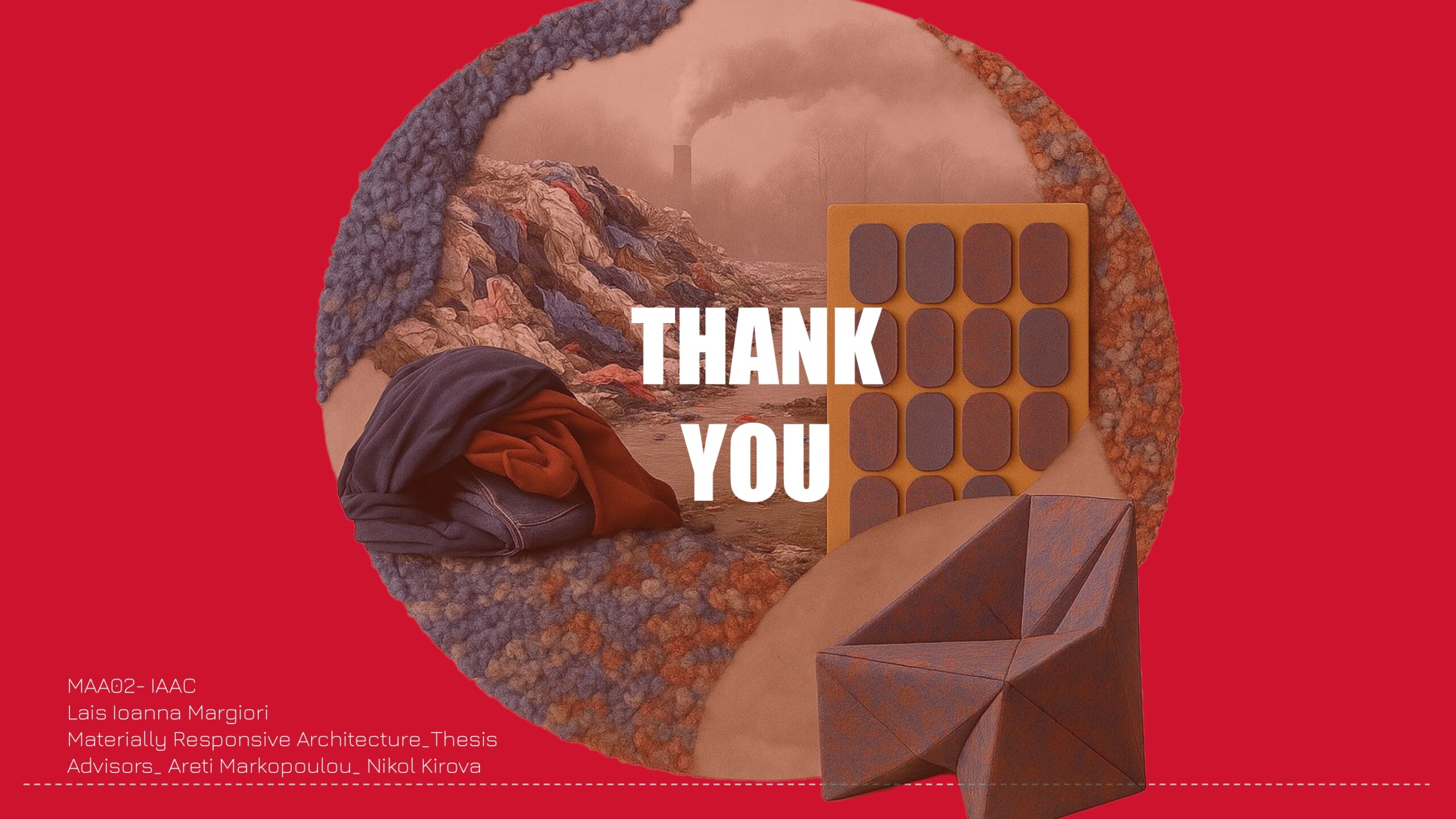