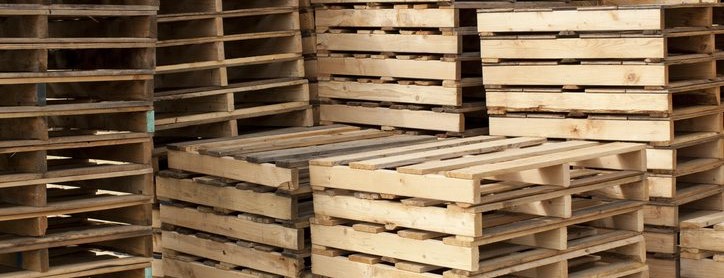
For the creation of our recycled beam we chose to repurpose parts of a wooden pallet that we found on the street, transforming discarded material into a functional structural element. This approach not only demonstrates the potential of upcycling in construction but also highlights sustainability by reducing waste and giving new life to materials that would otherwise be discarded.
Case Study
The Arevena Half House is an innovative architectural concept that redefines affordable housing. Designed to address urban density and economic constraints, it provides residents with a partially constructed, functional home that allows for gradual customization and expansion. By empowering homeowners to complete and adapt their space over time, this approach fosters flexibility, affordability, and a sense of personal ownership, all while promoting sustainable urban development.
Design Alterations
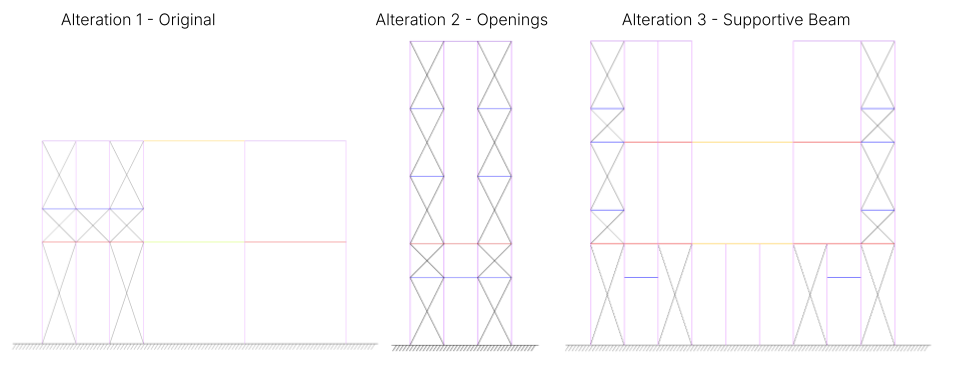
Analysis
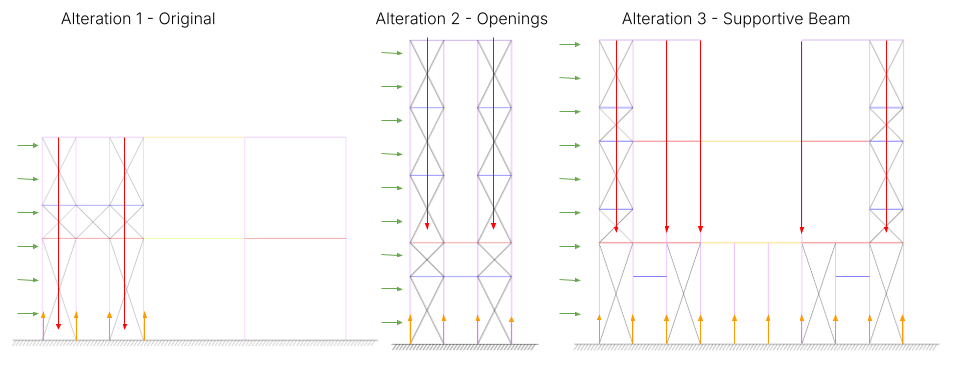
Alteration test – LC0

Alteration test – LC1
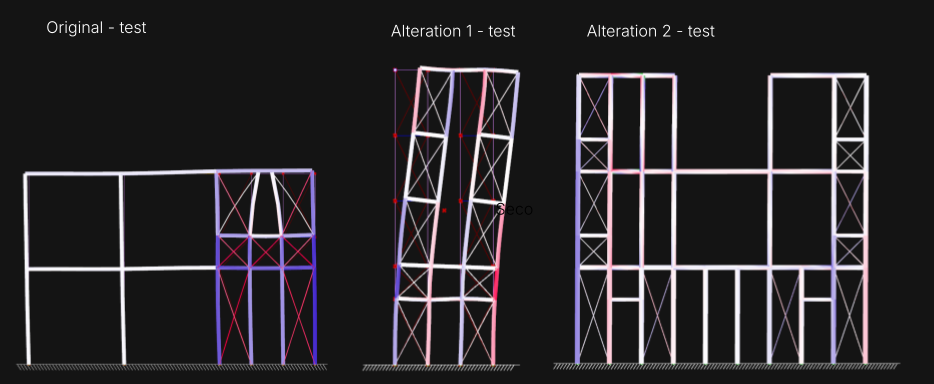
Beam Design
Fabrication Process
As part of the exercise, we decided to reuse discarded wood to design a beam. In looking for material, we found various palettes and realized how common and available they are. As a result, we began designing a beam structure made up of palettes. The main structure of the beam was composed of a a portion of a 4-way entry palette with no baseboard and a smaller 2-way entry palette with no baseboard that we sawed in half.
Adhering to the design limitations we were given (a 2 m long beam with a maximum cross section of 20 cm x 20cm), this is the design we came up with:
Beam Design Model, Made with Rhino
Beam Design Composition, Made with Rhino
Beam Test
After fabricating the final beam design, we tested it and these were our findings:
- The maximum load it supported before failing was 208 kg.
- Failure occurred at one of the original wood panels from the half palette attached to the end.
- Failure occurred due to the screws being inadequate for the forces encountered.
- Variations in wood grain and density created weak spots under load.
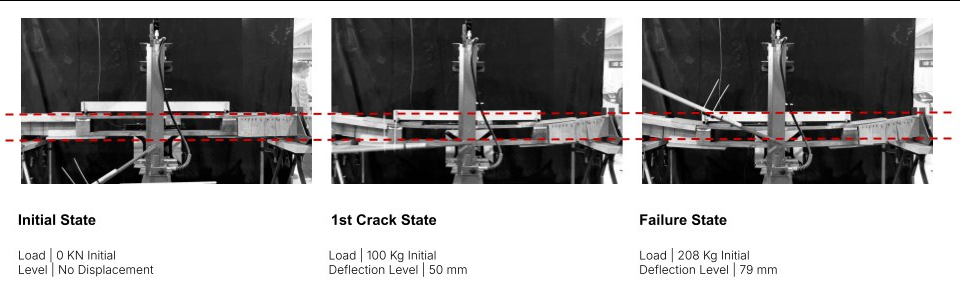
Displacement-Force Graph
Karamba Analysis & Design Variations
Using a digital model of our palette beam, we analyzed its performance using Karamba. Applying the maximum load from our real-life test with our fabricated beam, we found a significant difference in the displacements. Not surprisingly, our Karamba analysis, showed a much smaller displacement, almost minimal, in comparison to the real-life beam. We attribute this to the fact that the digital model was created with with assumptions that all the splices were aligned seamlessly, the connections were also screwed perfectly and it did not take into account the weathered conditions of the wood we reused.
Using a load of 208 kg:
- Displacement: 0.56 mm
- Shell Max Utilization: 3.7 %
- Beam Max Utilization: 21.3 %
Final Design Beam Analysis, Made with Rhino, Grasshopper and Karamba
Given that our final beam design was a hybrid composition of 2 different wood palette parts, we decided to explore other beam iterations of just one of the palette parts. Then we used the same load from our real-life test to compare the performance of all 3 iterations.
The first variation is made up of only the middle piece of our hydrid beam: the 4-way entry palette.
Using a load of 208 kg:
- Displacement: 1.4 mm
- Shell Max Utilization: 0 %
- Beam Max Utilization: 62 %
Beam Variation 1 Analysis, Made with Rhino, Grasshopper and Karamba
The second variation is made up of only the end piece of our hydrid beam: the half 2-way entry palette.
Using a load of 208 kg:
- Displacement: 0.21 mm
- Shell Max Utilization: 0 %
- Beam Max Utilization: 8.6 %
Beam Variation 2 Analysis, Made with Rhino, Grasshopper and Karamba