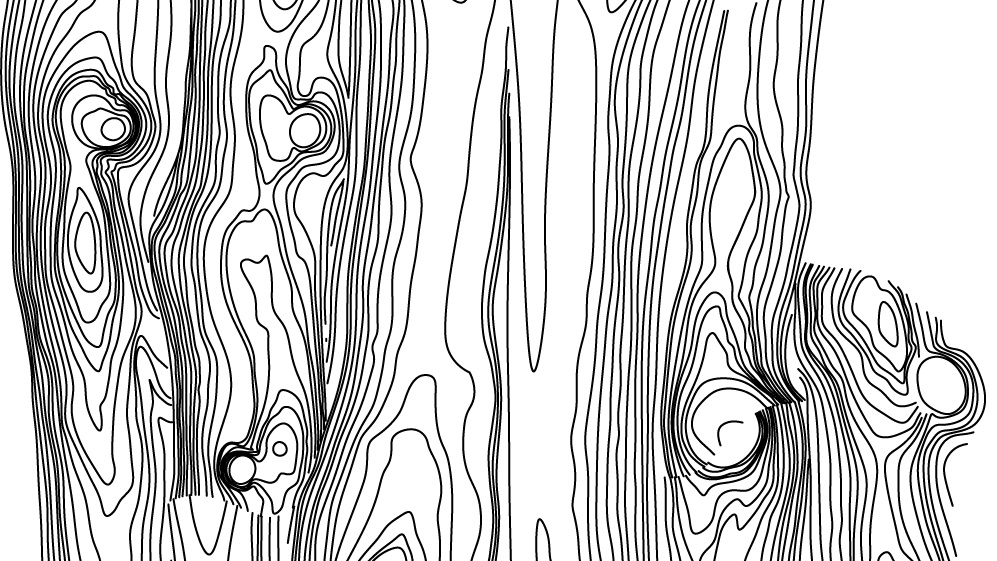
Wood is a naturally grown material that is often seen by industry as a linear and standardized entity.
“re(al)form” focuses on the resulting leftovers, which take the naturally grown form language of wood from nature to create an aesthetic and seamless facade which takes the fiber direction as a main input. The project embodies aesthetic through its dynamic process, as the design is dependent on the available material library. The use of digital fabrication methods to produce mass customization is the primary approach in this process.
Context
Wood production
The wood industry treats the wood as a linear standardized entity. Through their way of production leftovers are produced which get no bigger value then getting burned on site, cut into chips, used as fire-wood or in the best case used for small scale furniture. We try to cut the supply chain an add the leftover wood value.
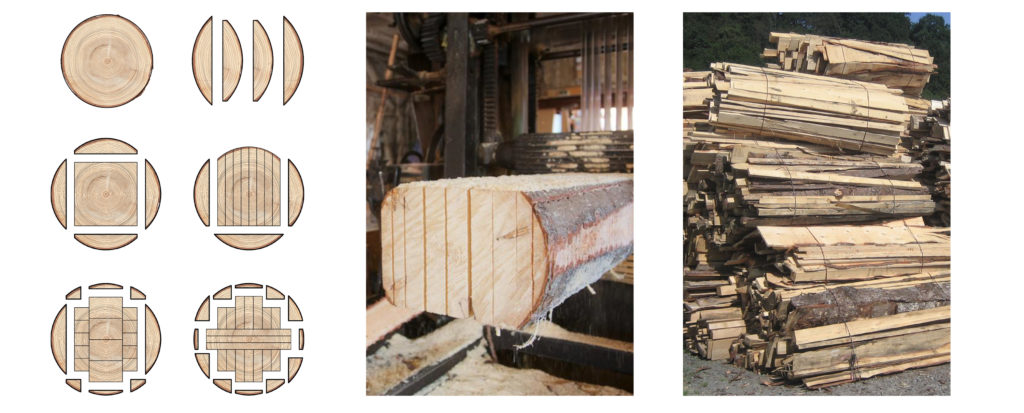

burned on site, wood chips, furniture, firewood
Design to execution issue
In the planing phase architects often create beautiful renders which show their imagination of seamless wood that follows the shape. The issue is that the execution doesn’t respect the imagined aesthetics.
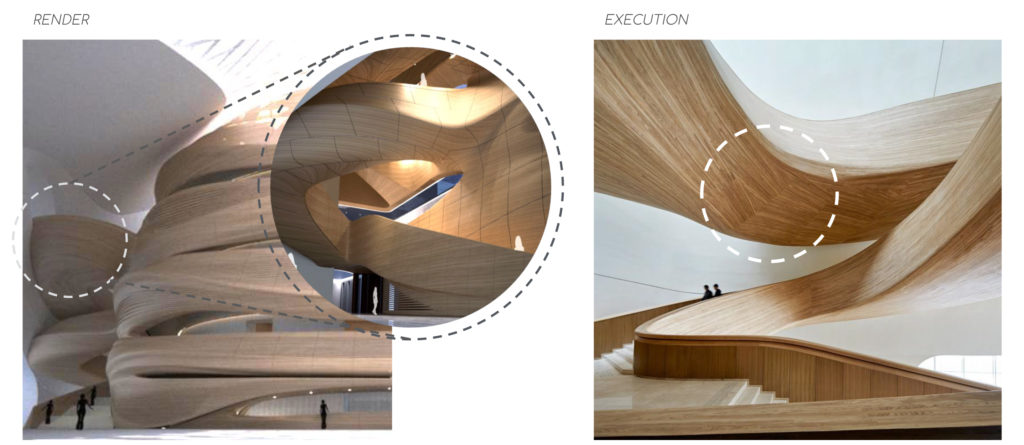
Research Aim
Develop an automated -design to execution- facade system that emphasizes the natural curved wood fibers by cutting the supply chain cycle and add value to the leftover wood
System Design
Abstract Design Process
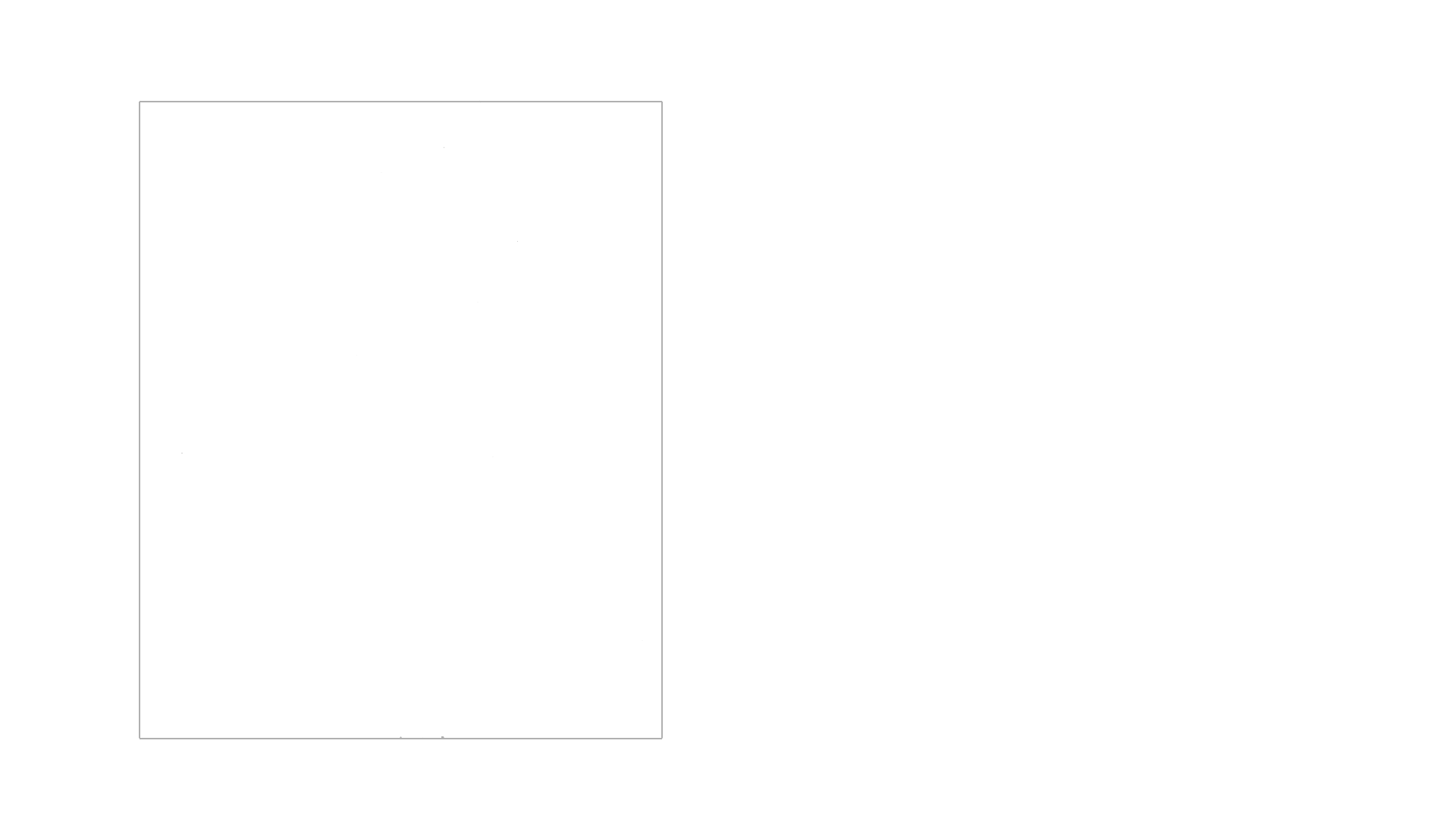
The general idea of the system design is to create a digital material library of the available leftover wood and matching it to a main facade design. This facade design uses only predetermined openings and main direction curves that drives the matching and output. The library doesn’t just match with the main design but also with the direct neighbors to create the most seamless transition possible. As following part comes the discretization in which we decide on how it should be separated into panels and from there on to the substructure that let the facade connect to have preassembled panels for the onsite construction.
Process Workflow
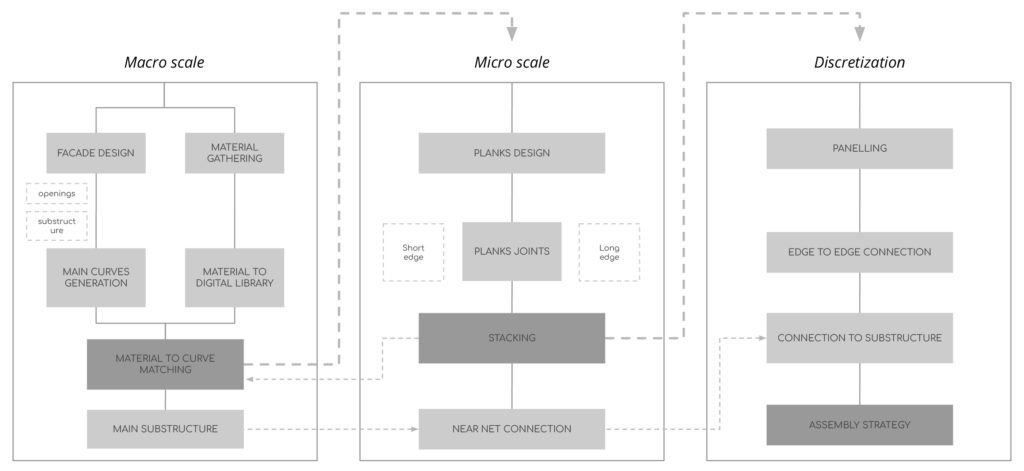
Preliminary design focus
This picture serves as preliminary design inspiration to make our small material library match on the design.
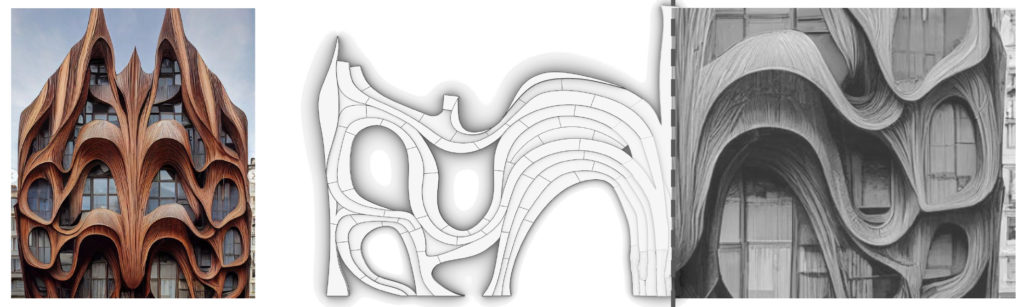
Material gathering
This step serves to create our digital material library to create from there on our prototype. After capturing a photo of each leftover plank it gets lens corrected to get the real size and proportions of the plank. To finalize the digitalization of the library the fibers of the wood pattern gets extracted to be able to find the best matching in macro and micro.
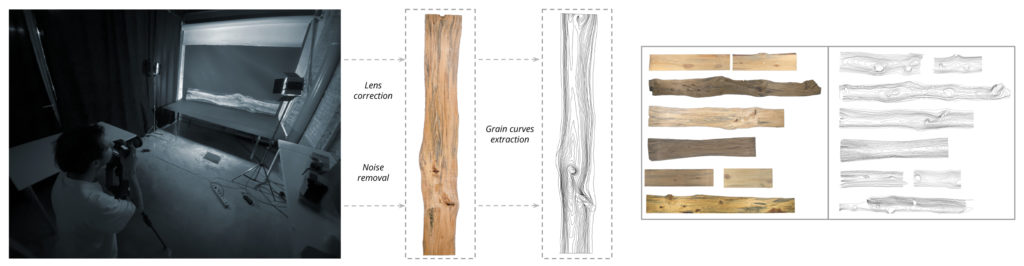
Macro matching
Matching digital library to main design and descritize single components into panles to have preassembled components into panels.
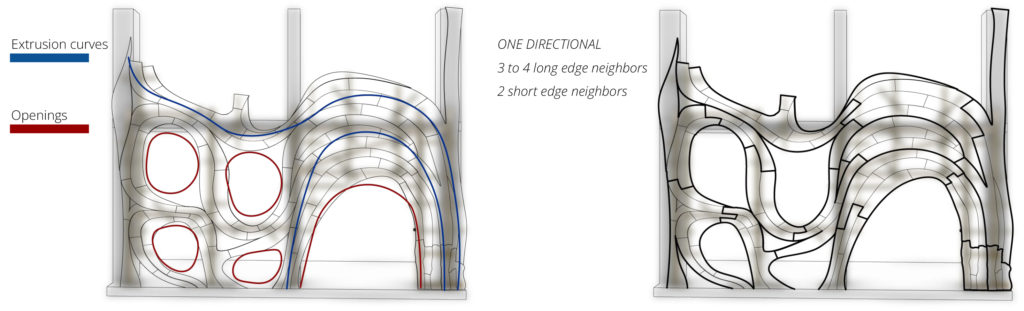
Micro matching
Taking digital library and trying to find best possible matching curve to create a seamless transition
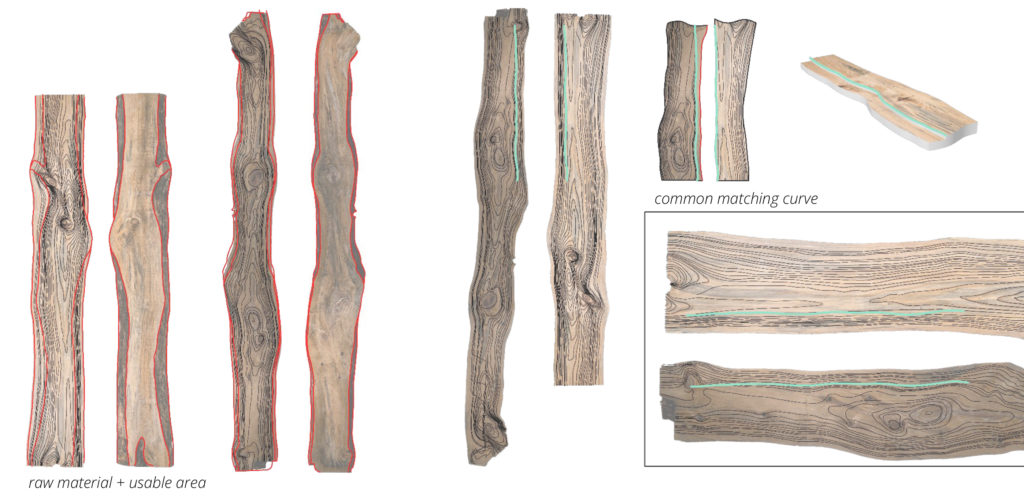
Panel structure
The near net structure of a panel connects all components together to one unit. Therefore it’s preassemblage makes it possible to assemble panels to a facade on site.
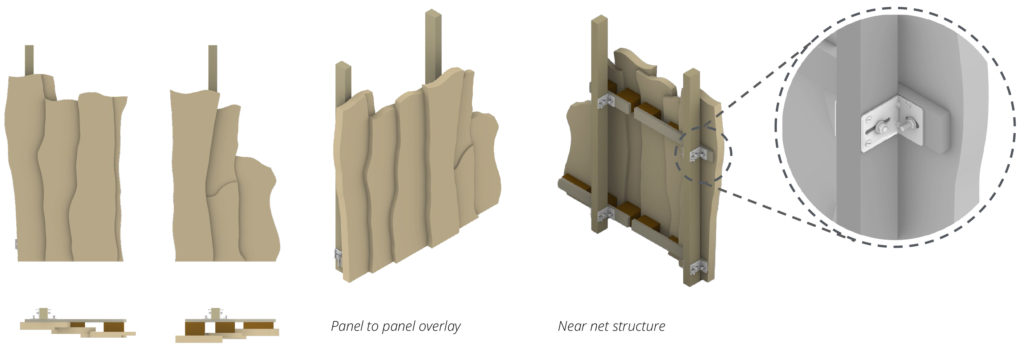
Discretization
The substructure is determined on the basis of the panels. Through them all panels are connected as a whole facade
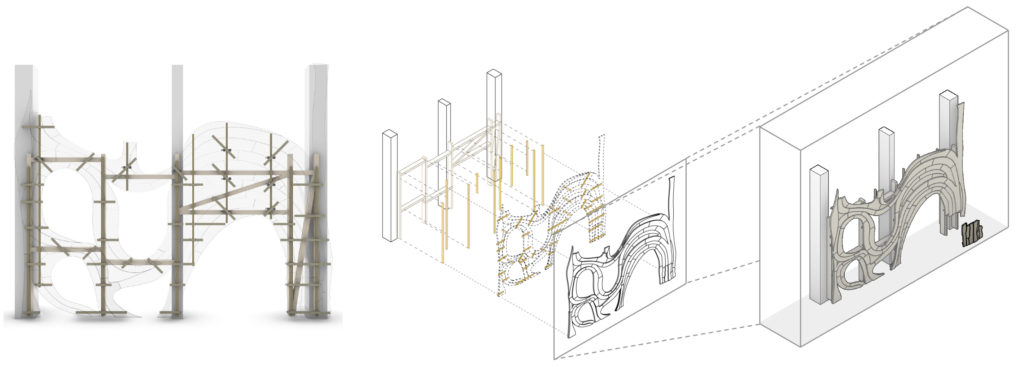
Manufacturing workflow
Panel prototype
a. CNC pre-processing
b. Components to panel assembly
c. CNC post-processing
d. Surface creation criteria
long edge connection, knots, screws, less milling
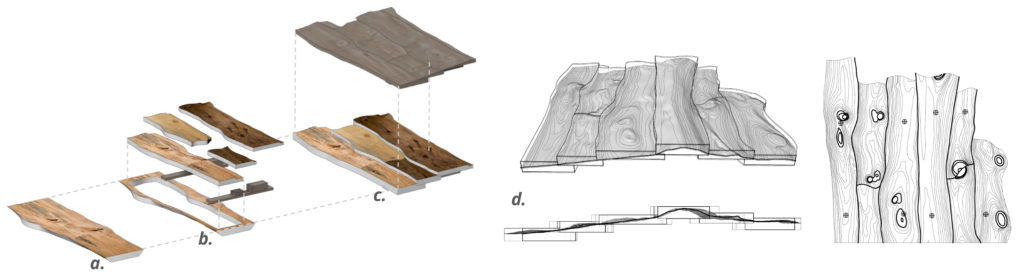
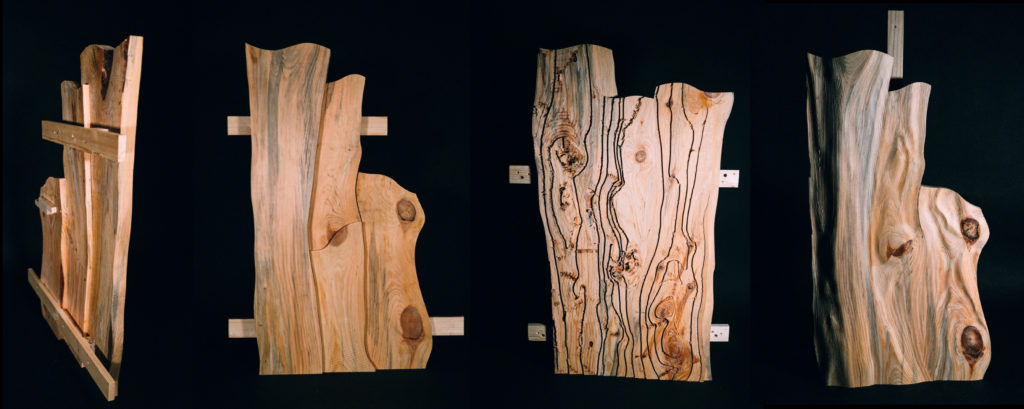
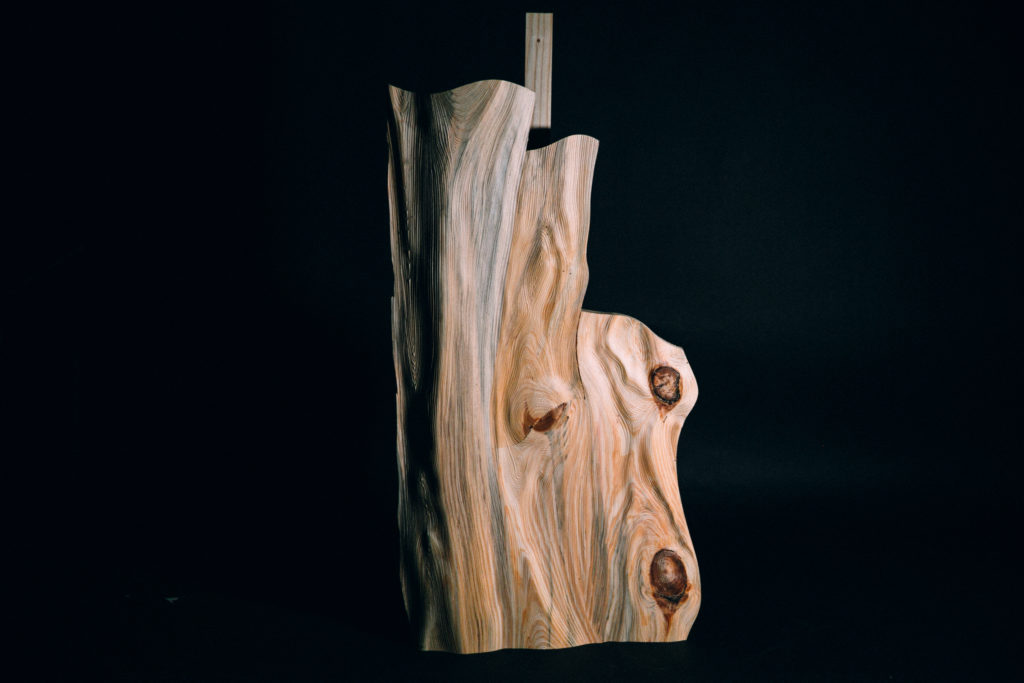
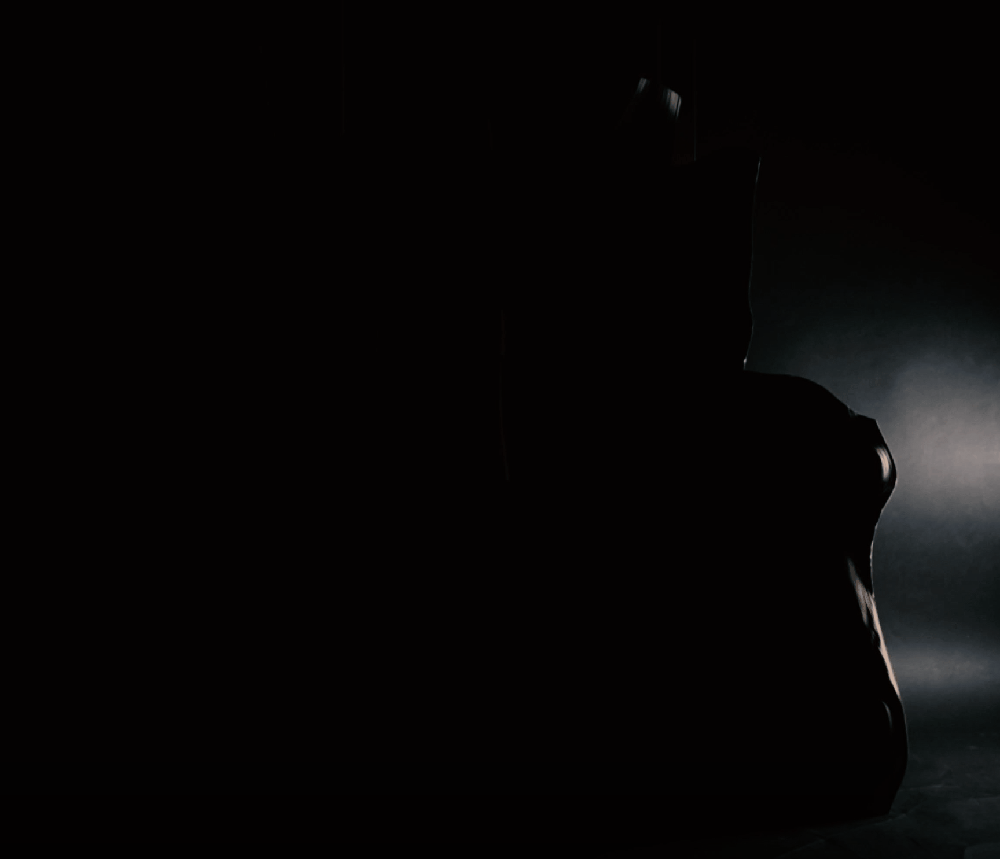