Hyl?, in ancient Greek philosophy, refers to matter. During MRAC Studio I the geometric affordances of raw, organic matter will be explored through flexible robotic workflows. Hyl? provides a framework for students to iterate their designs through semi-automated manufacturing pipelines with applications in architecture. Our material palette will be composed of natural materials, such as timber, clay, and cork. A project will be developed in tandem with your knowledge of one of the aforementioned material choices, computational design and detailing via a series of experiments. As a final deliverable, each group will build a prototype in 1:1, using the experience gained in the studio.
A robot is the most customizable component in a manufacturing system! It can be anything the system wants it to be. The designer in this space not only designs the product but also the technical capability of the robot. Design decisions will be re-evaluated based on gradual understanding of the material and the robotic process’ constraints. The process from inception to project completion will come with many stages of adjustment. In this context, product and process evolve concurrently.
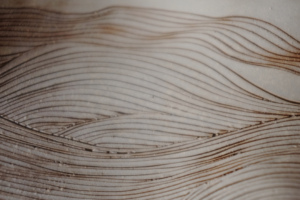
Photo Credits: Ruth Cepedano, Escultura Ceramica
Design element
As a design starting point we will use Barcelona’s modernist heritage. The frame, the surface or the arch will be the formal point of departure for each one of the groups. The aim of this exercise is to gain insights on modelling complex geometries with regard to material properties and tools. A rounded frame, a doubly curved surface, and an informed structural element provide a prolific design space for fabrication exploration aiming at the precise reconstruction of bespoke details with numerically controlled methods.
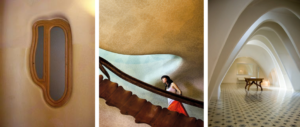
Photo Credits: Casa Batlló by Gaudí
Methodology
During the first weeks we will settle on a design element combined with a fabrication strategy. Students will have to define how the robot will be used as a manufacturing aid. As the robot is an unfinished machine, delivering a robotic fabrication project includes creating a custom workflow. In most other manufacturing equipment in the workshop, parameters are significantly more fixed. In this case, the flexibility of the tool grants enough space to consider the opportunities that this instrument offers in the design process.
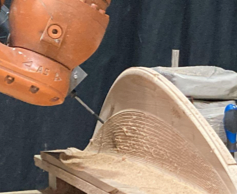
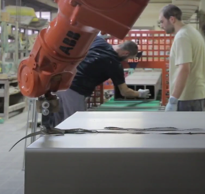
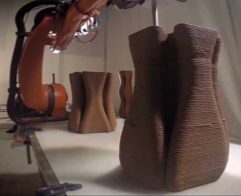
Photo Credits: Marielena Papandreou (a), Musical robotic facade (b), Robotic Mosaic (c), Pylos (d)
Parametric control in a design-to-production workflow offers a unique opportunity to have a feedback loop with the production method. A digital model, which can accommodate all the complex relationships of its contained elements, will be orchestrated properly in order to deliver valid information for every step of the design and construction of the studio project. Such digital definition has a lot of benefits for manufacturing since it allows for design variations to be explored and design changes to take place until the first day of final production.
Learning Objectives
Enter the learning objectives
The aim of the studio is to introduce students to holistic design to manufacturing workflows leveraging computational design and robotic fabrication.
- Computational design to manufacture workflows
- Designing for affordance of material and fabrication process
- Designing for mass customization
- Robotic fabrication