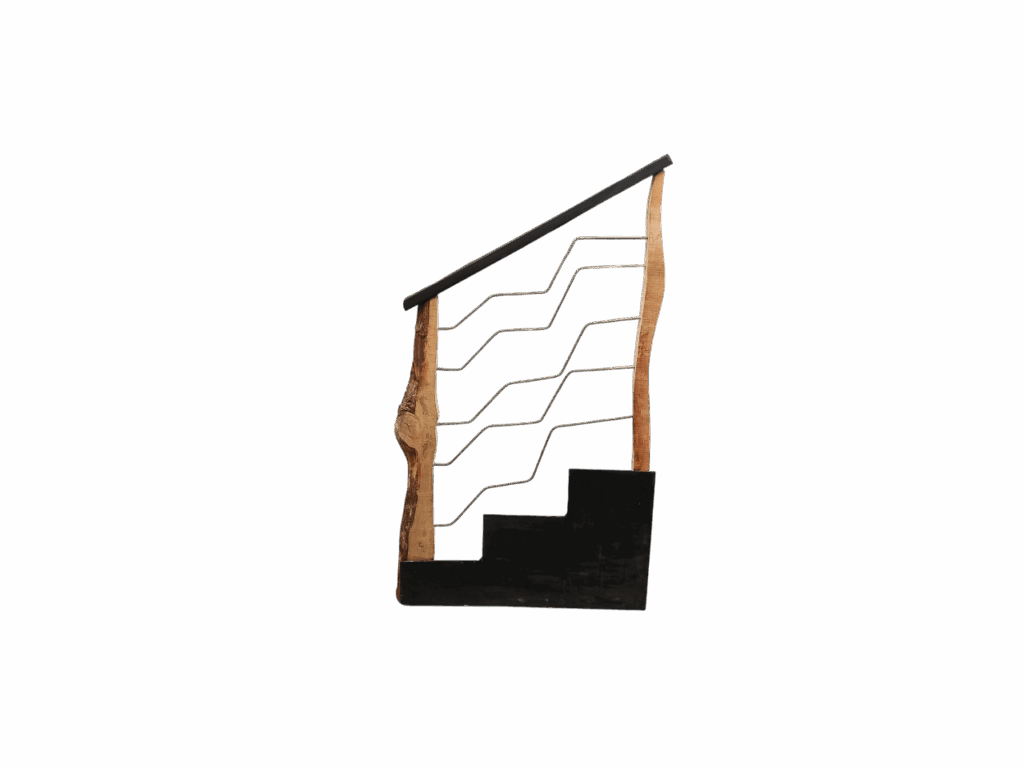
INTRODUCTION:
In today’s era of mass customization, robotics play a key role in shaping a variety of materials. This research investigates the capacity of the ABB IRB 6700 robotic arm to perform metal forming operations on 6 mm steel rebars. Despite axis torque limitations, the process successfully yields horizontal balustrade components intended for architectural integration at IAAC’s new campus facility.
SYNOPSYS :
Last term we explored robotic bending of rebars using an IRB 140 robot. This term, we reassess the process through a critical lens, analyzing limitations such as torque-restricted diameter (max 6 mm), gripper height constraints on bend spacing, and fabrication table height. By considering a higher-torque IRB 6700, horizontal feeding, and tailored dowel sizes, we evaluate whether robotic bending can outperform or complement manual, hydraulic, or CNC systems.
Can robots efficiently bend rebars for bespoke handrails?
Conventional methods offer force or scale, yet robots introduce geometric precision and adaptability. Rebars typically used in structures offer a raw, expressive quality, especially as horizontal balustrades. To comply with safety standards, specifications require 800 mm overall height with 100 mm between balustrades, reinforcing both functional clarity and design innovation. The IAAC campus offers varied sites for implementing these handrails.
COURSE OVERVIEW:
As IAAC prepares to relocate to its forthcoming campus on Avila Road in PobleNou. The MRAC01- STUDIO 3 course positions this transition as an opportunity to engage with real-world architectural constraints through the lens of robotic fabrication and advanced construction methodologies. Within the industrial fabric of the chosen site, students will develop speculative strategies for adaptive reuse, leveraging full-scale robotic prototyping and material experimentation. While the architectural renovation will commence prior to their direct intervention, the studio foregrounds the use of computational design, robotic toolpath development, and custom fabrication systems to propose viable constructive insertions within the evolving school infrastructure. The third term emphasizes critical translation—from conceptual frameworks and material logic to actionable, site-specific robotic construction solutions—resulting in a coherent architectural intervention supported by physical prototypes, digital simulations, and performance-oriented documentation.
ASSIGNMENT OBJECTIVΕ:
● design a architectural intervention for a refurbishment project
● explore design process through the production of design iterations
● construction of a constructive prototype, partially fabricated with robotic means
● production of necessary documentation for an architectural intervention
● articulation of a project narrative for a locally sourced robotically produced
intervention
PROJECT OVERVIEW:
This study is structured into four interconnected components:
- Status Quo Analysis
- Design Evaluation
- Design Development
- Fabrication Implementation
The opening phase, Status Quo, delineates the current technological landscape surrounding the processing and bending of steel rebars. As a continuation of the Term 2 exploration, it begins with a detailed account of the robotic process previously established.
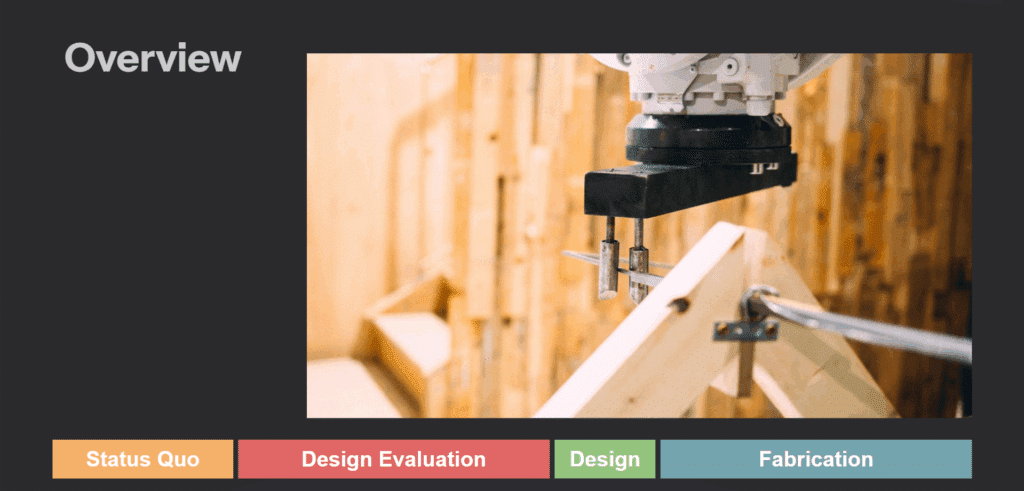
1. STATUS QUO
Last term we explored robotic bending of rebars using an IRB 140 robot., gripper height constraints on bend spacing, and fabrication table height.
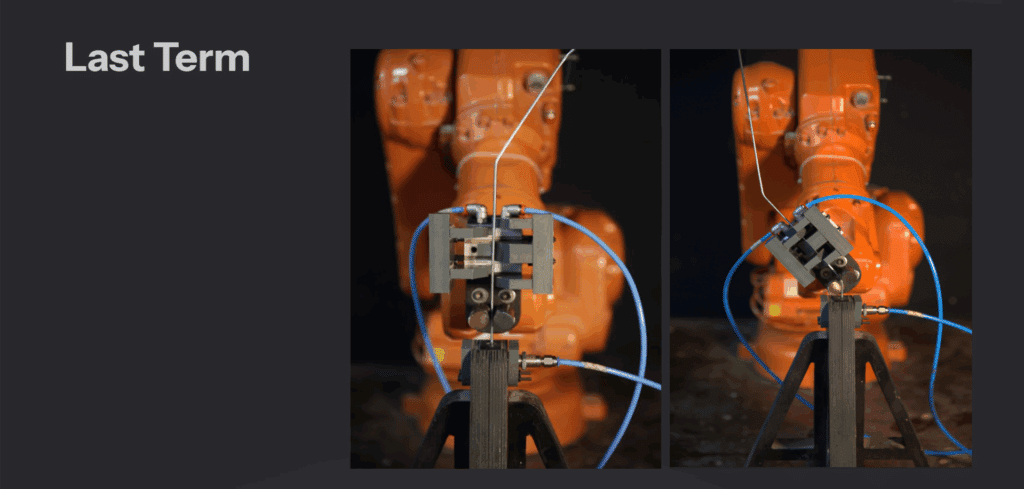
During Term 2, an experimental system was devised for the robotic bending of metallic rods, involving an end effector mechanism integrated into a robotic arm. This configuration includes an end effector equipped with two metallic bending dowels and a pneumatic gripper, which together manipulate and form the rebar, while a second pneumatically controlled component, the feeder, secures the rod in a vertical position.
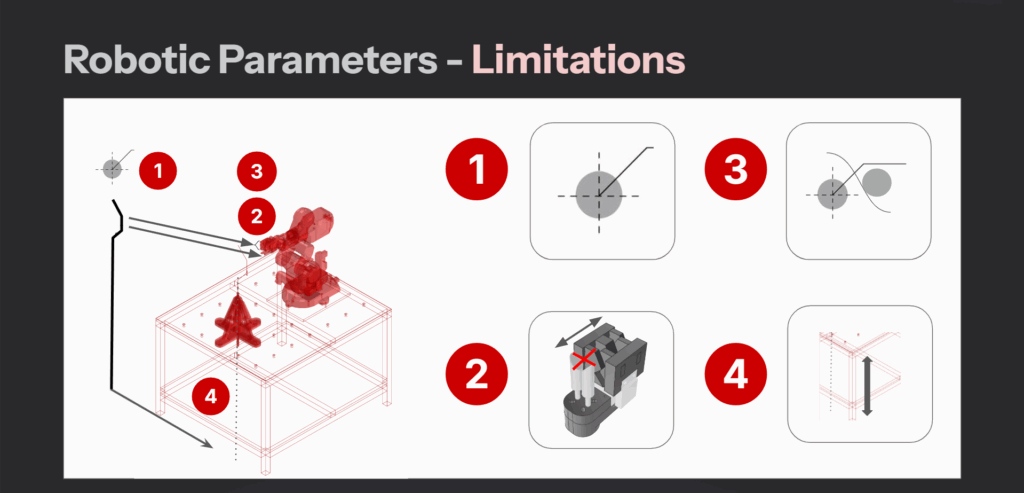
While functionally successful, this process revealed critical limitations warranting further investigation.
1. First, the torque required to bend rebar varies according to its diameter. For instance, an ABB IRB 140 robotic arm can accommodate rebars only up to 4 mm in diameter, posing a significant constraint given that architectural standards may demand processing rebars up to 50 mm. Scaling to larger robotic systems with higher torque capacity presents a promising path forward.
2. Secondly, the minimum length of any bent segment is inherently bound to the combined width of the bending dowels and the gripper. By potentially eliminating the gripper, which primarily prevents the rod from falling vertically under its own weight, the system could achieve reduced segment lengths, approximately equal to the dowel diameter.
3. Thirdly, the spacing between the dowels determines the maximum permissible diameter of the rebar, thereby necessitating precise calibration to accommodate different profiles
4. Lastly, the current vertical configuration of the bending setup imposes material constraints on the maximum rod length, as it cannot exceed the height of the working table. A reconfiguration of the feeder to operate in a horizontal orientation would accommodate longer rods, better aligning with architectural use cases.
Therefore by considering a higher-torque IRB 6700, horizontal feeding, and tailored dowel sizes, we evaluate whether robotic bending can outperform or complement manual, hydraulic, or CNC systems.
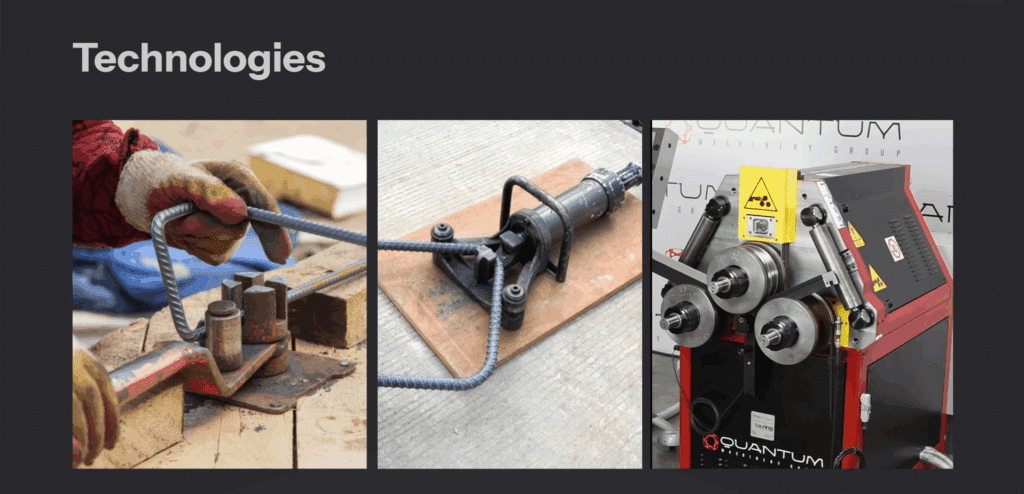
The evolution of rebar bending technologies can be broadly categorized into three principal typologies: manual, semi-manual, and automated systems. Manual bending relies on human-operated tools such as handheld jigs and simple lever-based devices. While this method remains economically viable and logistically accessible for small-scale or on-site operations, it inherently lacks precision, efficiency, and consistency. The absence of programmable control renders manual systems inadequate for geometrically complex designs or high-throughput production scenarios, especially in the context of advanced architectural construction.
Semi-manual systems introduce mechanical and hydraulic assistance while still requiring human oversight for tasks such as positioning and repositioning of materials. These systems strike a balance between cost-effectiveness and repeatability, enabling increased productivity and moderate design flexibility. Nevertheless, they remain constrained by operator-dependent variability and limited integration with digital fabrication pipelines.
In contrast, automated or robotic bending platforms represent the state of the art in this domain, offering programmable control, high precision, and adaptability for fabricating complex geometries at scale.
2. DESIGN EVALUATION
Building upon the established understanding of both the robotic bending process developed in Term 2 and the prevailing industrial practices in the market, the subsequent phase of this research focuses on the evaluation of design parameters. This stage is informed by a comparative analysis illustrated through a performance matrix, where various fabrication methods are listed along the vertical axis, while relevant evaluative parameters span the horizontal axis.
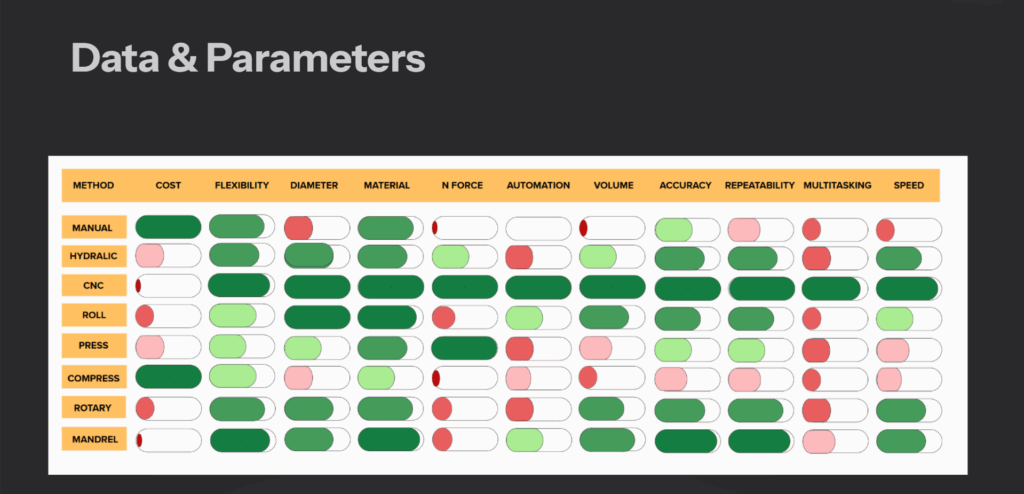
Each method is assessed across these parameters via a quantitative performance spectrum, visually represented by curved percentage indicators. The color gradient ranges from red, denoting suboptimal performance, to green, indicating optimal results. As illustrated in the diagram, the CNC-based fabrication approach though the most cost-intensive is also the highest-performing across multiple parameters. Conversely, more economical alternatives exhibit a broader variability in performance, with strengths and limitations contingent upon specific criteria. This matrix serves as a critical tool for identifying trade-offs, enabling a reasoned selection of fabrication strategies aligned with project priorities and resource constraints.
The next phase of the evaluation involves a quantitative assessment of the torque requirements for bending steel rebars across varying diameters and comparing these theoretical values against the operational torque capabilities of the robotic arms available within the institutional laboratory.
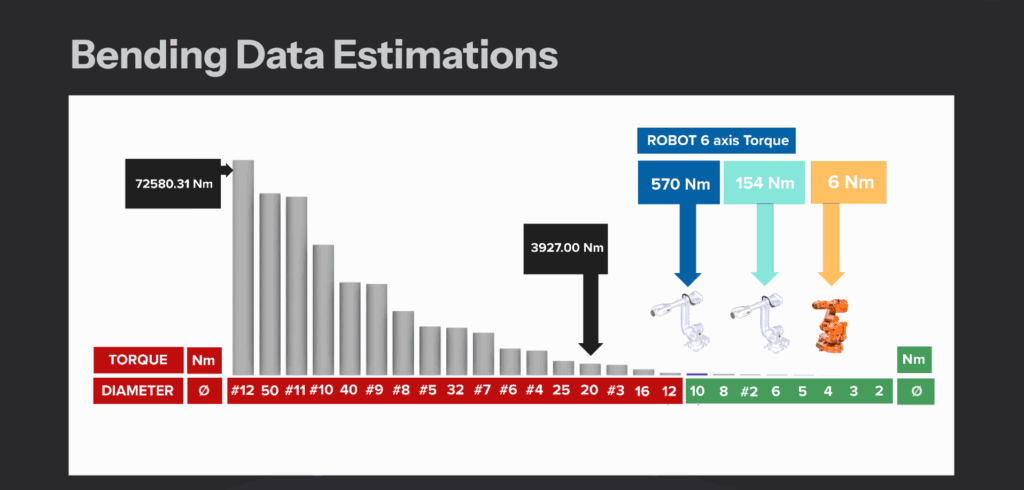
As visualized in the accompanying diagram, a series of vertical columns illustrates the estimated torque demand for different rebar sizes, with corresponding labels indicating both metric and U.S. standard classifications.
The red-highlighted torque range denotes values exceeding the operational limits of the current robotic infrastructure and is therefore excluded from further consideration. The focus is instead placed on rebars framed in green, signifying compatibility with the lab’s equipment. Among the available robotic systems, the ABB IRB 140 provides limited torque output, suitable only for lightweight, architecturally scaled operations. More robust performance is offered by the ABB IRB 6700–150/3.20, which delivers a maximum wrist torque of 570 Nm on axis 6, as specified in the manufacturer’s manual. An alternative model, the IRB 6700I–245/2.90, extends this capacity to 796 Nm, accommodating a wider range of diameters.
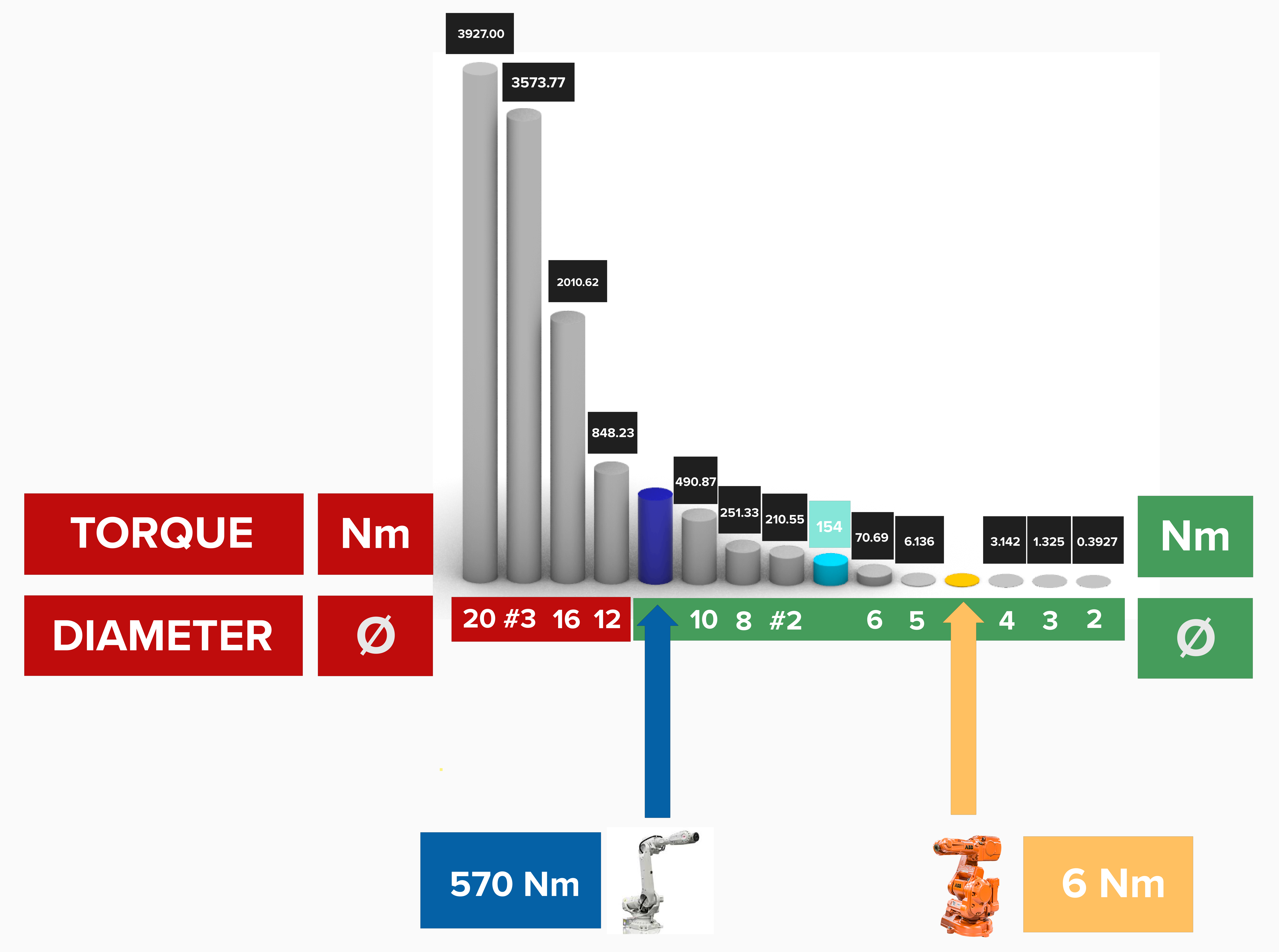
However, given that bending torque requirements increase exponentially with rebar diameter and that values begin to approach critical thresholds beyond 10 mm, it is both technically and operationally prudent to concentrate the investigation on 6 mm rebars, ensuring safety, repeatability, and system reliability during testing and prototyping.
Important Note : One of the ABB robotic arms with the highest torque on its 6th axis is the IRB 6600 series. Depending on the configuration, this robot can deliver wrist torques up to 1324 Nm, which is among the highest in ABB’s 6-axis industrial lineup.
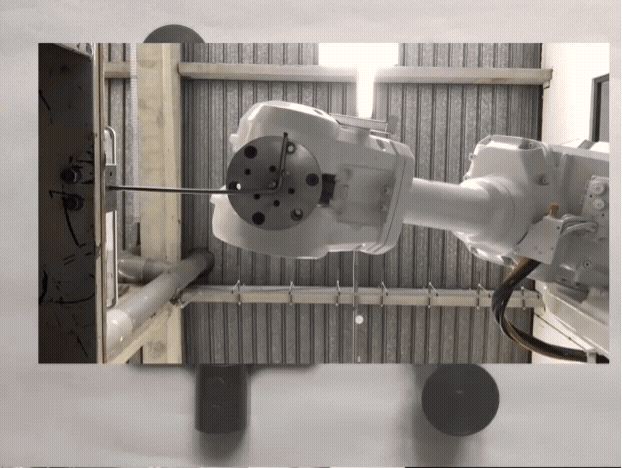
When it come to the State of the Art we nee to consider that contemporary systems integrate multi-axis robotic arms with custom end-effectors, real-time sensing, and algorithmic control to execute complex geometries with minimal human intervention. These technologies are increasingly embedded within digital workflows, allowing seamless transitions from parametric design to fabrication. Within this evolving landscape, Maria Smigielska’s contributions stand out for their fusion of computational intelligence and material expressiveness. Her Bendilicious platform exemplifies how robotic rod bending can transcend industrial repetition, offering a design language rooted in structural optimization and aesthetic nuance. By leveraging machine learning and feedback-driven toolpath generation, Smigielska has positioned robotic bending not merely as a fabrication technique, but as a generative process for architectural innovation.
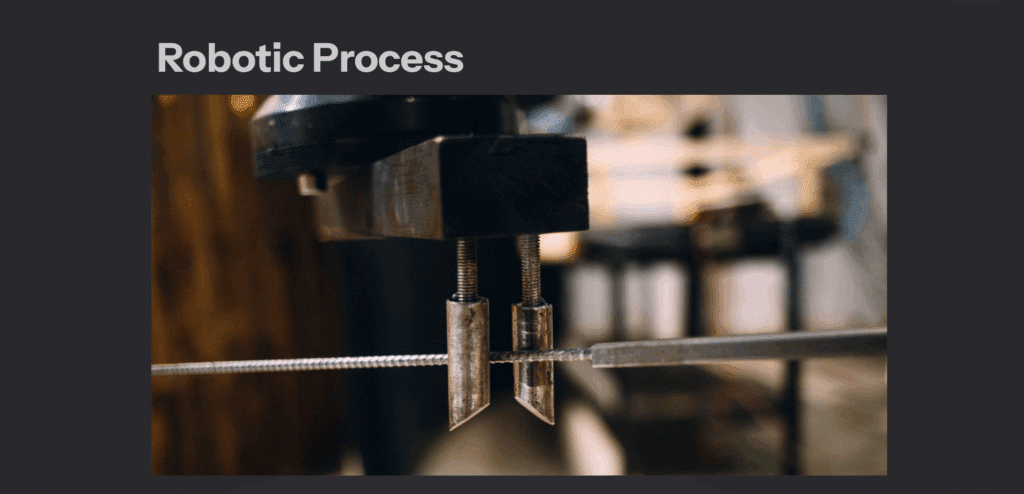
The analysis concludes that the development of a novel robotic system capable of horizontally bending rebars is essential. Such a system should prioritize mechanical efficiency, accommodate architectural-scale materials, and minimize cost through strategic design and accessible automation.
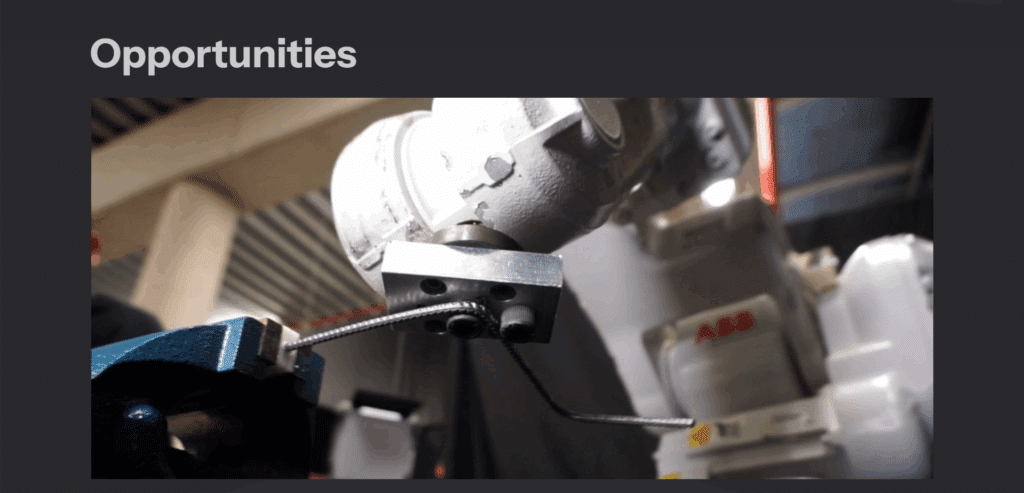
A robotic system capable of horizontally bending steel rebars unlocks new architectural potentials by enabling the precise fabrication of complex, non-standard geometries with greater material length and minimal spatial constraints. Its scalability and repeatability render it ideal for producing custom structural and ornamental elements that would be otherwise labor-intensive or cost-prohibitive using traditional methods. Moreover, such a system fosters seamless integration with parametric design tools, advancing mass customization and digital-to-physical continuity in architectural workflows.
Crucially, this robotic process presents a timely opportunity for application within the transformation of IAAC’s new campus. As the institute reimagines its spatial and constructive identity, implementing this technology offers a means of embedding robotic intelligence directly into the building’s physical interventions demonstrating IAAC’s commitment to innovation not only as an academic ethos but also as a material practice.
3. DESIGN
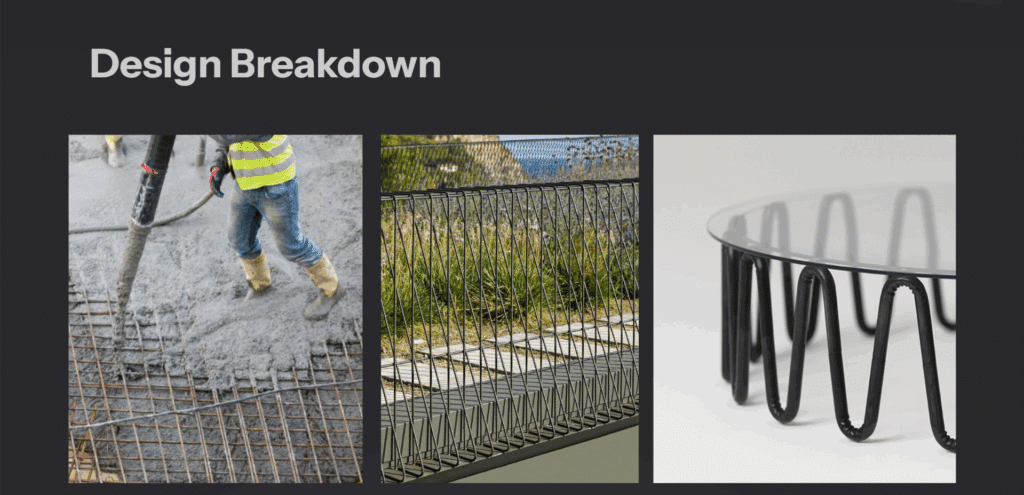
Rebars, while originally conceived for structural reinforcement in concrete systems, are increasingly being reimagined as active elements in architectural design. Their inherent strength, flexibility, and linear geometry make them ideal for a range of applications beyond structure. These include custom handrails, architectural screens, shading devices, and even decorative installations that contribute to spatial identity and expressive form.
Based on the identified technical constraints and fabrication potentials, it becomes essential to frame a research question that aligns the capabilities of robotic metal bending with a meaningful architectural application for the new IAAC campus.
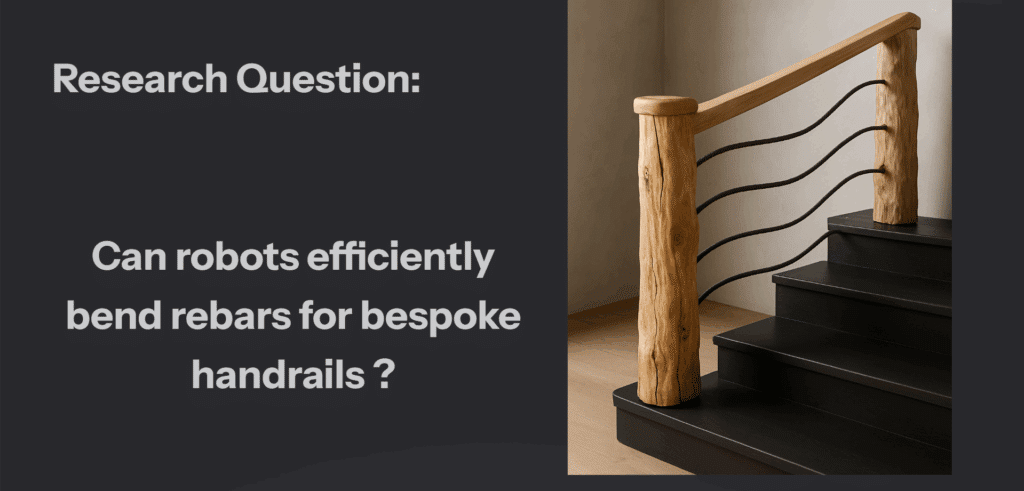
In the following image, we observe a series of balustrade design iterations showcasing handrail configurations in both horizontal and vertical orientations. These variations explore formal, spatial, and structural possibilities enabled through robotic metal bending, emphasizing how orientation affects curvature logic, attachment strategy, and overall aesthetic expression
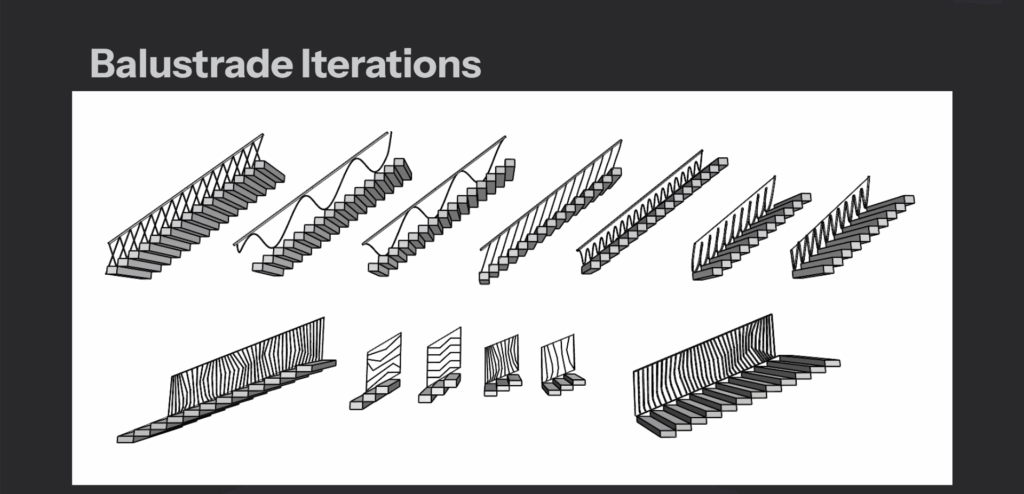
3. FABRICATION
Based on the prior assessment of the status quo and the formulation of targeted design applications, the next critical phase is the implementation strategy. Findings suggest the need for a robotic process consisting of a horizontally-oriented feeder for material stabilization and an end effector capable of bending 6 mm rebars using two metallic dowels. Several implementation pathways were explored, including modular, 3D-printed feeder inserts tailored to different diameters, and a simplified end-effector calibrated for 6 mm-20mm rods.
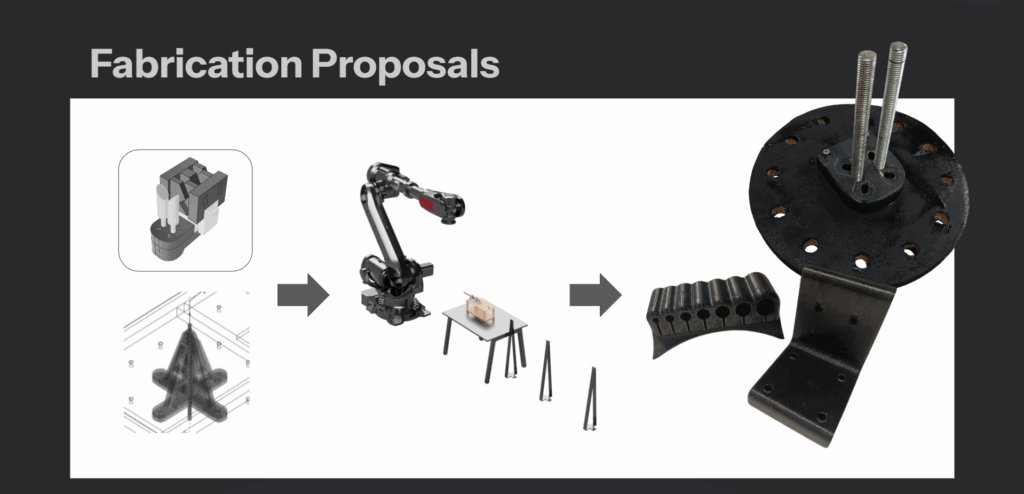
The conceptual rendering presented showcases potential tool configurations that support this setup. In alignment with Occam’s razor, the most efficient solution proved to be the simplest: a functional prototype employing just a clamp and two threaded steel rods mounted on a wooden flange though a metallic end effector, potentially fabricated from aluminum to reduce base weight, is recommended for improved durability and precision. Due to lab constraints, an adapted version of an end effector & feeder, originally designed by Lauren Deming was utilized, modified to exclude the gripper mechanism, as evident in the accompanying image.
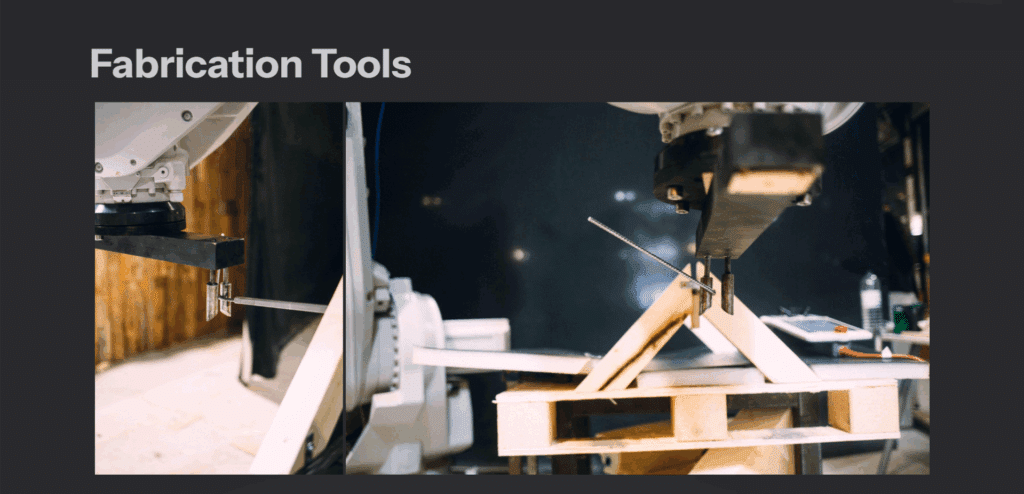
The 1:1 prototype demonstrates a system of horizontally aligned, wave-like balustrades composed of 6 mm rebars. These elements follow an iterative logic of curvature and spacing, producing varied yet controlled formal outcomes.
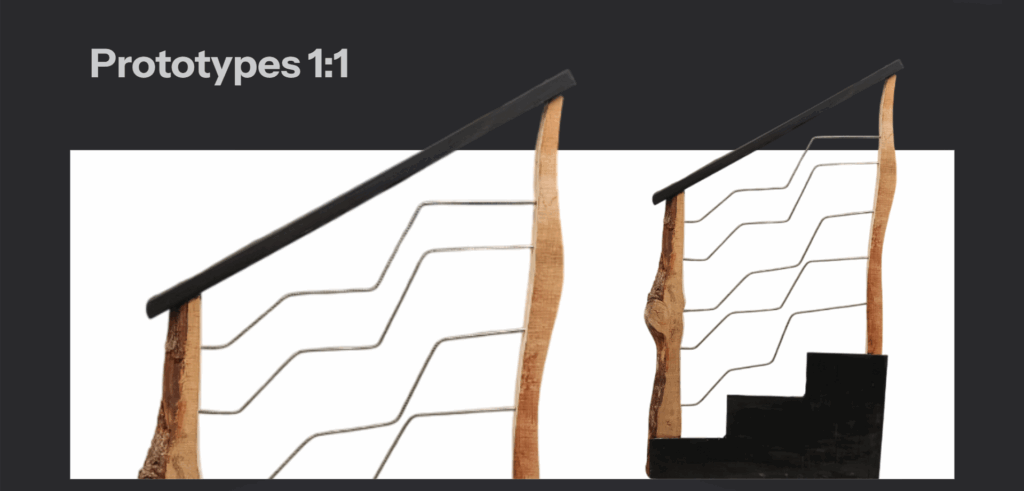
The following image illustrates a potential spatial integration of the fabricated handrail within the future IAAC campus environment.
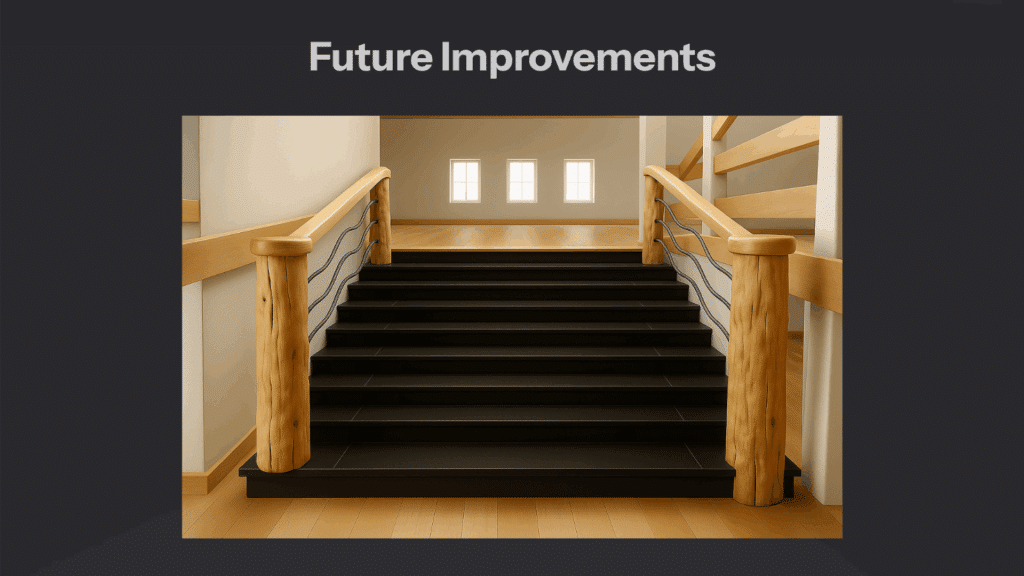
Future improvements may focus on the integration of interchangeable dowel modules to accommodate a broader range of diameters, dynamic torque feedback for real-time adjustment during bending, and optimization of feeder geometry to support longer rod lengths while maintaining alignment accuracy. Furthermore, the incorporation of lightweight, durable materials such as composites for the end effector could enhance both maneuverability and mechanical resilience.
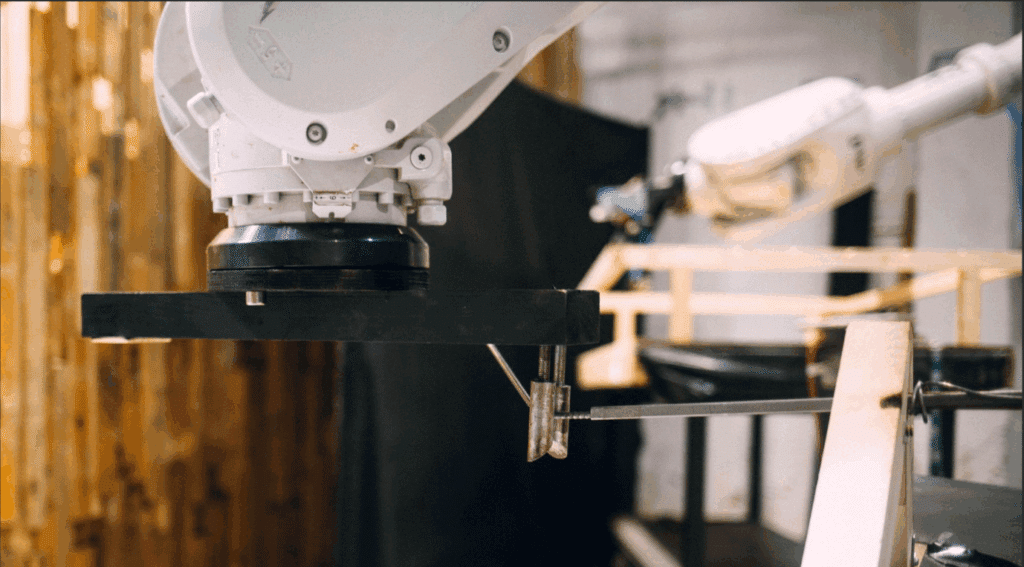