Objective.
The primary focus of the project is to foster a sense of curiosity about the robotic arm and its ability to manipulate various sustainable construction materials through different processes. Teams are encouraged to apply their newly acquired hardware and software skills, alongside the robotic tools and equipment available in the robotic lab, to explore ways of creating and shaping materials.
- Develop scientific approach to material manipulation
- Explore material plasticity
- Research material specificities
- Design custom made tools
- Develop knowledge of usage of ready to use tools
Deliverables.
In addition to the four to eight prototypes each demonstrating different materials, tools or processes, video documentation and graphic diagram of the robotic process are required for presentation. Analysis of the various materials´ relevance via physical qualities, carbon footprint, and cost in the form of a ¨specifation sheet¨ was conducted. Ultimately, a speculatation on the utility and potential applications of these techniques, materials, and tools was encouraged.
Materials.
The materials must meet specific criteria: sustainability (low carbon footprint, local availability, and low embodied energy), compatibility with the available tools, and affordability. The prototypes can be made from a single material or material hybrids. Through manipulation of the materials, teams are able to better understand their physical properties– plasticity, elasticity, viscocity, etc.
Initial experiments included combination of organic aggregates and binders in the hopes to create an extrudable material for 3D printing. Biomaterials such as coffee, eggshells, nuts hulls, flour clay, and sawdust were compbined with cornstarch and glycerine.
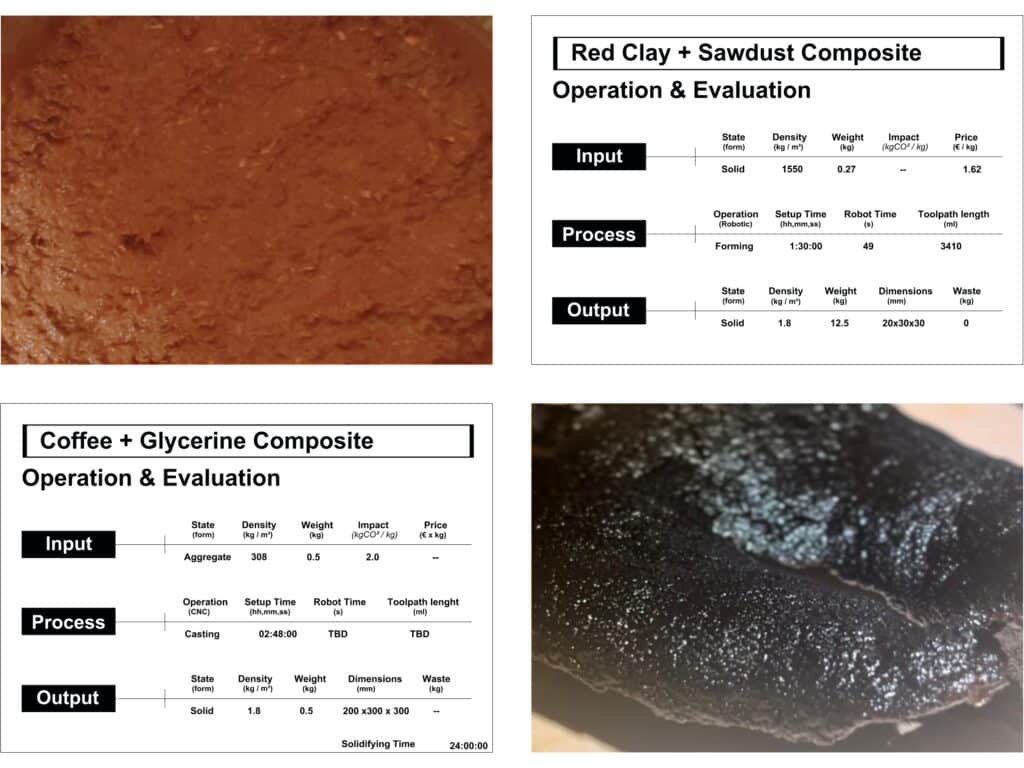
While crystalline wax and sodium trihydrate acetate are not traditional buillding materials, their physically properties (liquid to solid transformation) made for interesting experimentation in creating potentially extrudable material for a robot to manipulate.
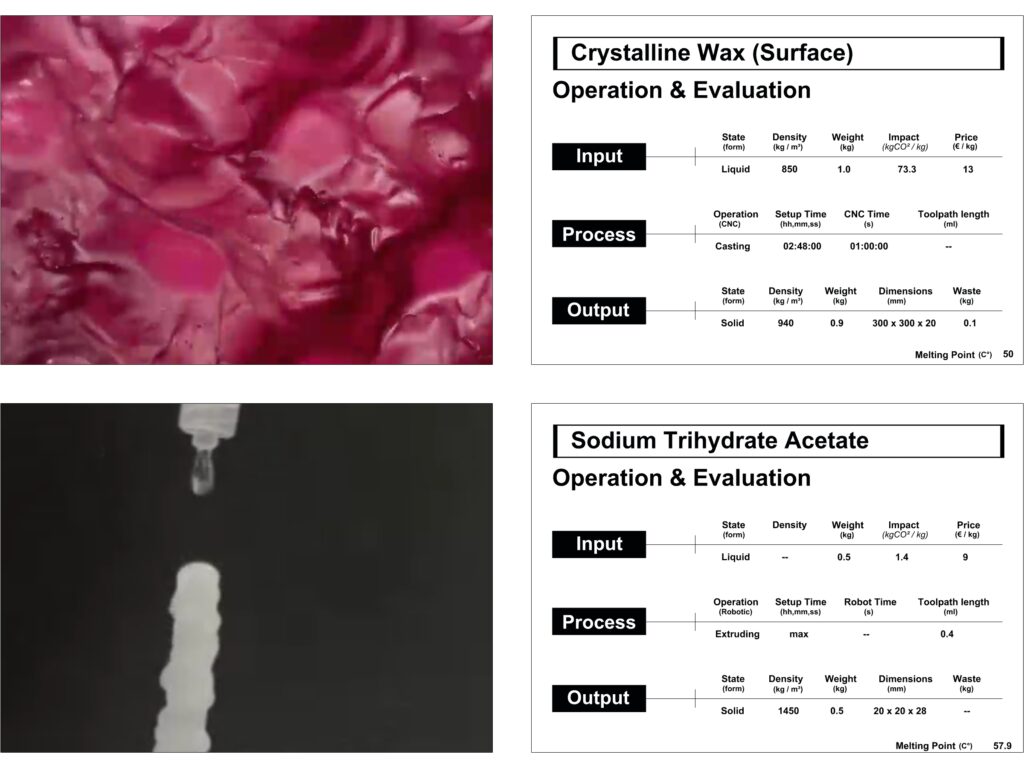
In addition to robotic process, these materials required extended drying times or heating processes to create a solid shape. Given the limitations on time and heating elements, the biomaterial composites and non-traditional materials were abandoned for more traditional construction materials.
Two such widely embraced materials were plaster and clay, each manipulatable with reasonable air drying times made for ideal prototype creations.
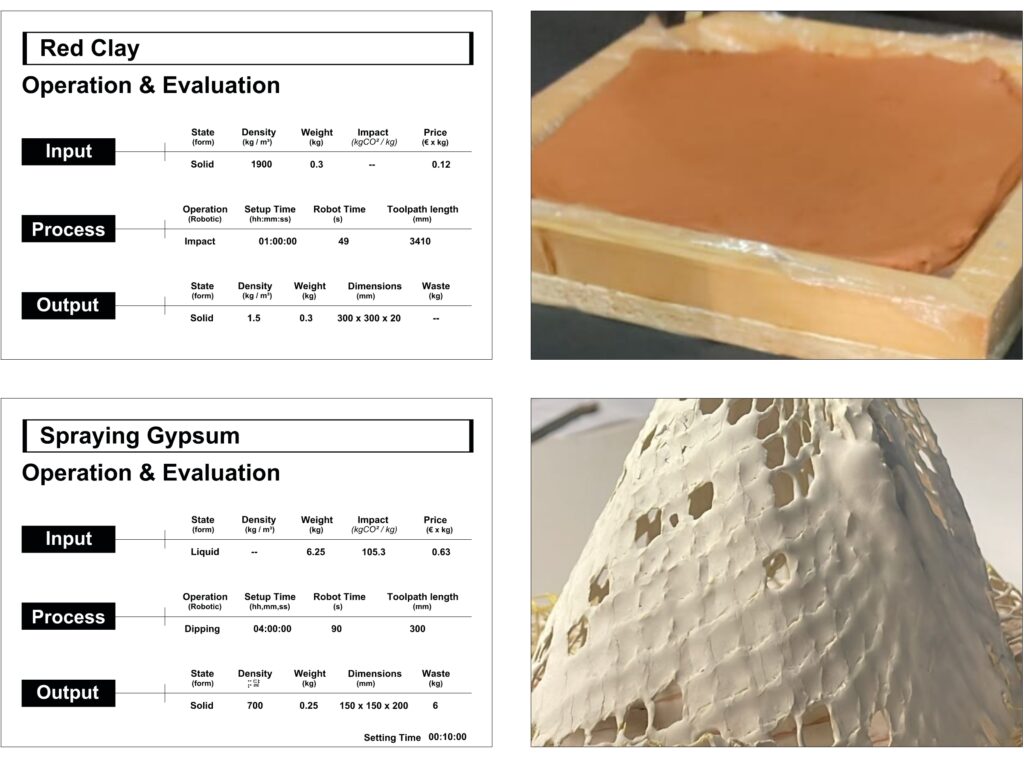
Inspired by a recent robotic weaving exercise, a final robotic process involving the manipulation of jute, a solid, organic twine, was then employed to ensure a diversity in processes.
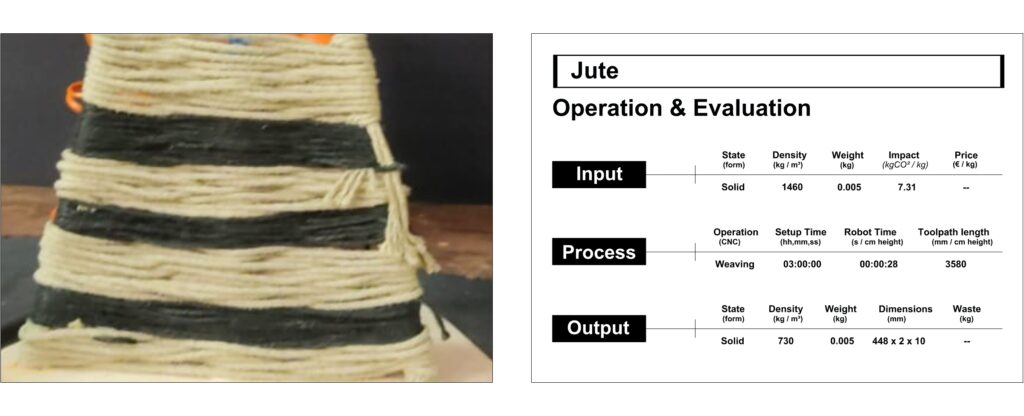
Tools Utilized and Created.
Initially, materials were manipulated by hand to see what accomodations may be necessary for a robotic arm to mimic the motions. Teams were encouraged to utilize existing robotic tools (or end effectors, such as extruders, grippers, and spindles) or to modify / build their own to ensure a diverse manipulation of the materials´physical properties. With just days between each experiment, playful improvisation turned processes with porous sponge-like tools to double-bladed knives. Careful consideration for relationships between the material bed, the material, and the tool center point (TCP) became integral to the seeming success or failure of each prototype. Plasticity and tactility of the array of the materials made each interation between robot and material changed the parameters and required careful consideration for speed and direction of the toolpath for each process.
Processes.
01. Stamp.
End effector: Impact Printer + custom CNC stamp
Material: Red Clay
Inspired by the process of stamped concrete, the first process creates a repetitive task with the efficiency and precision adventageous in robotics. The tool, a stamp, was created by parametric design and carved via CNC to ensure observable variety of impression dependant on the maleability or viscocity of the material´s surface.
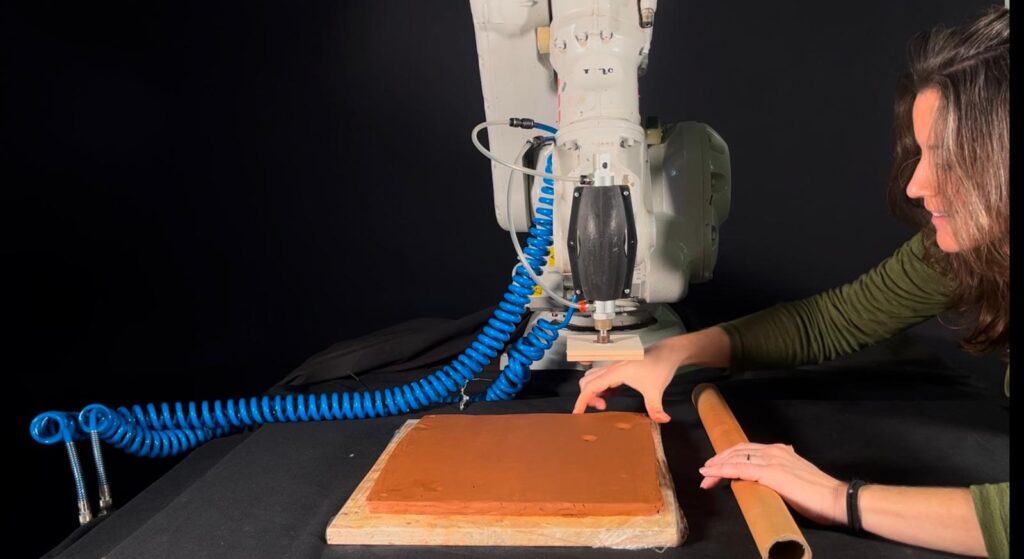
Variables such as pressure, time, and stamp texture were adjusted to optimize results.
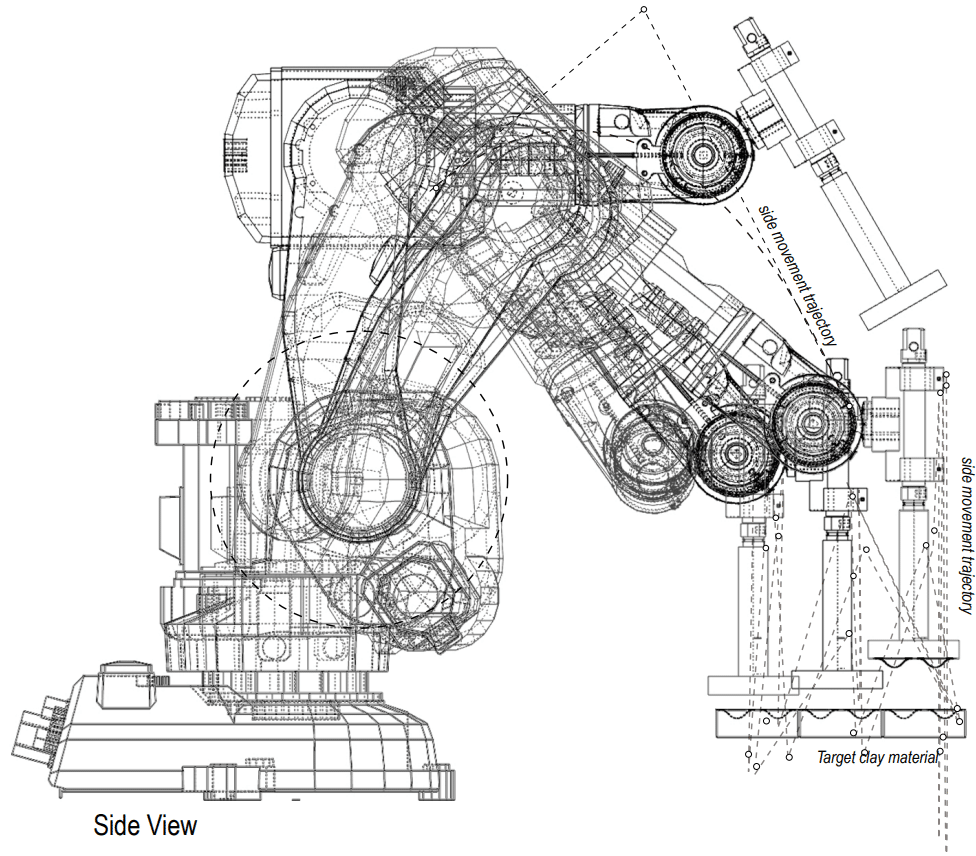
02. Lick.
End Effectors: sponge brush, wire armature and sponge, wooden knives.
Materials: clay + water, clay + glycerine + sawdust + water composite.
Once a predictable outcome was acheived, the team moved toward more complex toolpaths utilizing more of the range of motion of the robot´s six axes.
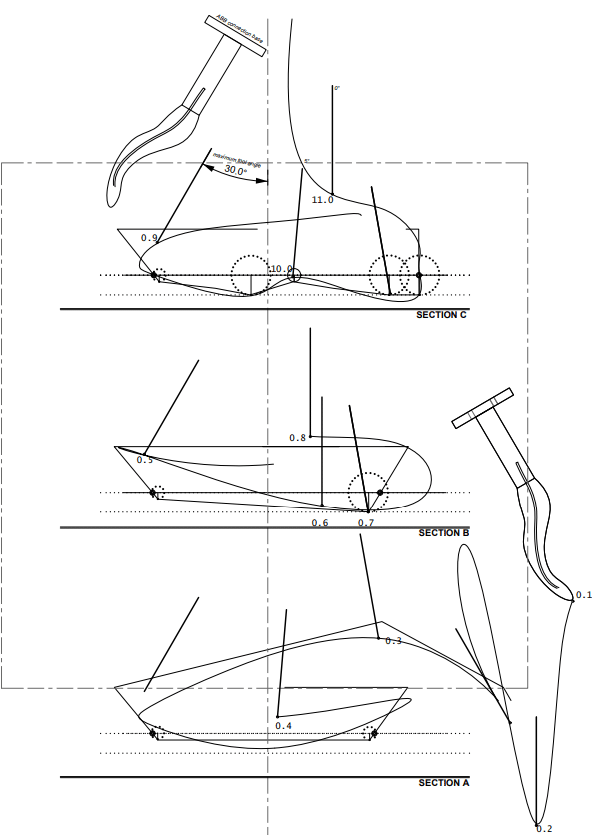
The ¨lick¨process creates a more organic or ¨human-like¨ motion of manipulating a surface (as if it were being licked by a tongue). The end effector, made with a wire armature and sponge-like elasticity, allowed gave rise to a smoothing quality on an otherwise porous and course wet surface, a glycerine, clay and sawdust composite. The motion of the tool made a sweeping directional motion across the surface with x-axis deviation swinging from -30 degrees to +30 degrees. A dipping well (to moisten the tool) was later added to the toolpath and gave rise to more observable manipulation of the surface.
03. Dip.
End effector: impact printer + (weighted) mesh form.
Material: Wax, spray plaster.
Inspired the catenary curve chain models on display at Gaudi´s Sagrada Familia and the repetitive process of candle stick forming, this process adapts the toolpath and impact printing tool initially used for the ¨stamp¨process to create a timed dip + dry process. Due to the solidifying rate of crystalline wax, an electric stove would have been required to keep the material consistently liquid enough for the robotic manipulation, so plaster was utlized for the sake of the robotic experiment. At first attempt, the drying time of the material proved faster than necessary to allow the robot to properly manipulate the material. As a result the material quickly took the catenary form without repetition. Ultimately, the shape formed was dramatic but no greater as a result of robotic automation.
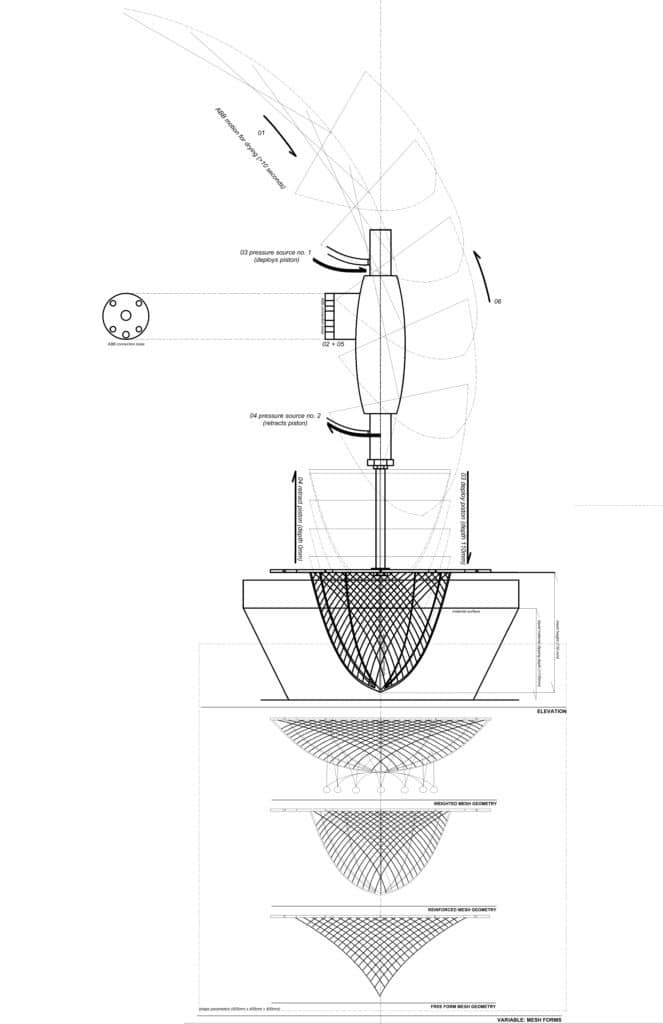
04. Weave.
Finally, the team abandoned the concept of state-changing materials and moved toward simpler materials and even more complex toolpaths. The final process, required the robot to agily wind its was around a peg board with jute to create a vertical weave. While the robotic motion was repetitive, each layers of jute increased the tension on the peg members ultimately distorting them from their original vertical configuration.
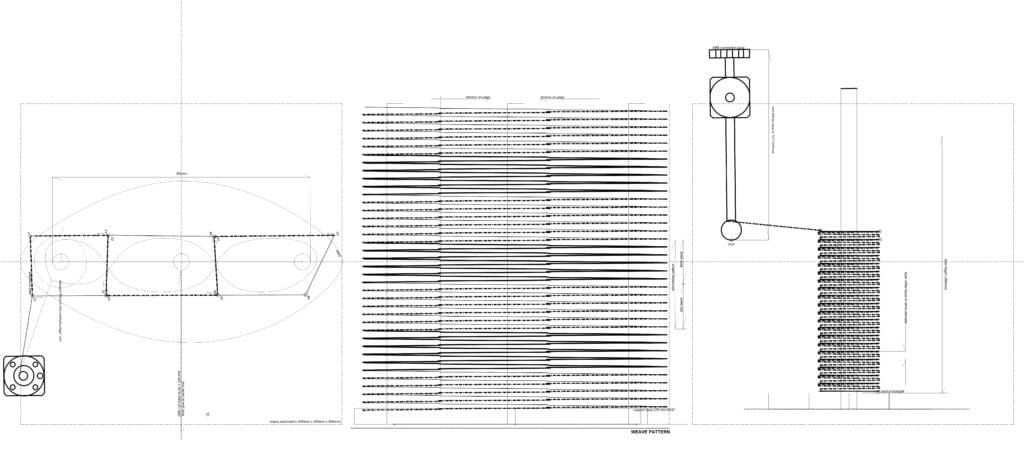
Conclusion.
The project successfully demonstrated the potential of robotic systems in the manipulation of both traditional and experimental sustainable materials. Although initial experiments with biomaterials and non-traditional materials posed challenges, the team adapted by focusing on materials with more manageable properties for robotic manipulation. The processes explored—stamp, lick, dip, and weave—showcased the robot’s ability to perform complex, precision-based tasks, demonstrating that robotics can contribute to the development of sustainable construction materials. However, the project also highlighted the importance of carefully considering material properties, tool capabilities, and process limitations to achieve successful outcomes. Moving forward, further refinement of both the materials and tools would be necessary for optimizing robotic manipulation in sustainable construction applications.