
ArtNest stands as a versatile pavilion, conceived to serve as a dynamic exhibition space for a variety of art installations. Purposefully crafted to blend functionality with aesthetic allure, ArtNest redefines the pavilion typology by providing a flexible framework that adapts to diverse artistic needs.
The architecture of ArtNest illustrates the compelling synergy between traditional design principles and cutting-edge digital fabrication. Through the precise integration of CNC milling, laser cutting, and 3D printing, the pavilion’s structure embodies a refined yet practical aesthetic, carefully calibrated to maintain visual harmony while supporting its various functions. These digital techniques allow for an innovative assembly of materials and forms, enabling intricate detailing and structural coherence that would be difficult, if not impossible, to achieve with conventional methods alone.
CNC – Milling :
Reference :
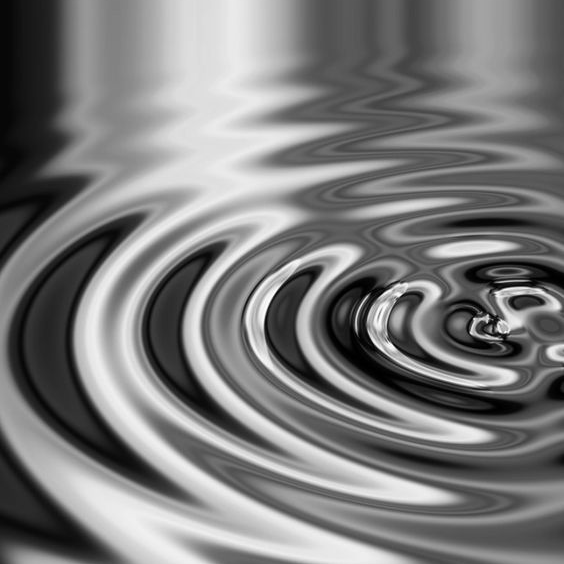
The design concept is inspired by the rhythmic patterns generated by waves on water, translating this natural phenomenon into an architectural language of flowing, interconnected elements. The structure is organized into three distinct layers that mimic the undulating movement and layered depth of water waves: a primary framework of “wave crests” forming the structural backbone, secondary “trough” elements that interlock with the primary frame, and a flexible, folded “surface skin” that spans across the form, creating a fluid, cohesive envelope. This layered approach captures the dynamic interplay of stability and motion, mirroring how waves shape and support each other in continuous motion.
3D Model :
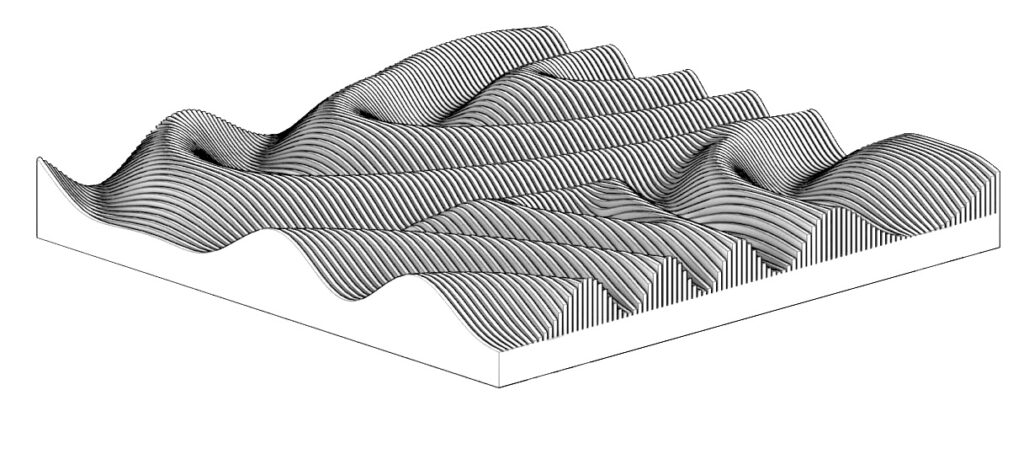
The wall pattern is conceived as a fluid, wave-inspired design that adds layers of sensory and visual depth to the space. Wave-like grooves run along its surface, capturing and channeling light to produce dynamic shadows that shift with the viewer’s perspective, enlivening the wall with a subtle, ever-changing play of light and dark.
The organic curves within the pattern also serve a functional purpose, improving the acoustics by dispersing sound evenly across the space. This reduction of echoes creates a more immersive and intimate environment, enhancing the auditory experience of the pavilion.
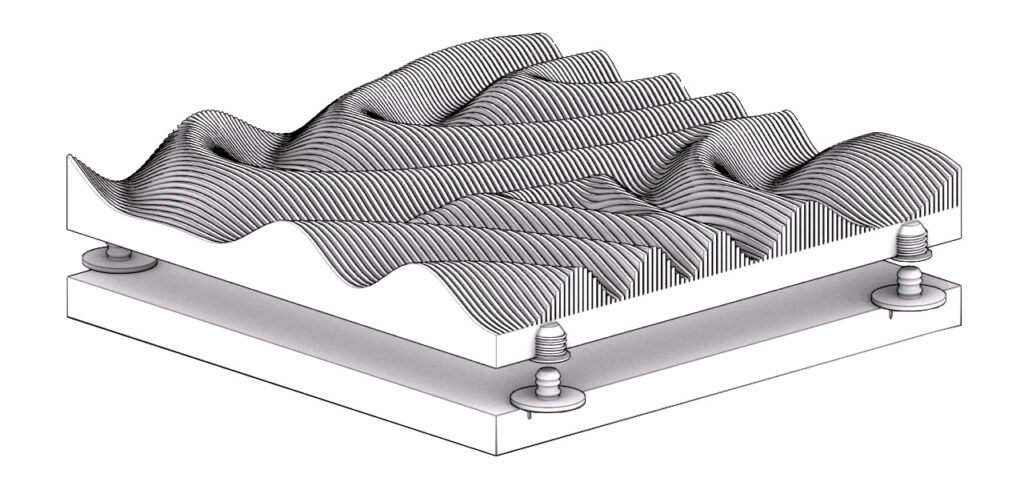
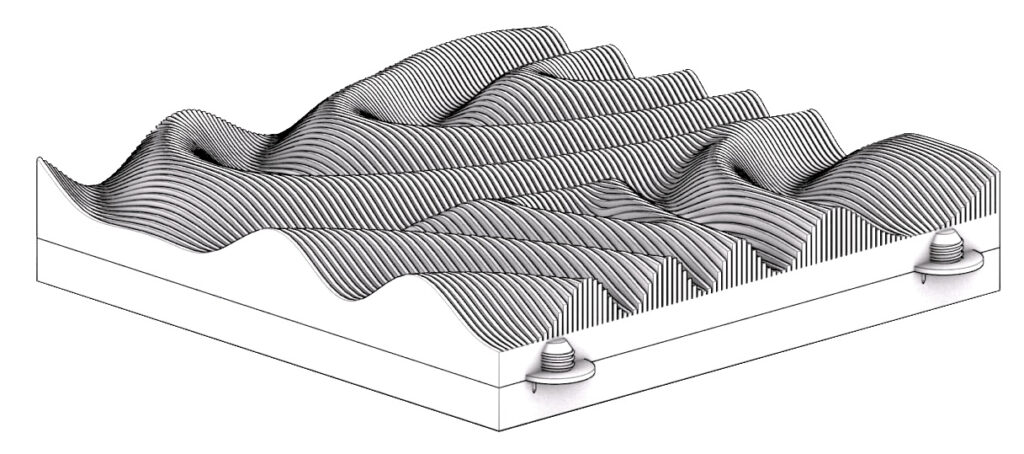
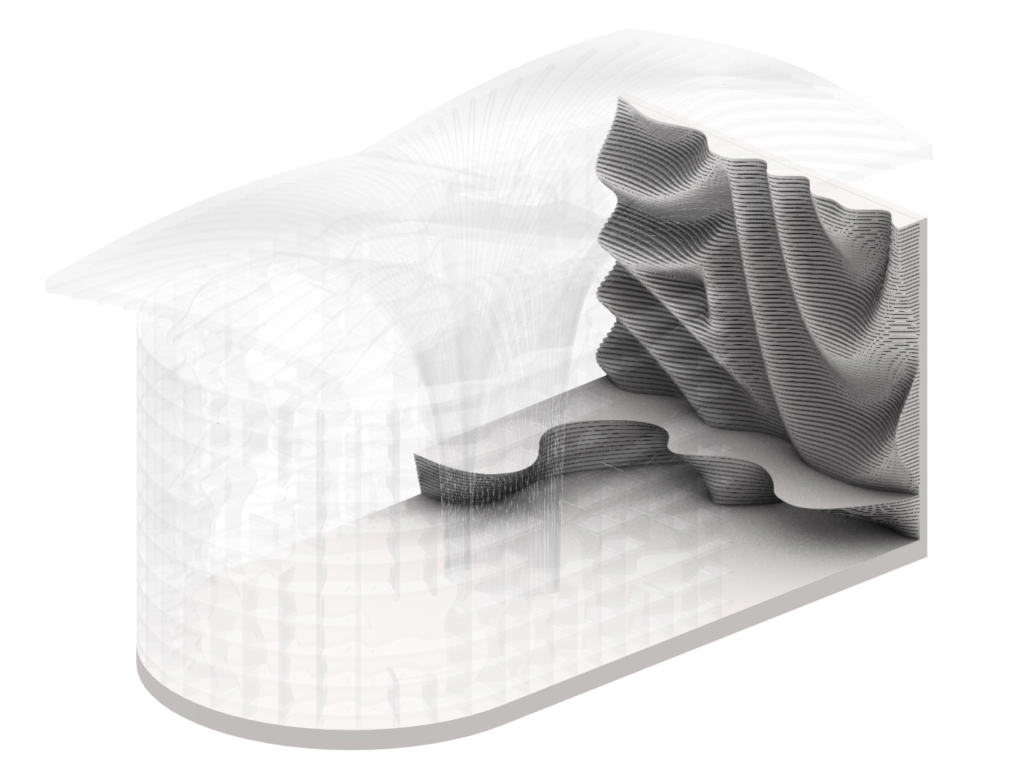
With the Fastmount system, we have used clips to securely attach the panels to the cabin frame, allowing easy installation and removal for a seamless appearance. The image shows this mounting solution in action, illustrating panel attachment.
Fabrication Strategy :
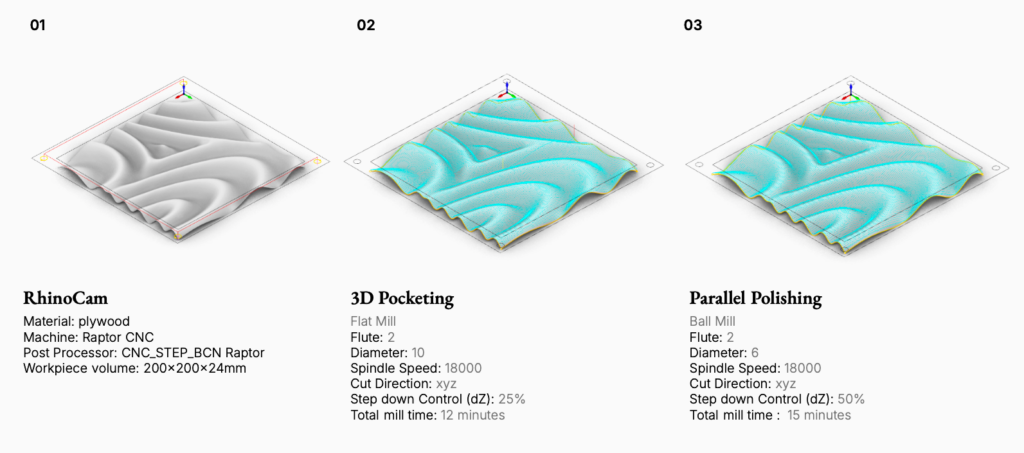
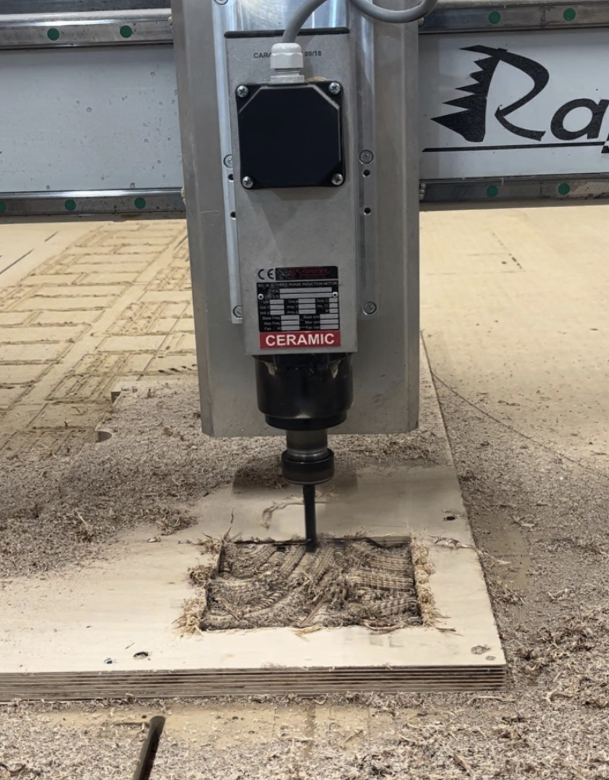
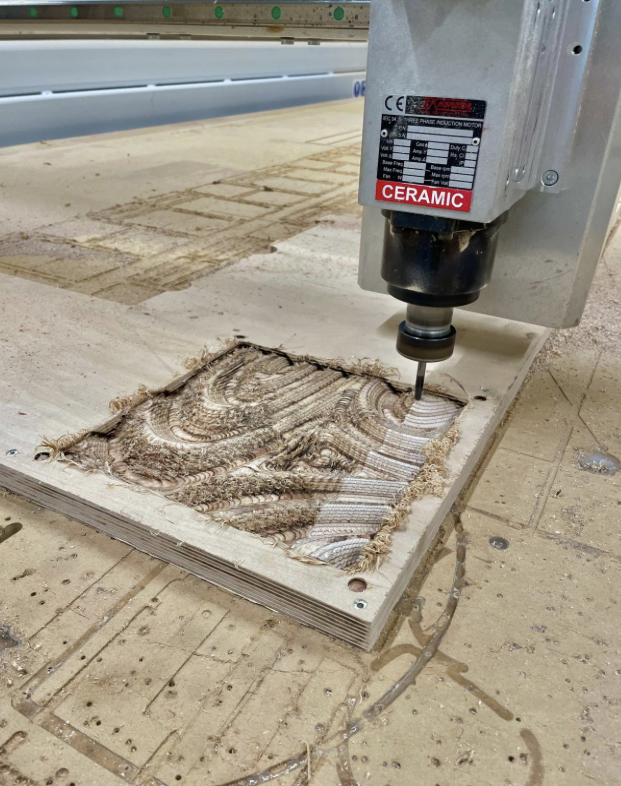
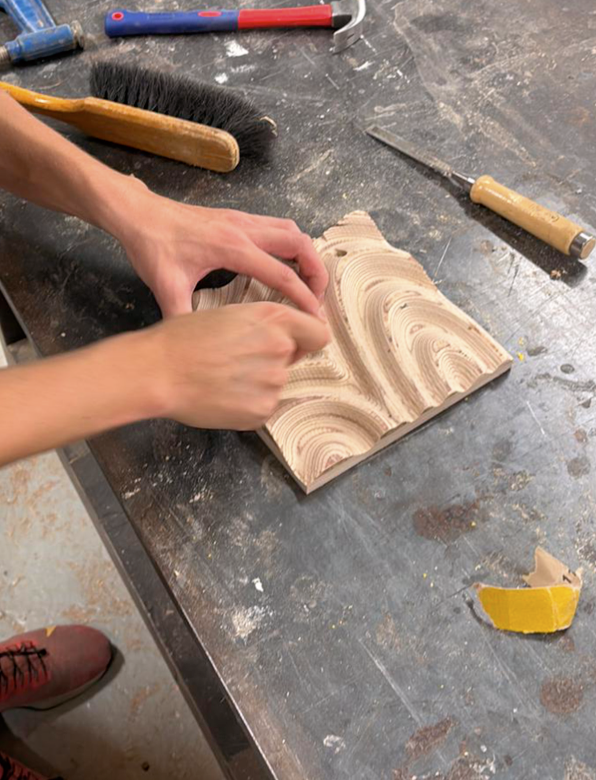
Final Prototype :
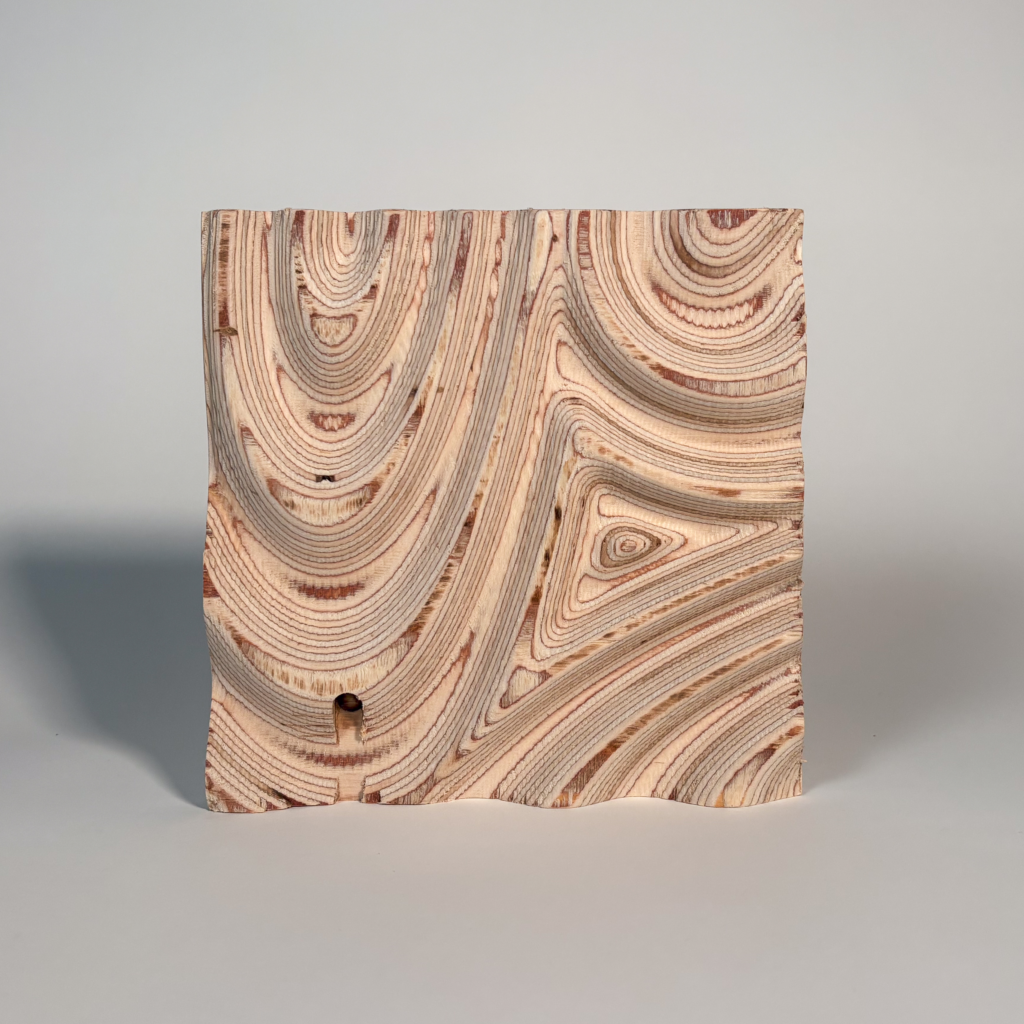
For the final production, we’ve chosen 24mm plywood. It allows us to vary the tones thanks to the multiple layers that make up this material. It gives dynamism to the prototypes and accentuates the curves.
Render image :
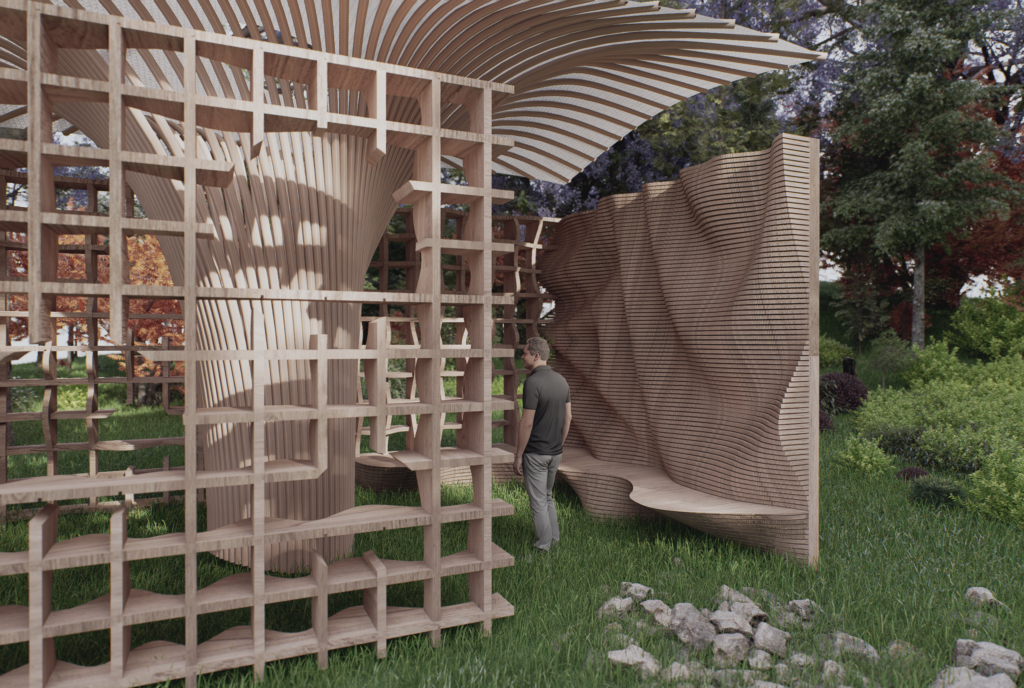
Laser – Cutting :
Reference :
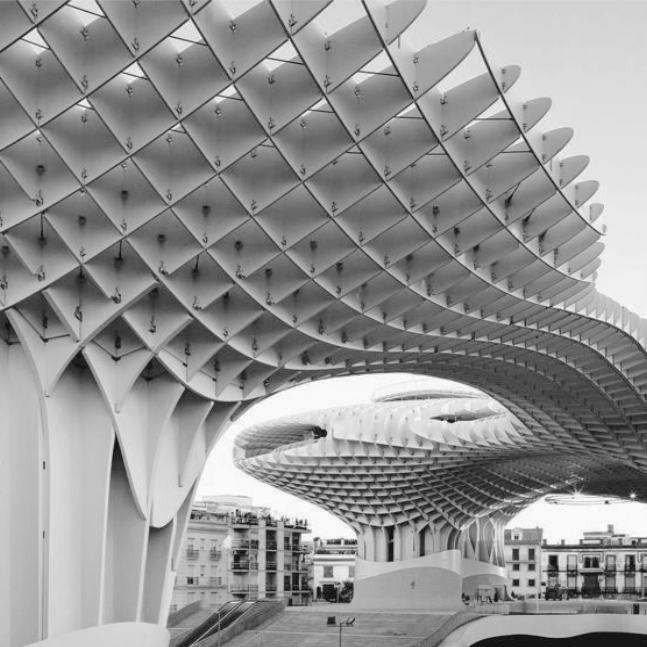
The design concept for this technology takes inspiration from the distinctive waffle pattern, a lattice structure where intersecting elements form a cohesive, load-bearing grid. This pattern is elegantly exemplified by the parasol structure in Seville, known for its expansive, open-air canopy that provides both shade and visual intrigue. The structure is arranged with panels that intersect at regular intervals, creating a continuous series of square apertures. Each panel within this grid serves a dual purpose: providing structural stability while allowing light and air to permeate the space below.
Conception :
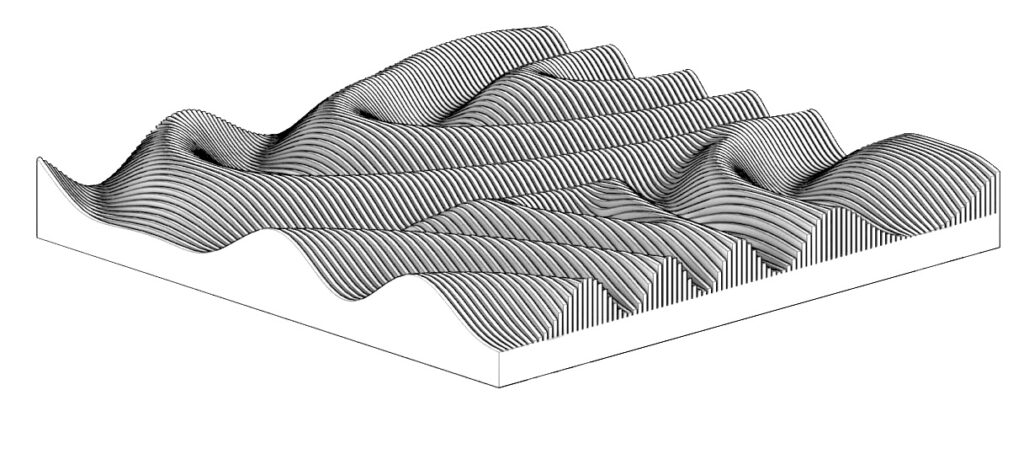
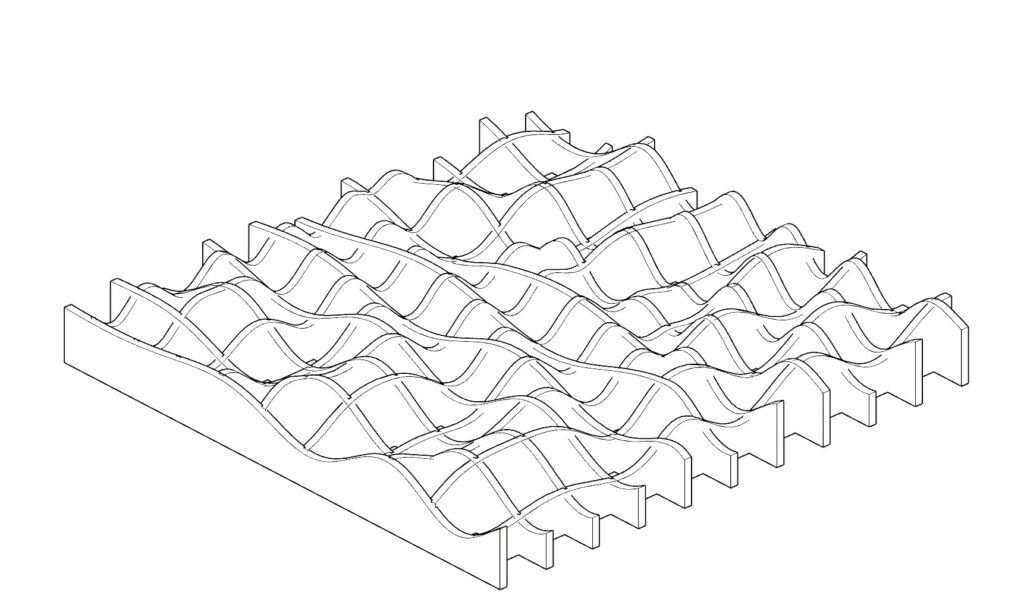
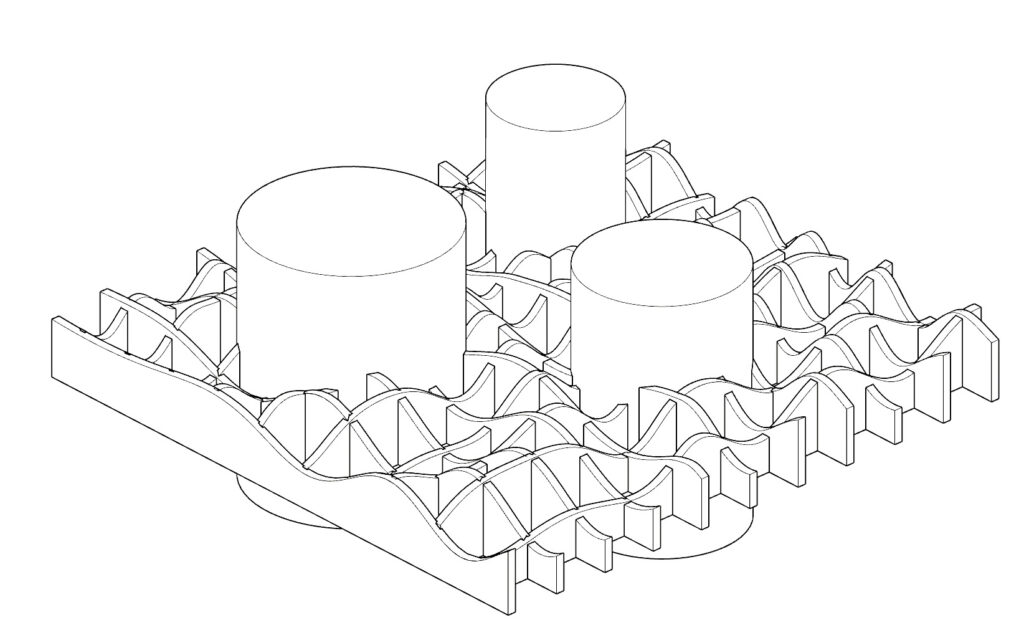
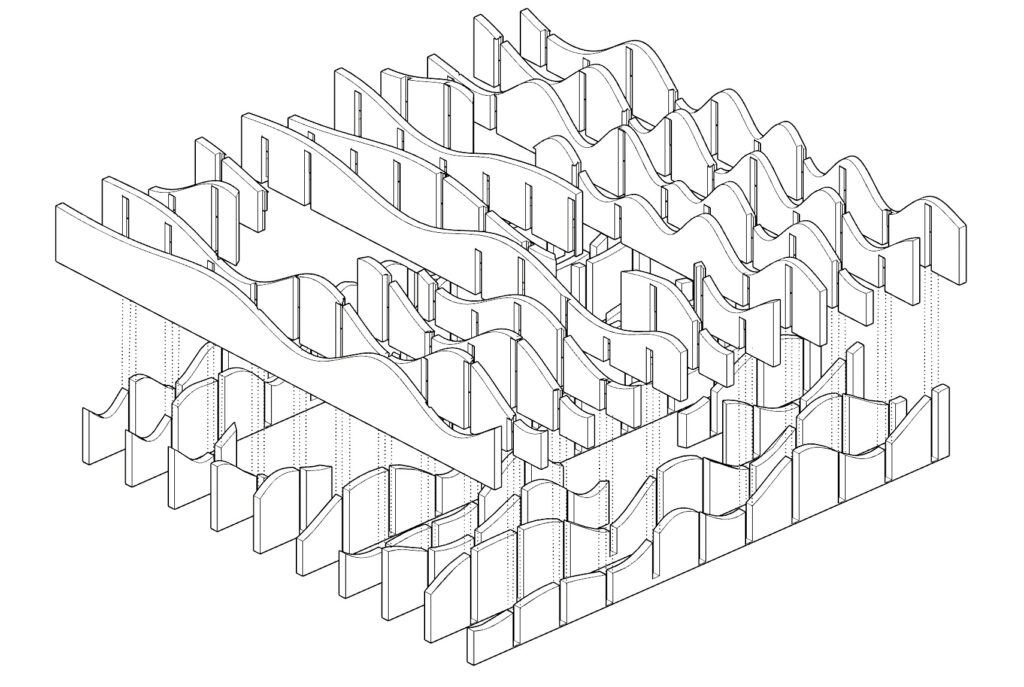
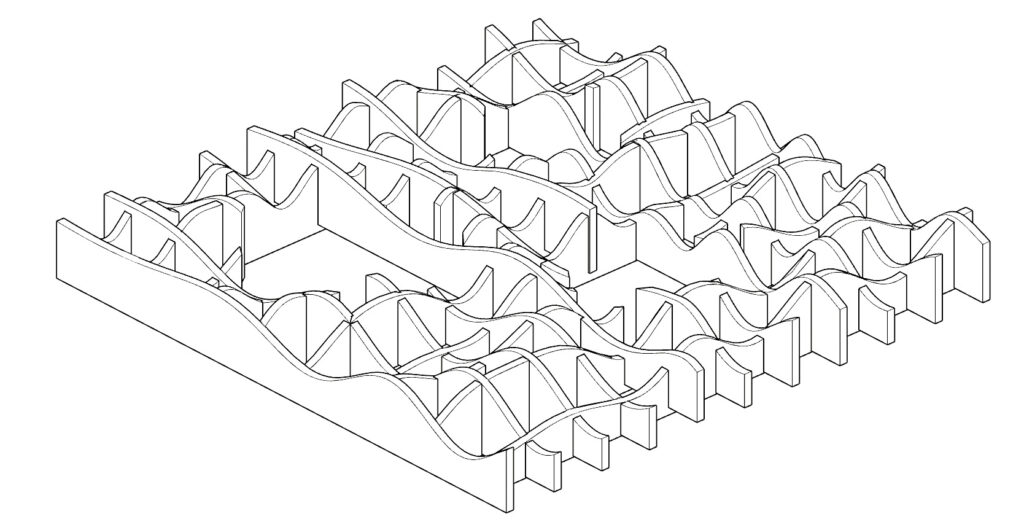
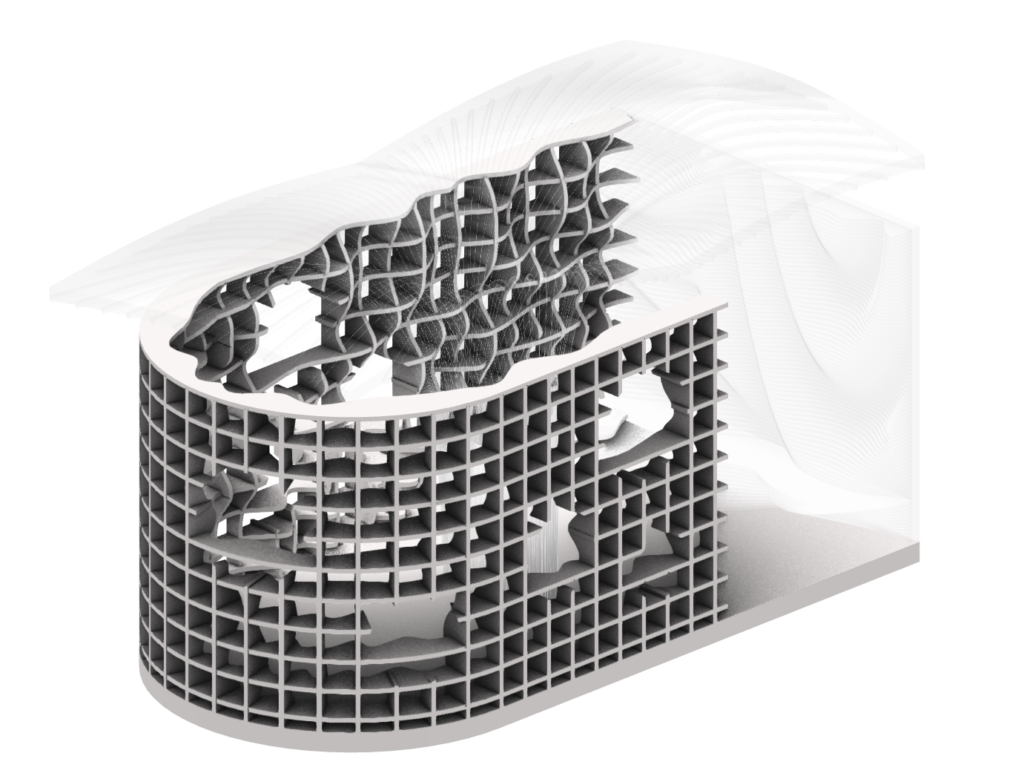
For the design of the prototype, we started from our first prototype’s morphology. Then we divided with computational software and try to make this geometry evolving through different parameter.
The structure is composed of interlocking panels arranged in a grid, forming a series of waffle-like, wave-shaped patterns. The technical drawing illustrates how these layers stack and connect to create a stable yet visually lightweight facade. Circular openings of varying sizes are incorporated into the design, providing niches for displaying art pieces of different scales. This geometry was selected to harmonize with the wave-like walls and the pavilion’s overall pattern.
Fabrication Strategy :
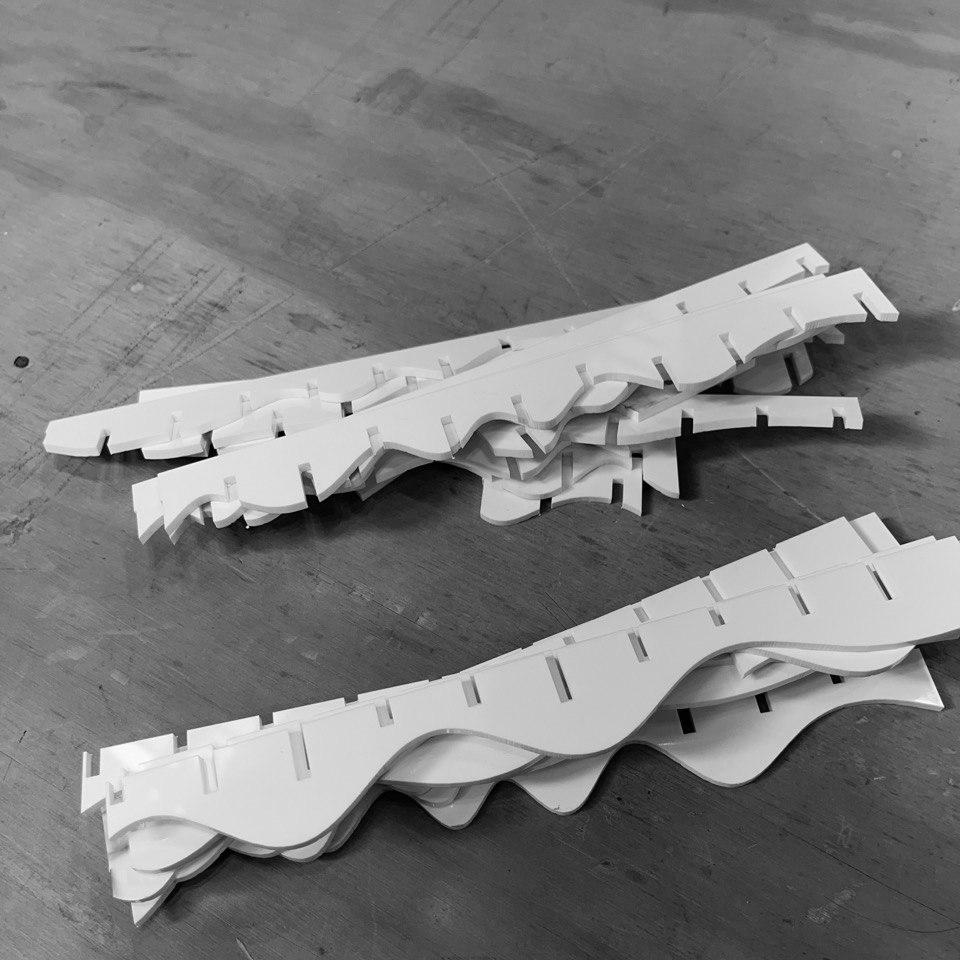
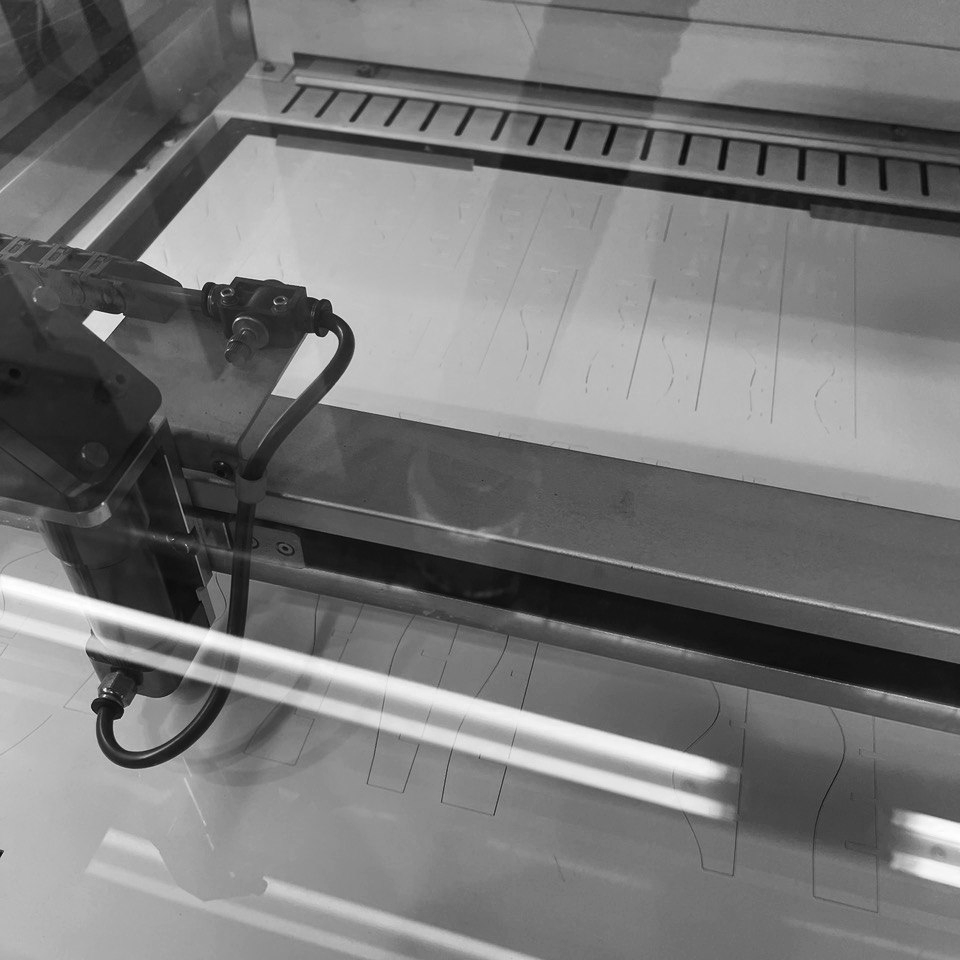
Tool: Rayjet 500 Laser Cutter
Material Type: acrylic
Thickness: 3 mm
Description: a transparent plastic material with outstanding strength stiffness and optical clarity
Properties:
– Tough
– Lightweight
– Heat Resistant
Laser Cutting Parameters:
– Speed: 1.4
– Power: 55
Time:
– 15 mins
Final Prototype :

Render Image :
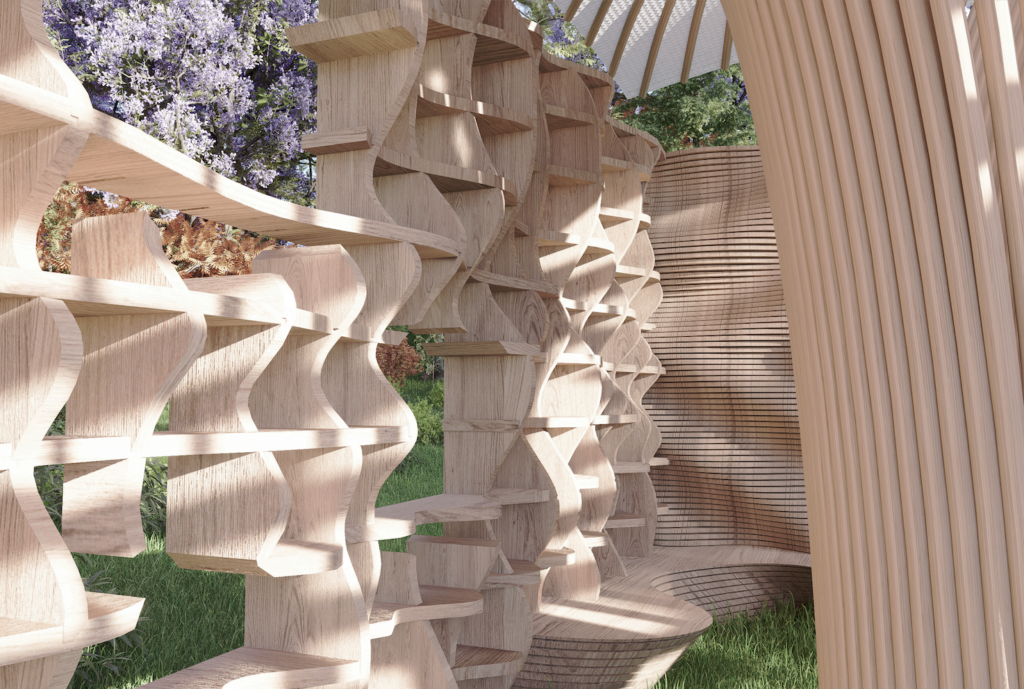
3D Printing :
Reference :
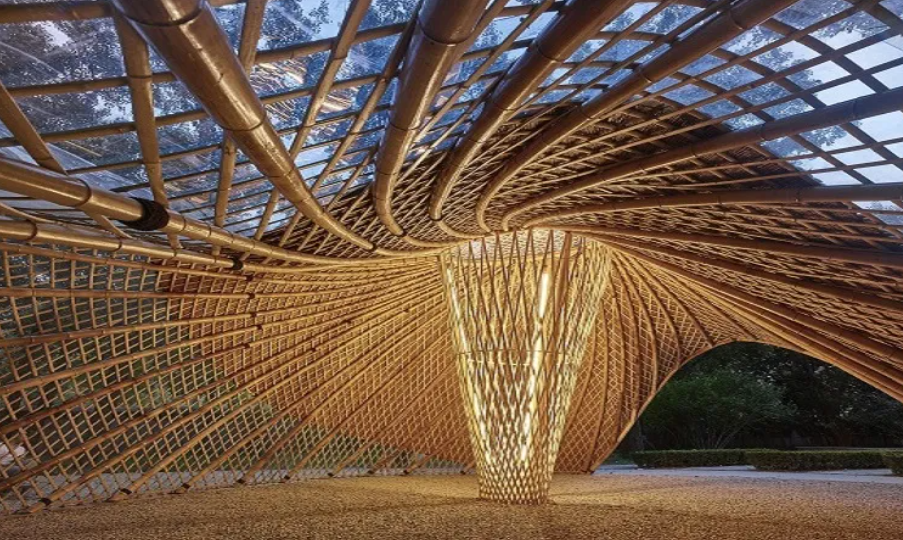
The central column, constructed from bamboo and anchored with a 3D-printed floor connector, provides essential structural support for the roof. The bamboo column serves as a visual focal point, embodying the harmony between organic materials and contemporary fabrication techniques
Conception :
Side view of how bamboo columns are combining each to carry the roof structure
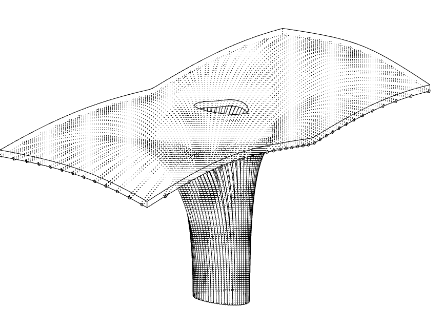
Final form of the roof
Joining elements for each bamboo column using 3d printing
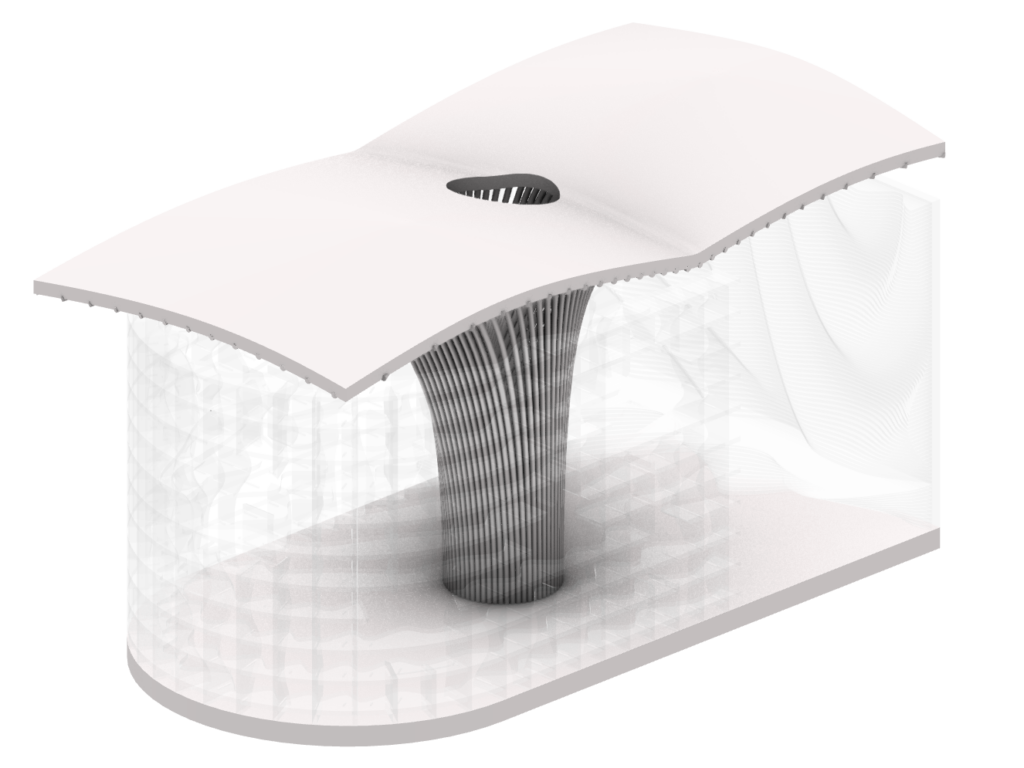
3d model
- Harmony with Nature: Using a sustainable material like bamboo makes the structure eco-friendly and respectful of natural resources. This approach represents an architectural philosophy that aligns with nature and supports ecological balance.
- Biophilic Design: Natural materials and organic forms allow the structure to harmonize with its surroundings, providing a peaceful space for users. This approach aims to enhance the connection between humans and nature
- Centralized Structural Stability: The roof structure, rising from a single central column, brings minimalistic and graceful strength to the building through a central load-bearing principle. This design focuses on using materials efficiently to achieve a lightweight yet durable structure.
Fabrication Strategy :
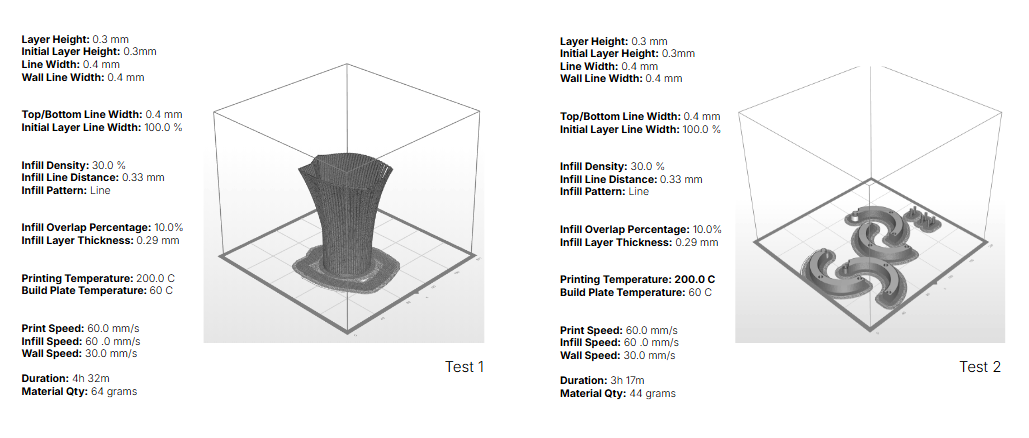
Divided roof part finished joint element with raft changing the strategy
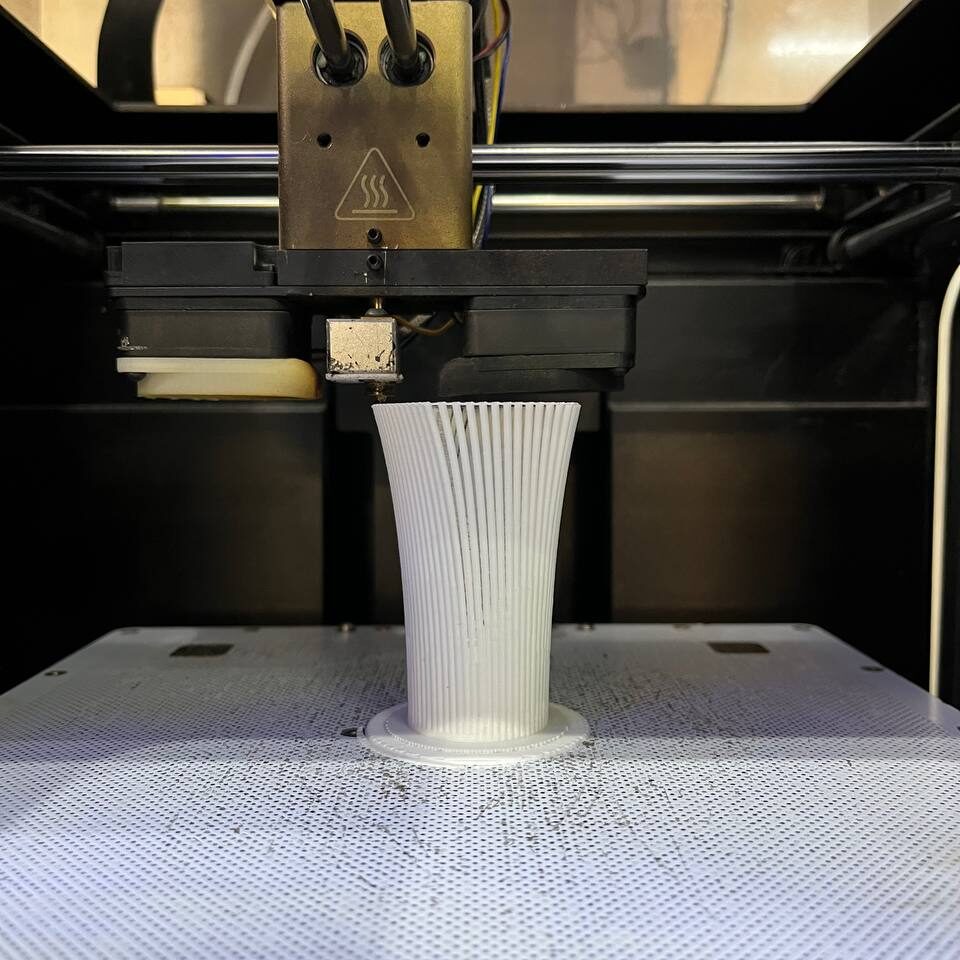
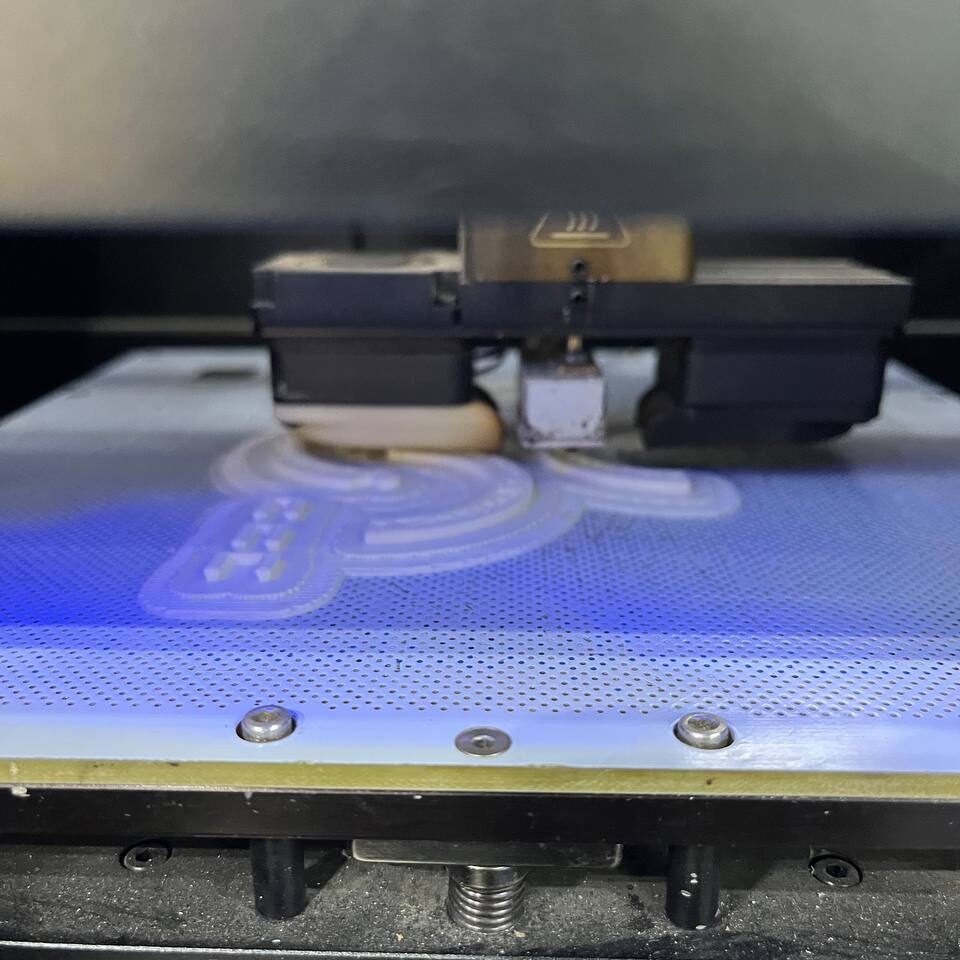
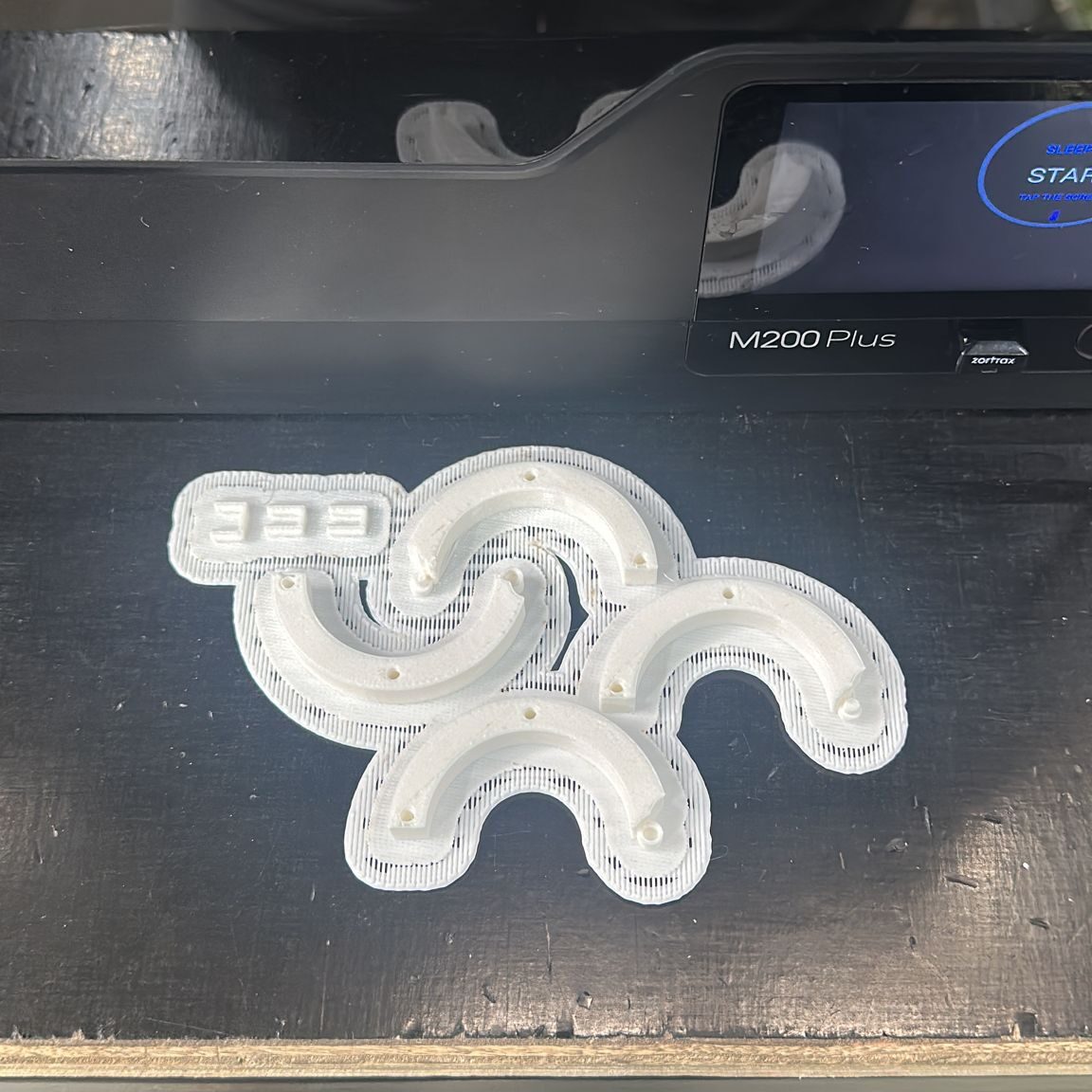
Final Prototype :
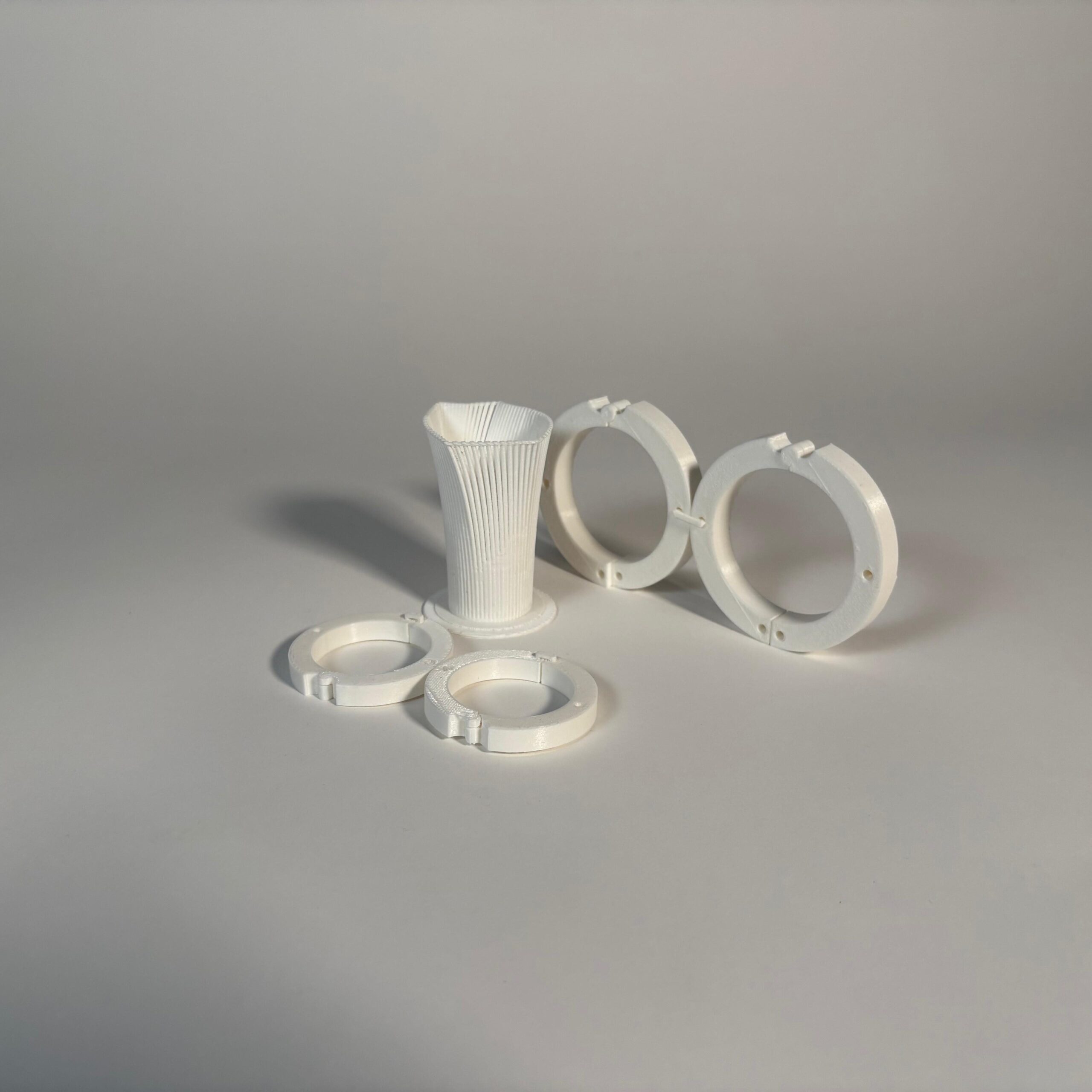
Render Image :
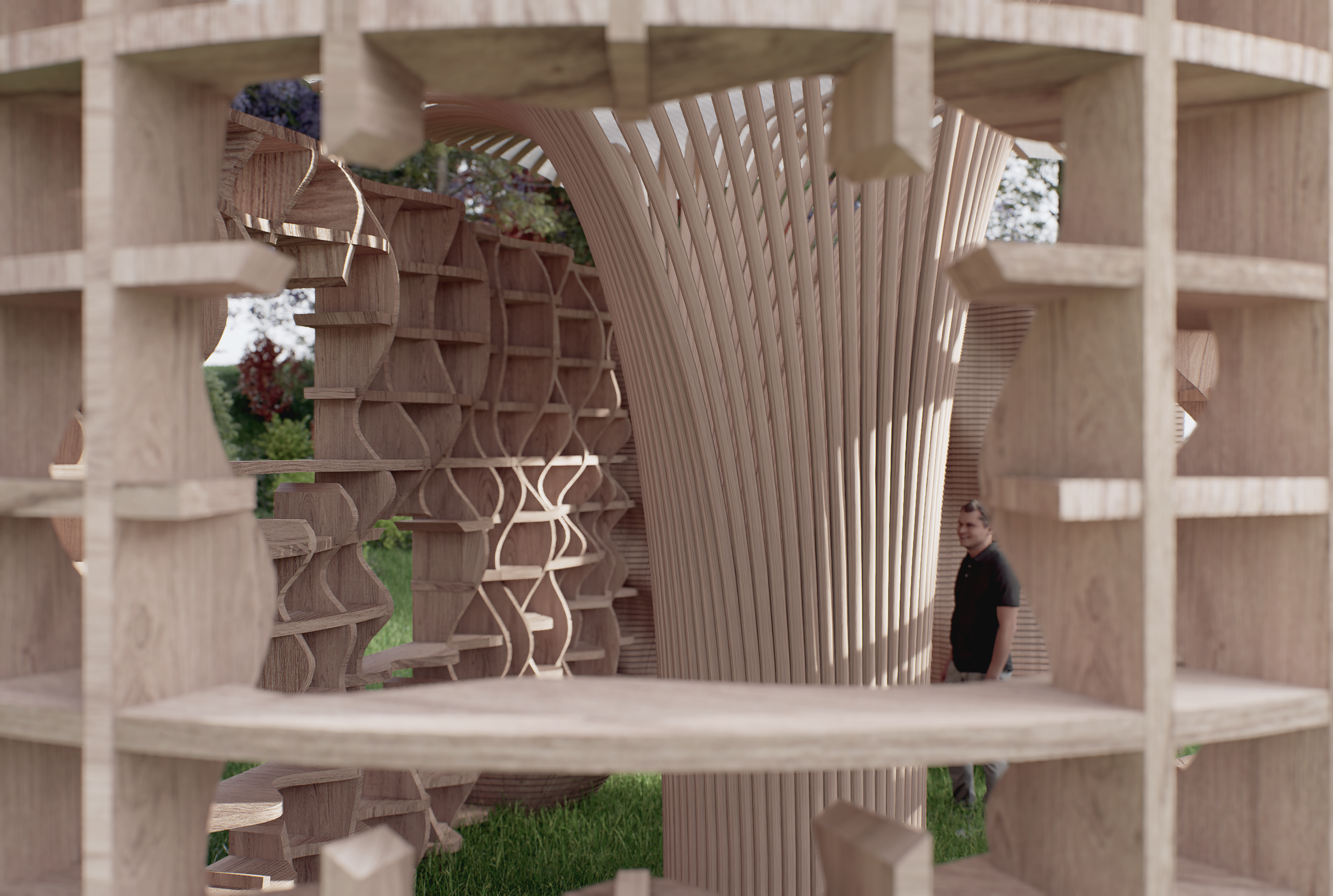