Mechanical Inserts for 3D printed Clay
Due to land scarcity, the construction industry pushes architecture to shift its focus towards the entire life cycle of the final construction, considering its various phases, from its sourced material and manufacture, to its utilization and eventual end of life. Minimizing material usage and construction time has provoked the emergence of prefabricated interlocking elements that can be easily assembled without mortar and then disassembled as a solution for reconfiguration or possible relocation.
Additive manufacturing has significantly influenced the construction industry in recent decades. Both Additive Assembly and 3D printing have gained attention for simplifying construction into a single process. Giving architects the opportunity to have a direct design-build system, enabling the creation of more intricate shape geometries while minimizing material waste. Reducing labor costs and facilitating rapid production.
3D printing has served as a tool for addressing complexity in assembly-level design, particularly for performative products. Many contributions in this field focus on consolidating assemblies, integrating components as a permanent part of the structure.
However, challenges persist in extrusion-based ceramic 3D printing. Manufacturing considerations, such as dealing with overhangs during the printing process, and material properties like shrinkage or cracking, pose constraints that can lead to collapse and failure.
HOW TO IMPROVE THE ASSEMBLY-TO-DISASSEMBLY PROCESS OF 3D PRINTED CLAY COMPONENTS?
RESEARCH GOAL
To innovate the manufacture process of 3D printed clay components intended for architectural purposes. Its main objective is to integrate a hybrid manufacture process by integrating mechanical connectors into the clay during its production, simplifying both, manufacture and assembly to disassembly processes of temporary structures.
OBJECTIVES
- Examine the clay properties and its application in 3D printing.
2. Study the physical benefits and limitations of integrating an external component with different material properties than clay.
3. Analyze factors like precision in fittings and tolerance thresholds that impact the integration of the embedded piece
4. To create a dual end effector that enables 3D printing and robotic embedding simultaneously.
5. Examine the relation between the integrated mechanical connectors and the final geometric form.
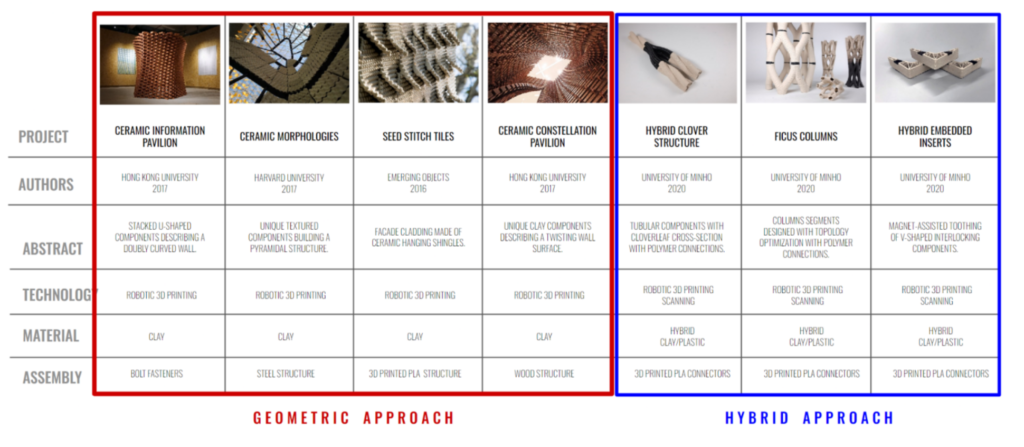
STATE OF THE ART: HYBRID ASSEMBLIES.
The University of Minho, within academia, has focused on assembly-level design for interlocking elements. They’ve innovated by creating hybrid components using both 3D printed clay and Polymer 3D printed connectors.
Their manufacturing process begins by designing fittings into the clay components’ design. These components undergo the complete clay cycle, including production, drying, and firing, leading to deformation due to the loss of water particles. Following this transformation, they scan the modified fittings to generate mechanical connectors precisely tailored to the dimensions of these fittings.
STATE OF THE ART: FORM DESIGN TO FIRING.
The Master’s program in Robotics and Autonomous Systems from UPENN has created a prototype of a façade screen brick. Their design incorporates slip-casted rotatable bird nests directly into the clay components, offering a multifunctional aspect.
The inserts, made of the same clay material as the envelope, are slip casted and fired separately. They are then integrated into the printing process and undergo the same clay cycle, including drying and firing, alongside the main envelope components.
STATE OF THE ART: EMBEDDING WHILE 3D PRINTING.
The University of Texas has also explored embedding different materials during the clay printing process. One of their projects include embedding a wireless temperature sensor within the printed clay. To maintain the sensor’s integrity in challenging conditions, they use porcelain for the printed envelope, ensuring durability in harsh environments. This approach to embedding in 3D prints showcases a versatile solution applicable across multiple industries.
METHODOLOGY
The research will be divided into 3 main phases.
The phase 1: is to develop and design fittings for the embedded pieces, analyzing the relation between the clay envelope properties (shrinkage) and the reception of the embedded piece.
Phase two will explore the creation and design of a modular 3D printed system featuring a hybrid robotic process for embedding mechanical connectors into the clay and analyzing the fittings among its individual components.
Phase 3 will take the phase two findings further, contextualizing it into a commercial product that uses clay as a viable material for trade show stands.
PHASE 1
In Phase one I delve deeper into understanding the materials and processes employed by academia for embedding in clay.
In the hybrid embedded inserts project, the envelope consisted of earthenware clay with a firing range of 1050-1100ºC and a shrinkage factor of 7%. The inserts, on the other hand, were 3D printed ABS elements characterized by a water absorption capacity of 0.80% and a melting point of 200ºC.
In the nest rotable slip casts project, the envelope also utilized earthenware clay with the same firing range and shrinkage factor as mentioned previously. The inserts, in this case, were fired slip casts made from the same material as the envelope. Normal earthenware typically exhibits a water absorption rate of 10% after firing, and its melting point aligns with its full material maturity at 1200ºC.
Both projects involve the manual placement of inserts after firing and also manually during the printing process.
MATERIAL SELECTION
For phase one, the experiment material selection will continue the academia approach, the inserts will consist of ABS and ceramics. Deviating from the previous earthenware clay choice. I selected porcelain due to its mineral compounds, which undergo vitrification during firing. This process binds clay particles, reducing porosity and enhancing overall strength.
Also I’ll introduce a third material: stainless steel pipes. Stainless steel is non-porous and boasts a melting point higher than the firing range of the clay. This property will allow the components to undergo a full clay cycle. These initial three experiments will involve these materials as embedded inserts to explore their interactions within the clay envelope.
DESIGN FOR SHRINKAGE
Earthenware clay experiences shrinkage due to water evaporation during both the drying and firing processes. In 3D printing, the majority of this transformation occurs in the upper layers, resulting in less shrinkage towards the base of the printed object.
For designing these experiments, I’ve considered the shrinkage factor associated with the clay mixtureI’ll be using. This involves scaling the top part of the geometry according to the anticipated shrinkage factor. This adjustment accounts for the expected shrinkage, ensuring the design aligns with the final intended dimensions after the printing and firing stages.
EXPERIMENT 1
The aim is to design fitting for 3D printed ABS as an embedded piece analyzing the envelope shrinkage across the x and y axis.
EXPERIMENT 2
Same as for experiment two with the porcelain pipes.
EXPERIMENT 3
And in experiment 3 with the stainless steel pipes.
EXPECTED OUTPUTS.
In the experiment results, my aim is to counter the anticipated deformation by directing the shrinkage towards the inserts. And analyze which material exhibits fewer cracks due to its water absorption factor.
PHASE 2
In phase two, the goal is to develop a modular 3D printed system that incorporates a hybrid robotic process. This process aims to embed mechanical connectors within the structure and subsequently analyze the fittings among its individual components.
HYBRID ROBOTIC PROCESS
Integrate 3D printing and additive assembly by developing a dual end effector tailored for robotic manufacturing. This setup will combine a material extruder with a vacuum gripper, ensuring an effective process for both 3D printing and embedding components.
PHASE 3
“Ephemeral Clay for trade shows” transforms research findings into a marketable product, offering clay as a viable material solution for trade show stands.
Characteristics of Common Trade Show Stands:
Materials: Trade show stands commonly utilize materials like wood, metal, plastic, fabric, and paper. However, if these materials are not reduced or recycled, they contribute significantly to landfill waste.
Single-use Nature: The majority of stands are designed for single-use purposes, leading to their disposal after the event, resulting in waste generation.
Packaging: Stands often come packaged in bulky materials that are discarded after unpacking, further contributing to waste generation.
Obsolete desgin: Stands may become outdated after the event due to changes in branding or design trends, leading to their direct disposal.
The drive to minimize waste associated with trade show stands is urging companies to seek more sustainable options.
“Ephemeral Clay” offers a solution to this industry problem in several ways:
1. Recyclability: Clay serves as a material that can be recycled as aggregate for future envelopes, contributing to a sustainable lifecycle for trade show structures.
2. Reusability of Embedded Connectors: The embedded mechanical connectors can be reused in future structural systems and new printed envelopes, reducing waste and promoting a circular approach to materials.
3. Local Sourcing: Clay as a material is locally available, enabling production anywhere in the world, reducing transportation and carbon footprint associated with sourcing materials.
4. Customizability: Utilizing a single type of mechanical connector allows for the creation of temporary bespoke structures tailored to specific needs, providing versatility and adaptability in design.