A story of mosaic leftovers and their robotic revitalization
In alignment with the circular economy and Barcelona’s climate action plan of 2030, we want to use broken ceramic tiles from the demolition site for large-scale applications.
It offers numerous benefits, including cost savings, environmental sustainability, mass-customization, and increased efficiency.
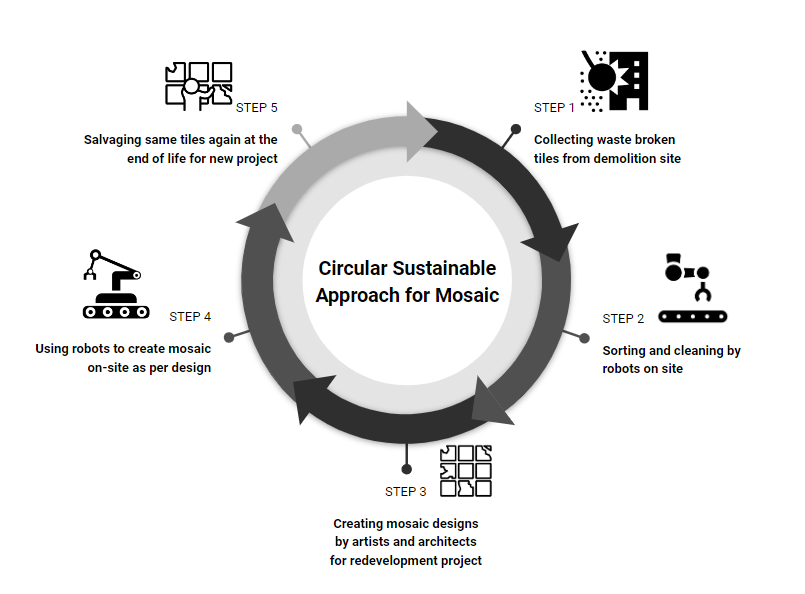
The goal of the workshop is the assembly of a mosaic using recycled leftover pieces, and our goal is to design according to the imperfections of mosaic waste. The design will be then assembled using a robotic arm UR and making some finishing touches by hand to present the final tile.
We got some inspiration ideas focused on having an order in chaos by using scale, symmetry and swarms. Afterwards we started generating some manual explorations to visualize the approaches we could achieve using the material we had. These tiles differ from each other in sizes, colors and glazing.
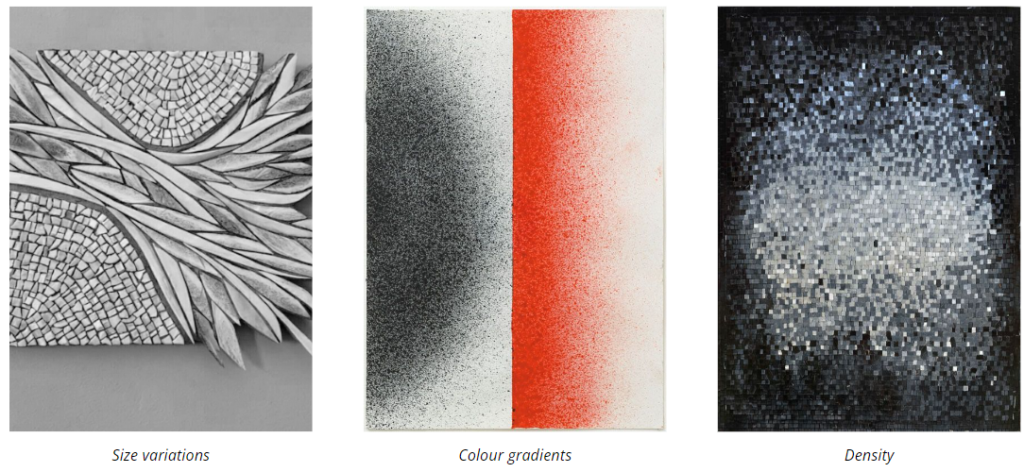
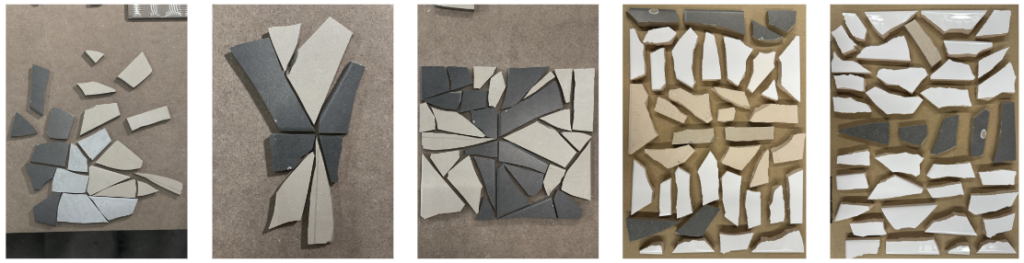
We generated some manual iterations varying the broken mosaic tiles and started scanning them to place them in a digital context.
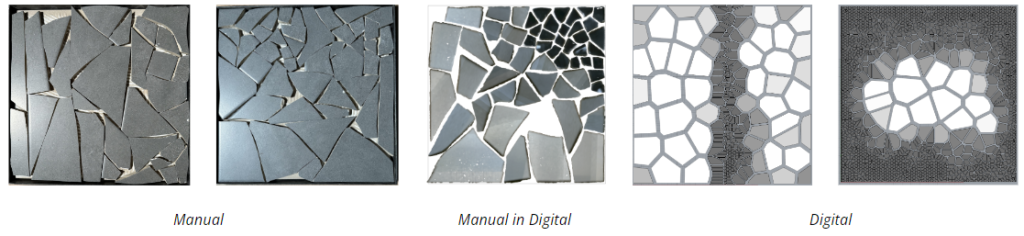
With the scanned pieces from the previous steps, we generated 4 iterations in which we played with gradients in gaps and sizes. The images below show how different these can look like depending on each situation.
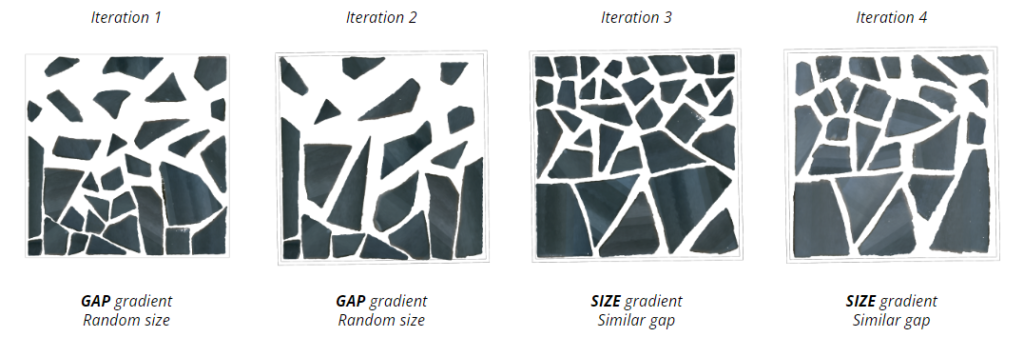
Since the design goal is to create gradients, we wanted to generate them by using size and also using color. For this next step, we used a gradient with patterns for 5 different iterations according to size and gaps.
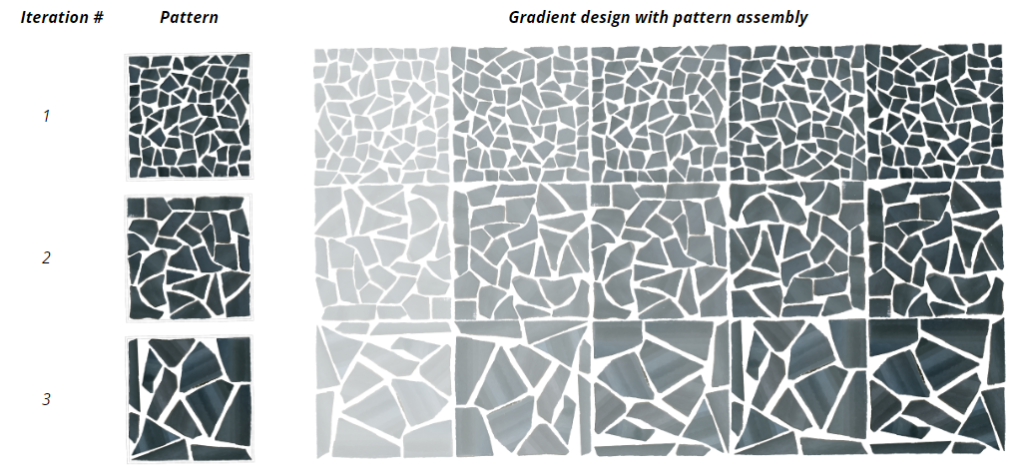
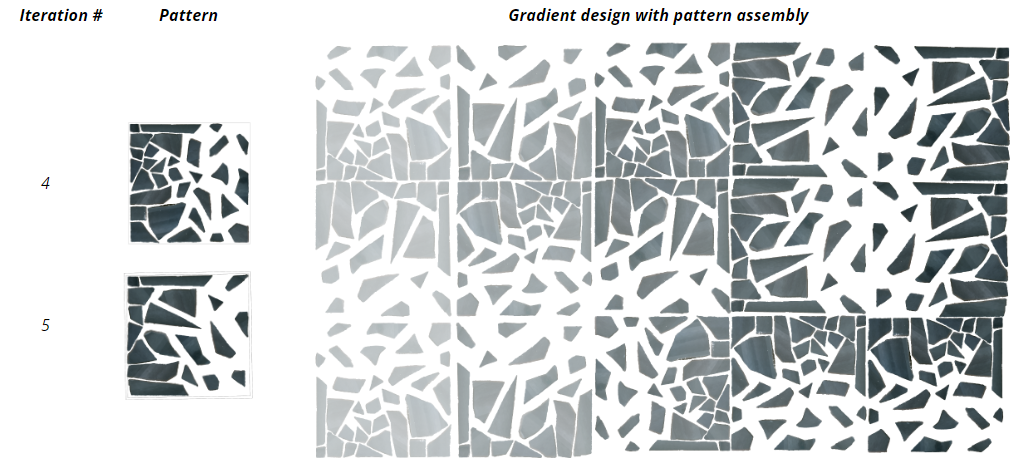
With these scanned pieces, we started then to generate a catalog, which would be the one used to generate an overall design. Also, we started at this point using the UR to see how the pick-n-place works.
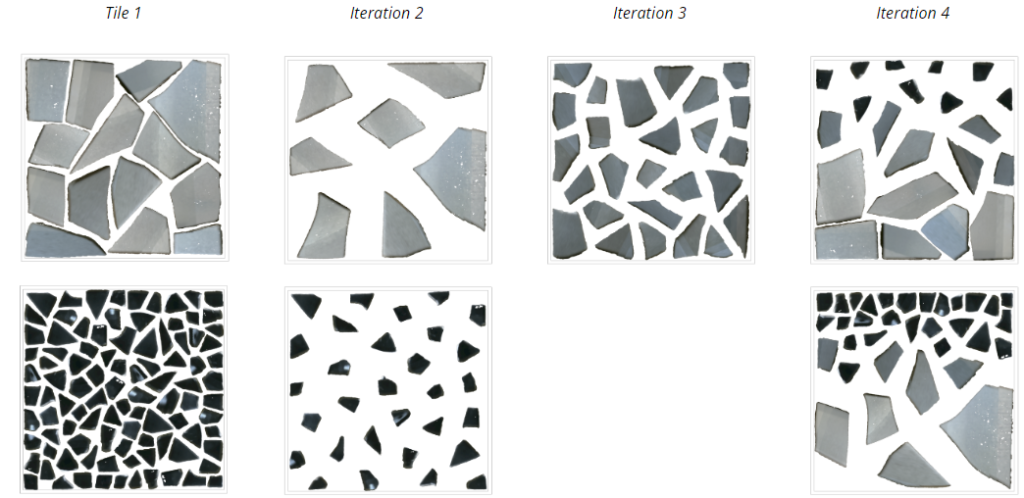

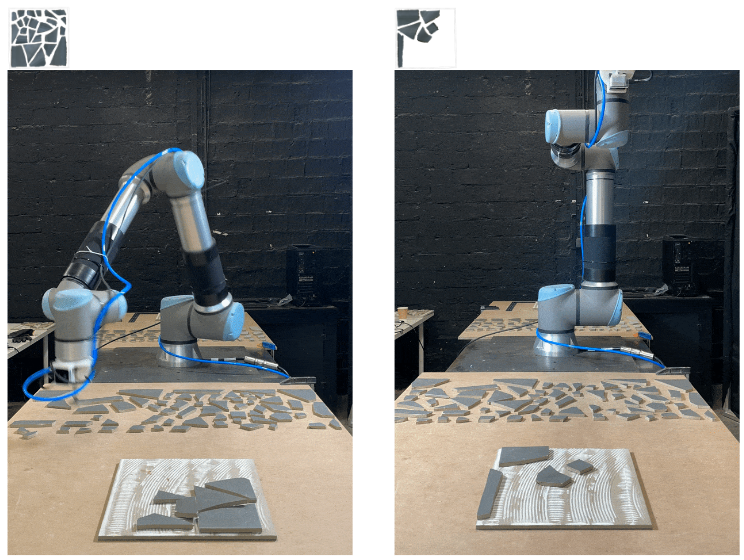
After this we started using the scans to create designs using software algorythms. The workflow would be having first the scanned pieces in the digital environment, then obtaining their contour to measure their sizes and sorting them in Small, Medium and Large scales, so that at the last step they would be located in a rectangular tile according to their sizes. In the images shown below, the pieces are sorted according to their size and color into the colored areas within the rectangular tile. (Small pieces are located on the orange area, medium pieces are located on the blue area and big pieces are located on the white area). With this process, we got to the conclusion that since it is fully parametric and we have control of the areas, we can get many design variations. Placing the tiles in array with each variation in gradient and color would also give many interesting results, just as the ones shown below.
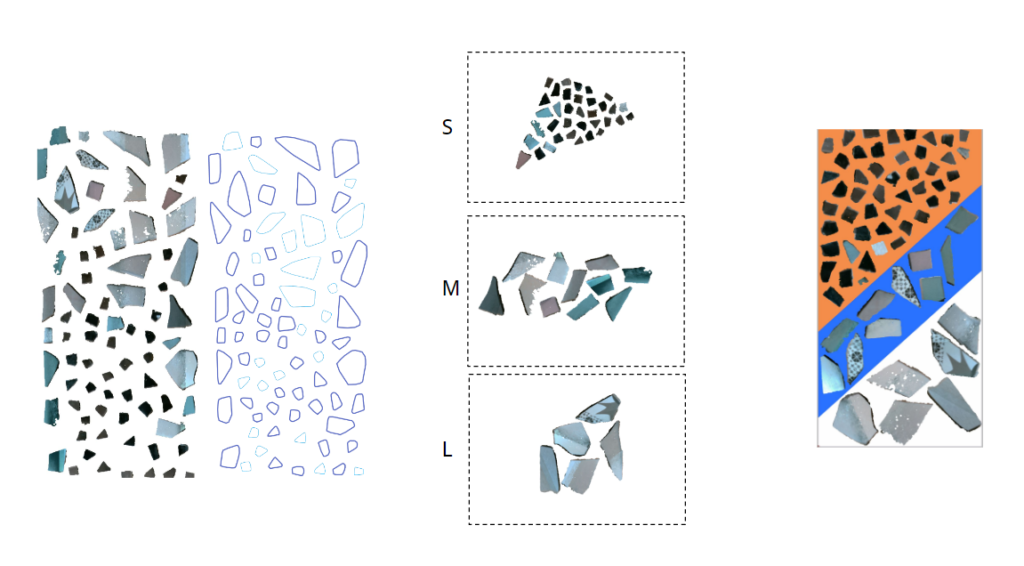
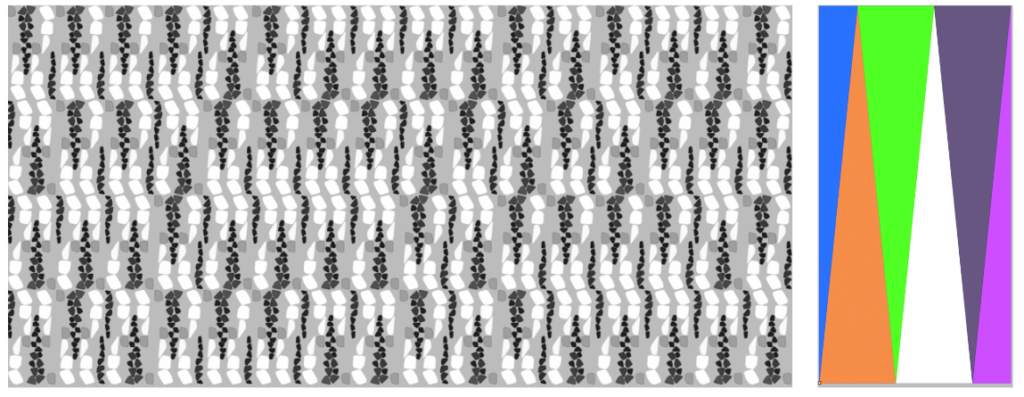
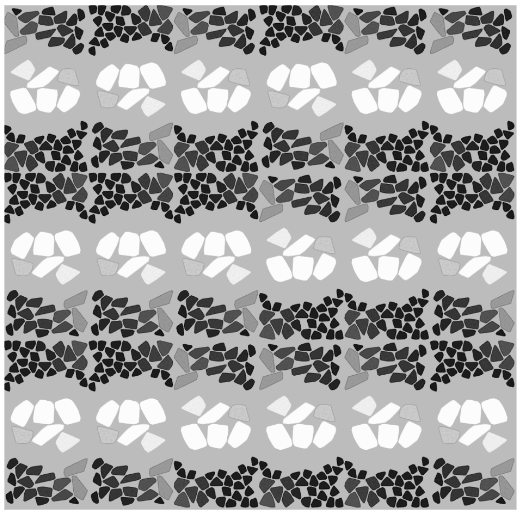
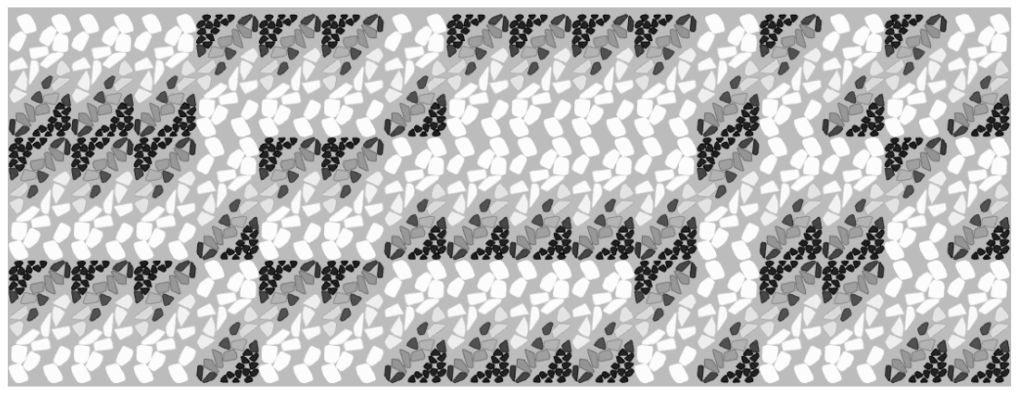
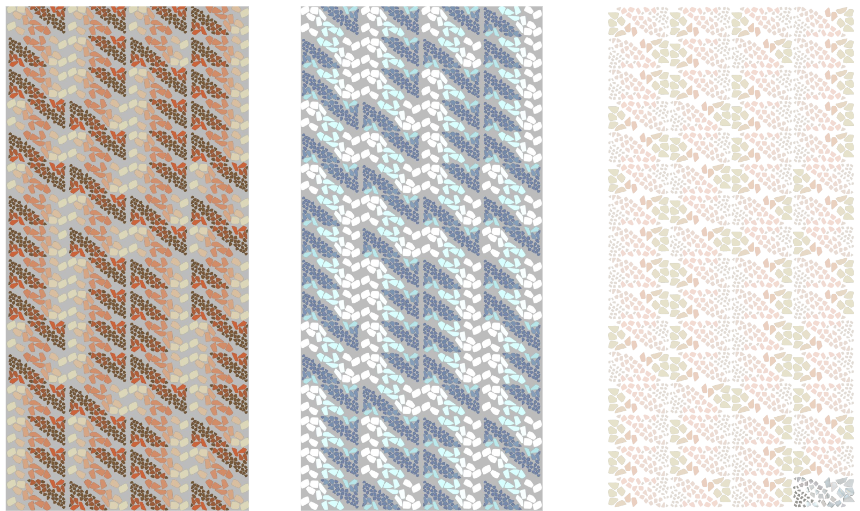
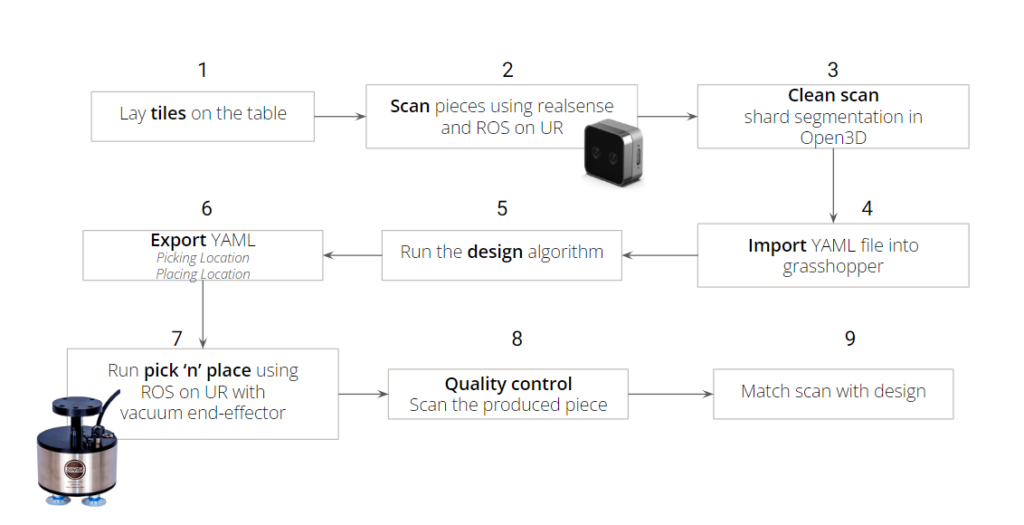
The following images represent the process following the workflow:
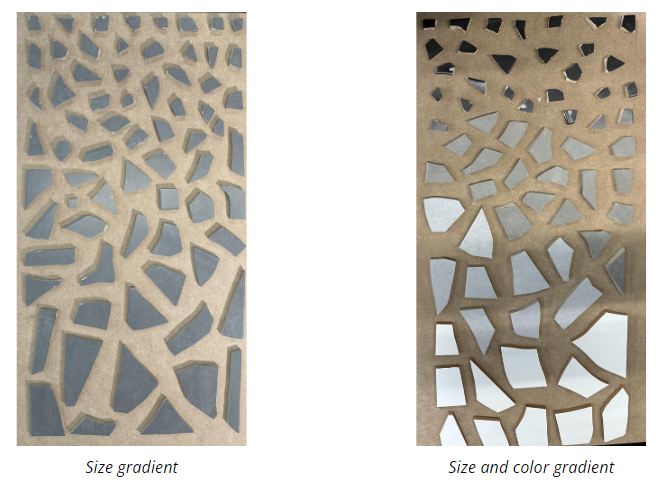
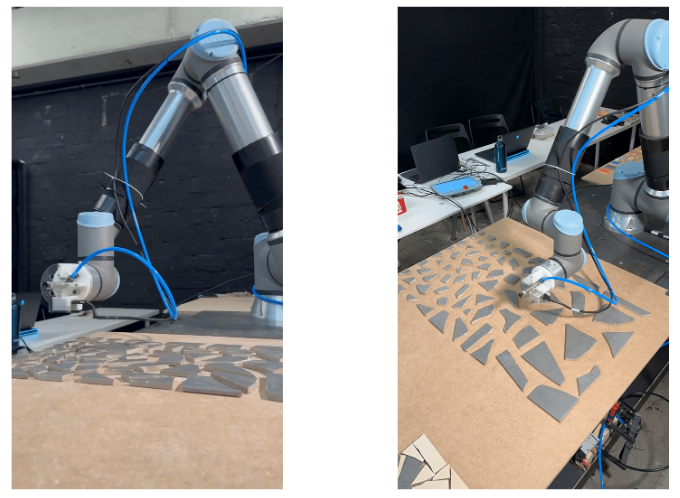
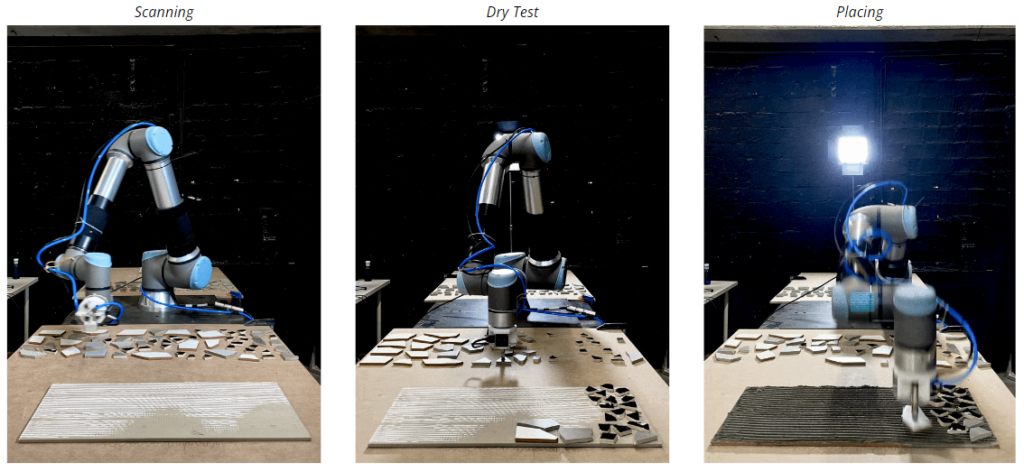
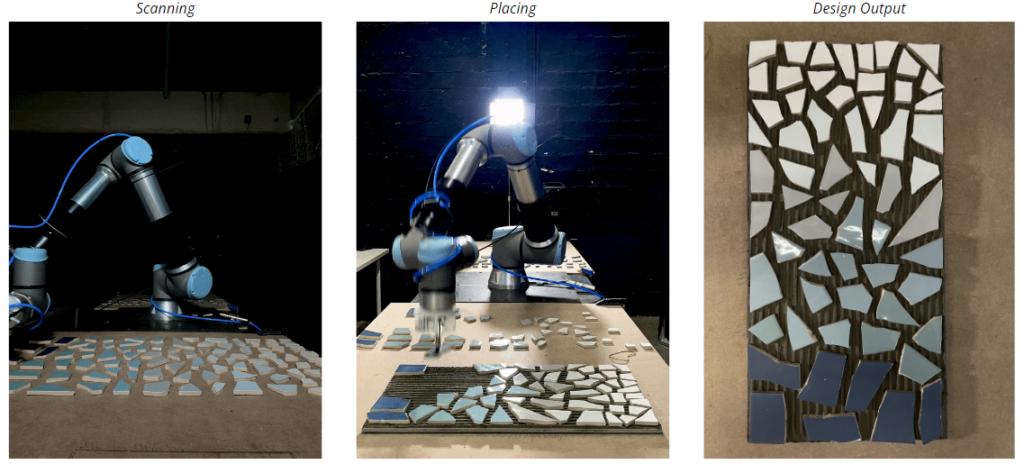
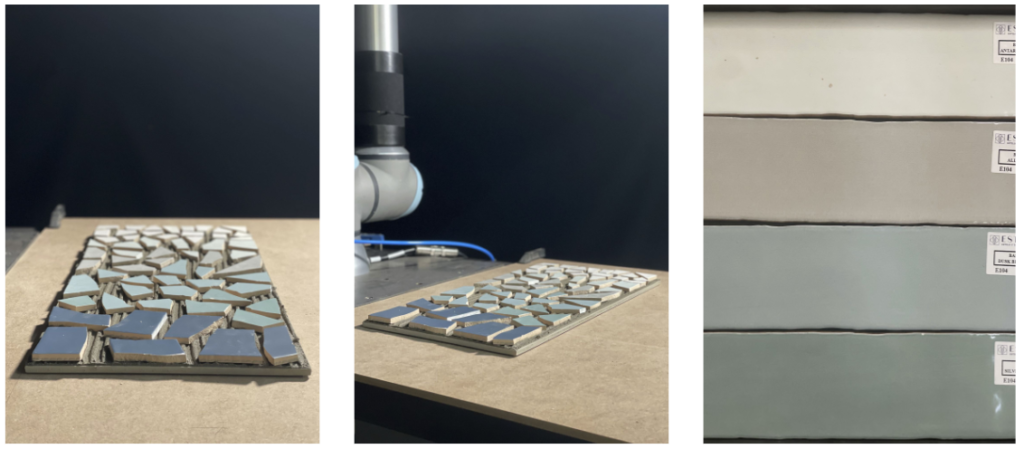
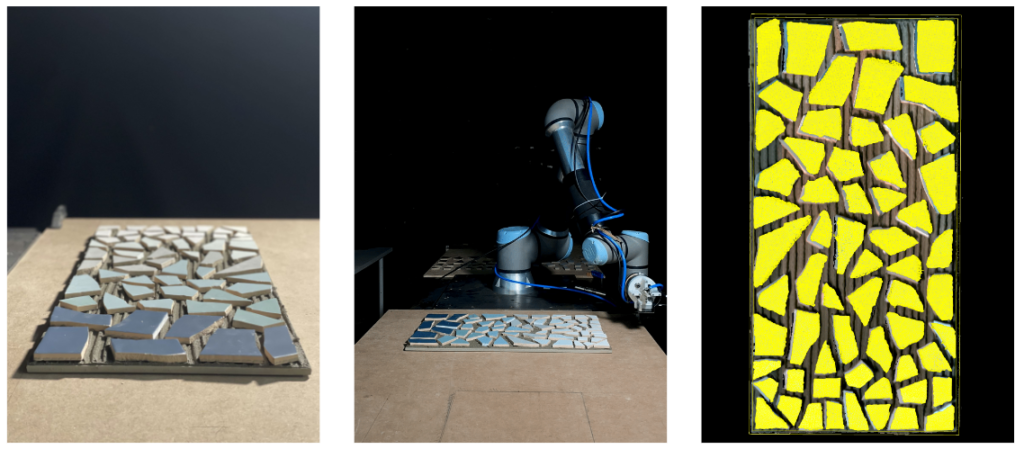
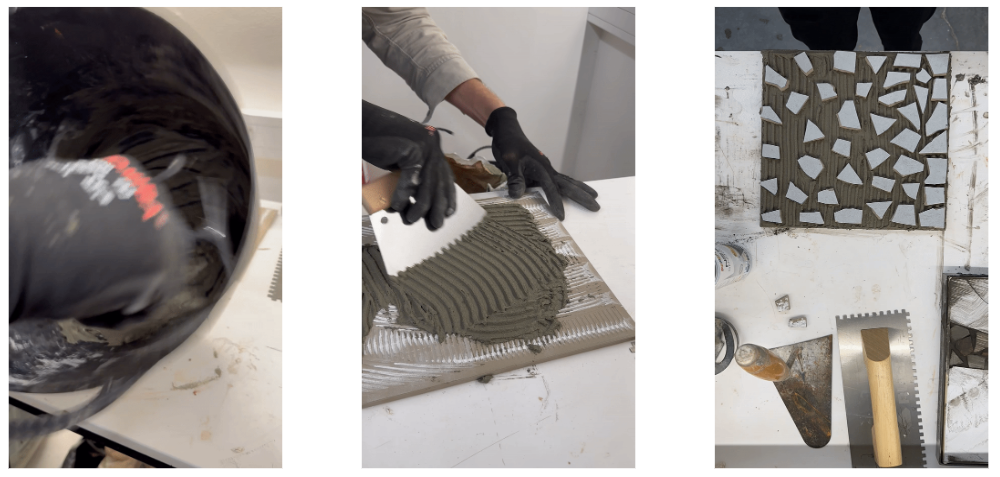
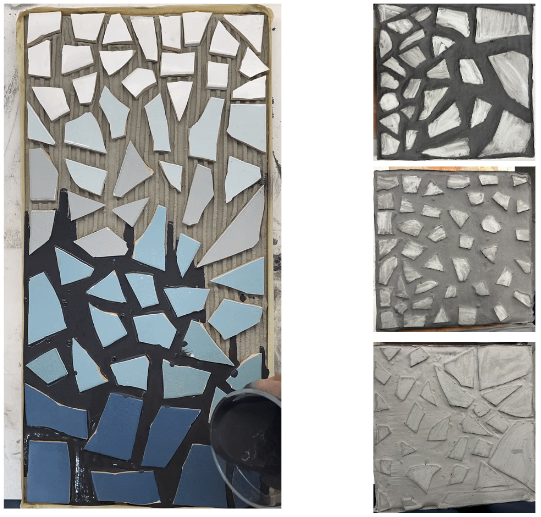
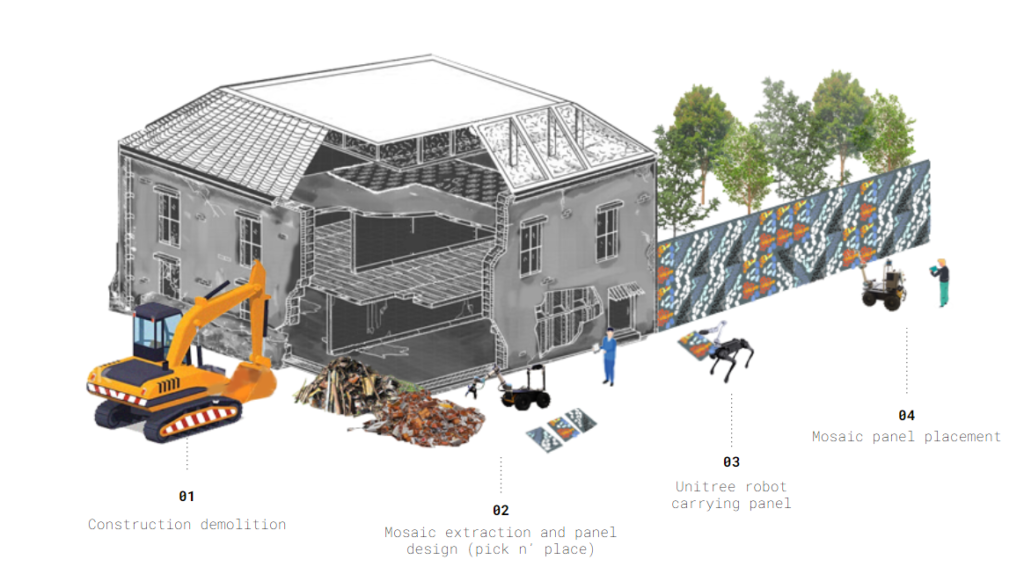