| Problem Statement
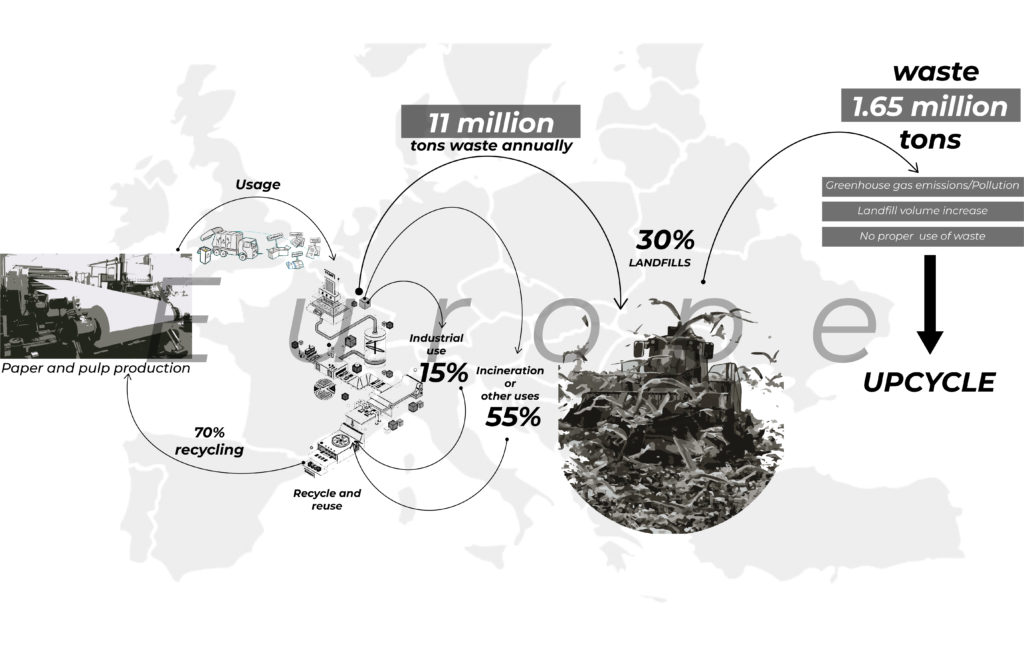
This paper and pulp sector is resource intensive and produces 11 million tonnes of waste yearly. It has been found that 25-40% of municipal solid waste generated each year worldwide is paper-related.
Recycling rates have climbed substantially in recent years. Nevertheless, 30% of paper ends up in landfills every year.
And The research is set within Barcelona’s municipal waste management policies, which were adopted in 2020 as a way to encourage waste minimization.
| Scientific interest
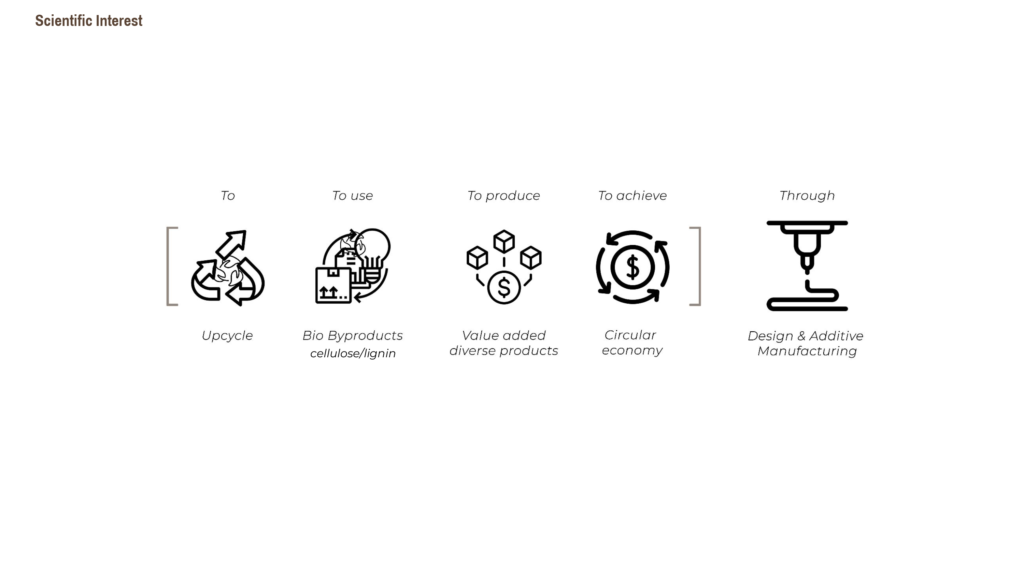
Upcycling of waste paper helps in taking the approach towards the circular economy
And all of this could be done by Additive manufacturing as it will offer more design freedom to achieve this material system and fastens the process.
| State of the art
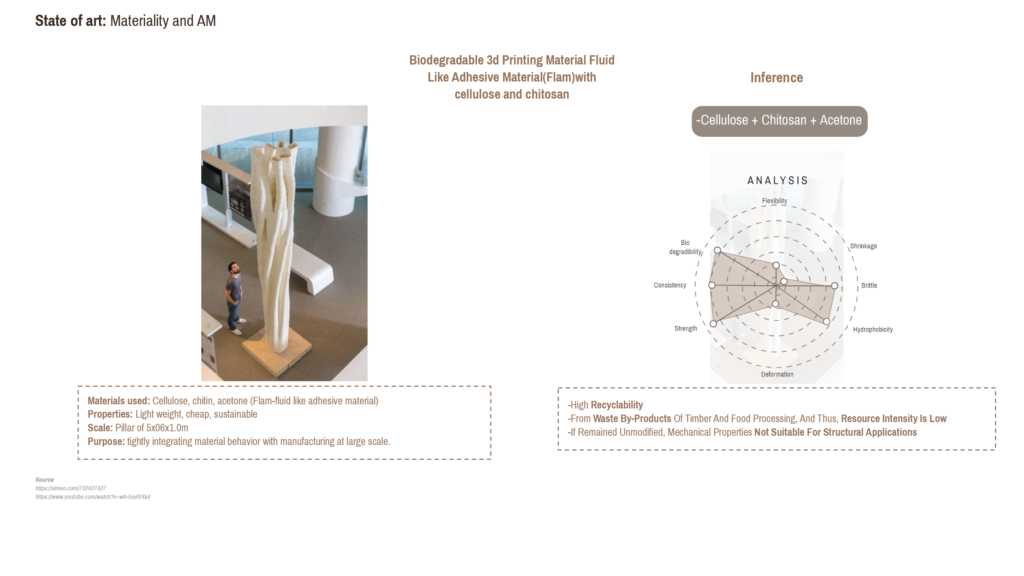
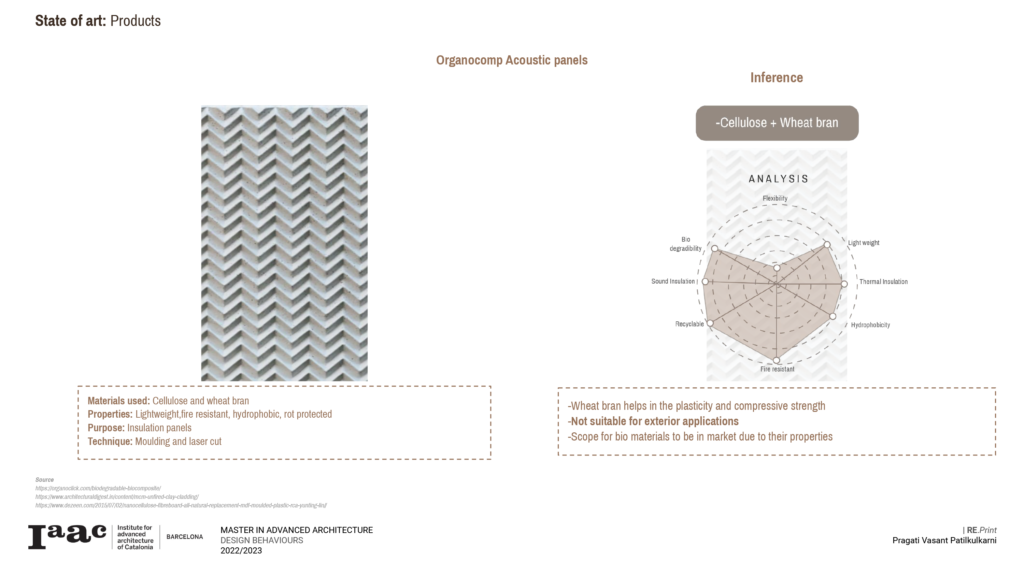
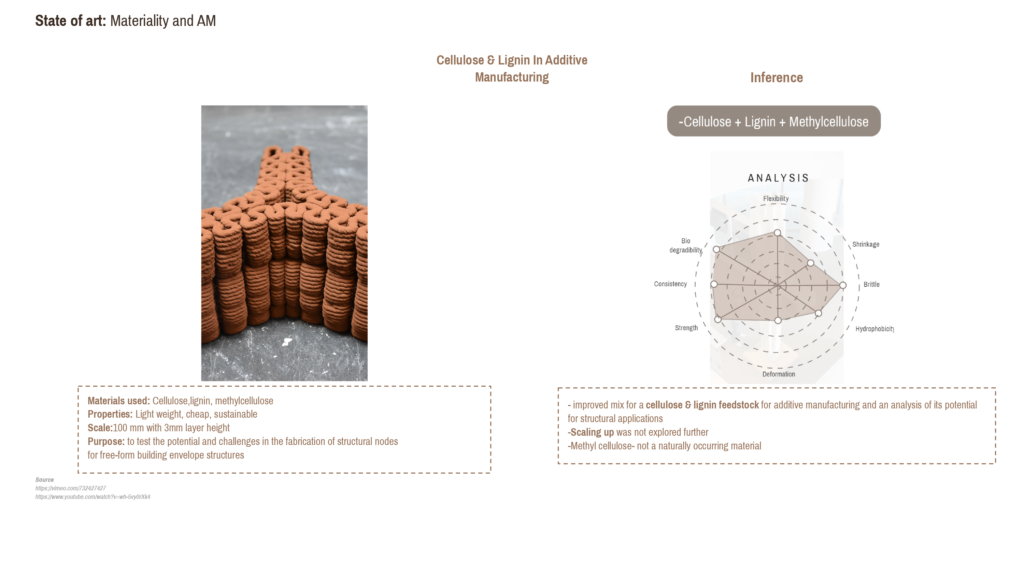
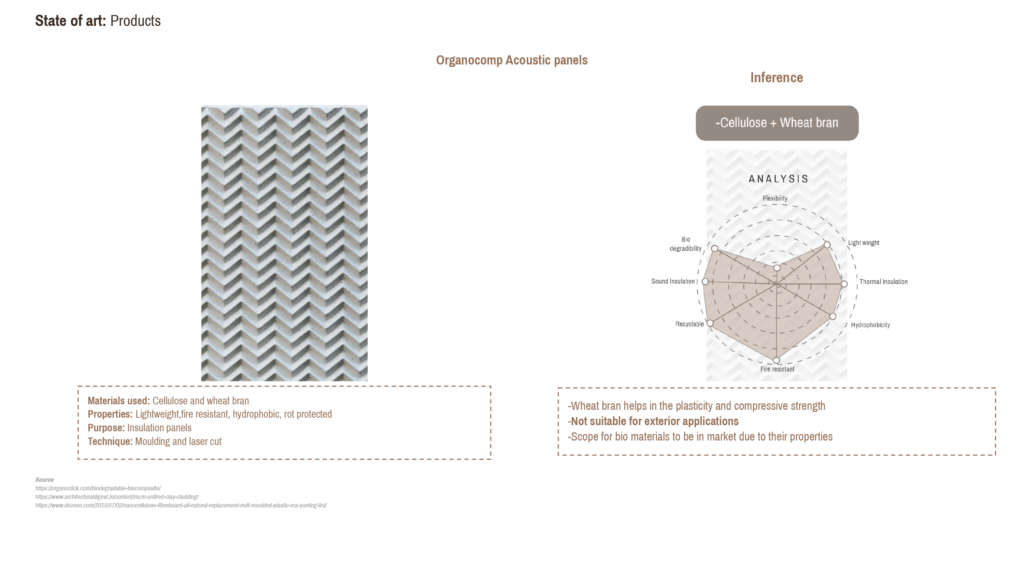
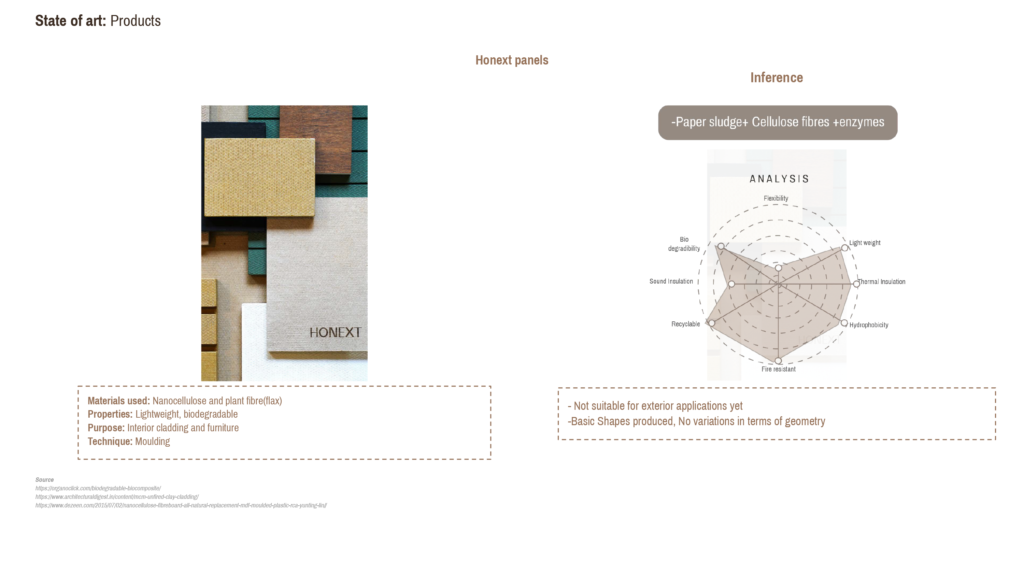
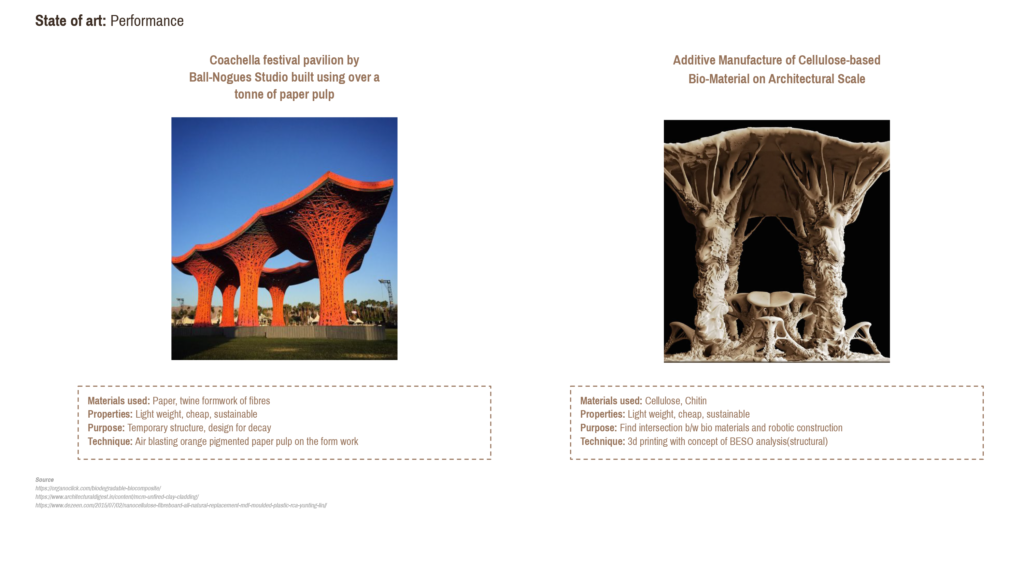
| Research Question
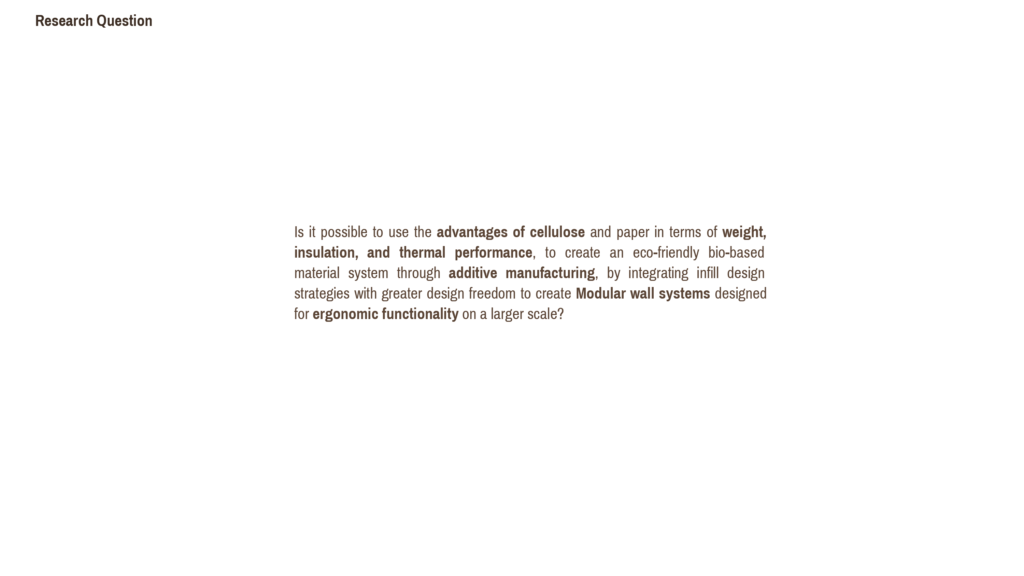
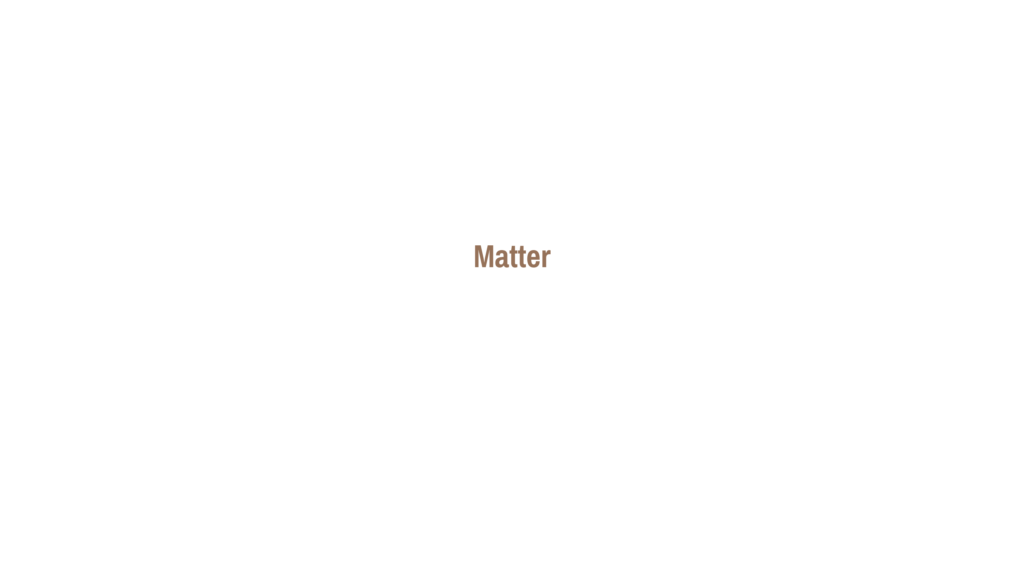
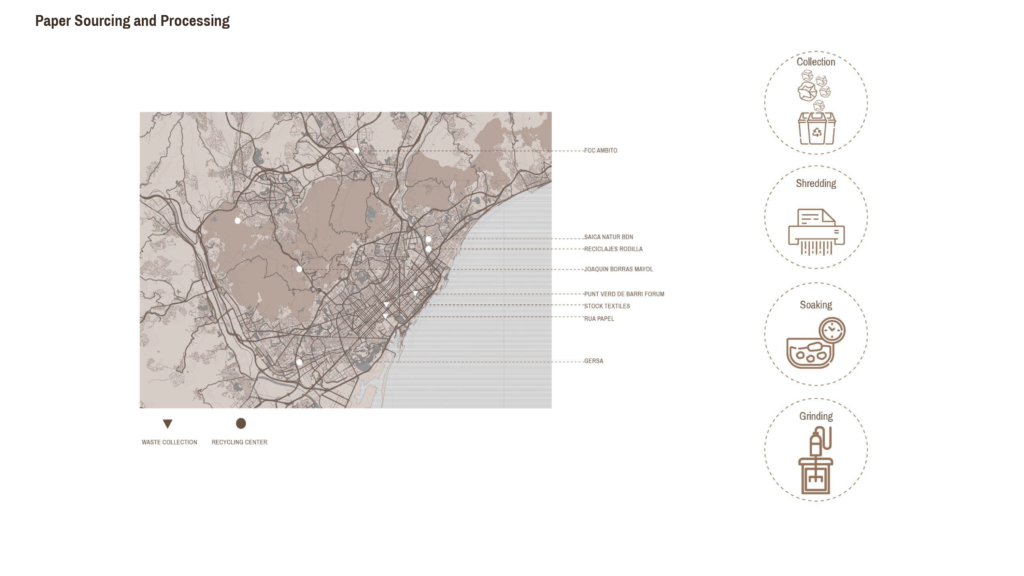
After sourcing the waste paper, It is shredded, soaked and grinded to further use the paper mache for the material system
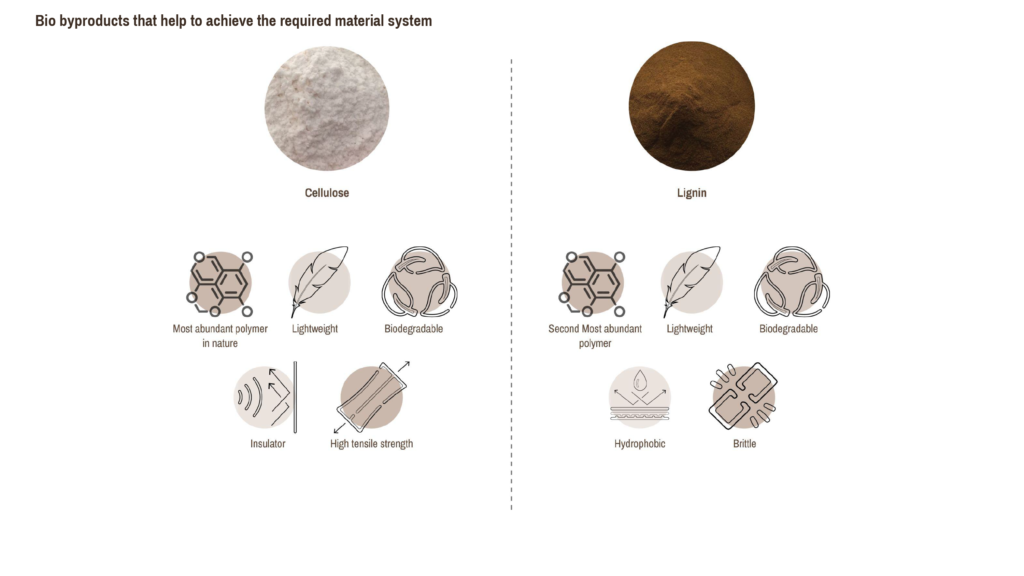
They both are lightweight, biodegradable.
Where as cellulose is a good insulator and lignin shows some properties of hydrophobicity and helps in strength.
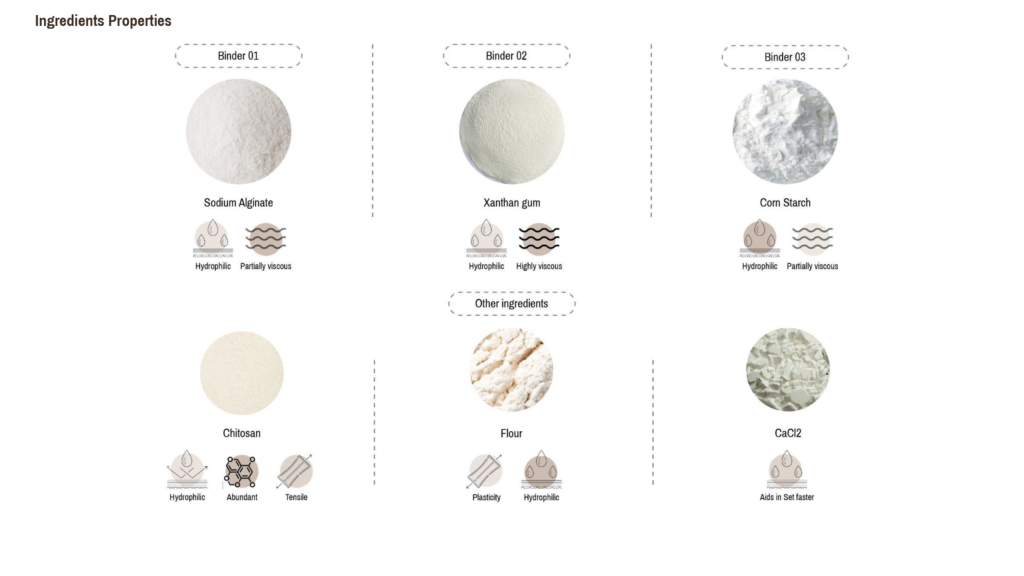
The other additives include Chitosan which is an abundant material too which hydrophobic property and helps in strength
And CaCl2 helps in setting faster.
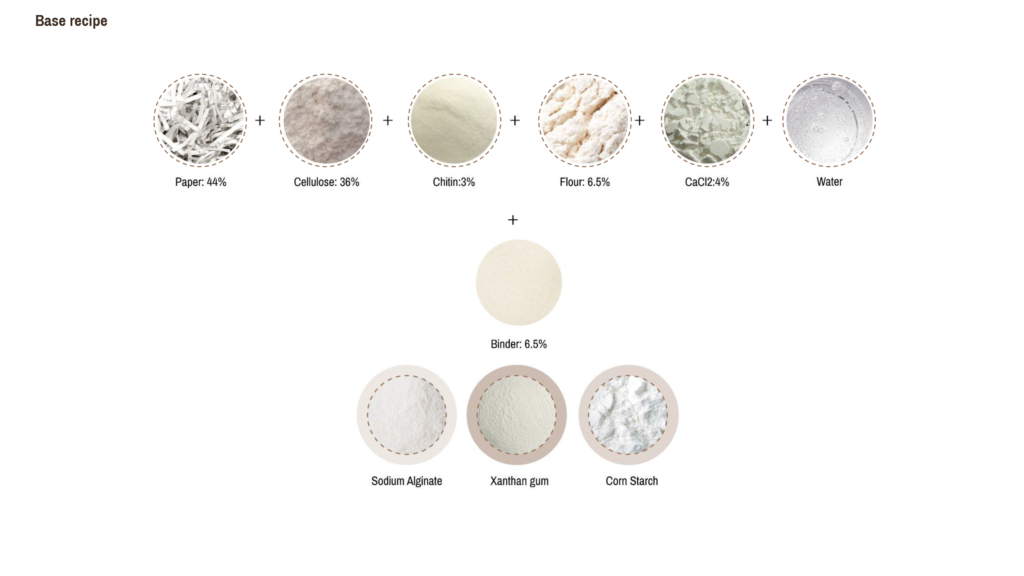
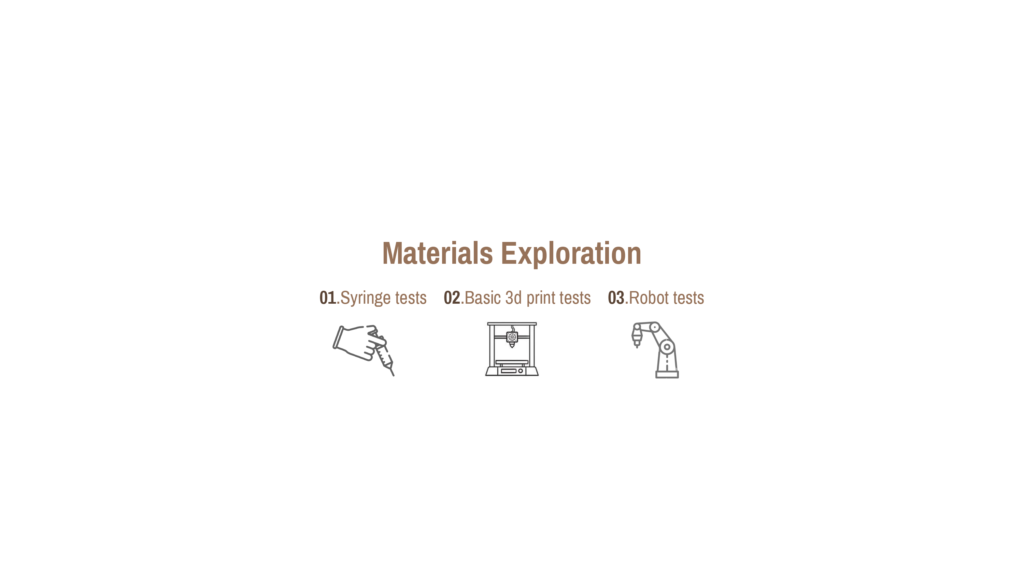
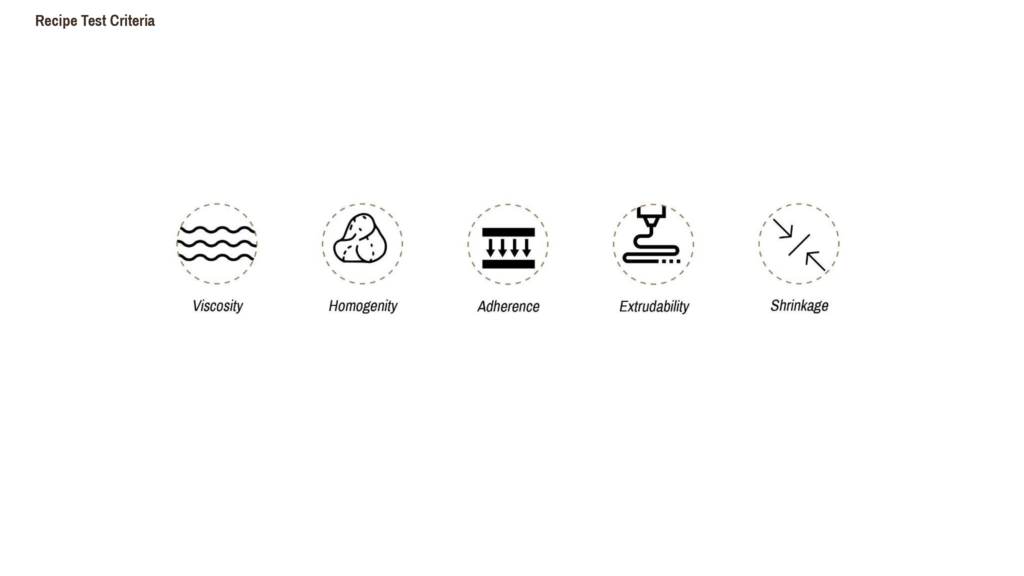
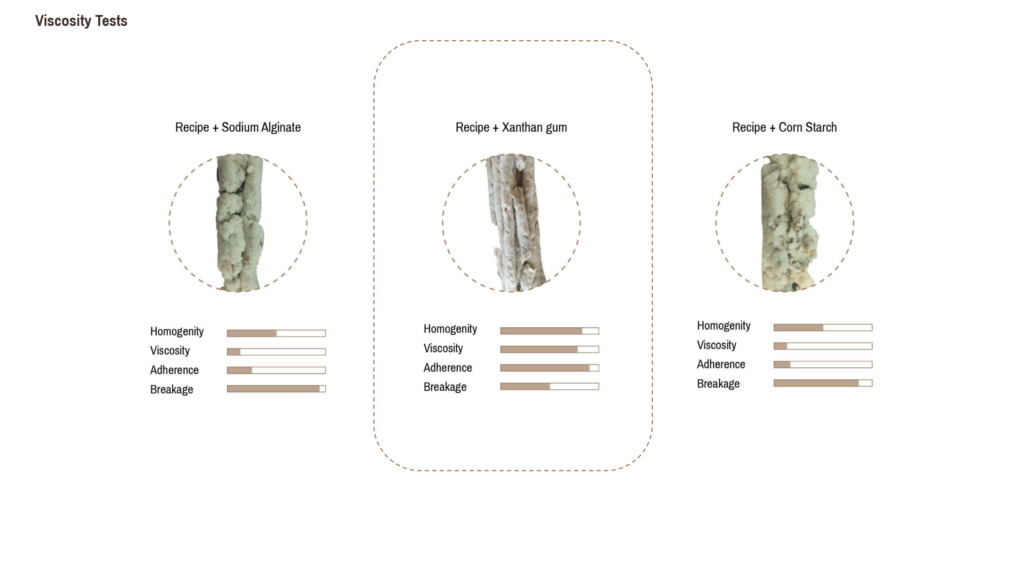
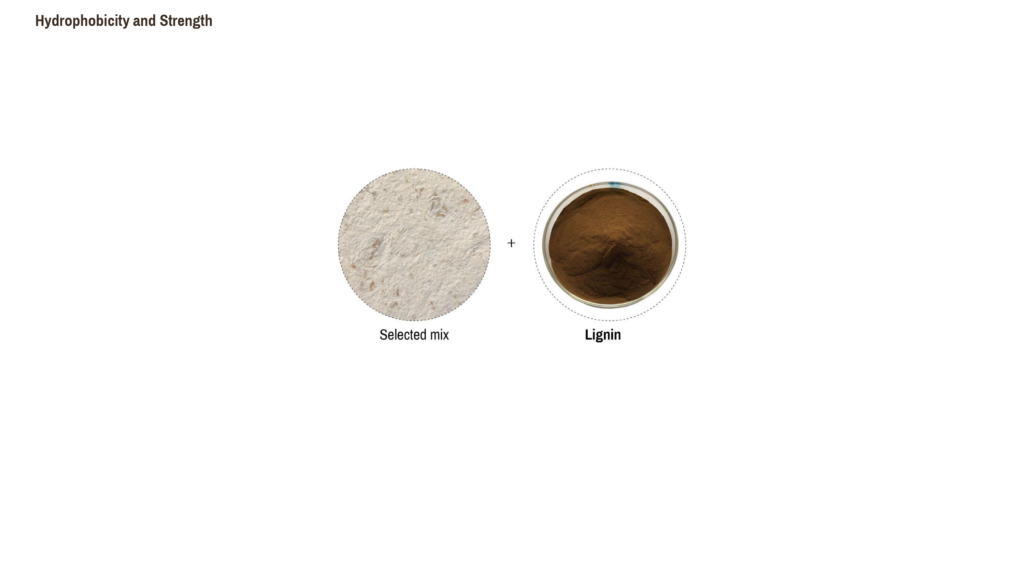
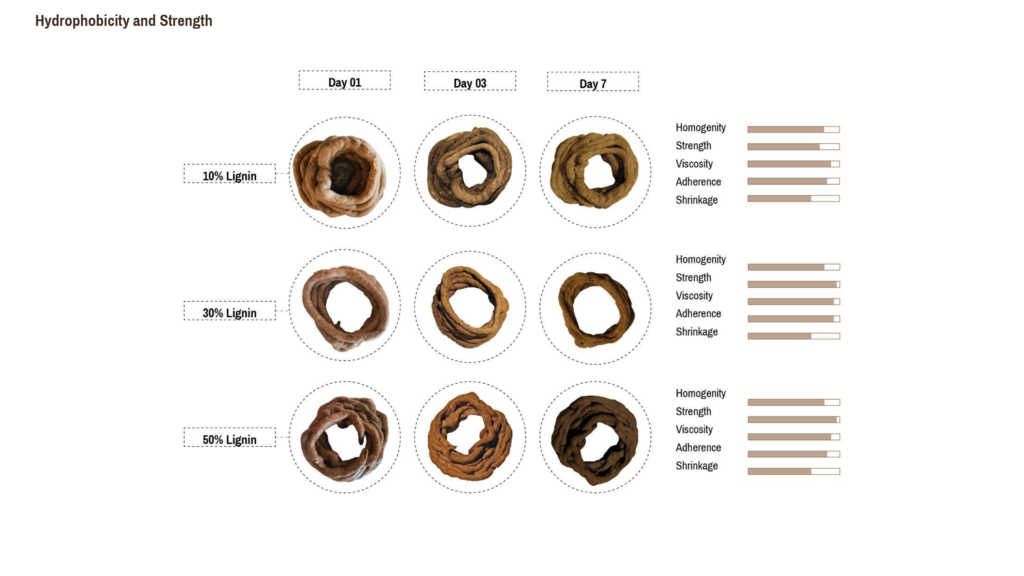
The material extrusion was smooth with all 3 mixes.
The strength of the last two samples was pretty much the same.
Therefore further tests were carried out with 30% lignin
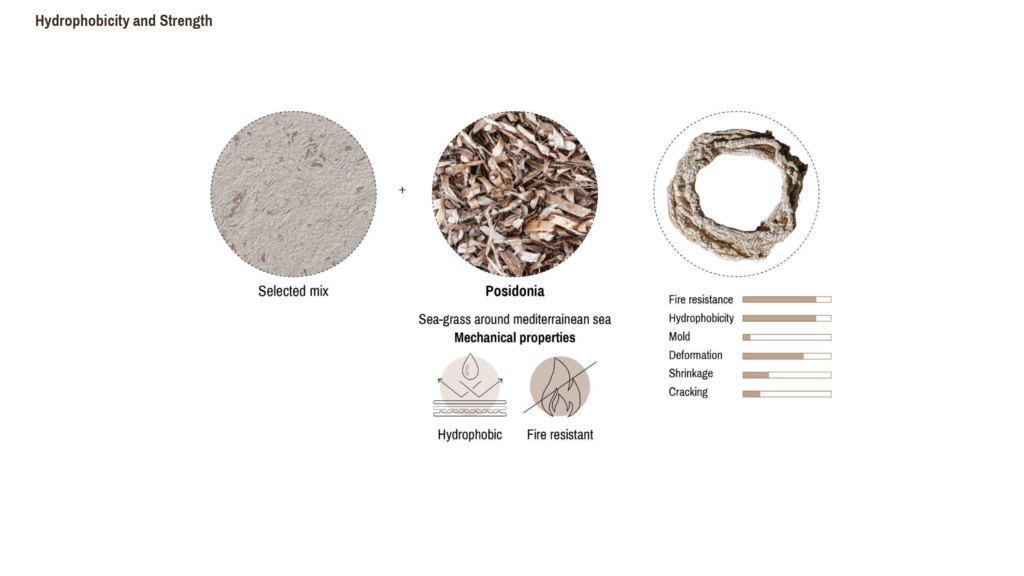
The fibres were powdered to be extrudable and tested.
The consistency was fairly extrudable although posidonia hampering the nozzle sometimes
The sample showed good strength after drying.
The fibres held well with the material mix
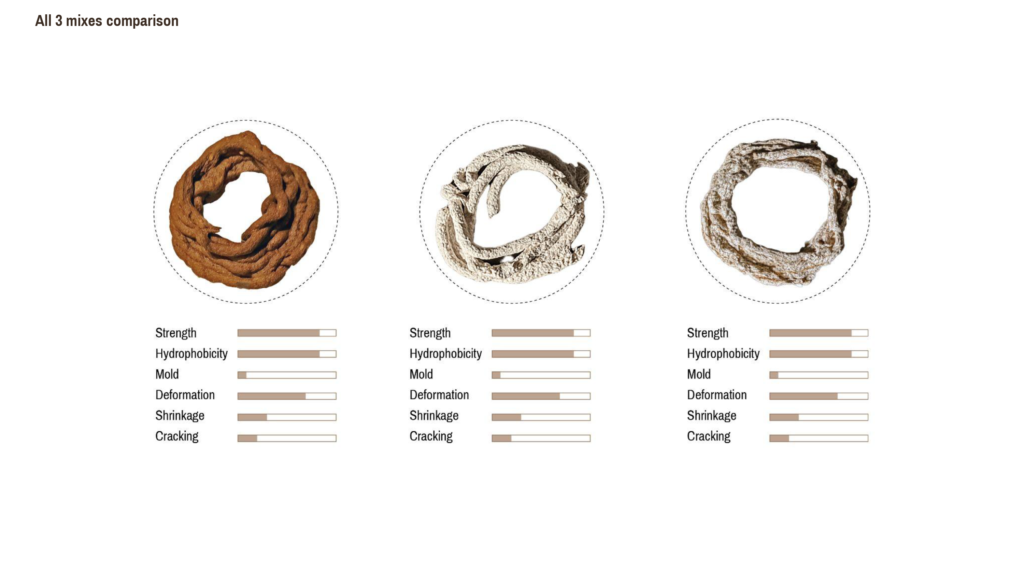
base recipe being the most suitable one for extrusion with less obstructions
Lignin mix has to be studied further to understand hydrophobicity after completely dry
Posidonia mix was a little hard to extrude due to obstruction offered by powdered posidonia that were stuck at nozzle.
All the 3 samples were immersed in water for a day.
Until 12 hours the samples were intact with wet layer on the outside and brittle inside.
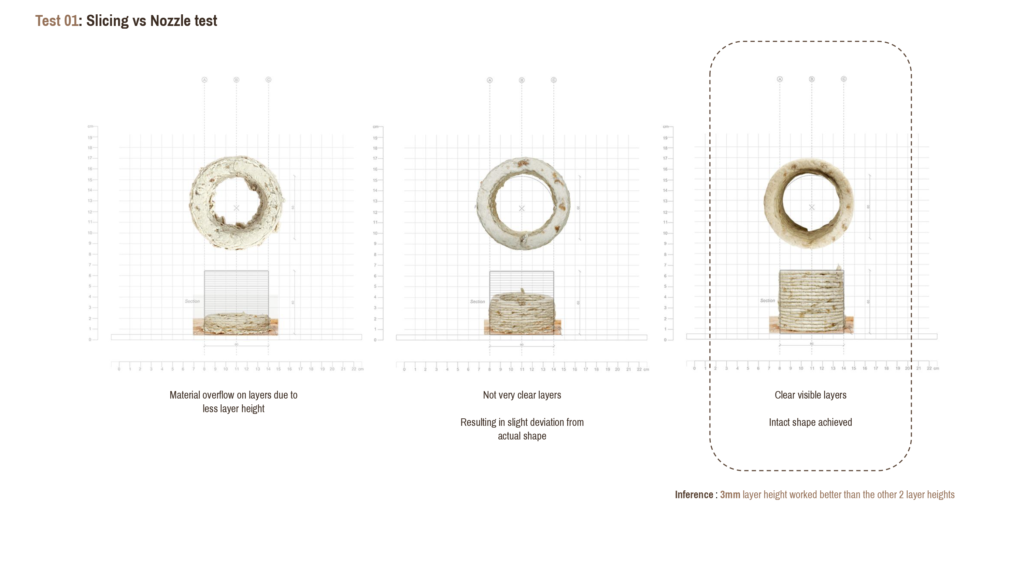
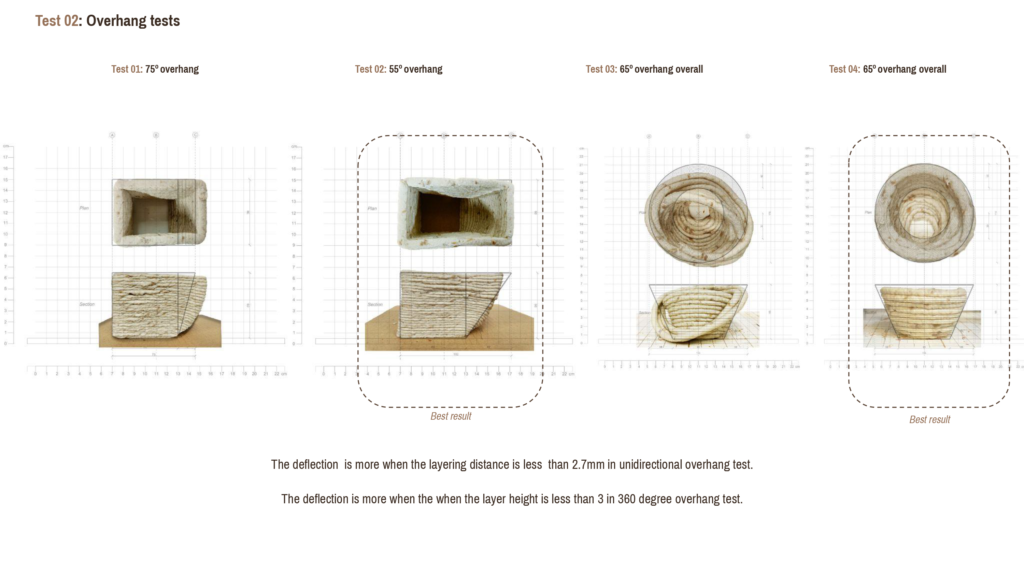
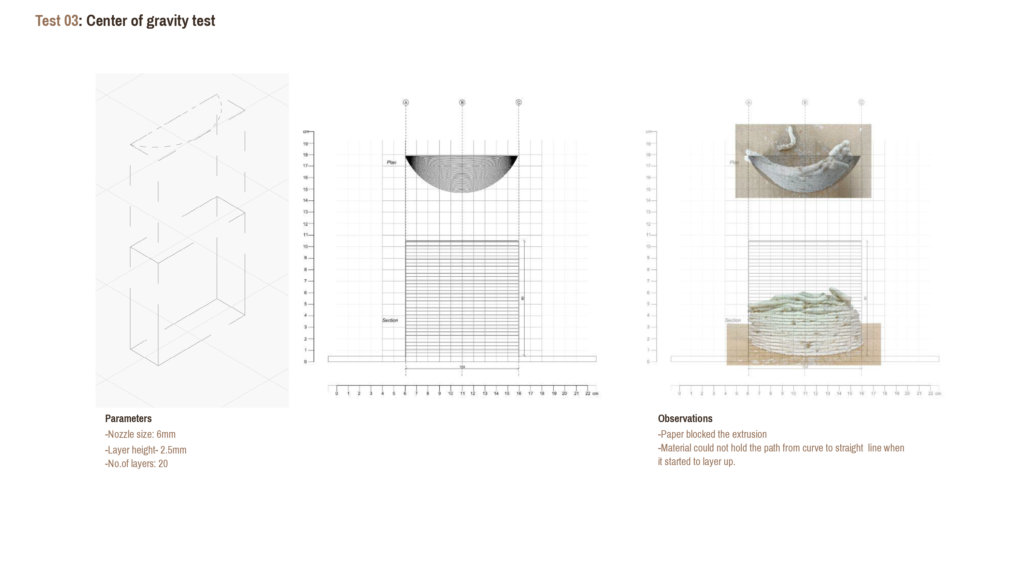
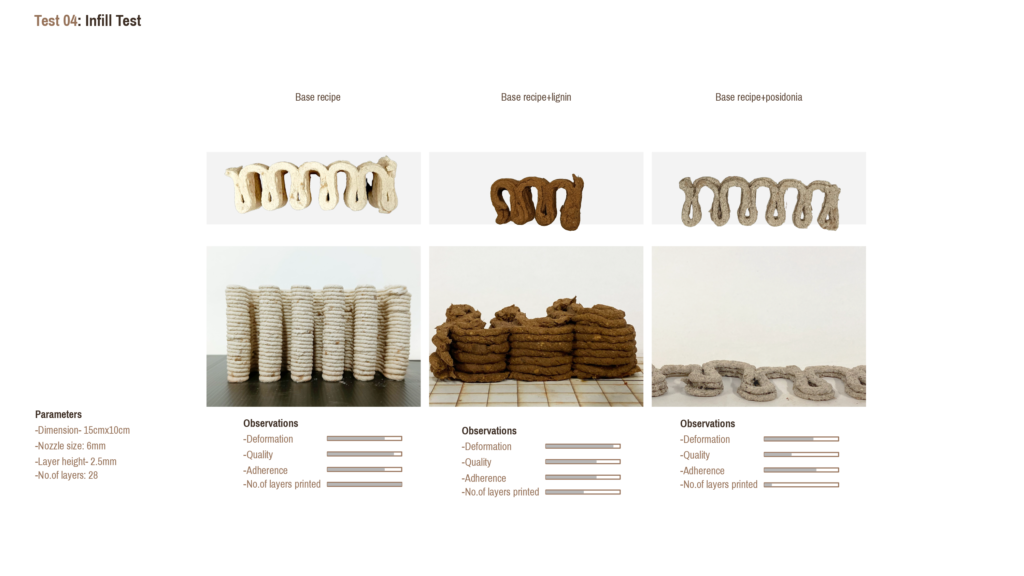
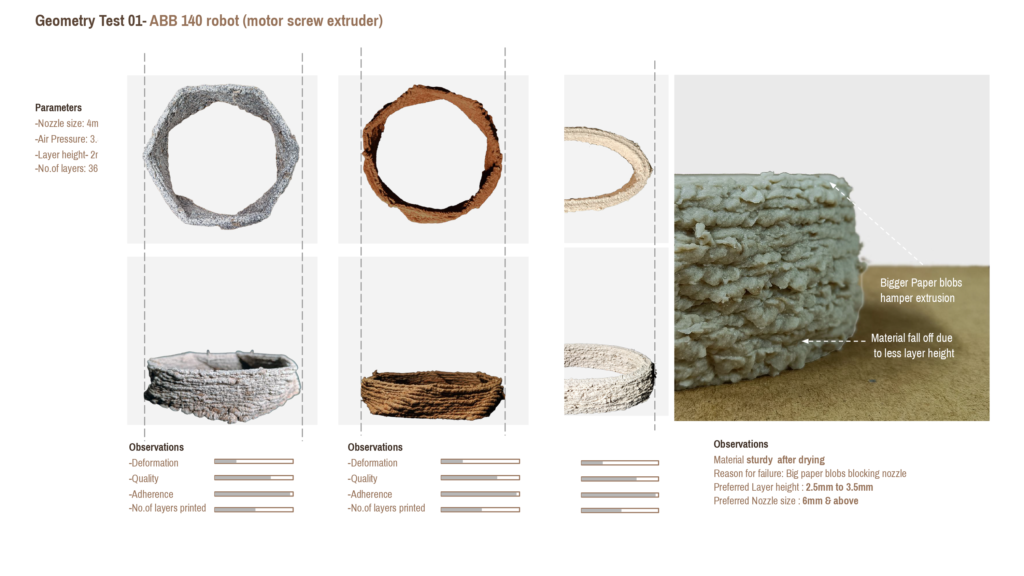
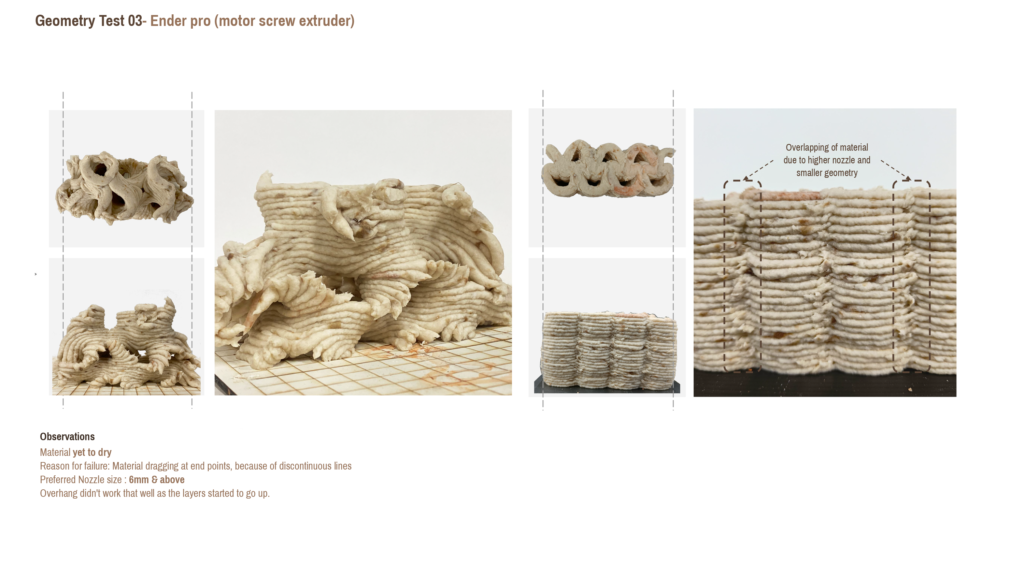
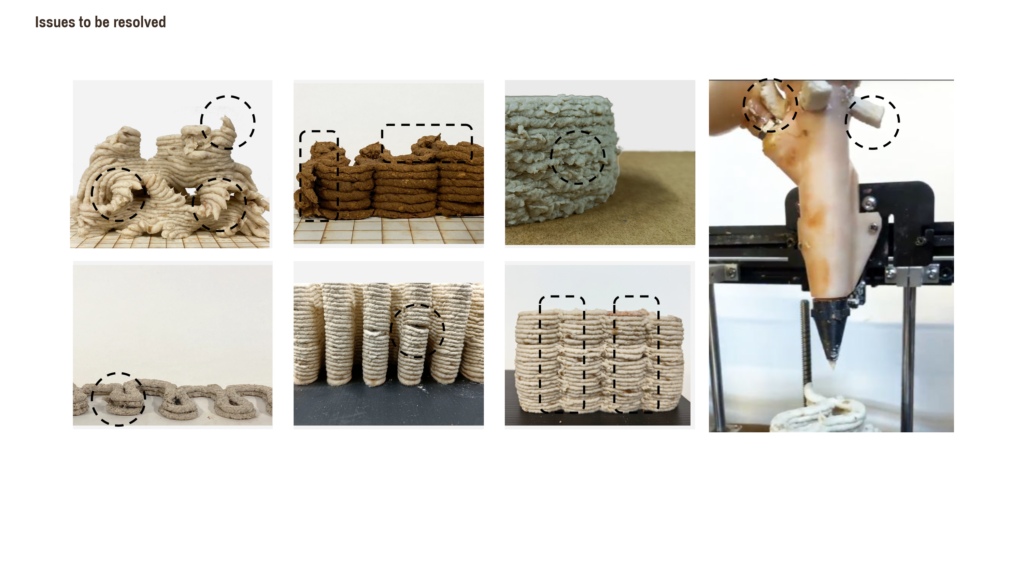
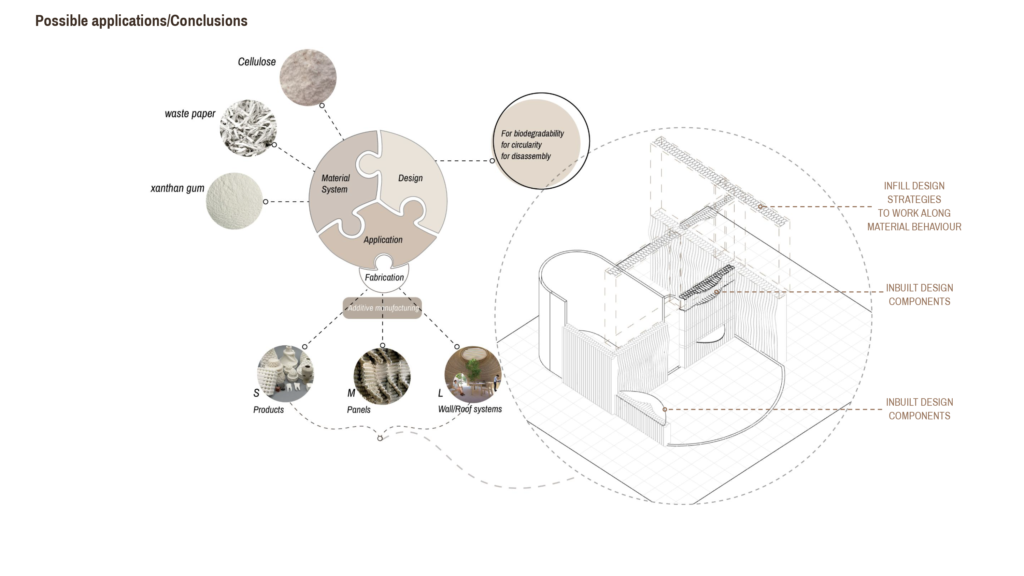