with Theophile Peju + Alfredo Chavez, Heatherwick Studio
OBJECTIVE
Ceramic tile manufacturing is a craft that requires a level of customization per client, and also replication per project. An original tile finish may be created once, replicated over thousands of tiles. In this industry, replication requires precision, refinement, tactile quality, and efficiency. This creates a unique opportunity for artisanal craftsmanship and robotic repetition and precision may create an optimal partnership. The following project explores the overlap and divergence between manual artisanship and mechanical replication in an effort to optimize the qualities of each approach to production.
CHALLENGE
MRAC students + IAAC students with an interest in ceramic glazing are invited to manually glaze a series of tiles, using a paint brush application equipped with a HTC Vive sensor and Grasshopper Code for recording the motions made. With the recorded toolpath, the robot is callibrated and ” trained” to playback the recorded manual motions. An analysis between the original manual glazing and the robotic copy is intended to ultimately improve the replication process, creating close replicates of the manually applied glazing technique.
In summary, the challenge is to control the process by defining the variables acting on the manual application and the discrepancy between the manual recordings and robotic playback,
PROCESS
The process, therefore, is broken into a series of steps:
01 Technical Glazing
The demonstration of glazing techniques at Ceramica Cumella introduced the students to modern professional manufacturing techniques. Students understand the diversity of bespoke shapes, textures, and finishes created for each commission and the value of automation in the process. Students are inspired to apply these techniques in their challenge.
In addition to the variety of glazing colors, opacities, textures, and sheens available, the craft of glazing involves many application methods, like sponges, sprays and brushes. The students had an opportunity to briefly experiment with manual applications using paint brushes as tools for applying glaze. In these experiments, the group discovered challenges related to maintaining consistency and control between manual applications. Students observed variations in each stroke and iteration.
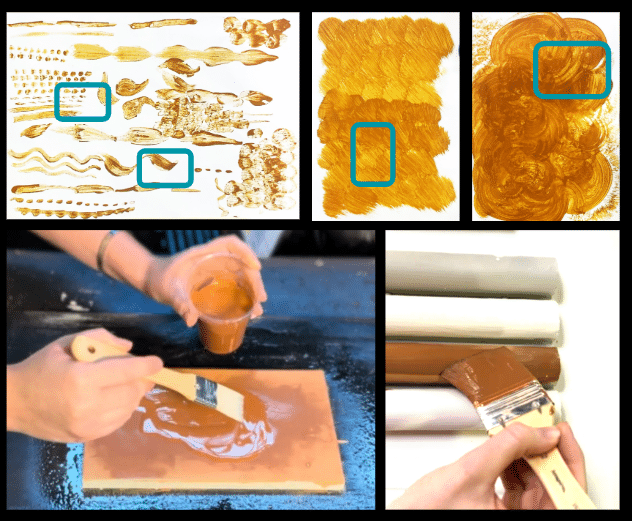
02 Manual Tracking to Robotic Replication
Once students have the opportunity to grasp the craft of glazing, they are ready to program the robots to replicate their glazing techniques. The process begins with callibration of the tracking tool, followed by the sensing / tracking + recording of the manual glazing. Once the recording is complete, the spatial plane is translated with calibration to the robot´s work surface before the robot is coded to replay the recorded application.
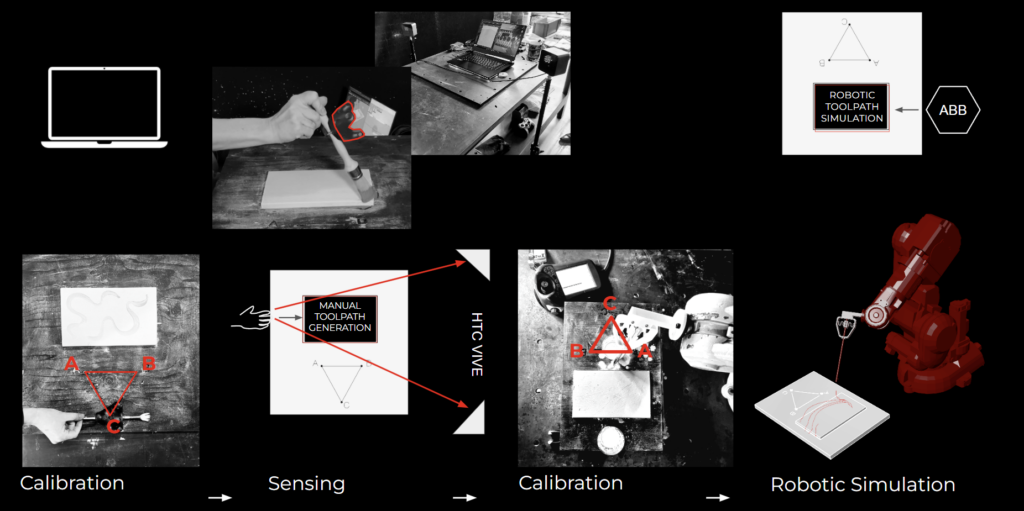
Preliminary results indicated additional variables related to motion, the medium, and the tool.
Motion
Visual comparison of recorded manual gesture (left) and robotic playback (right) for calibration, sensing of extreme wrist rotation, speed, brush pressure, brush angle.
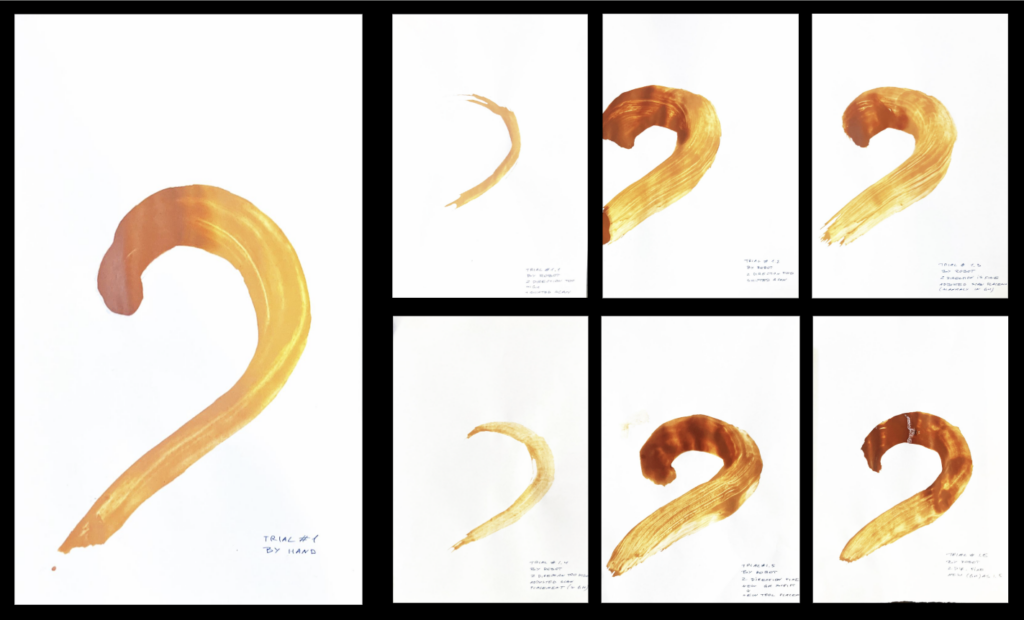
Medium
Visual analysis of manual gesture (left) and robotic iterations (right). Focus on variations in glaze viscosity due to brush type, surface type (tile or paper), and saturation of glaze on brush.
Tool Orientation
Manual Test Drawing focusing on wrist angles and the movement of the brush in the Z direction to create a pattern that focuses on the shape of the brush.
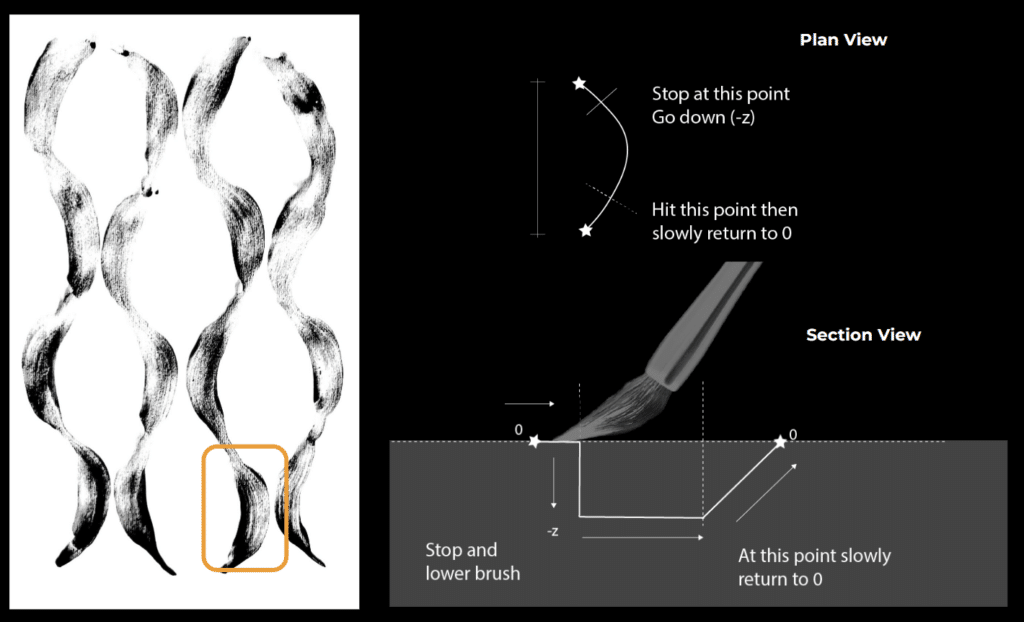
03 Post Processing
In post processing, the students photograph the manual output and robotic outputs. Through Python OpenCV, the images are simplified to their black and white form and deviations in the background texture are eliminated before these images are overlayed along the the recorded toolpath. The discrepancies between these applications are then analyzed for discrepancies.
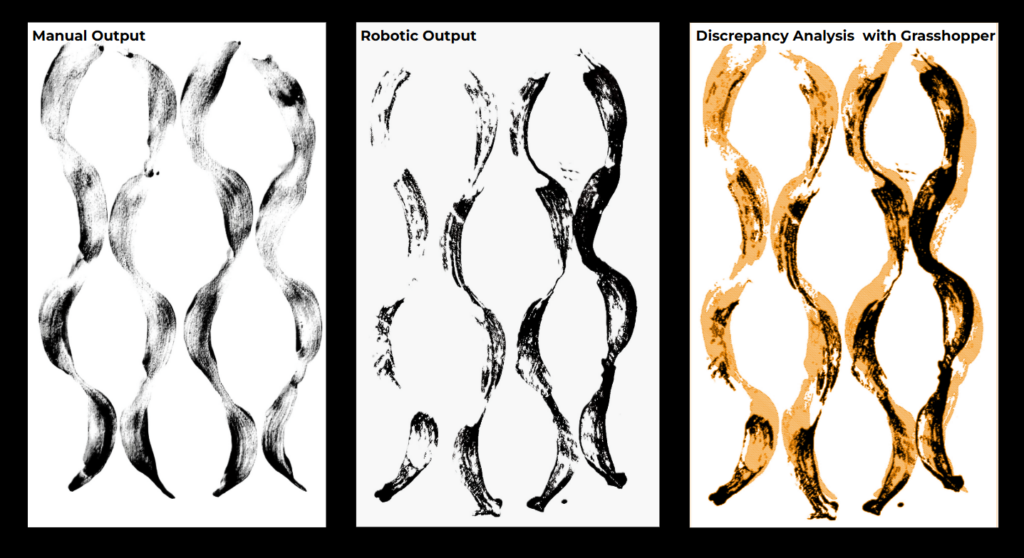
In a brush stroke application, comparisons are easily drawn where each stroke´s centerline and width deviate from the toolpath and tool dimensions. Where the glaze was applied in splatters or drops, the dispersion of the drops was more telling then the size and relative contours of each mark. The below images compare an even dispersion of spots made manually to the robotic cluster made with the same toolpath. This deviation may be more related to glaze viscocity or calibration issues.
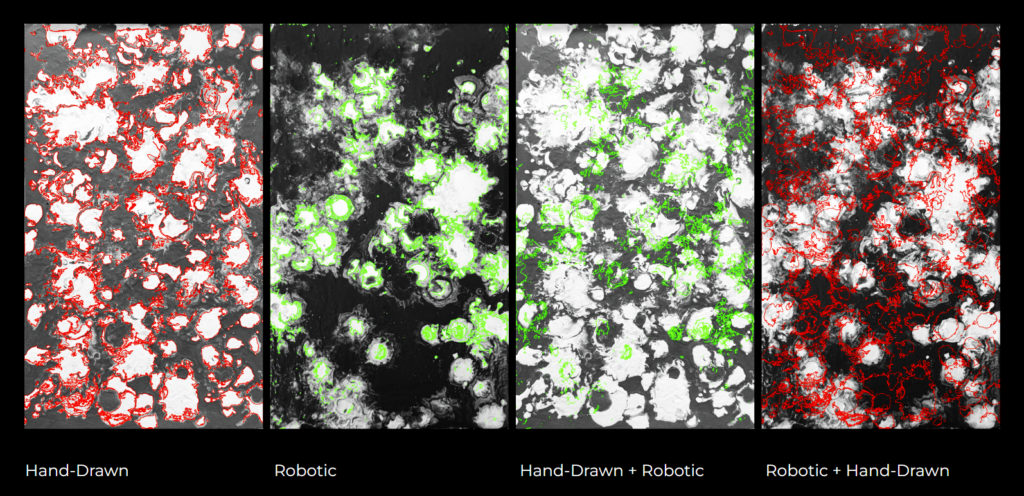
04 Robotic Production
Students take part in the robotic production, creating multiple iterations using the same recorded toolpath and tile type. Variations again become evident as the brush saturation and tile texture / viscocity continued to vary between iterations. In addition, robotic speeds, glazing visccity (dryness) over time, and depletion of glaze in the dipping cup undoubtedly changed the outputs between robotic iterations.
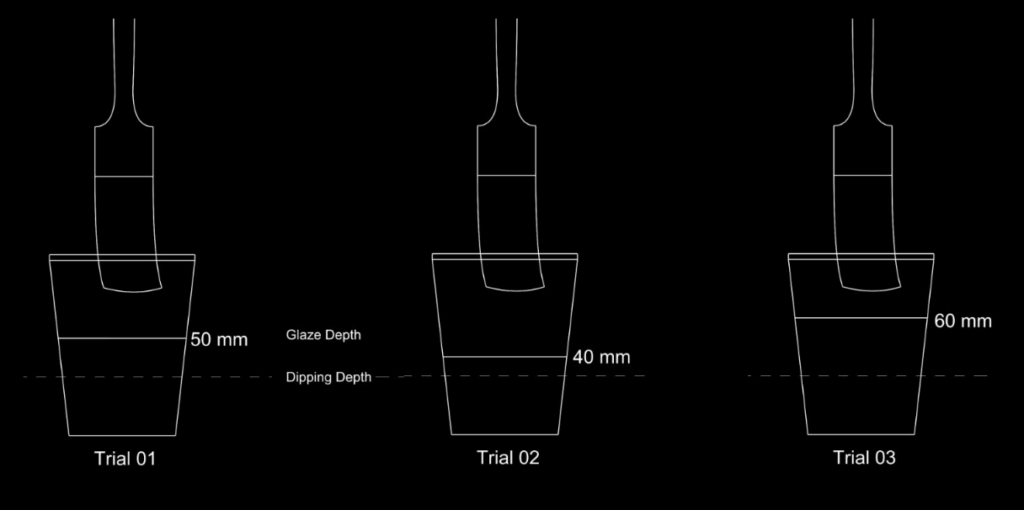
05 Results + Analysis
If the intent of the exercise was to replicate a hand-crafted technique to create a catelogue of tiles, we recognized the value in controlling the variations in the process.
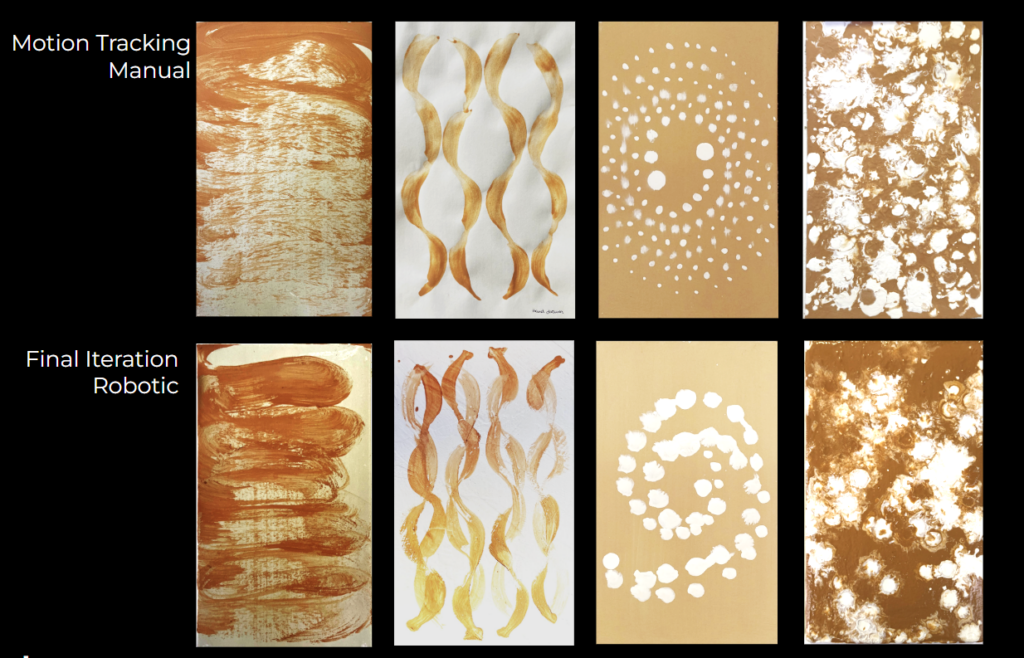
Each phase of the process presented its own challenges in maintaining a consistent output. These variables were listed here:
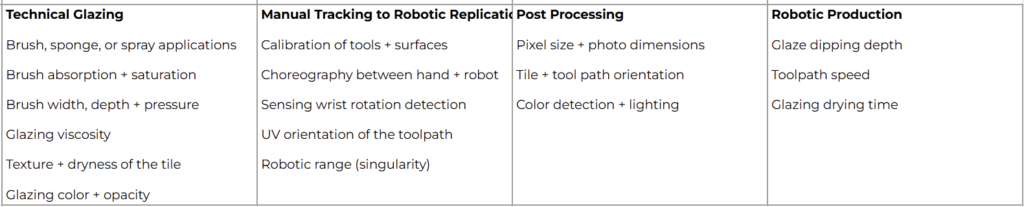
Process of tracking and replay the motions yielded detectable variations from hand gesture to robotic simulation and from robotic simulation to production. Through tools like Grasshopper and Python OpenCV, the 2D outputs created by both hand and robot can be precisely compared for further refinement of the robotic toolpath and optimized simulation of manual glazing. In order to refine the manufacturing process, the above variables would each have to be addressed and controlled to ensure a consistent output.
Conclusion
While this exercise was used to supplement a hand craft with an robotic one, the implications transcend the hand-like made ceramic glazing. The closer human motion is observed and understood, the better the synergy between human and robot in execution of a complex craft.
In craftsmanship, this application may be best suited to support humans on expediting repetitive and complex tasks. A software program developed to record hand gestures from the experts opens the possibility of plug + play expertise for any novice.
In construction, tasks that cause injury due to repetition (or dangerous conditions) can be supplemented via robotic process.