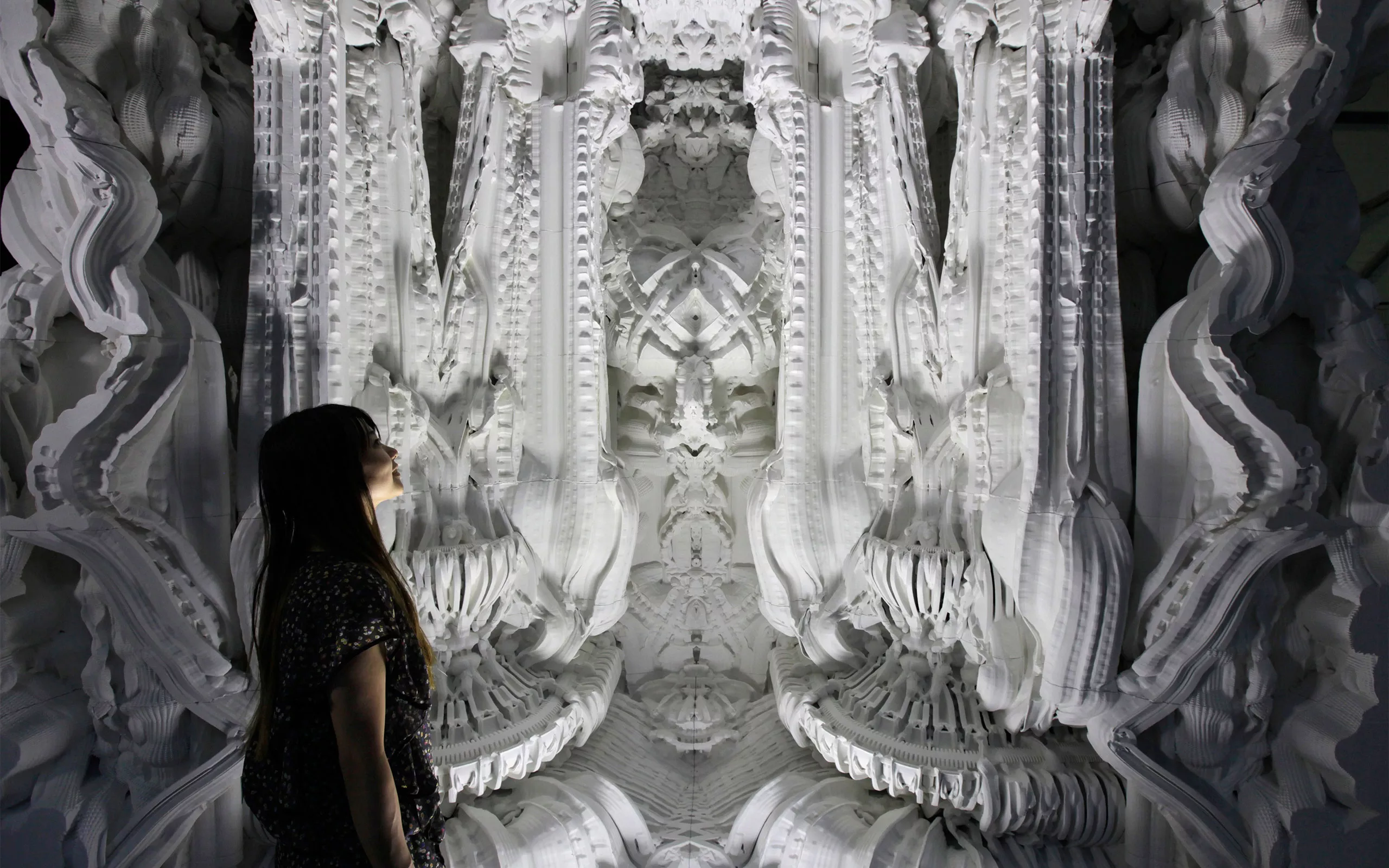
Revolutionizing Architecture with 3D Sand Printing
A Case Study Analysis by Reuben Diamond
In recent years, the intersection of computational design and 3D printing has pushed the boundaries of what architecture can achieve. The article “Printing Architecture: Castles Made of Sand” by Benjamin Dillenburger and Michael Hansmeyer explores how 3D sand printing—a cutting-edge additive manufacturing technology—can be applied to create highly complex, large-scale architectural structures that were previously unimaginable.
The Problem: Designing Beyond Traditional Methods
Architectural innovation has long been constrained by the limitations of fabrication technologies. While computational design software enables architects to imagine intricate geometries and freeform shapes, traditional construction methods often fall short. Tools like CNC machining require adapting designs to the capabilities of the machinery, limiting the realization of ambitious digital concepts.
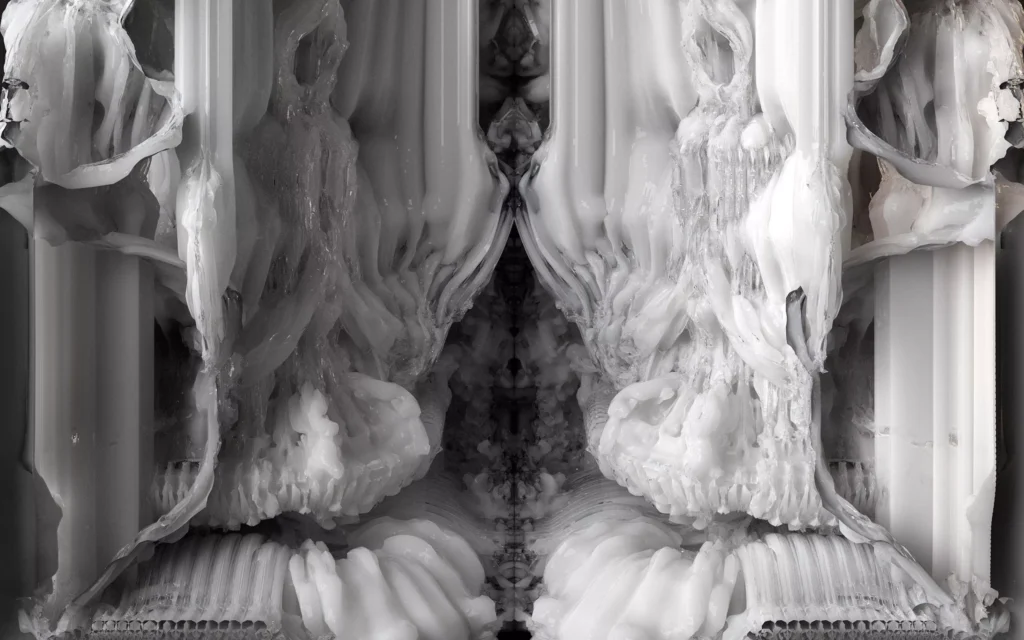
The Solution: Additive Manufacturing
Additive manufacturing, or 3D printing, offers a new paradigm for construction. Unlike traditional methods that remove material (e.g., cutting or milling), 3D printing adds material layer by layer, enabling the production of highly detailed and customized forms. However, most large-scale 3D printing technologies have struggled with trade-offs between resolution, size, cost, and material strength—until now.
Enter 3D Sand Printing
Dillenburger and Hansmeyer present 3D sand printing as a game-changing technology for architecture. This method, typically used for industrial casting, has been adapted to print large-scale architectural components with remarkable precision. Key advantages of 3D sand printing include:
- High resolution (up to 200 dpi) for intricate designs
- Large printable dimensions (up to 4 x 2 x 1 meters)
- Cost-effective and sustainable production using natural materials
- Structural capacity suitable for architectural applications
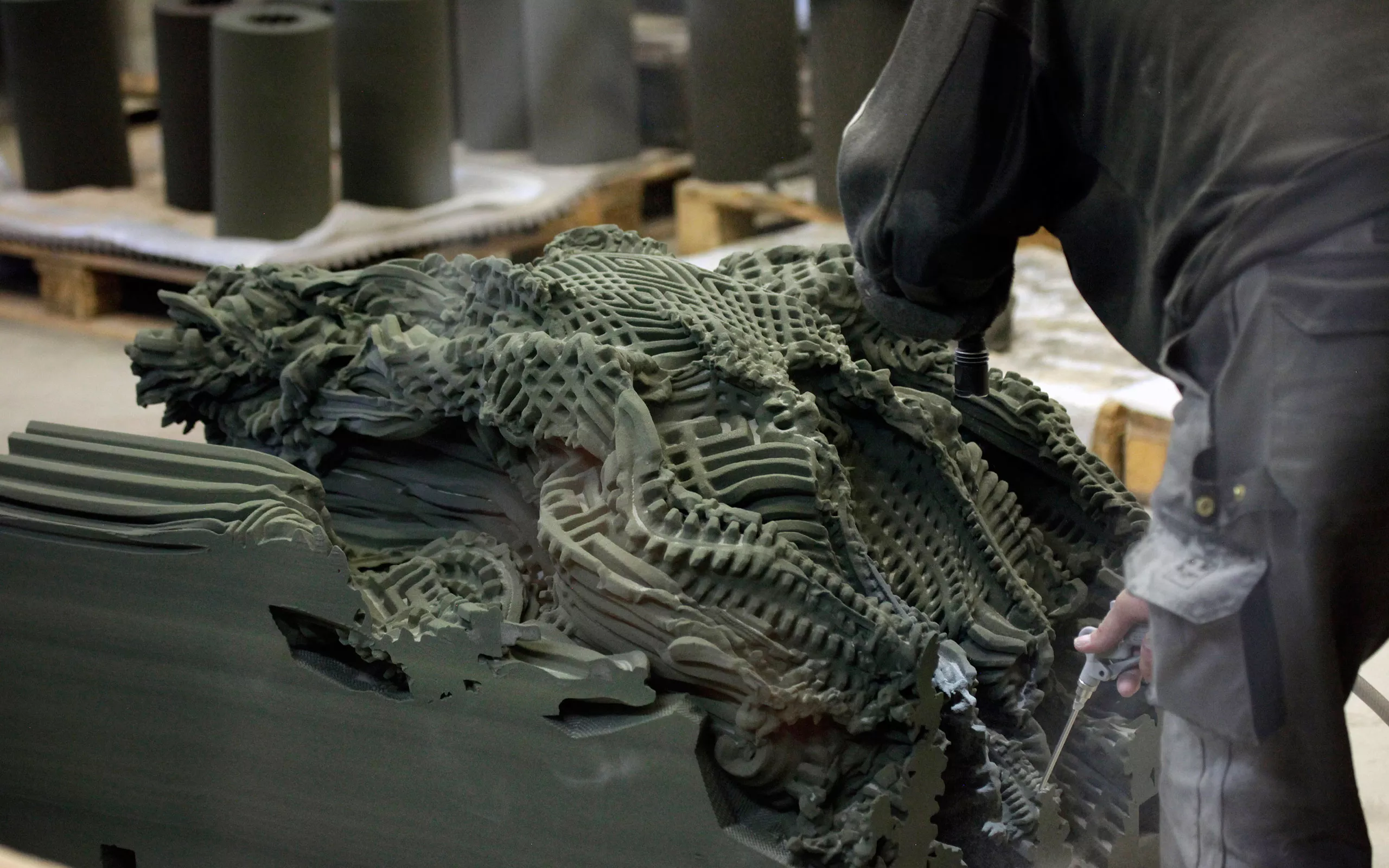
The Case Study: Digital Grotesque
The Digital Grotesque project showcases the potential of 3D sand printing in architecture. This 16-square-meter room, entirely constructed from 3D-printed sandstone, features millions of intricate facets designed through an algorithmic process called “mesh grammars.” Inspired by natural growth patterns, these algorithms generate highly detailed, organic shapes that blur the line between natural and artificial forms.
The printing process involved segmenting the design into six transportable components, each reinforced with resin for structural stability. Post-processing techniques, including a smooth coating, further enhanced the aesthetics and durability of the elements.
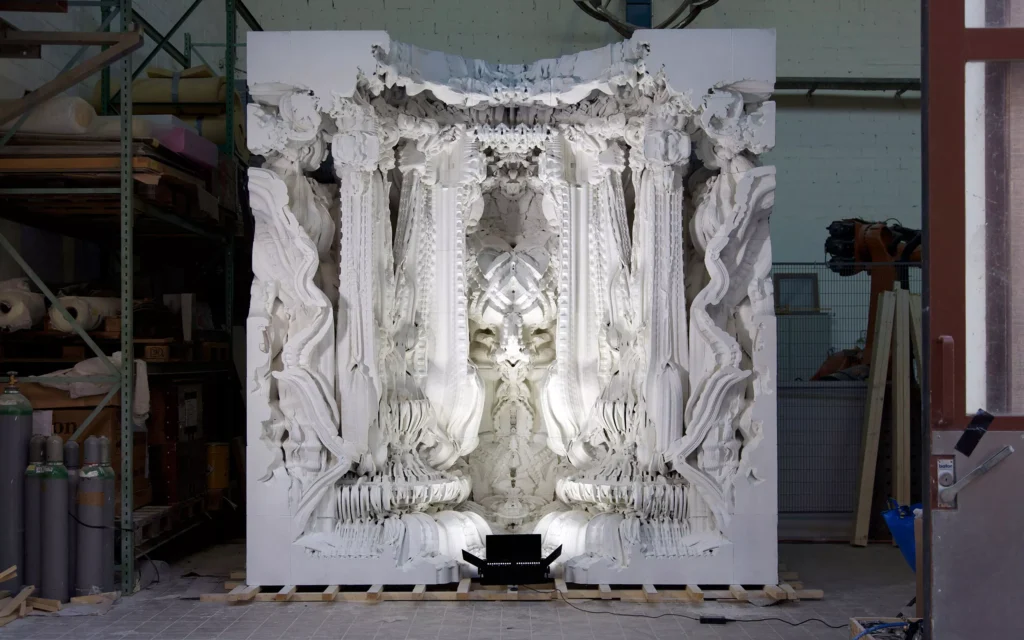
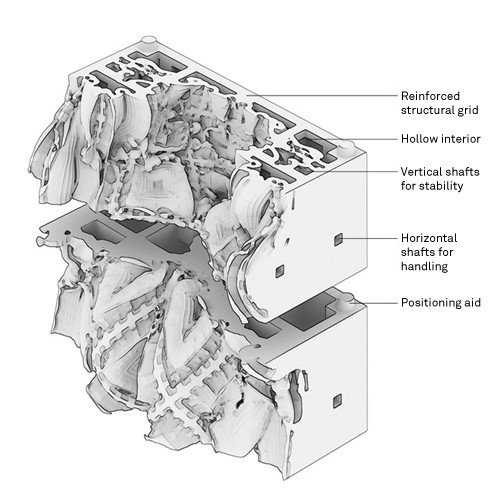
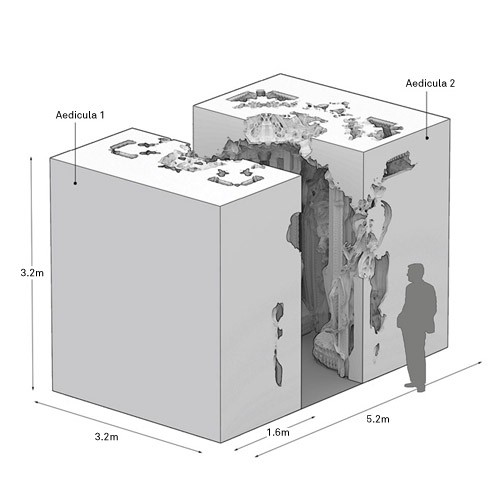
Challenges and Future Directions
While the project demonstrates the immense potential of 3D sand printing, there are challenges to address:
- Improving material properties like fire and weather resistance
- Enhancing surface smoothness without sacrificing detail
- Optimizing structural stability and weight
- Developing efficient joints for assembly
Interdisciplinary research in computational design, digital fabrication, and material science is needed to refine these processes and expand their applications.
A New Era for Architecture
Dillenburger and Hansmeyer’s work highlights the transformative potential of 3D sand printing. By enabling the creation of complex, large-scale forms with unprecedented precision, this technology redefines architectural possibilities. From reconstructing historic buildings to fabricating futuristic designs, 3D sand printing offers architects a new level of creative freedom and structural innovation. As the technology evolves, it holds the promise of making non-standardized, custom-built architecture accessible on a broader scale.
Through projects like Digital Grotesque, the future of architecture is being reshaped—layer by layer.
Digital Grotesque in Figures
Virtual:
• Algorithmically generated geometry
• 260 million surfaces
• 30 billion voxels
• 78 GB production data
Physical:
• Sand-printed elements (silicate and binder)
• 16 square meters, 3.2 meters high
• 11 tons of printed sandstone
• 0.13 mm layer resolution
• 4.0 x 2.0 x 1.0 meter maximum print space
Team
Fabrication:
Maria Smigielska
Miro Eichelberger
Yuko Ishizu
Jeanne Wellinger
Tihomir Janjusevic
Nicolás Miranda Turu
Evi Xexaki
Akihiko Tanigaito
Video / Photo:
Demetris Shammas
Achilleas Xydis
Partners and Sponsors
Chair for CAAD, Prof. Hovestadt, ETH Zurich
Department of Architecture, ETH Zurich
Voxeljet AG
FRAC Centre
Strobel Quarzsand GmbH
Pro Helvetia
Research for the Digital Grotesque project was carried out at the Chair for CAAD at the Swiss Federal Institute of Technology (ETH) in Zurich. All components were printed by Voxeljet AG. The first part of the grotto is a commission by FRAC Centre for its permanent collection.