Main idea for this research is to:
- Use industrial reconstruction developed by ROS-industrial (ros_industrial_reconstruction_github)
- understand the parameters of the depth camera to get better resolution of scan
- expand this understanding to create an optimized workflow to scan non-standard raw wood
Requirements + Setup
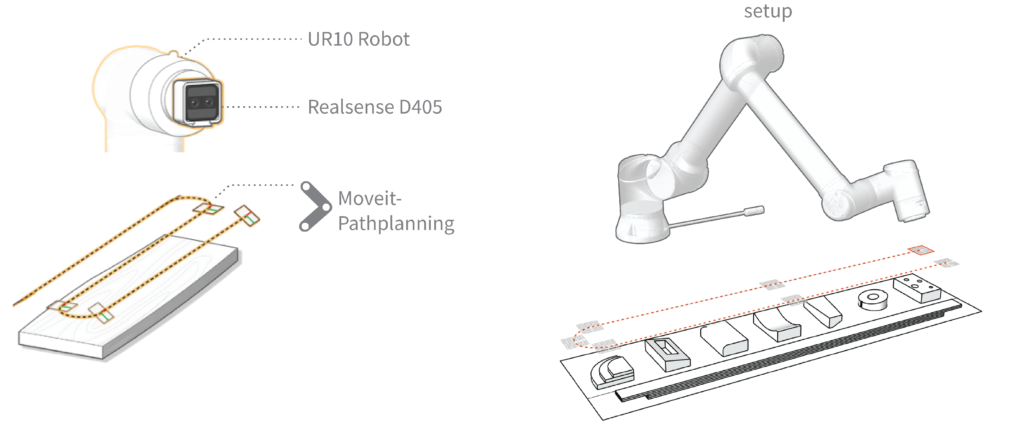
This package requires a depth camera (for rgb and depth data) and an industrial robot (to broadcast its state, and track movement of the attached camera). The path planning is done with Moveit Motion Planning (moveit_github). The motion planner used for this particular series of experiments is Pilz because it is the simplest to implement and more predictable.
Path planning workflow
Different experiments had to be conducted to understand the best parameters to obtain a better resolution scan. The Realsense D405 works better with short-range distance, with approximately 7cm from the scanned object. The following tests are done with sending a single pass (two goal poses), with an adjustment to two parameters of the reconstruction node that affects the resolution: Voxel Length and SDF Trunc.
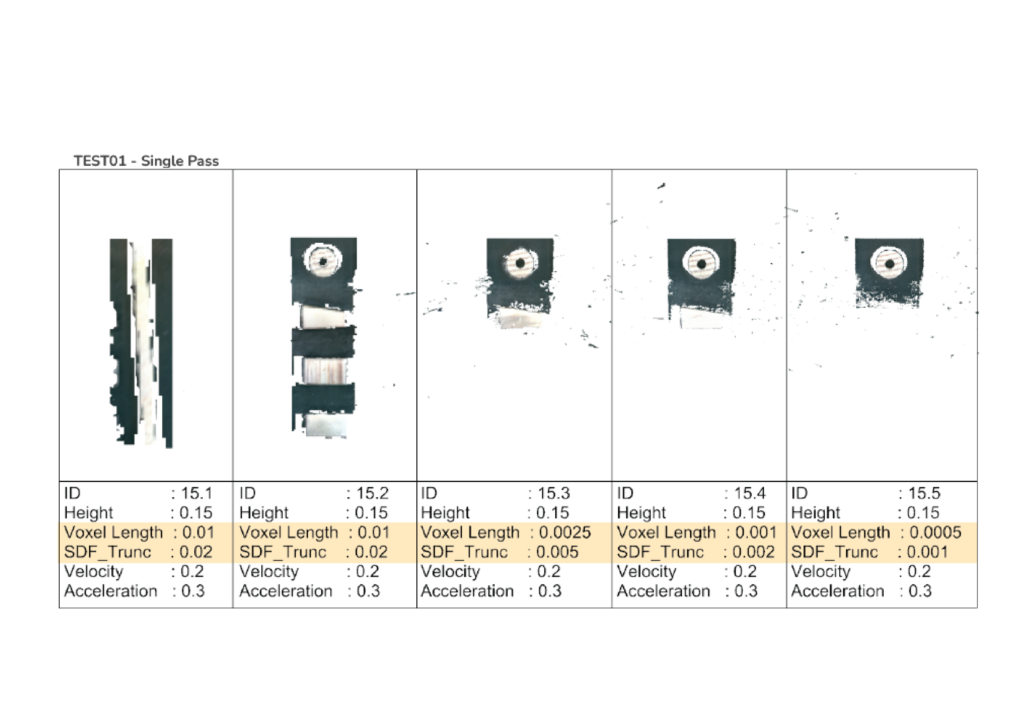
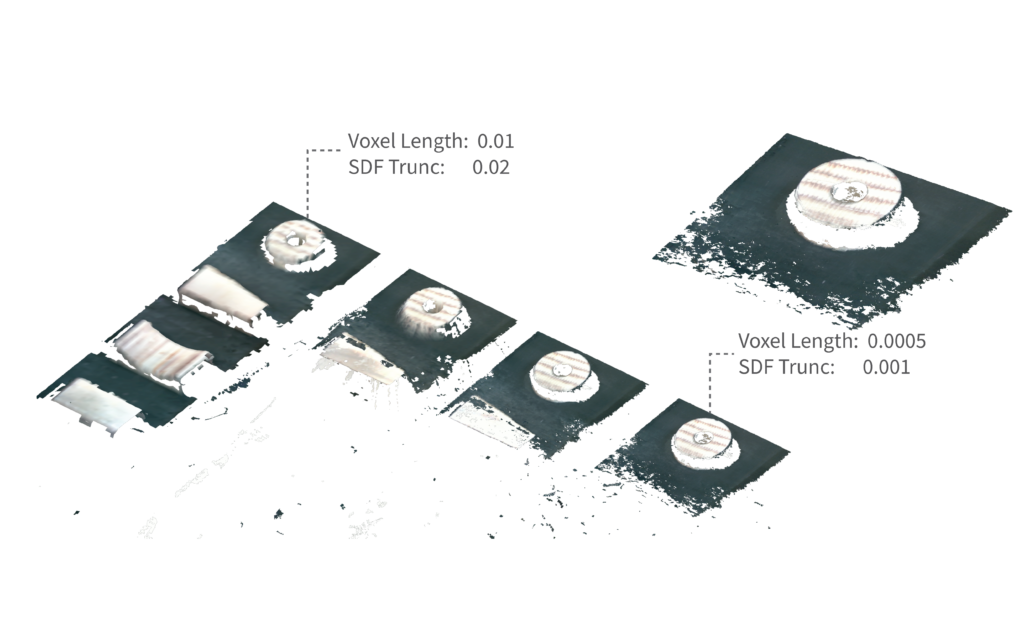
The results of this initial research is that with the distance ranging from 7 – 8cm from the scanned objects, voxel length of 0.0005 provided an ideal resolution of scan. However, there were anomalies in the scanned result that need to be investigated. Further testing of introducing tilted camera angle and extra passes require more investigation on path planning, and potentially require the use of different path planner.