The purpose of the study is to investigate a potential solution for the increasing urban expansion in Cairo’s informal settlements.
Could a timber lattice system growing vertically on the roofs of the urban context offer the programmatic growth needed for the community?
- Egypt population is rapidly increasing reaching above 110 million by the year 2023.
- Around 40% of the population live in urban area.
- The rapid increase in population led to a wide spread of informal settlements adjacent to active city center.
- Government initiatives to relocate the inhabitants is underway, however the rate cannot keep up with the current situation.
- The nature of these communities is based on “family homes” built from local materials (mainly concrete and red bricks).
- Those dwellings expand vertically (due to the high density) as the family grows.
With different architectural applications depending on the program such as residential, community facilities and vertical elements such as pigeon towers. We started looking into a specific module which is the residential, the most common one, starting with the volume, adding the enclosed spaces, floor plates then the skin.
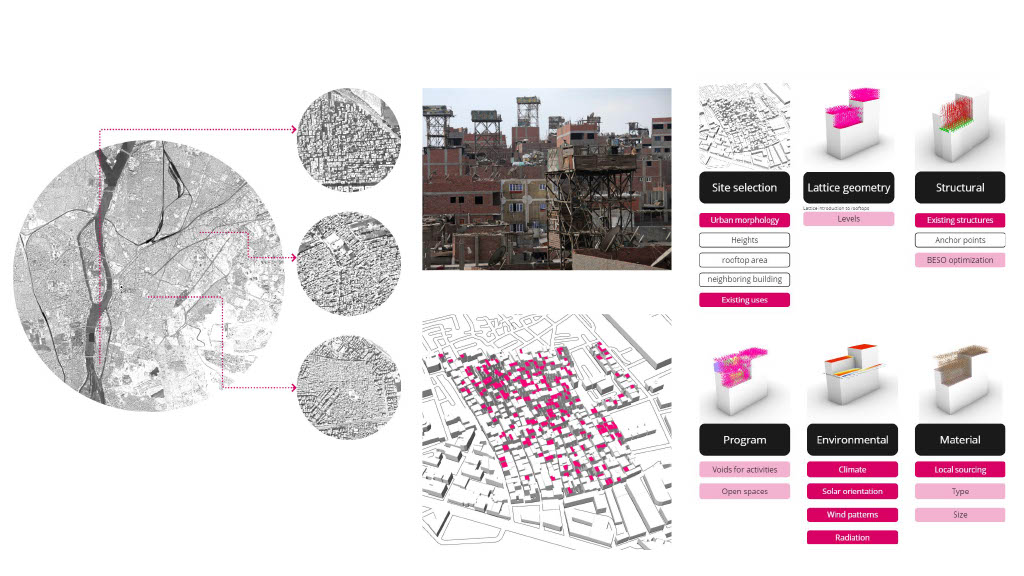
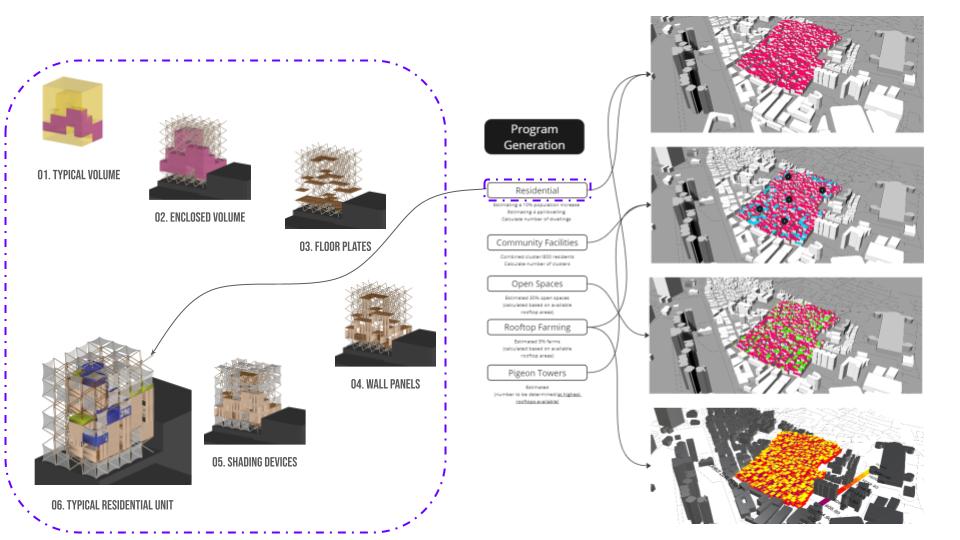
Materiality
Part of the study was to look into innovative, locally sourced materials for construction. Recycled palm tree wood turned into steel reinforced MDF, palm fronds window elements, as well as recycled cotton shading elements in addition to recycled steel joint system. Our cited materials are locally sourced, recycled materials.
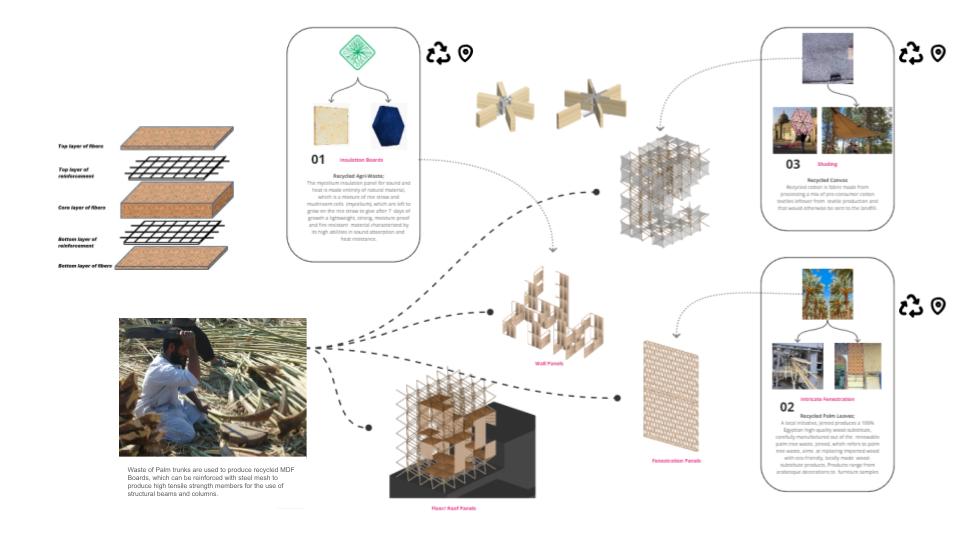
Structural Design Analysis
Starting with the initial thoughts of the module and system overall configuration, we did some preliminary testing of multiplicity, module sizes, layering, shapes led the way to further thinking about how architectural apertures would form in addition to various density depending on structural need while maintaining the architectural intent.
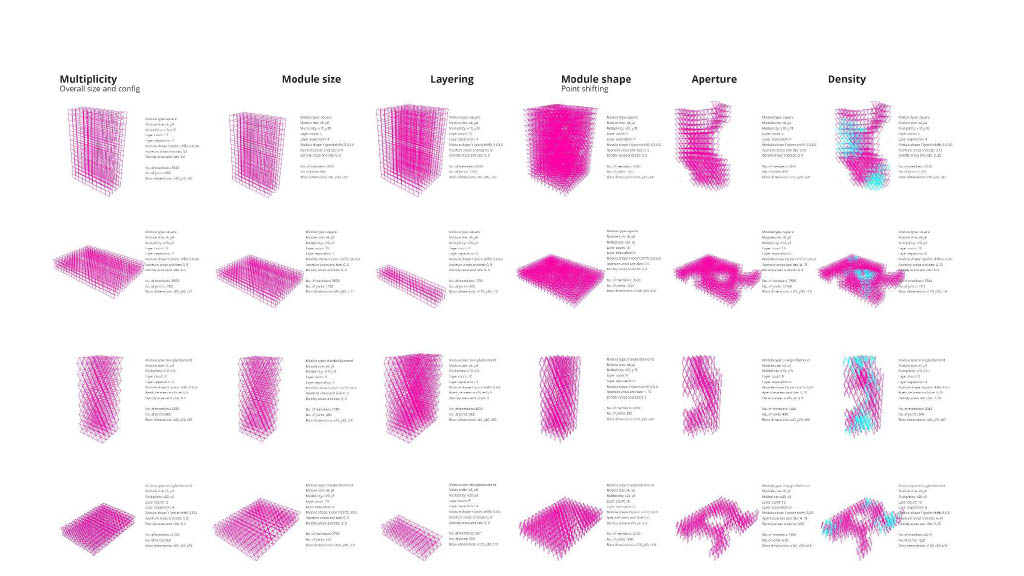
Structural Design Explorations and Optimization
Within the design exploration was to run a geometrical optimization exercise for initial connections between points horizontally and vertically to reduce material use.
Our optimization goals included:
- Minimizing Displacement
- Reducing Overall Material Use based on member utilization.
- Optimizing Cross Sections and Member Sizes
- And resultantly reducing overall carbon impact.
We have used a simplified line model to run the Finite Element Analysis for our primal analysis, trying to minimize utilization and displacement using three cross section sizes; 1cm, 6 cm and 10cm, through a process of elimination of slender members.
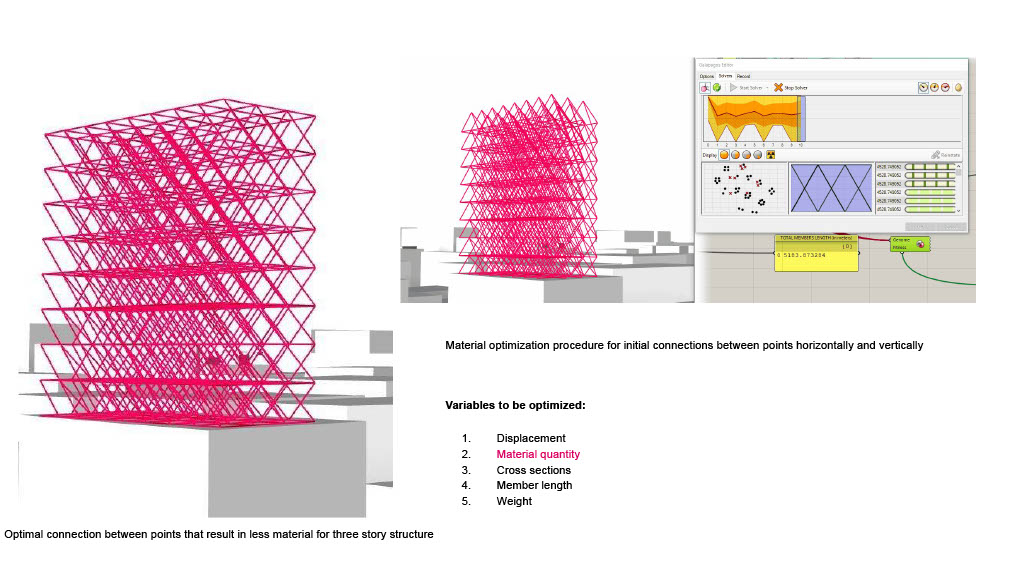
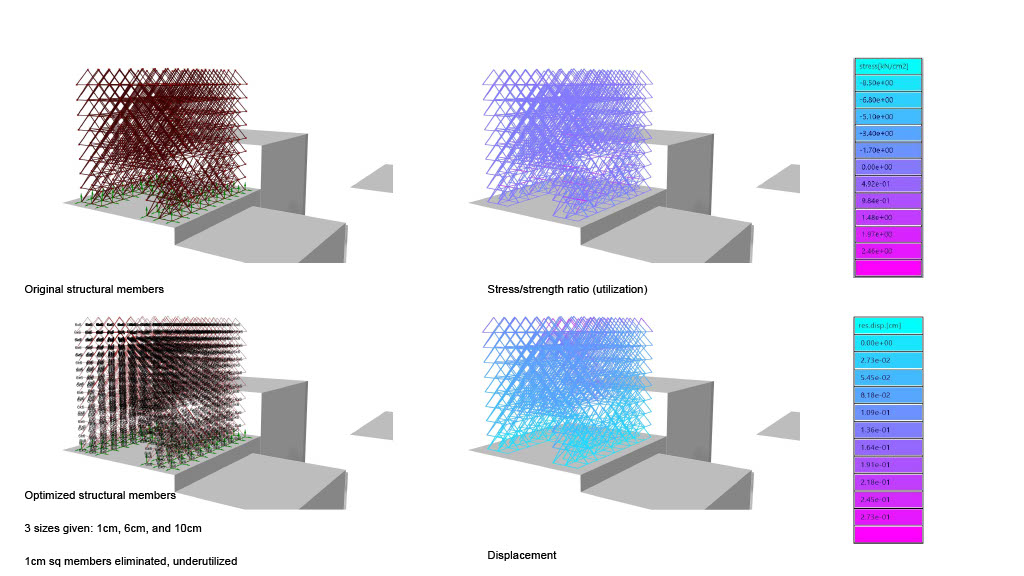
For the overall structural optimization process we explored 2 strategies:
- The first one, described before, was to use 3 member sizes (1cm, 6cm and 10cm) with the purpose of locating where within the system the thinnest one was being utilized the least.
- The second strategy consisted of making use of the Bidirectional Evolutionary Structural Optimization (BESO) procedure within Karamba 3D eliminating the underutilized members for 50cm and 1m module configurations.
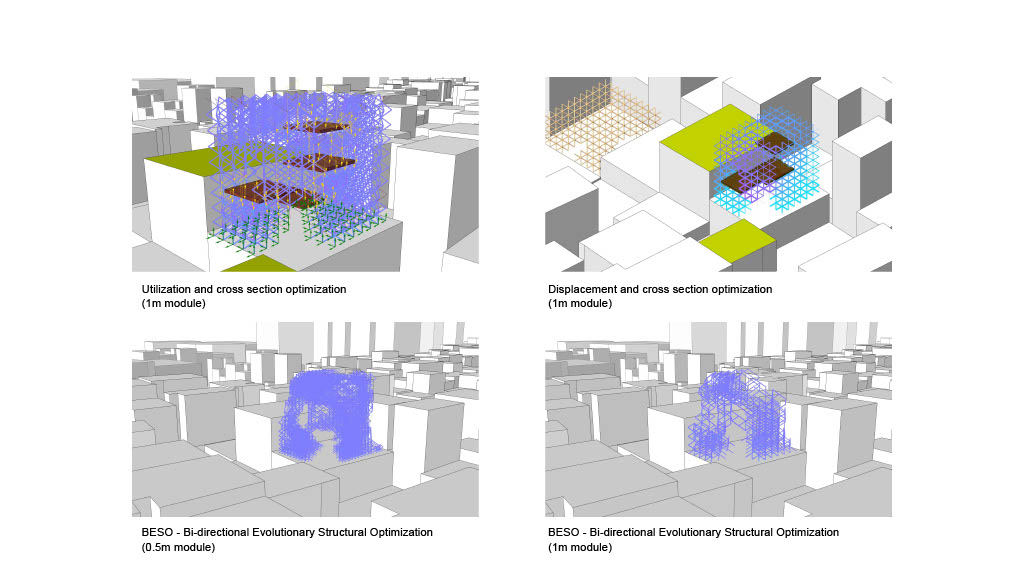
Learning from earlier explorations and introducing architectural programs within the lattice, we then started looking at 2m long modules at 10 and 30cm cross sections. Optimizing the options to achieve minimum mass while striving for minimum displacement and utilization of the members. We reached the conclusion that a hybrid configuration between diagonal and cubical lattice systems was more effective.
Further optimizations through evolutionary Multi-Objective engines were conducted to fine tune our goals of minimized overall mass by removing under-utilized members while reducing the maximum displacements to 1cm.
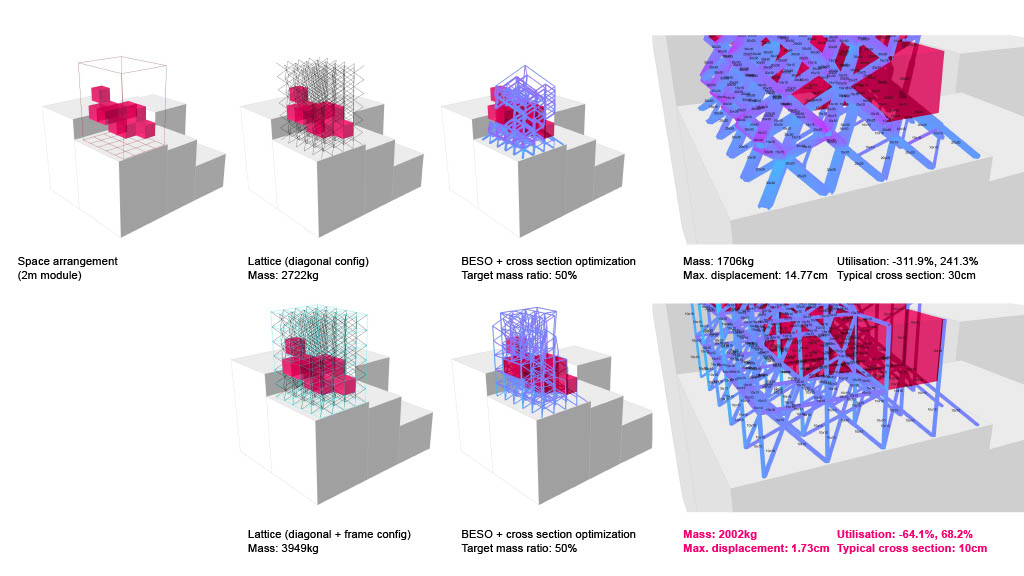
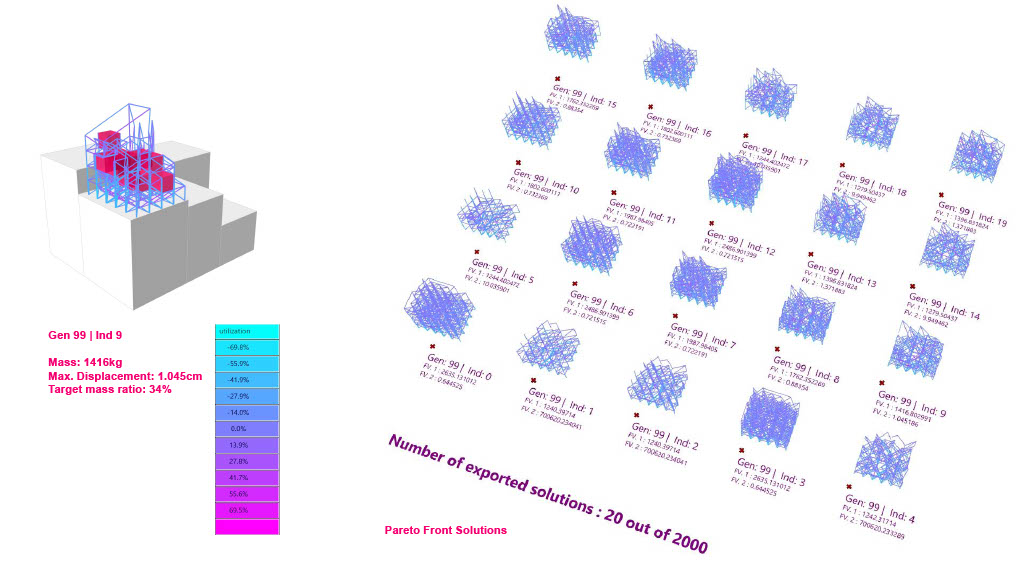
Results
Our optimization run on a typical residential configuration resulted in:
- 66% reduction in material quantities
- And 64% in weight (mass).
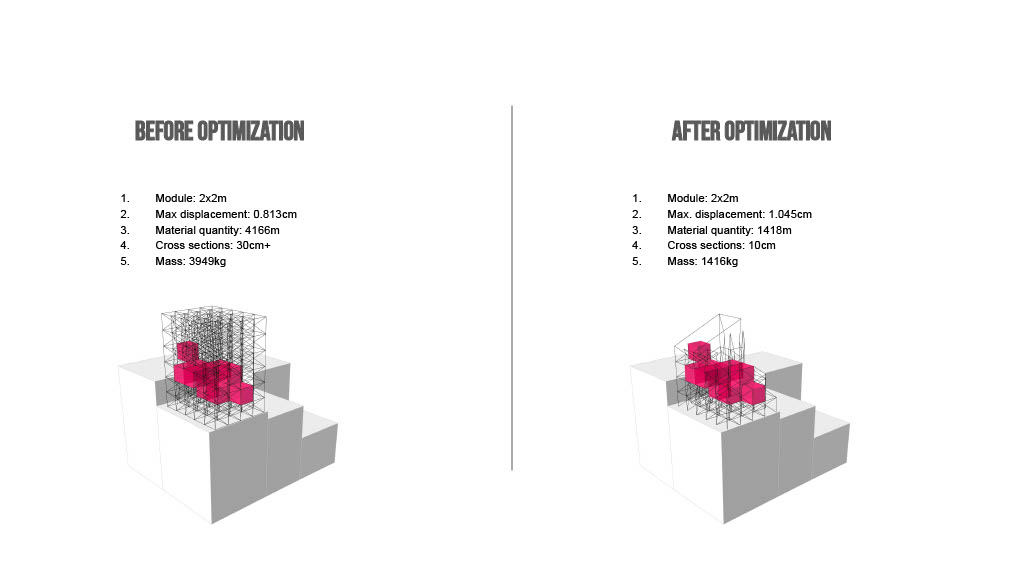
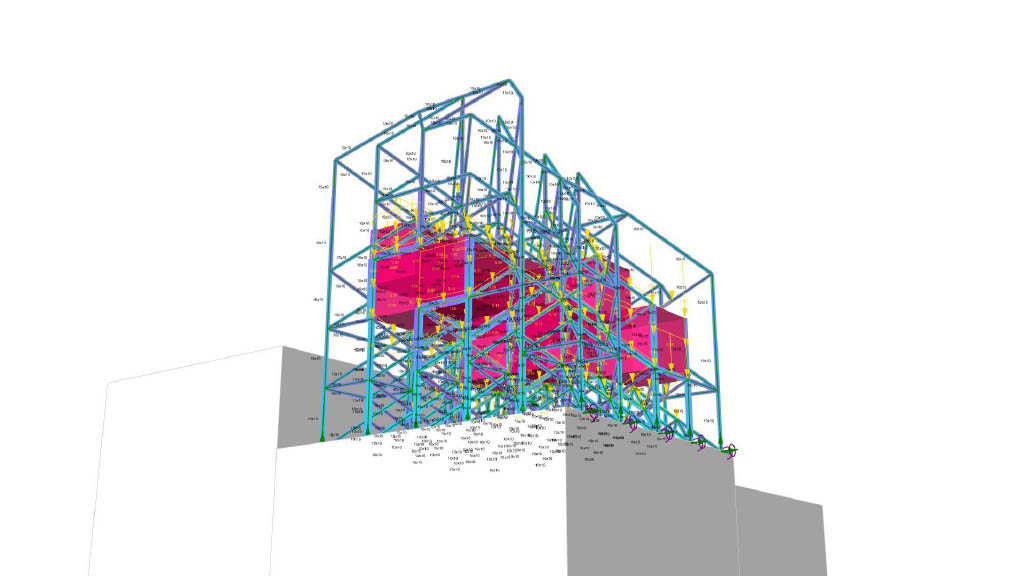
The diagram shows the load distribution for the optimized model. A connection between the lattice system and the inhabited volumes as well as the connection to the existing structures.
Using the Elliott Wood Structural Carbon tool we assessed our LCA performance before and after structural optimization. From 110 kgC02e/m2 to 43 kgCo2e/m2, considerably reducing our carbon footprint by reducing timber structural members for the same GFA (60 m2). SCORS Rating goes from A to A++. Keeping in mind that the LCA studies are based on virgin timber and not the recycled sources we have cited. This gives us the metric for the environmental impact we have made by optimizing our structural members.
Optimized structural configuration considerably reduces the impact caused by the structural frame, bringing its share down by 60% and an overall improvement of 61% considering the reduction in number of joints etc. It is also worth noting that for the structural timber, in the optimized configuration, has a module D or the recyclability index at 27kgCo2e/m2 to the overall 48kgCo2e/m2 of its footprint created.
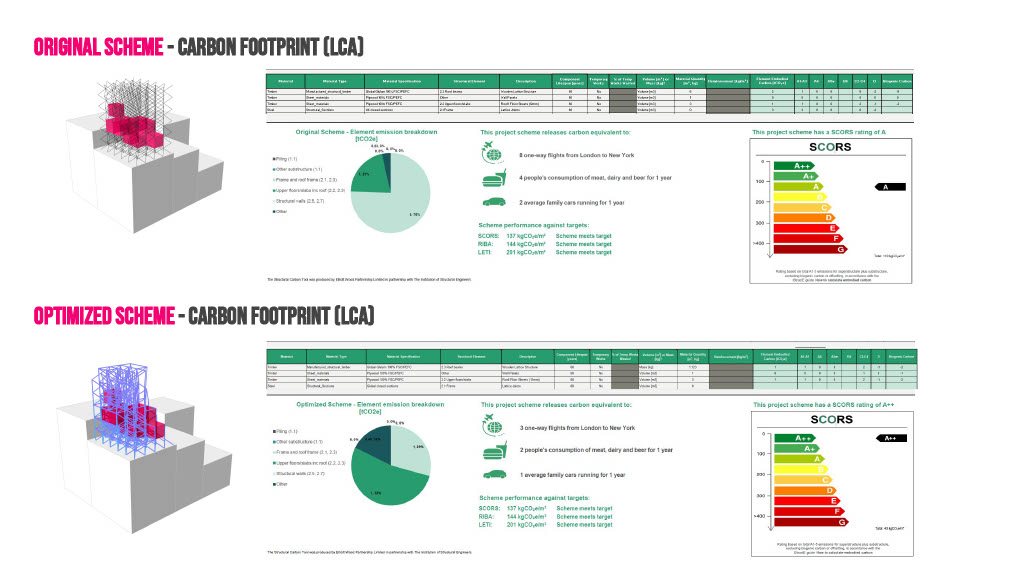
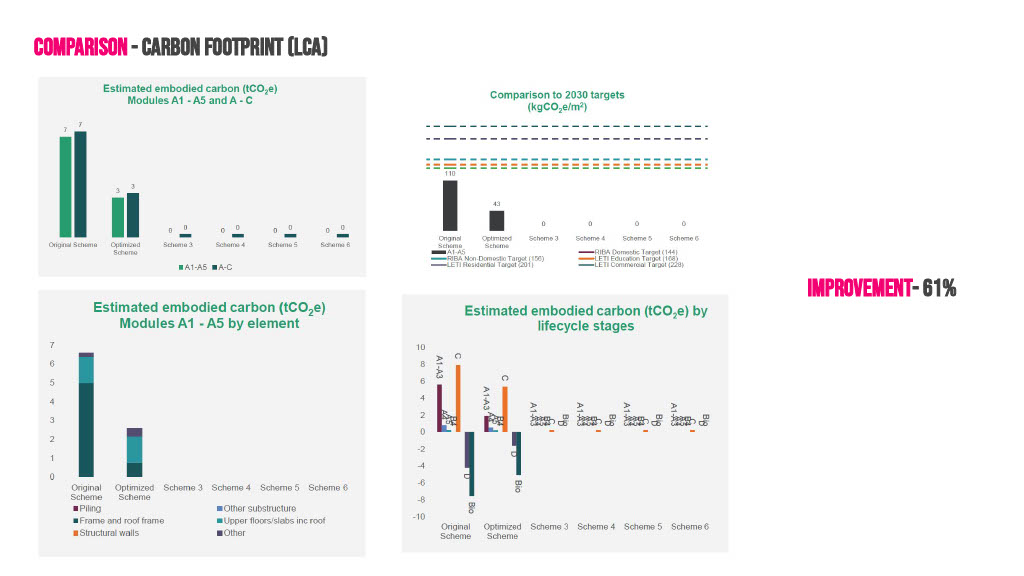
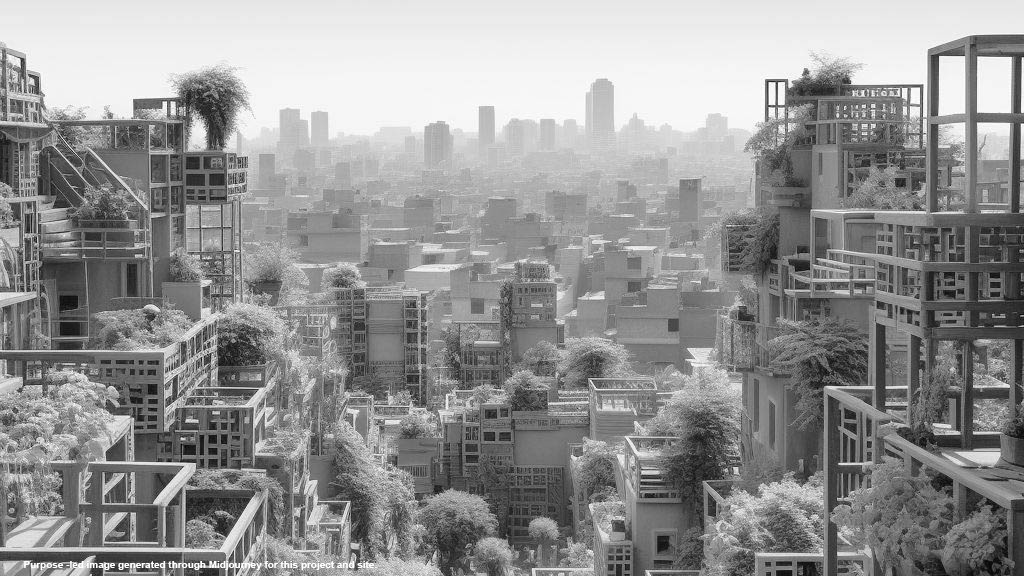