The goal of this project is to present a Case Study about an adaptive additive manufacturing toolpath with a robotic arm. The process of printing sometimes brings variations or corrections on its way.
The experiment seeks to 3d print a cylinder in clay where in the middle of the process, two pieces of PVC pipe will be manually located so that the path correction will finish the second half avoiding the new elements.
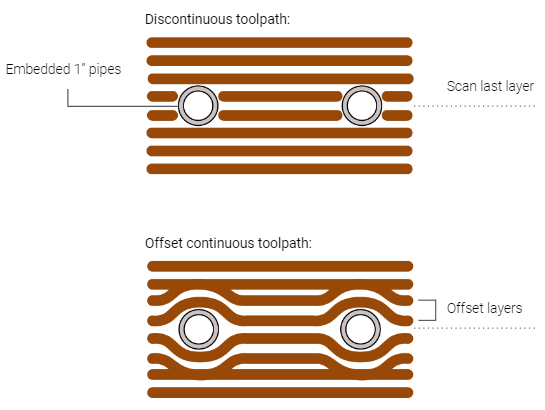
The methodology process will be held as follows:

An the workflow of the process will be divided in:
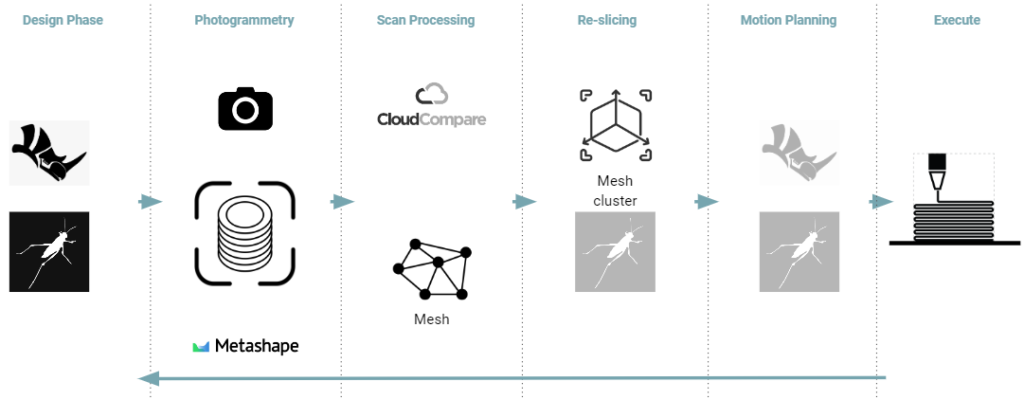
The design phase includes the basic geometry that will be set on Rhino, then printing toolpath design on Grasshopper.
After printing the first half and locating the 2 objects, there will be a photogrammetry process to capture every detail on the surface and obtain a point cloud of the new geometry.
The point cloud will be processed and transformed into a mesh which will become lighter to work with.
This new geometry will be re-sliced to reorder the new motion planning that will become the new execution path.
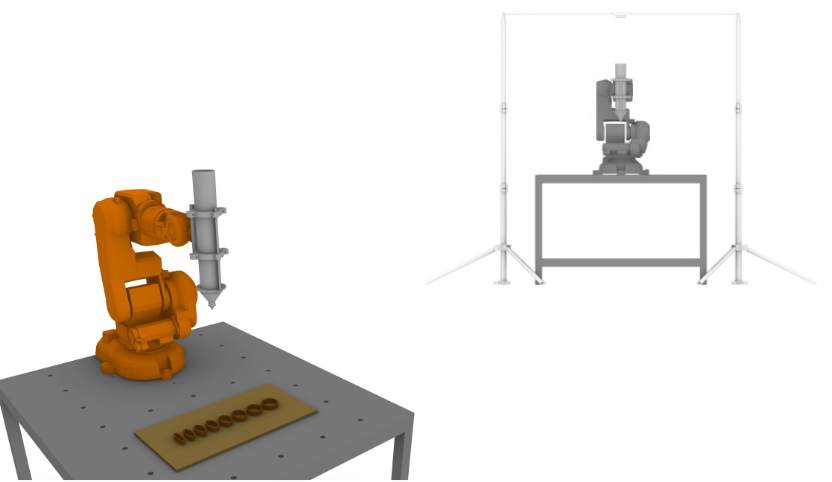
This are the results of the scanned cylinder as a point cloud after the photogrammetry process:
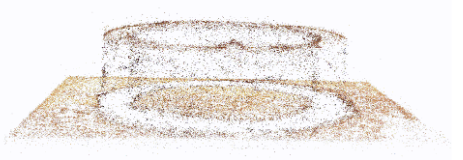
and the mesh conversion compared to the digital toolpath design:
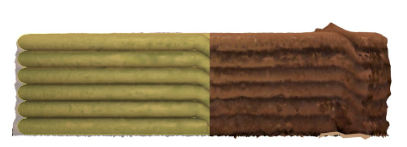
The alternative presented before using a depth camera would include a Realsense D405 camera fixed on the top or 2 pointing at 45º on the sides of the end effector as shown below:
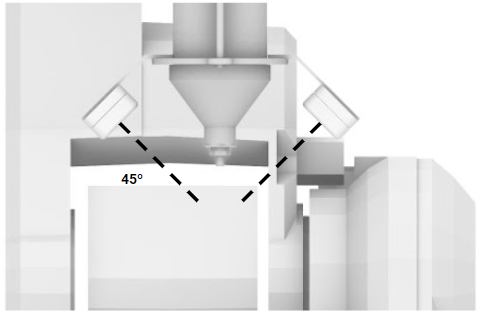
The depth camera will transform the image into a grayscale and HUE augmentation image, where we can mask the new elements defining its height on the model that we will use to offset the new layer over this model to adapt the toolpath to the new geometry.
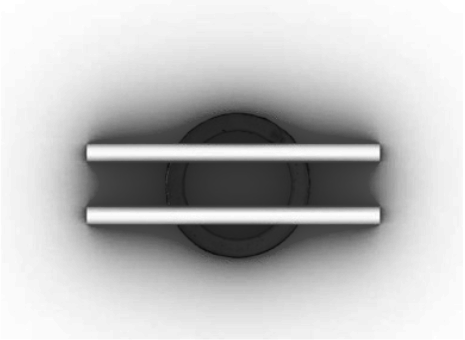
This is the final workflow of the actions taken by the human and the robot along the process:
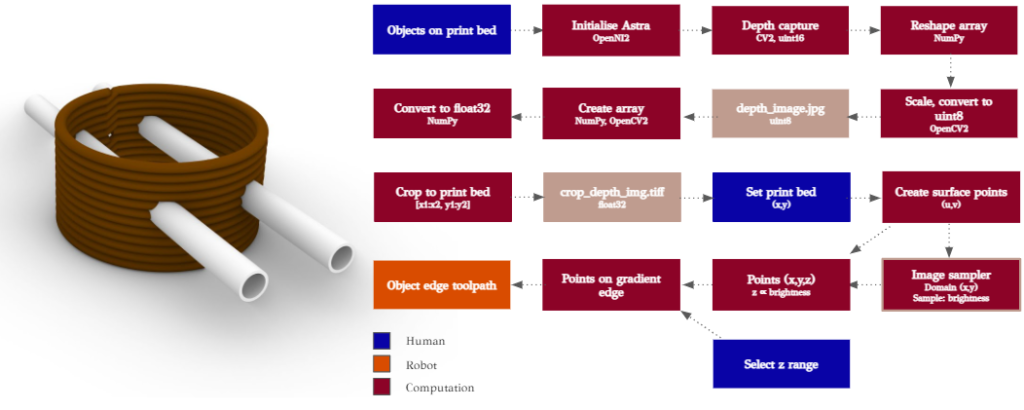
Some further steps in the process:
- Create object libraries
- Print other geometries
- Scan different objects
- Add infills
- Print over irregular 3d surfaces
Context aware AM is a project of IAAC, Institute for Advanced Architecture of Catalonia developed at Master in Robotics and Advanced Construction, in 2022/2023 by:
Student: Alberto Martínez | Faculty: Vincent Huyghe