Testing the potential of cork as a construction material through non-planar 3D printing of computationally generated branching structures.
INTRODUCTION
Our investigation takes place against the backdrop of rapidly growing trends towards computational design tools and advanced construction methodologies. This investigation forms part of a 1 week workshop which focusses on additive manufacturing of biomaterials. In particular our investigation builds on the research that was done in April 2024 at Iaac on non-planar 3D printing of cork. We aim to go further and test the potential of cork for large scale non-planar printing, our goal height being 450mm. Our initial goal was to see if it would be possible to produce a coffee table in this manner.
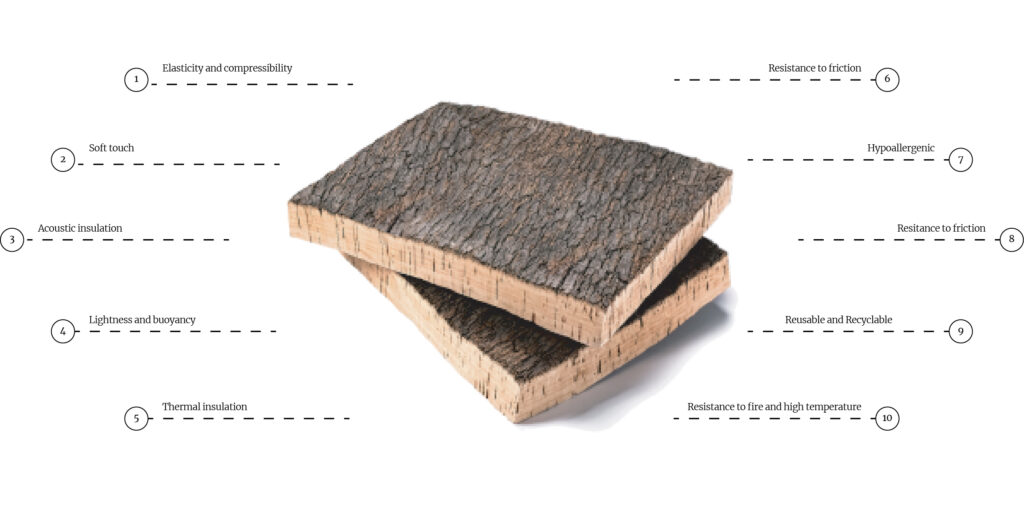
BACKGROUND
Cork has played a critical role as a part of the economy of Catalonia since the 17th century. Today 60% of cork stoppers for sparkling wines globally, are produced in Catalonia. As a material cork is incredibly versatile as it is light, elastic and has excellent acoustic and thermal properties. Cork is produced by harvesting the bark of the Cork Oak. Trees take 25 years before they are ready for first harvest and then 7-9 years between harvests. The first two harvests are unusable and and thus at about 40 years, cork trees produce their first useful harvest. The tress live for around 300 years. Today there is around 2,200,000 hectares of cork producing cork oaks trees in the Mediterranean, 27% of which is in Spain. This places Spain in an ideal position to capitalize on cork as a biomaterial for 3D printing.
CORK PASTE
Material Mix:
- Cork
- Gelatin
- Xanthan gum
- Bicarbonate
- Pectin
- Distilled Water
The materials can be divided into the aggregate, binders and thickeners, pH controller and the solvent. The cork forms the aggregate and the primary structural material of the dried biomaterial. The gelatin and pectin and xanthan all increase the viscosity of the paste, which is what allows the undried material to retain structural integrity while printing, in particular pectin makes the solution tacky and binds layers together. Given that the materials being used are all natural a big issue is microbial agents and mold, thus the best way to control this is through changing the pH, in this regard it doesn’t matter much whether the pH is acidic or alkaline, it merely need to be as far from 7 as possible. In this case bicarbonate is basic and increases the pH. Finally distilled water is the solvent which all the dry components are mixed into to create the paste used for printing, distilled water is used specifically to prevent unknown interactions from mineral in the water

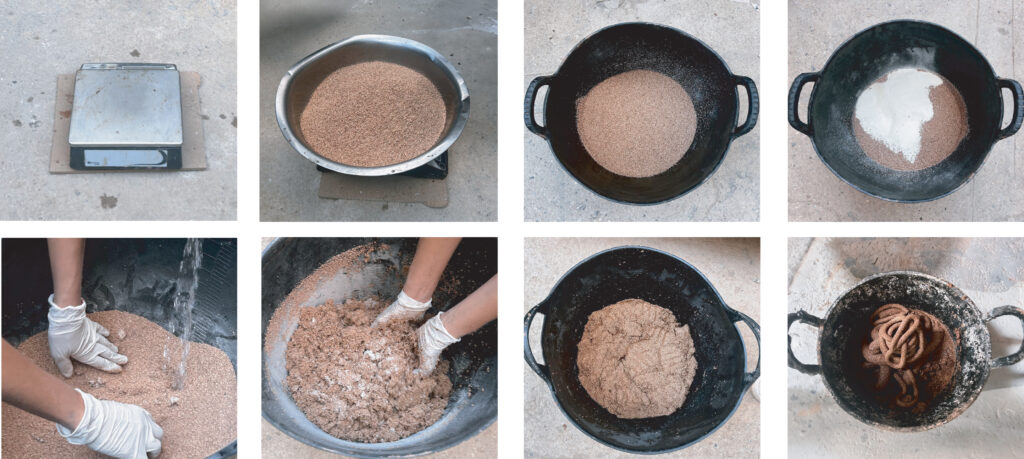
GEOMETRY DESIGN STRATEGY
Design Concept:
Our design concept was a tongue in cheek play on words on the concept of “coffee table”. In this case this manifested in our design through the plan form of a coffee bean. Using the hemispherical segmentation present in coffee beans, we split the table into two separate table tops. The next idea was to attach the table top to its base through thin tendril or branch-like connections.
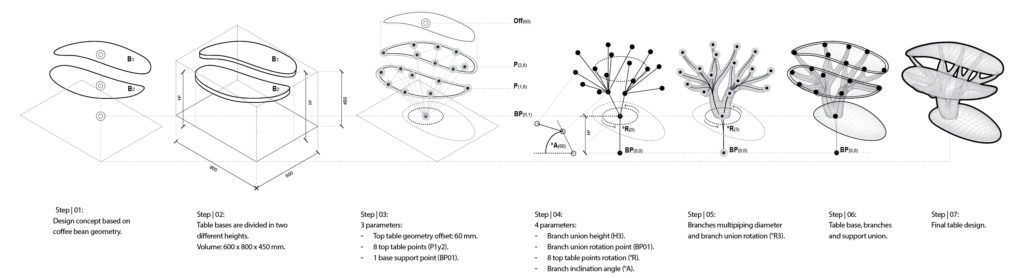
Topology Optimization:
Initially we investigated the possibility of using topology optimization as a means of generating the form of the coffee table. Topology optimization is a mathematical method of optimizing material within given constraints, with the intent to optimize for the maximum performance to material ratio, the outcome generally leads to very interesting and unique organic forms. One of the main constraints of topological optimization is that it’s outcomes are generally hard to manufacture, thus it is often the industry norm to use this as an initial form finding exercise and later use other methods to create the final manufactured form. When using planar slicing for 3D printing, topology optimization is generally easy to fabricate, however when trying to apply this to the constraints of the material and trying to create a slicing strategy, the results were not to our satisfaction.
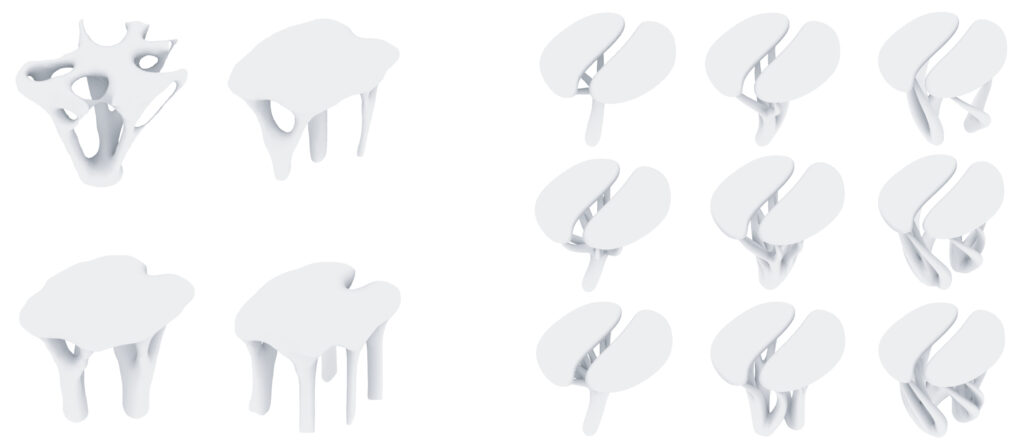
Digital Tree Generation:
Thus we opted for different form generation. It was based of off creating a 3D skeleton of a branching tree like structure and generating the volumetric form of the geometry from this skeleton. Similarly to topology optimization was also a generative process that we did not have direct control over, however in this case our geometry generation and slicing strategies lent into one another. Similarly we had much more control over the form generation which allowed us to make sure that the design and our initial perceived material constraints align. Further more our design strategy allowed for rapid iteration and prototyping.
The following outlines pseudocode that breaks down how our form generation script functions:
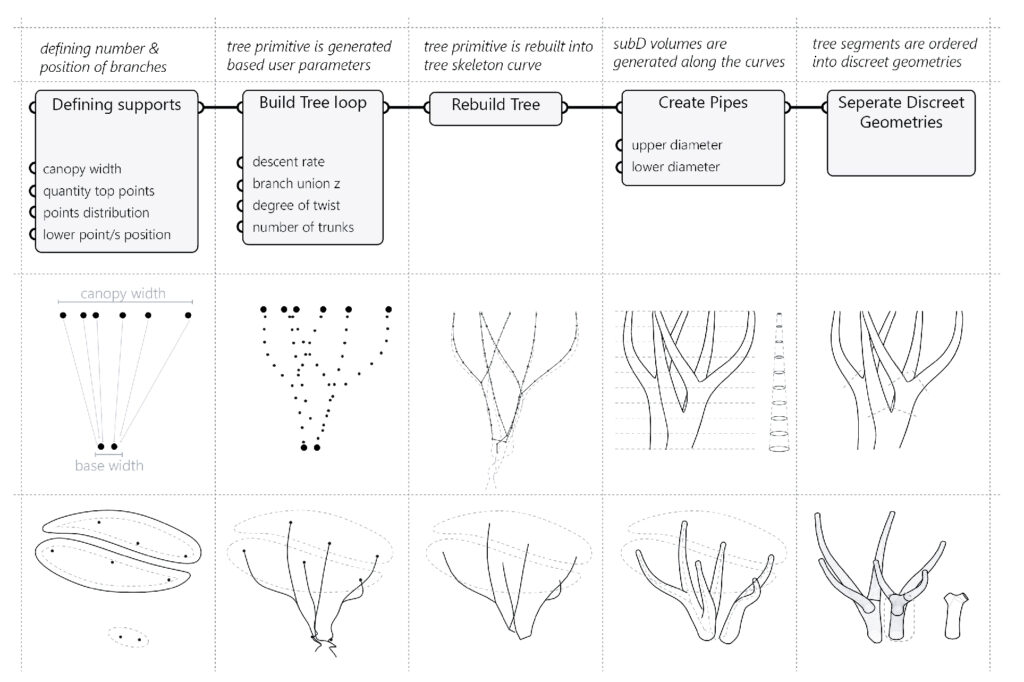
ITERATING
In the process of trying to decide on the ideal design, we decided on an iterating strategy where we would create 9 different forms each one with different variables being controlled. The optimal design is selected form this list of 9 different iterations.
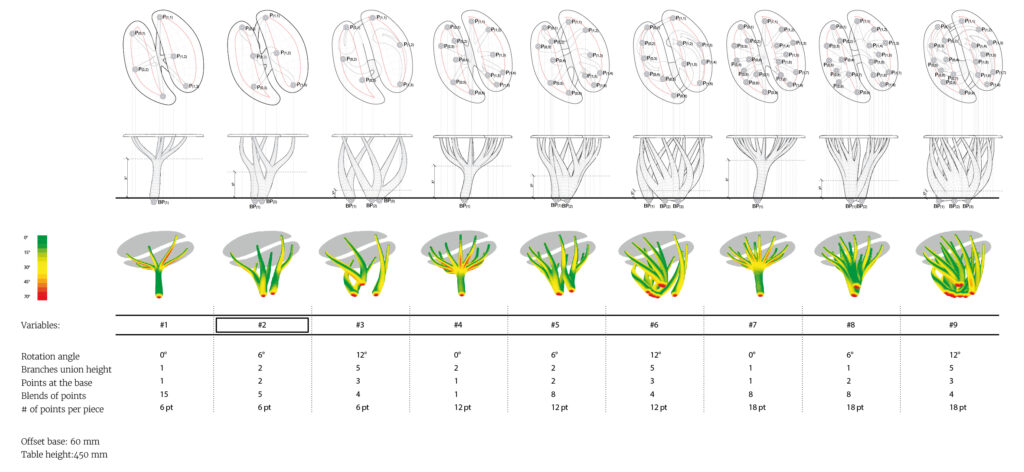
The 5 variables that were being adjusted in creating these 9 iterations are:
- Angle of twist
- Branch union height
- # of trunks
- Blends of points
- # of table top attachment points
After doing an angle analysis on each design, assessing it’s printability, stability and as well as other factors including aesthetic bias, we landed on design iteration 2.
SLICING AND TOOLPATH STRATEGY
Our slicing and toolpath strategy was intrinsically linked to the tree skeleton curves and the pipe geometry that is the base of the form generation strategy. The advantage of this is that our slicing and toolpaths dynamically adapt to any design changes that are made to the tree geometry. One of the primary features of our toolpath script is adding three components that were entirely dedicated to creating the most comfortable toolpath for the robot to follow, as we had a lot of issues with collisions with the tool and the robotic arm.
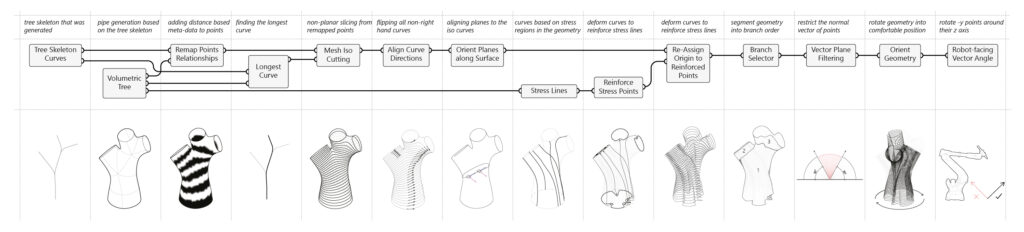
PROTOTYPE PRINTING
We printed 6 total prototypes during our investigation. Before printing our first prototype, we started by creating a simplified version of the tree structure form, so as to first dial in on the nature of the material and it’s printing tolerances, before attempting to implement our ultimate design.
Our first print humbled our expectations very quickly as the geometry collapsed at around 150mm and introduced us to the primary limiting factor throughout our entire investigation. The printable material although displaying exceptional performance when printed at small scale, at larger scales it is unable to retain it’s shape or hold its own weight.
When of the first changes that we implemented for the second print, was to add what we later called the reinforcing curves. This involves identifying structural weak points and displacing the points close close to the stress curves in the opposite direction to the normal plane of the surface. We saw immediate improvement in material performance as the point of collapse increased to just over 200mm.
Our next iteration included decreasing the angle of the branches and increasing the diameter of the form. This increase in diameter lead to an increase in stability and total print height before collapse at around 250mm.
Our next print we did the same things, whilst also further increasing the
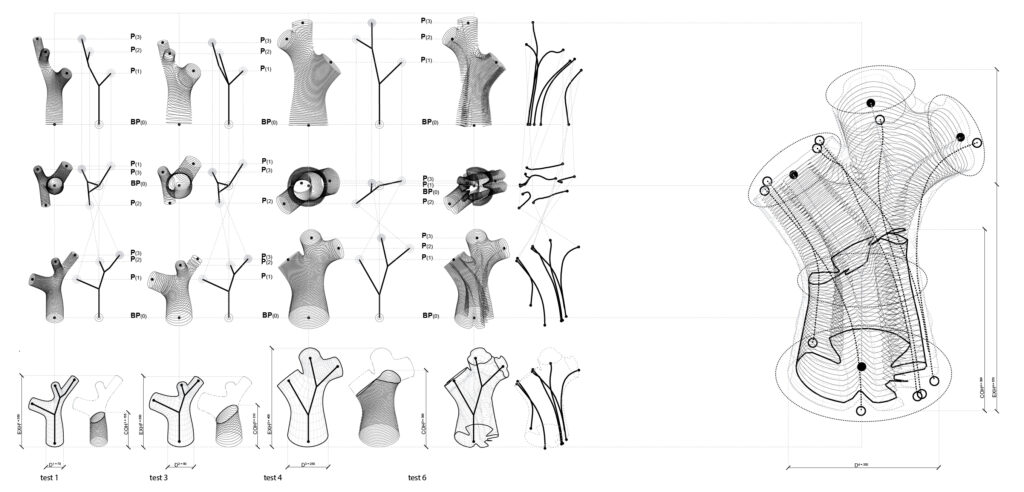
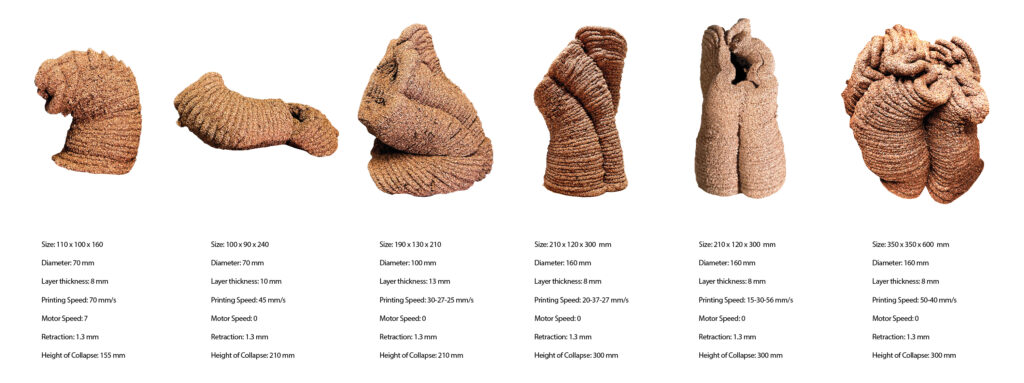
REFLECTION
We ran into the limitations of grasshopper when it comes to manipulating industrial robotic arms. 60-70% of our time on grasshopper was spent troubleshooting tool collisions. We ended up developing three strategies of tweaking the toolpath to optimize the movement of the robot, however these methods required us to arbitrarily change variables until the robot was in its most comfortable position. We think this can be solved by using a different tool to communicate instructions to the robot and getting feedback. Furthermore, if the extruder were reduced this would significantly decrease instances of collision between the robot and the tool.
As a material Cork shows massive potential for 3D printing. Specifically, it’s viscosity and tackiness as a printing material allows it to reach angles that other materials such as clay and concrete cannot. However, one of the major limitations of the material is its load bearing capacity in the wet state. In all of our testing we could not exceed 200mm before experiencing significant deformation and collapse. Furthermore, the material has massive variation in inclination tolerance from small to large scale. The tests done in April achieved angles close to 90°, however we could not exceed 25° at our scale. The walls were also unstable and required stress line reinforcement. Thus, we think the material needs to be improved on. Primarily the material needs to be more structurally strong while printing to support its own weight. The gelatin limits the use of heat to speed up drying. Water makes up the majority of the wight of the material, thus an alternative solution for mixing should be investigated. Lastly agents that can speed up the drying and hardening process should also be looked into.
Ultimately, cork as a building material and specifically it’s application in non-planar 3D printing is very exciting and there is massive potential, we look forward to seeing our shortcoming blown away by future successes.
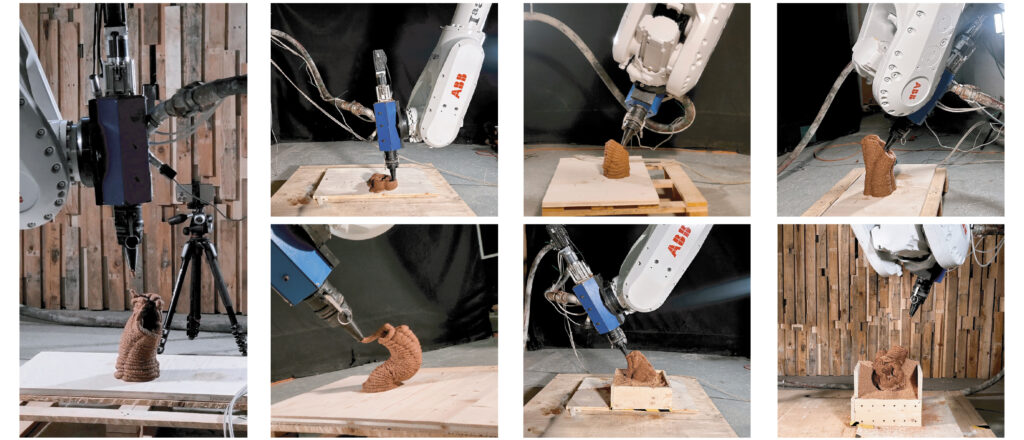
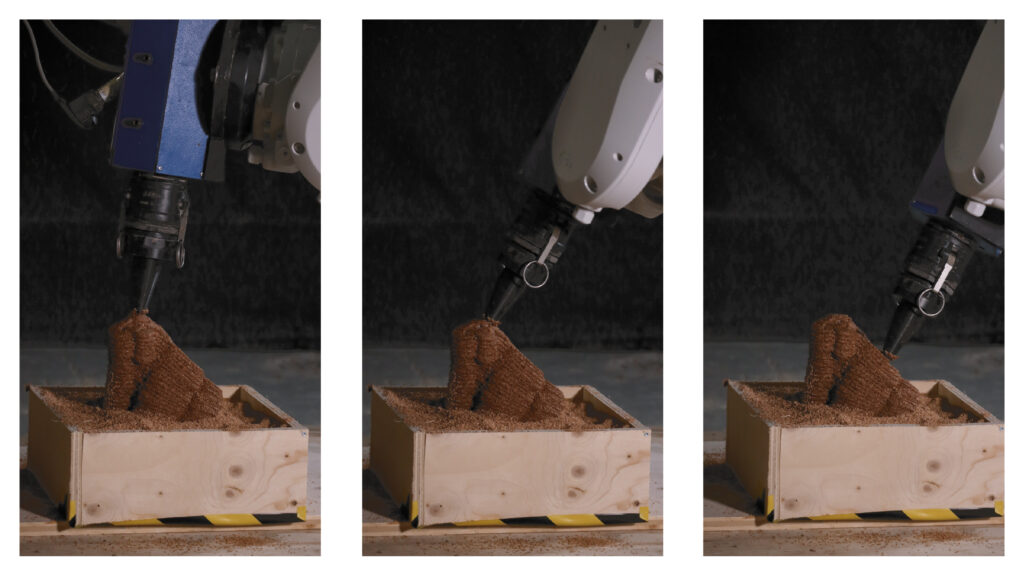