With parametric models as its allies, Building Physics simulates and optimizes, offering a glimpse into the future of building design with tools capable of analyzing thermal comfort, lighting, energy consumption, and structural performance.
In the age of circular and environmentally driven approaches, computational design becomes the compass, guiding deep dives into material optimization, environmental impact assessments, life cycle considerations, and waste reduction strategies.
Geometrical optimization, through tools like Kangaroo and Karamba, becomes an art form. Structural forms evolve through Thrust Network Analysis, pushing boundaries of strength, deflection, and stability. Generative design, driven by algorithms, unlocks the potential of complex, organic geometries, ushering in an era of structural innovation.
Building Aerodynamics steps into the spotlight setting the standard in comfort, and structural integrity, understanding how wind and structure engage in a delicate dance.
Acoustic Performance becomes a key player to choose alternative materials, revealed through the sound absorption coefficient, showcase the potential for harmony in building acoustics.
Structural Optimization, marries analytical models. From SAP to Karamba3d, a new era of optimization unfolds, shaping structures that stand not just as physical entities but as embodiments of efficiency and innovation.
Building Physics emerges not just as a study but as a philosophy that embraces sustainability, innovation, and a deep understanding of the intricate dance between physics and architecture. It is a call to architects, engineers, where every structure is a direct result of informed and conscious data driven decision making.
What is Building Physics?
“Building physics is the study of how the laws of physics apply to the built environment. It determines how a building interacts with its environment in terms of energy, heat, light, sound, air movement and moisture.”
Building physics are the properties that control how a building interacts with the world.
Potential uses of Building physics in design:
Energy: Embodied energy, operation costs, structural system
Heat: Passive Heating
Light: Natural Daylighting, Exterior Reflections, Passive Shading
Sound: Reverberation Time, STC ratings
Air Movement: Aerodynamics, Passive Ventilation
Moisture: Air tightness
Structural: Material efficiency
What is Building Physics in the context of Computational Design?
Many parts of building physics can be simulated and optimized through computational design processes. This is best done with a parametric model which can easily adapt to the data resulting from the simulations. Some of the tools allow us to analyze building performance including, thermal comfort, lighting, energy consumption, and structural performance among others.
Building Physics as the basis of optimization
How do Building Physics relate to circular design and environmental friendly approaches?
Building Physics have a significant impact and role in moving forward circular and environmental driven approaches. Thanks to computational design, we can take a deep dive and make informed decisions in areas such as. Material optimization, this includes assessing the environmental impact such as embodied carbon and recyclability factors. Life Cycle Assessments, waste reduction, energy performance to name just a few.
Form Based:
In Building physics Context – Form Based has many meanings in terms of Optimization and reducing Embodied Carbon consumption. As per recent development in Digital Construction/Fabrication process allowed them to optimize material consumption in many ways. Using Computational Tools allow them to reduce the amount of Material/Energy consumption and maximize efficiency of building elements.
Shape optimization – Geometrical Optimization include form finding based on several goals for intended performance and optimized form by complex forming computational tools like Kangaroo, karamba to evaluate the structural form based on defined goals (TNA- Thrust Network Analysis). Structural Forms can then be optimized further for Structural Strength, deflection and several Load conditions including stability analysis. Optimization process performed by Karamba-3D, Millipede, Ameba and other computational Tools.
Form-based structural optimization involves optimizing the geometric form or shape of a structure to achieve the best possible structural performance, often in terms of load-carrying capacity, material efficiency, and overall stability. This can be achieved through computational design methods and often employs advanced algorithms and simulations to explore different forms and configurations. Here are key aspects and steps involved in form-based structural optimization:
- Geometry Generation:
Begin by creating or defining the initial geometry of the structure. This could be a conceptual form or an existing design.
- Parametric Modeling:
Use parametric modeling techniques to represent the geometry with adjustable parameters. This allows for easy exploration of different forms by varying these parameters.
- Optimization Criteria:
Define the optimization criteria and performance objectives. This could include minimizing material usage, maximizing structural efficiency, or meeting specific design constraints and criteria.
- Computational Analysis:
Perform structural analysis using computational tools to evaluate the performance of the structure under various loads and conditions. This analysis helps in understanding how different forms respond to external forces.
- Optimization Algorithms:
Employ optimization algorithms to iteratively modify the geometric parameters of the structure to meet the defined objectives. Genetic algorithms, particle swarm optimization, and simulated annealing are examples of algorithms commonly used for structural optimization.
- Topology Optimization:
Utilize topology optimization, a specific type of structural optimization, to iteratively distribute and optimize material within the defined design space. This helps in identifying the most efficient material layout for the given structural requirements.
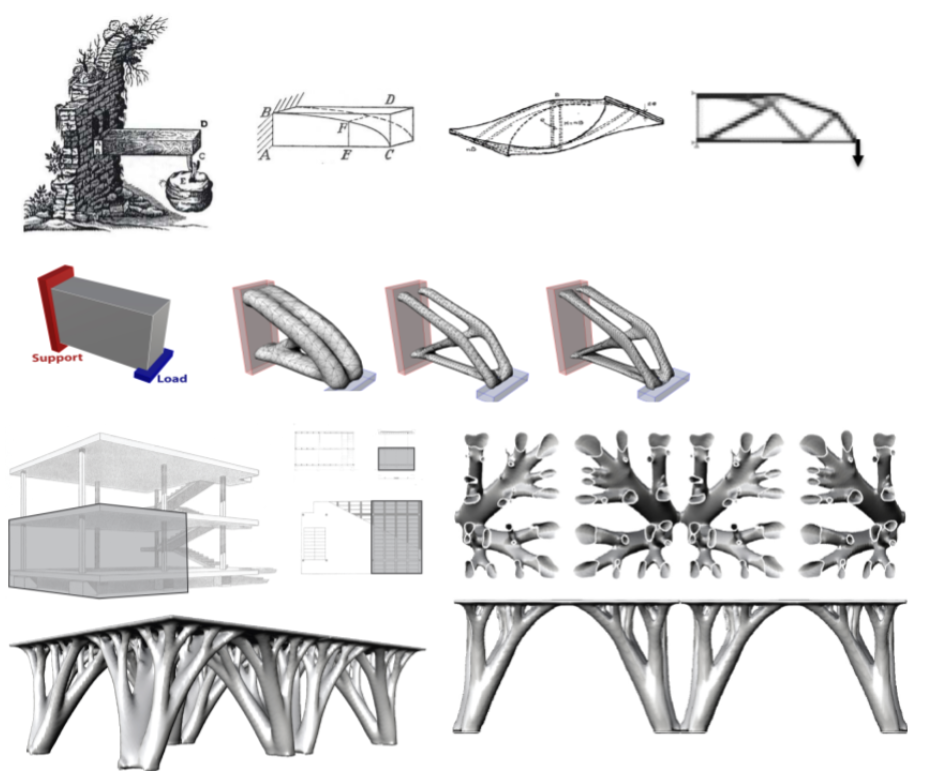
- Sensitivity Analysis:
Conduct sensitivity analysis to understand how changes in design parameters affect the structural performance. This information guides the optimization process and helps identify critical design variables
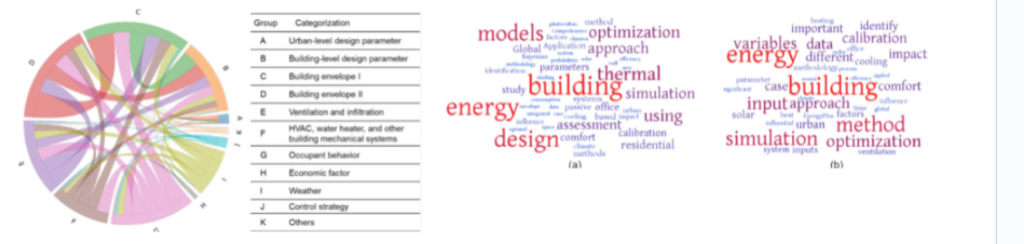
- Constraint Handling:
Address design constraints during the optimization process, such as architectural or functional constraints, to ensure that the final optimized form meets all specified requirements.
- Visualization and Evaluation:
Visualize the results of the optimization process and evaluate the performance of different design iterations. This could involve generating visualizations of stress distribution, displacement, or other relevant structural parameters.
- Feedback Loop:
Establish a feedback loop where insights gained from the analysis and evaluation inform further adjustments to the design parameters. This iterative process continues until the optimal form is achieved.
- Fabrication Considerations:
Consider fabrication constraints and feasibility during the optimization process. Ensure that the optimized form is practical to fabricate using available construction methods and materials.
- Documentation and Communication:
Document the optimized form and communicate the results effectively to stakeholders. This may involve creating detailed reports, drawings, and visualizations.
Form-based structural optimization is a powerful approach that integrates design, analysis, and optimization to create structures that are not only aesthetically pleasing but also highly efficient in terms of structural performance. The use of advanced computational tools allows designers and engineers to explore a wide range of possibilities and discover innovative solutions.
Structural Optimization – Digital Fabrication:
Structural optimization using digital fabrication involves leveraging advanced computational methods and digital manufacturing technologies to design and produce structurally efficient and innovative building components or entire structures. This approach allows for the creation of complex geometries, improved material usage, and the realization of structures that might be challenging or impossible to construct using traditional methods. Here are key aspects of structural optimization using digital fabrication:
- Generative Design:
Generative design involves using algorithms to explore a vast design space and generate multiple potential solutions based on specified design criteria and constraints. This approach is particularly useful for structural optimization as it allows for the exploration of complex, organic, or unconventional geometry.
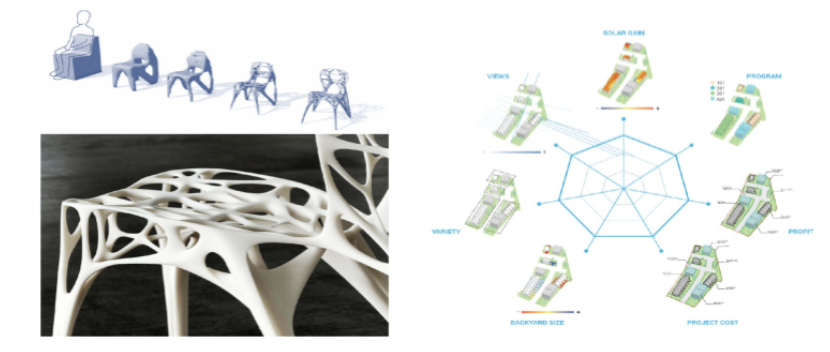
- Topology Optimization:
Topology optimization is a computational method that iteratively determines the optimal distribution of material within a given design space to achieve the best structural performance. It helps in creating lightweight and efficient structures by removing material where it is not needed.
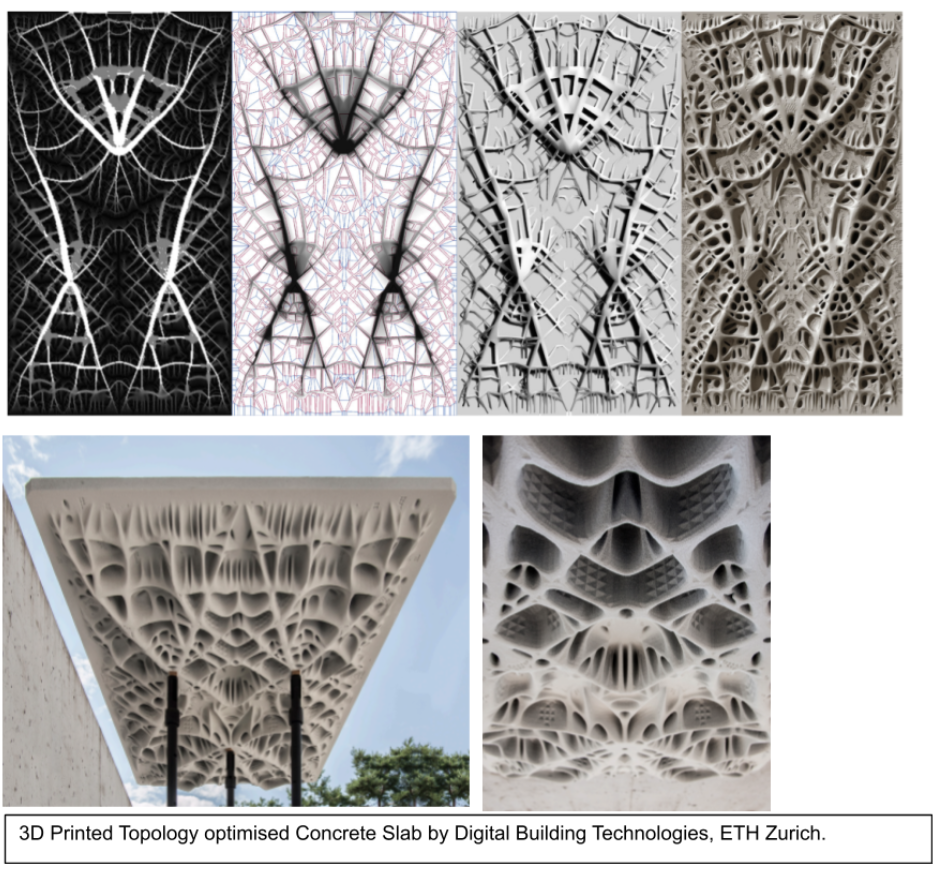
- Parametric Design:
Parametric design involves creating a digital model with parameters that can be adjusted to explore different design options. This allows for easy modification and optimization of structural elements based on various criteria such as material usage, load-bearing capacity, and aesthetic considerations.
- Digital Twins:
Creating digital twins involves creating a digital representation of a physical structure or component. This allows for real-time monitoring, analysis, and optimization of the structure’s performance throughout its lifecycle, enabling data-driven decisions.
- 3D Printing and Additive Manufacturing, Robotics and Automation:
Digital fabrication often involves techniques like 3D printing or additive manufacturing, where structures are built layer by layer based on digital models. This allows for the fabrication of intricate and customized structural components, reducing waste and enabling novel geometries.
The use of robotic systems and automation in construction can enhance precision and efficiency. Robotic fabrication can be employed to assemble complex structures with high accuracy, especially when dealing with repetitive or intricate tasks.
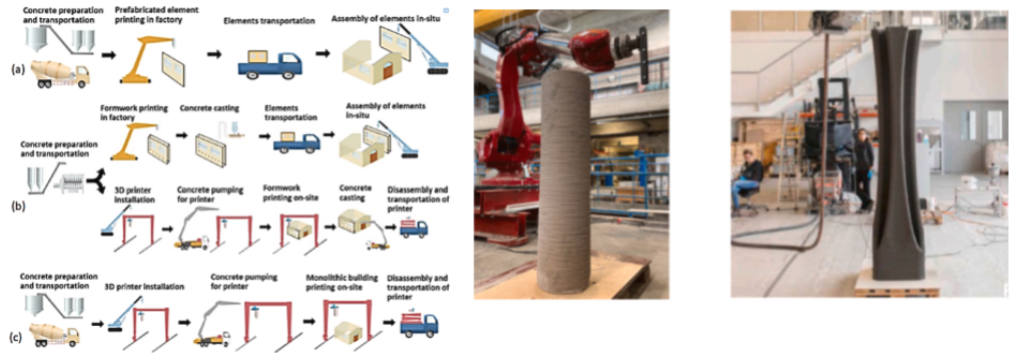
- Material Innovation:
Digital fabrication opens the door to exploring novel materials and composites that may have specific structural properties. This includes materials designed for enhanced strength-to-weight ratios, sustainability, or unique aesthetic qualities.
Examples of Material Innovations like Cross Laminated Timber, Aluminum Foam, Mycellium, Clay, Low carbon and Light weight Foam concrete 3D printing technology boostup construction process and reduce embodied carbon consumption.
- Integrated Workflows:
Seamless integration of design, analysis, and fabrication processes is crucial for successful digital fabrication. Building information modelling (BIM) and other collaborative platforms facilitate communication and coordination between different stakeholders involved in the design and construction process.
- Customization and Mass Customization:
Digital fabrication enables the customization of structural elements to suit specific project requirements. Mass customization, where standardized components are efficiently adapted to meet individual project needs, becomes feasible.
- Sustainability:
Digital fabrication can contribute to sustainability by optimizing material use, minimizing waste, and allowing for the efficient construction of lightweight and resource-efficient structures.
The integration of digital fabrication and structural optimization can lead to the creation of more sustainable, efficient, and visually striking structures. It requires a multidisciplinary approach involving architects, engineers, fabricators, and other stakeholders working collaboratively throughout the design and construction process.
Aerodynamics & Geometrical configuration:
Building performance can be improved by Improving resistance to Wind by parametrizing geometrical configuration. Wind Tunnel Testing of Prototype/Scaled model to validate engineered data/Codal provisions with response of building by application Wind Dynamic conditions and improving performance. Critical Scenarios based on site specific data utilized and can be used to improve building performance for its intended Life cycle. Study of Wind Behaviour/dynamics and modifying conflicting elements to improve efficiency of building performance.
Building aerodynamics refers to the study of how wind interacts with buildings and structures. It is a crucial aspect of building physics, particularly in the design of tall or complex structures where wind forces can have a significant impact on safety, comfort, and structural integrity. Here are some key considerations in building aerodynamics:
- Wind Loads:
Understanding the wind loads that act on a building is essential for designing a structurally sound structure. Wind loads include both static and dynamic components. Static loads are due to steady wind, while dynamic loads result from fluctuations and gusts.
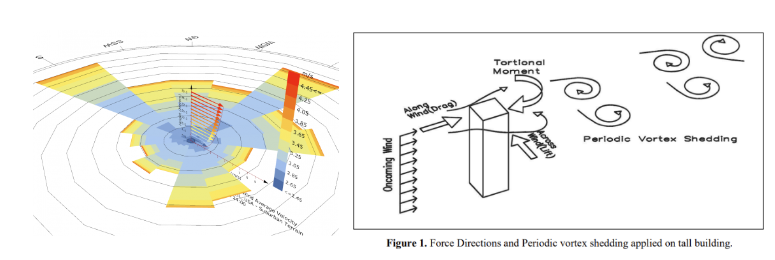
- Wind Pressure Distribution:
The shape and form of a building influence how wind pressure is distributed across its surfaces. Windward and leeward sides, as well as corners and edges, experience different pressure distributions. This information is critical for designing structural elements and cladding that can withstand these pressures.
- Vortex Shedding:
Tall and slender structures can experience vortex shedding, a phenomenon where alternating vortices are shed from the sides of the building. This can lead to structural vibrations and, in extreme cases, failure. Design considerations, such as adding damping devices, can help mitigate the effects of vortex shedding.
- Buffeting and Flutter:
Buffeting occurs when turbulent wind flow causes oscillations in a structure, leading to vibrations. Flutter is a more severe form of buffeting that can result in large and potentially destructive vibrations. Both phenomena must be considered in the design of bridges, towers, and other structures.
- Aerodynamic Shape Optimization:
Building shapes can be optimized to reduce wind loads and enhance aerodynamic stability. Streamlining and tapering shapes, as well as adding aerodynamic features like fins and canopies, can help control wind flow and minimize the impact of wind forces.
- Wind Tunnel Testing:
Physical wind tunnel testing is a common practice in building aerodynamics. Scale models of buildings are subjected to wind flow to simulate real-world conditions. Testing helps validate computational models, refine designs, and assess the structural performance of a building.
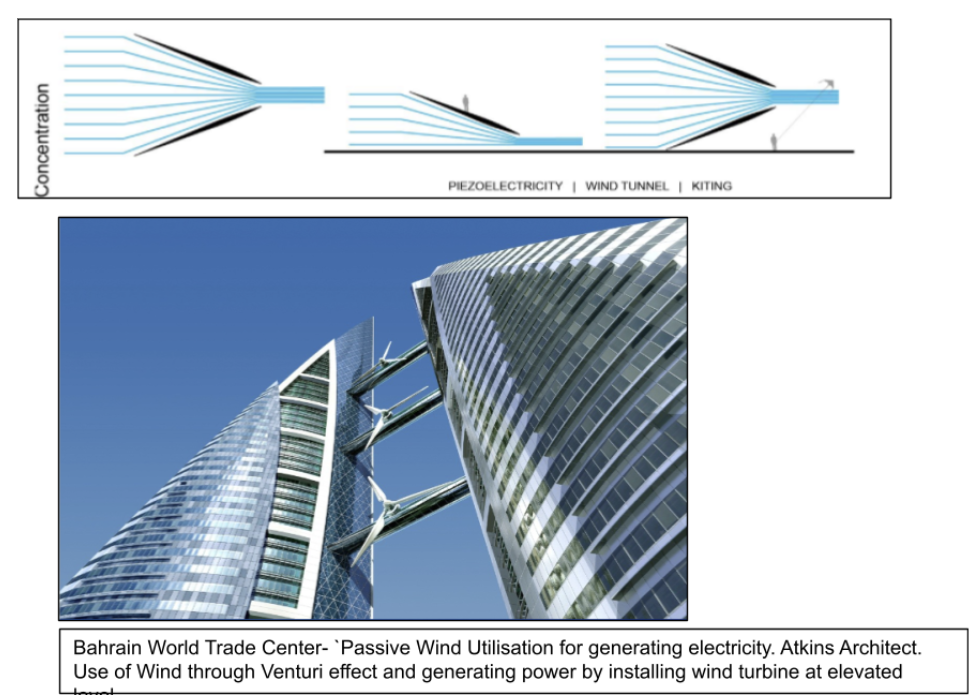
- Cladding and Facade Design:
The design of building facades and cladding materials is influenced by aerodynamics. Wind pressure on the facade must be considered to prevent issues like water infiltration, excessive noise, or structural failure. Wind tunnel tests and computational fluid dynamics (CFD) simulations can inform facade design.
- Environmental Impact:
Building aerodynamics also plays a role in the environmental impact of structures. For example, the way buildings affect local wind patterns can impact the microclimate around the structure, influencing factors like temperature and air quality.
In summary, building aerodynamics is a critical aspect of building physics, particularly for tall or uniquely shaped structures. Understanding how wind interacts with buildings helps architects and engineers design structures that are both safe and comfortable, while also considering the broader environmental impact. Computational tools and wind tunnel testing are commonly used to analyse and optimize building designs for aerodynamic performance.
Material Based:
Transparency & reflection:
Some materials such as glass allow light to pass through while many others block light. Natural lighting can be used in place of electrical lighting which can minimize the electrical load of the building, but can also result in a higher heat gain. Some smart facades control this condition to strategically allow light in some places and exclude it in others.
Insulation & thermal conductivity:
The material of the exterior enclosure of a building determines its thermal performance. A well insulated building will have a strong thermal break on the exterior, preventing energy from being transferred from the interior to surroundings and vice versa. The most common way of judging a material’s thermal properties is its r-value.
Both Form & Material:
Acoustics Performance / Dynamic Sounds:
Acoustic performance within building physics is the evaluation and management of sound in the built environment. An integral part of the design, operation, and construction of buildings. In general, acoustic optimization has a high impact on the health and well-being of occupants.
The evaluation of materials and systems in acoustic energy is facilitated by the sound absorption coefficient. Utilizing the impedance tube, their results showcased comparable performance, with peak values ranging between 0.70 and 0.84, demonstrating the potential efficacy of alternative materials in contributing to effective sound absorption in building acoustics.
Reverberation Time and STC ratings
In the realm of acoustics, there are two critical parameters that govern the sound experience within a space: reverberation time (RT) and Sound Transmission Class ratings (STC). Reverberation time, denoted as RT60, measures the persistence of sound after the source is turned off, while STC ratings measures a material’s ability to block sound transmission.
Reverberation time significantly impacts the clarity and comprehensibility of sound, more particularly for speech. Excessive reverberation can confuse the speech, making it difficult to understand, while a reverberation time that is too short can sound harsh and unnatural. Optimal reverberation times vary depending on the space’s intended use, ranging from longer durations for concert halls to shorter durations for classrooms and conference rooms.
Space Type
Recommended RT60
Concert Halls
2.0 – 3.0 seconds
Theaters
0.8 – 1.2 seconds
Classrooms
0.5 – 0.7 seconds
Conference Rooms
0.3 – 0.6 seconds
STC ratings, on the other hand, focus on the transmission of sound between spaces. Higher STC ratings indicate better soundproofing, reducing the transfer of unwanted noise from one area to another. STC ratings are particularly important in noise-sensitive environments like offices, apartments, and hospitals. The relationship between reverberation time and STC ratings is often inverse. Materials with higher STC ratings tend to reflect more sound energy, leading to lower reverberation times within a space. This interplay between sound reflection and absorption is crucial for achieving an optimal acoustic environment.
STC Rating
Sound Reduction
20-25
Minimal sound reduction
25-30
Some sound reduction, noticeable for loud sounds
30-35
Moderate sound reduction, noticeable for normal speech
35-40
Good sound reduction
40-45
Excellent sound reduction for most sounds
45-50
Very good sound reduction, effective for privacy
50-55
Exceptional soundproofing
55-60
Excellent soundproofing for most situations
60-65
Nearly perfect soundproofing
65-70
Near-perfect soundproofing, effective for critical applications
In conclusion, reverberation time and STC ratings are fundamental concepts in acoustics, influencing sound perception, comprehensibility, and privacy. By understanding these parameters, we can effectively manage sound within a space, creating environments that are both acoustically pleasing and functionally optimized for their intended purpose.
Structural Optimization:
Structural optimization involves the use of analytical models and computational techniques to test and optimize structural performance of individual members or entire structure. The process typically begins with defining the design space with all possible variations in geometry, materials, and other relevant parameters. The optimization process often includes iterative analyses, where the performance of candidate designs is evaluated using tools like SAP, ETABS, RAM but lately computational driven approaches have been added and new tools such as Karamba3d, kangaroo, lattice, NuadaCFD, among other CSI toolbars have been created.
There are studies for dynamic and evolutionary structural optimization such as graphic statics and evolutionary algorithms.
Graphic statics is a powerful method for the design and analysis of structures that, by using force polygons and simple geometric construction techniques, provides intuitive visual information about the relation between form and forces of a structural system.
Evolutionary Structural Optimization (ESO) is a design method based on the simple concept of gradually removing inefficient material from a structure as it is being designed. Through this method, the resulting structure will evolve towards its optimum shape.
Conclusion:
Building Physics transcends the theoretical as it steps into the realm of computational design and data driven optimization. With parametric models as its allies, Building Physics simulates and optimizes, offering a glimpse into the future of building design with tools capable of analyzing thermal comfort, lighting, energy consumption, and structural performance.
Building Physics emerges not just as a study but as a philosophy that embraces sustainability, innovation, and a deep understanding of the intricate dance between physics and architecture. It is a call to architects, engineers, where every structure is a direct result of informed and conscious data driven decision making.
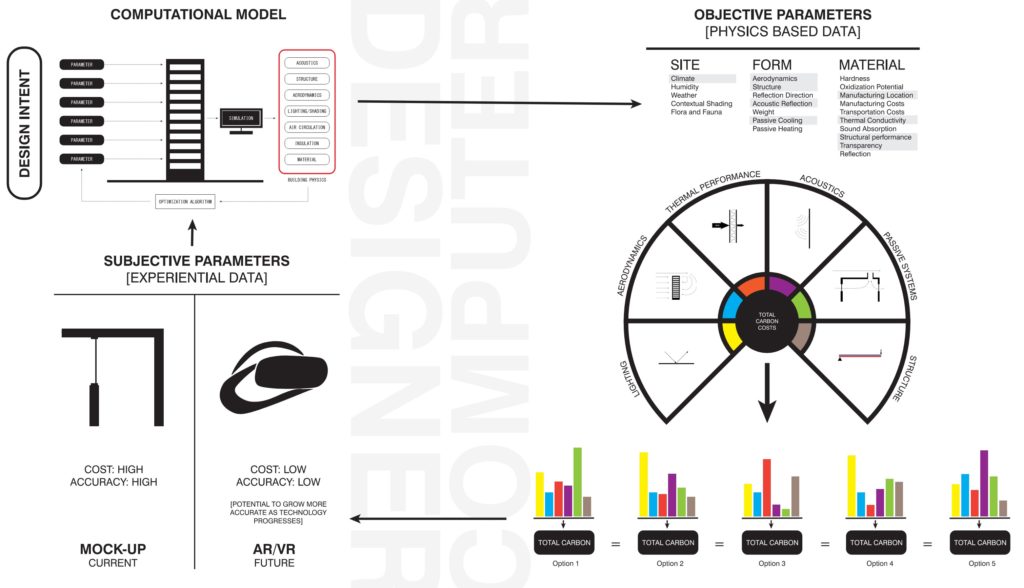