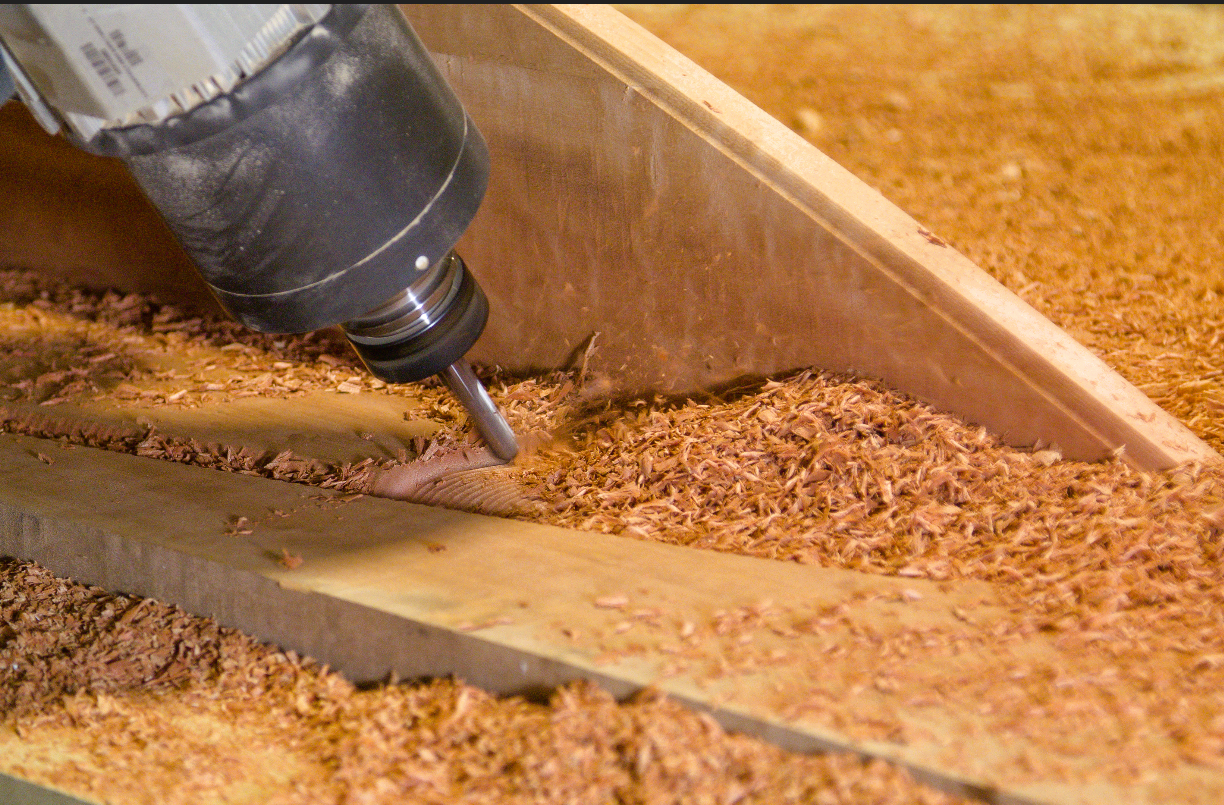
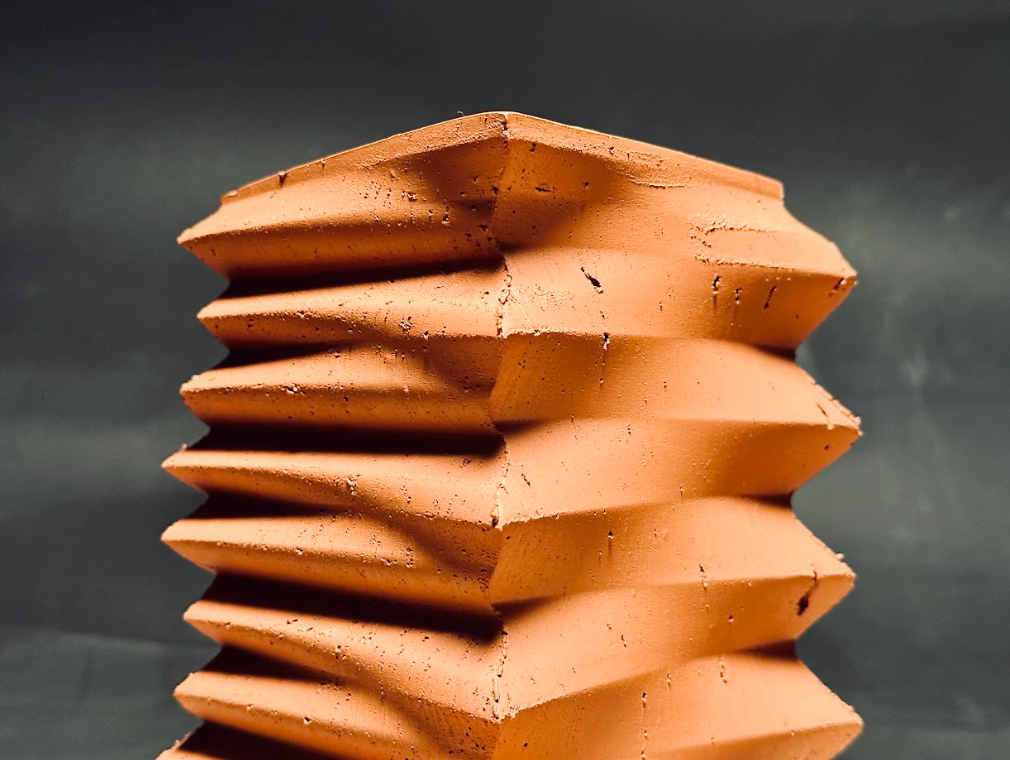
Photo credit: DARE, MRAC 2023
Description
The mid-1800s marked an era of tailor-made products, spanning from intricate product design to elaborate building elements. This period represented the moment in time when geometry, material, process and tools were interconnected. The synergistic interplay between these elements has always been a fertile ground for design and technical exploration.
For natural materials such as wood and clay, the tactile relationship between the artisan and the inherent attributes of the materials, be it the wood’s grain or clay’s malleability, profoundly
influenced the final product’s resolution. In the 20th century, industrialization streamlined production processes and significantly increased production capacities. However, it also ushered in an era of material standardisation and product uniformity. This advancement overshadowed the nuances of bespoke detailing and traditional craftsmanship. Modern architecture design became more about choosing materials from catalogues, borrowing building details from BIM libraries, and sidelining the rich connection to native materials, ancestral traditions and nuanced processes.
Today, sustainable construction is not optional; it’s an essential requirement. It requires ethically sourcing materials and comprehensively evaluating building solutions throughout their lifecycle. The
rise of cutting-edge technologies like numerical manufacturing, computer vision and AI offers promising avenues to reimagine and reinvent our built environment. They signal a transformative shift from mass production to mass customization. There’s a compelling need to devise workflows that resonate with material attributes and availability, championing material reuse and endorsing circular economic models.
Hybrid workflows
Hybrid workflows aim to uncover new opportunities by studying the blend of materials, contemporary manufacturing processes and sensing technologies. Our chosen materials will focus on renewable, reclaimed, or sustainably sourced options, predominantly looking at timber and clay. We will investigate digital craftsmanship as a combination of additive and subtractive processes.
We will create manufacturing workflows that respond to material properties, non standard dimensional materials (reclaimed, waste) by harnessing the full potential of modern manufacturing. To unlock the full potential of these manufacturing pipelines, design needs to stay flexible in order to respond to material and fabrication constraints. Here parametric or computational design emerges as a crucial tool. Parametric control in a design-to-production workflow offers a unique opportunity to have a feedback loop with the production method. A digital model, which can accommodate all the complex relationships of its contained elements, will be orchestrated properly in order to deliver valid information for every step of the design and construction of the studio project. Throughout the course design and manufacturing process will be developed concurrently. This symbiotic approach will culminate in the creation of prototypes, serving as practical platforms for testing and validation.
Design element
In the initial weeks, the primary focus will centre on selecting a design element, prioritising surface compositions, and concurrently devising an appropriate fabrication strategy. Whether the design
target is rich detailing or optimising for a specific performance, practical aspects of its construction will need to be addressed. This encompasses design for manufacture and assembly and supply chain
logistics. A holistic approach will be required ensuring that not only the aesthetic and functional aspects are impeccably resolved but also the seamless integration of the element into its intended application, whether it be for a floor, wall, or roof.
Learning Objectives
Enter the learning objectives
The aim of the studio is to introduce students to holistic design to manufacturing workflows leveraging computational design and robotic fabrication.
? Computational design to manufacture workflows
? Designing for affordance of material and fabrication process
? Designing for mass customization
? Robotic fabrication
Keywords
DFMA, Robotic Fabrication, Computational design