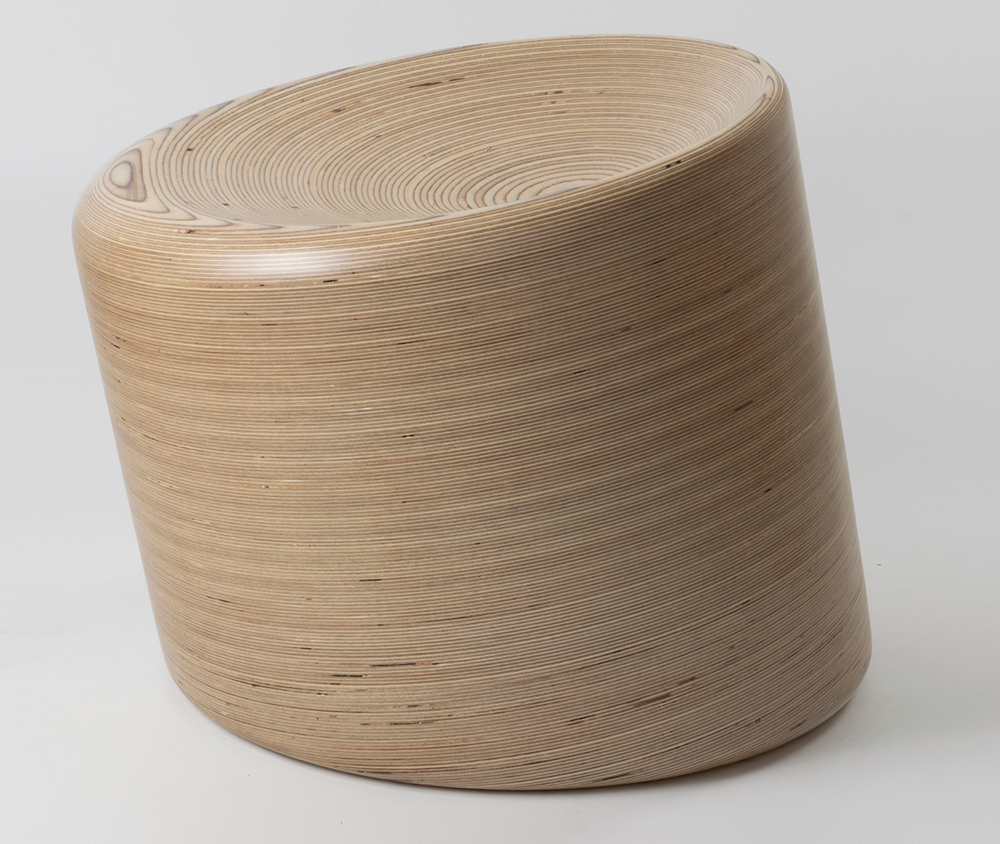
Description
Stack lamination is a versatile technique that seamlessly integrates both subtractive and additive fabrication methods. It involves the construction of a substantial volume of material using sheet stock, typically utilising plywood or similar manufactured boards. These boards are CNC machined and stack laminated into blocks that approximate the shape of a larger form. Subsequently, the pieces undergo 3D robotic milling, and finishing.
This one-week workshop is designed to acquaint participants with the stack lamination process, encompassing a blend of digital and traditional fabrication techniques. Participants will gain hands-on experience in 3-axis CNC milling, robotic milling, and traditional woodworking as they collaborate in groups to develop a design and fabrication strategy for a small sculptural product within the realm of interior design. Specifically, participants are challenged to conceptualise and create a piece of furniture suitable for a potential cafeteria in Barcelona. Examples of such pieces may include bar stools, coffee tables, side tables, display shelves, and more.
Various fabrication methods are available to attain final products with a seamlessly smooth, monolithic appearance from wood. In this context, stack lamination offers a significant advantage due to its efficient utilisation of materials. The combination between the hollow core of the end product and the stock material closely approximating the target shape allows for the creation of highly efficient designs while preserving a monolithic aesthetic.
Furthermore, the contouring strategy also plays a pivotal role in optimising material usage, as it influences how the layers nest together for 3-axis milling and, consequently, the quantity of sheet material required. Hence, we encourage students to integrate material efficiency considerations into their design processes.
The workshop unfolds in the following stages:
Stage 1: Design for Fabrication
- Introduction to Robotic Milling in Architecture and Interior Design
-
- Analysis of case studies and practical tutorials
- Understanding the capabilities and constraints of robotic milling
- Basic comprehension of tool path design using Grasshopper and motion programming with Kuka|prc
- Focus on tool path design for sculptural applications employing flat end mills for efficient 5-axis parallel finishing
- Development of designs considering the limitations inherent in the proposed robotic fabrication method
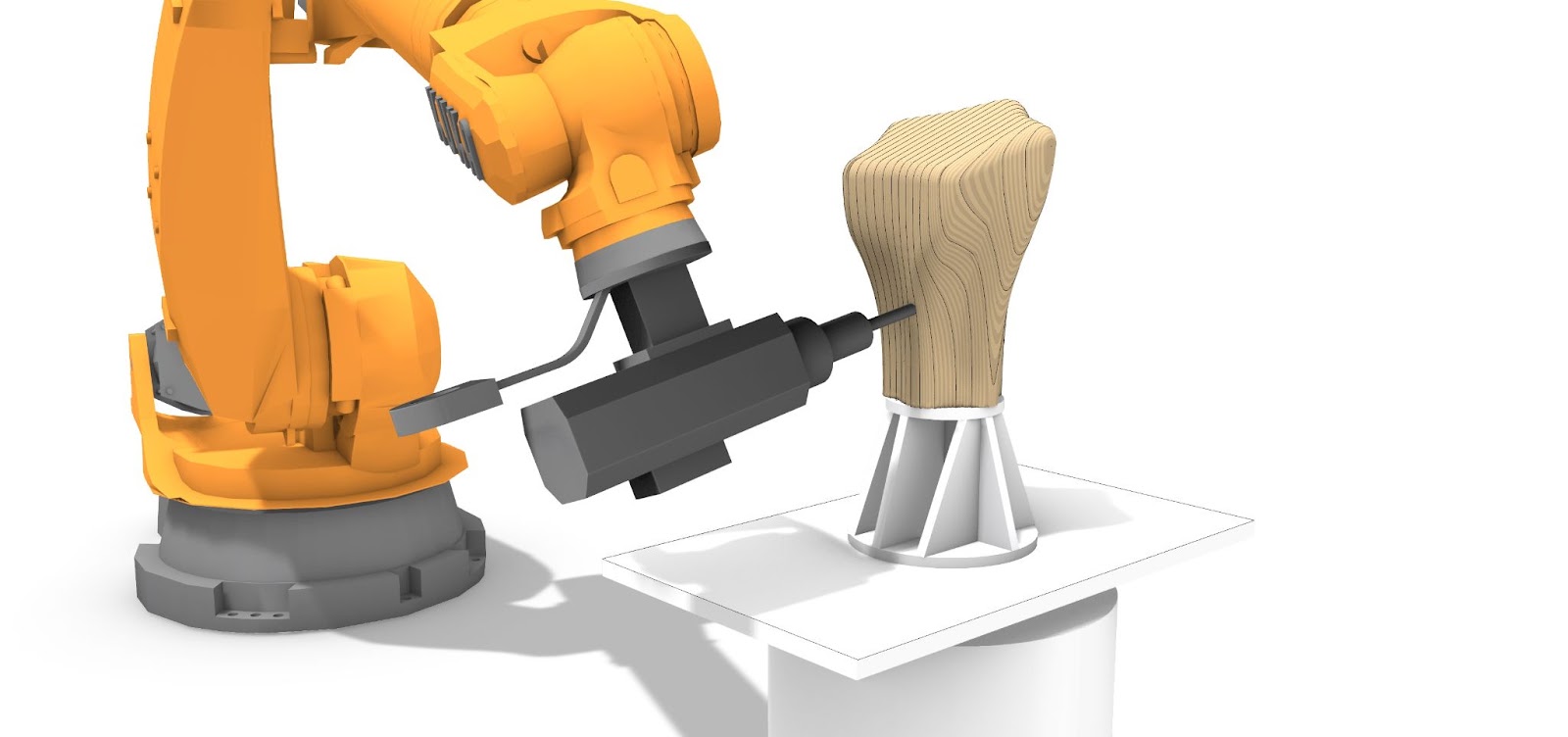
Photo credit: Valentino Tagliaboschi
Stage 2: Slicing and 3-axis CNC Milling
- Slicing and nesting to achieve stock that approximates the designed object’s near-net shape
- Execution of the first fabrication step involving 3-axis CNC milling
- Subsequent stacking, glueing, and clamping of layers to realise the design
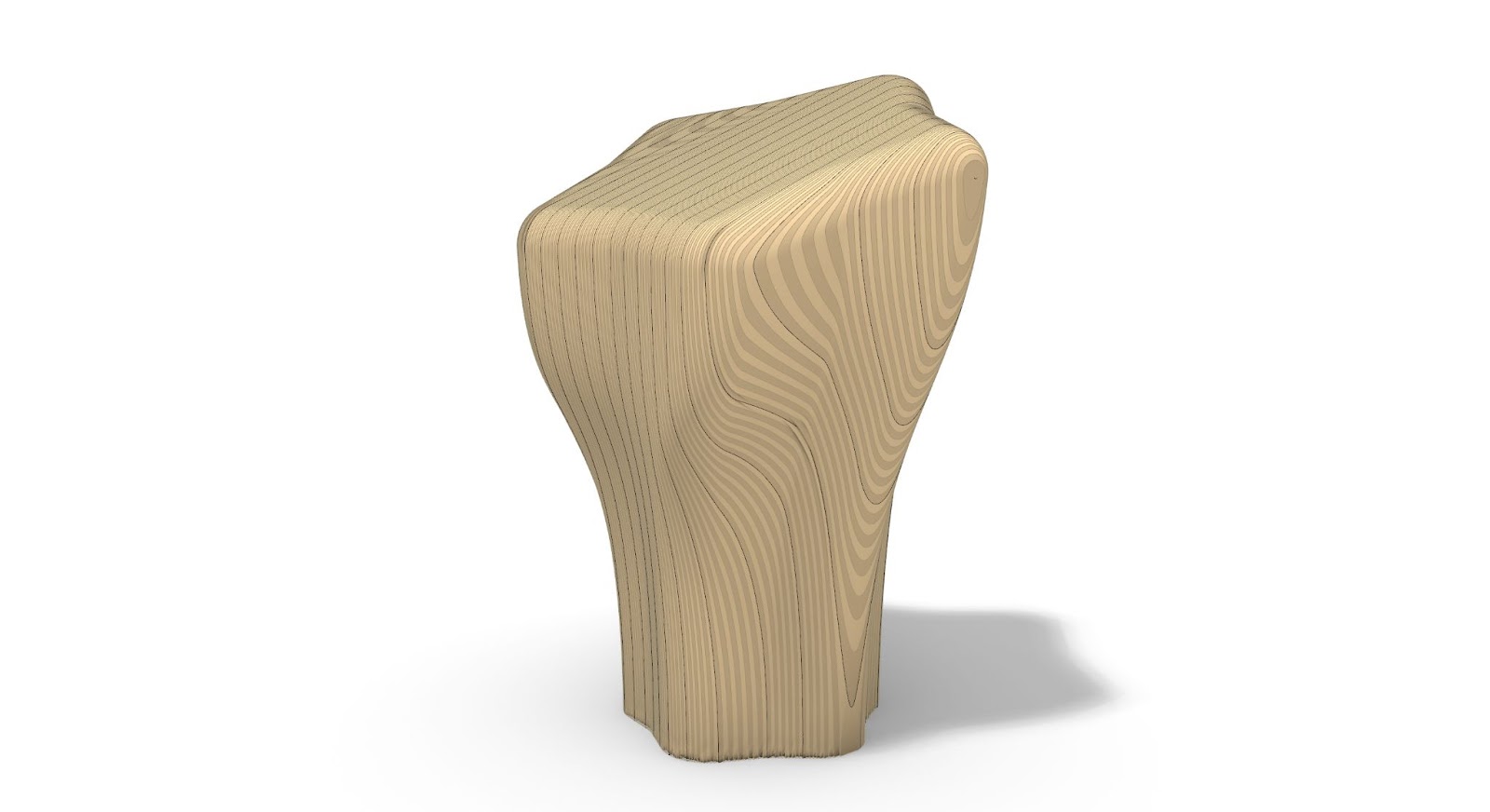
Photo credits: Valentino Tagliaboschi
Stage 3: Robotic Milling – 5-axis Parallel Finishing
- Fine-tuning and validation of robotic fabrication files through digital simulations
-
- Ensuring geometric consistency of the toolpath
- Defining angular offsets on the external rotary axis (turntable)
- Avoiding self-collisions (robot-spindle) and collisions with work objects, workholding, or the robot cell environment
- Engaging in hands-on robotic fabrication sessions
Stage 4: Finishing, Sanding, and Varnishing
- Concluding the workshop with manual finishing processes
- Employing hand tools for sanding and the potential application of various treatments
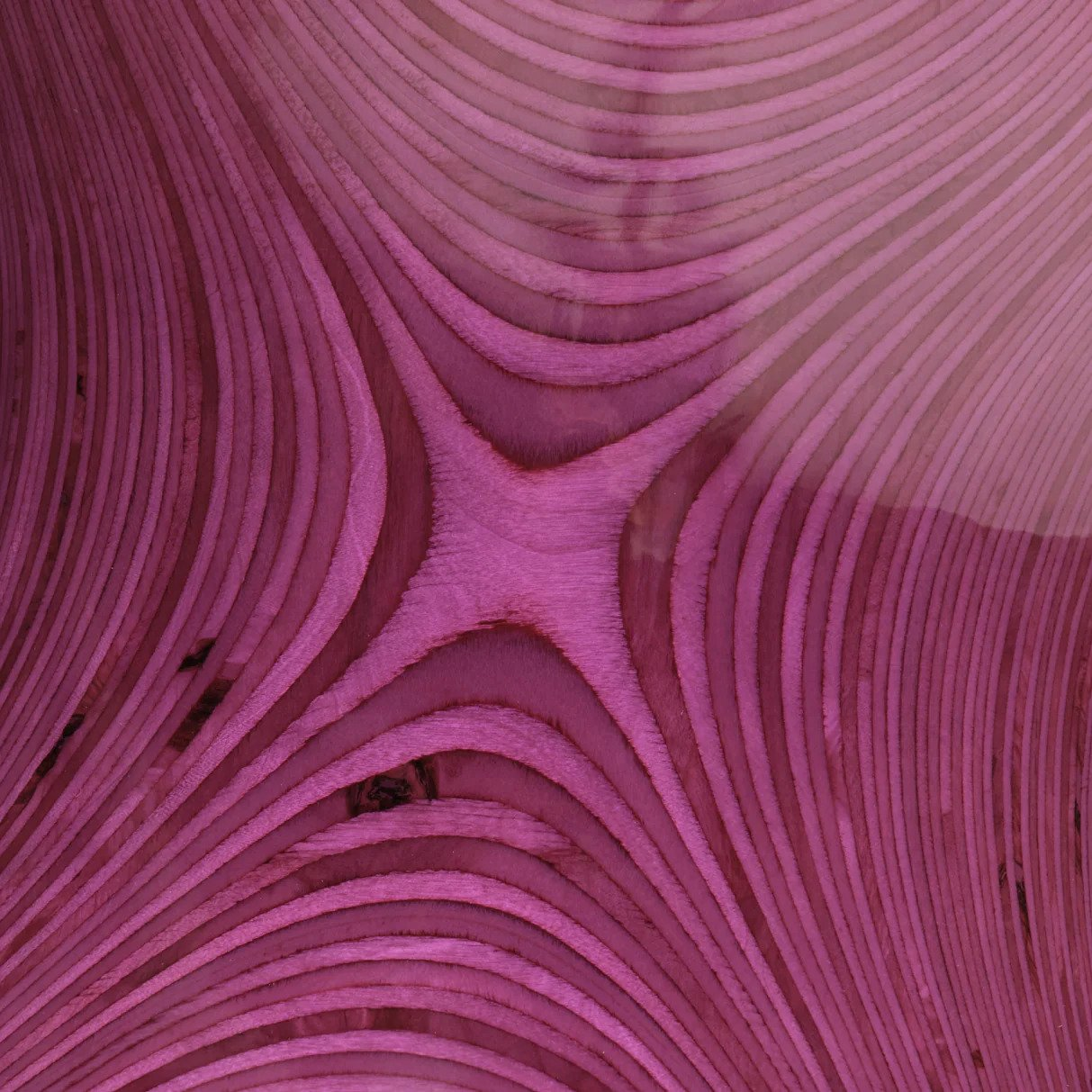
Learning Objectives
This course aims to improve the knowledge of the students in the following fields:
- Fundamentals of motion programming and toolpath design in Kuka|prc
- Robotic milling strategies:
-
- RhinoCam-to-KukaPrc workflow
- Sculptural applications
- Flattening, labelling, nesting
- Design for fabrication and file making