Stack Lamination: Exploring the Intersection of Subtractive and Additive Manufacturing
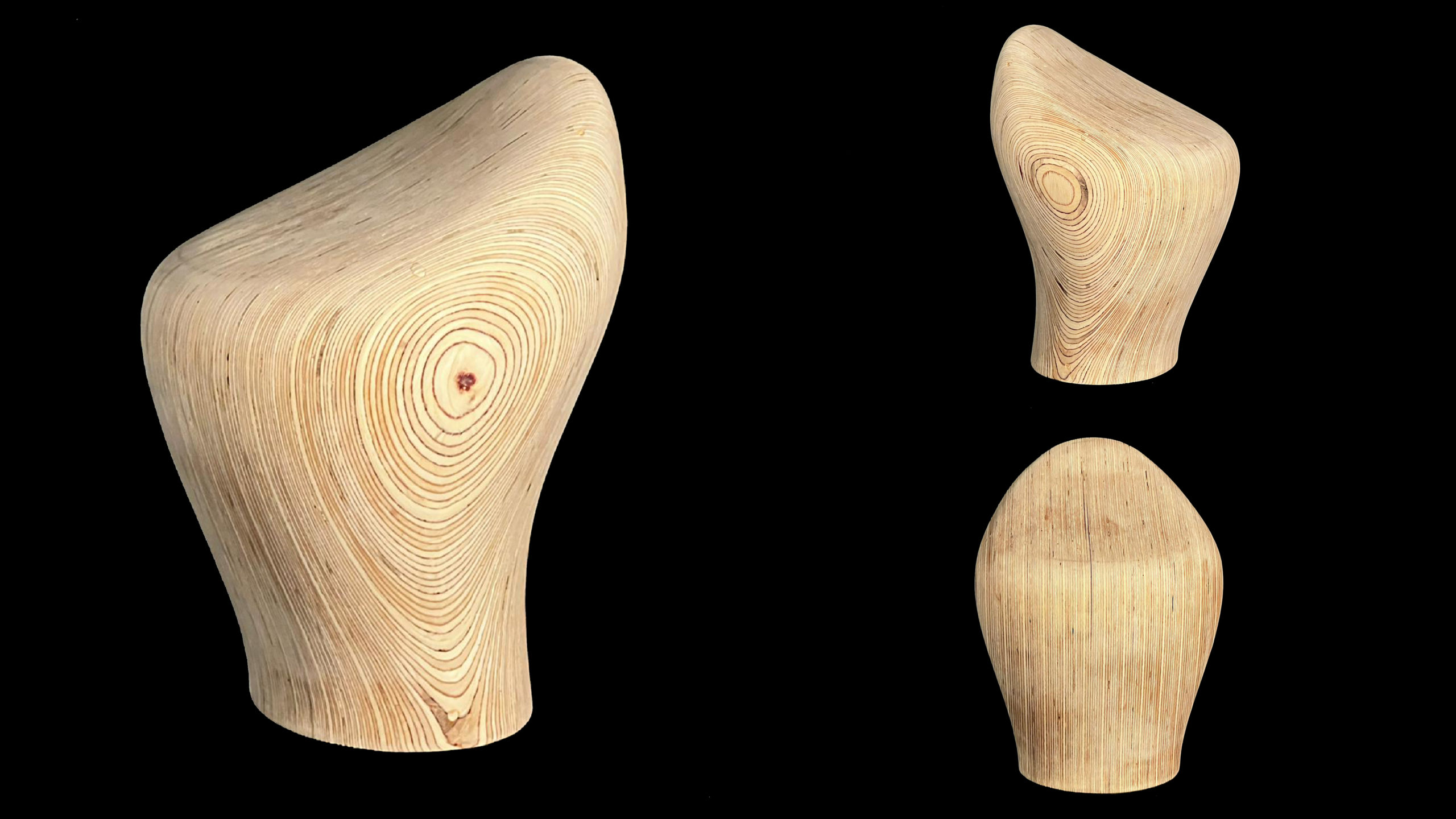
Brief:
This workshop was conceived with the aim of familiarizing participants with the procedural intricacies of Stack Lamination milling, employing an Industrial KUKA robot arm. The methodology encompassed the integration of both digital and conventional fabrication approaches. We engaged in practical applications of 3-axis CNC milling, robotic milling, and traditional woodworking practices, including manual sanding, among others. This workshop mandated the conceptualization of a furniture design tailored for a prospective cafeteria in Barcelona, coupled with the formulation of a corresponding fabrication strategy. The following summarizes our research findings and the results we achieved through the workshop.
Workflow :
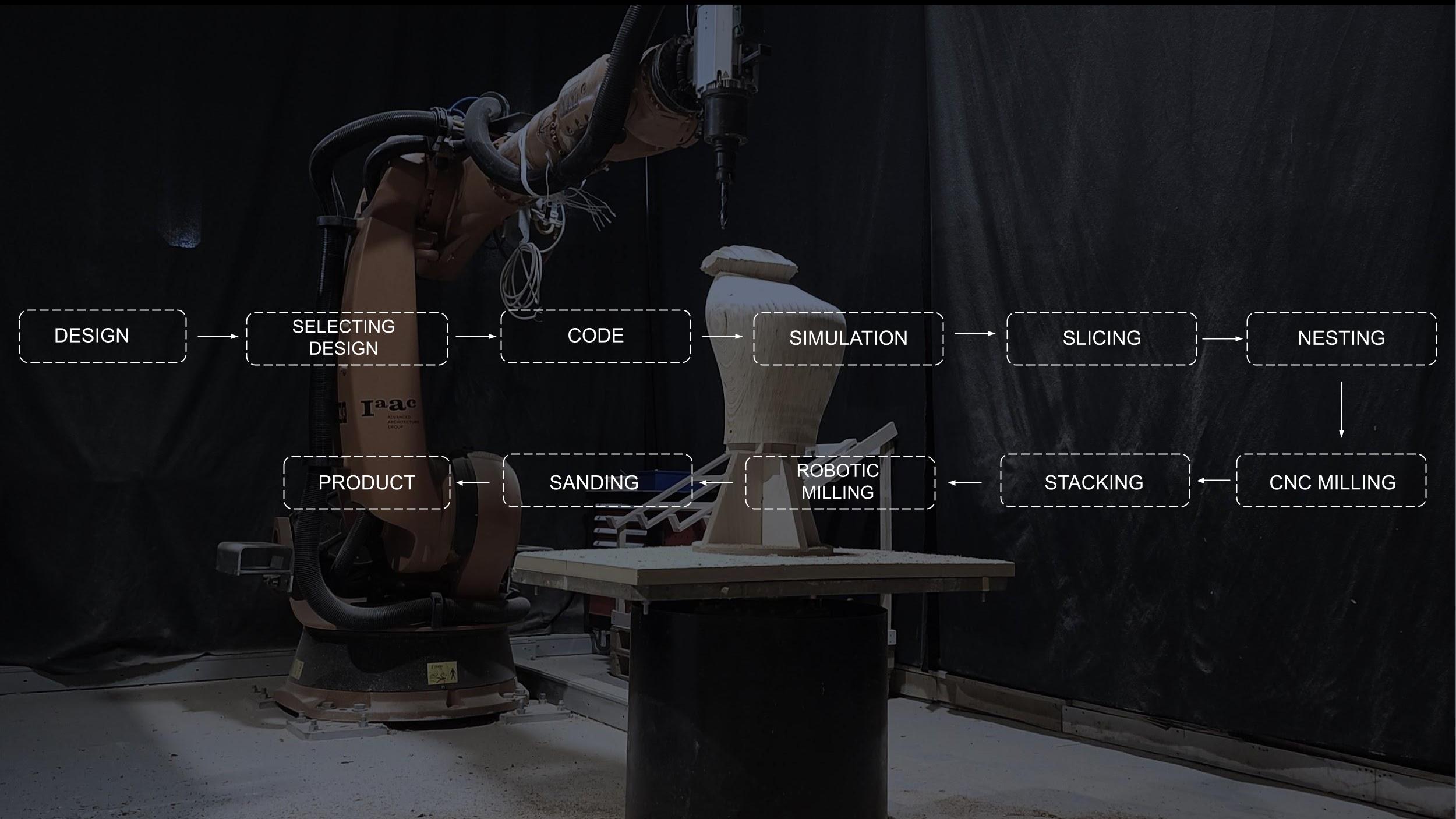
Prototypes:
When developing designs based on the constraints of the workshop, we filtered down to three prototypes based on design, function, and fabrication. The following are the three prototypes: 1) Prototype A is a design of a Chair, 2) Prototype B is a design of a Coffee table, and 3) Prototype C is a design of a Sculpture.
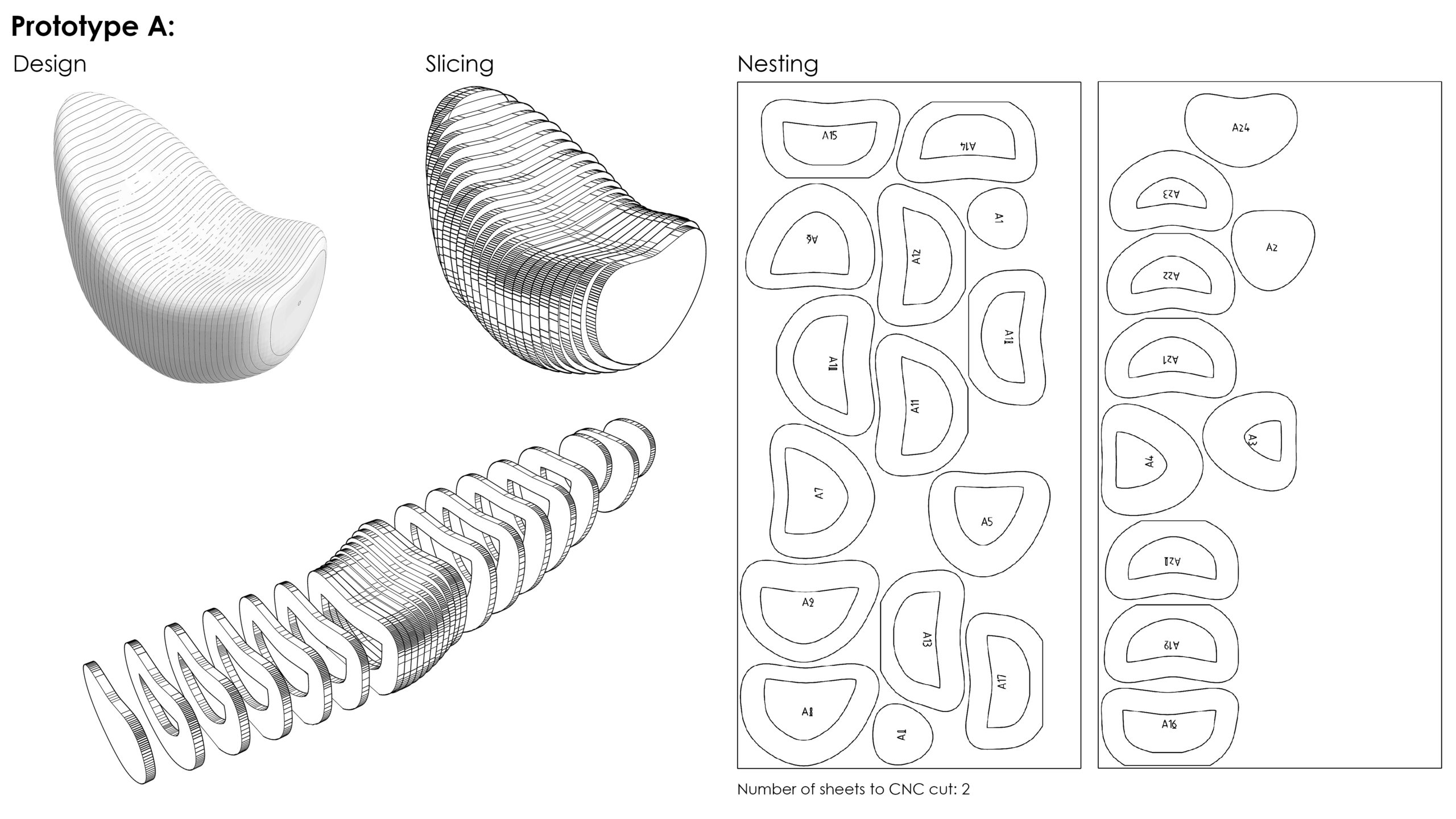
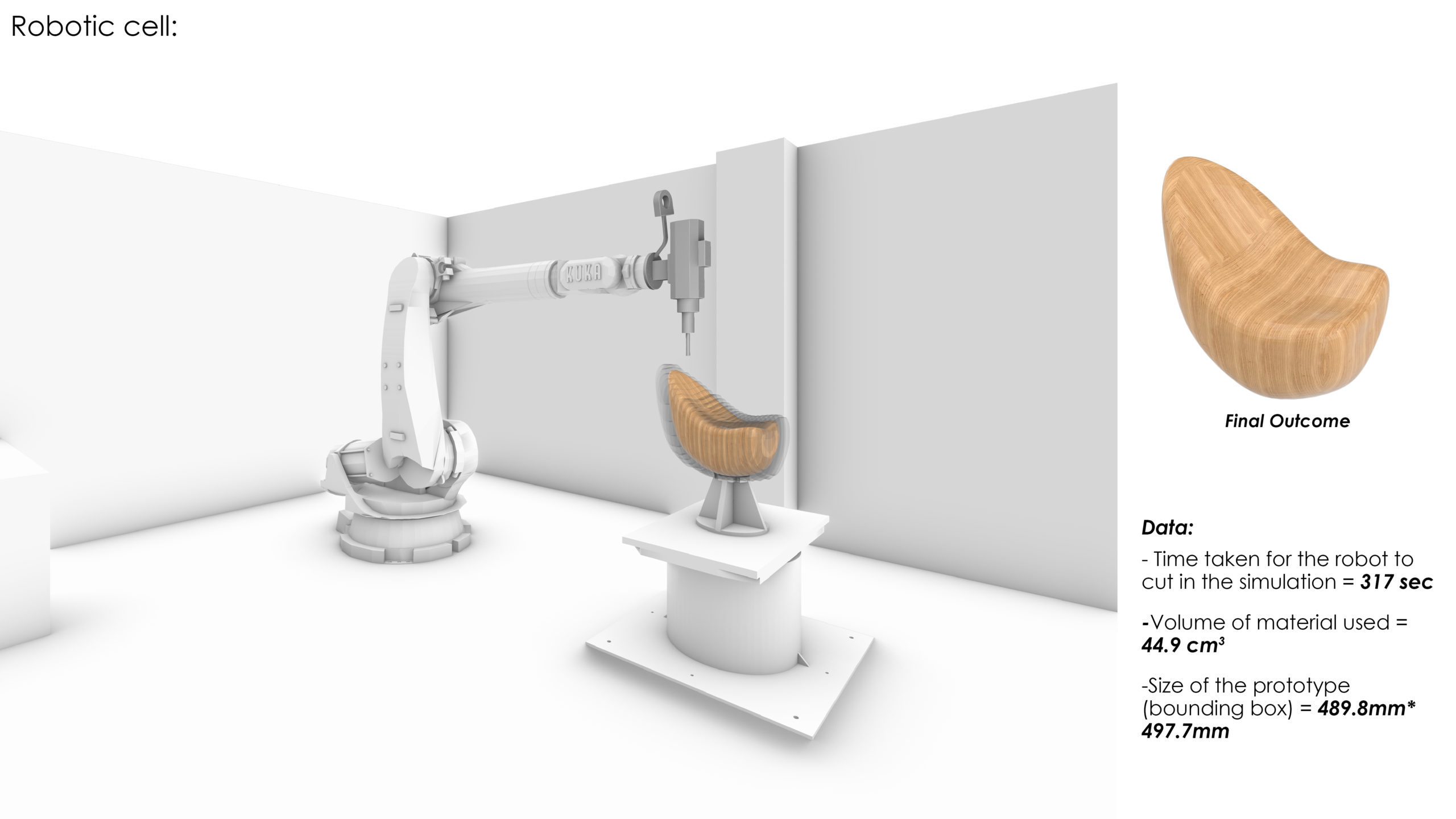
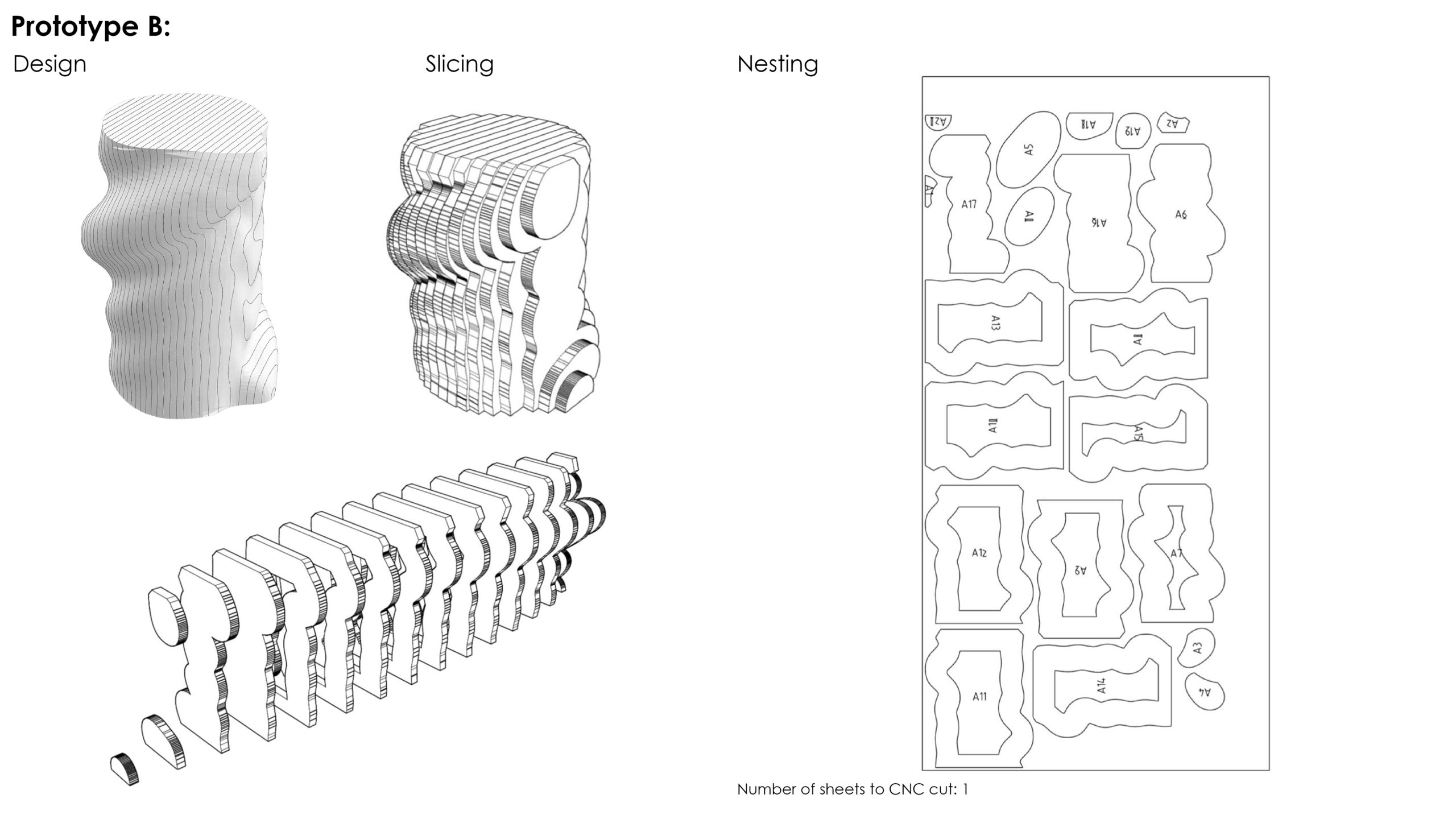
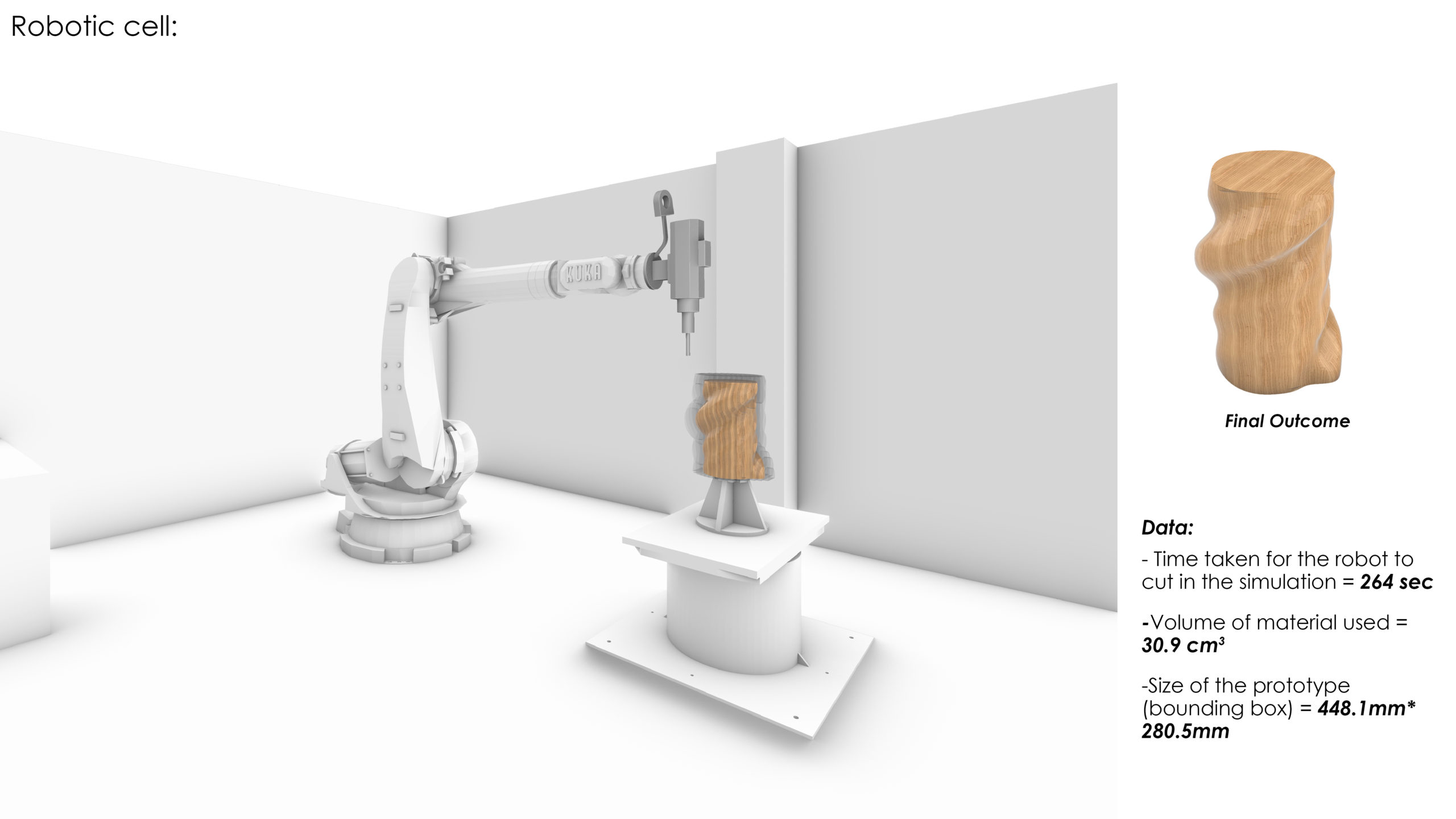
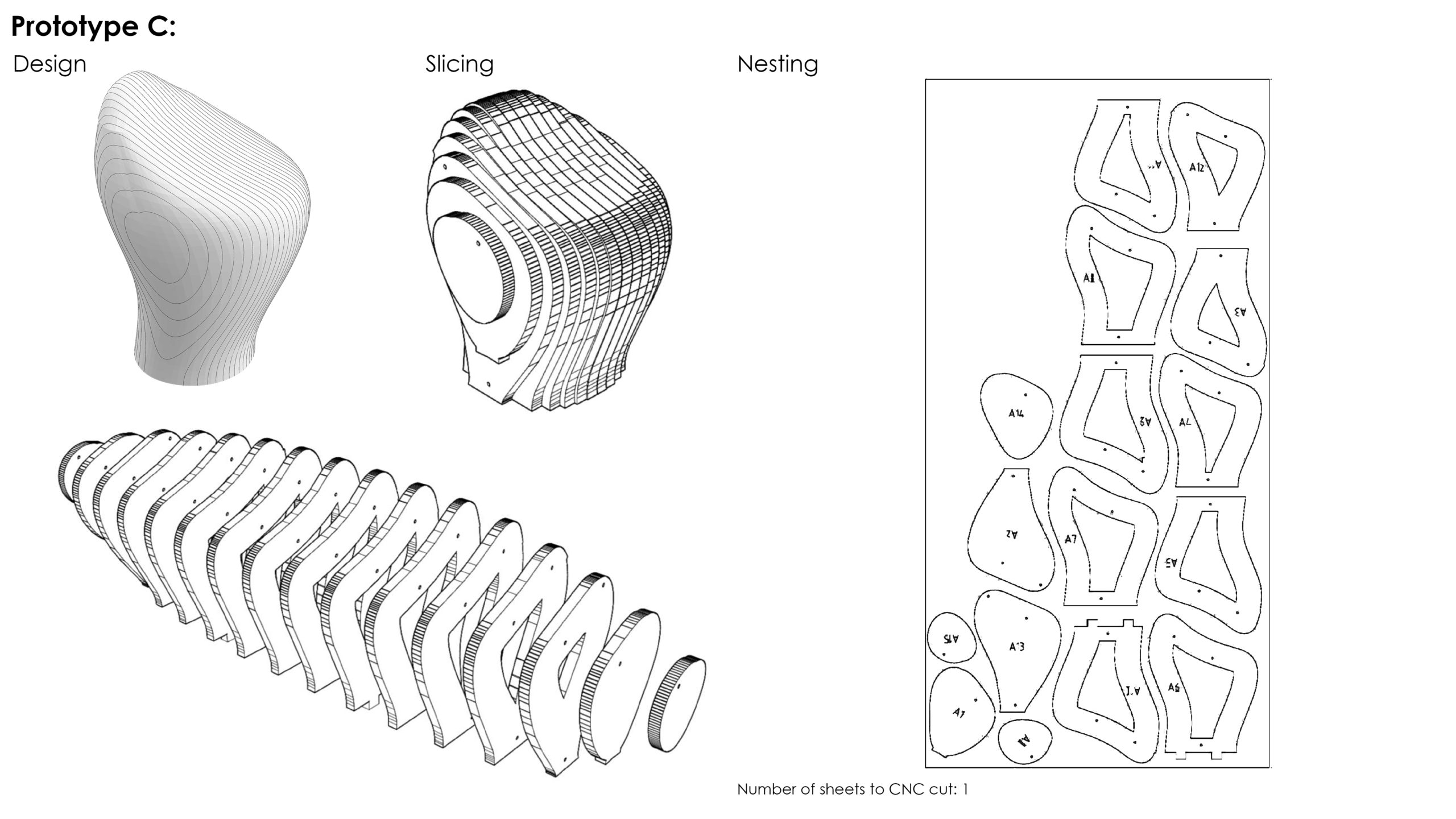
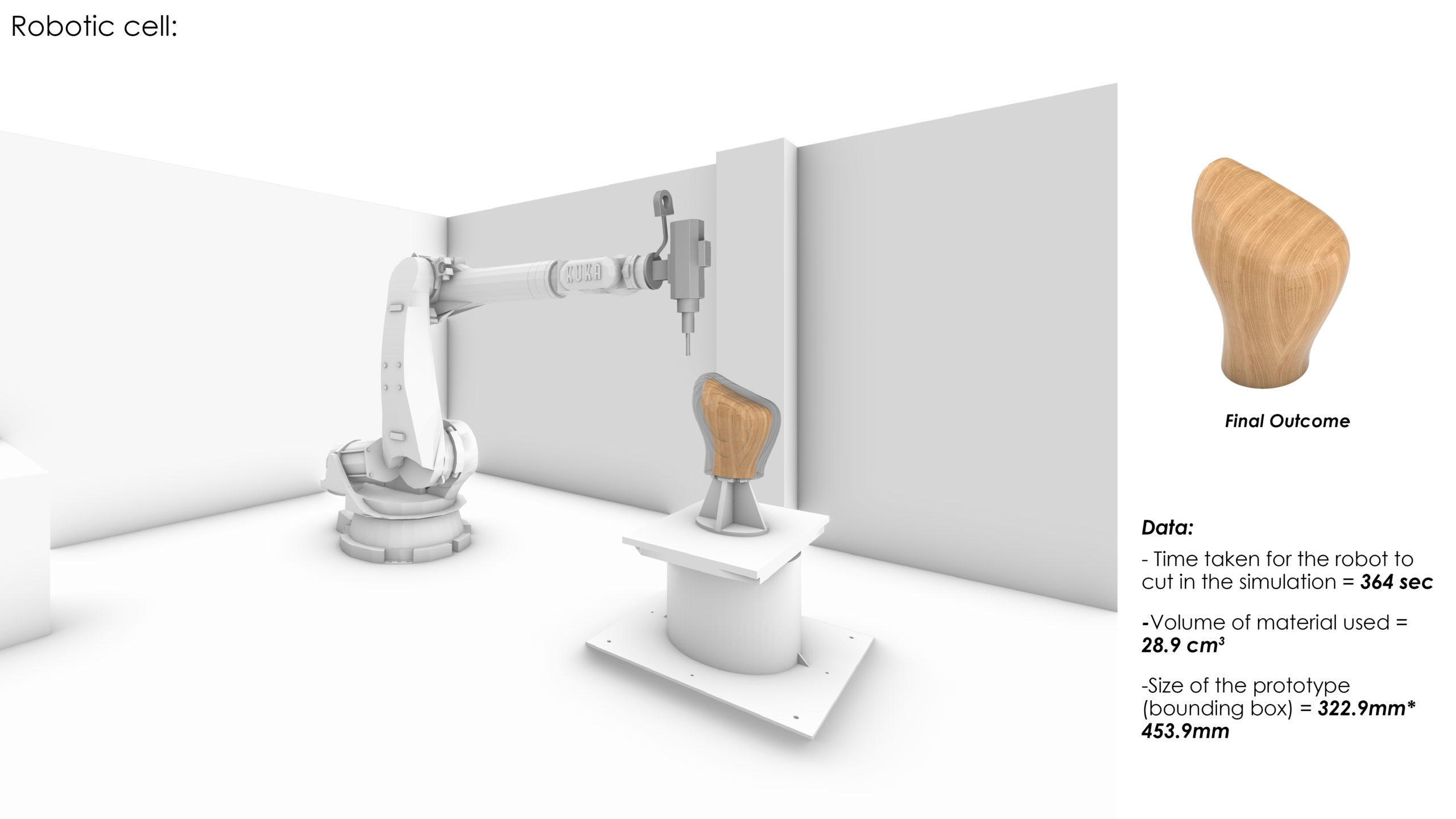
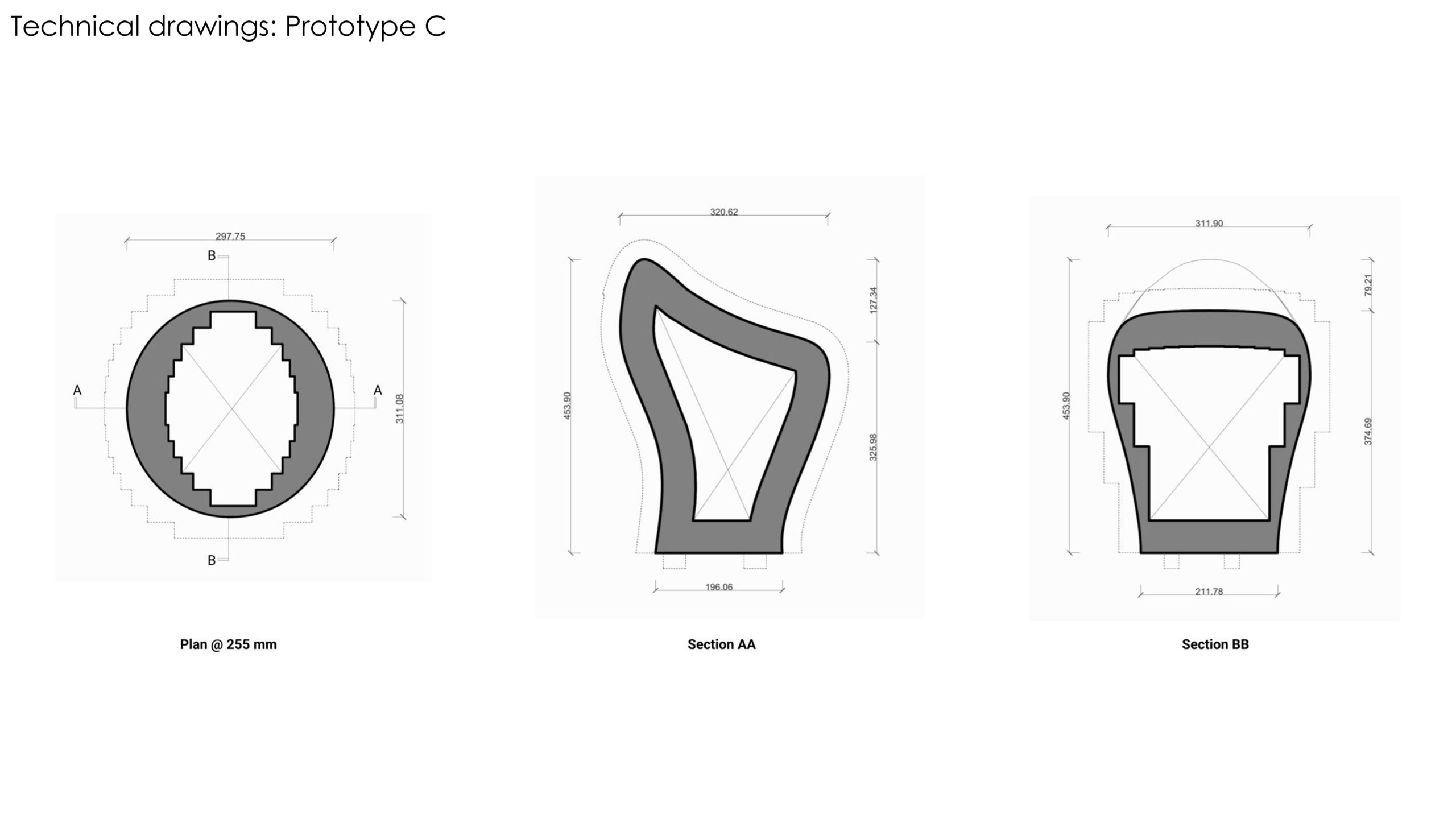
After evaluating all three prototypes, Prototype C was selected to be fabricated since it was under the constraints of the fabrication process of the workshop.
Robotic simulation of the selected prototype – Prototype C
Technical Data:
- Plywood Thickness = 24mm
- CNC Milling
- CNC milling bit used= 6mm
- Drilling with CNC = 5 minutes
- Inside cuts milling bit = 20 mm
- Inside cuts = 20 minutes
- Robotic Milling
- Speed = 10000 RPM
- Bit size=20 mm flat mill
- For the top dome
- Speed = 8500 RPM
- Finishing layer speed = -9000 RPM
- Bit size =16 mm ball mill
Process:
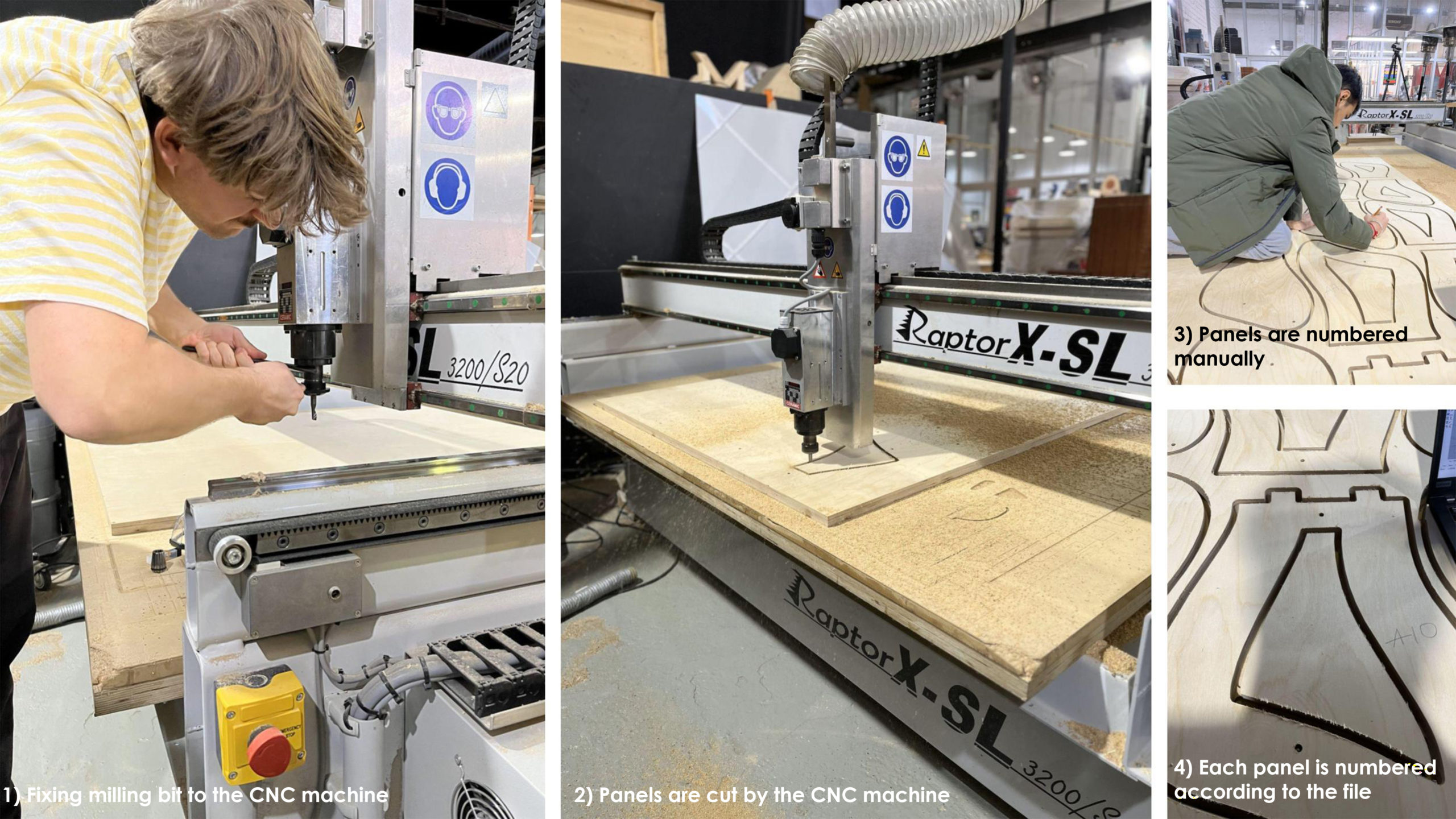
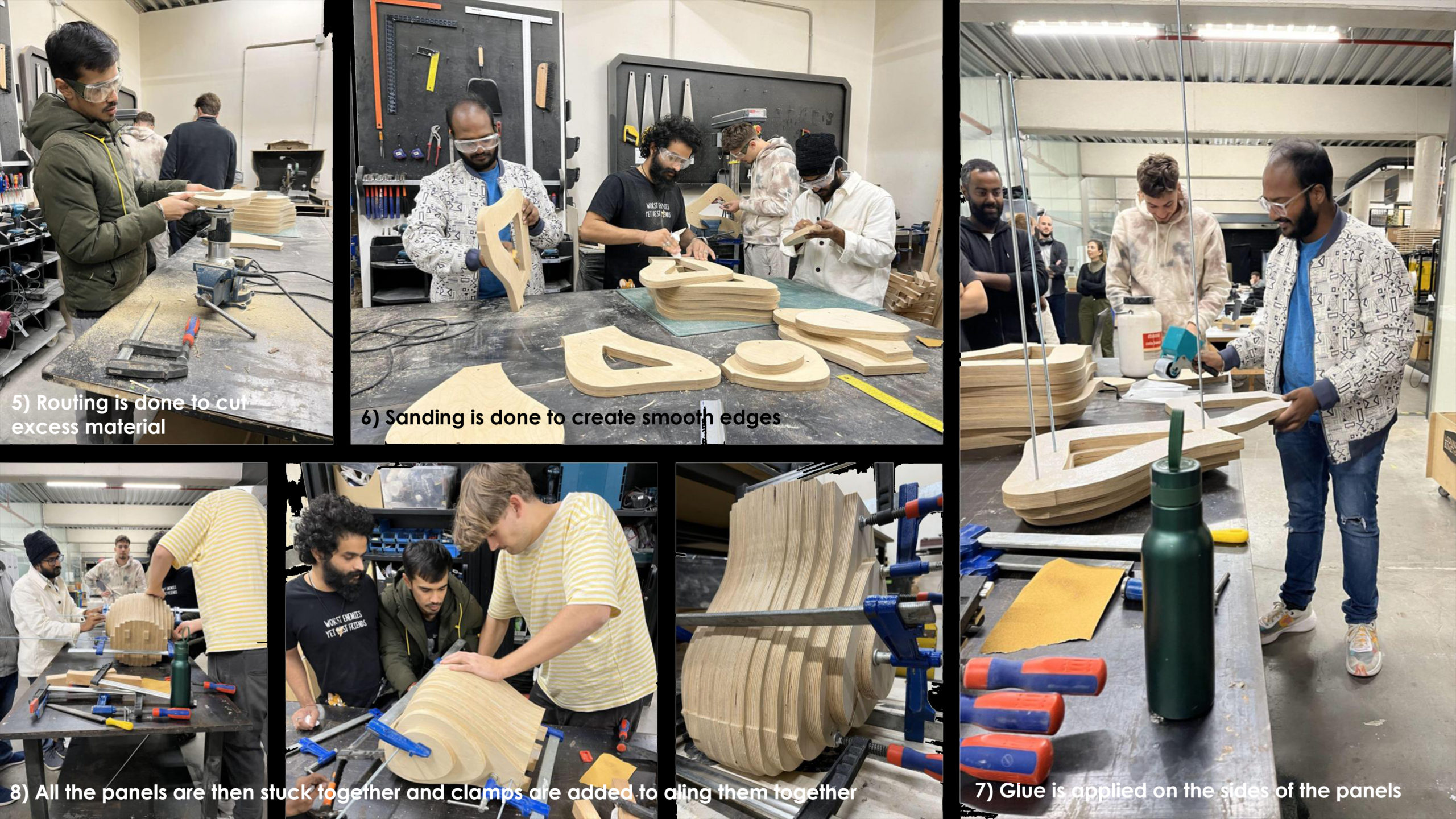
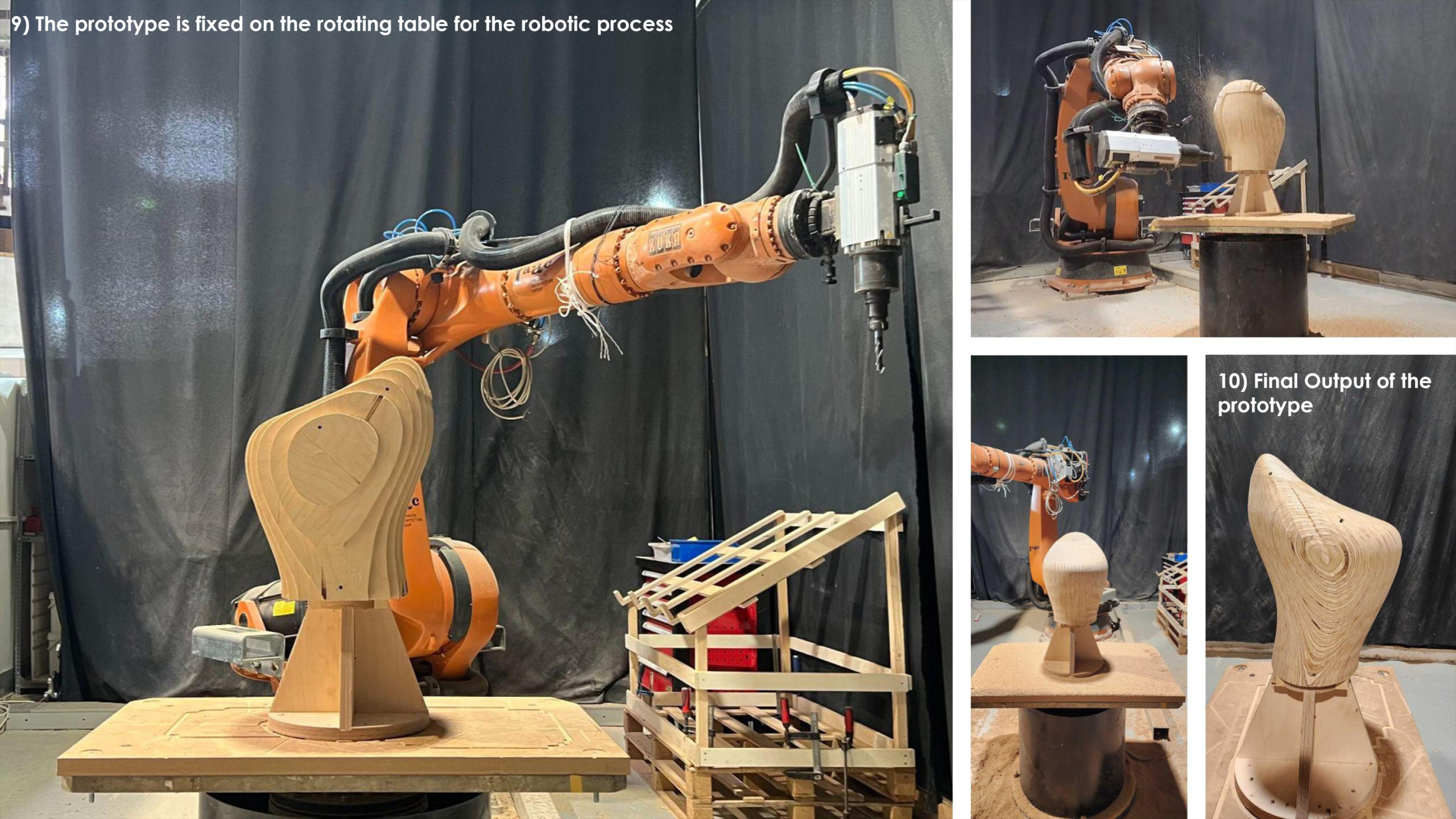