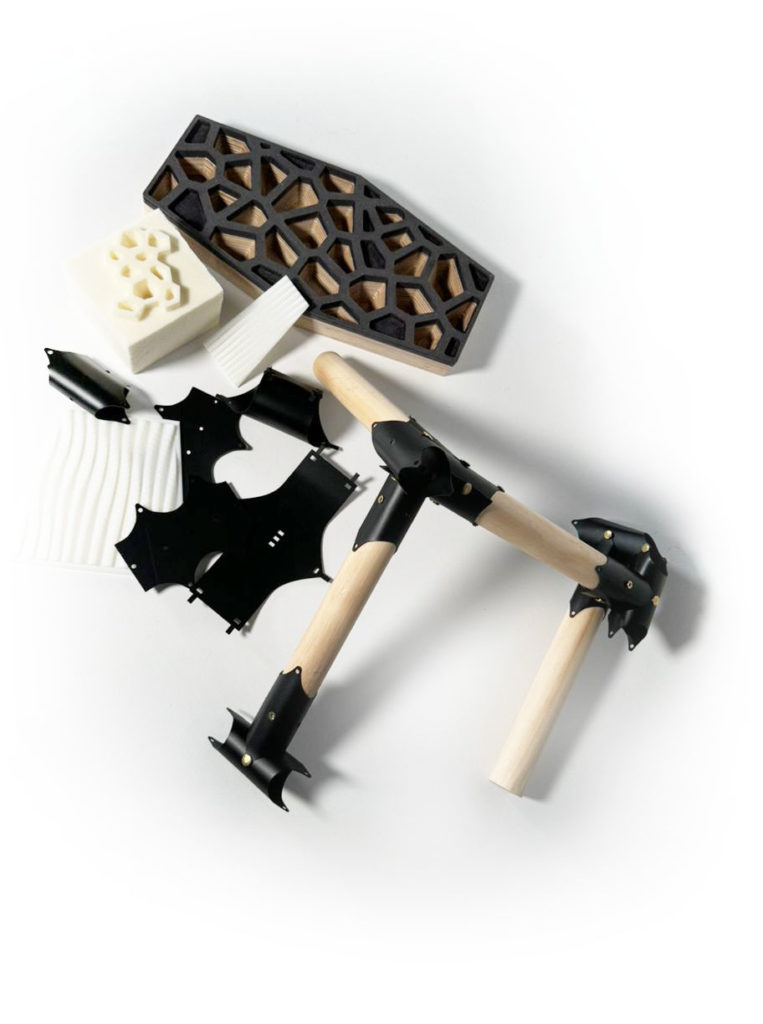
ABSTRACT
The aim of the digital fabrication course was to prototype and produce desired designs in 3 different methods like 3D printing, laser cutting and CNC milling. We explored variety of machining strategies to create particular textures and joints while the fabrication time was under consideration.
EXERCISE 1 _ CNC Milling _ Prismatic Voronoi
The final model is created from 6 millings in two different materials (plywood 30mm, black MDF 10mm). In the black MDF we have two pocketing processes, one fully cut with Rough Depth/Cut(dz): 100% and one with Rough Depth/Cut(dz): 70%. The second cutting is selected for the small shaped voronoi pieces that cannot be cut into large depth based on the diameter of the mill (6mm), as we noticed in test 1. For cutting the plywood we used horizontal roughing with Flat Mill 6mm where the MDF holes are converted in prisms. For parallel finishing we needed BallMilla 6mm.Finally, we joined the two layers of each material.
CNC Milling strategies
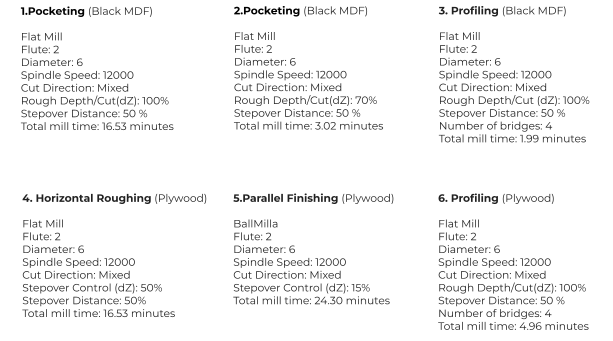
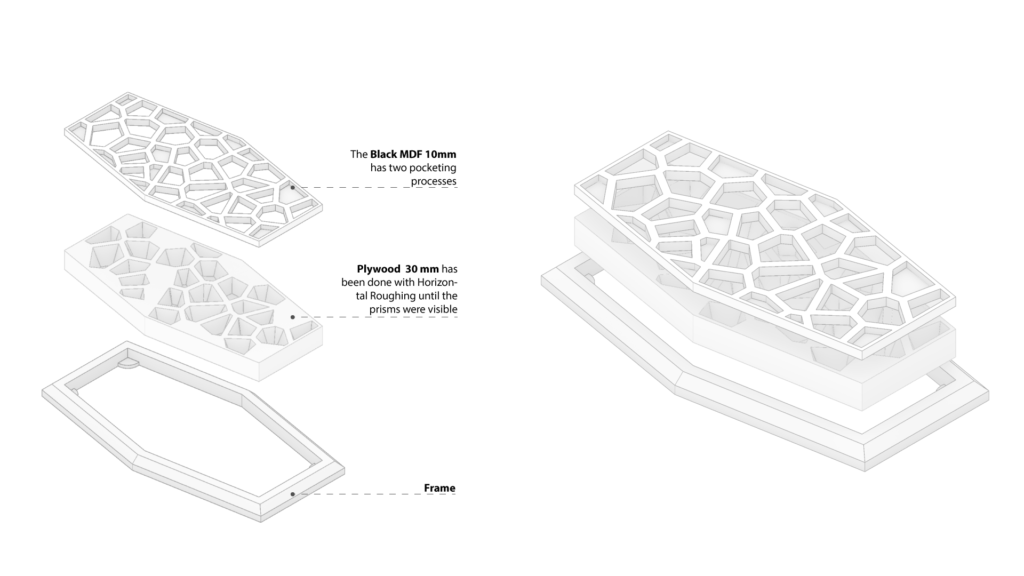
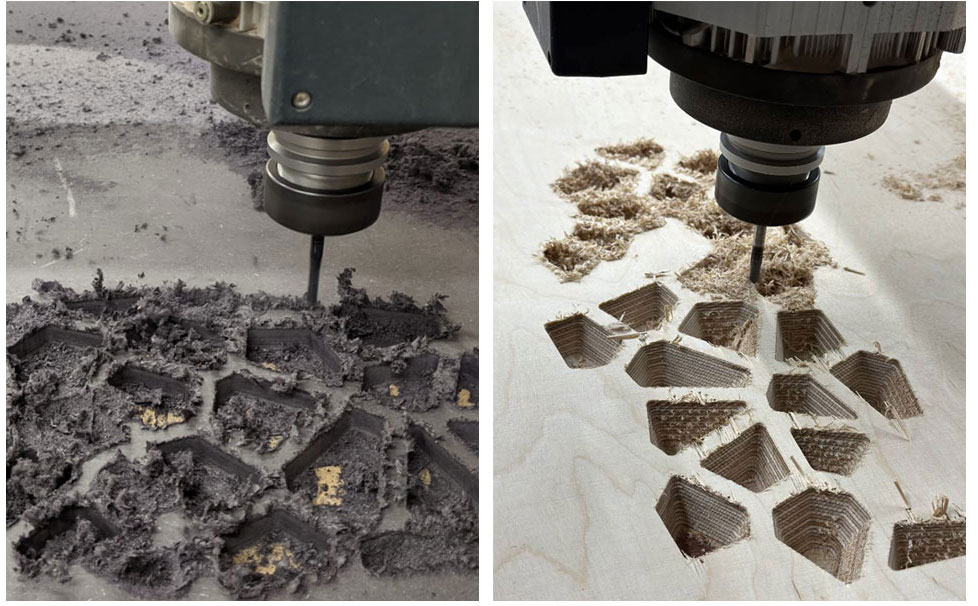
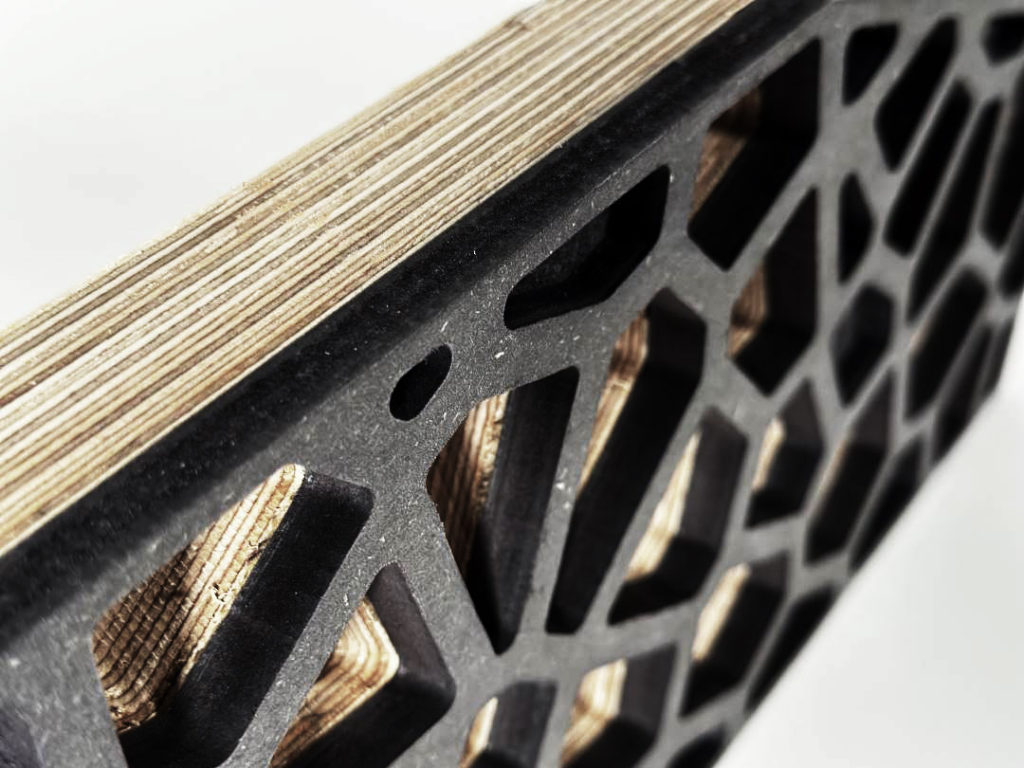
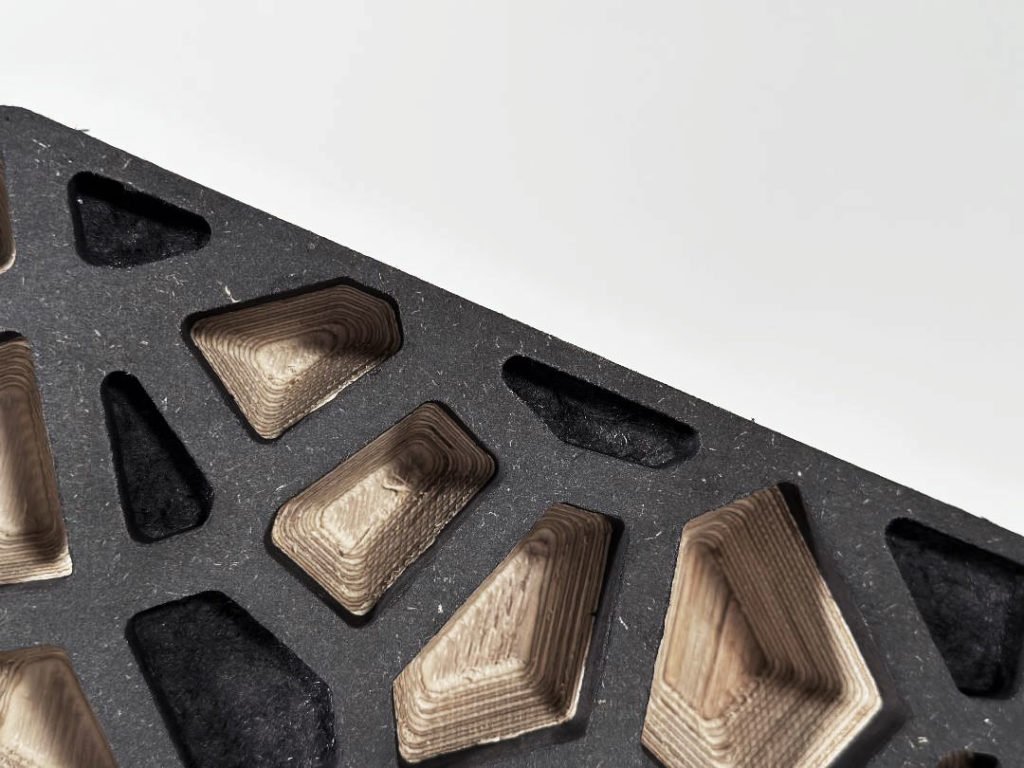
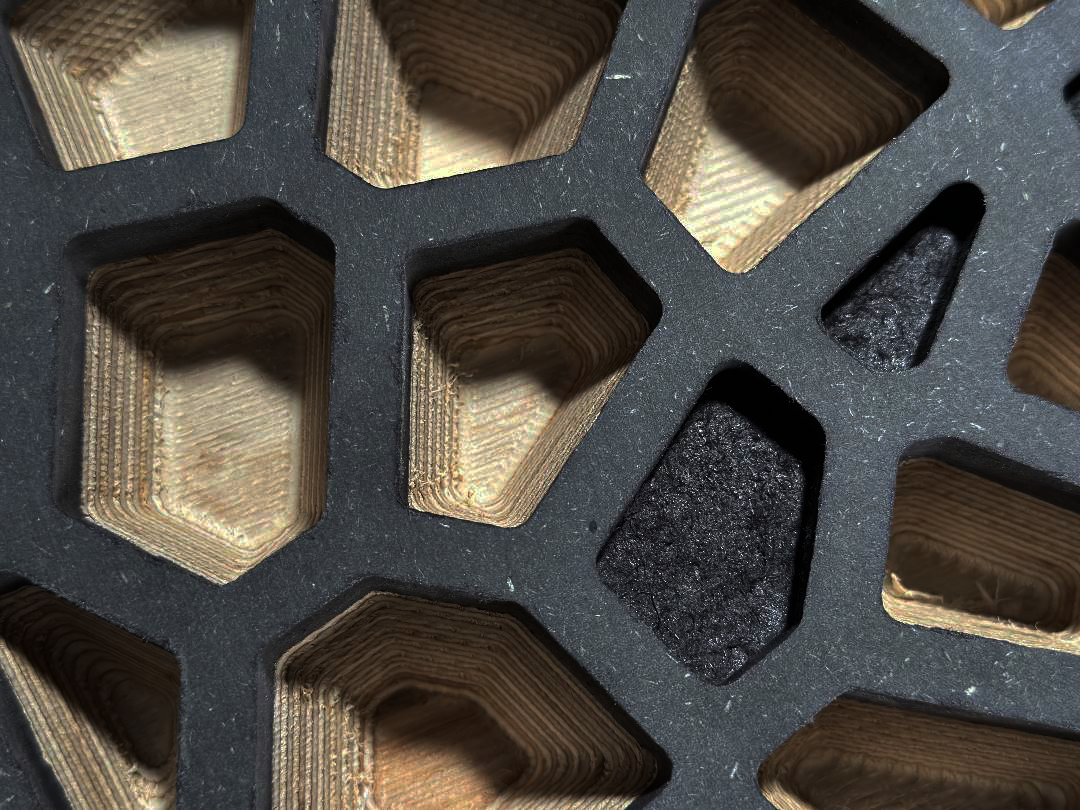
EXERCISE 2_ Laser Cutting_Bending Modulor
Taking advantage of laser cutting techniques, the aim of this exercise was to join recycled timber beams into informed and complex spatial structures using the bending technique. We managed to combine them all to reach to the desired output. Joints locking to each other while having timbers in between led us to have an unlimited modification of design. We used polypropylene material for our joints and assembled them with rivets.
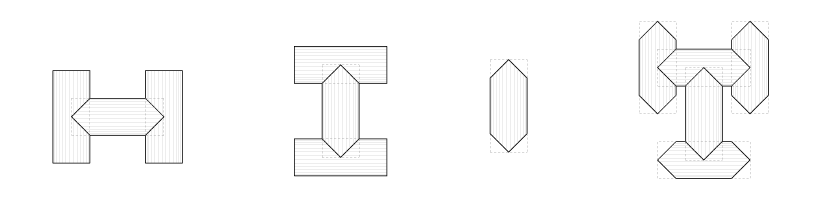
Parameters
- Laser cutter: Rayjet 500
- Power: 60
- Speed: 3
- Material : Polypropylene, 0.8 mm
- Lasertime : 15 minutes
Digital design process
- Identify the geometrical terms in order to make a stationary bending joint
- One modulor that could be aggregate
- Creating multiple joints and positions
- Finding adaptive object for joint
- Making paper modulor to test the overlap
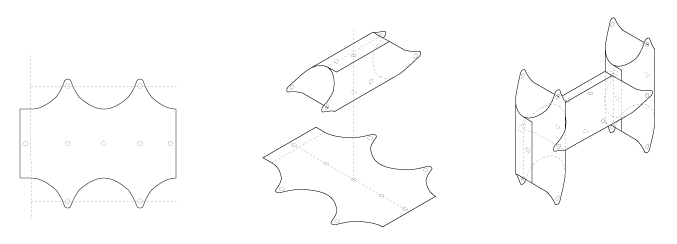
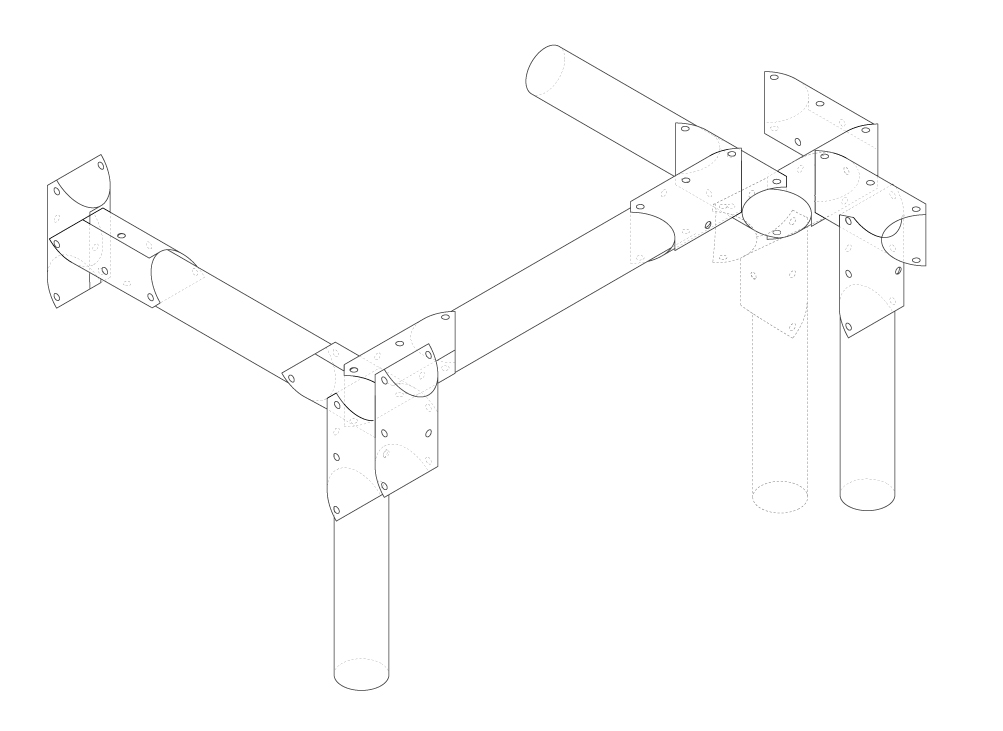
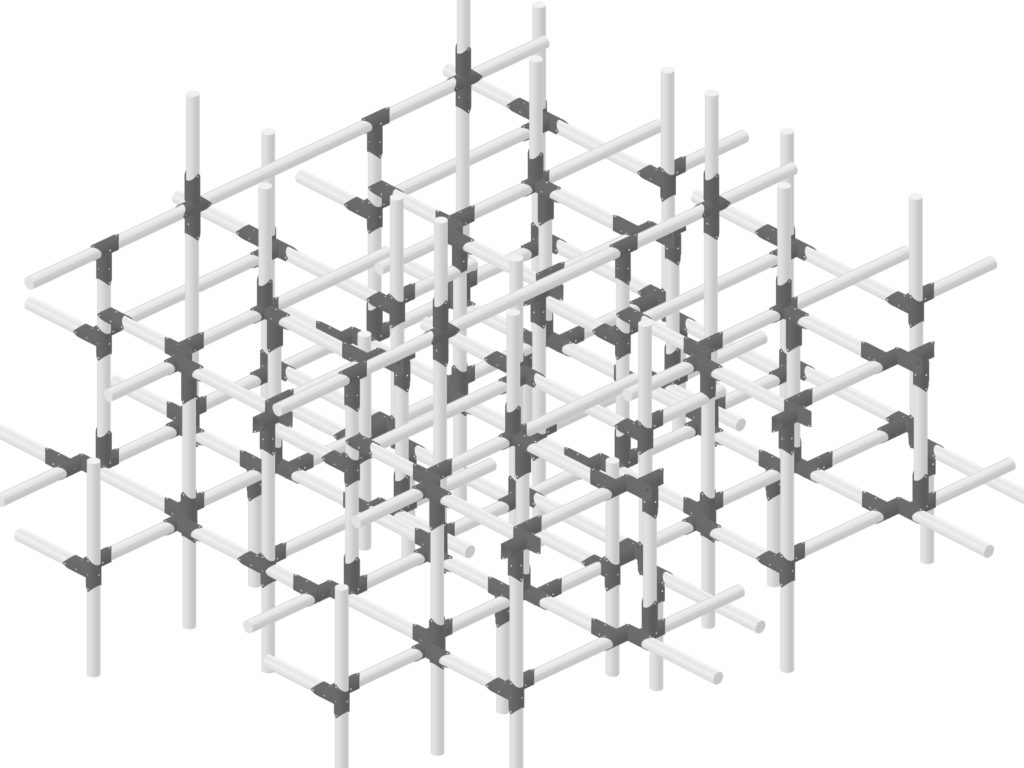
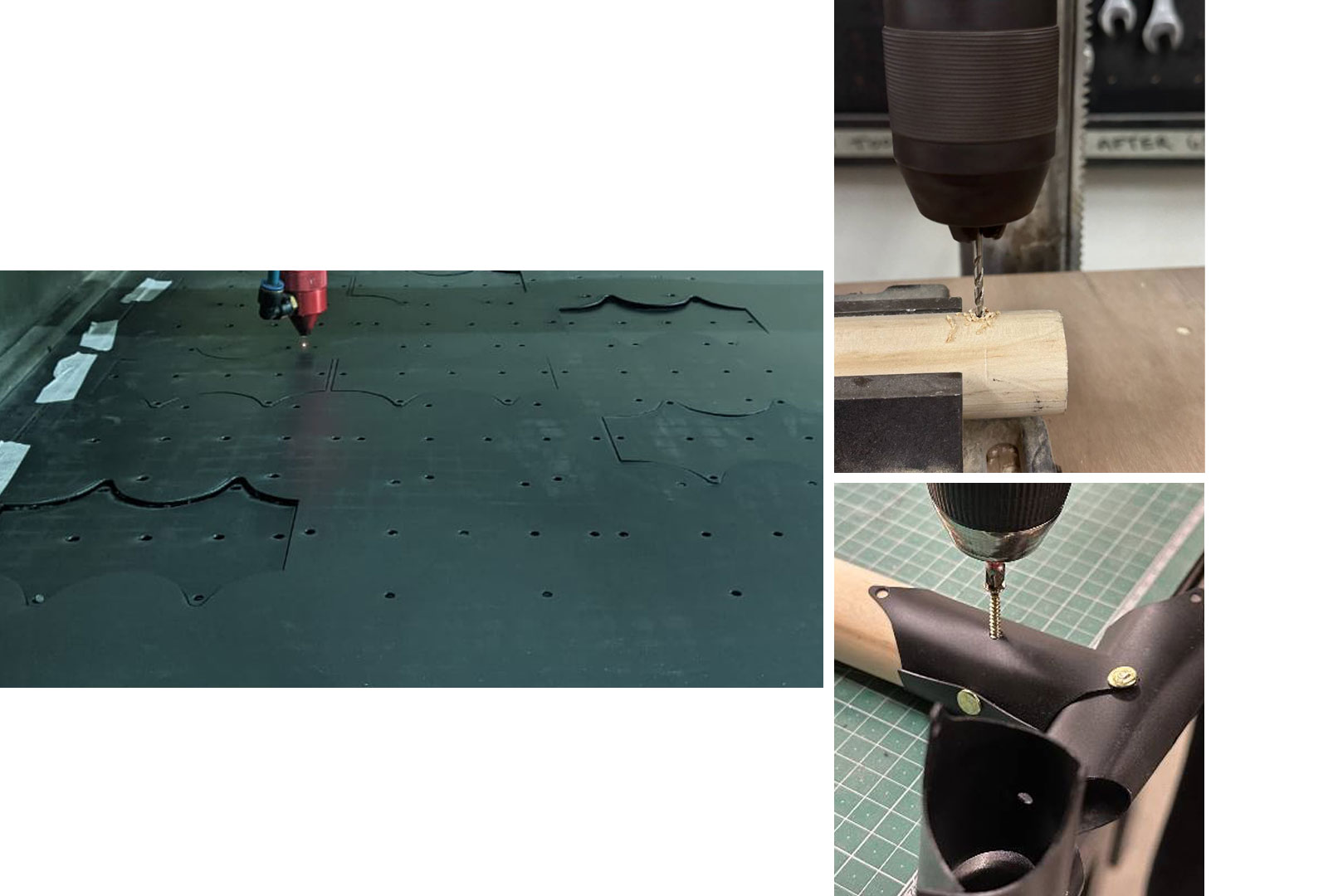
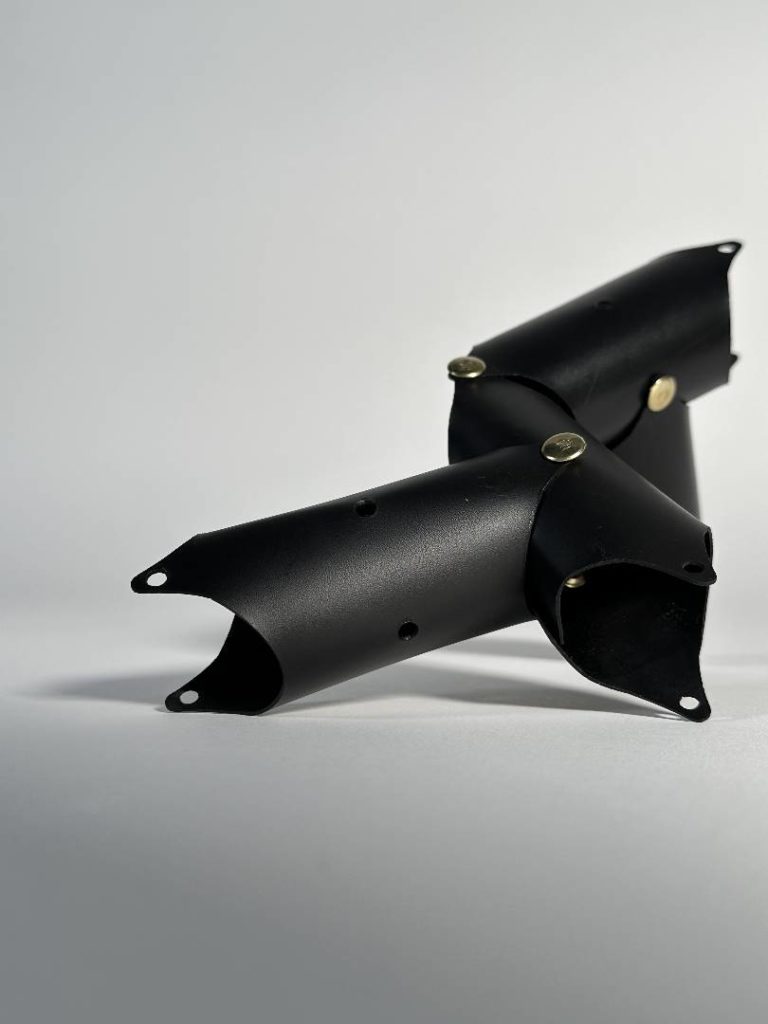

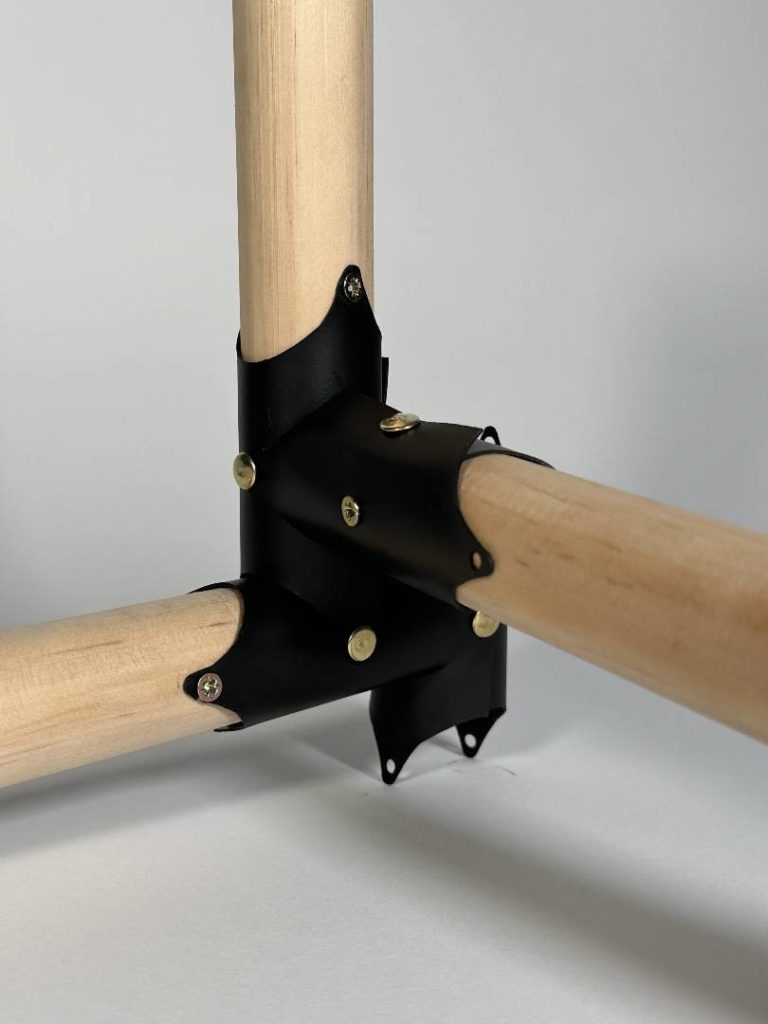
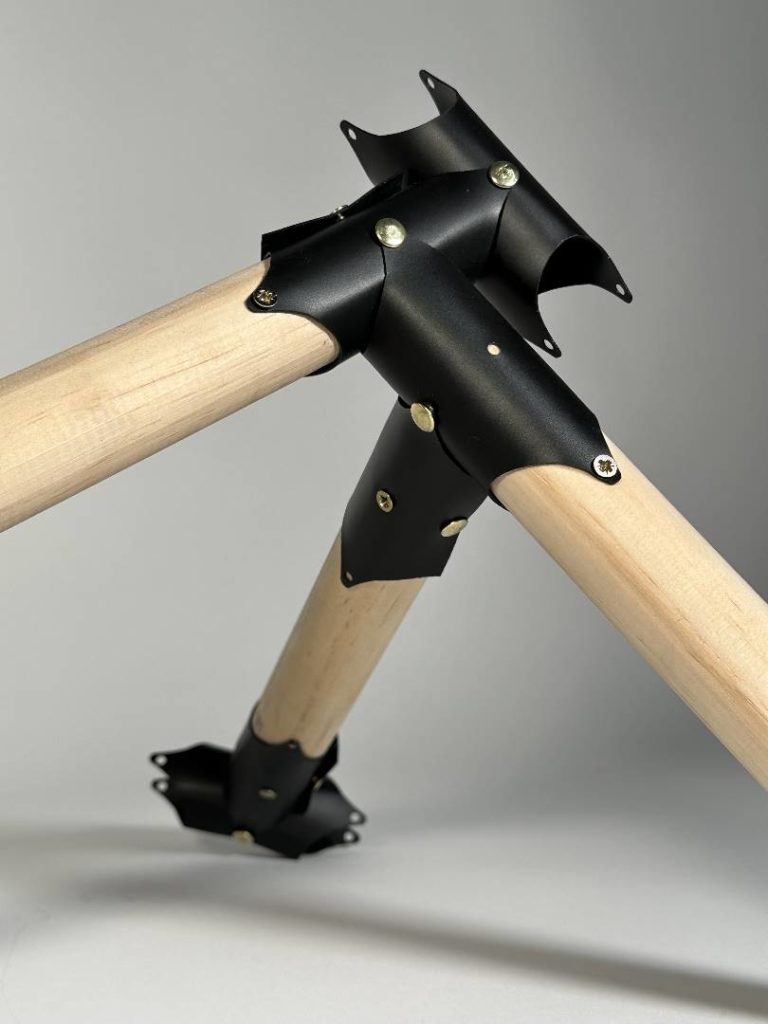
EXERSICE 3 _ 3D Printing _ Waving

This project was to practice 3D production with M200 3D printer. We took algorithms into account by using the desired attraction point on grasshopper. The extracted mesh was edited in Rhino and saved with .stl formatting so that it could be readable by Z-suite. In this software, factors of printing was checked before sending the data to the printer.
Parameters
- Estimated print time: 7h 59m
- Material usage: 42.16m (100g)
- Printer: Zortrax M200
- Material: Z-ABS
- Nozzle diameter: 0.4 mm
- Layer: 0.39 mm
- Quality: Normal
- Infill: 20%
- Raft: Enable

