Group Y1
A series of experiments, to reflect on internality, movements away from the outside and to look upon it. A swift movement which engulfs you, a series of lines to project your light through, an open face held in deep space by many arms.
There is nothing outside to look at, if you don’t look at it from the inside.
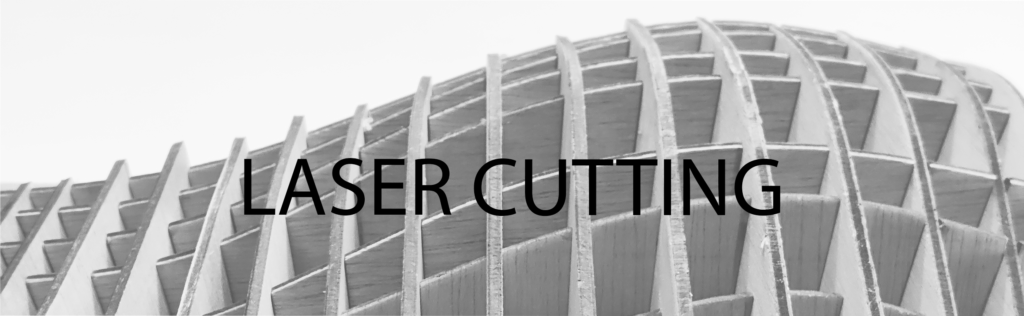
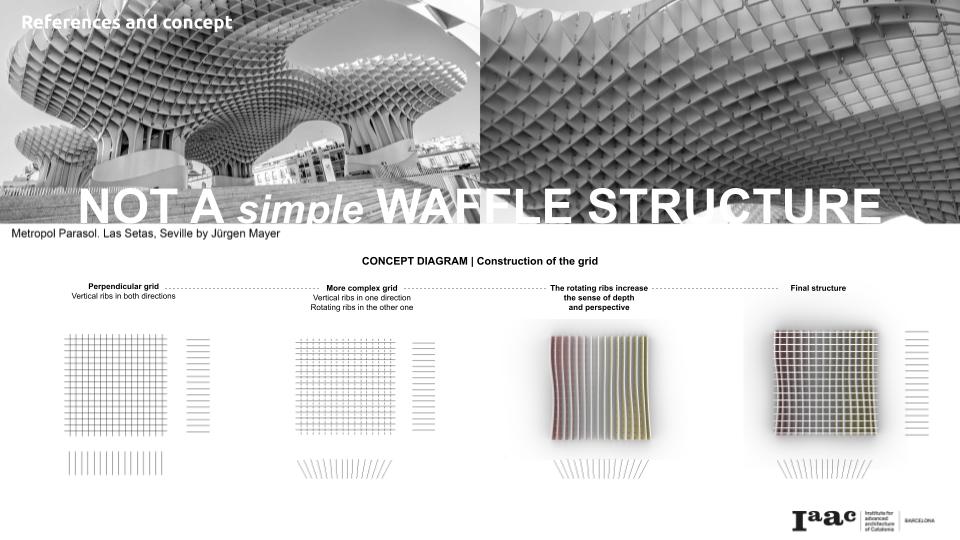
The geometry was derived to heighten this connection of the inside to the outside, by rotating the ribs of a single axis. This creates a modulating effect of light and depth perception, with a consistent structural and sensory force underneath it.
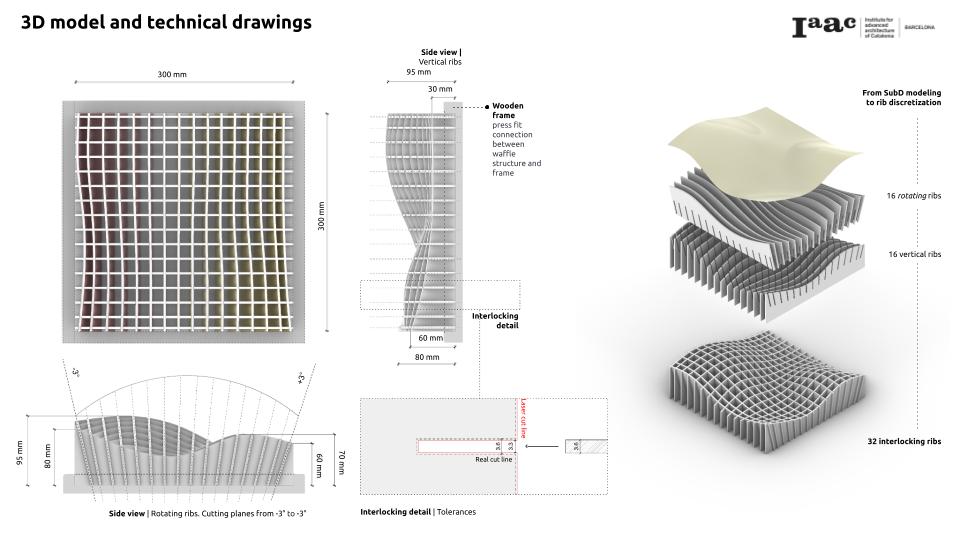
The movement across the surface plane was derived from SubD modeling, allowing vertical shifts across the rotation and creating the impression of a material pulse. This creates tension in the plywood, giving it rigidity and outward pressure to help lock it into the frame.
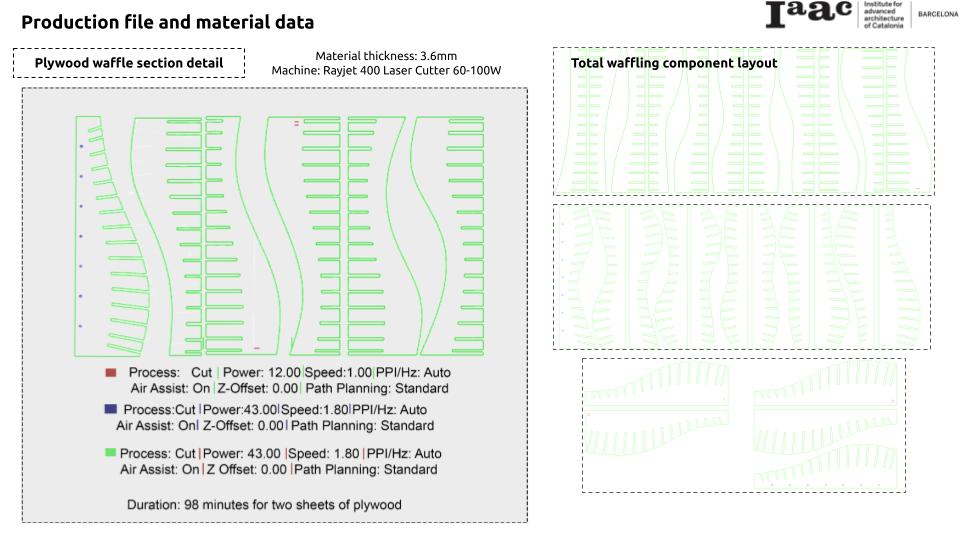
The waffling components were then partitioned and nested to optimize for plywood usage. The material was 3.6mm thick, making it reasonable to produce using 3 cutting processes with 2 different operations (one marking and two cuts) under 100 minutes.
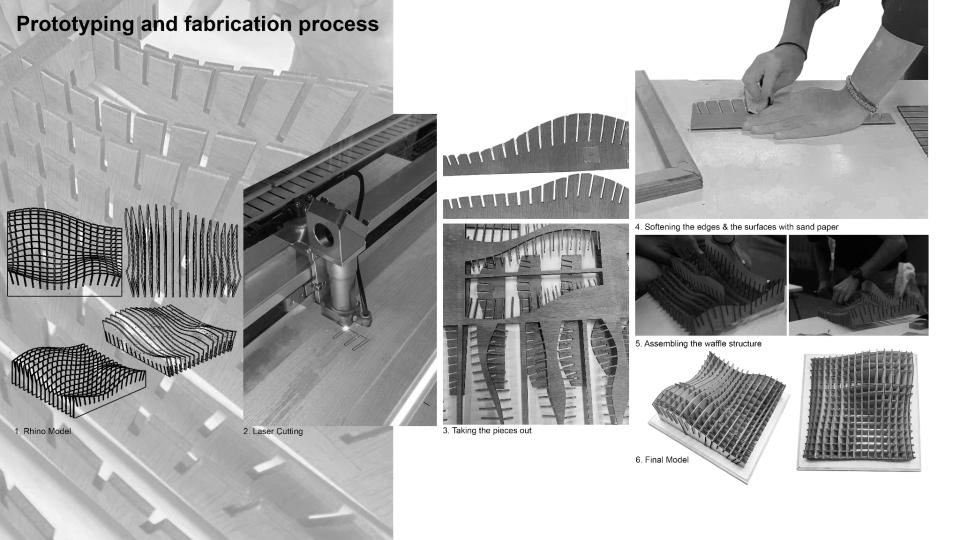
The pieces were individually sanded and softened to adjust tolerances and overall finish. The twisting rib pressure lead to some difficulties in assembly, and this showed us the interaction of material capability and geometrical forces in this process. In this case, it leads to some damage to some individual pieces, and tensile capabilities must be looked at more carefully for complex waffle structures.
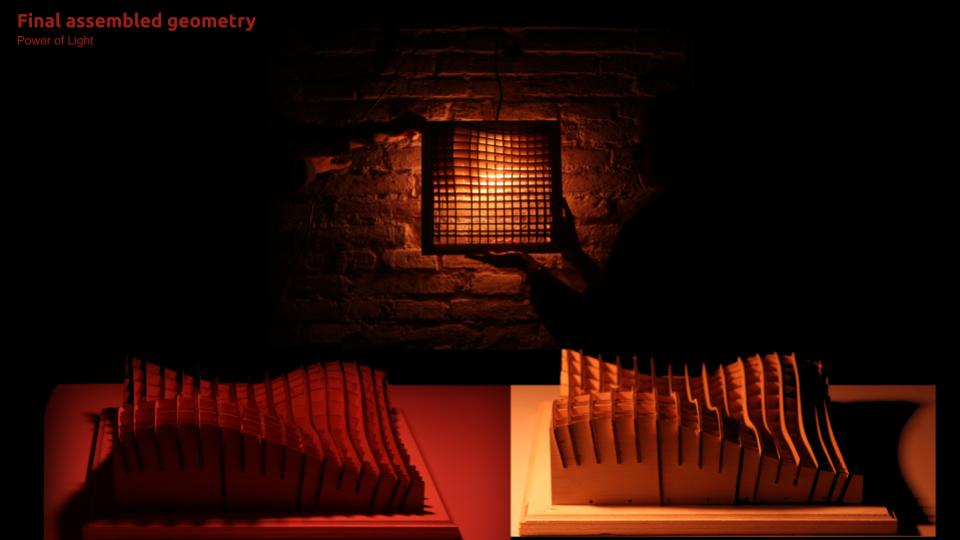
The light diffusion from the final result is captured here by these photographs, under a dark illumination effect. When viewed from the top or the front, there is a connection in the splitting and shaping of light from the inside and the outside. A harmonious flow between these separated spaces.
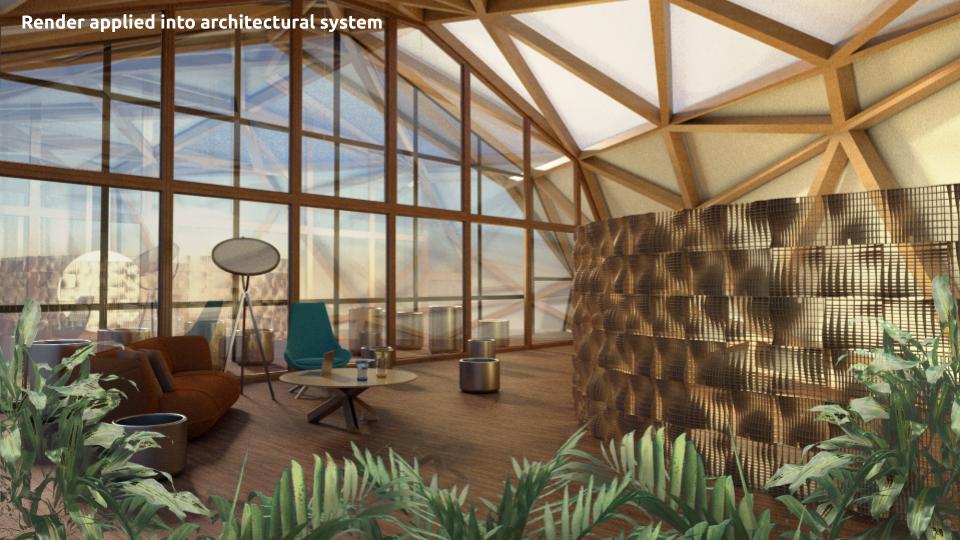
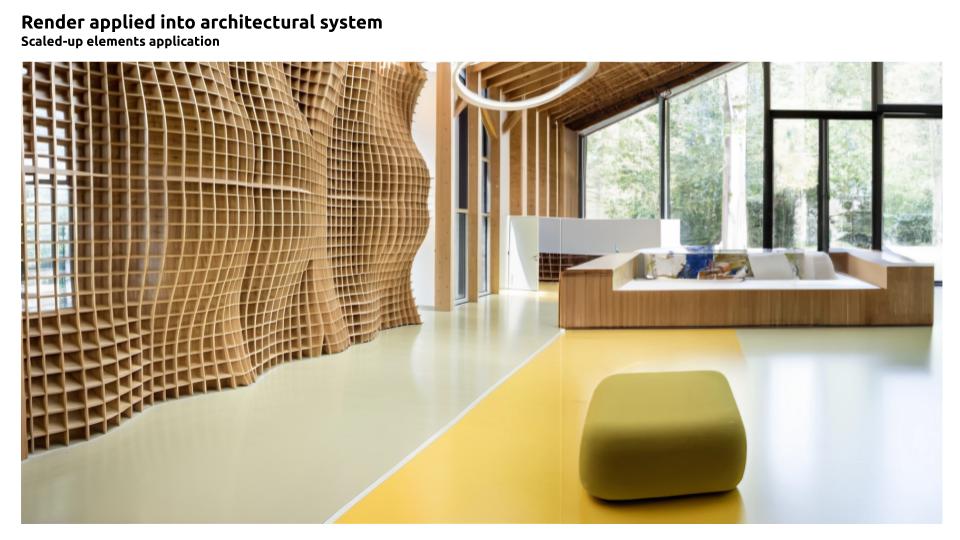
The above images, speculate on the possible architectural implications of this piece, either through modular installation in an interior space as a hollow partition wall, or as a larger structural element using a material such as timber. They both share the effect of transparent intimacy, and could be shaped for either use.
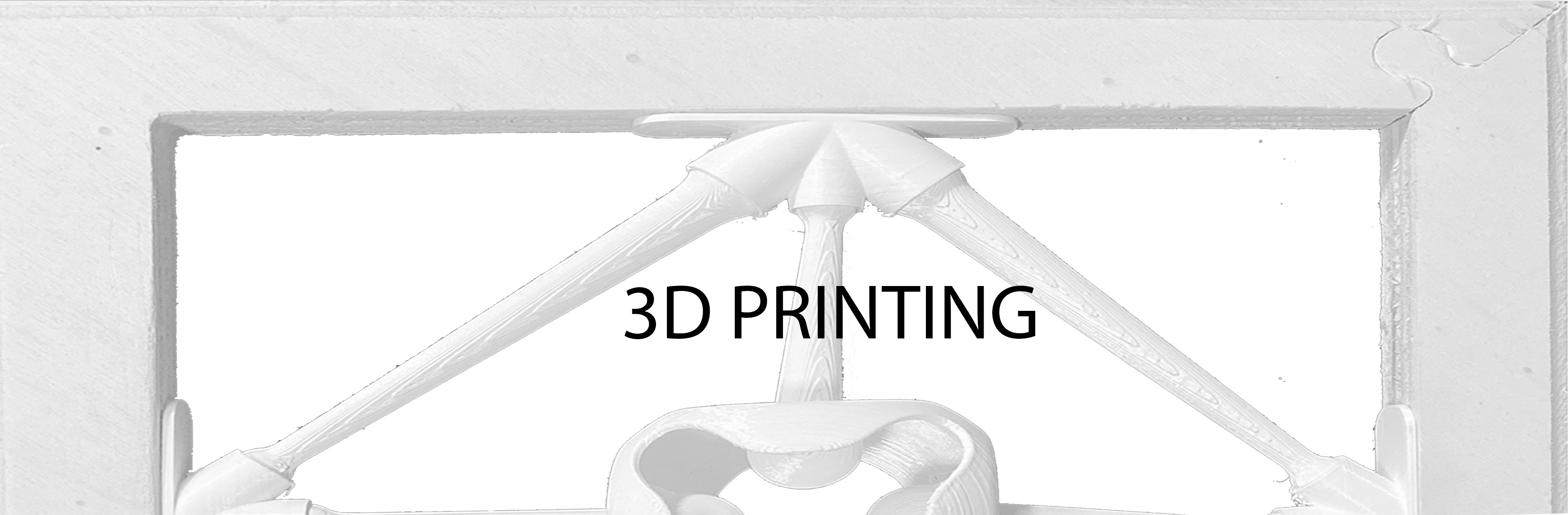
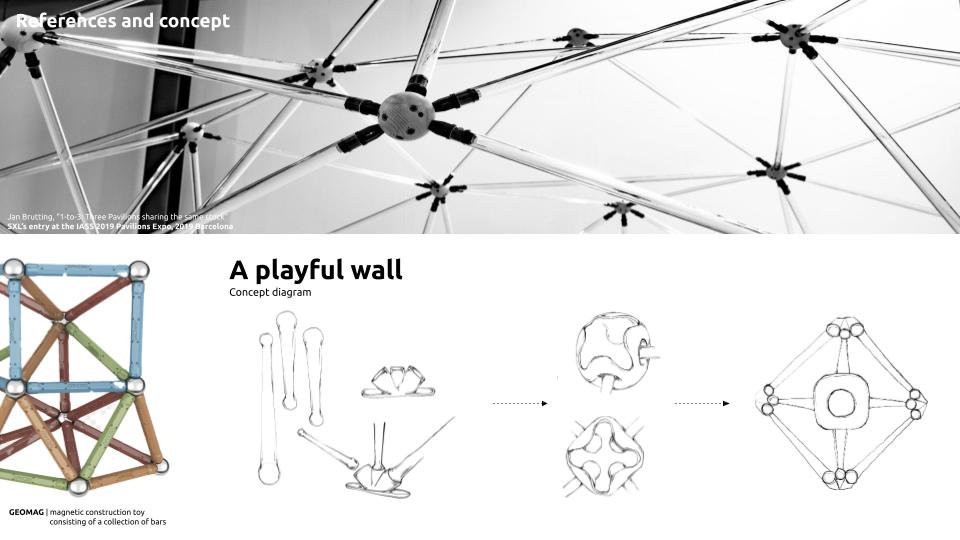
In this technology, we were interested in studying the limits and possibilities of 3D printed modular units, and therefore learning more about the deformation qualities of PLA, a commonly used printing filament. This lead us to discussing the Geomag, a children’s geometry toy, which has magnetic sticks for edges and balls for vertices, to create unique and easily constructible shapes.
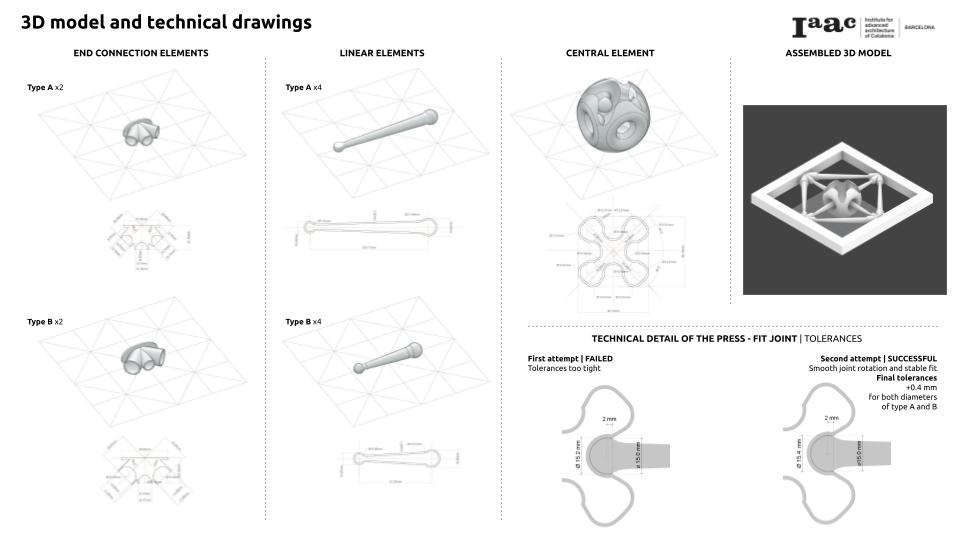
We decided to create 3 components: edge connections, the edges themselves and a single large component in the center to bring together the connections. The complete model creates an effect of an orbit, pushing outwards the frame and held up only by tension. We had conducted several tolerance tests for the ball-and-socket joints, and were successful on the second attempt. This had the ball fit and rotational capability we were interested in exploring.

The central element was printed vertically as a single piece. The linear edge elements were printed horizontally, and split in 2 to reduce the need for supports. The edge connection elements were printed first without supports, and this led to some detailing issues at the base of the socket. They were then reprinted with a 40 degree overhang support at 10% density, and this formed clear and well-formed pieces. The total printing time was 7.5 hours in total.
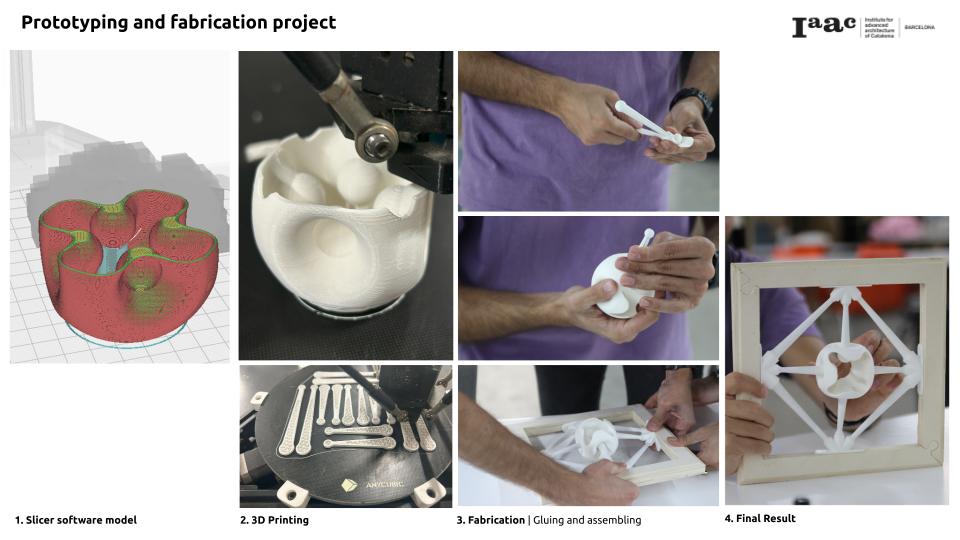
The STL model was sliced and interpreted by CURA, and printed over 3 print cycles. The linear elements were then pressed into the socket joints and central element, and completed the assembly procedure.
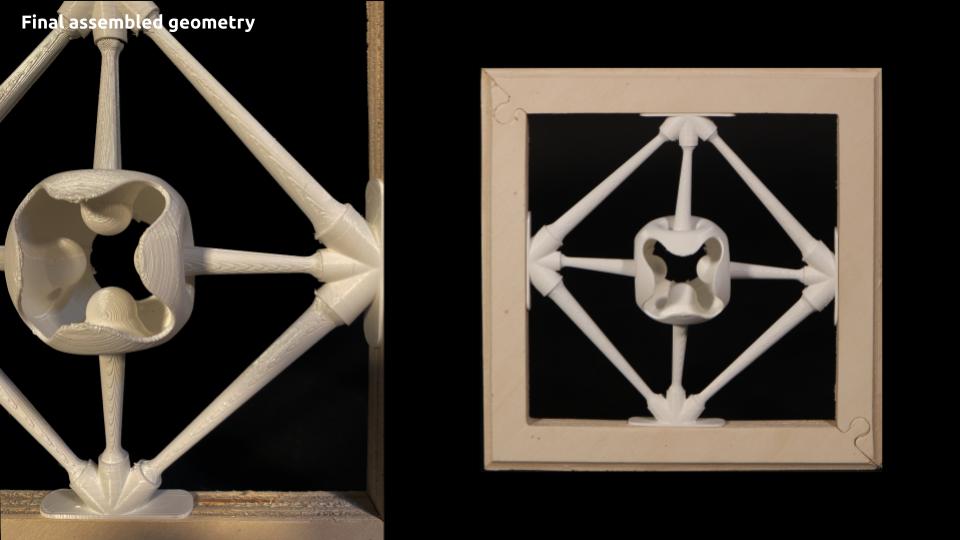
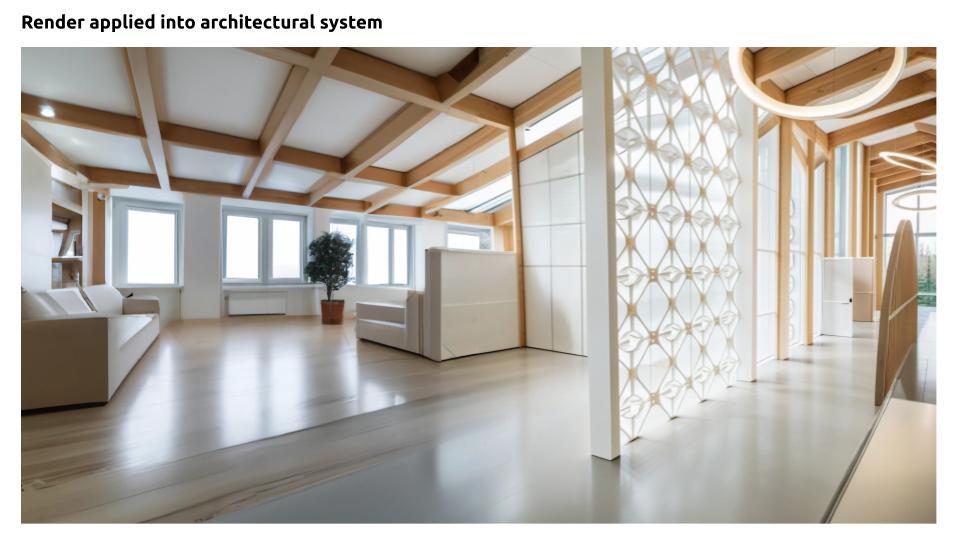
The orbit is held up with a softness, and the moving shapes of the layers on the objects create an effect of rotation and stretching under tension within the bounds of gravity. This is visible on the current scale, and at a larger installed level, the orbit can be used to create a partition wall. The wall brings a strength in its rigidity, but is also incredibly playful, resulting on a very unique pattern overall.
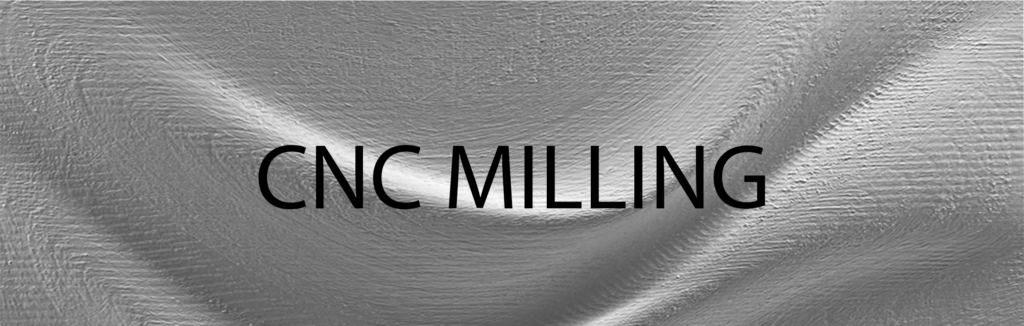
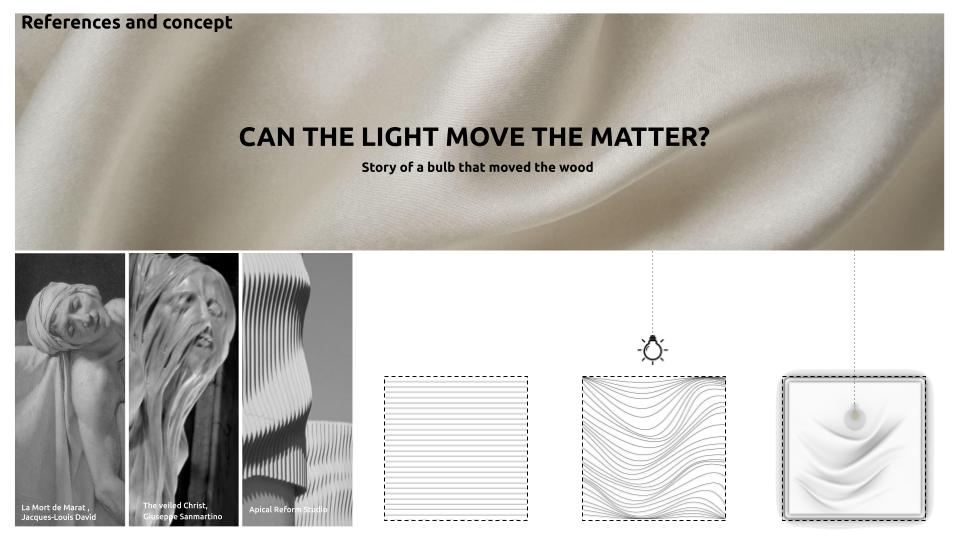
For this technology we were much inspired by the possibility of invoking intimate lightness, through the movement of fabric and light textiles. The shadows of a folded fabric are almost hidden, until they’re brought out and moved by the light. This fabricated piece which could almost be interpreted by the light was incredibly interesting to us, and something we wanted to explore.
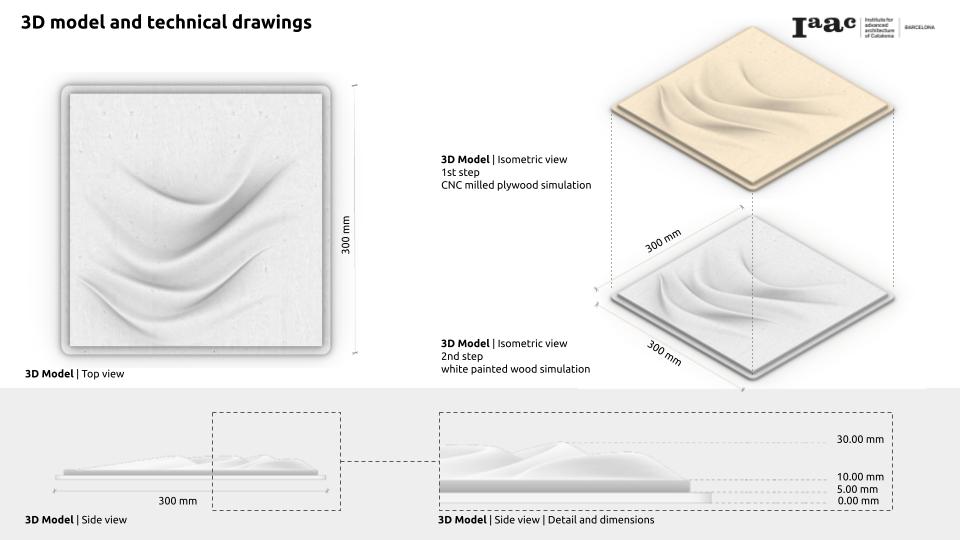
The model’s geometry was done using SubD modeling again, which allowed us to create organic draping moves and have a sense of rolling verticality across the piece.
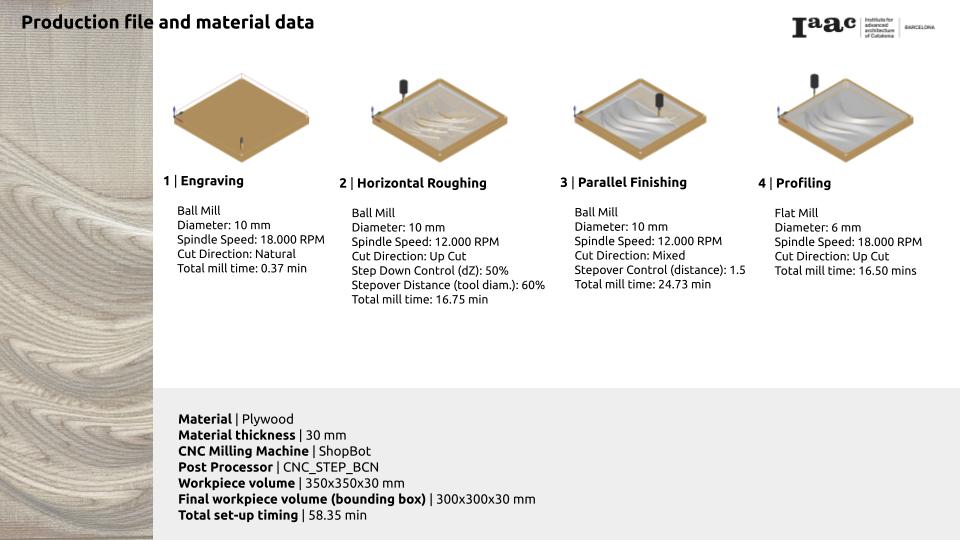
The piece was engraved on a single plywood block with a thickness of 30mm. There were 4 milling processes used to create the block, which was engraving for the frame support, horizontal roughing, parallel finishing and then profiling. The total production time was just under 1 hour.
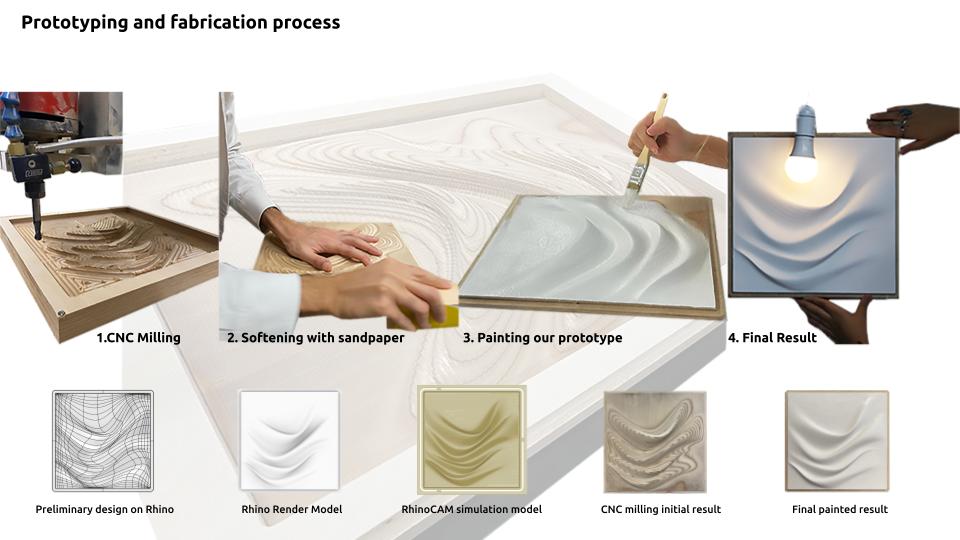
After milling, the piece was sanded progressively to heighten the curve profiling, and create a smooth surface texture which accentuated the geometry. After varnishing, we painted the piece with white paint, which leads to the final result. The hybrid manufacturing process led to a very interesting result of machine efficiency and human warmth.
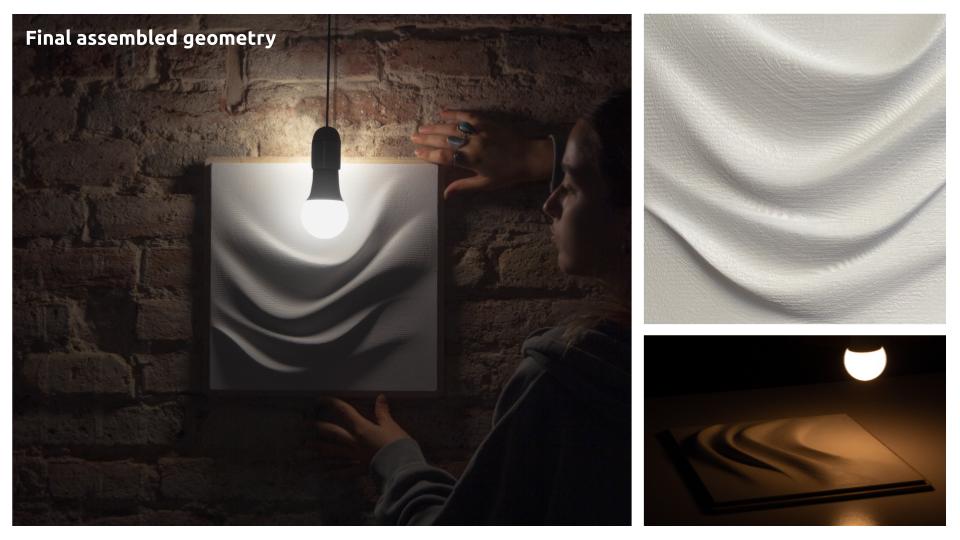
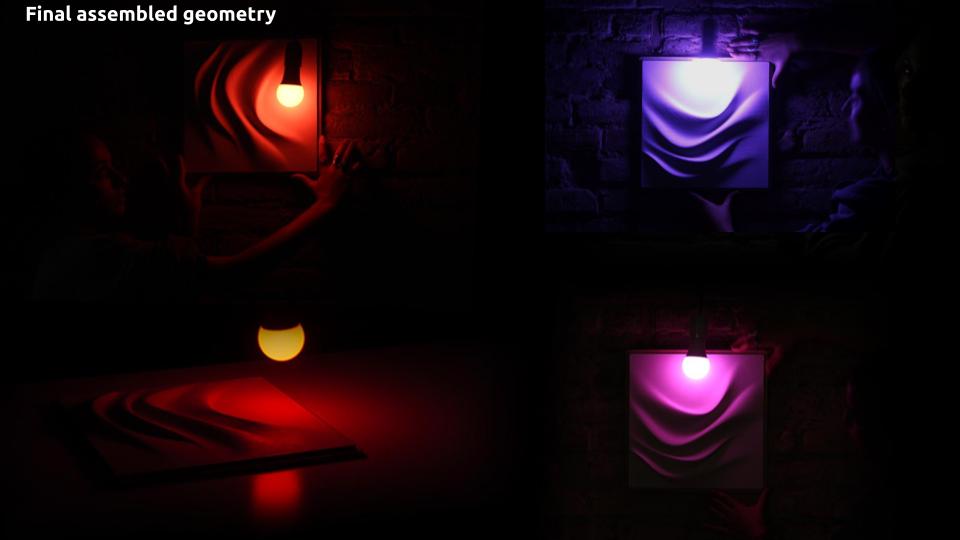
We experimented with many lighting combinations, using direction, distance and saturation to reshape the object in various ways. The piece has a very interesting quality of being dynamic without any light, and with light, finds its own shape and rests into something enveloping and intimate.
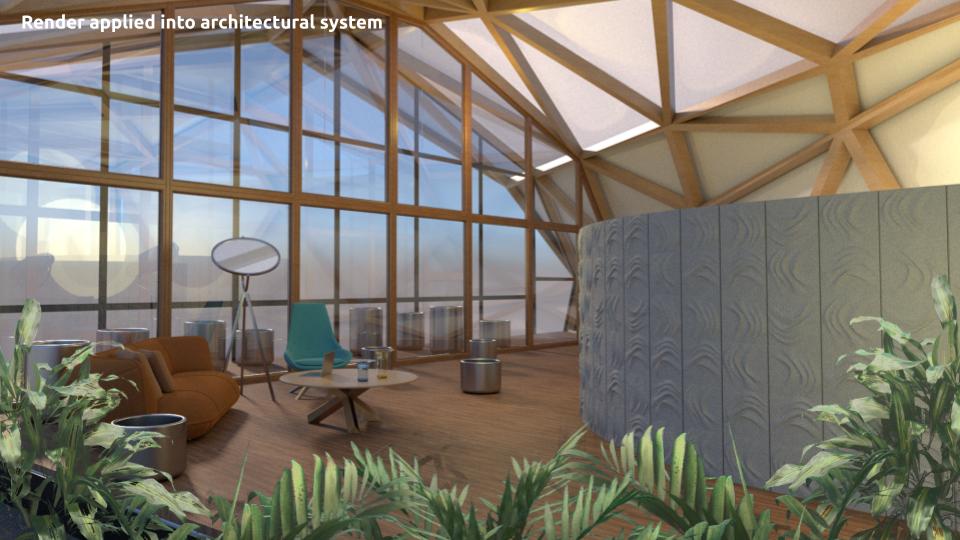
In the render, we place this module as a part of a wall, where the vertical movement of the piece creates an undulating pattern across the solid wall. The piece in repetition, visually drives you around the shape and back at its origin, encouraging you to place your presence right in the space where it exists.