The Concept
GeoCabin is an exploration of three forms of digital fabrication: CNC Milling, Laser Cutting and 3D Printing. It features a continuous, blob-like geometry inspired by the lime-green blobs found in the Andes. The geometry was created through parametric algorithms, blending curves and voids. The design process evolves from a base geometry to a mesh pattern, culminating in a perforated, latticed shell. Its network of triangles reflects structural optimization principles, while the perforated surface enhances aesthetics, light, and ventilation. Utilizing these fabrication strategies, we designed a terrain form, a facade system and an inner structure to hold the cabin up. The design merges form and function.
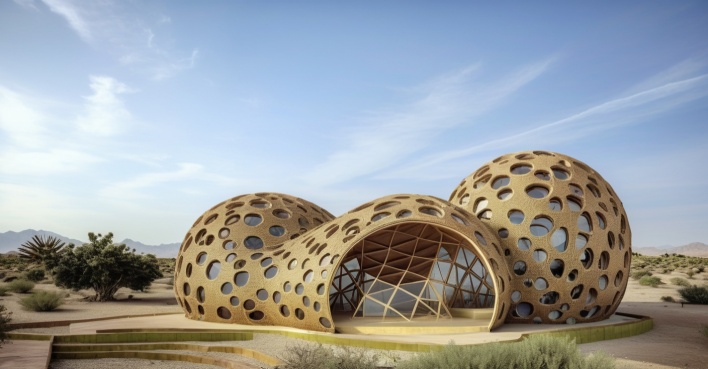
Sketching & Designing
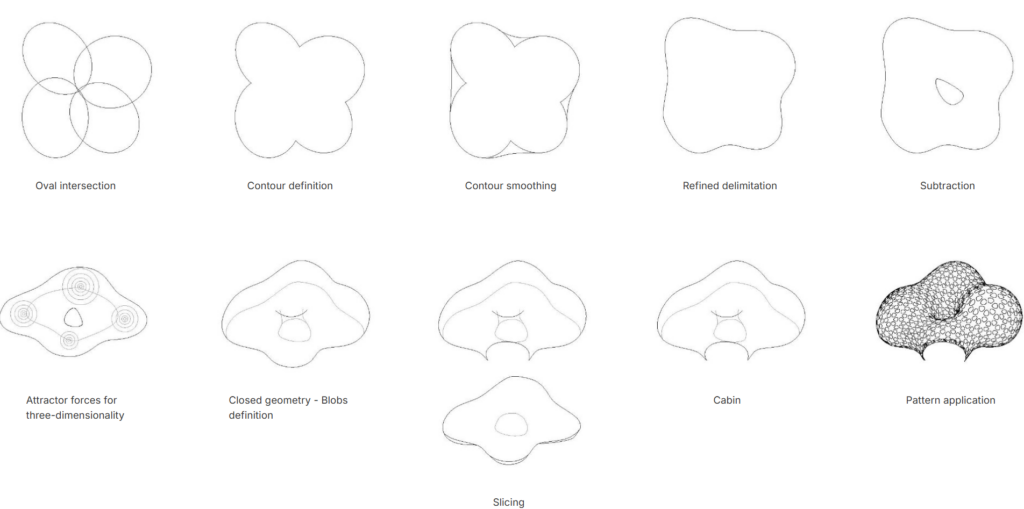
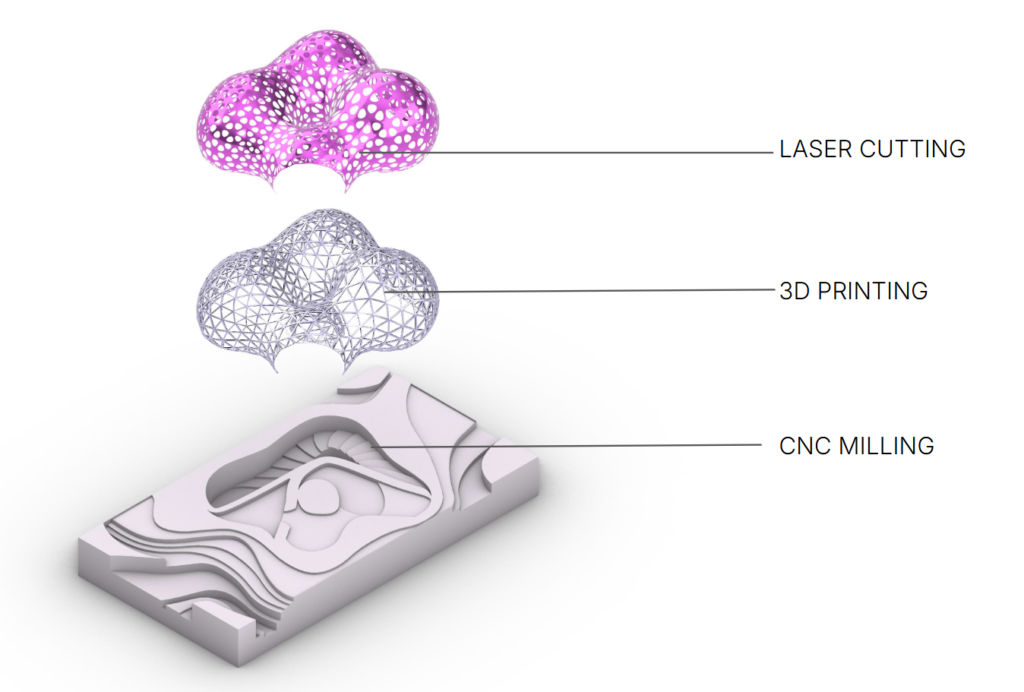
CNC Milling
We designed the terrain for our cabin by following the natural contours of the cabin’s overall geometry, creating organic along the cabin’s exterior path. In order to achieve such depth, our team chose to mill a block of foam which was dimensioned at 240mm x 450 mm x 50 mm.
Fabrication Strategy
- Post Processor: CNC_Step_BCN_Raptor
- Flat Mill – 6 mm
- Flute: 2
- Spindle Speed: 18000
- Cut Direction: Downcut
- Stepdown Control (dZ): 50%
- Stepover Distance: 50-60%
- Total Mill Time: 33 minutes
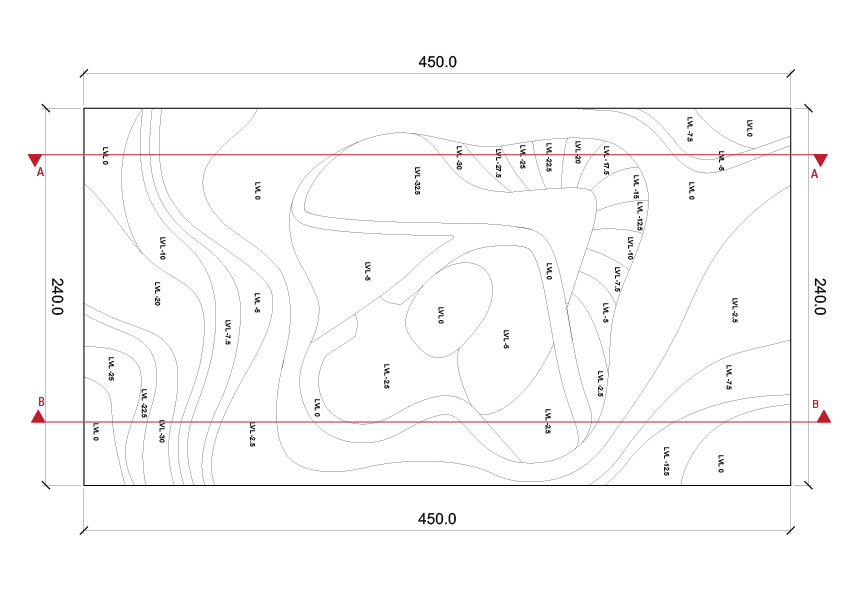
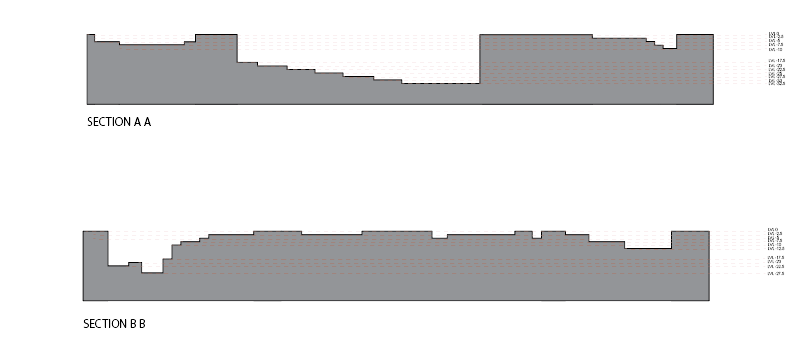
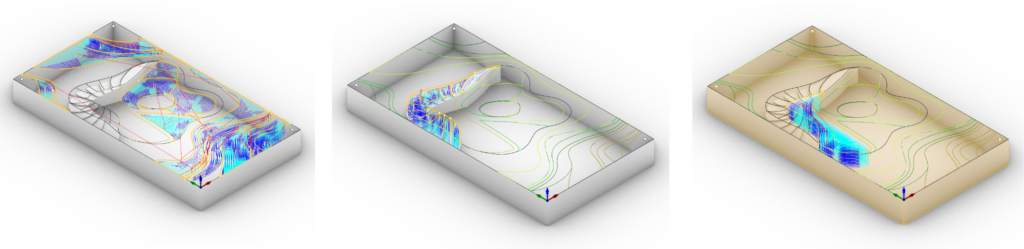
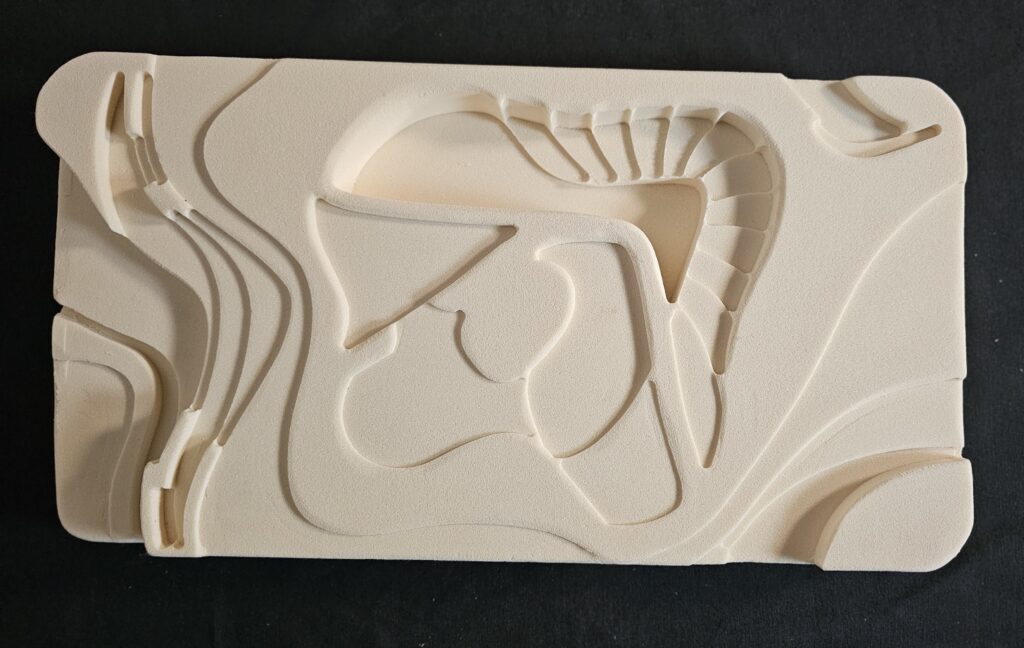
Laser Cutting
Moving to our next fabrication technology, we were tasked with using Interlocking on 4 mm Plywood.
The first step was to design a facade system that utilized the technique of interlocking. Drawing inspiration from Marc Fornes perforated pavilions and installations, we designed an interlocking system of triangles that vary in shape and size that wrap around to form a dome-like shape as the triangles stack up. Starting with setting the dome base, we then segmented the circle to start drawing triangles from each segment, altering their rotation to create a curved profile.
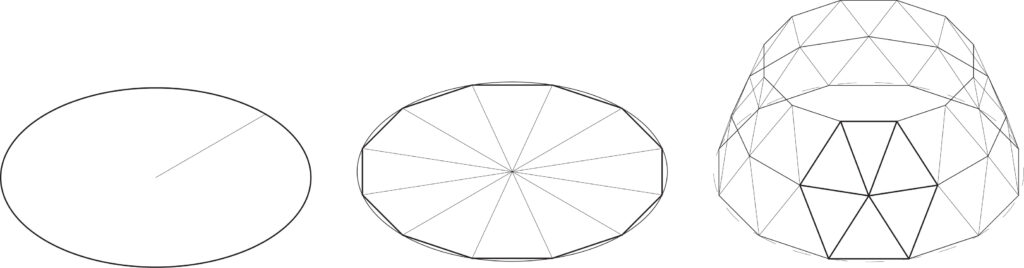
Fabrication Strategy
- Machine: Ray Jet 500
- External cut: power 42 – speed 1.80
- Internal cut: power 42 – speed 1.80
- Marking: power 15 – speed 60
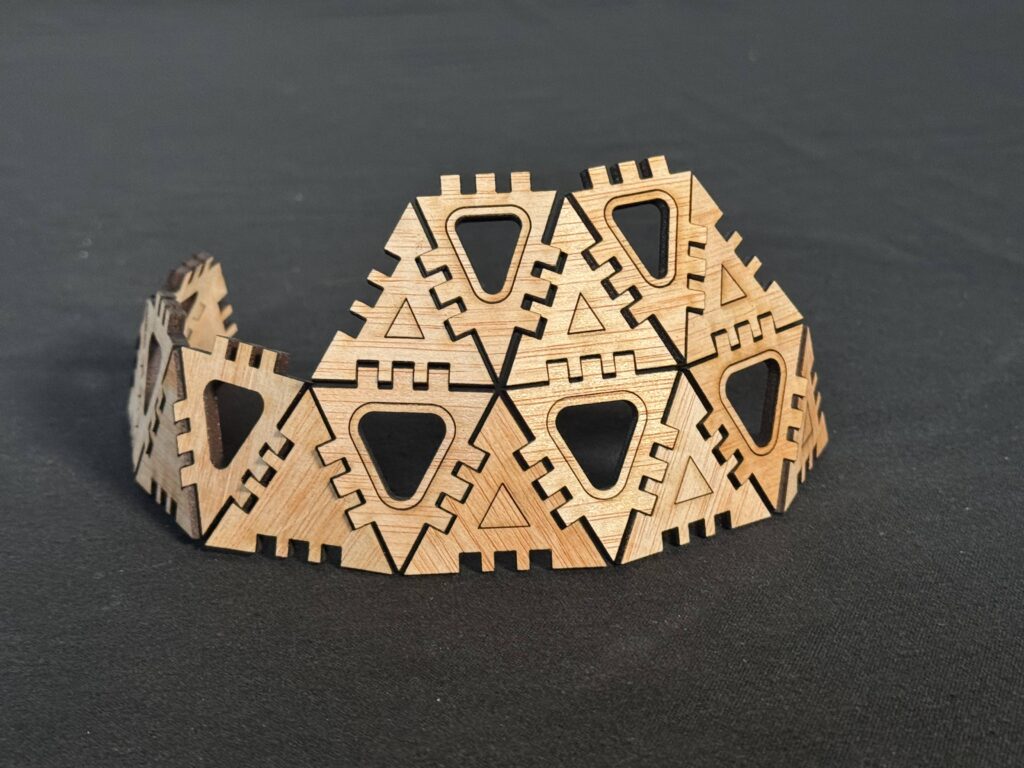
3D Printing
During our final week, we explored ways to design a structural system using a 3D printer. Following the same geometry we used to design the facade system. we generated a digital model that nestled right under the facade system.
After testing the prototype at 50% of its final scale as well as a portion of the final prototype, we ultimately decided that to optimize printing time we would not use supports during printing. The final prototype showed minimal imperfections and was sturdy.
Fabrication Strategy
- Infill Density: 20%
- Infill Pattern: Grid
- Shell Thickness: 6 mm x 6 mm
- No Supports
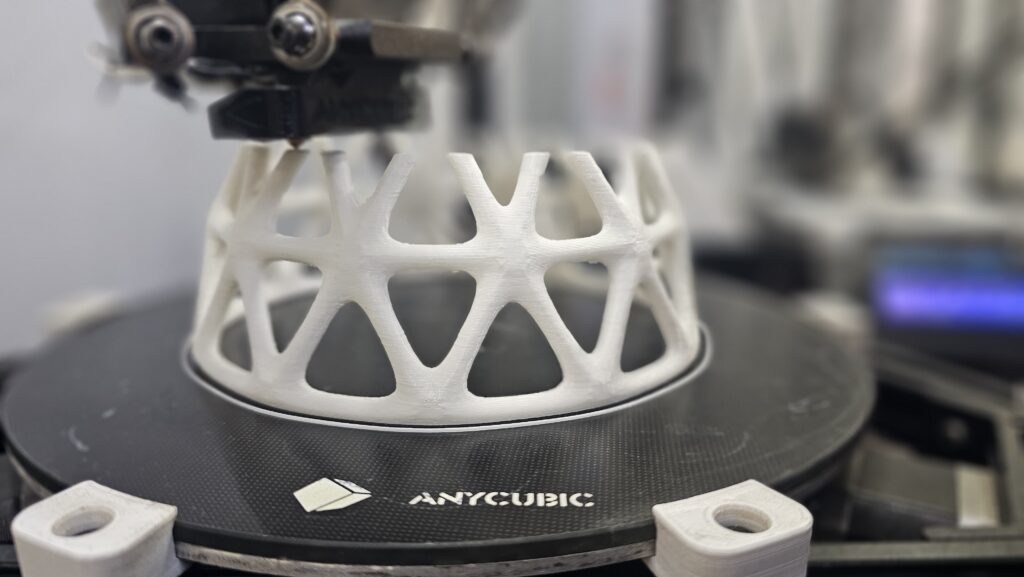
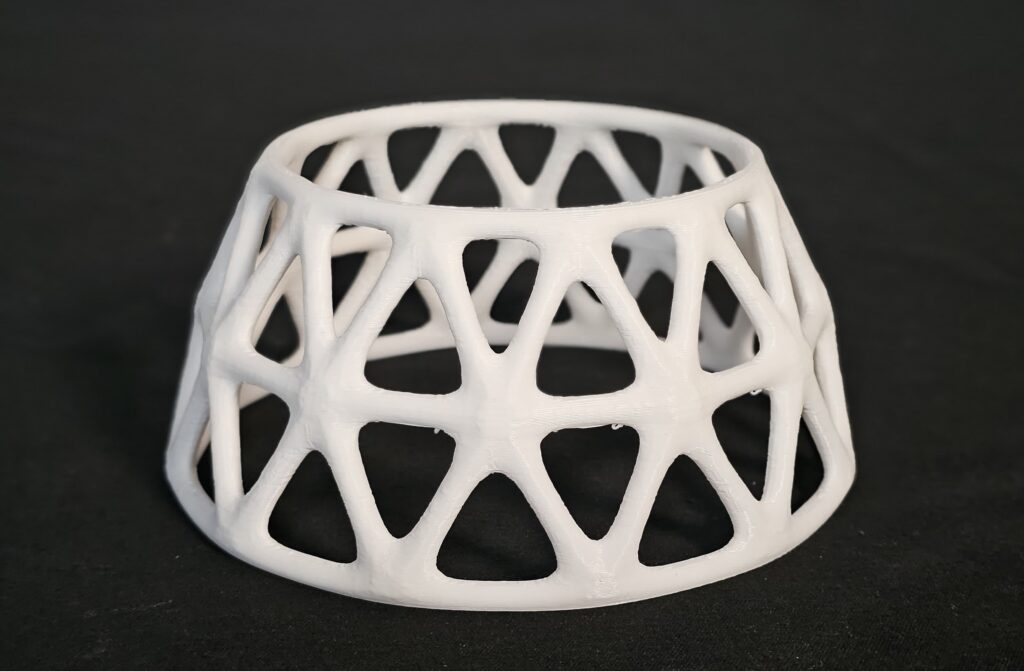
Exploring the structure at a larger scale, we also printed a node derived from our structure’s geometry. This piece was created at a larger scale to fit 8 mm diameter wooden rods and starts mimicking what this joinery system would look like at an architectural scale.
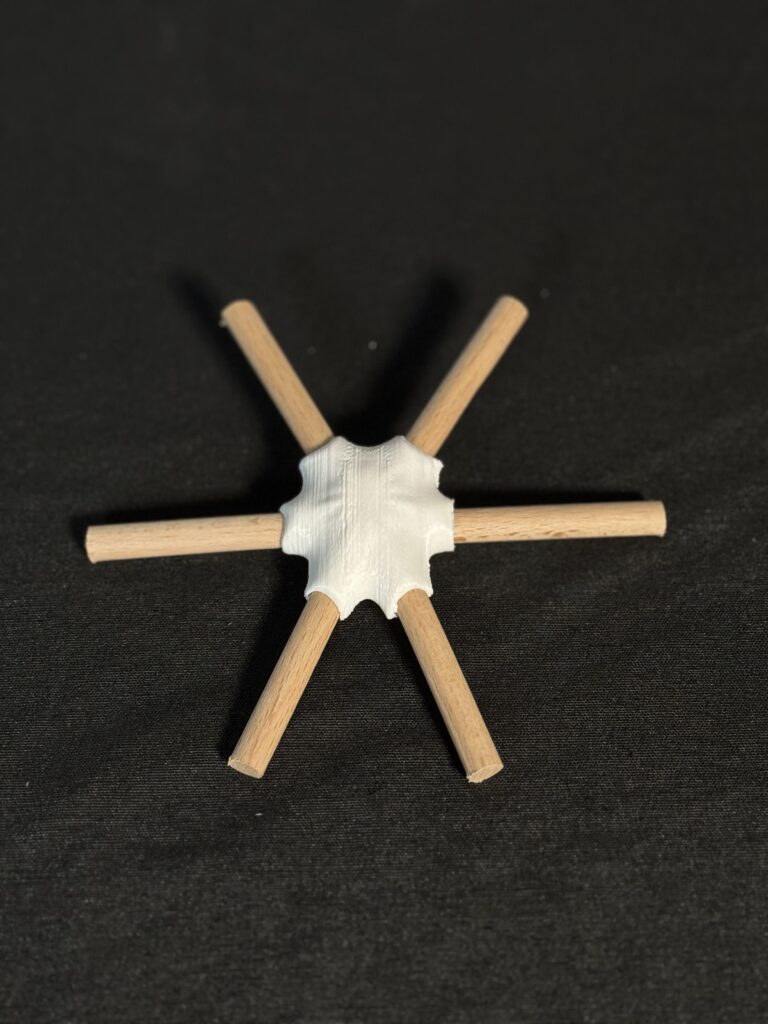
GeoCabin Final Prototype
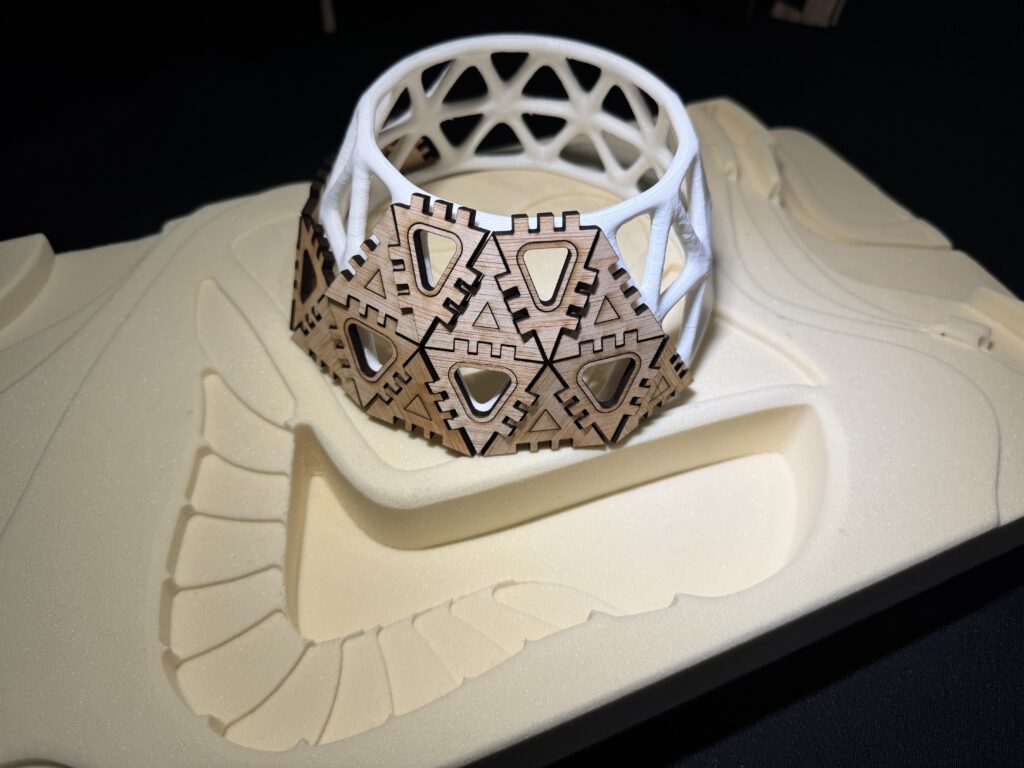
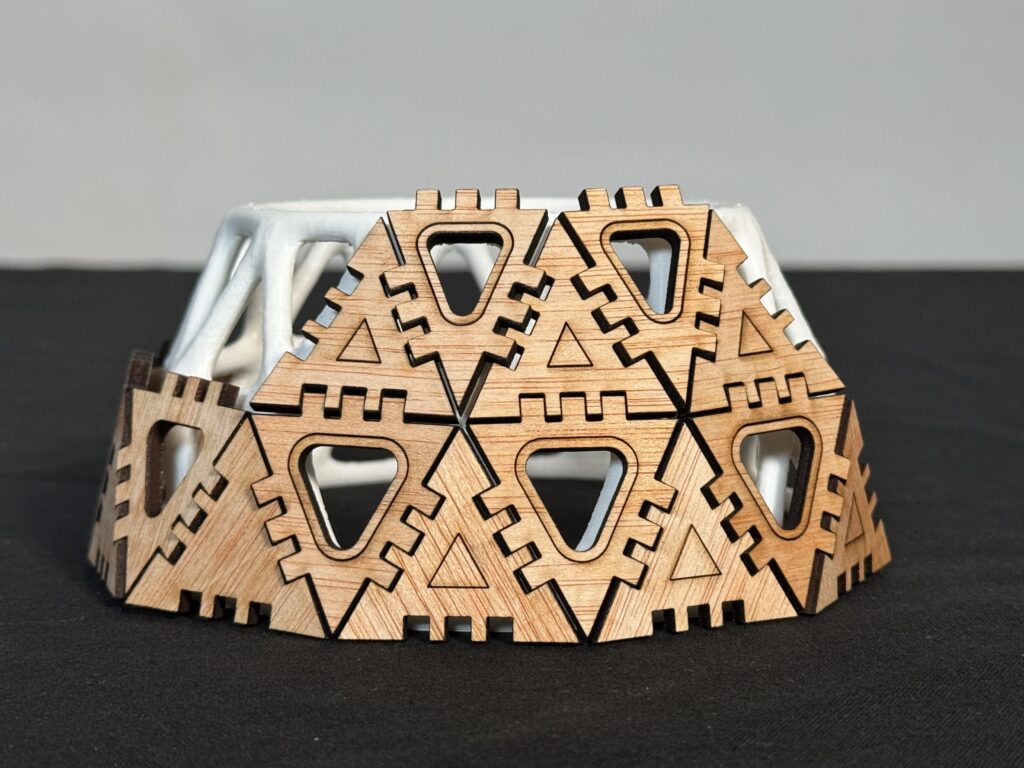
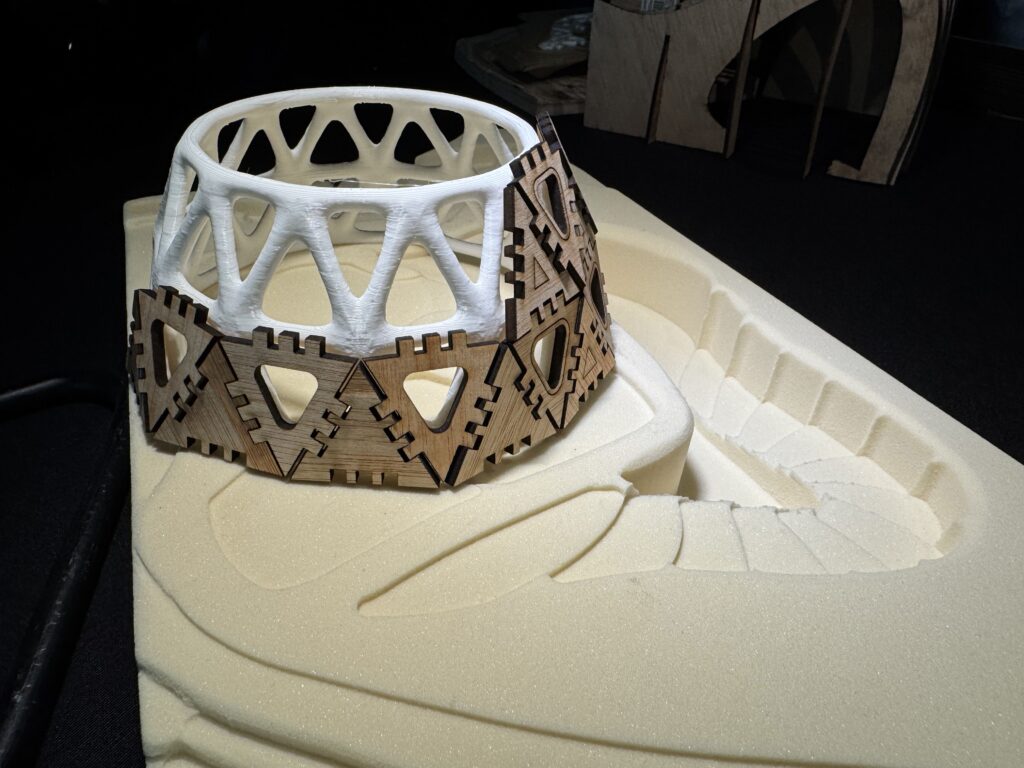
GeoCabin is a project of IAAC, Institute for Advanced Architecture of Catalonia developed at Masters in Advanced Architecture 2024-2025 by students: Queenie Fan, Pamela Sanchez and Nihal
Faculty: Shyam Zonca | Ricardo Mayor | Valentino Tagliaboschi