During the 3-week course of the Digital Fabrication course, we tested and investigated the opportunities and limitations that the latest fabrication methodologies provide in terms of design and fabrication. In this regard, we tested different materials and machines using CNC Milling, Laser Cutting and 3D Printing strategies.
CNC Milling
For the CNC Milling testing and fabrication, we chose the Hydraulic Floor tiles as a design pattern to be carved out on an MDF board.
The process included engraving, horizontal roughing, parallel finishing and profiling as the main techniques for the fabrication process. Using a Flat mill of 10mm diameter, the entire process took around 1 hour and 10 mins to create the final piece.
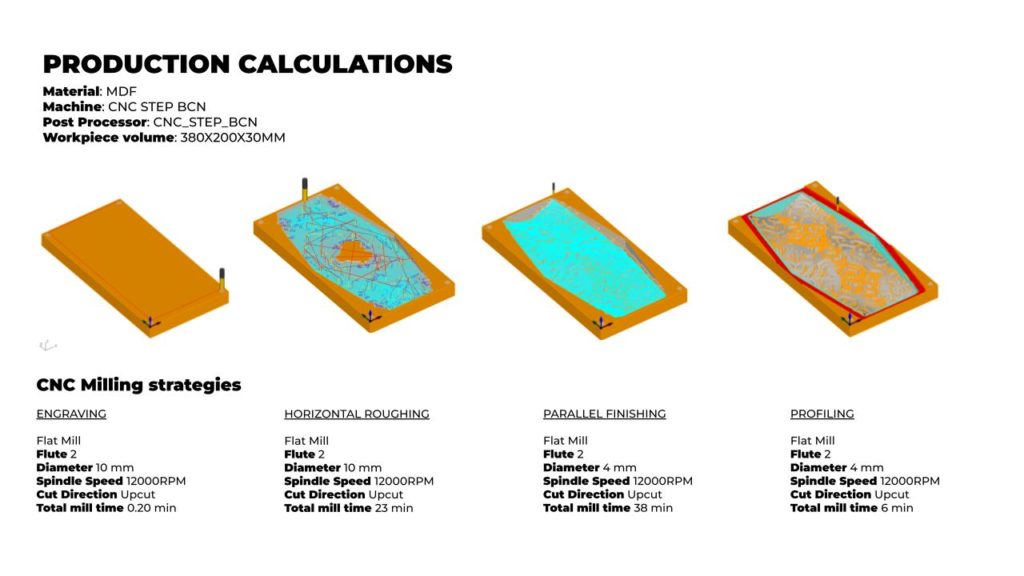
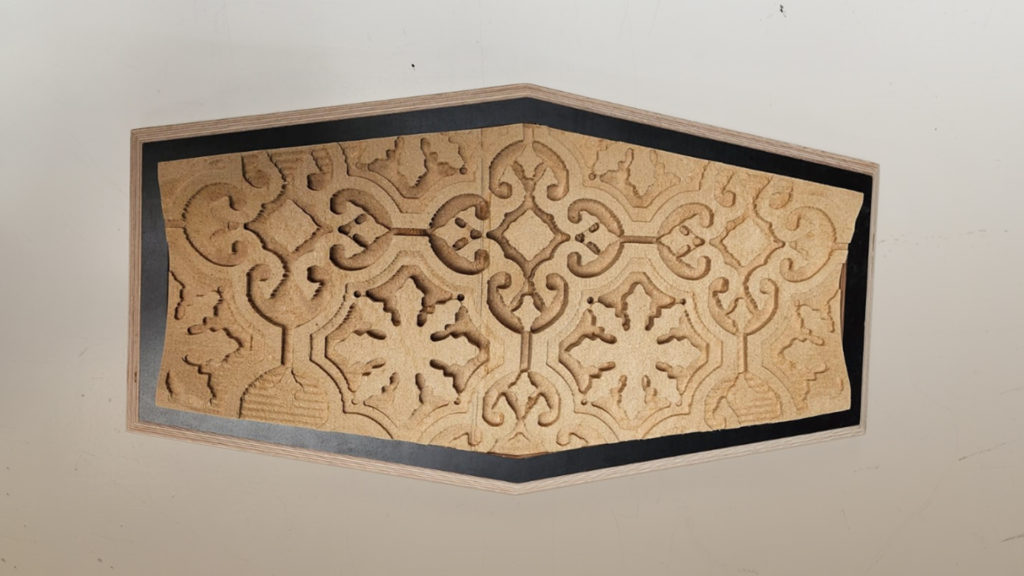
Laser Cutting
For the laser cutting fabrication exercise, we tested and experimented with different set of joineries using a number of different materials. Using an interlocking and bending technique, we designed a joinery system based on the concept of box joints. In order to achieve the bending with kerfs, we experimented with different materials including Acrylic, Plywood and MDF. However, MDF proved to be the most flexible and durable with the kerf bending technique and hence was used in our final design.
For the final design, using curved modules, bended and interlocked at their joints, we proposed each module as a part of the systematic whole, connected by Timber which are 35mm thick.
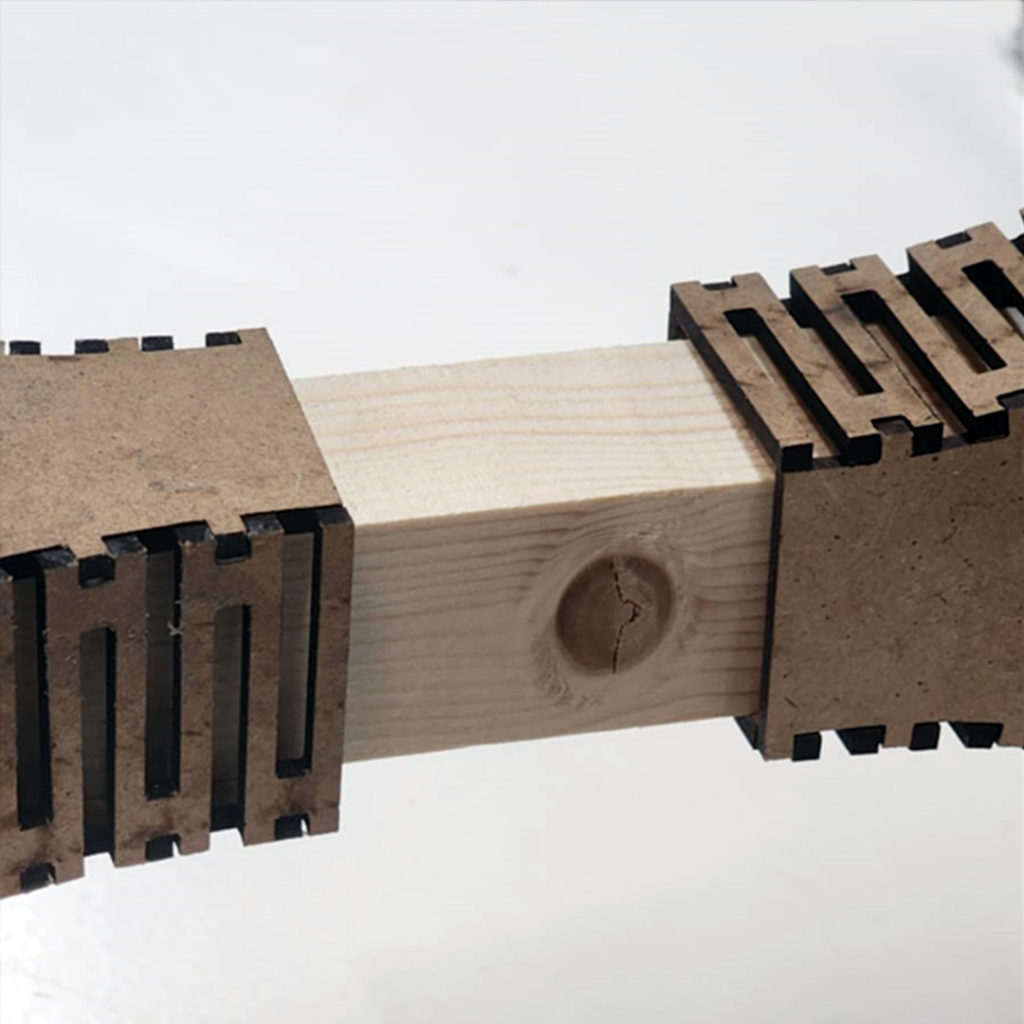
The final designed proposed a spatial system that transforms and expands according to purpose and can be used as a joinery system for multiple design components.
3D Printing
For the 3D Printing Fabrication exercise, we used to Zortrax M200 for testing and prototyping our design. The design was based on certain parameters and limitations of the printer, most importantly, the time limitation.
We proposed a 1:1 scale shading device that is modular and can be applied and fitted onto South-West facades to tackle direct heat and sunlight while keeping optimum visibility. The final prototype took around 7 hours to print along with the raft. The print was conceived and printed vertically in order to save time and remove excess supports.
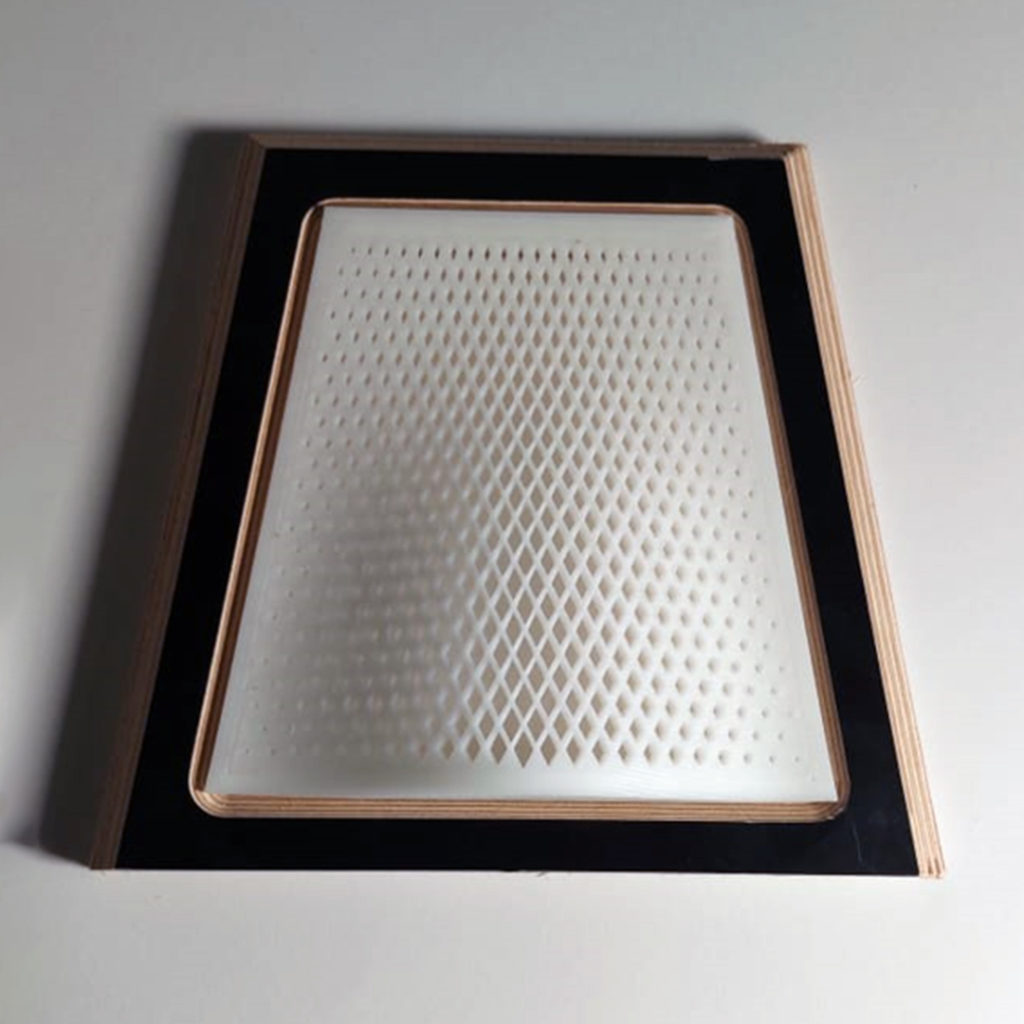
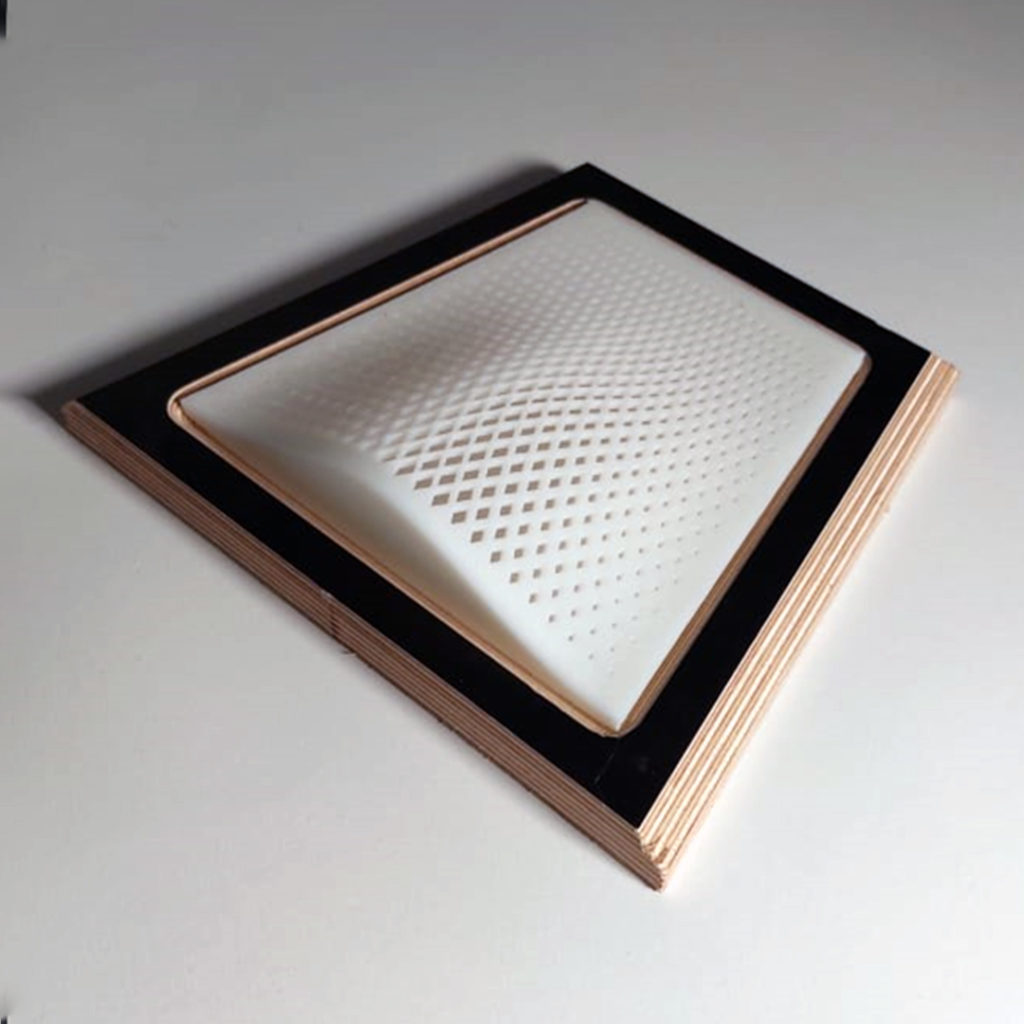