The analyzed material of our team in this class is clay, which is a fine/grained sediment primarily composed of small particles of minerals that are formed when rocks are exposed to different elements such as rain, wind and temperature changes. It can be considered as a natural material which is taken from the Earth, however it is important to understand how it is processed to know the environmental impacts it has regarding pollution and climate change.
Clay is used in construction mainly to create bricks which are made up from a mixture of clay, water and some other additives, which is then formed into a desired shape and fired at high temperatures to create a strong building material. These bricks are managed in basically 8 steps which refer to the Business As Usual (BAU): preparation of raw materials, transport to site, construction and installation, use of the brick, end-of-life transportation, end-of-life processing, end-of-life disposal and loads beyond system boundary (reuse, recycle). Figure 1 shows the phases of the material and the Global Warming Potential (GWP) which describes the relative greenhouse gas taking account of how long it remains active in the atmosphere and is calculated according to the Bre Statement of Verification.
Figure 1. BAU clay phases and GWP
The story of our material starts from our studio project’s aim which is to use the clay material in order to create components using additive manufacturing and post-processing techniques for customizable surfaces. Then, the story continues to see if the material can contribute to the sustainability of the project calculating the CO2 production. For this, we calculated the emissions of the BAU from steps A1-A3 mentioned above according to the EPD from clay tiles, which result a base of 250kg*CO2eq / T. With that taken into account, we added the emissions from the additive manufacturing process: 50kg*CO2eq / T. After this step, we take the decision of firing or not-firing the bricks: if we don’t fire the bricks, the final amount of CO2 emissions would be of 75kg*CO2eq / T; if we do fire the bricks, the final amount of CO2 emissions would be of 275kg*CO2eq / T. You can visualize the emissions diagram shown below.
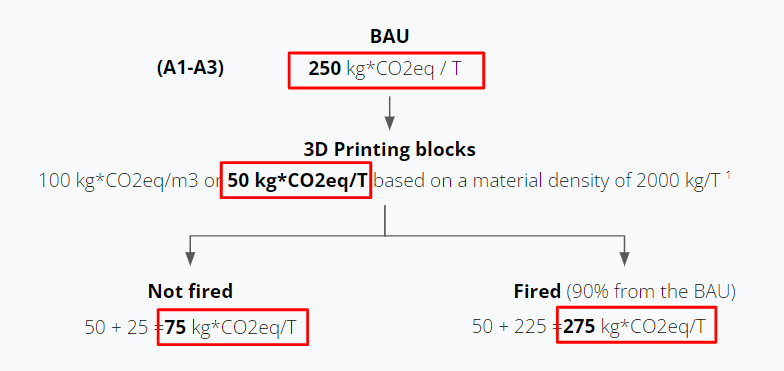
Figure 2. CO2 analysis BAU+AM (fired and non fired)
It is important to mention that the amount of CO2 produced during the production of a brick can vary depending on several factors, such as the type of fuel used in the kiln, the efficiency of the kiln, and the production process itself. On average, it is estimated that the production of one standard-sized fired brick (230 x 110 x 75 mm) can emit around 0.7-1.3 kg of CO2. This estimation takes into account the entire production process, including mining of raw materials, transportation, and firing.
As we can see on the above diagram, the majority of CO2 emissions during brick production come from the firing process, as it requires a high temperature and large amounts of fuel to heat the kiln. Nowadays, natural gas or biomass are used seeking a more sustainable alternative, reducing the carbon footprint of brick production.
Coming to the next step of the story, we note the importance of reducing the carbon footprint by different methods for example reducing waste, reusing bricks or using them as additives for future material generations. Bricks can be cleaned and reused as-is in building projects. Also, they can be crushed on site and be re-used as an aggregate for other blockworks. (1 ton of crushed clay brick results in a (net) production of 950kg of recycled aggregates with 50kg to landfill from crushing). Nevertheless, they can also be used in agricultural soil and may even improve production.
We end the story with the question: in what context is this process justified? The answer for this question is responded in 4 specific topics:
- Aesthetics and complexity: Designs and materials that are culturally relevant or commercially desirable.
- Integration of stratified construction processes: If we implement better BIM solutions we could reduce time and increase quality of results.
- Improved process: Either sustainable firing or no firing requirements.
- Analogue material when learning: Choosing a cheaper and less complex extrudable material for teaching.
In conclusion, clay is an excellent material to work with due to its versatility and accessibility. However, it is important to note that clay, like any other material, can have harmful effects on the environment if not properly managed. Therefore, while it is a great material to work with, it is important to know different waste and disposal methods to minimize their impact on the environment.
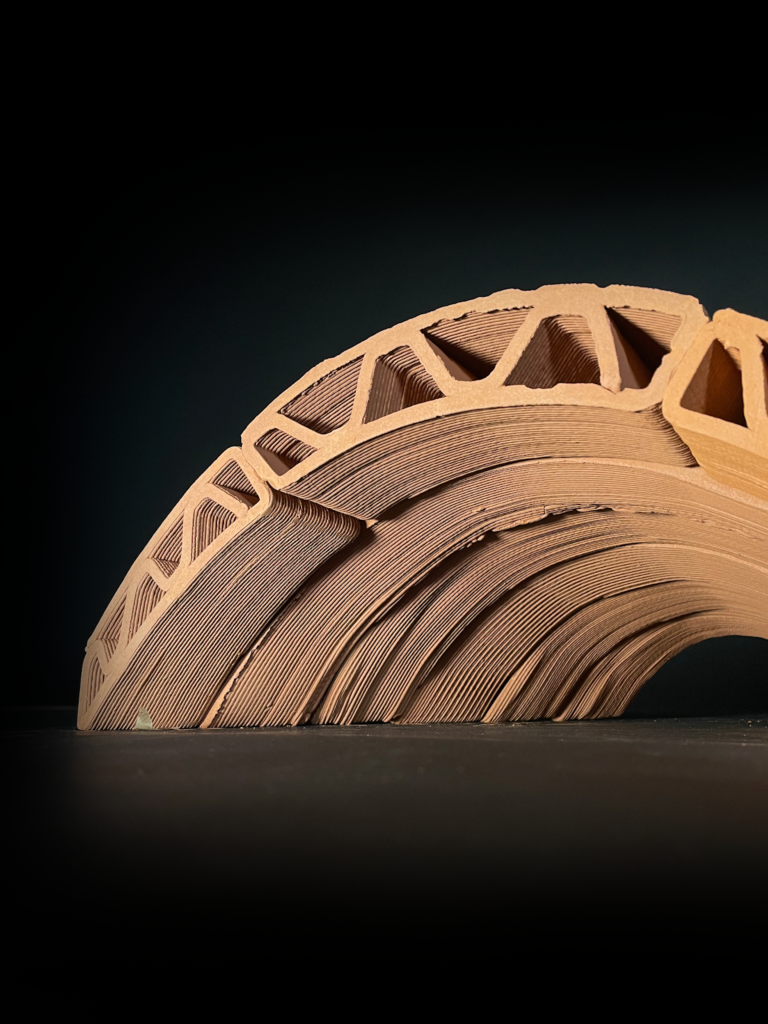
Figure 3. Clay bricks used for studio project
References:
Dos Reis, G. S., Cazacliu, B. G., Cothenet, A., Poullain, P., Wilhelm, M., Hoffmann Sampaio, C., Lima, E. C., Ambrós, W. M., & Torrenti, J.-M. (2022, July 1). Fabrication, microstructure, and properties of fired clay bricks using construction and demolition waste sludge as the main additive. Journal of cleaner production. Retrieved February 15, 2023, from https://upcommons.upc.edu/handle/2117/184329
BRE Environmental Product Declaration. (2017). Retrieved February 1, 2023, from https://www.wienerberger.co.uk/content/dam/wienerberger/united-kingdom/marketing/documents-magazines/sustainability/correct/UK_EPD_UK_Clay_Brick_202402.pdf
EPD U.S.–Canada Industrywide Clay Brick. (2020, October 7). The Brick Industry Assosiation. Retrieved February 1, 2023, from https://info.nsf.org/Certified/Sustain/ProdCert/EPD10447.pdf
Physical and Mechanical Properties of Fired Clay Bricks Incorporated with Cigarette Butts: Comparison between Slow and Fast Heating Rates. (2013). Applied Mechanics and Materials. Retrieved February 3, 2023, from https://core.ac.uk/download/pdf/18462947.pdf
Bauer, M., Krause, M., Heizinger, V., & Kollmann, J. (2022, June 16). Using crushed waste bricks for urban greening with contrasting grassland mixtures: no negative effects of brick-augmented substrates varying in soil type, moisture and acid pre-treatment. Urban Ecosystems; Springer Science+Business Media. https://doi.org/10.1007/s11252-022-01230-x