“Notched In” is the final project developed as part of the Collaborative Design Studio course, which aimed to produce a shelving system to be used as a vertical farm at the Máquina Climática exhibition that will take place at the Invernadero from Parque de la Ciutadella (Barcelona/Catalonia).
Shelving System For Vertical Farming
No glues, No screws
The shelving system is crafted exclusively from wooden components, employing traditional construction techniques such as notches and dowels, with no screws or glue involved. The trees used for the pieces were responsibly harvested from Collserola Park, following sustainable forestry practices that prioritize the well-being of the forest ecosystem. The Valldaura Labs team undertook the milling of the lumber, which was then transported 90km away to Boix Timber for the drying process. Following the drying phase, the pieces were returned to Valldaura Labs, where the group meticulously processed and assembled them. The comprehensive workflow encompassed tree marking, harvesting with the assistance of foresters, milling, drying, planing, notching, and the final assembly using dowels.
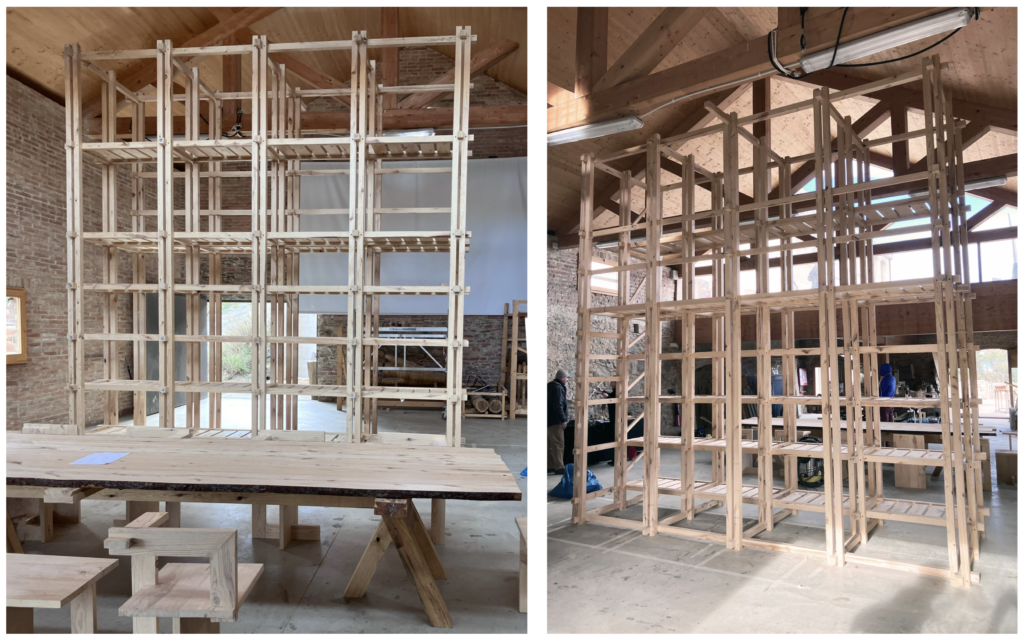
Traceability
One of the given goals of the project was to track the trajectory of the materials used. Therefore, all the harvested trees were marked due to a color coding system; their information such as geolocation, diameters, length and the part of shelving system that they would be used for. During the processing of the wood this information was transferred down to each pieces that were produced.
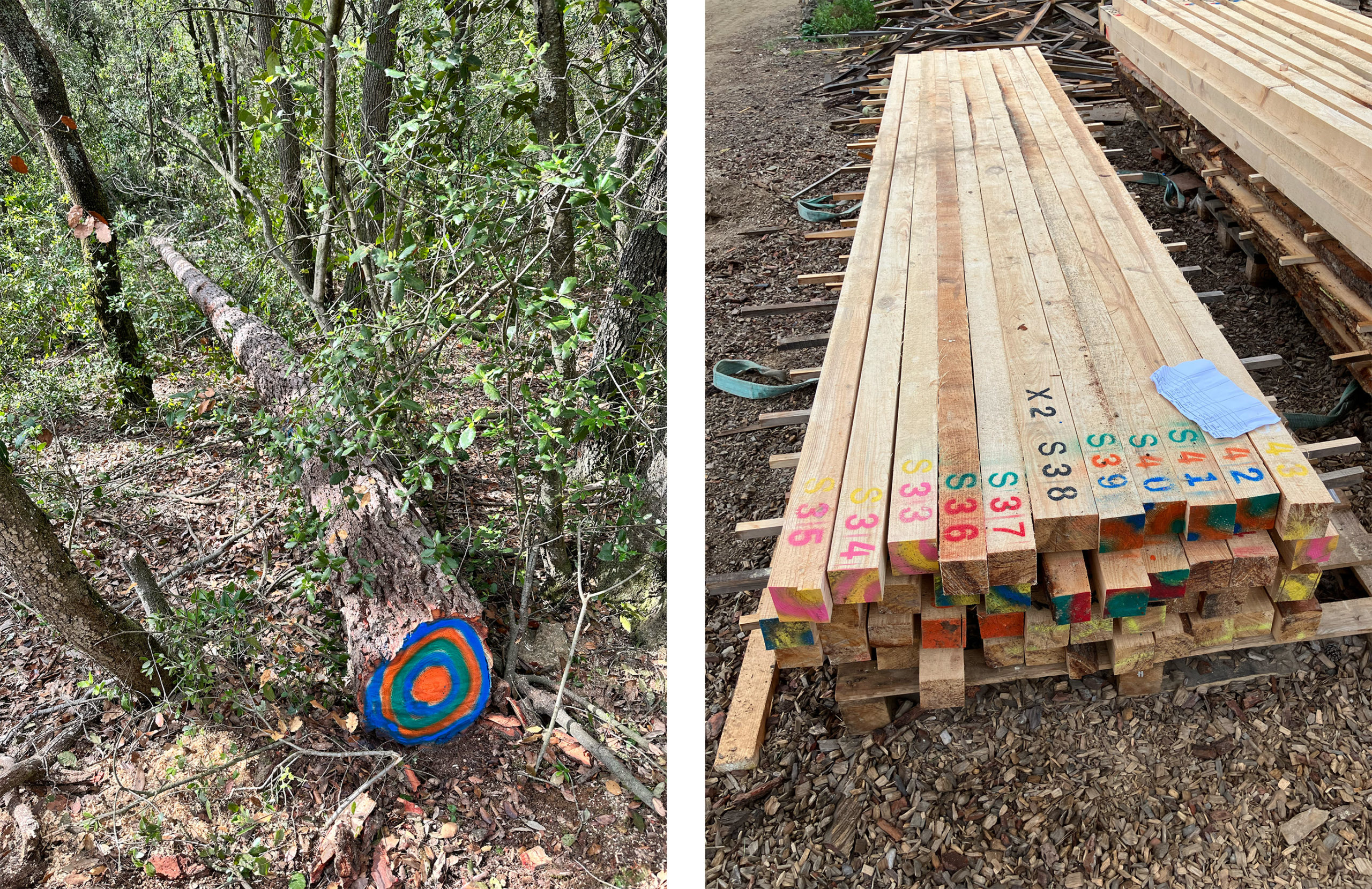
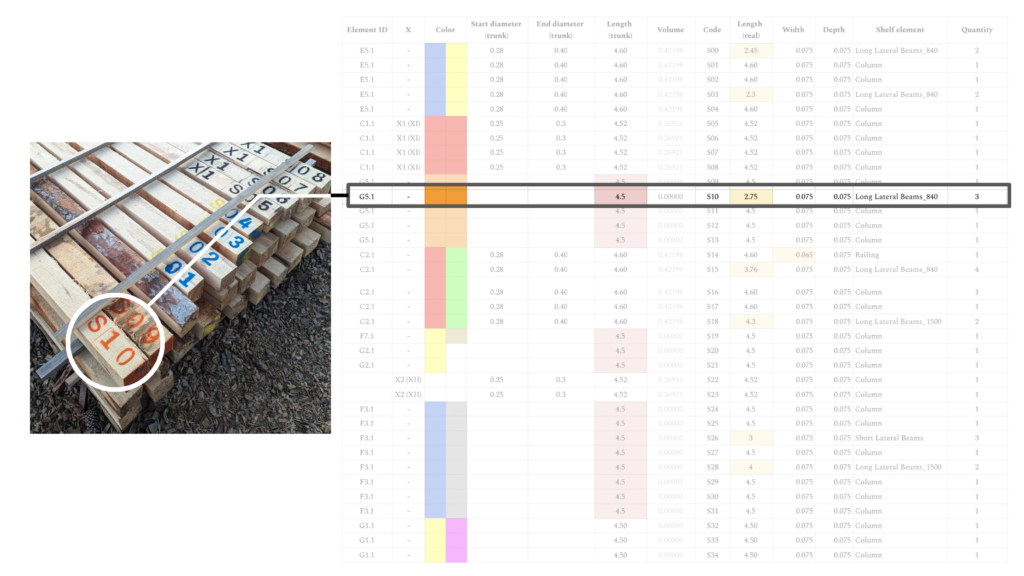
Design
The overall dimensions of the shelving system is 446x446x150 cm. The design is composed of a double-column & single beam frame structure made out of 60X60 mm structural members. Each column and beam are notched respectively avoiding the use of screws and glue. When assembled, the beams and columns lock themselves and dowels fix the elements in their place. When disassembling, all that is needed is to take the dowels out and remove the beams from the column frames. A platform was integrated to the design at the 2,5m height in order to provide access to the upper shelves. The platform constitutes a corridor within the structure that is encircled with railings to provide safety. It can be reached by authorized person when the removable two steps on the bottom are inserted back to their slots.
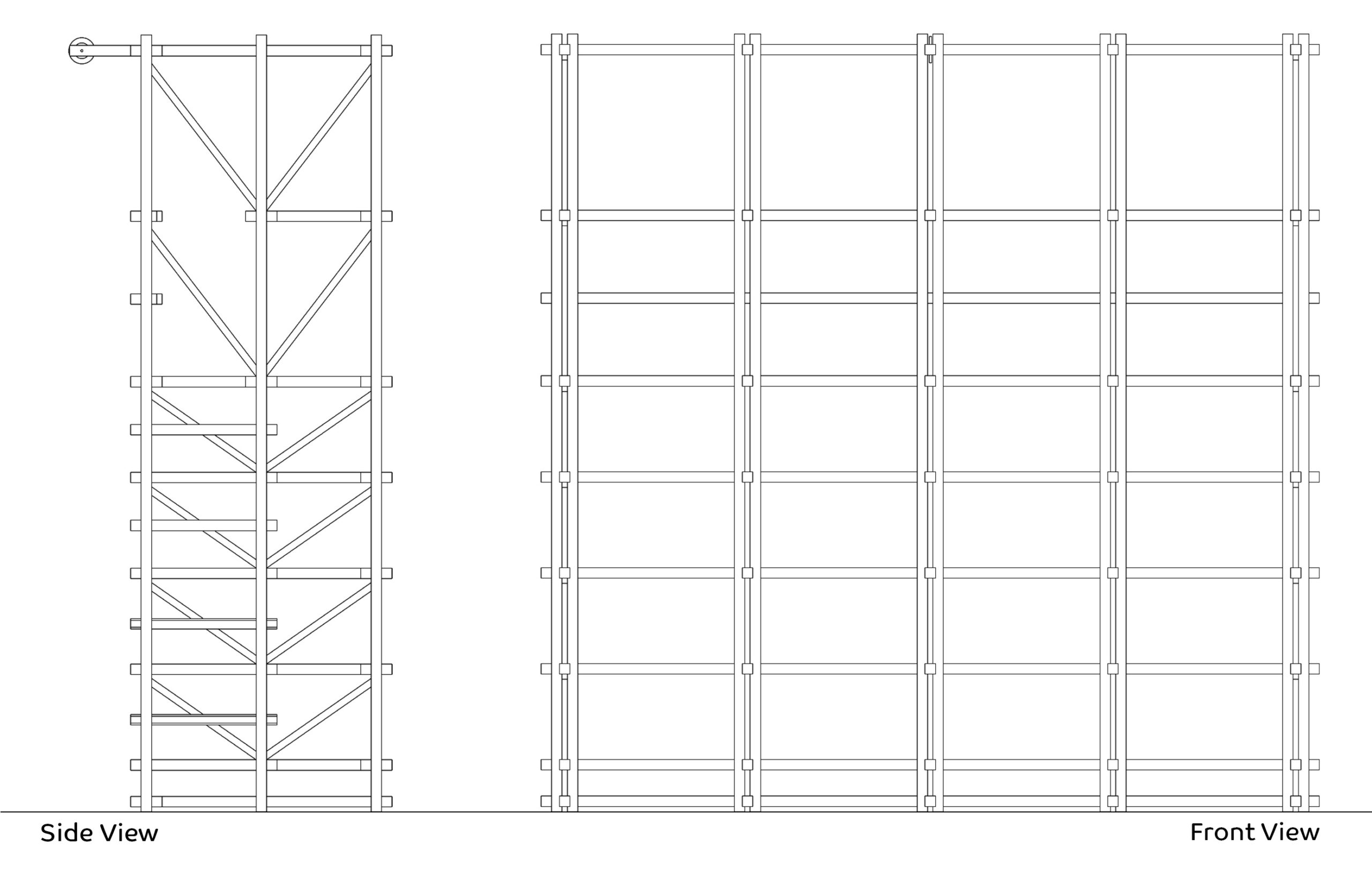
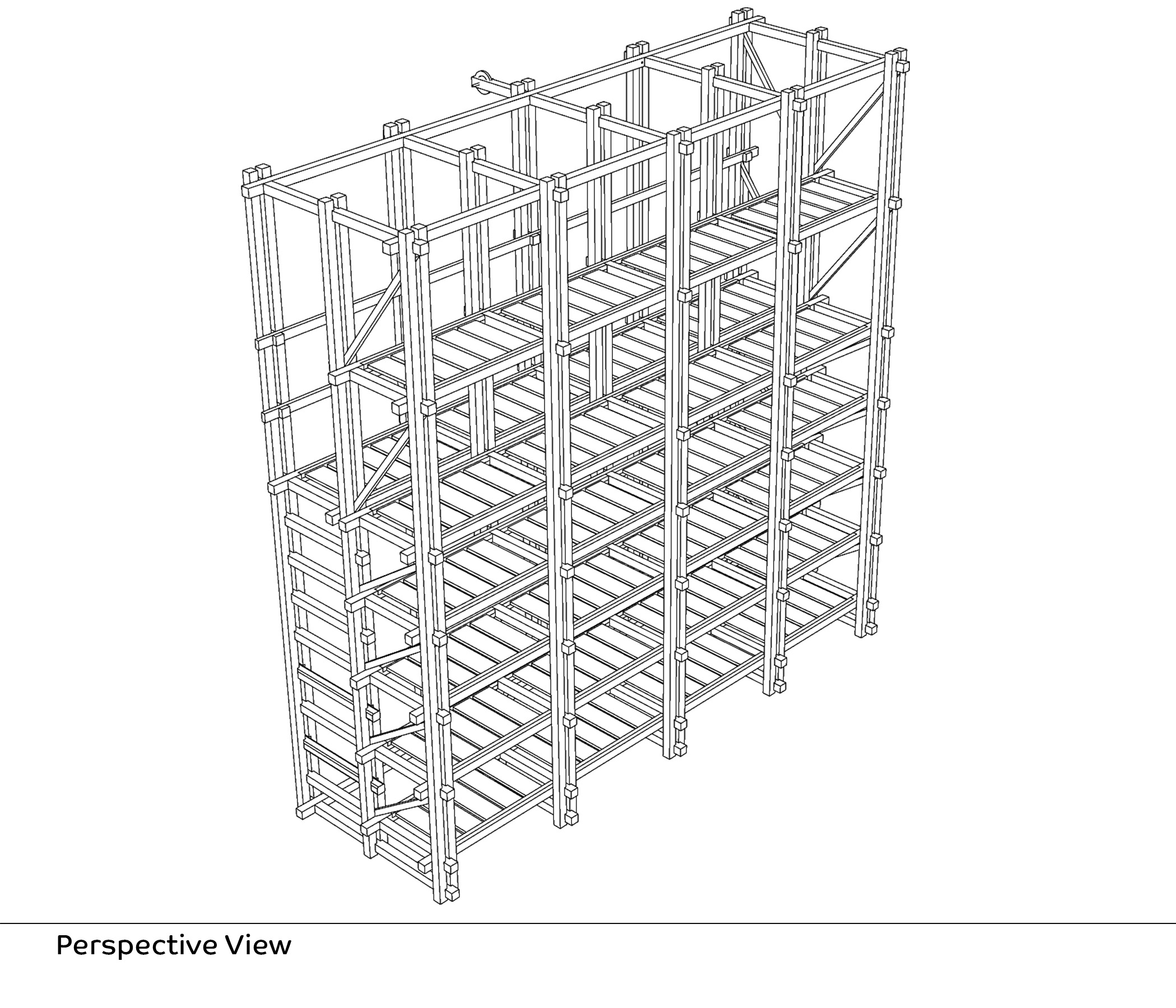
Prototyping
Before deciding the final design, prototypes were made in order to explore the connection details in real life, strenght and aesthetic. More information about this process can be found at another blog post “Prototyping “Notched In”: A journey to the final model“.
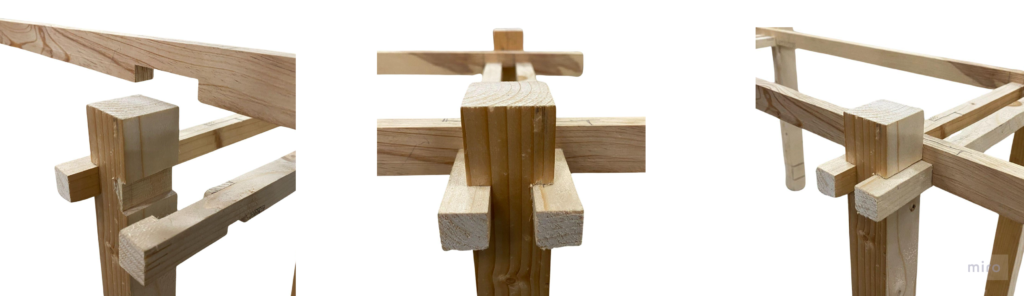
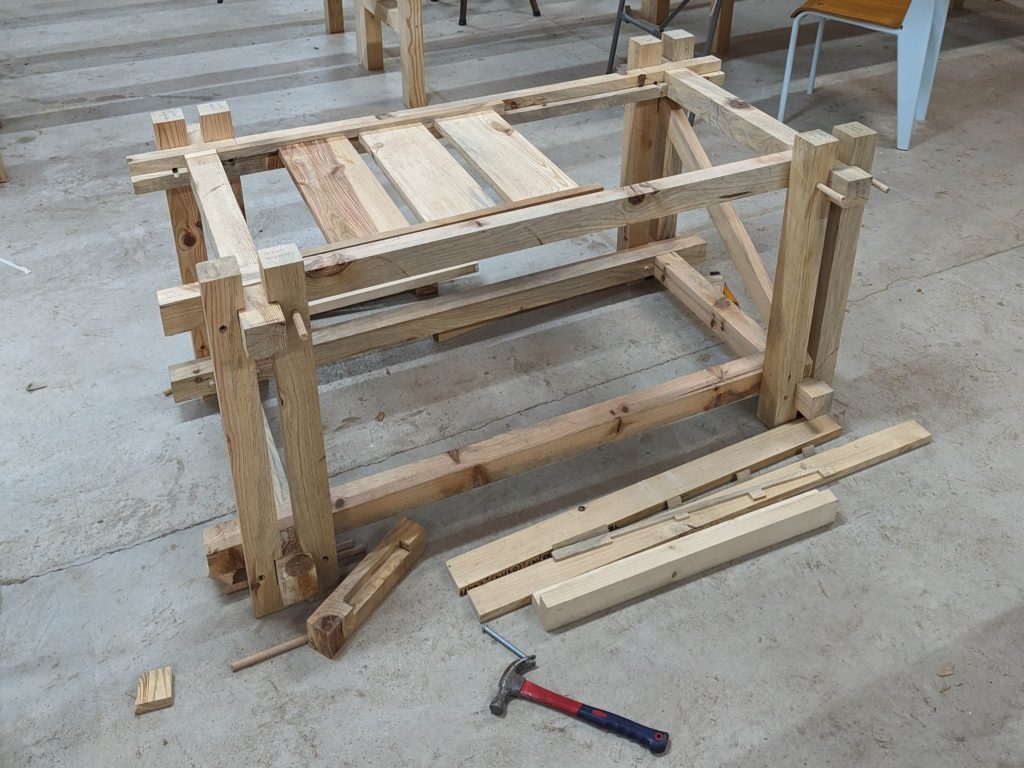
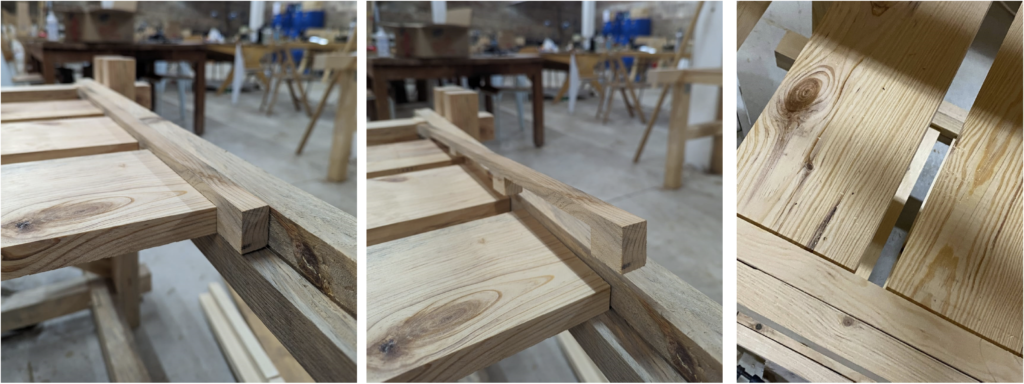
Fabrication
The fabrication process before the wood was taken to the drying kiln consisted of 4 days of miling. After the timber was brought back from the kiln, the fabrication was carried out over a period of 8 days and comprised of the following steps: Planing & thicknessing and notching & routing for the full length beams. The smaller beams, diagonals, railing supporters, slats and slat mounts were made using the table saw after planed and thicknessed.
Milling
After harvesting the trees, which were marked according to sustainable forestry principles, the foresters cut the trees into large pieces of approximately 4,5 meters in length and delivered them to the main site at Valldaura Labs. We milled the tree trunks to dimensions that could be processed in later stages for the designed dimensions, which consisted of long beams around 4500x75x75mm and 4500x250x30mm lamellas.
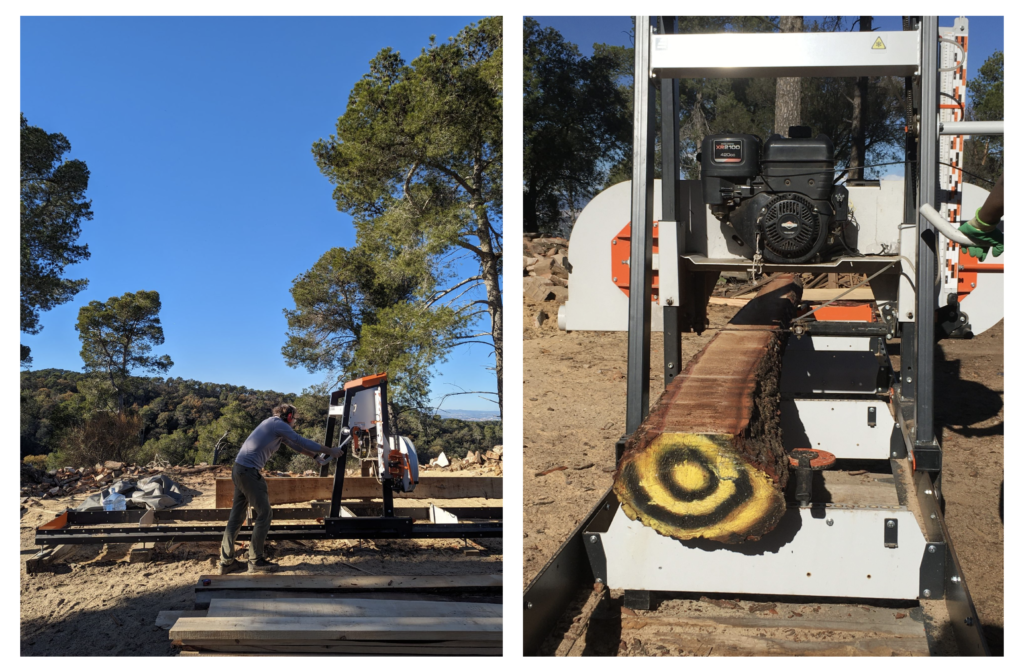
Planing & Thicknessing
After going through the milling machine, all the pieces went through the jointer and thicknesses machines in order to get its final dimensions and smooth surfaces. Because they lost the codes that were marked on the surface, it was necessary to remark them on the top or bottom.
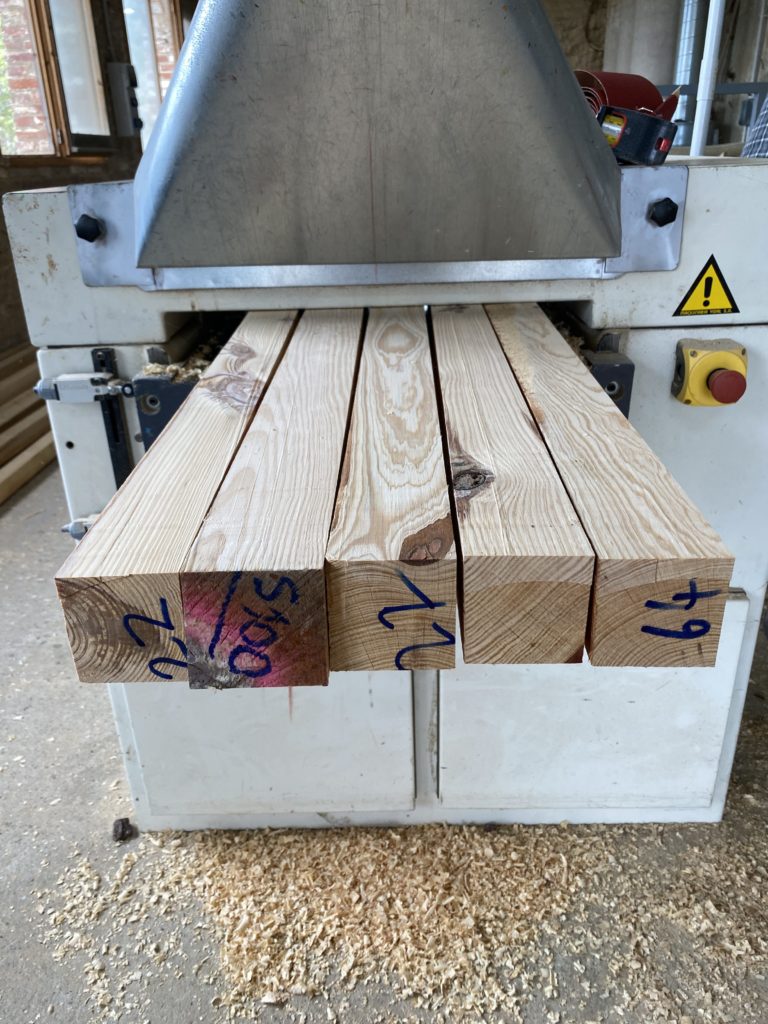
Notching & routing
After getting the final dimensions for the pieces notching process started. The pieces were laid on the wooden horses and clamped. Outer cuts were made using track saw. For cleaning cuts circular saw was used. The final finishes of the notches were made using hand router.
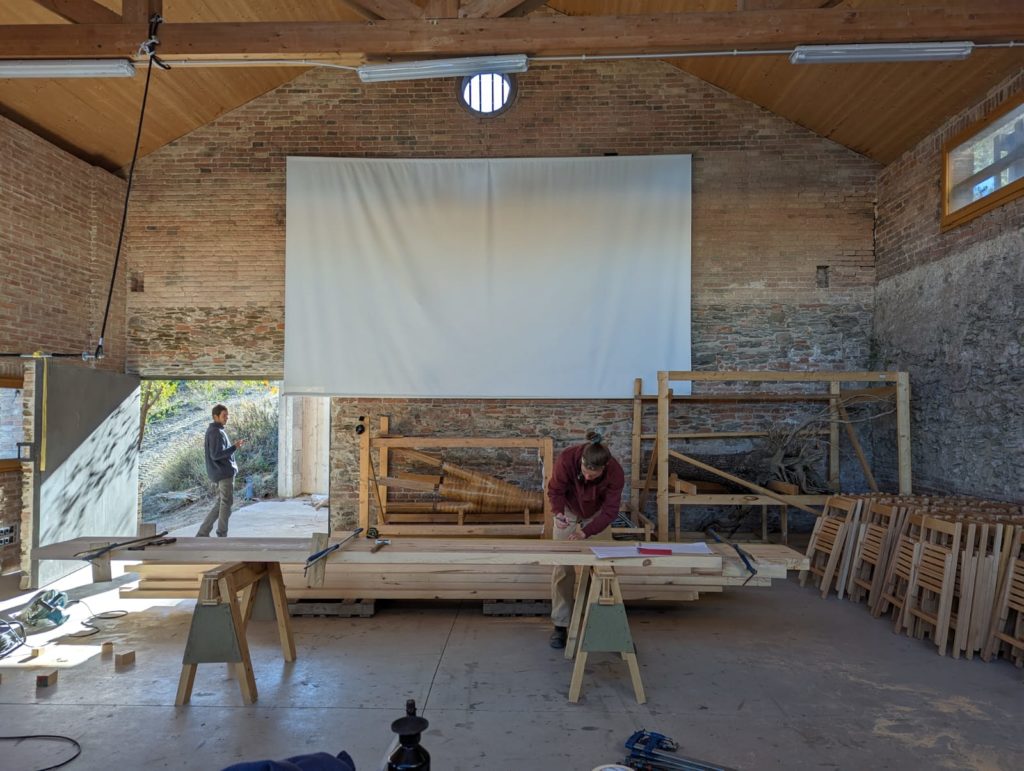
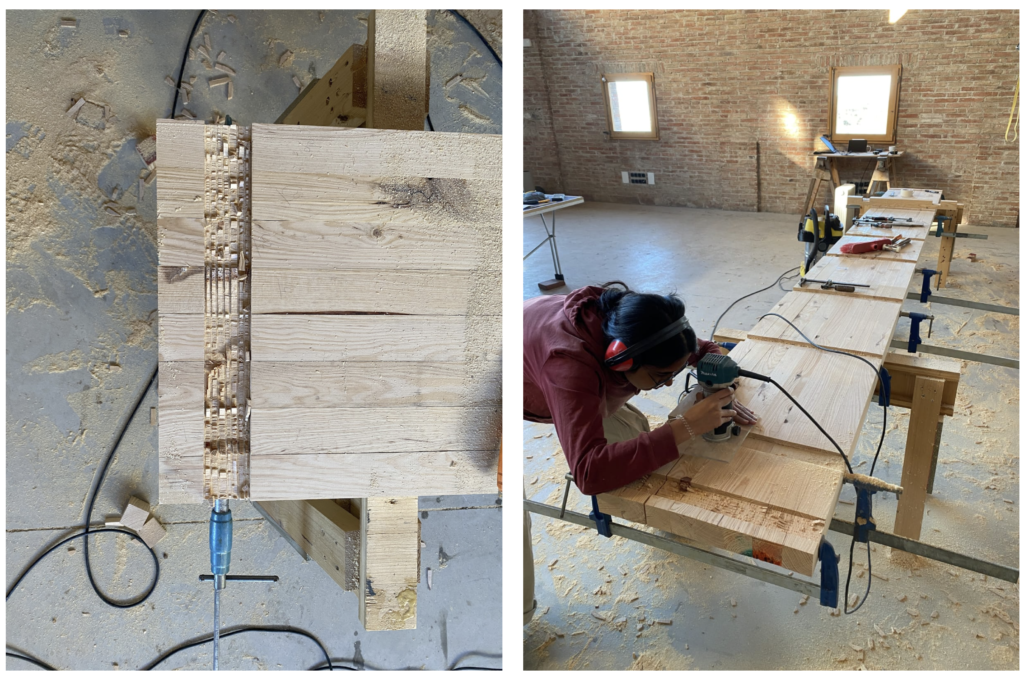
The pieces that were produced and required for the final assembly are as follows:
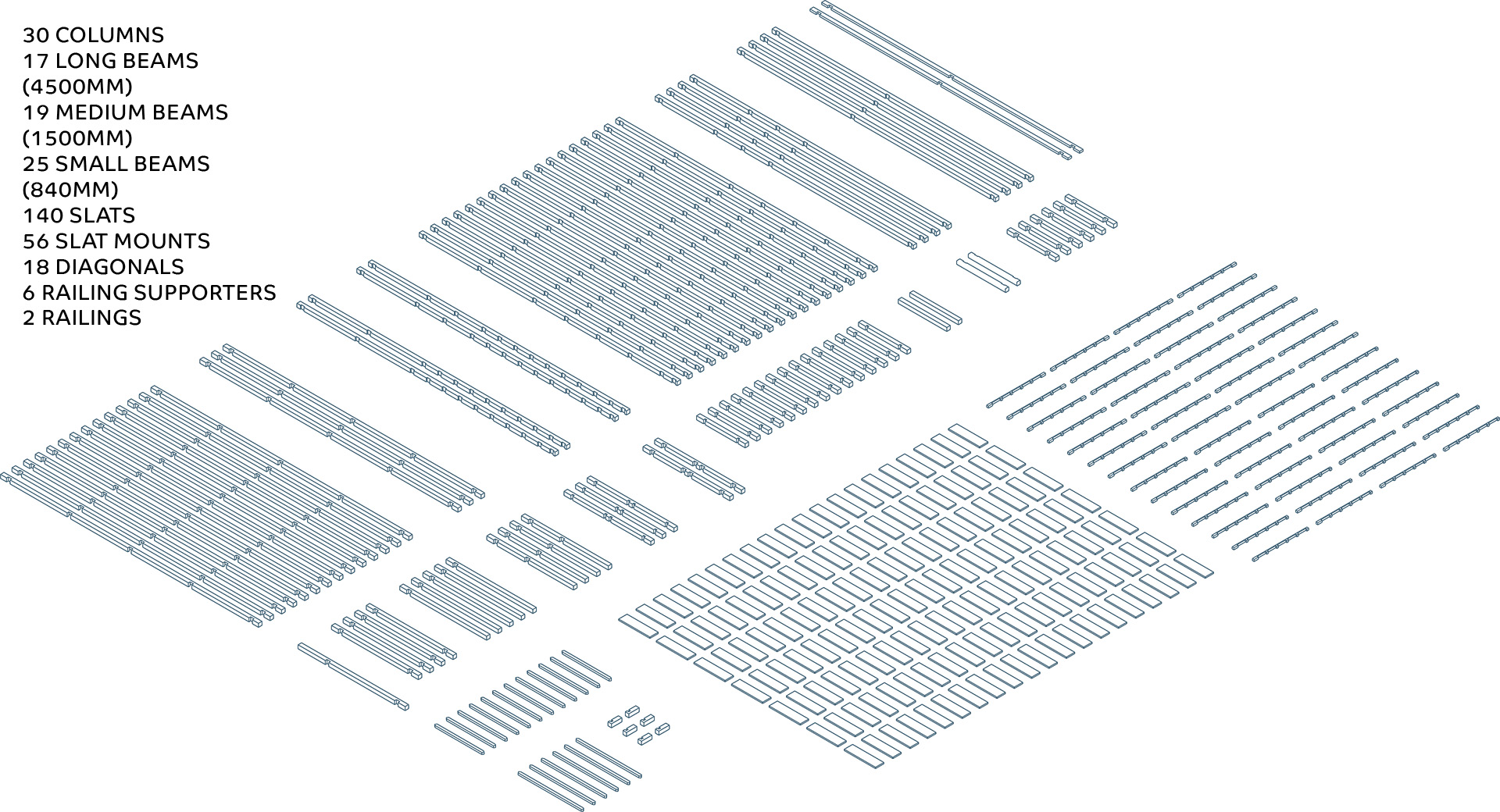
Assembling
The structure was assembled during the last two days. In order to have a better organization and to make sure no piece was missing, all columns and medium/small beams of each frame were placed on the floor. In sequence, they were positioned according to the frame design so they could be clamped, drilled and doweled.
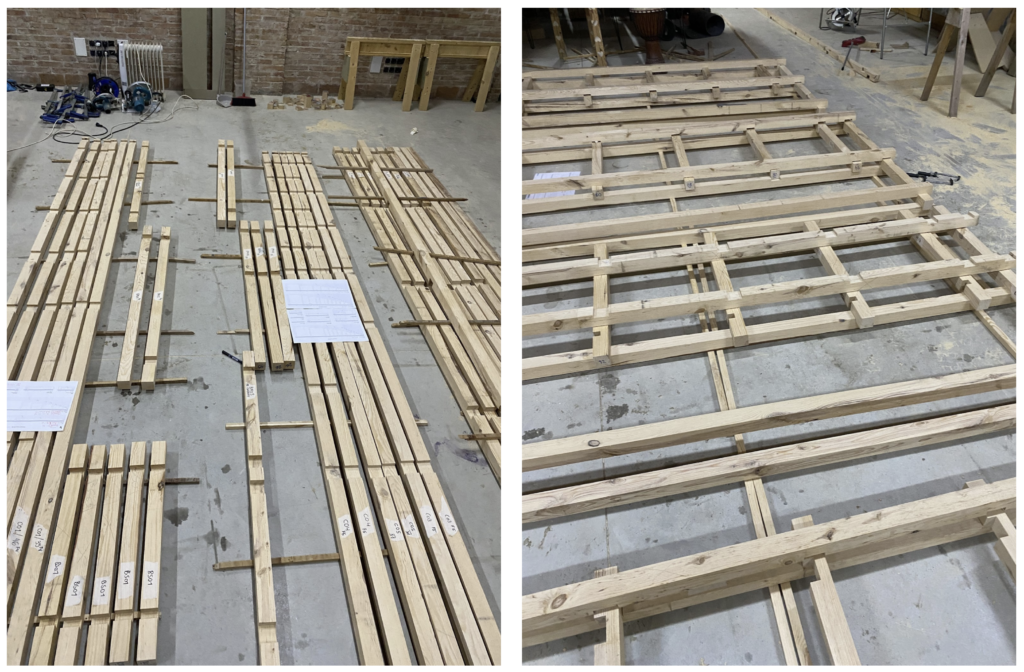
After all frames had they their dowels in, they could be lifted and we could start positioning the long longitudinal beams to connect the frames.
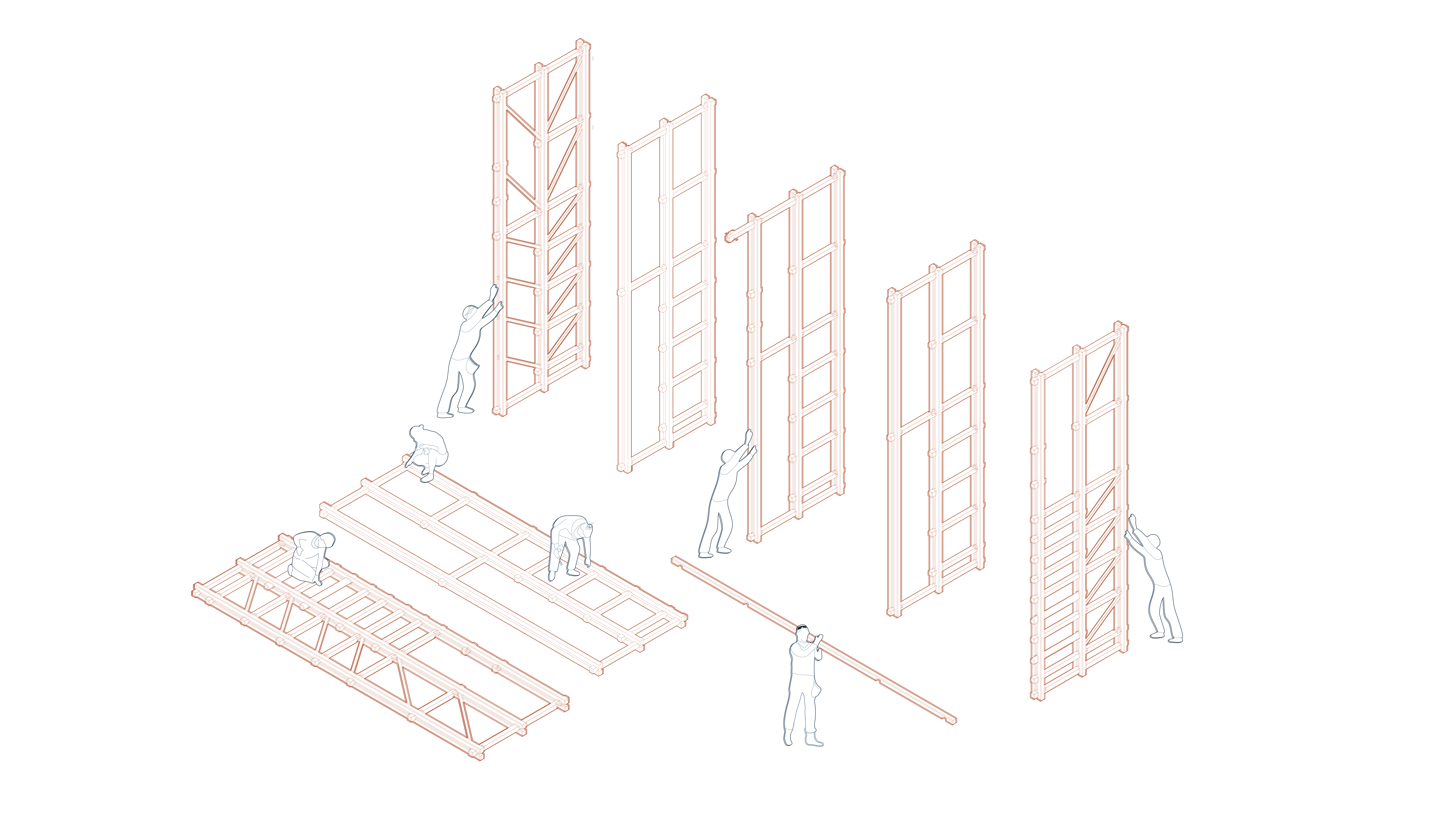
One important aspect of the assembly process was the use of long pieces of wood that were positioned diagonally and screwed so we could lock the structure. As the frames were moved or the longitudinal beams were placed, we would unscrew and screw according to our needs. After we finished the assembly, the structure was locked by itself, so the diagonals were removed.
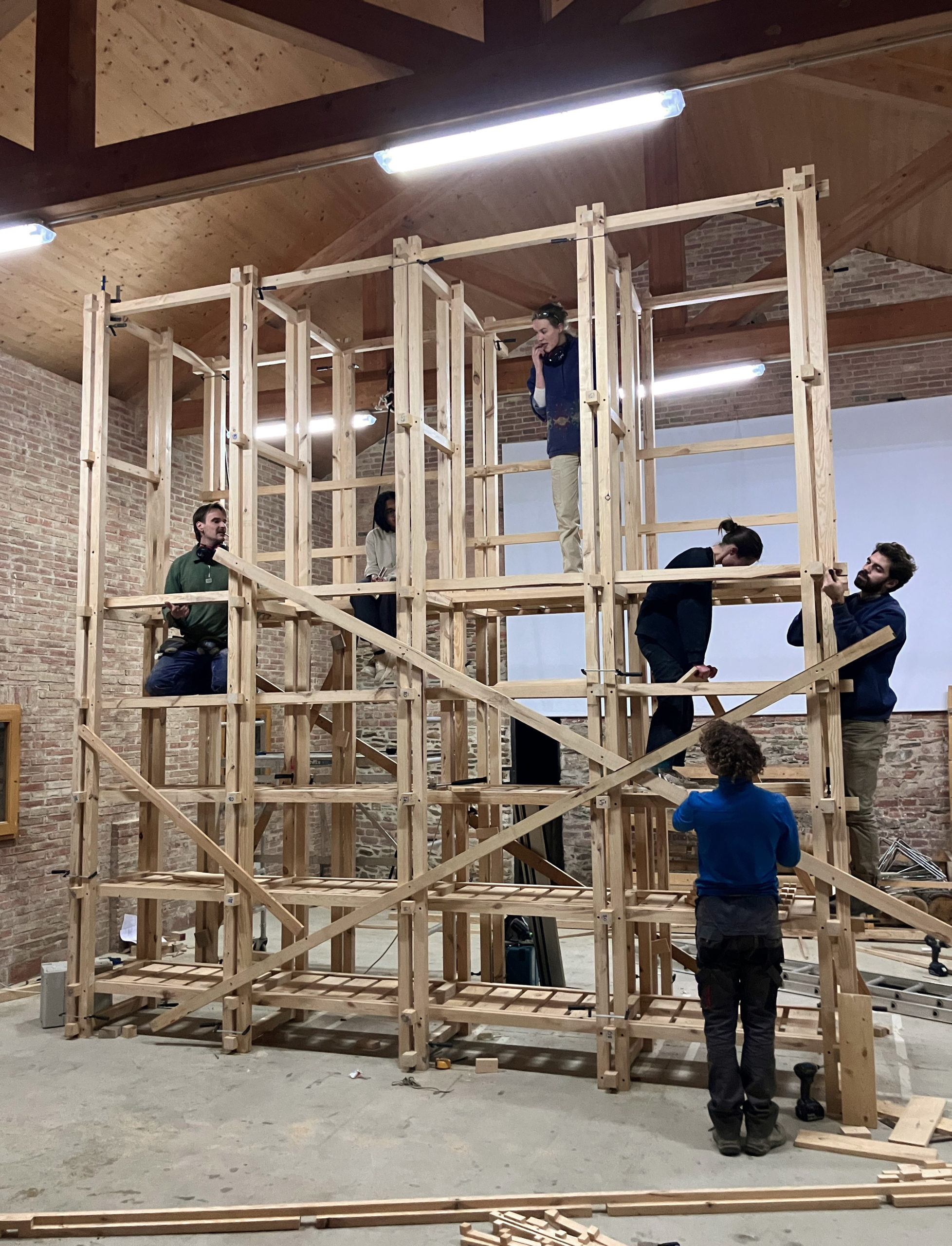
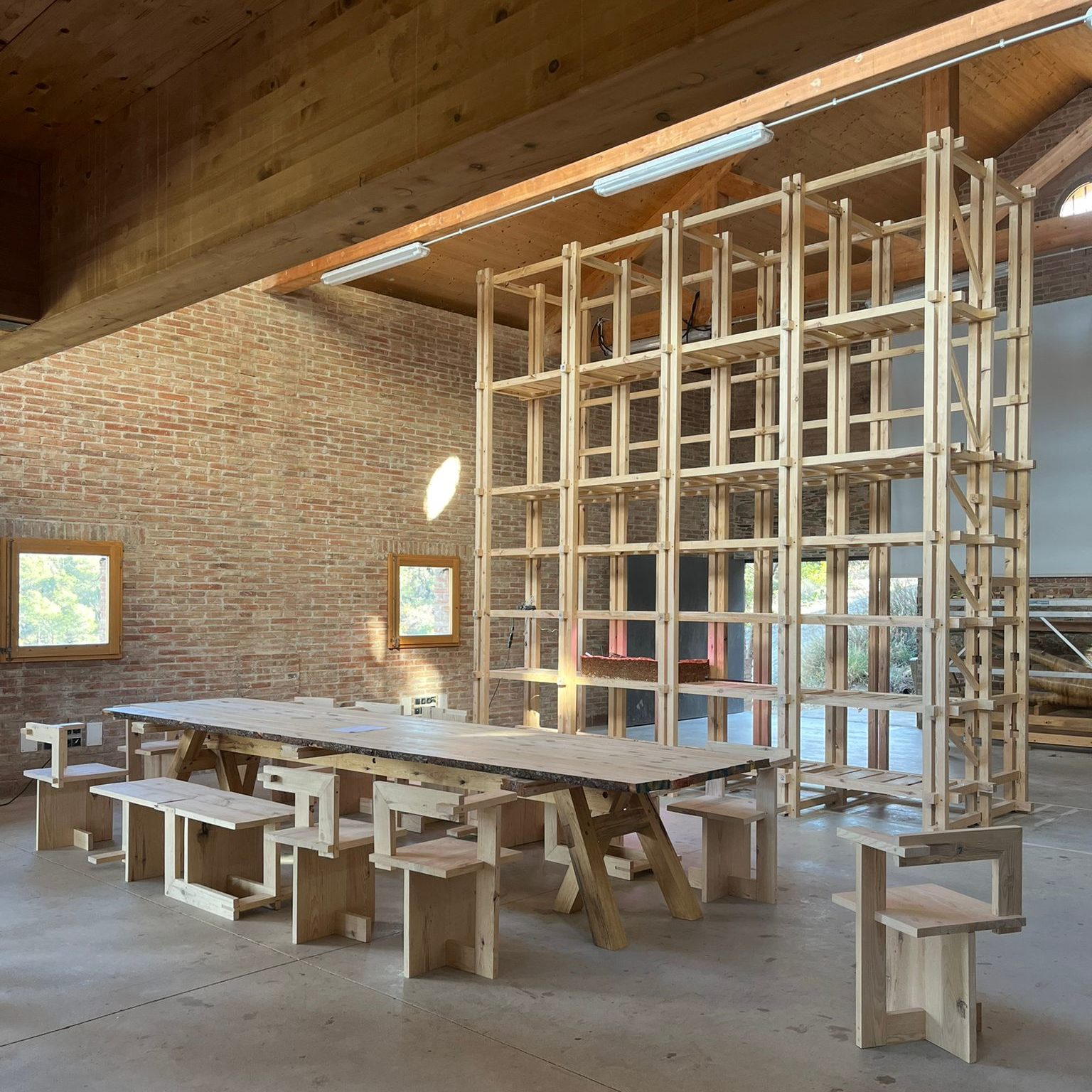
In summary, the task of producing and assembling an entire structure within the constraints of an 8-day timeframe posed a considerable challenge. Nevertheless, successful execution was achieved through meticulous planning. This included a comprehensive schedule outlining all necessary steps, the availability of technical drawings, and a well-coordinated assembly sequence. The collaborative efforts of a diverse team, each contributing unique skills, played a crucial role. The team’s ability to divide responsibilities enabled the simultaneous management of multiple tasks, contributing to the overall success of the project. Additionally, the invaluable assistance from our FABLAB manager, Bruno, who came up with great solutions, was instrumental — particularly in addressing the logistical challenge of working with lengthy pieces of 4.5 meters that did not fit in the carpentry cut machines.