The plastic crisis has reached staggering proportions. If all the plastic waste on Earth were laid out, it would be enough to cover the entire surface of Argentina ankle-deep.
Every year, we produce 300 million tons of plastic globally. Yet only 10% remains in use, while more than 80% is discarded. Of this discarded plastic, just 20% is recycled, leaving the vast majority to accumulate in landfills, pollute the environment, and infiltrate ecosystems as microplastics.
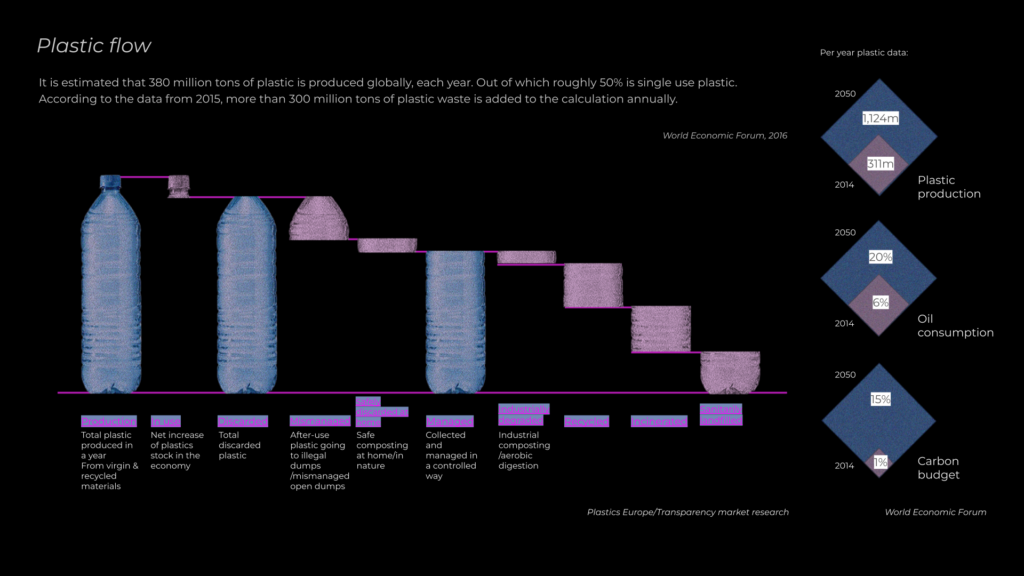
This overwhelming issue demands urgent and new solutions—like utilizing biodegradable materials and natural processes to rethink how we produce, use, and dispose of plastics. The main focus of this thesis has been trying to find ways to deal with plastic waste. This project has evolved through three distinct phases, it began with a focus on addressing the issue of plastic waste. To tackle this, I first sought to understand what plastics actually are and how they are made.
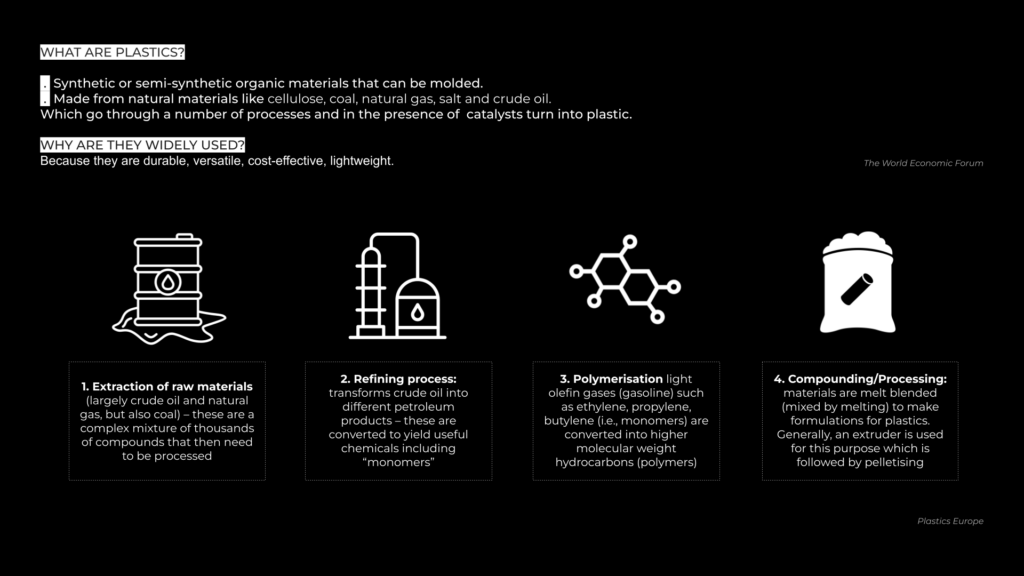
The production of plastics starts with the extraction of natural resources like oil, gas, or coal. These raw materials undergo a refining process to be transformed into monomers, which are the building blocks of plastic. The next step is polymerization, where monomers are chemically bonded together to form long polymer chains, creating plastic. This process typically relies on a catalyst to facilitate the chemical reactions.
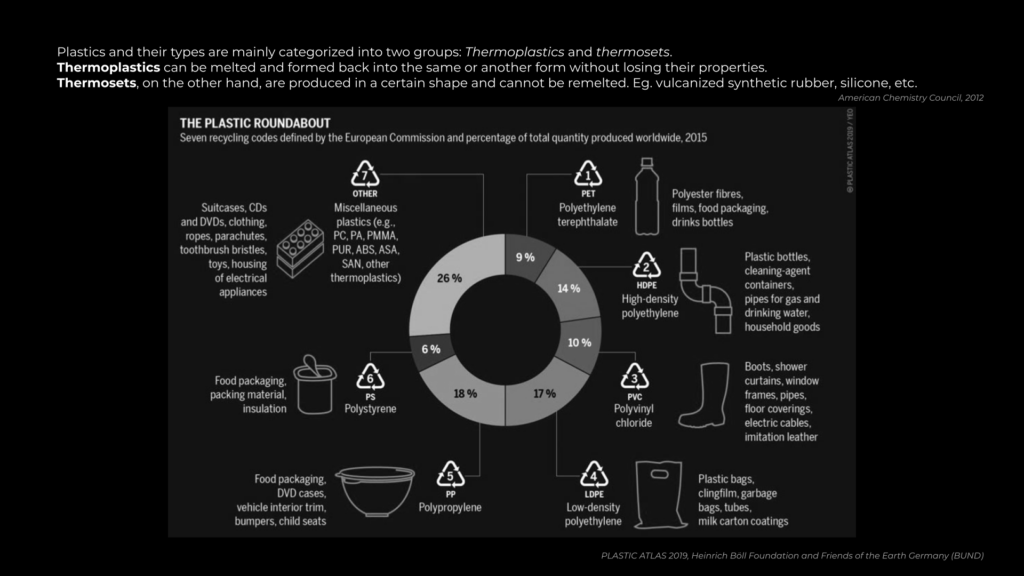
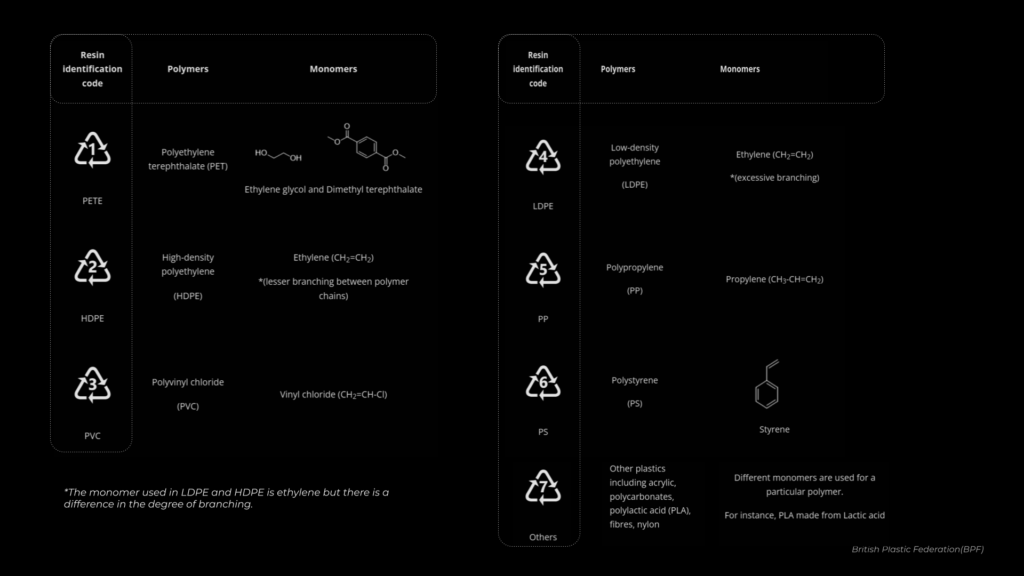
There are seven types of plastics, each designed for specific purposes based on their properties. To actually understand plastic degradation, I examined the composition of each type, as understanding their chemical structure was critical for identifying ways to break them down.
While researching natural ways to degrade plastic, I came across the bacterium Ideonella sakaiensis, which has the remarkable ability to break down PET (polyethylene terephthalate), a common plastic used in bottles and packaging. The concept was to integrate this bacterium in the form of a culture into structures made from waste PET. This approach aimed to simultaneously recycle and biodegrade the material.
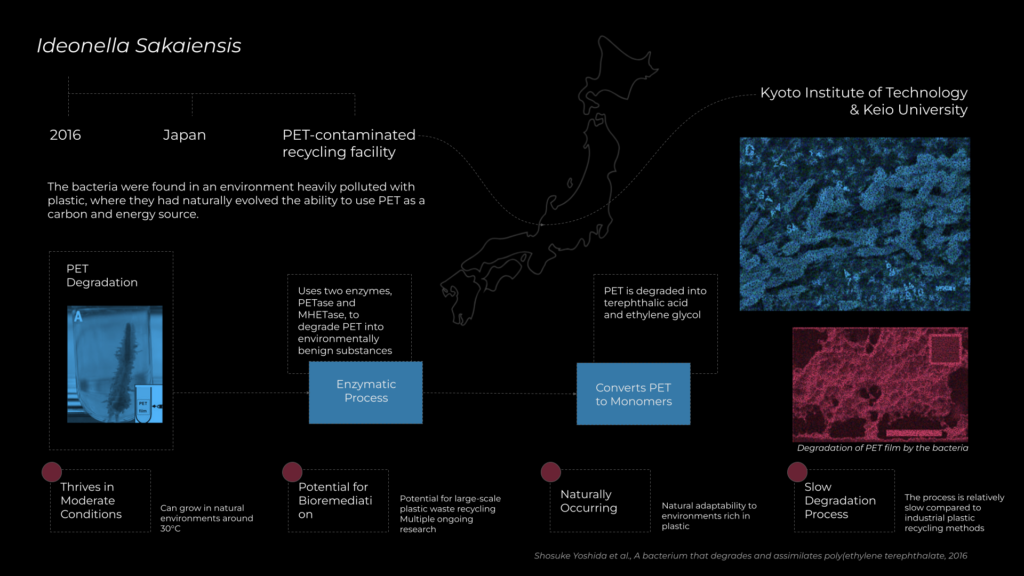
To bring this idea to life, the next step was to explore fabrication techniques and understand the behavior of PET and other plastics. I began experimenting with heating PET bottles, creating abstract compositions as part of a study on material properties. These experiments also helped me explore fabrication methods that aligned with both functional and aesthetic goals.
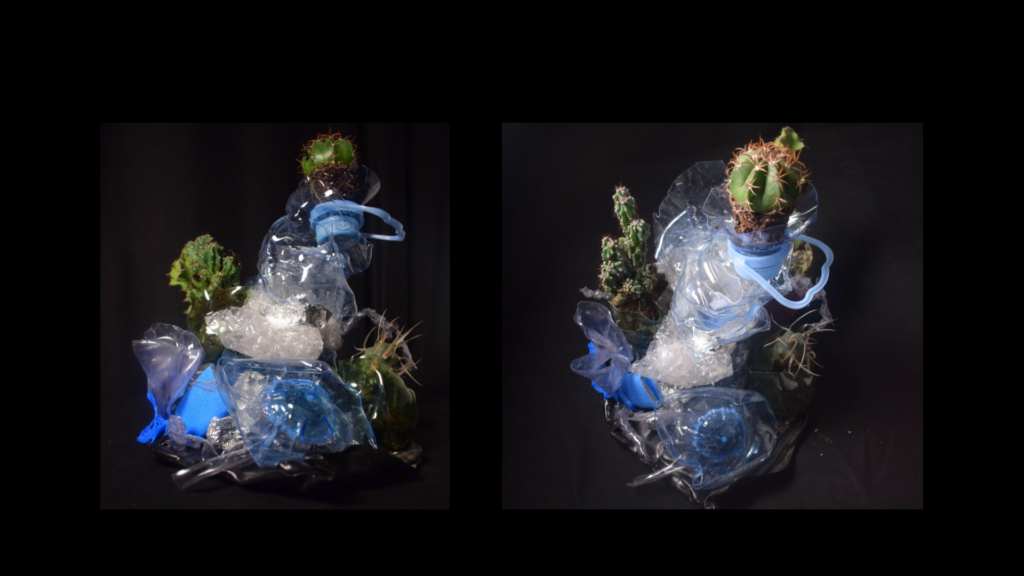
Additionally, I researched similar projects to draw inspiration and refine the direction of my work. This phase was crucial for understanding the interplay between material science, design, and fabrication processes.
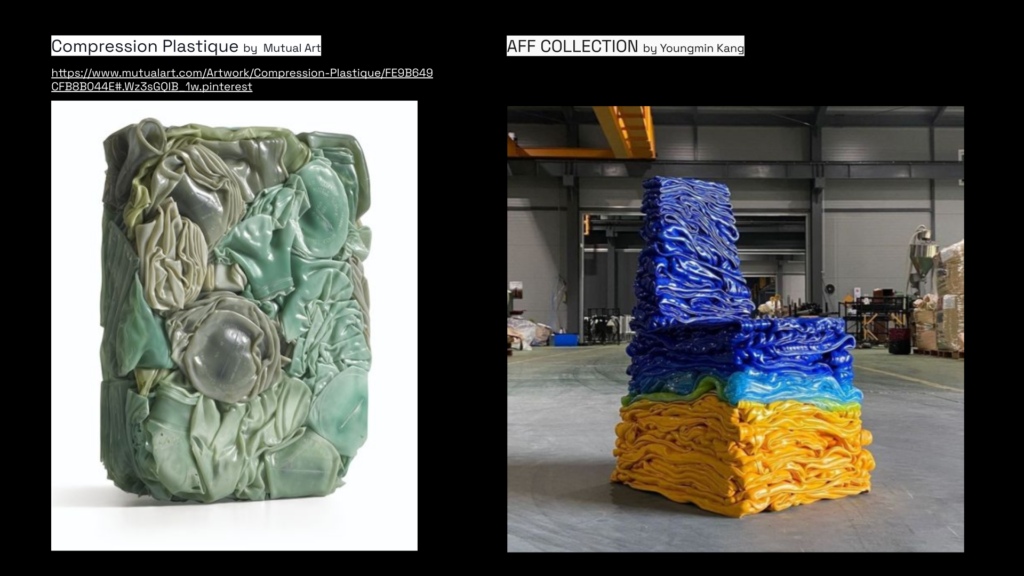
While exploring 3D printing with waste PET, I encountered significant challenges related to the process’s technical feasibility and environmental safety. Heating PET to the required temperatures for extrusion releases potentially harmful fumes and requires specialized facilities with proper ventilation and filtration systems. Additionally, achieving consistent material quality from shredded PET waste for 3D printing is complex and resource-intensive, often requiring advanced preprocessing. These challenges led me to shift my focus toward shredding and embedding PET waste in biopolymer materials, which are also sometimes called “Bioplastics”. But, during my research, I discovered that this term is often used interchangeably for various types of plastics, leading to confusion. To better understand the distinctions, I looked into academic papers and research articles to clarify the differences, as it will be crucial later.
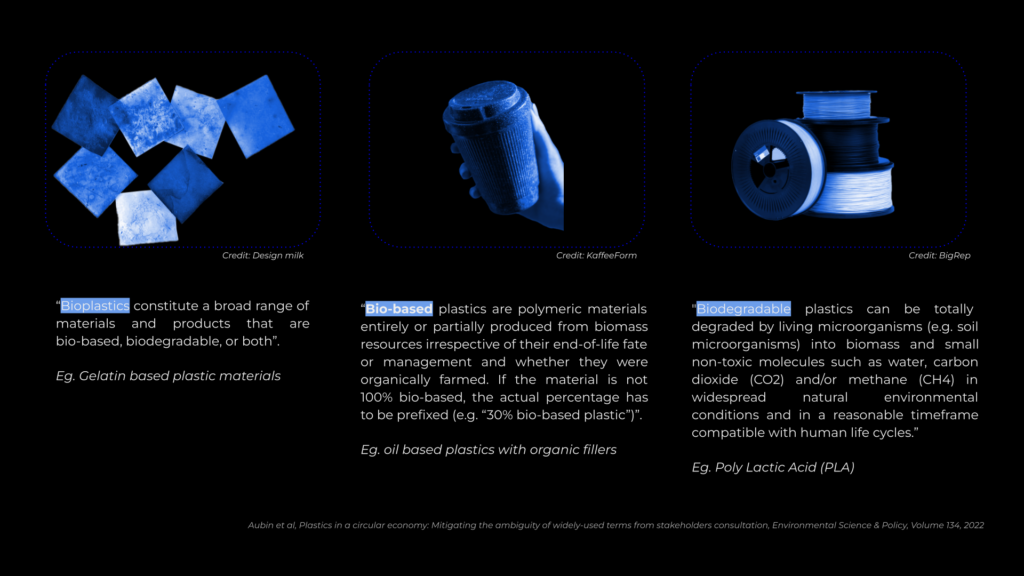
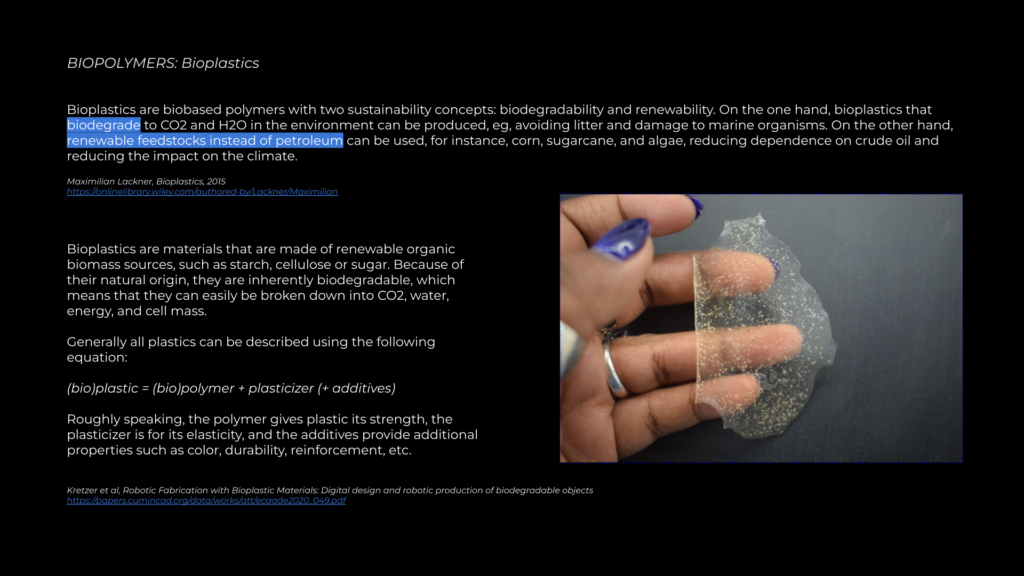
During my research, I came across a paper that detailed various bioplastic recipes specifically designed for robotic fabrication. Intrigued by the possibilities, I decided to test each recipe to determine which one would be most suitable for the fabrication technique I aimed to use.
Recipe 1:
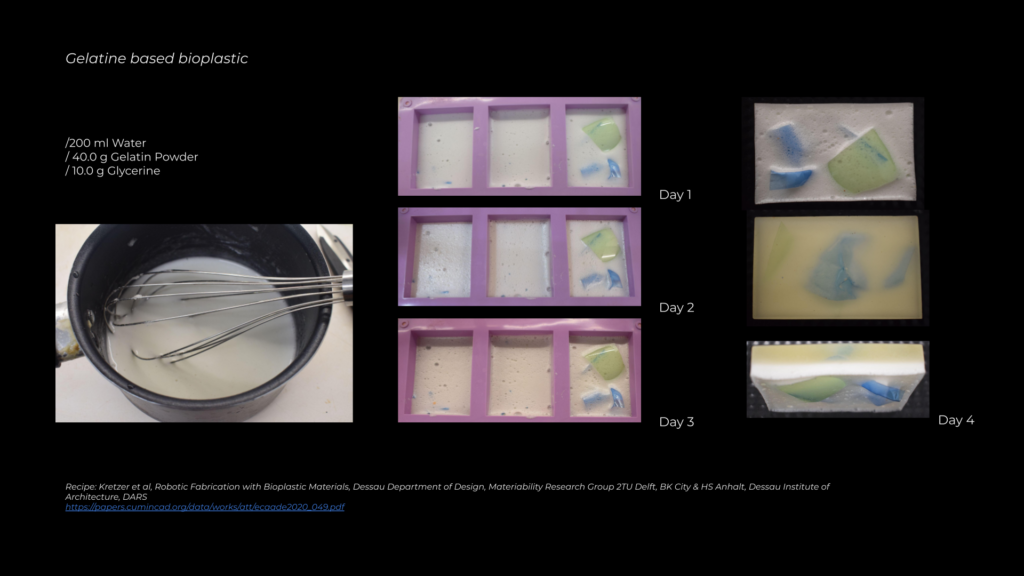
Although this recipe was not suitable for 3D printing, I still documented the drying and aging process to evaluate the performance and consider alternative extrusion techniques that could accommodate the physical consistency of the material. By doing so, I could identify the recipes that not only looked the best but also worked effectively, regardless of their initial compatibility with 3D printing.
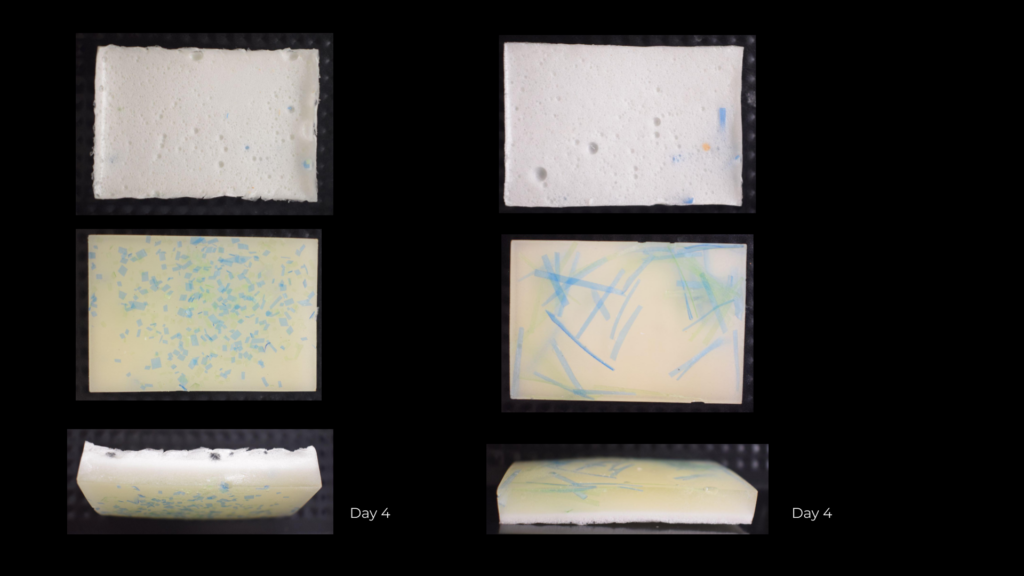
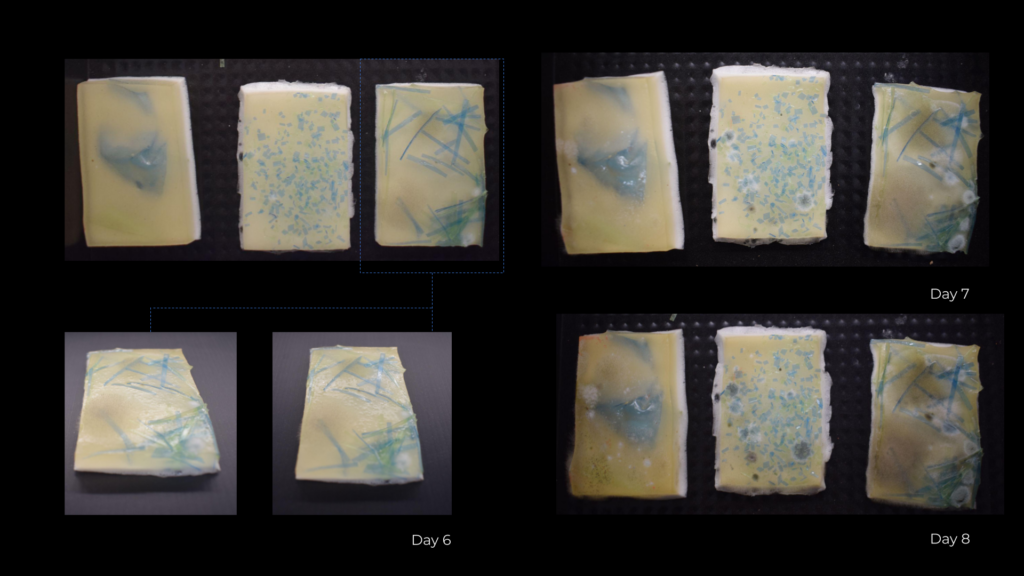
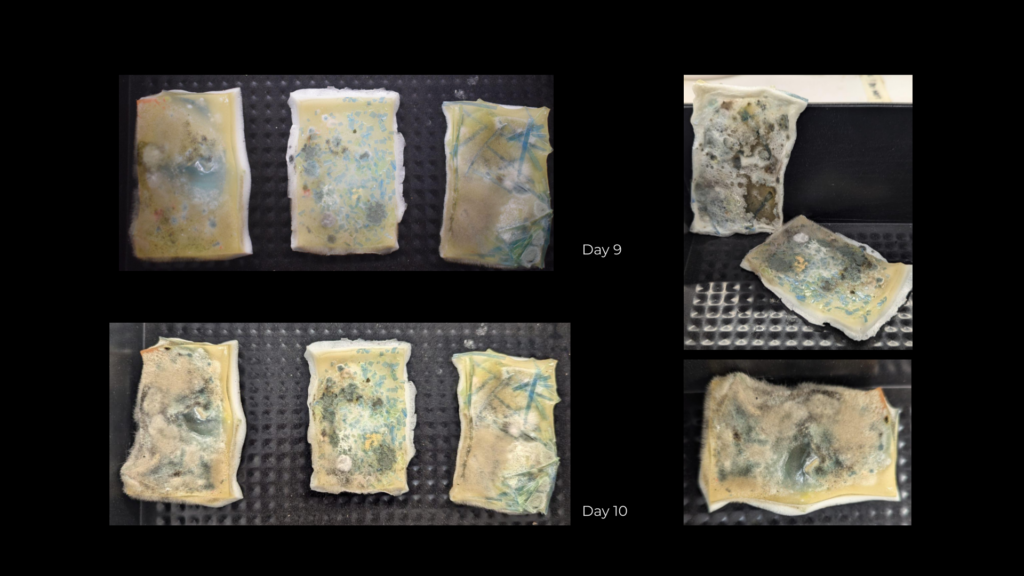
However, the material began to catch mold pretty quickly, and there was a need to discard it by day 10.
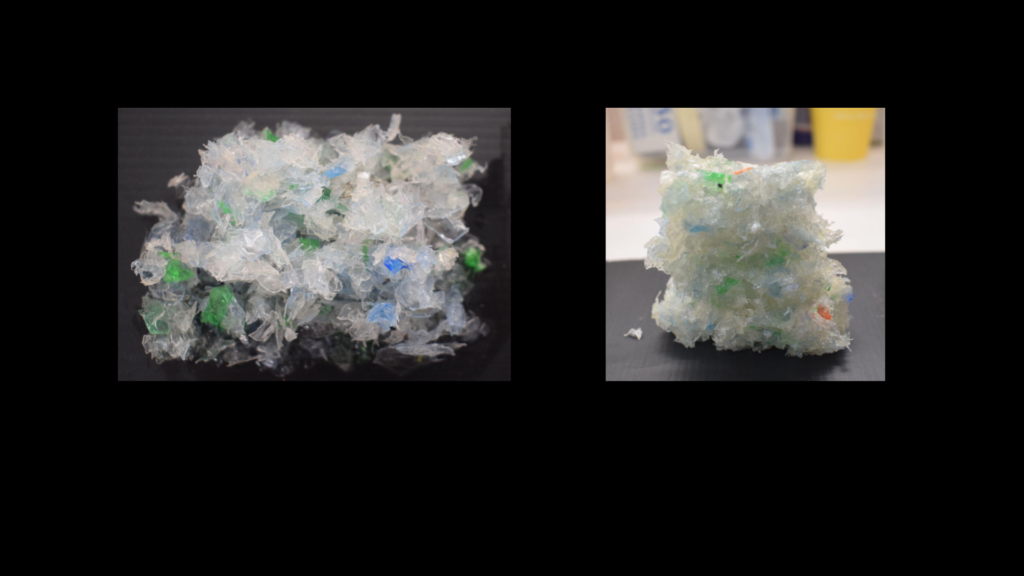
Though in the mixture with more plastic and less binder, it did not catch mold.
Recipe 2:
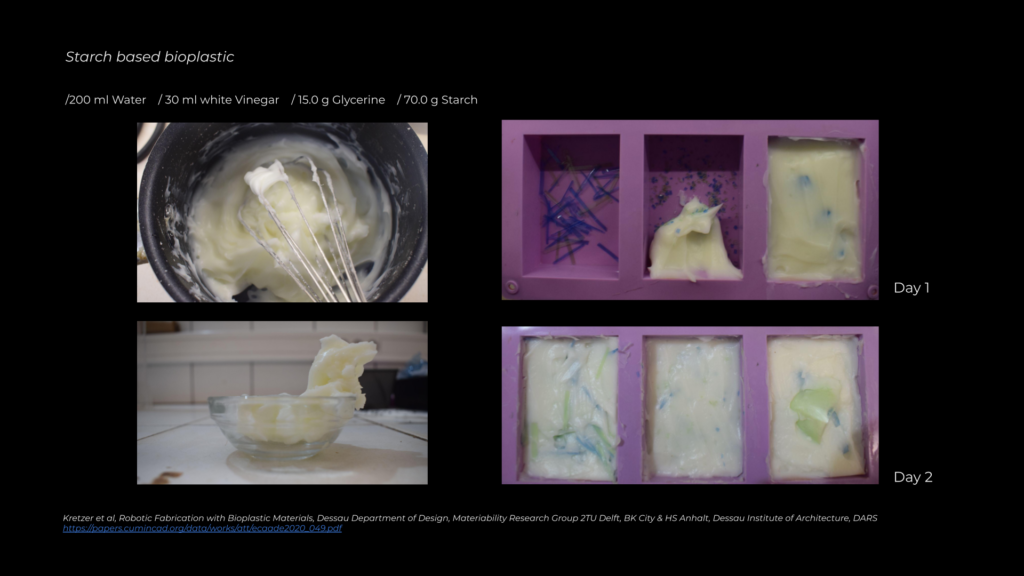
The next recipe I tested used starch, and its consistency turned out to be perfect for 3D printing.
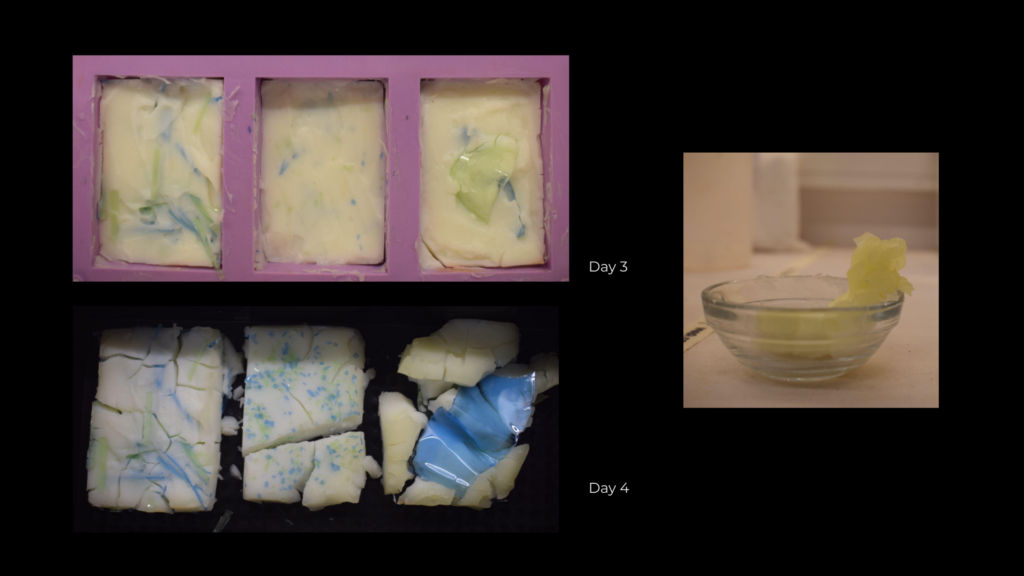
However, the material aged poorly, breaking and falling apart as early as the second day. This instability made it unsuitable for long-term applications.
Recipe 3:
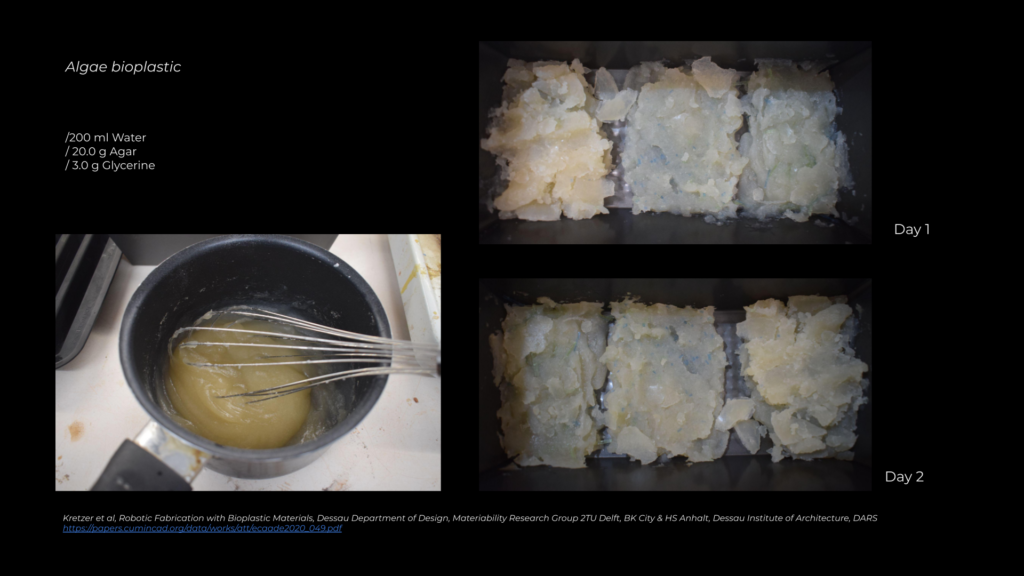
The third recipe used agar, and while the consistency was suitable for a couple of minutes, the material set very quickly. Unfortunately, it began coming apart in layers with just a light touch, making it unsuitable for practical use.
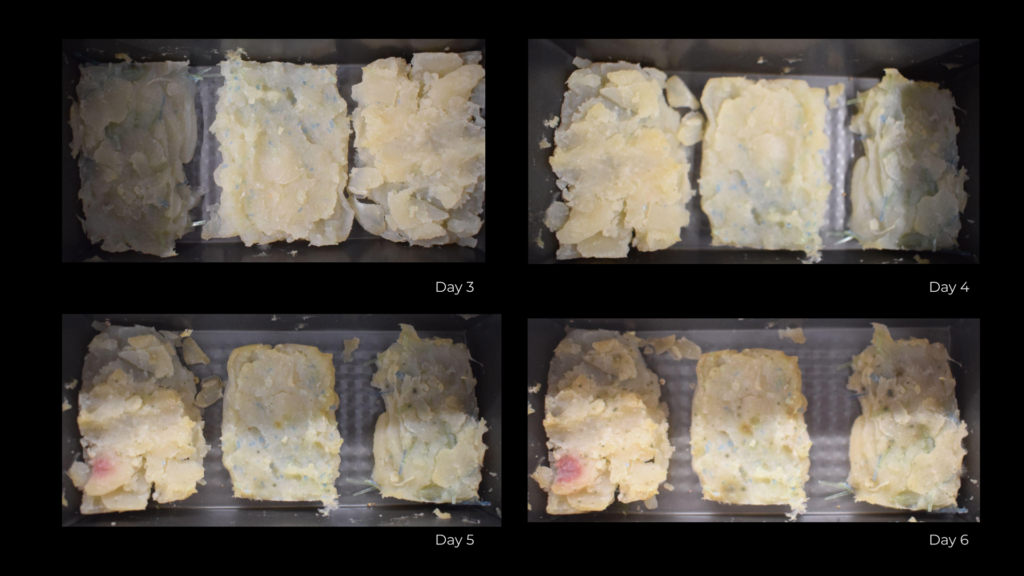
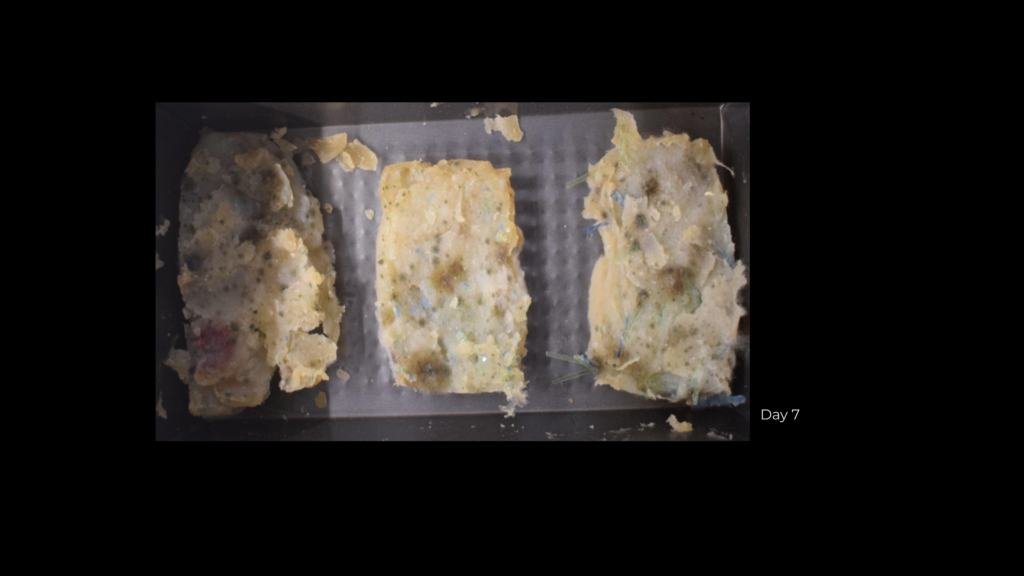
It had to be discarded on the 7th day due to excessive mold growth.
Recipes 4 and 5:
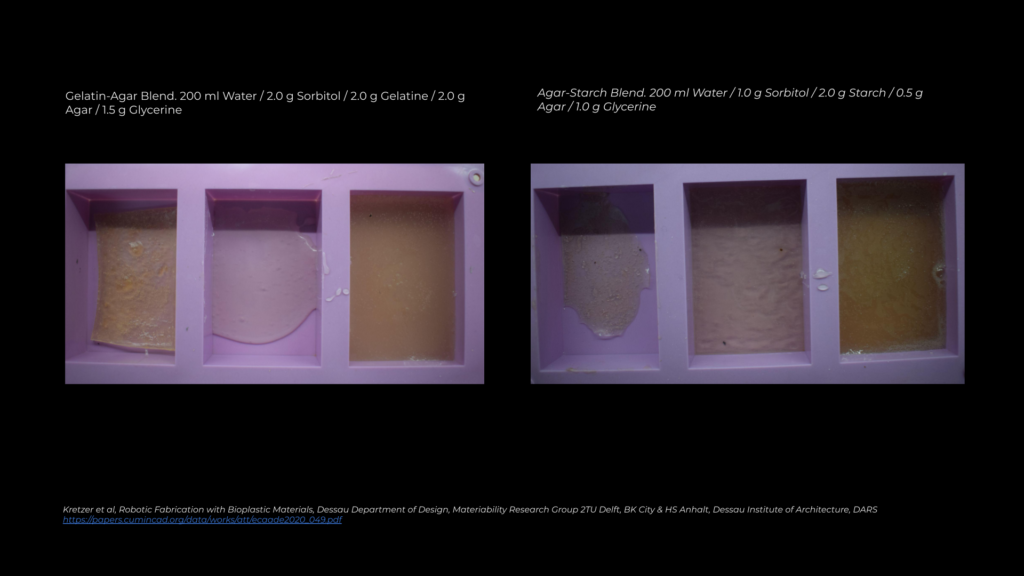
The next batch of recipes had better plastic qualities, but the liquid consistency was still off and made it unusable. By this point, I had already decided to 3D print the material, so the consistency needed to be just right. On top of that, the material ended up being really sticky, like it had been soaked in sugar syrup, which made handling it tricky.
Recipes 6, 7 and 8:
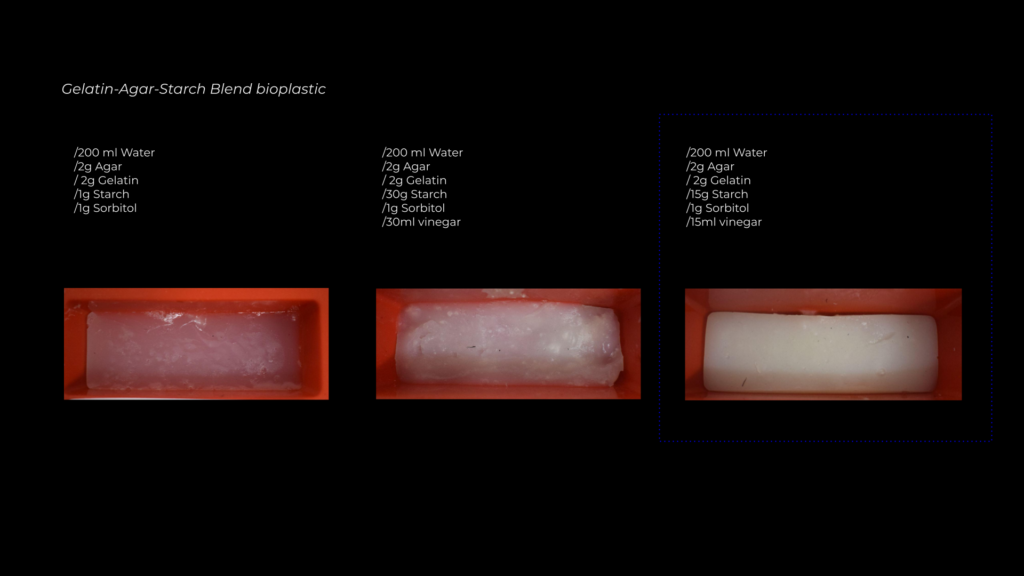
Since I liked how the gelatin and agar recipes set and the consistency of the starch-based ones, I decided to experiment by mixing both to see if I could find a balance. It turned out to work really well, so I decided to move forward with 3D printing using the blend in the middle.
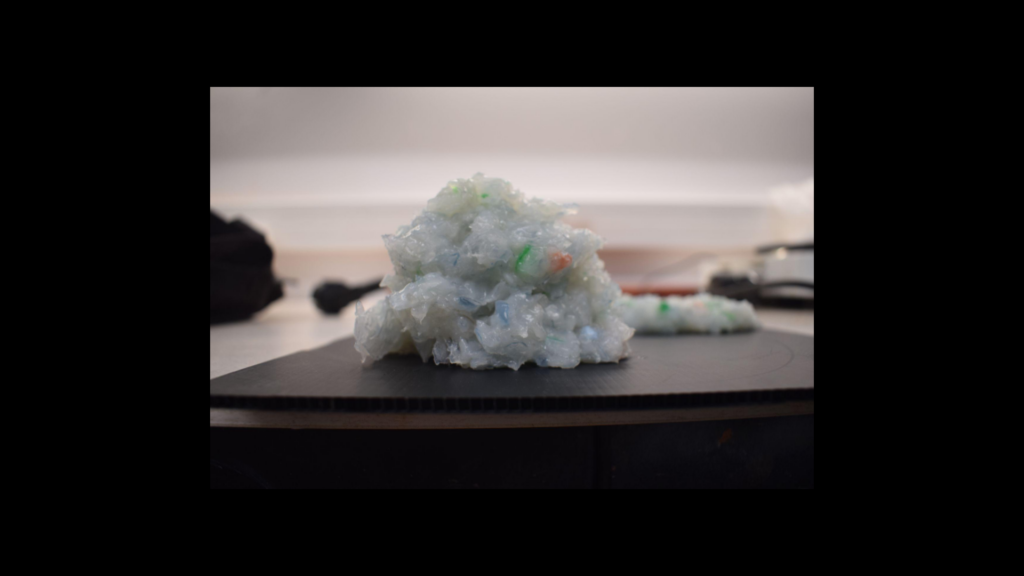
Since, the idea involved shredding plastic waste and binding it with bioplastics to create 3D-printed structures. I also tried some hand extrusions with the mix of biopolymer and shredded PET to test its functionality as a 3D-printable material.
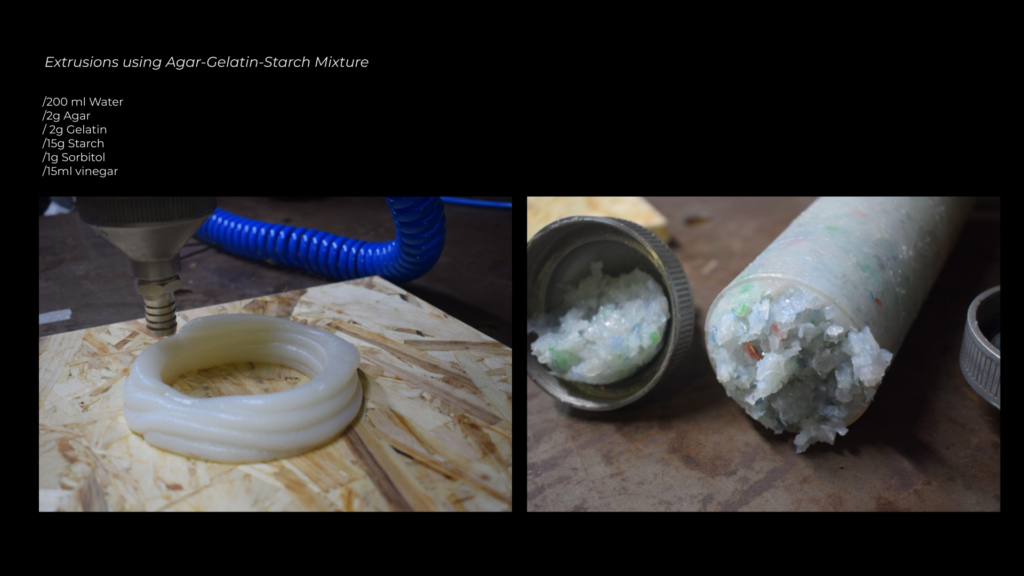
However, fabricating with it came with more challenges, as the plastic tended to accumulate at the nozzle, and only the biopolymer was being extruded.
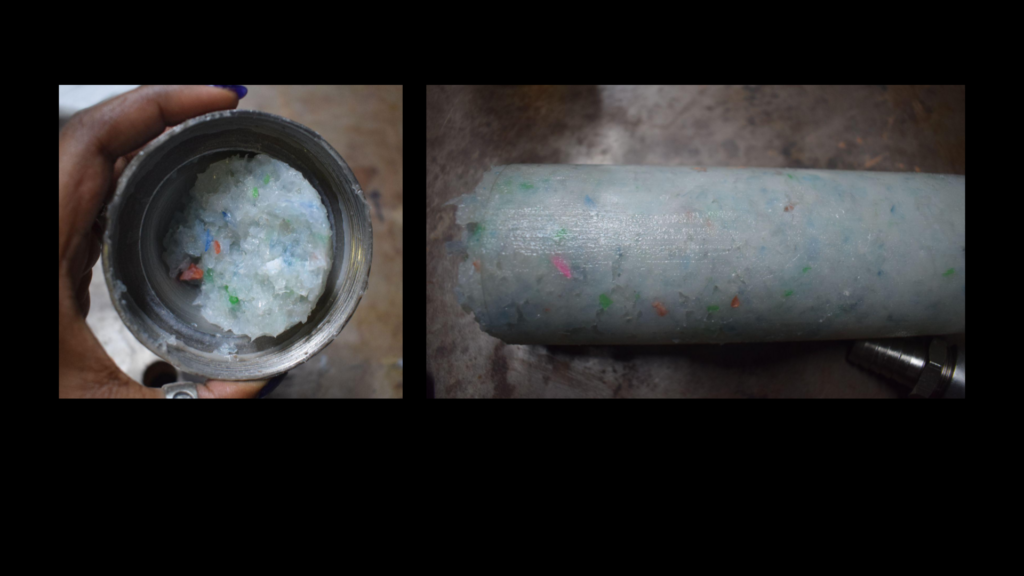
The issue was that the material wasn’t thick enough to bind properly with the plastic shreds.
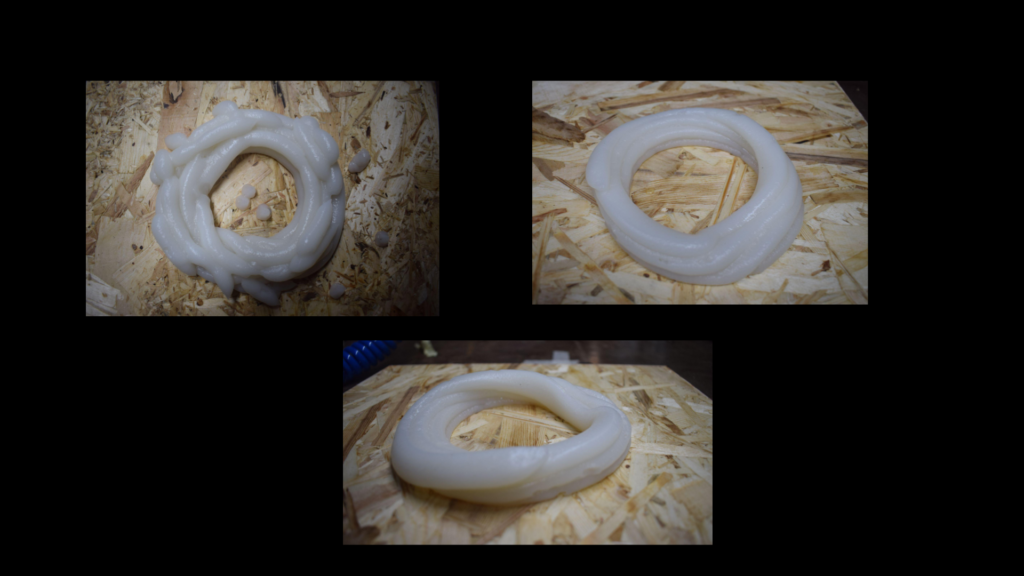
However, after testing its drying process over time, I realized it didn’t age well, so making adjustments to thicken the recipe wasn’t a viable option.
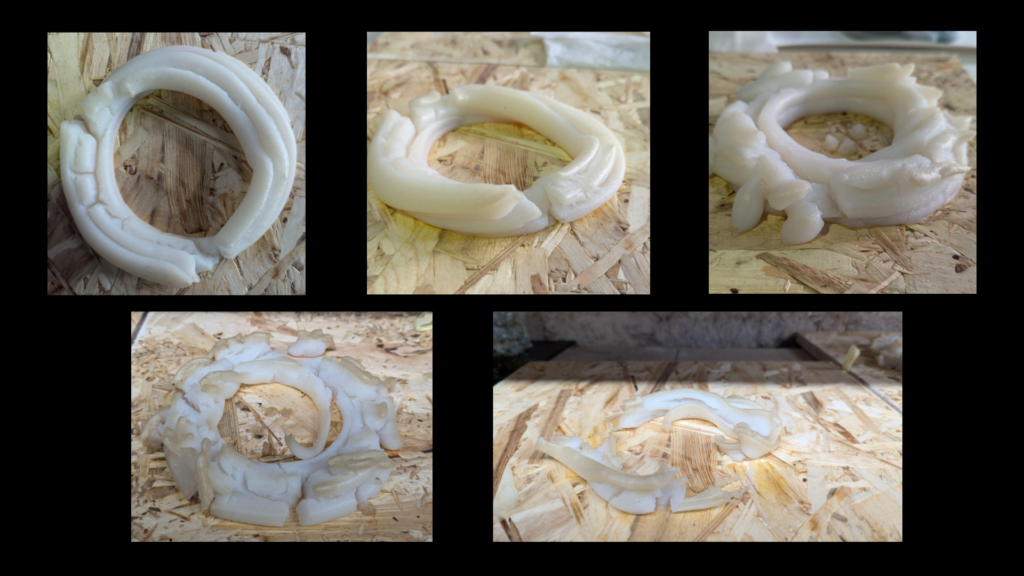
While discussing the challenges of working with these materials with my thesis advisor, Ricardo, he accidentally referred to the mix as a hydrogel. That gave me the idea to use hydrogel (methylcellulose, sodium alginate, and water) as the binding material instead.
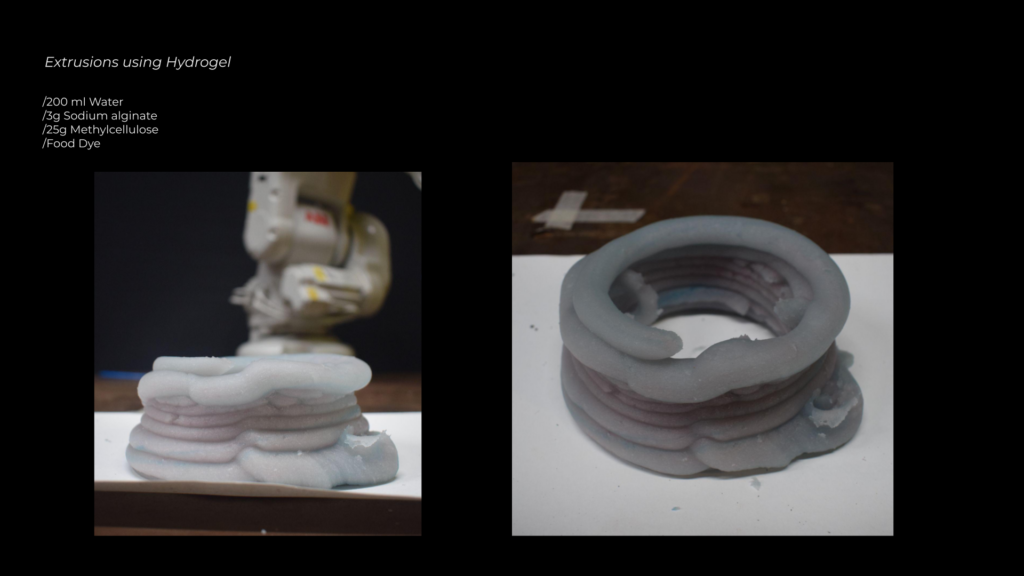
However, I wasn’t sure about its printability, so I did some test prints using only the hydrogel material.
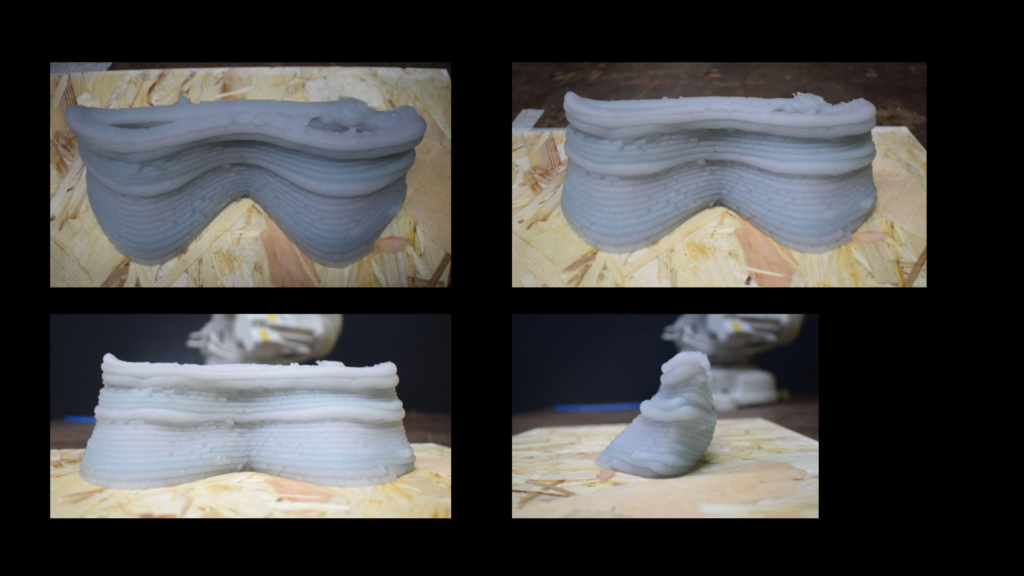
Since it worked well, the next step was to add PET shreds in increasing amounts to avoid the issues I had with the gelatin-agar-starch mixture.
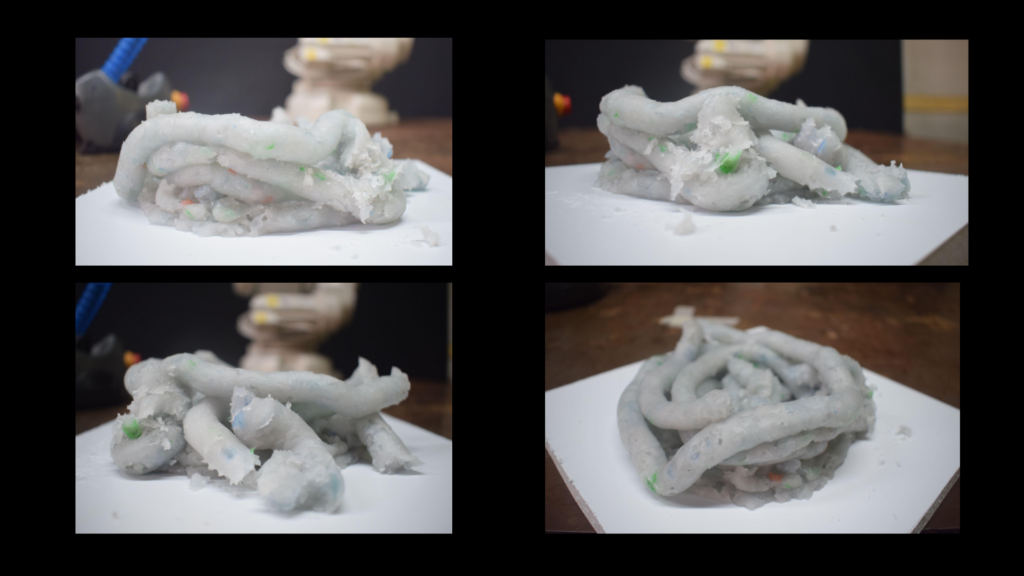
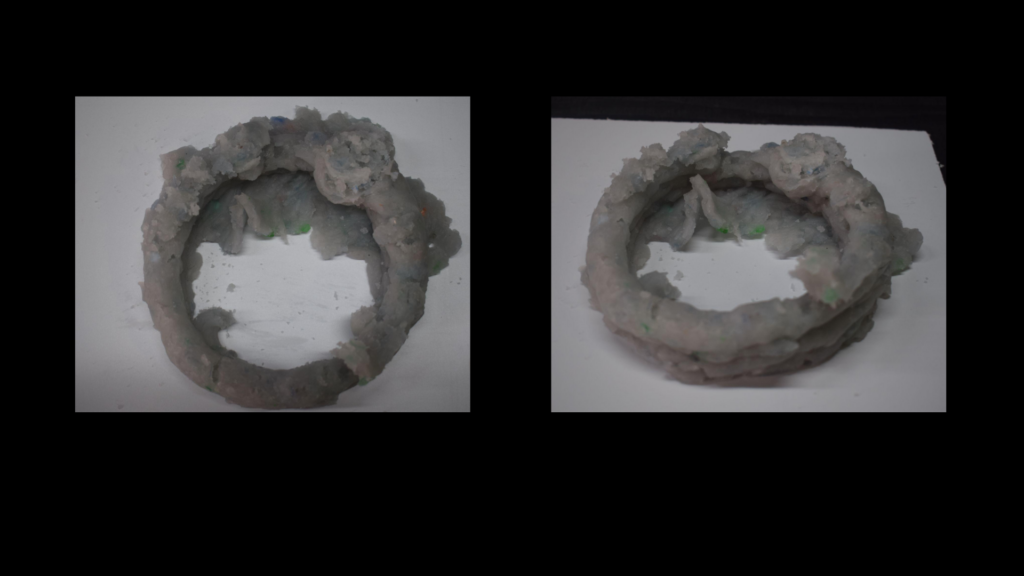
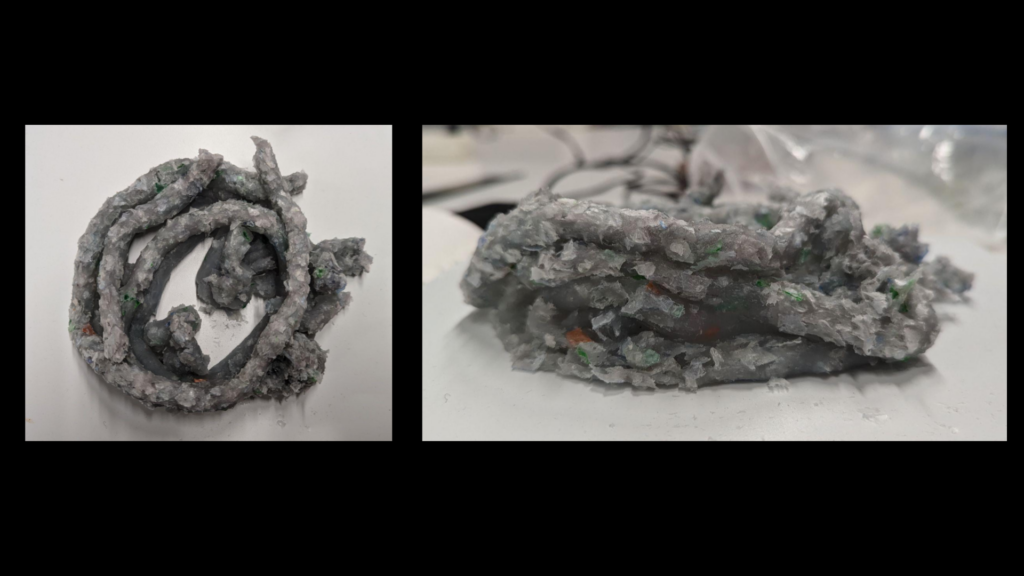
Now that I knew the mixture worked, I focused on addressing the issue of degradability. Since methylcellulose breaks down faster than conventional plastic, and knowing that plastic can sometimes degrade in compost and soil, I decided to use plants to help hold the structure together. The cellulose would serve as a food source for the plants, aiding in the degradation process.
To test this, I first experimented with growing moss on all the bioplastic mixtures to observe how it would grow or would not grow.
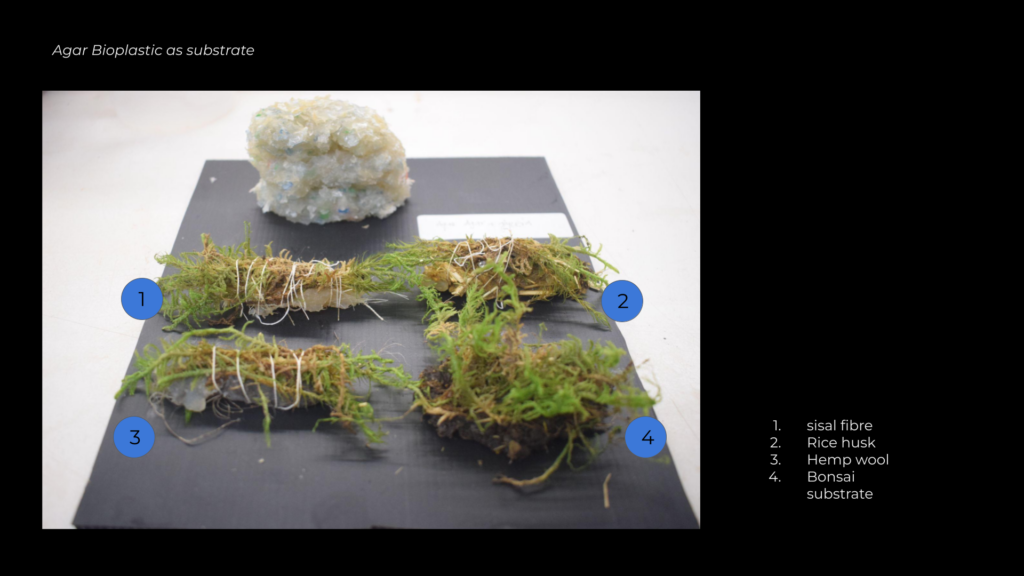
I also added some substrates to the bioplastic mixture, such as sisal fiber and hemp wool, to see if they would positively affect the growth. This would also give us potential options for additional structural support in the future, if needed.
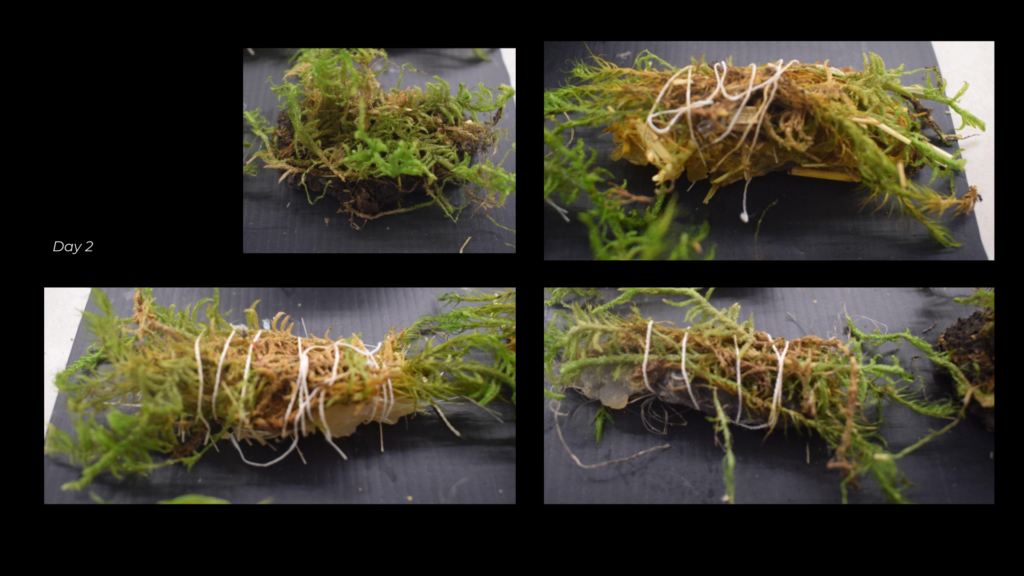
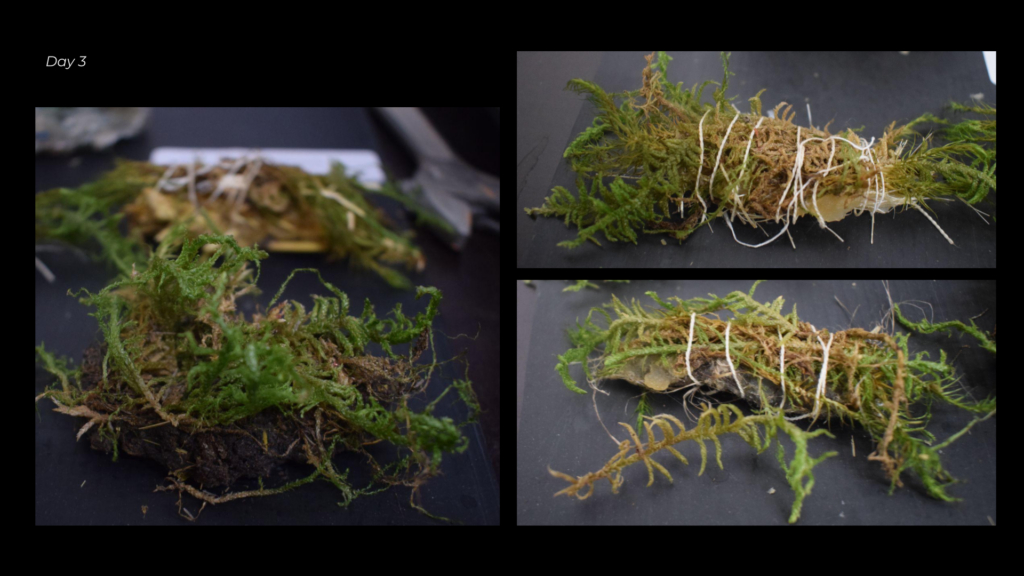
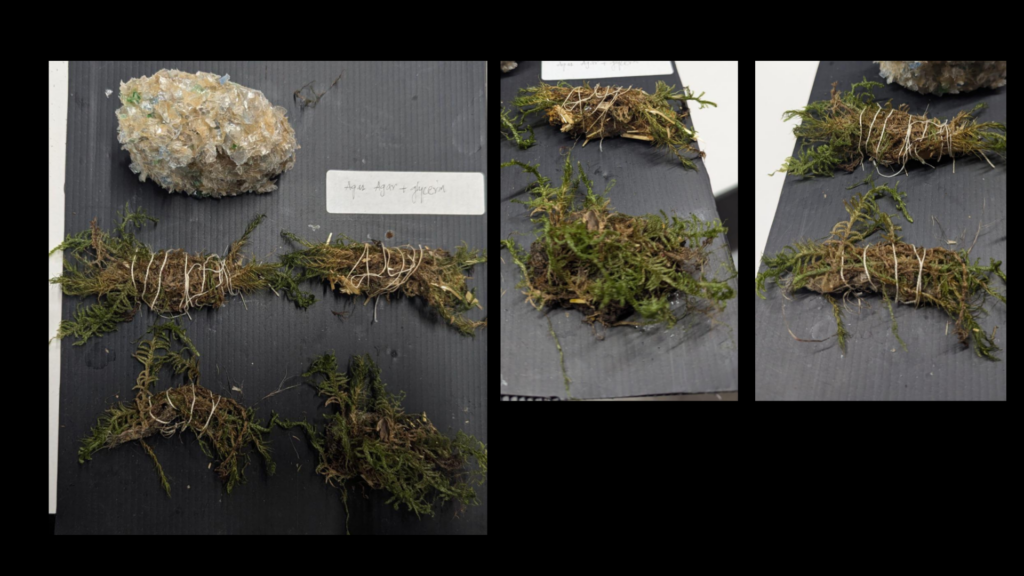
Apart from the need to be watered frequently the moss grew well on all of them.
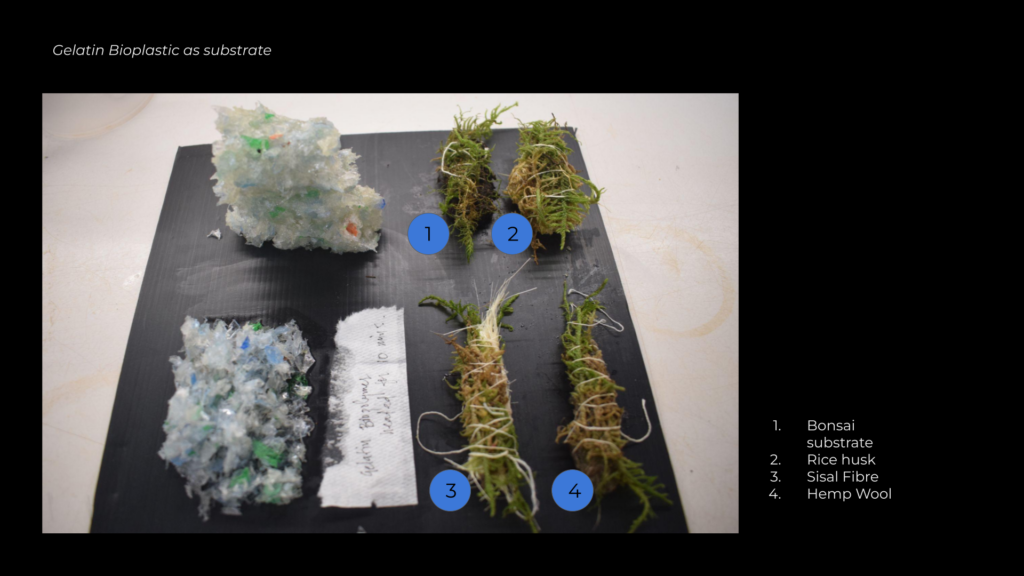
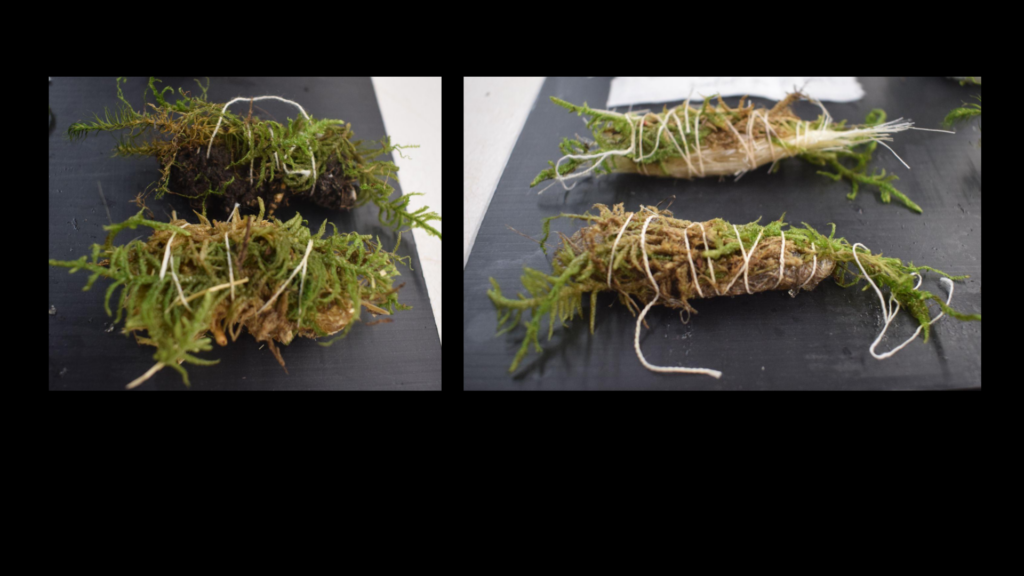
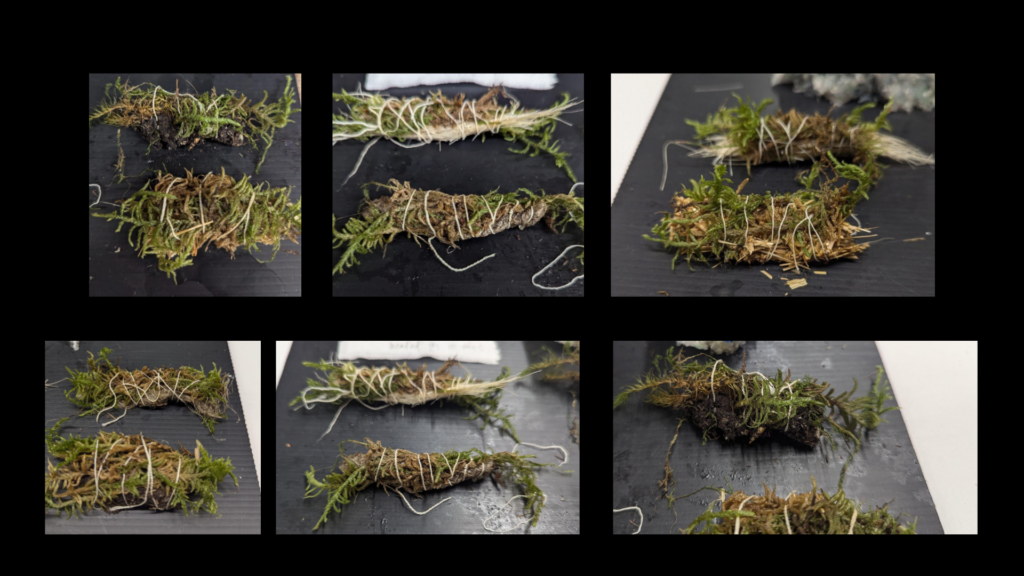
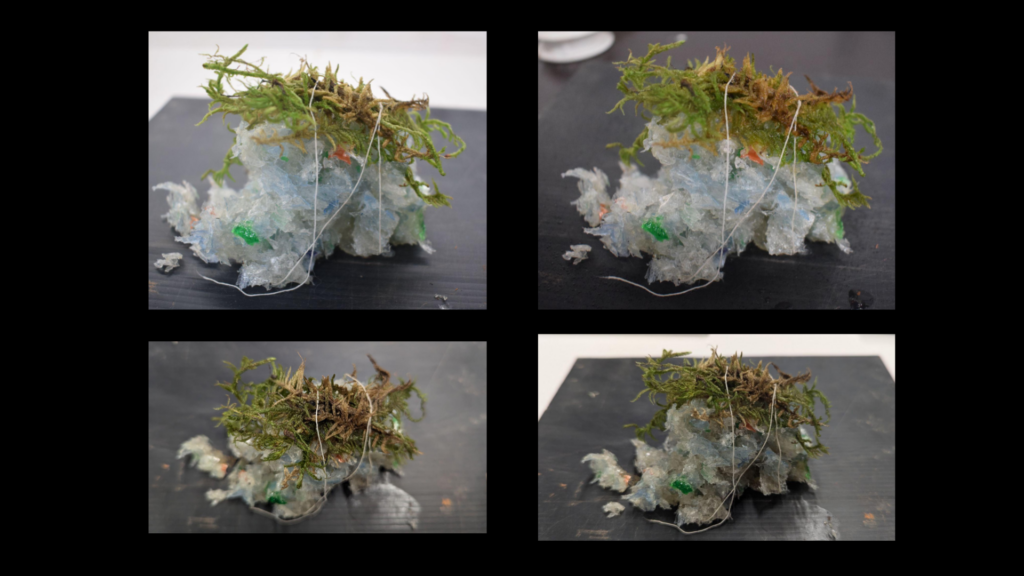
I also set up the moss experiment with Bonsai substrate with xanthan gum in case there was no growth on the bioplastic mediums. The idea was to have alternating layers of bioplastic and PET mixture and Bonsai and xanthan gum mixture.
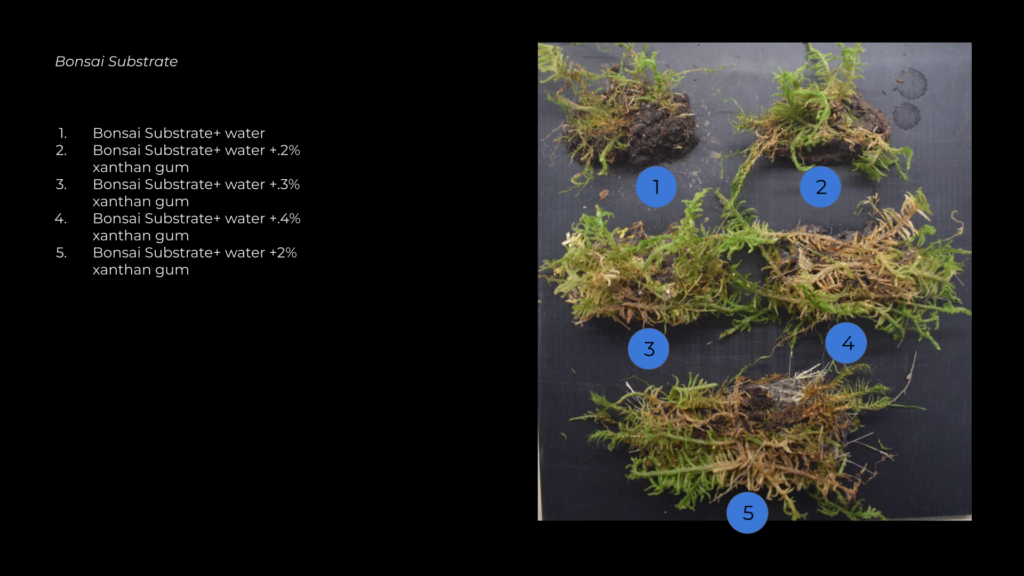
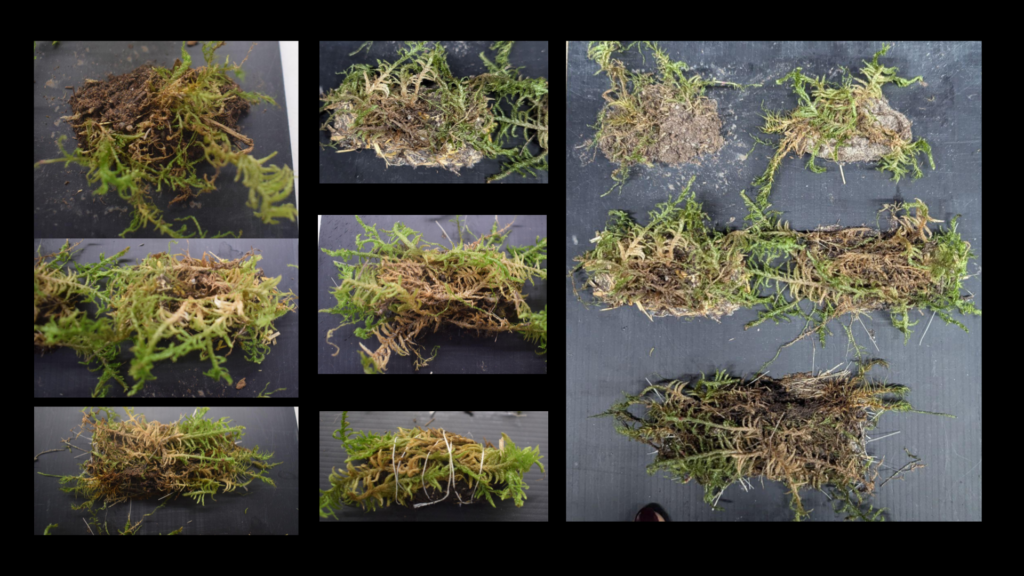
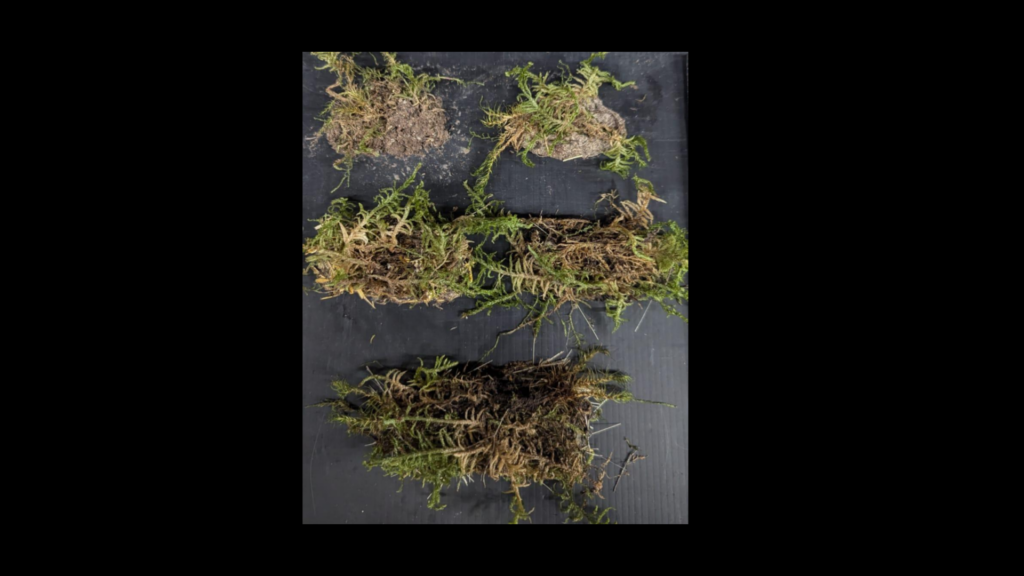
The turning point in my research came during a discussion about whether plants can degrade plastic. Our visiting faculty scientist revealed that, while plants themselves can’t, some bacteria on their roots are capable of degrading PLA. This insight led me to shift my focus from PET to PLA.
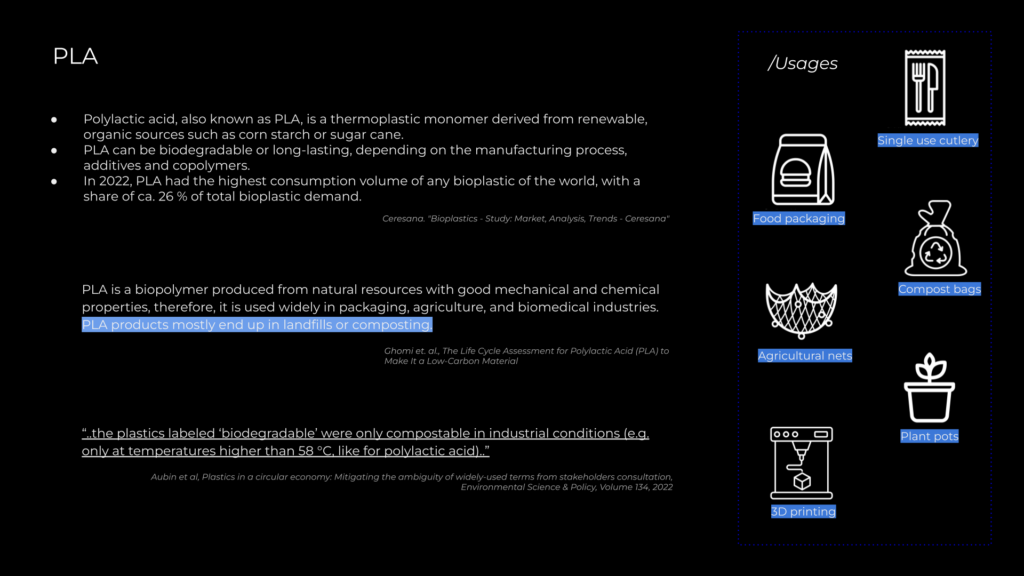
While researching PLA, I discovered that, despite being marketed as a compostable plastic, it isn’t compostable in regular home composts. Instead, it requires industrial composting, which is an energy-intensive process. Many people buy PLA thinking it’s environmentally friendly, but in reality, it often takes hundreds of years to degrade in natural conditions. At that point, the research shifted to focus on accelerating the degradation of PLA while exploring its potential as an architectural material.
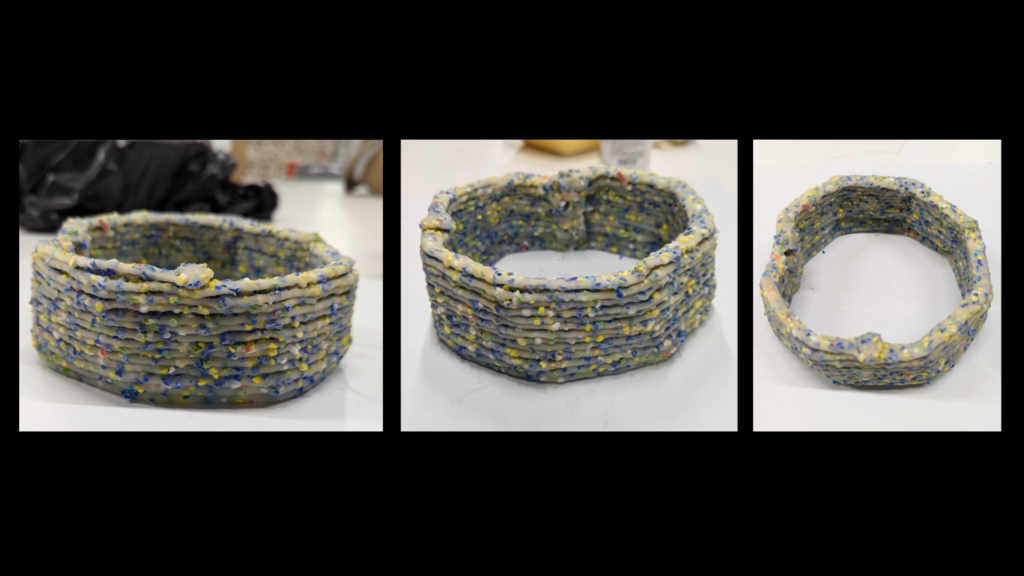
Another extrusion was done with PLA and hydrogel mixture to check its functionality.
The next step was identifying bacteria and plants that could help accelerate the degradation of PLA.
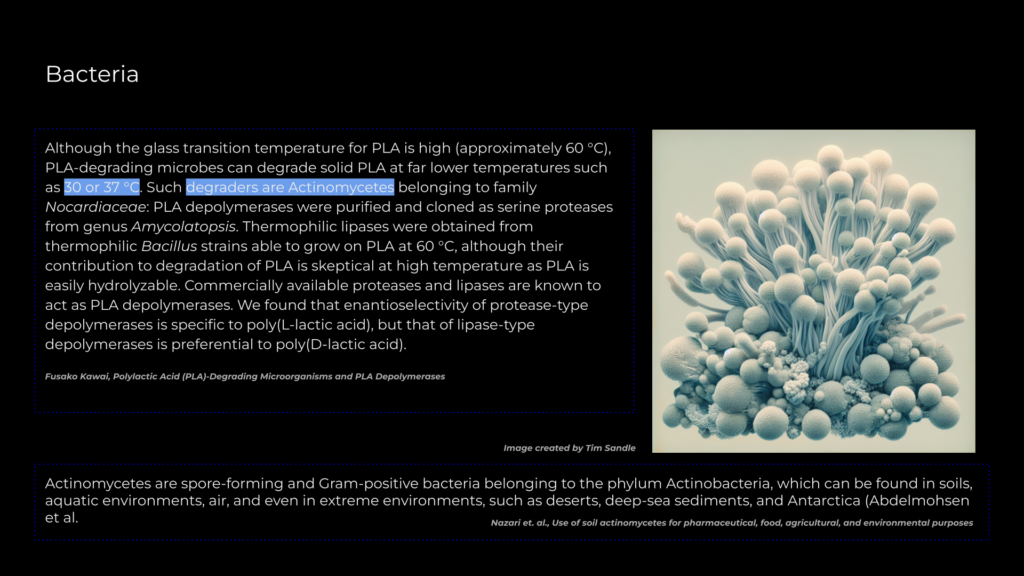
The bacteria identified as suitable for this project was Actinomycete, known for its ability to thrive in natural conditions. This group of bacteria is commonly found in soil and is known for breaking down complex organic materials. Its enzymatic activity makes it an ideal candidate for aiding in the degradation of PLA in a more sustainable and efficient manner.
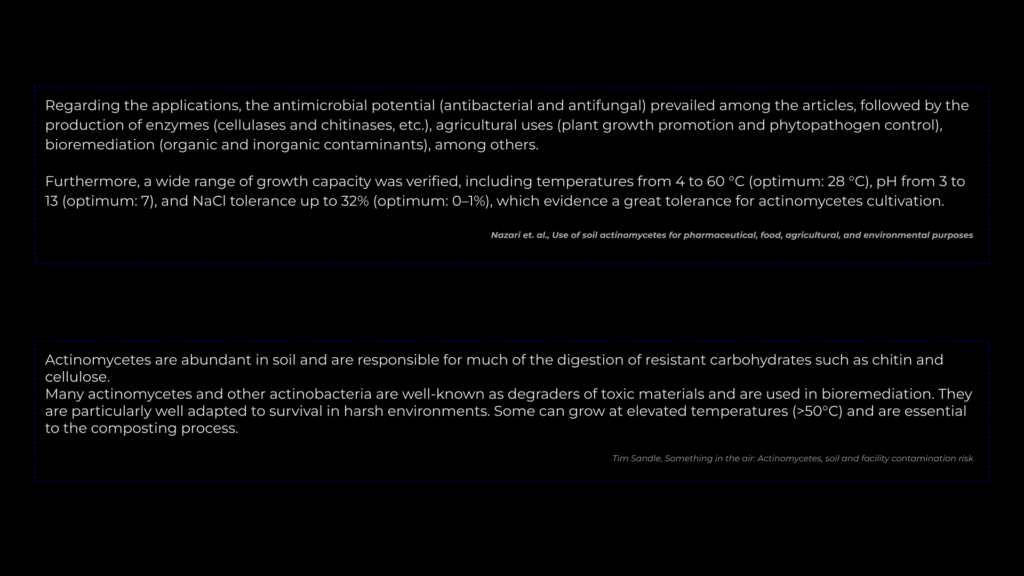
The identified plants have rhizobacteria in their roots, which play a crucial role in further degrading PLA. These bacteria form symbiotic relationships with the plants, enhancing their ability to break down the material through enzymatic activity and contributing to a more efficient degradation process.
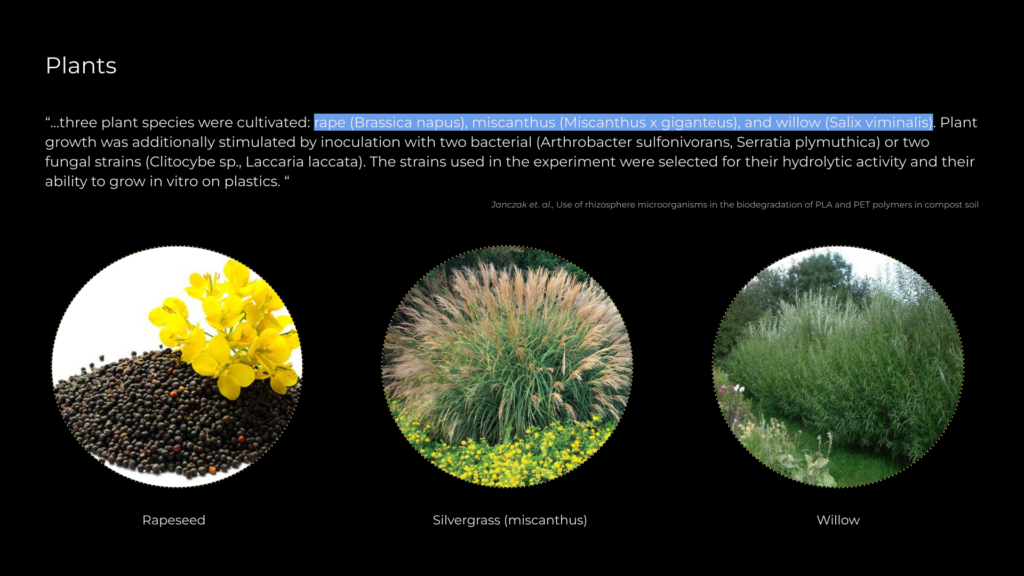
The next step was designing a geometry that would maximize the interaction between plant roots and PLA, enhancing the degradation process.
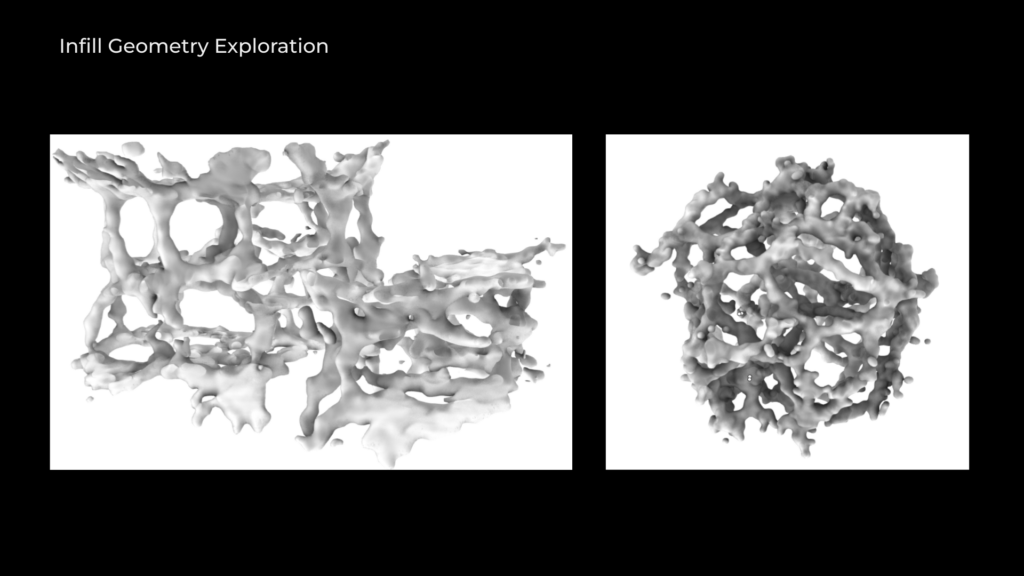
The initial geometries were inspired by materials commonly used in hydroponic systems. They were made porous to encourage better root interaction and material breakdown.
However, since these designs were extremely difficult to fabricate, I started exploring simpler geometric shapes.
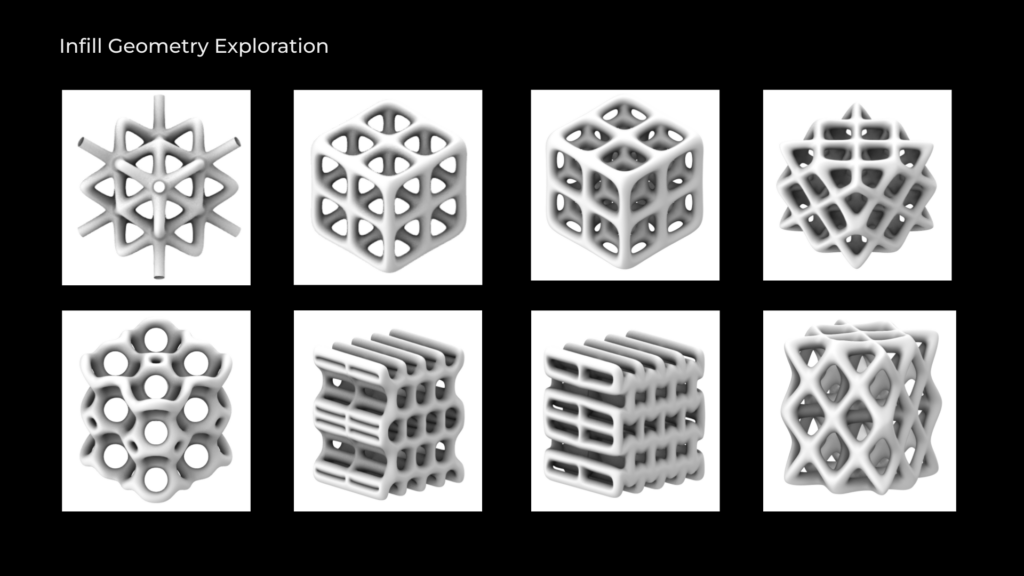
The overall design proposal drew inspiration from flower pots, focusing on simple and efficiently fabricatable shapes. Additionally, the polka-dot pattern of the material reminded me of Yayoi Kusama’s work, which led me to design metaball structures. These structures create a garden-like system that supports small-scale agriculture while enhancing the visual appeal.
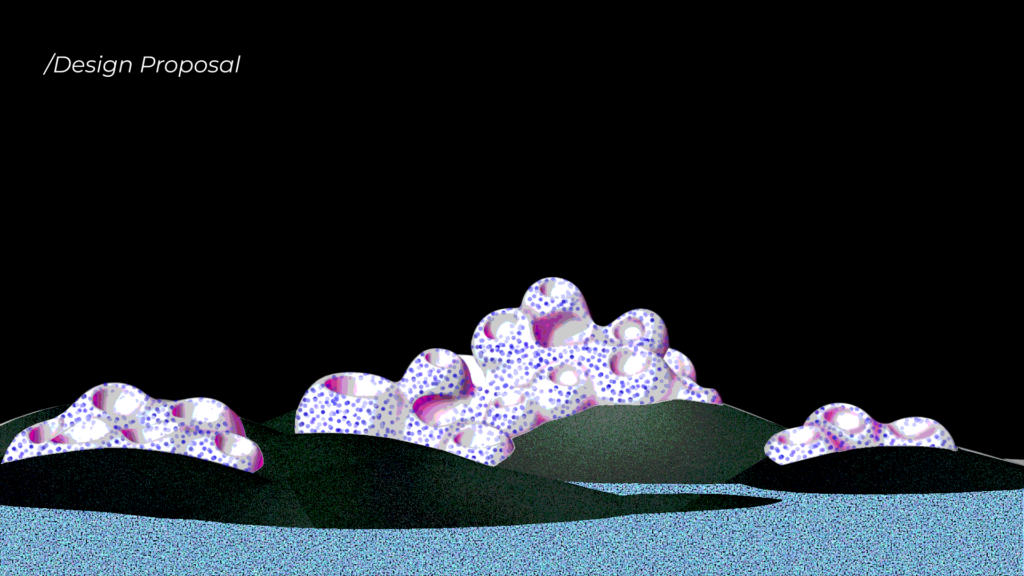
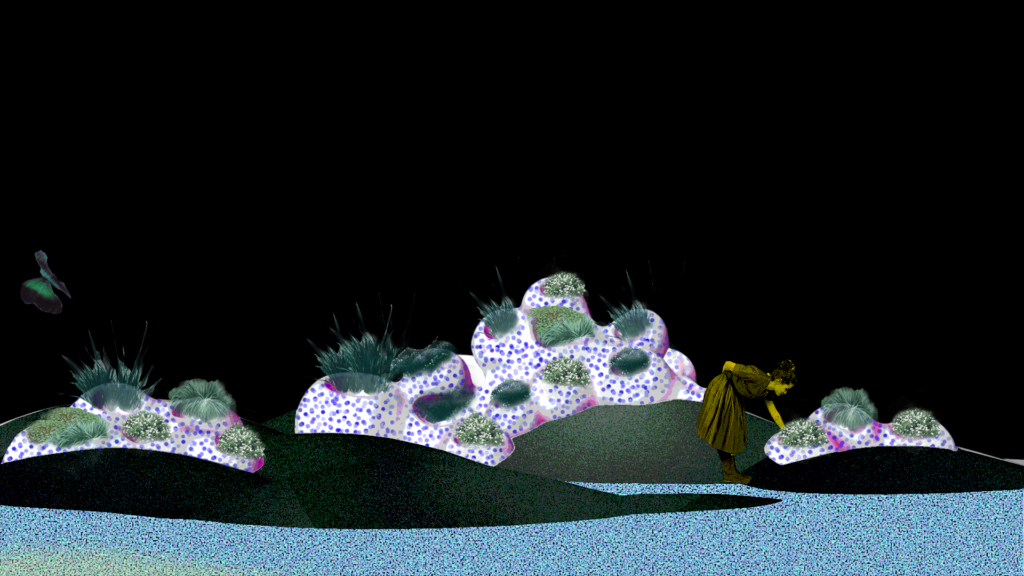
The concept behind these structures is that, as the material decomposes, they will become part of the earth, leaving no plastic behind. So that the system not only supports small-scale agriculture but also contributes to the natural cycle of degradation and regeneration.