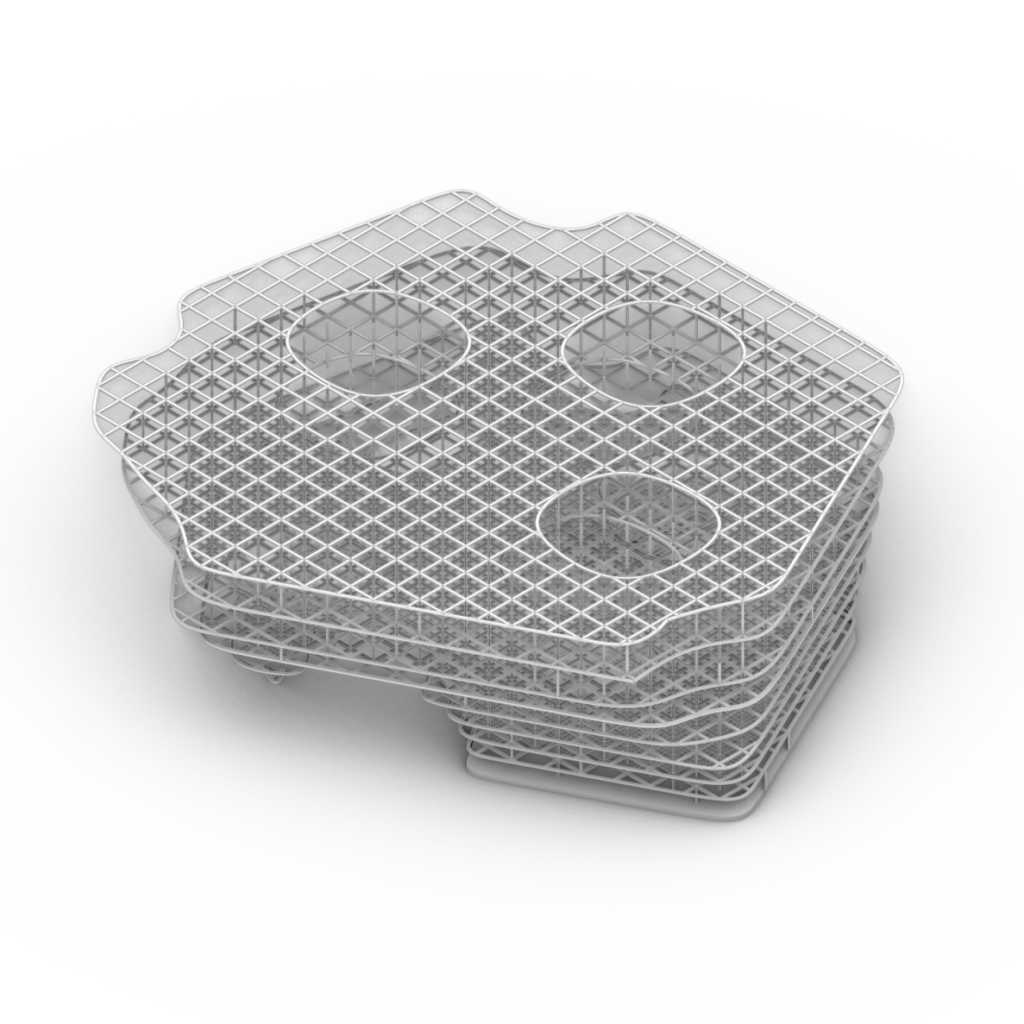
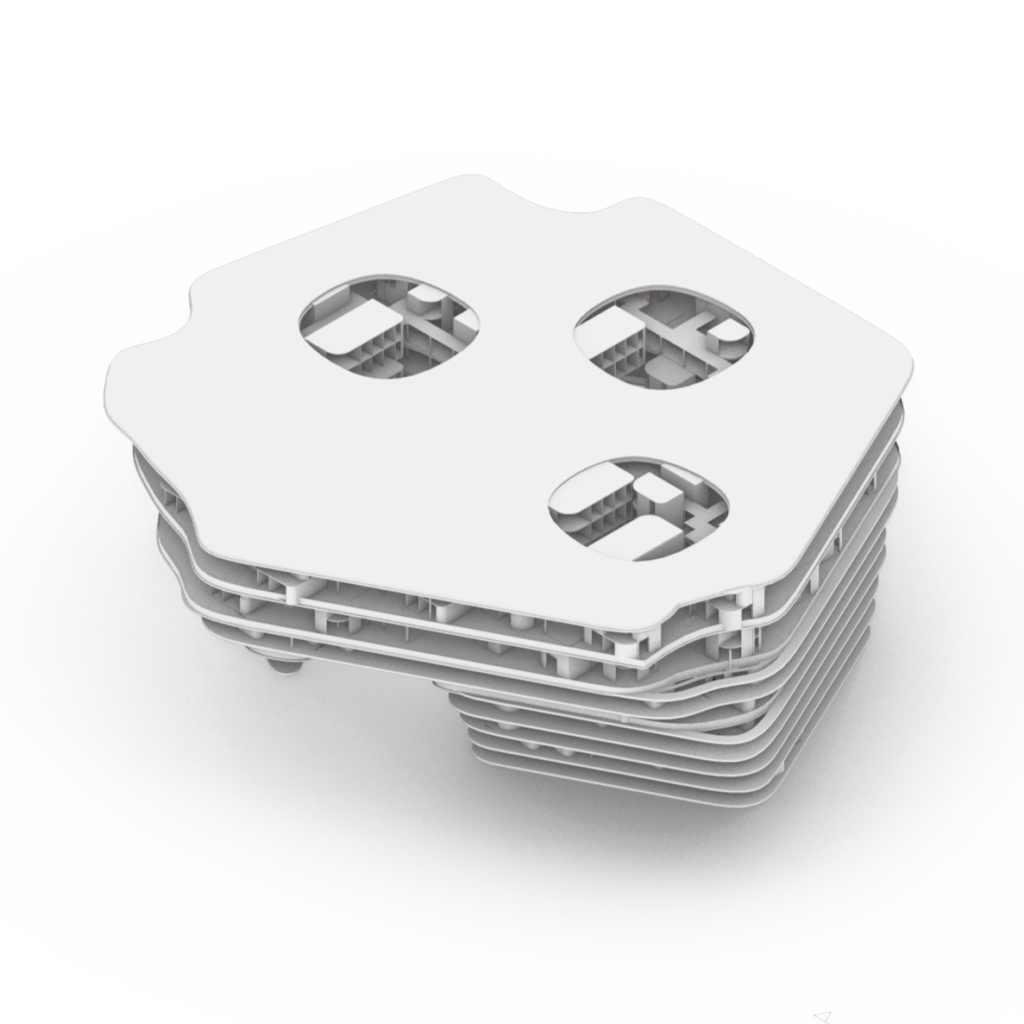
Our generative building is a mixed-use typology with height ranging from 4 to 12 stories. The primary design focus is to create a transformable and adaptable structure that can respond seamlessly to changing functional needs. To achieve this, the building incorporates lightweight, recyclable, and circular materials, paired with modular connection elements that allow for easy assembly and disassembly.
The core structural framework is based on a fixed 6m x 6m grid system, providing stability and uniformity. Within this grid, flexible partitions and components enable the transformation of the building’s interior and exterior spaces, ensuring versatility in its use.
The design also integrates a variable number of voids, strategically positioned based on the building’s location, solar exposure, and functional requirements. These voids enhance natural light and ventilation while contributing to the overall adaptability of the building, ensuring its long-term sustainability and usability. The structural system utilizes a mass timber construction approach, emphasizing sustainability, efficiency, and adaptability. The primary framework is composed of Cross-Laminated Timber (CLT) suspended floor slabs and modular partitions, seamlessly integrated into a fixed mass timber grid based on a 6m x 6m layout.
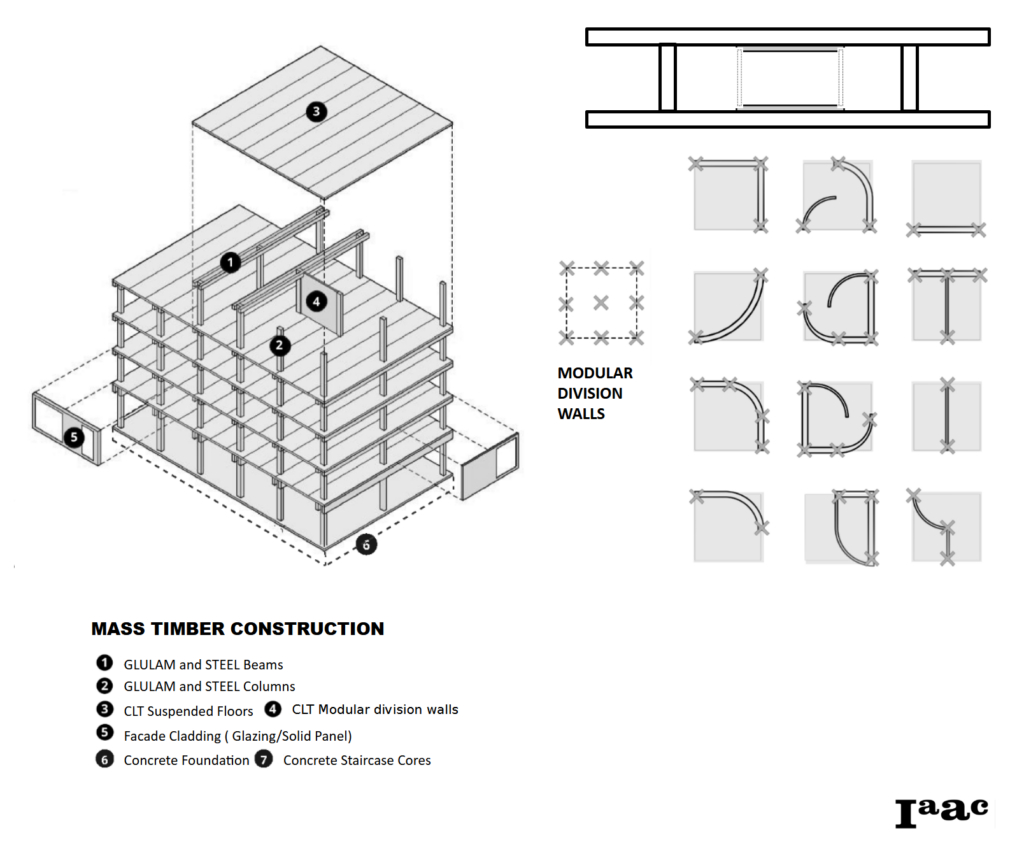
The structural system utilizes a mass timber construction approach, emphasizing sustainability, efficiency, and adaptability. The primary framework is composed of Cross-Laminated Timber (CLT) suspended floor slabs and modular partitions, seamlessly integrated into a fixed mass timber grid based on a 6m x 6m layout.
The floor slabs are securely anchored to the timber structural grid, providing stability and load-bearing capacity, while the divisions, designed as modular, lightweight elements, are locked directly into the floor slabs. This allows for flexible reconfiguration of interior spaces, aligning with the building’s ethos.
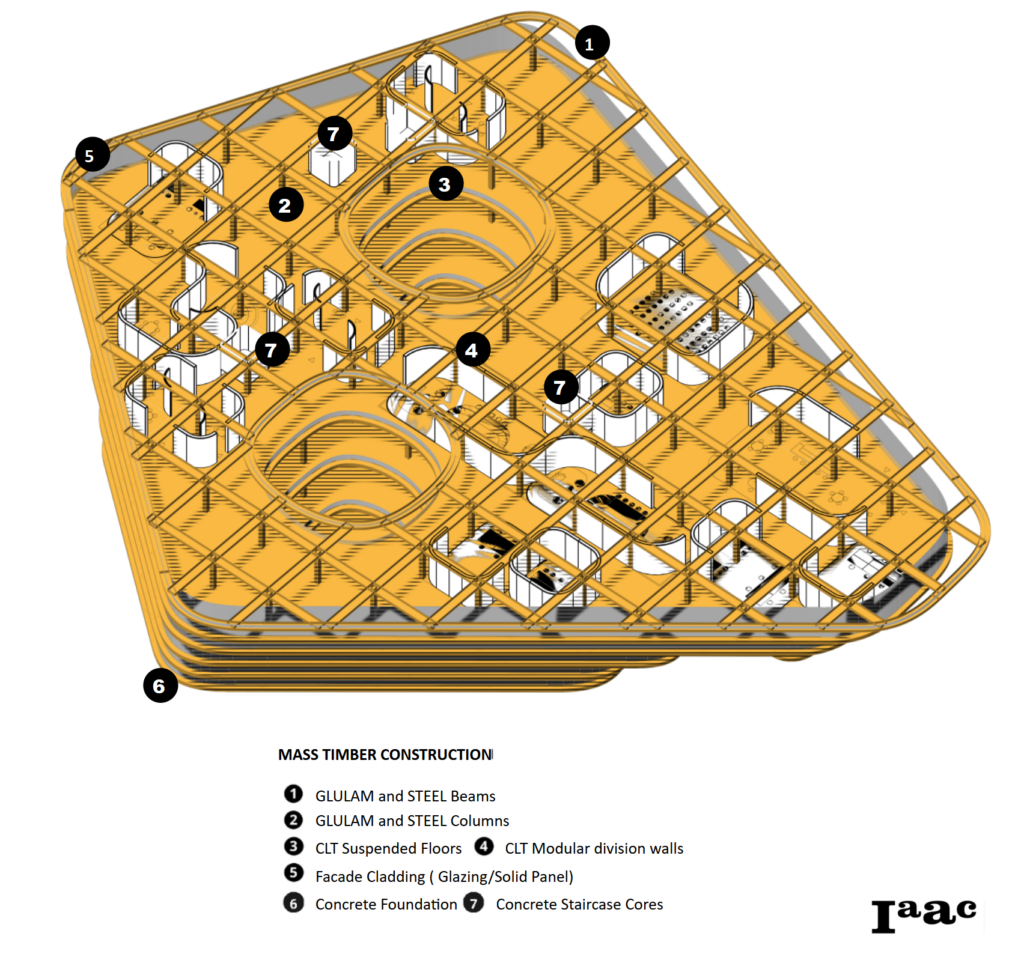
For additional structural integrity, the system incorporates concrete cores strategically placed to house vertical circulation (such as elevators and staircases) and provide lateral stability. The foundation is also constructed using concrete to ensure a robust base that supports the mass timber structure above.
This hybrid construction method combines the renewable and low-carbon benefits of mass timber with the strength and durability of concrete, resulting in a system that is not only sustainable but also highly adaptable to changing functional needs over time. The synergy between the timber grid, CLT slabs, and modular divisions reinforces the project’s commitment to lightweight, recyclable materials, efficient assembly, and long-term flexibility.
We used four load cases, dead, wind, live and gravity.
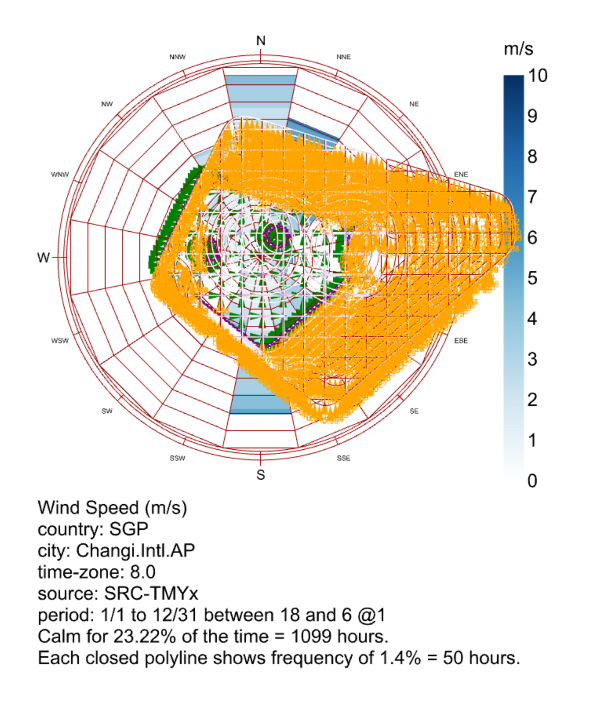
Singapore is our test location for wind loads with relatively low basic wind speed, ranging from 13-20 m/s.
Basic wind pressure qw: ~0.1 to 0.25 kN/m² for most scenarios.
For glulam, the dead load is 3 to 5 kN/m² for typical floors and roofs, considering structure and finishes. For light steel structures, 0.3 to 0.6 kN/m² per floor. For steel structures with typical floors and cladding: 4 to 6 kN/m².
DEAD LOADS: 4 kN/m²
WIND LOADS: 0.15 kN/m²
LIVE LOADS: 5 kN/m²
GRAVITY LOADS: 1 kN/m²
After calculating optimization for these loads, a Load Case Combinator was applied for collective displacement assessment, using SLS and ULS methods.
Our dead loads assume a mix of glue-lam, and steel structure. After calculating optimization for these loads, a Load Case Combinator was applied for collective displacement assessment, using SLS and ULS methods.
Before material and cross section optimization, we optimized the structural frame grid size, for our beams and columns, for the least displacement. A grid size of 9 meters square generated the best results with displacement values of 64 centimeters.
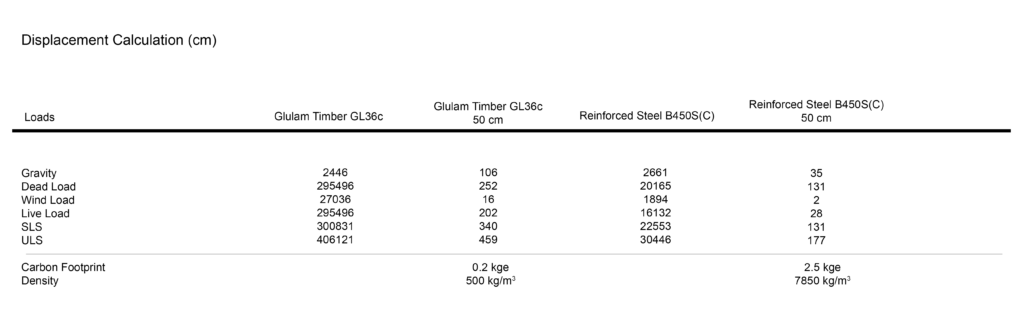
Application of Glulam Cross Section
Application of Reinforced Steel Cross Section
We applied the different loads to the structure, adding material thickness to decrease displacement. While steel shows a better control of the deformation than timber, it also has a higher carbon footprint equivalent and density. Using a mix of steel and glulam helps optimize these building standards.
We used varying cross section parameters to explore how different thicknesses would impact the displacement, focusing on the effect of gravity as the main cause of deformation.
Using the glulam and steel model, we gave Opossum the parameters attached to our cross sections to experiment with element utilization. The load displacements did not shift as we chose to keep the values as close as possible to the original. We chose to go with an 80% utilization to not have our elements constantly at full capacity and to allow more flexibility with our loads.
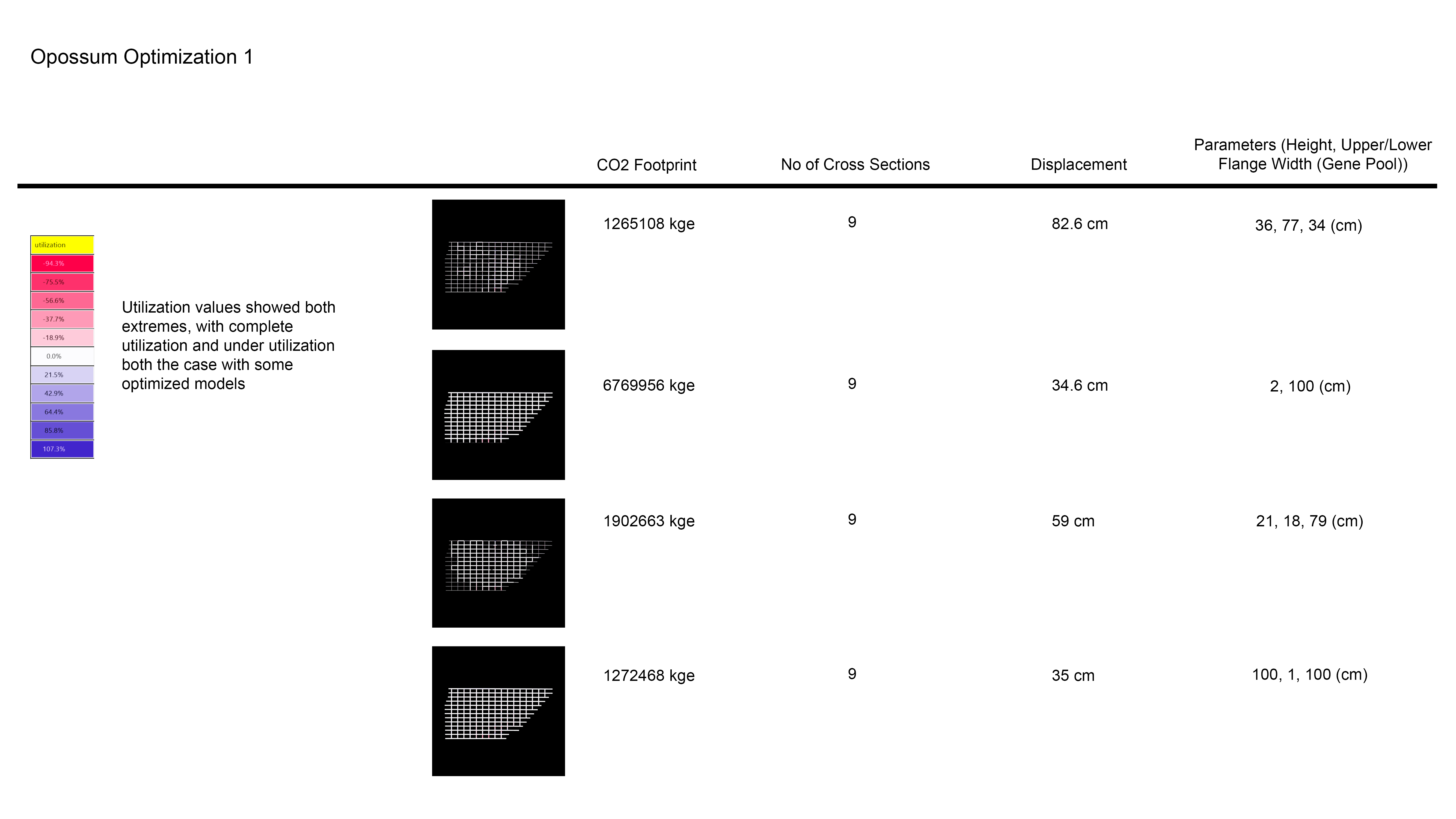
Once we achieved the right efficiency, we applied Opossum to the model with a multi-objective optimization process to compare values of carbon footprint and displacement with respect to the quantity of cross sections. Here we see how a lower value of displacement can significantly impact the carbon footprint of the structure, with some parameters making more construction sense than others.
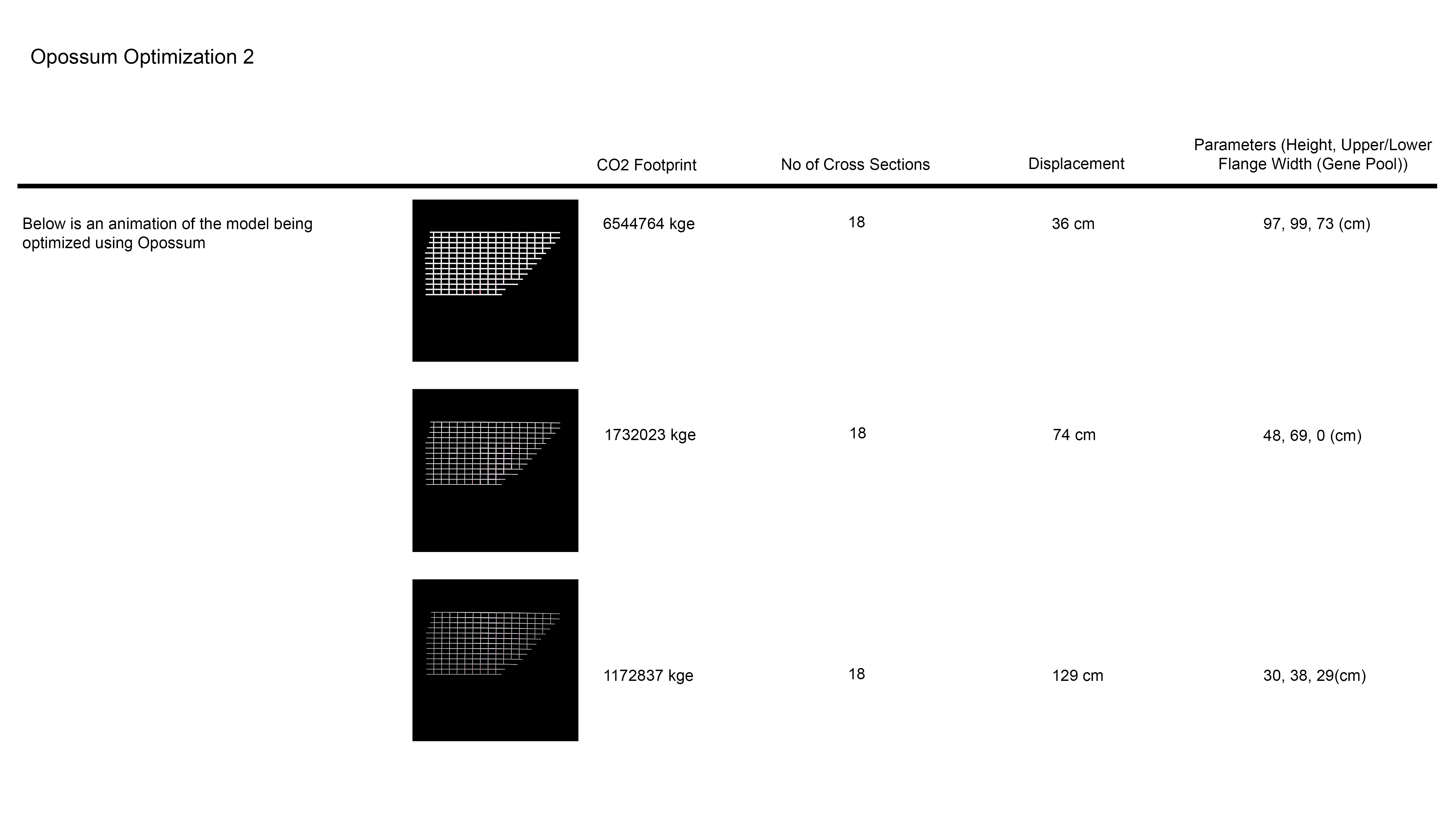
Our second multi-objective optimization included the use of 18 different cross sections alternating between three different parameters. We selected parameters from our earlier optimization to avoid the extremes shown here.