3D Concrete Printing (3DCP) is reshaping the construction industry by combining innovation and sustainability. This cutting-edge technology involves the automated layering of concrete through robotic systems to create durable, customized structures efficiently. The process integrates components like robotic arms, nozzle systems, and advanced computational control to deliver unparalleled precision and speed.
How Does It Work?
The 3DCP process begins with raw materials like cement, aggregates, and water, combined using a mixer to form mortar. A pump then transfers this mortar through a nozzle controlled by a robotic arm to construct structures layer by layer. Key components like electricity, water supply, and computer-aided control systems ensure streamlined operations.
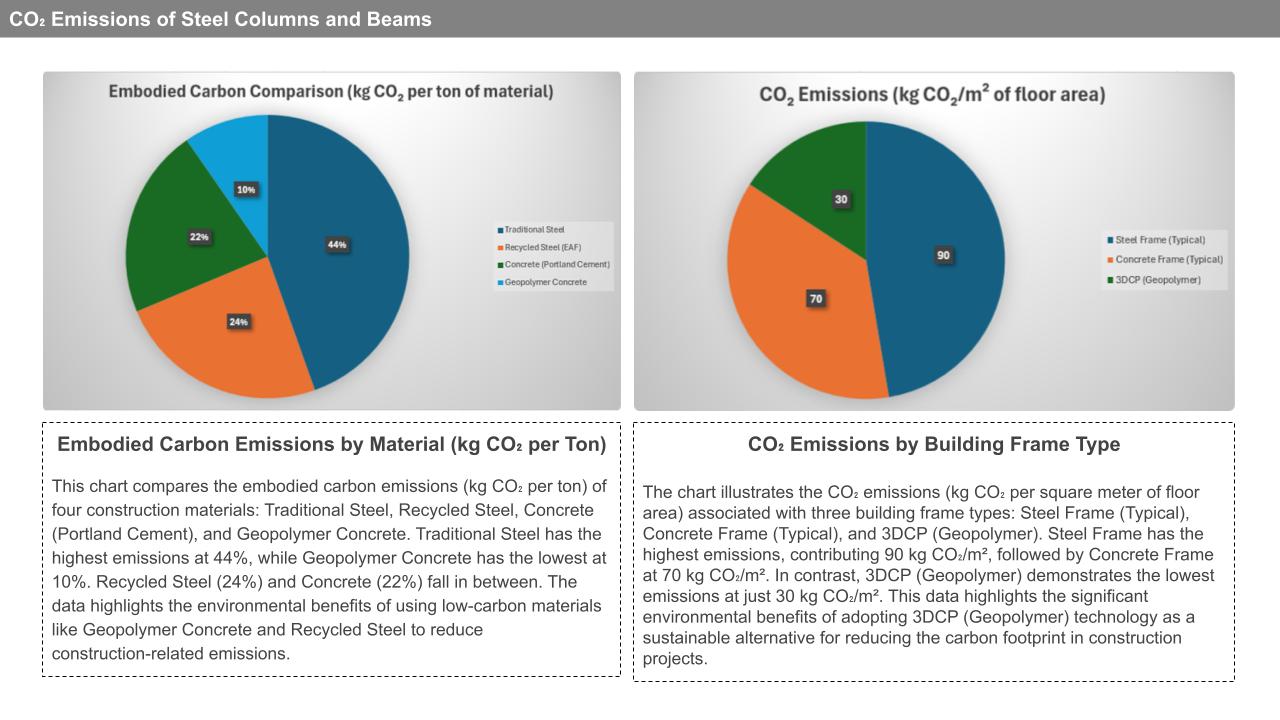
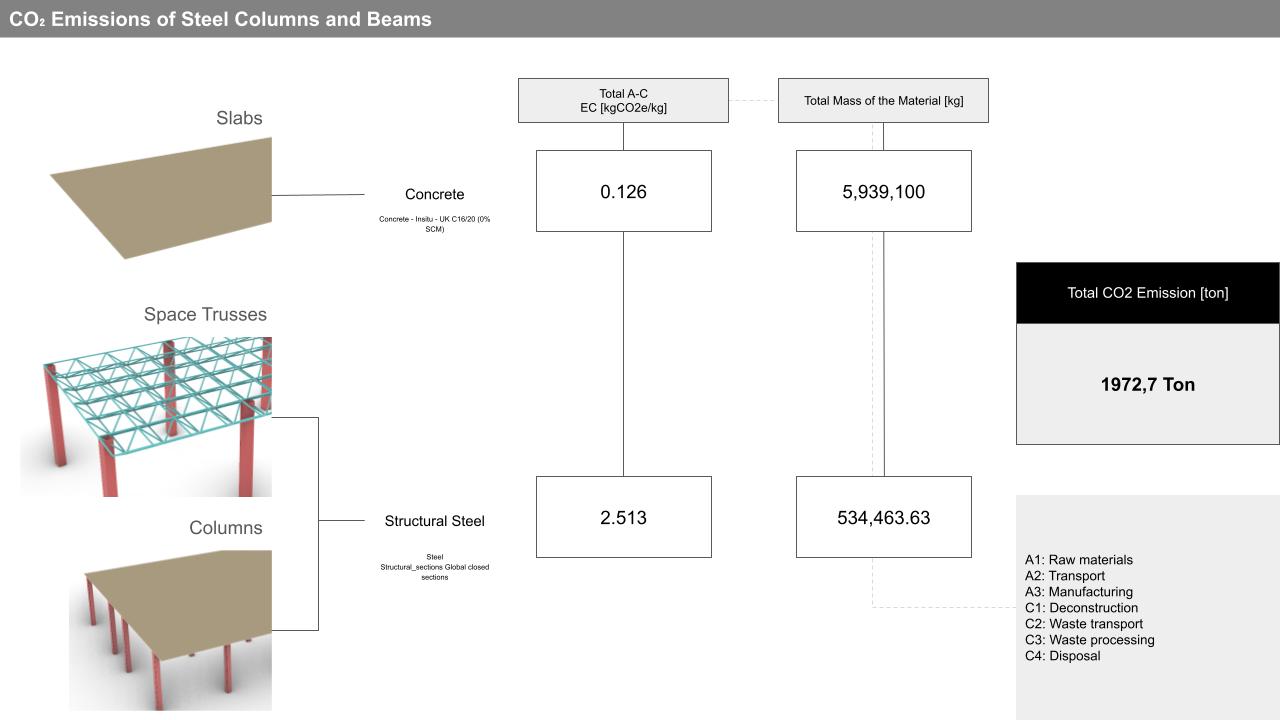
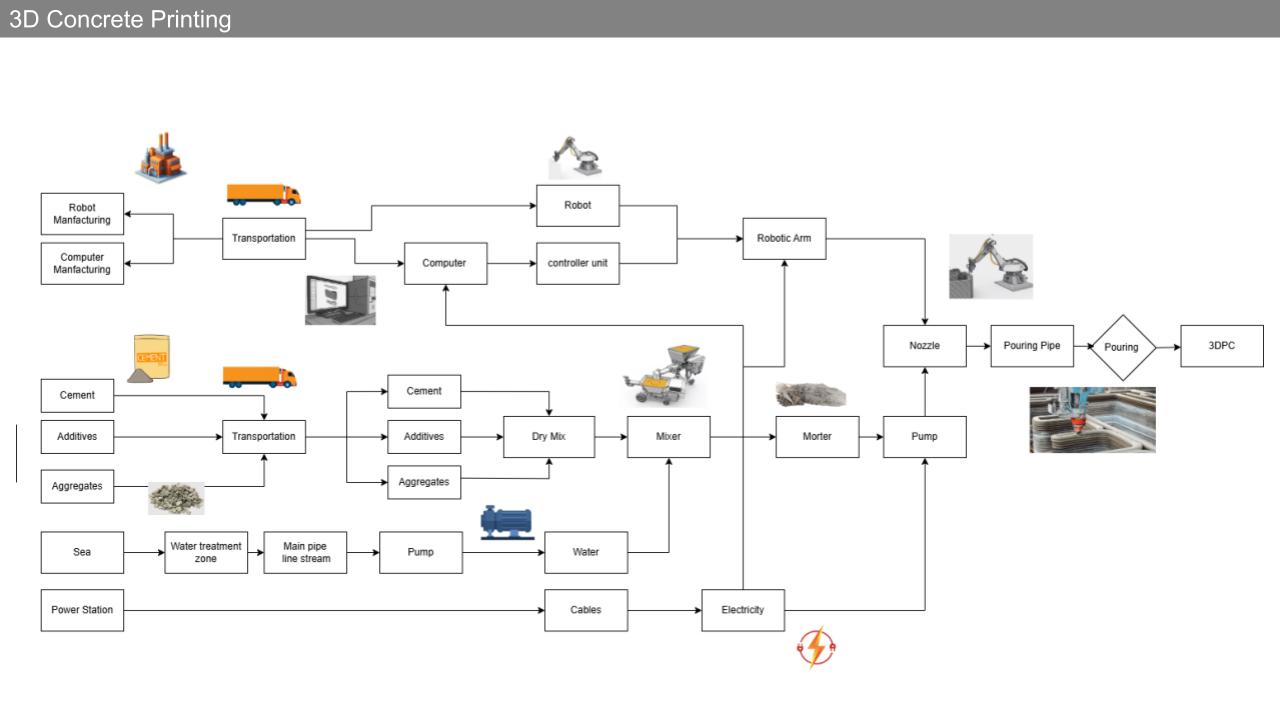
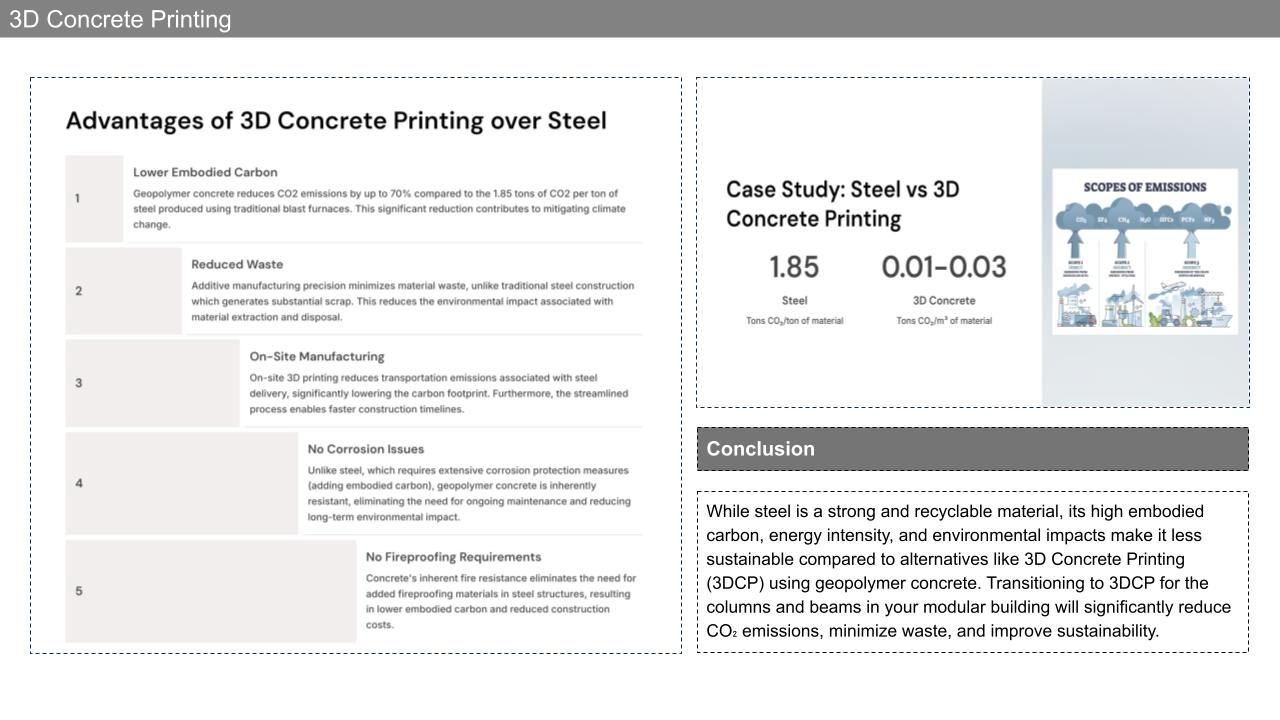
Steel has long been a cornerstone of construction, offering strength and recyclability. However, its high embodied carbon and energy intensity make it less sustainable. 3D Concrete Printing, especially using geopolymer concrete, is emerging as a viable alternative to steel structures. With its lower emissions, reduced waste, and efficient on-site manufacturing, 3DCP paves the way for a greener future in construction.
Adopting 3DCP for beams and columns in modular buildings can significantly cut CO₂ emissions, minimize waste, and improve overall sustainability. The choice is clear: embracing 3D printing technology is not just a step forward in construction innovation—it’s a leap toward a sustainable tomorrow.