Exploring the Intersection of Subtractive and Additive Manufacturing
In the pursuit of challenging manufacturing norms and pushing the boundaries of creativity, our team delved into the intricate world of stack lamination during the recent workshop. Focused on creating functional and visually stunning furniture pieces for a potential cafeteria in Barcelona, our journey unfolded through three unique design proposals, with one stealing the spotlight – a mesmerizing twist in wood forming a side table.
Table Design
Base Geometry Design
The base geometry, resembling an arrow, was intentionally designed with challenging twists and turns, introducing undercuts that added complexity to the manufacturing process. The aim was to create a piece that goes beyond conventional boundaries, requiring the precision of a robot arm for realization.
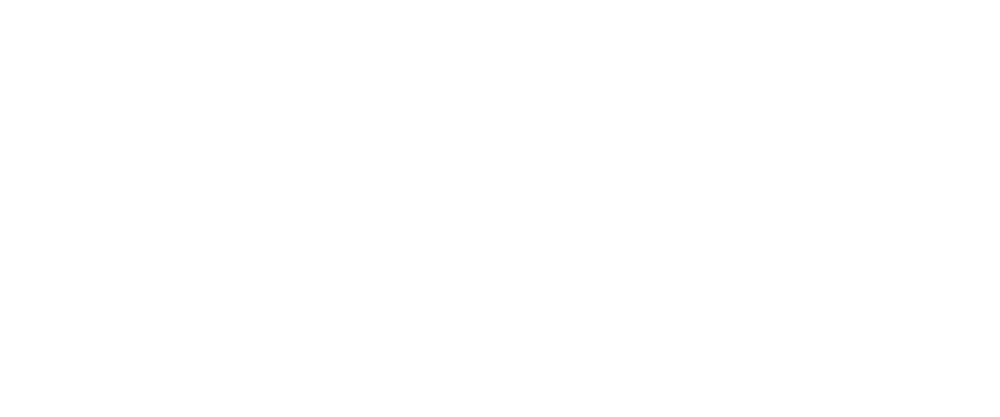
Table Dimensions
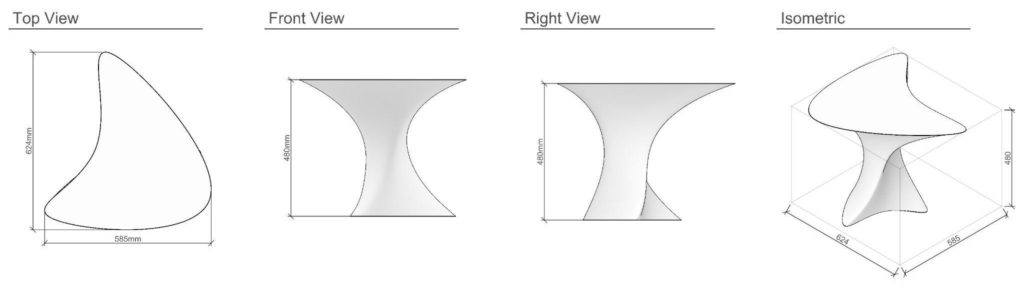
Fabrication Strategy
The process involves the construction of a substantial volume of material using sheet stock, typically plywood or similar manufactured boards. These boards are CNC machined and stack laminated into blocks that approximate the shape of a larger form. Subsequently, the pieces undergo 3D robotic milling, and finishing.
Nesting for CNC
Each piece is precisely aligned and nested with the help of ‘Open Nest’ in grasshopper. The challenge lay in the unique twists of the design, making the nesting process a critical factor. The CNC operations involved a step-over of 15 millimeters and a tool diameter of 20, with four passes to achieve the desired finish.
With Grasshopper guiding the slicing process, each piece was meticulously labeled for efficient assembly. Despite the challenging twists, our team successfully utilized nesting techniques to optimize the use of a single sheet of plywood.
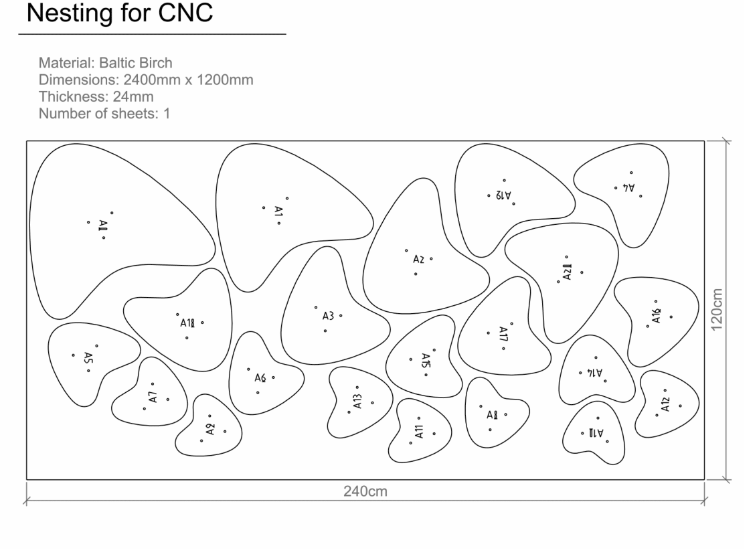
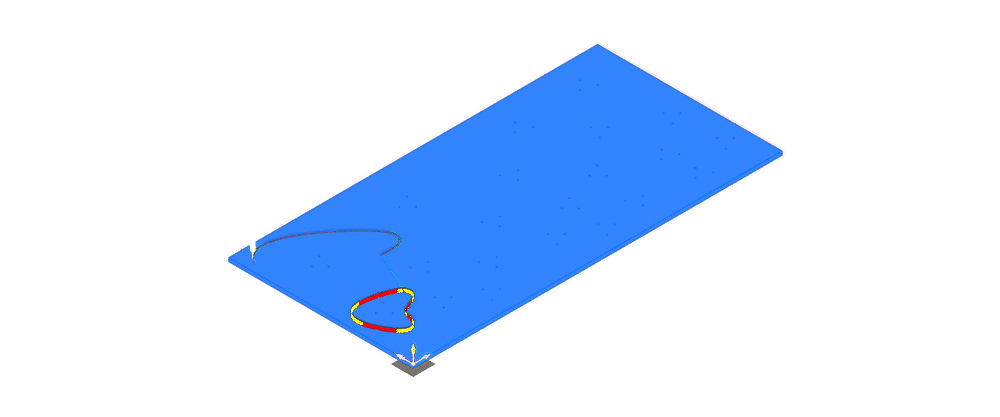
Stacking Layers

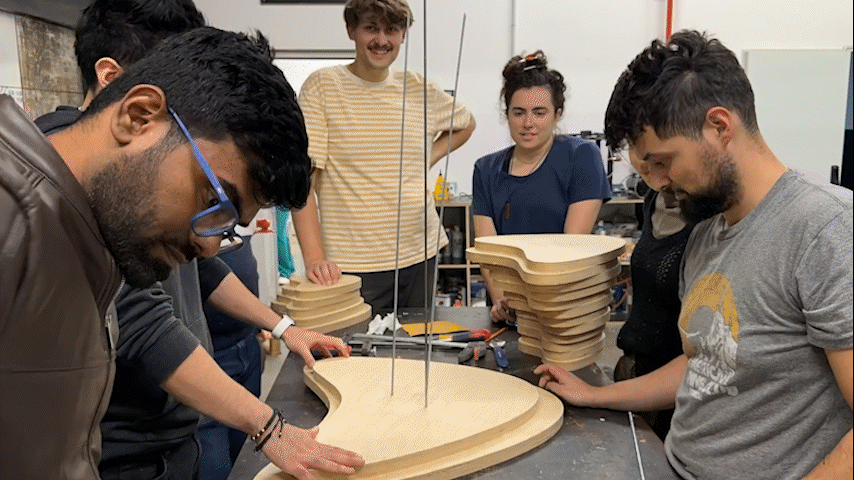
Robotic Setup
A five-axis robot, driven by the geometry generated in Grasshopper, was employed for the slicing process. The robot executed the intricate cuts, transforming the stacked pieces into a cohesive and captivating table. The robotic fabrication strategy involved a flat-end tool, emphasizing simplicity. The simulation phase proved crucial in preventing collisions, highlighting the significance of precise glue-up. Although the real-life outcome deviated slightly due to inherent inaccuracies, simulations served as invaluable testing grounds.
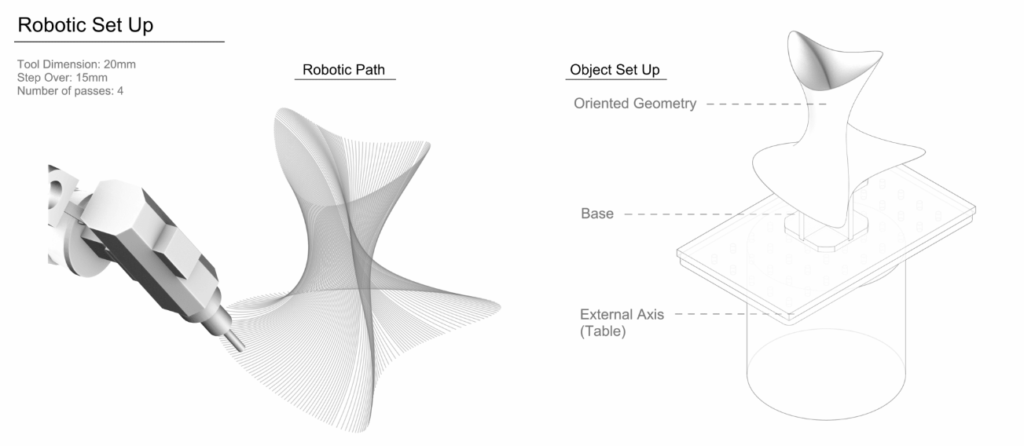
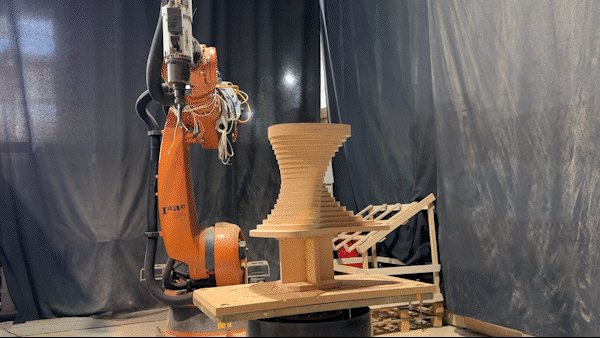
Prototype and Final Design
The resulting side table, with its arrow-inspired twists, not only fulfills the functional requirements of a cafeteria but also creates captivating shadows when illuminated. Our documentation process captures the essence of the design iterations, CNC operations, and the challenges overcome during fabrication.
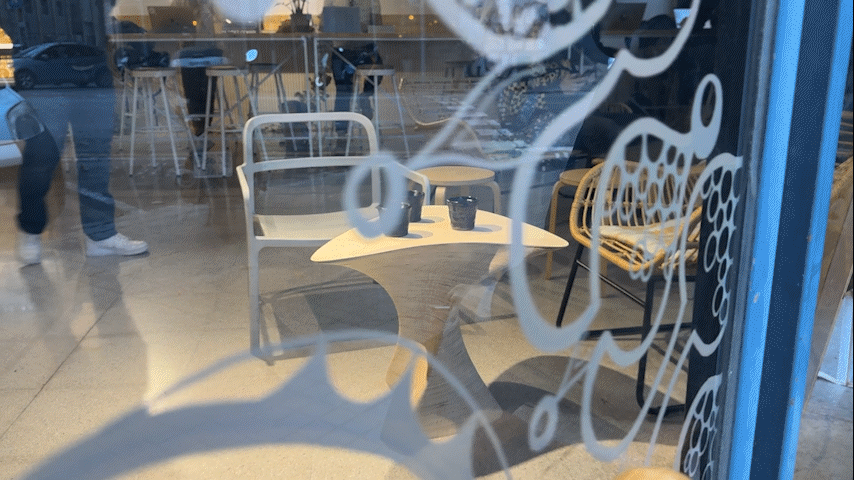
Further Work and Development
Looking ahead, our team envisions exploring the possibilities of incorporating lights within the table, experimenting with hollow spaces for nesting different-sized pieces. This forward-thinking approach aims to minimize material usage and waste, fostering sustainability while creating visually intriguing furniture.
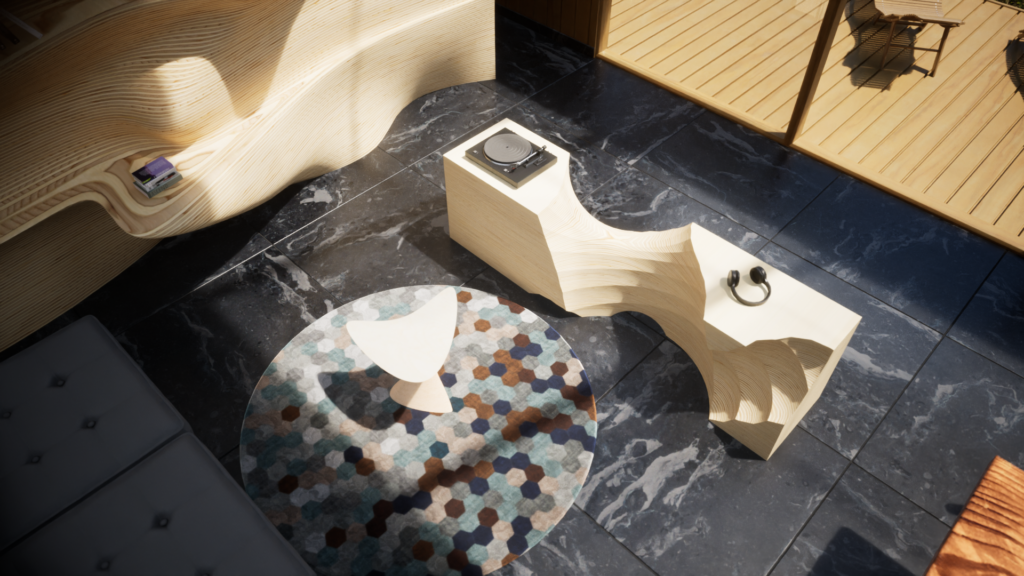