From exterior soil remediation to interior acoustics enhancement
The goal of this project is to create a non-cementitious geopolymer, using as the main component biochar, an worldwide abundant material, and amplify its qualities to sequester carbon in order to make carbon sink architecture. Through the process of material engineering and testing, it was possible to create designs that incorporate the multiple qualities biochar has, among them: heat insulation, humidity retention and most importantly acoustics enhancement. The proposal introduces the opportunity of utilizing biochar and transforming its current state into architecture pieces, such as bricks, panels, and facades.
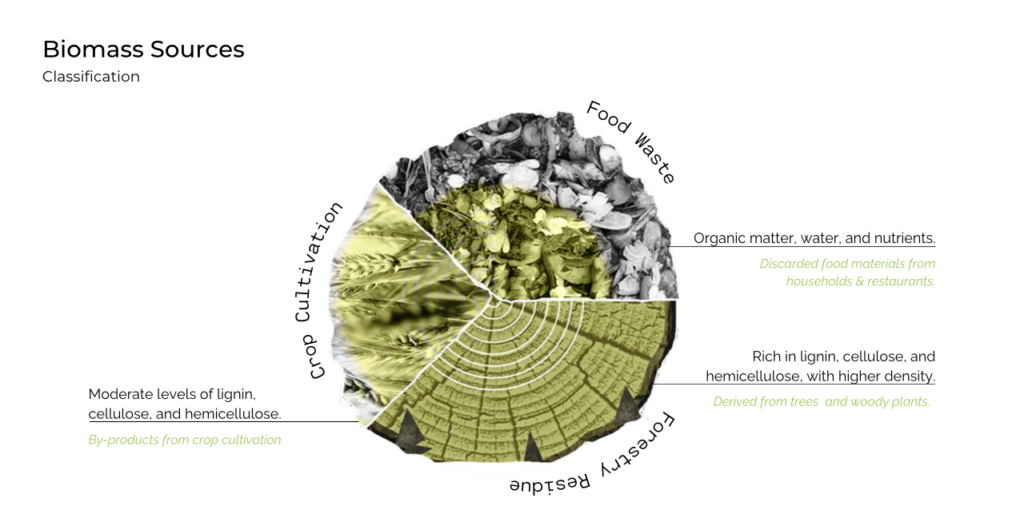
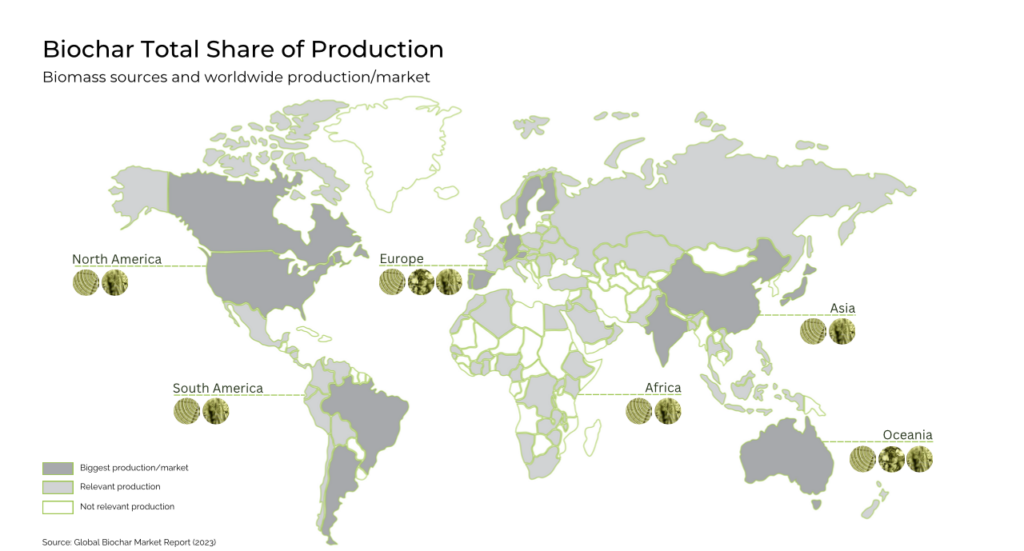
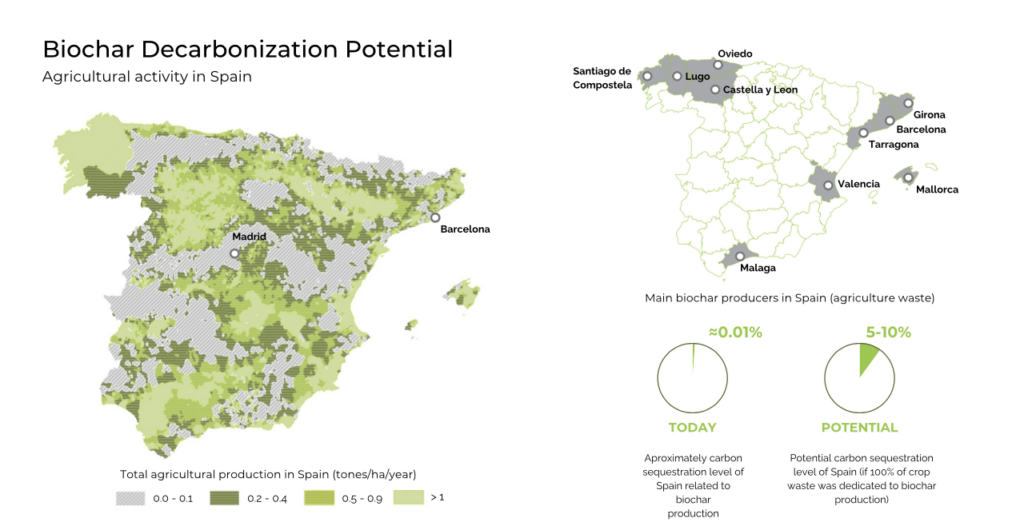
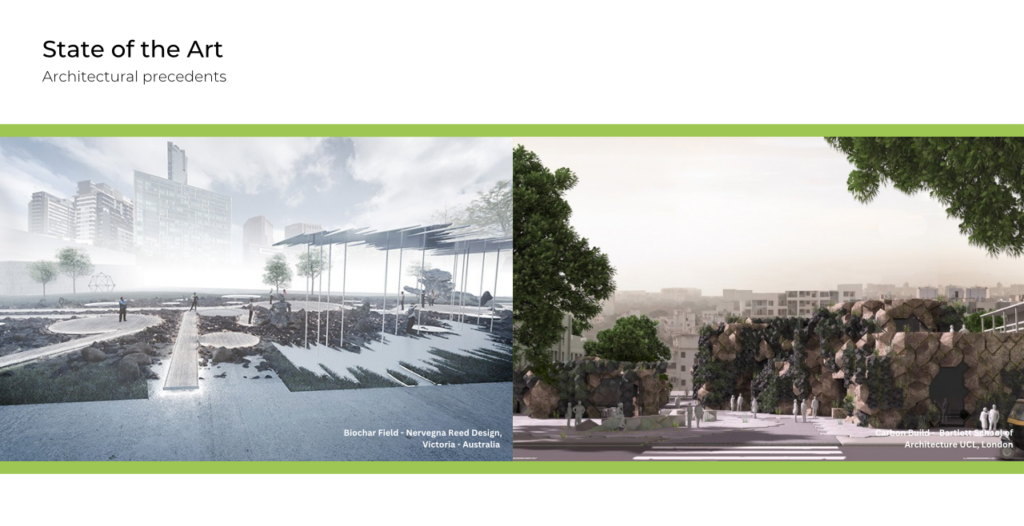
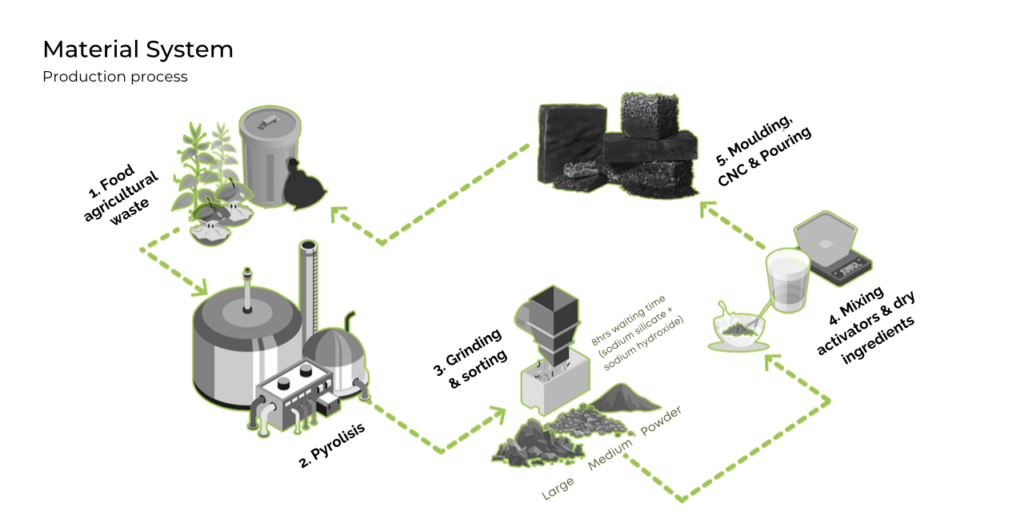
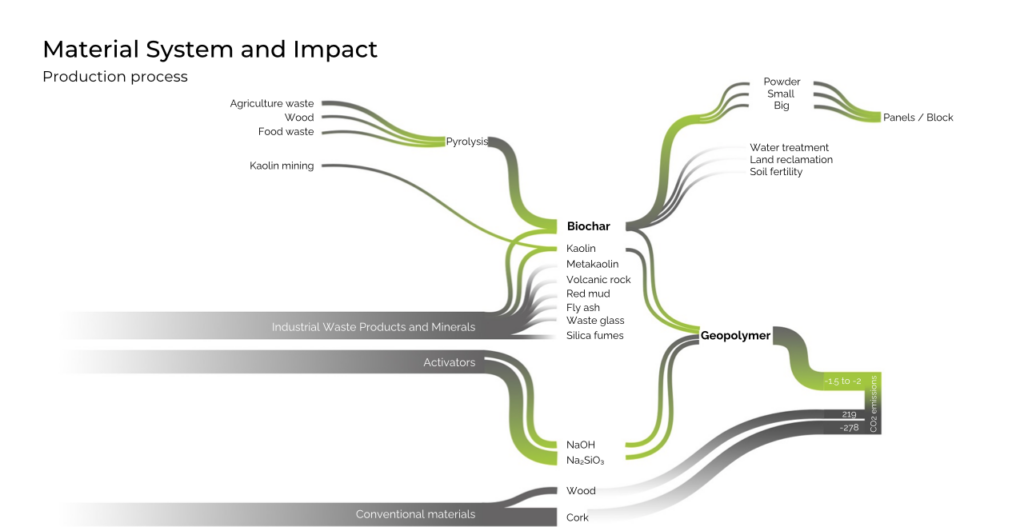
Initial Prototypes
Different brick sizes, testing shapes and geometries, and also big, medim and small biochar particles to understand the performances.
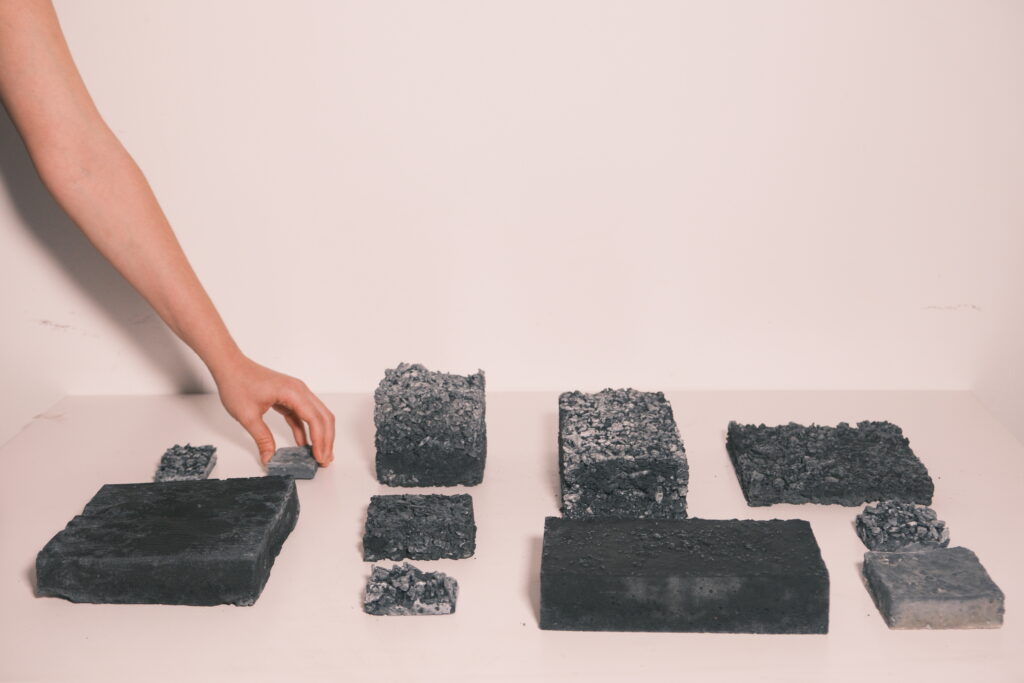
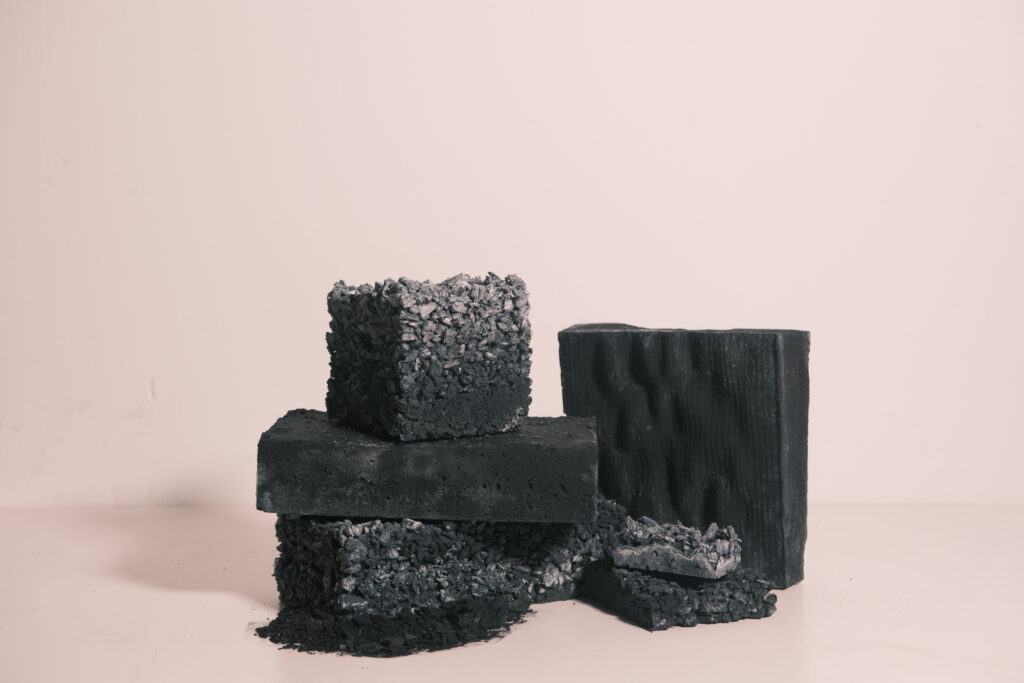
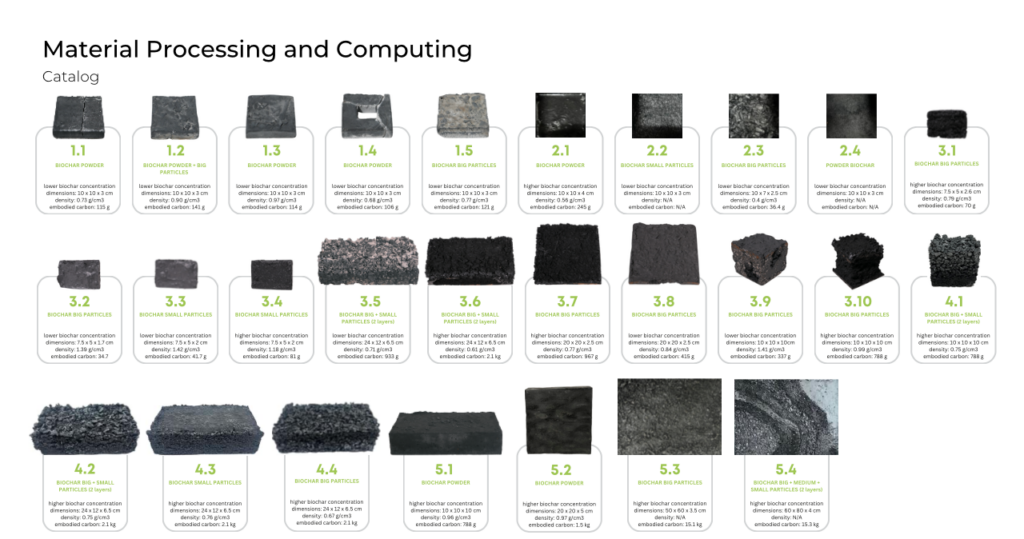
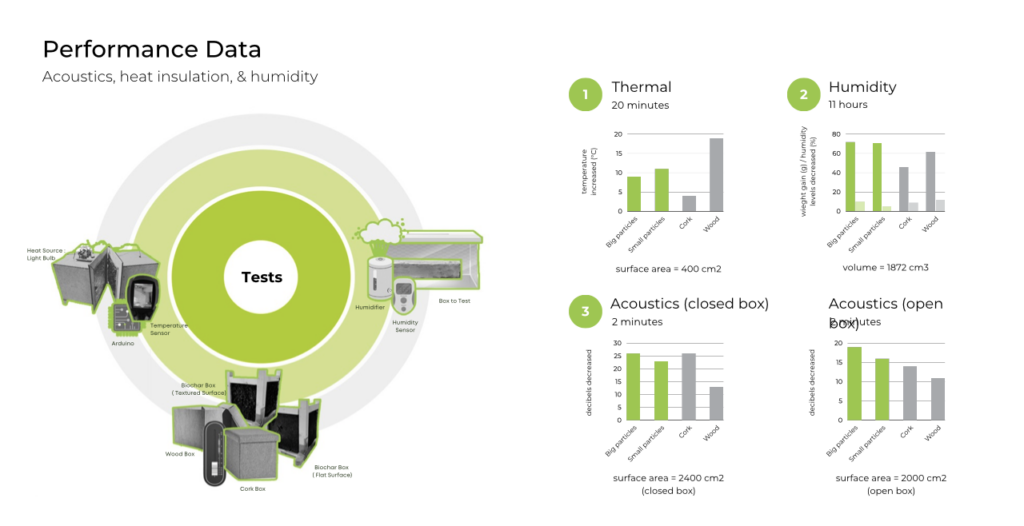
Through the process of prototyping and experimenting, it was possible to test 2 main things, the concentration of biochar in the recipes and the particle sizes. From the 4th round of prototyping until the last one, the focus was maximizing the concentration of biochar, being able to find a good ratio for a balanced recipe to make the prototypes strong and durable, and at the same time lighter and with increased amount of embodied carbon. As for the particles, the conclusion is that by using bigger particles the prototypes are less dense and with a maximized surface area, and turned out to be better performers when it comes to absorption: humidity, heat and sound, and also reducing the need to pre-processing and energy consumption to grinding.
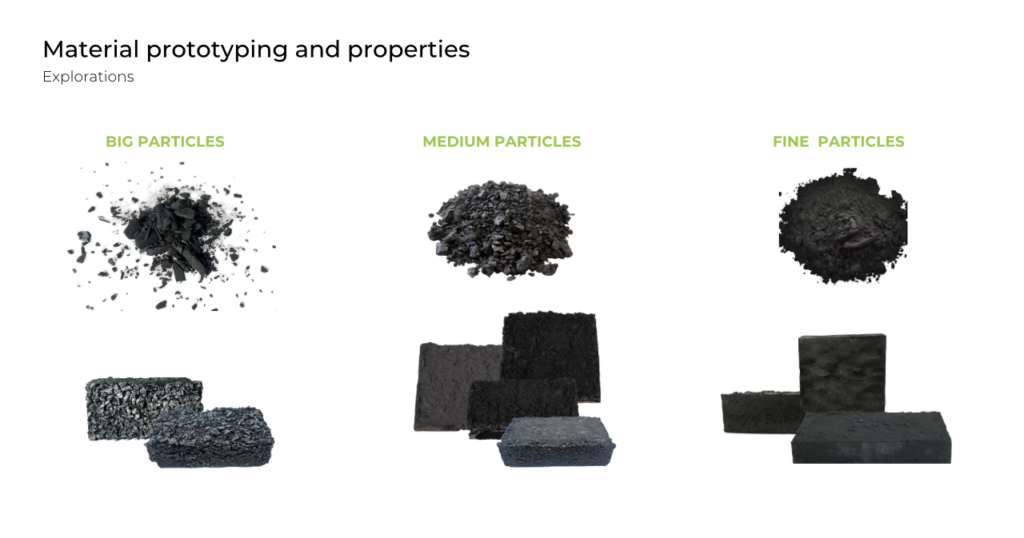
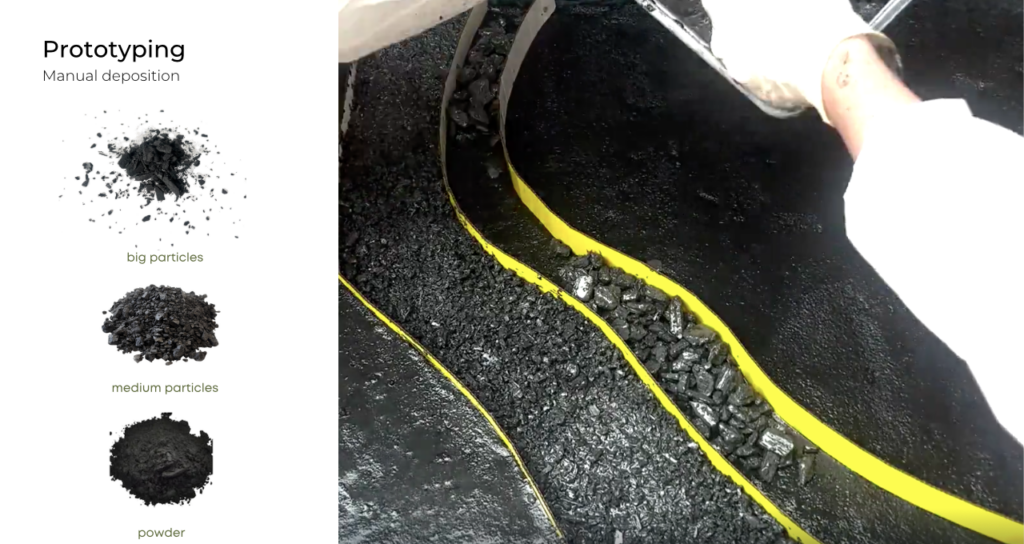
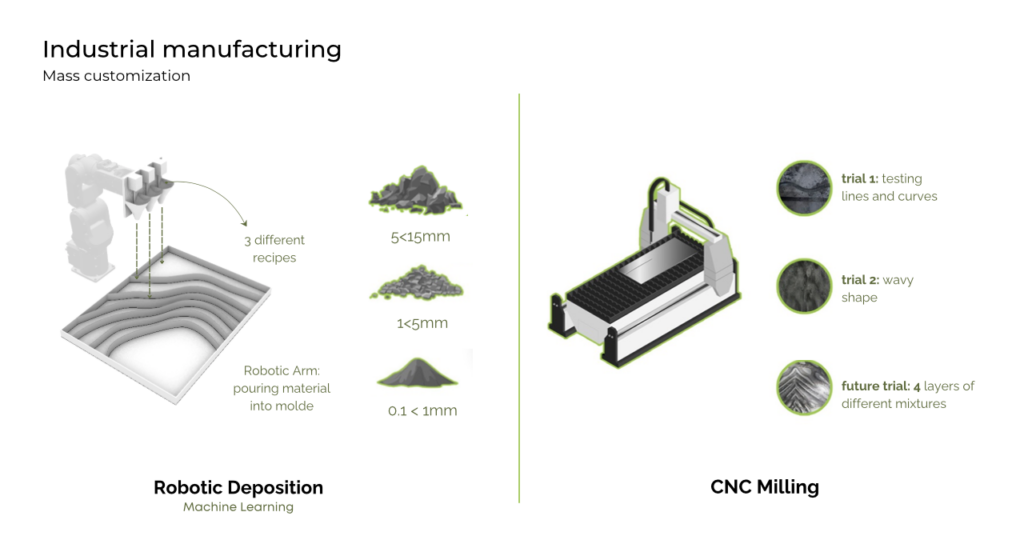
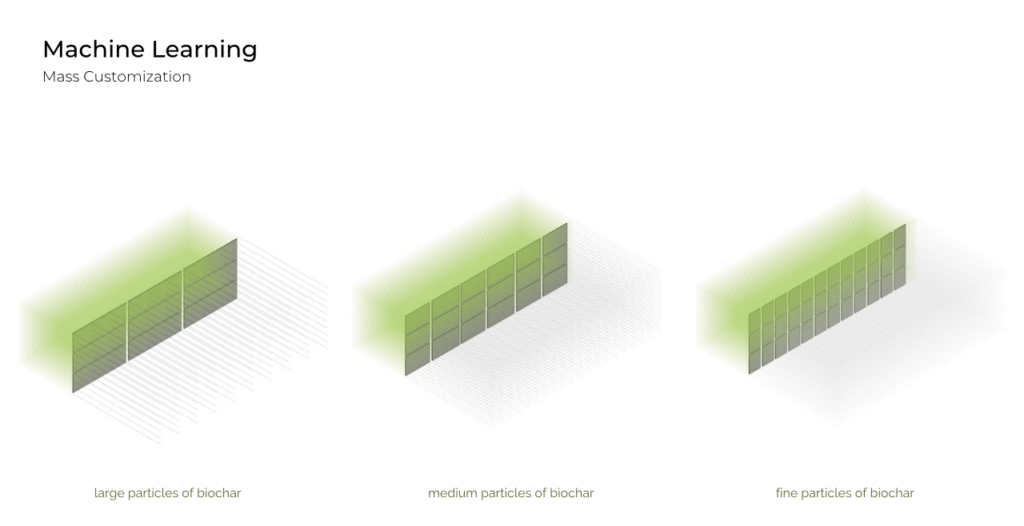
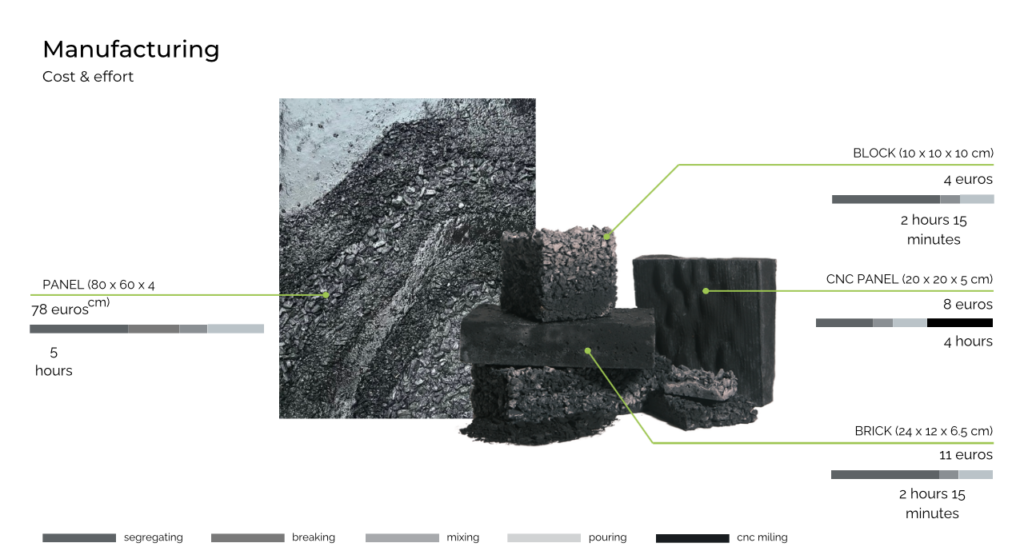

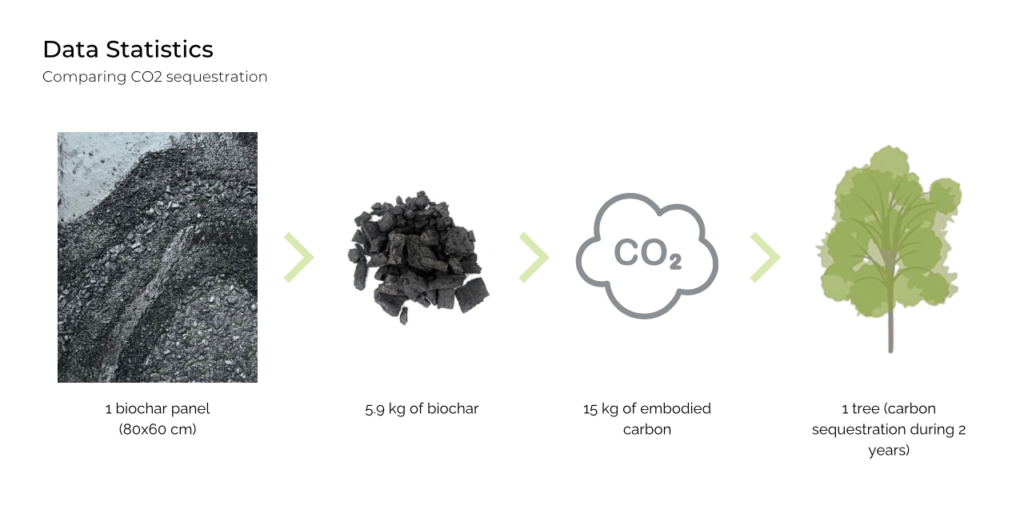
An interesting comparison to be made is the equivalence between the embodied carbon in a biochar panel, for example, and the capacity of carbon sequestration of a tree during its lifetime. One tree has the ability to sequestrate 880 kg of carbon its whole life, the equivalent of 338 kg of biochar. Per panel, there is approximately 5.9 kg of biochar, meaning that it has 15 kg of embodied carbon, the equivalent of what a tree can sequestrate in a period of almost 2 years.
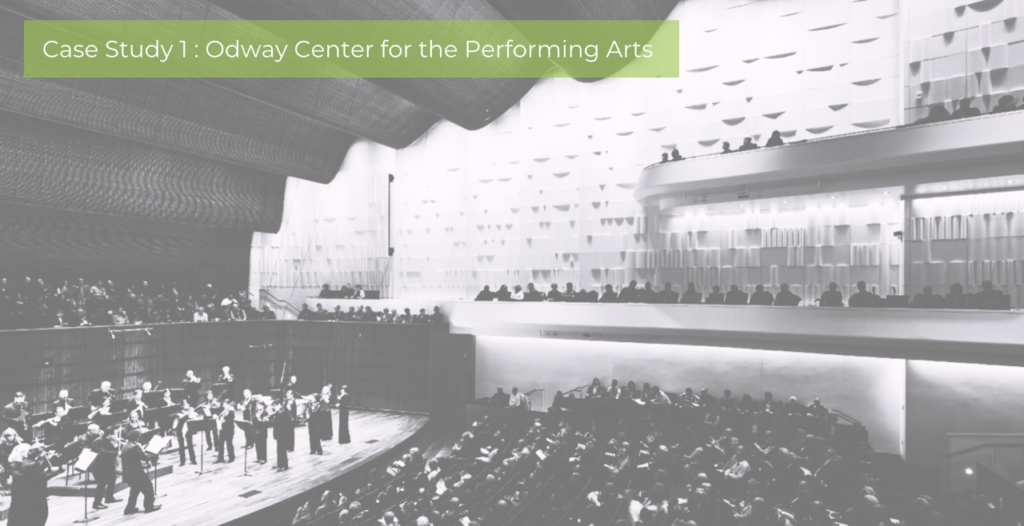
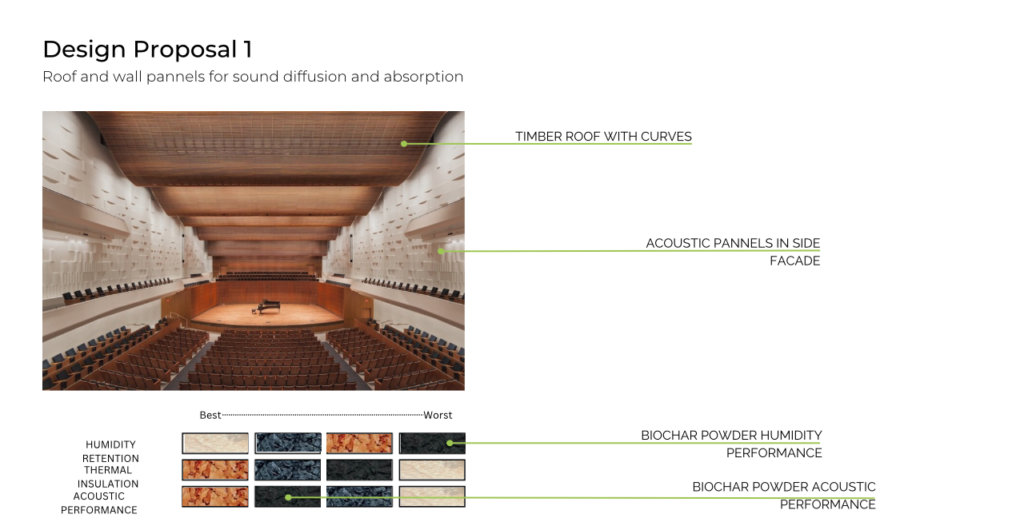
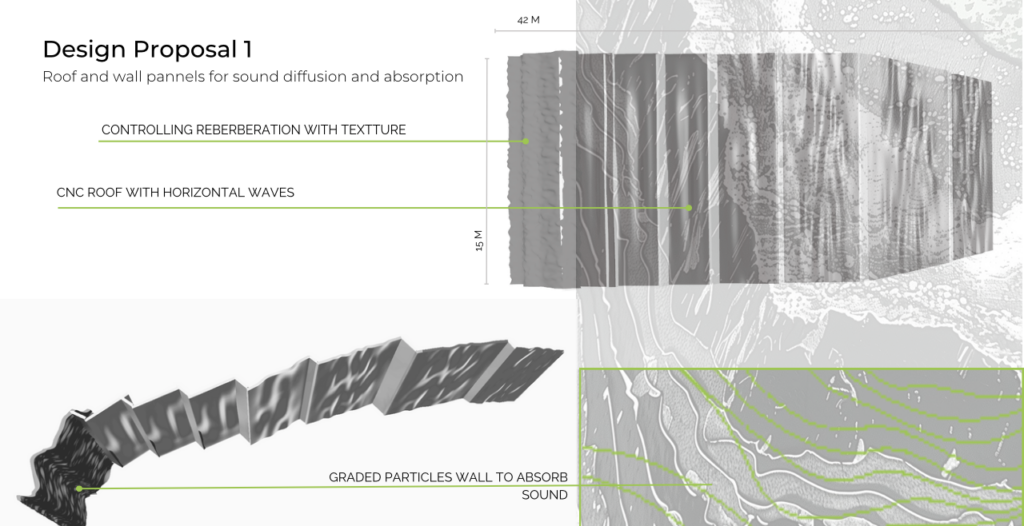
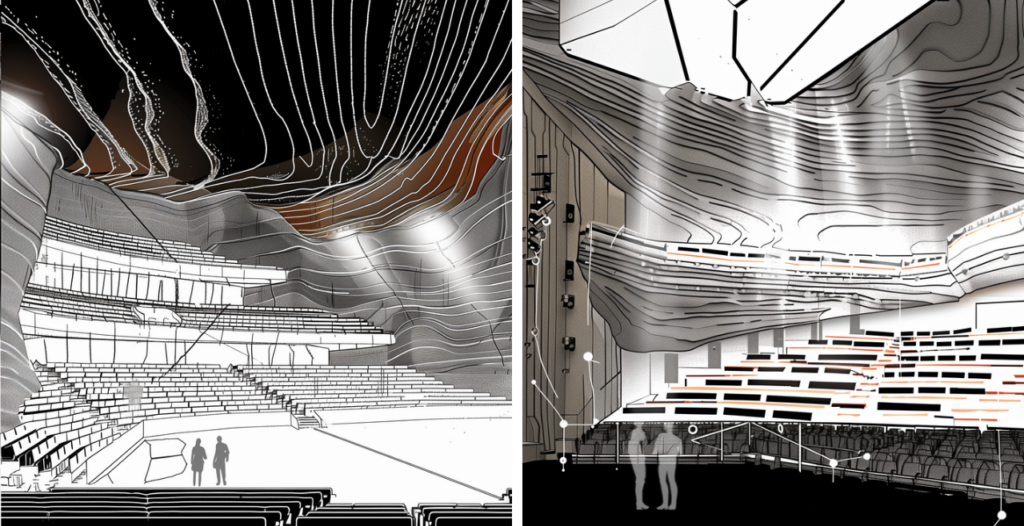
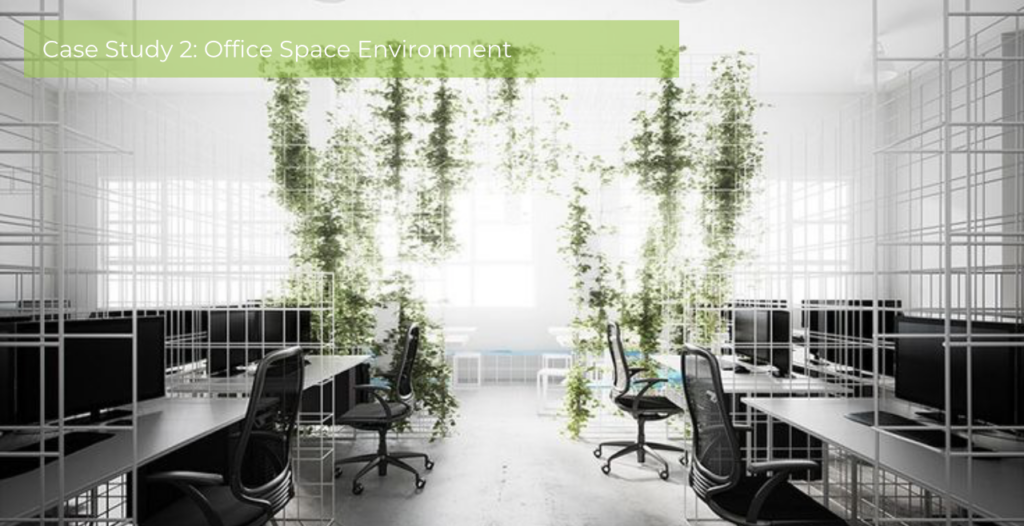
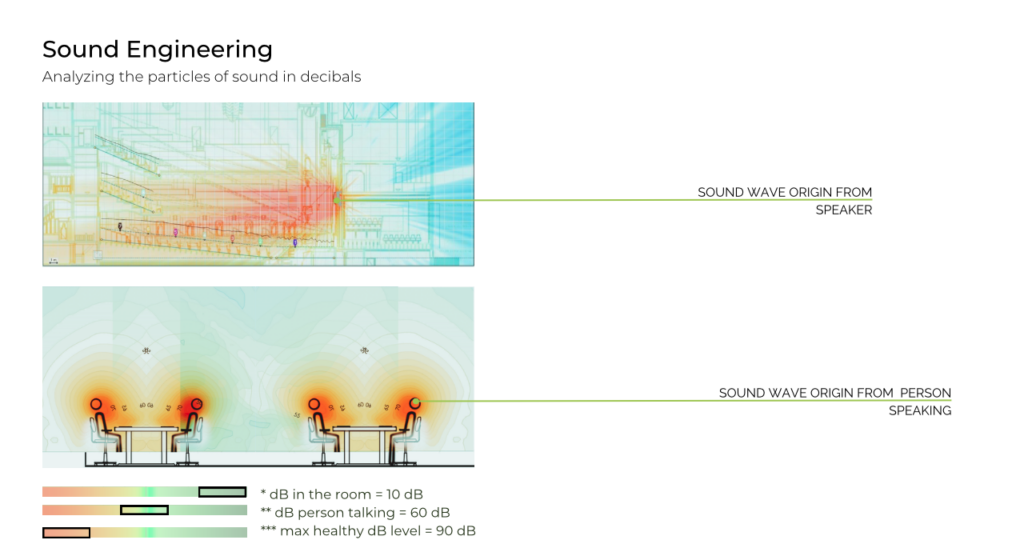
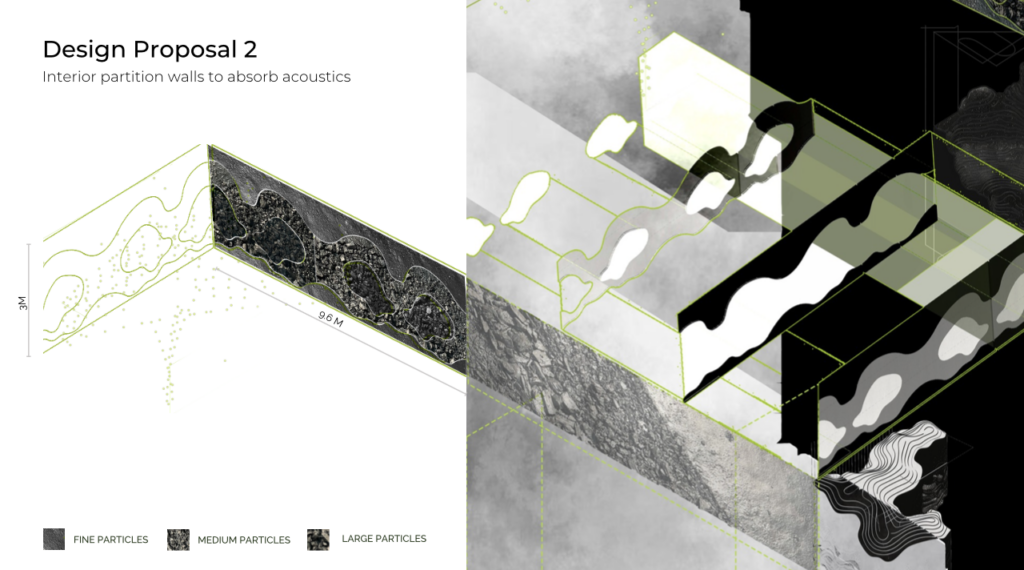

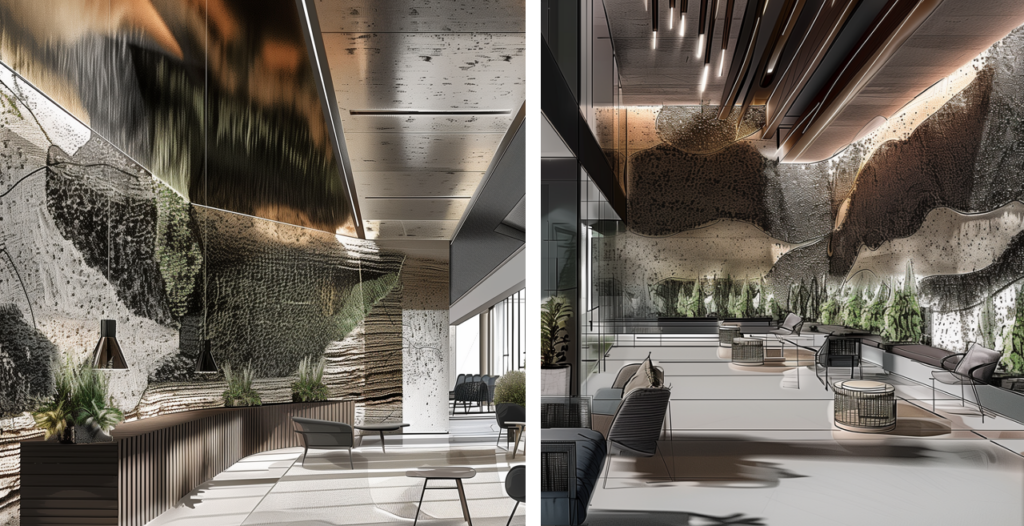
Final Prototype
Acoustic panels with particles grading to achieve acoustic diffusion and absorption performances.
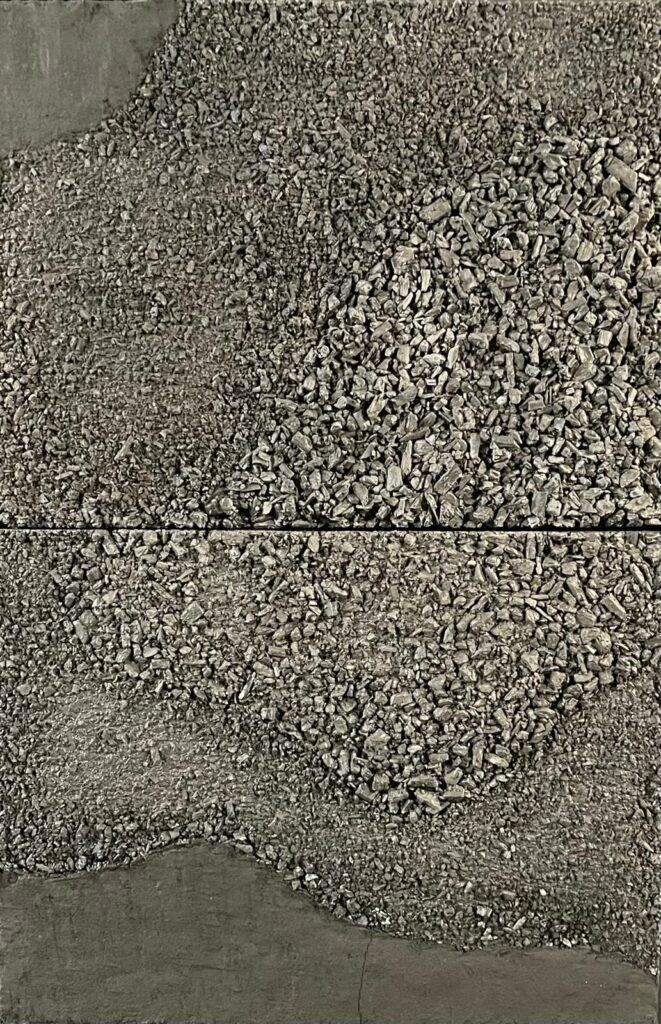