Concept
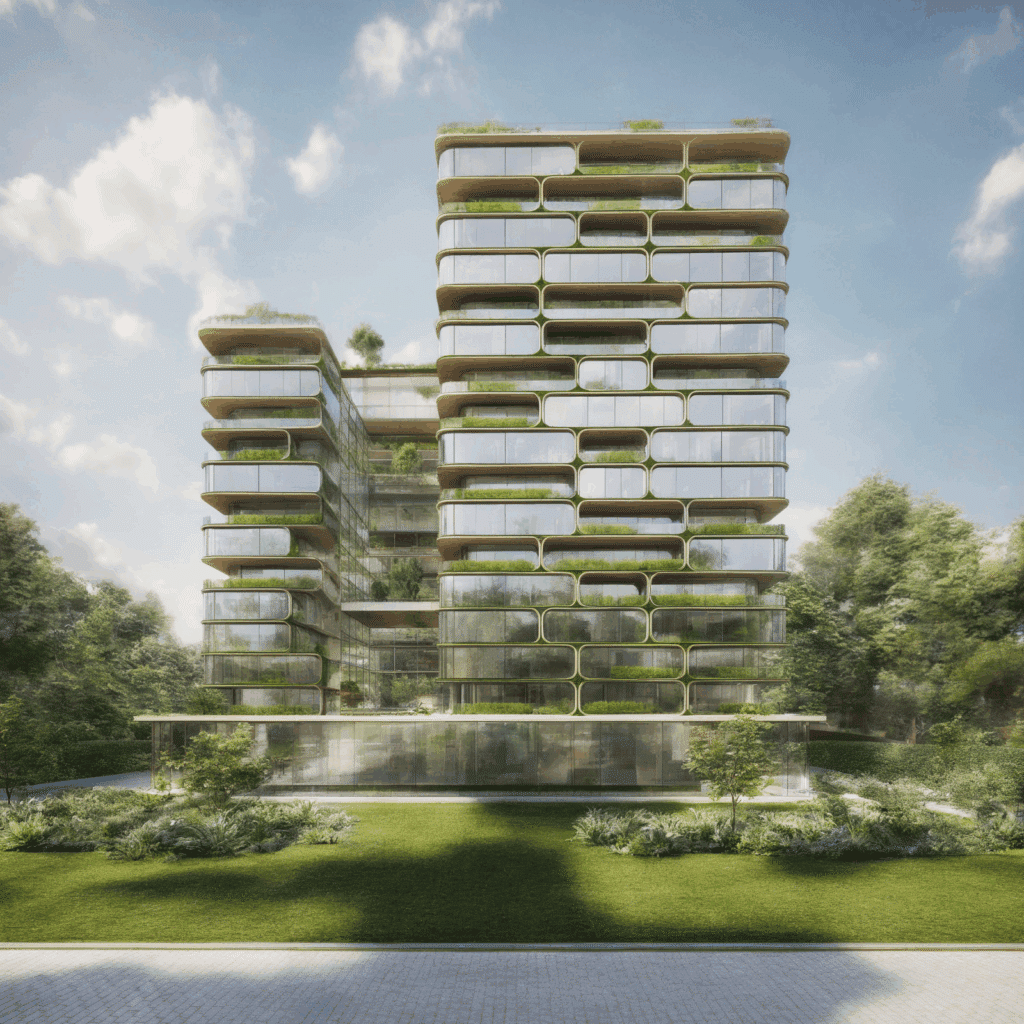
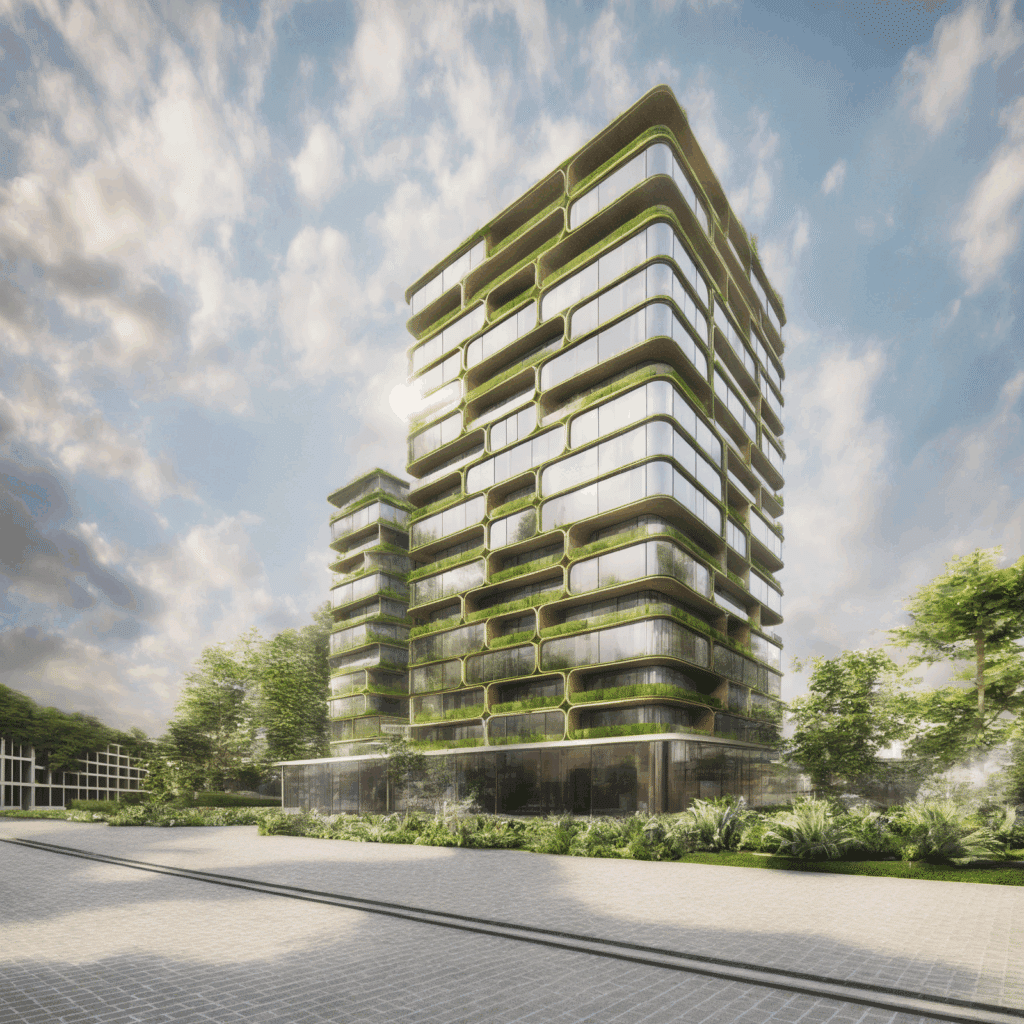
Our project reimagines the modular design of the Nakagin Capsule Tower for modern sustainable architecture. We’ve created a parametric adaptable building system featuring:
- Central concrete core for stability
- Steel bracings for lateral support
- Lightweight, replaceable living modules
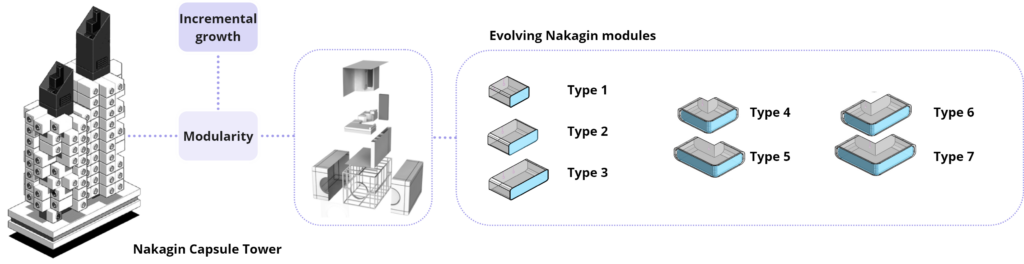
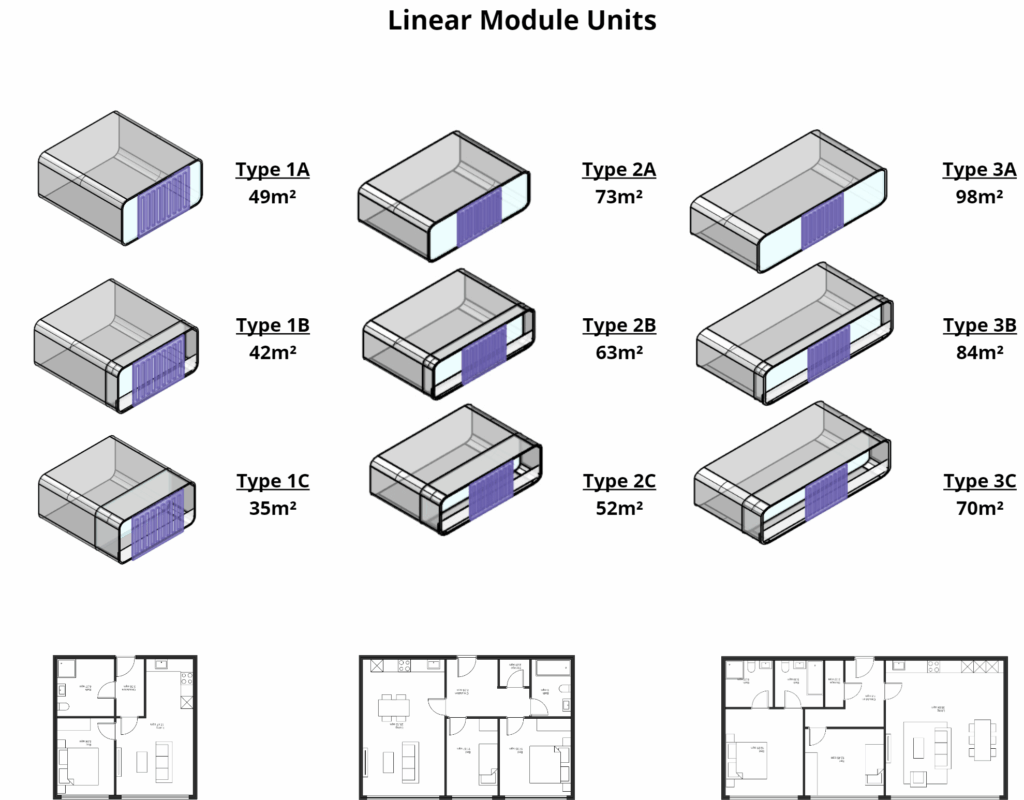
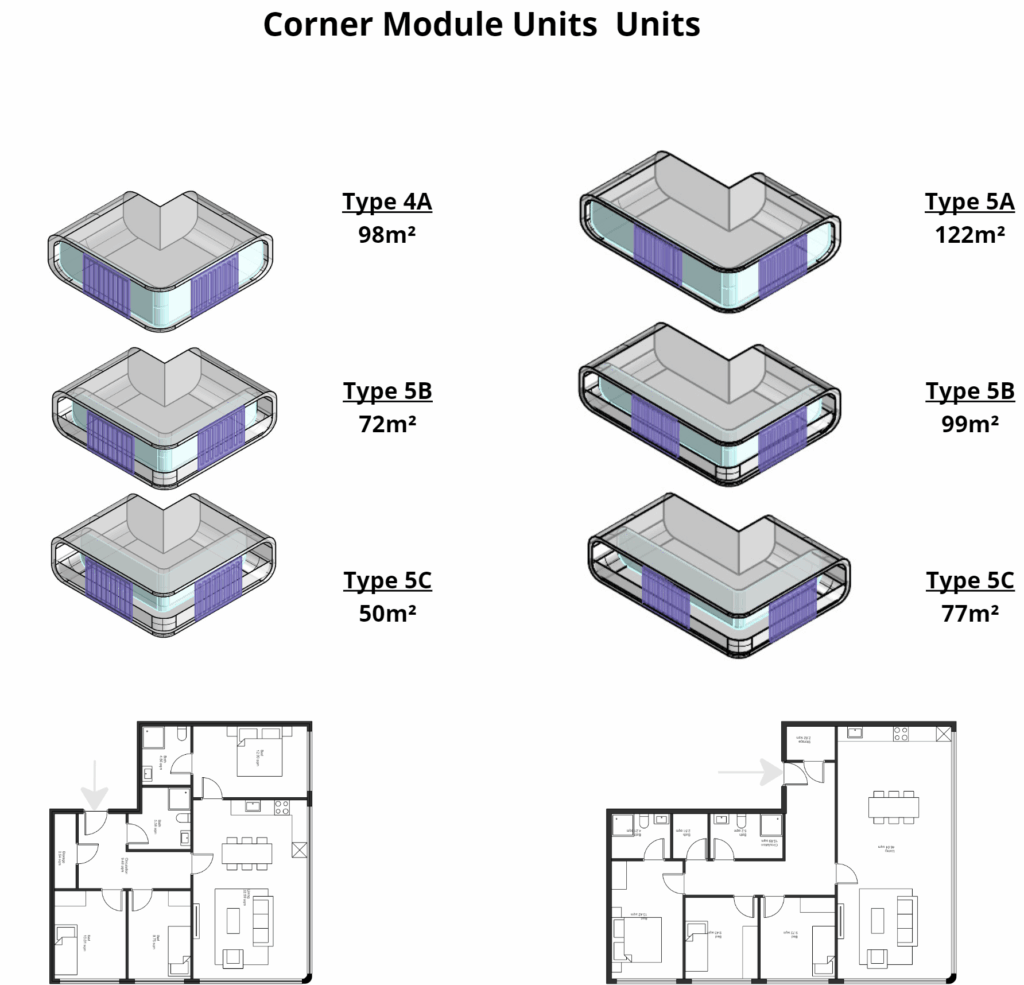
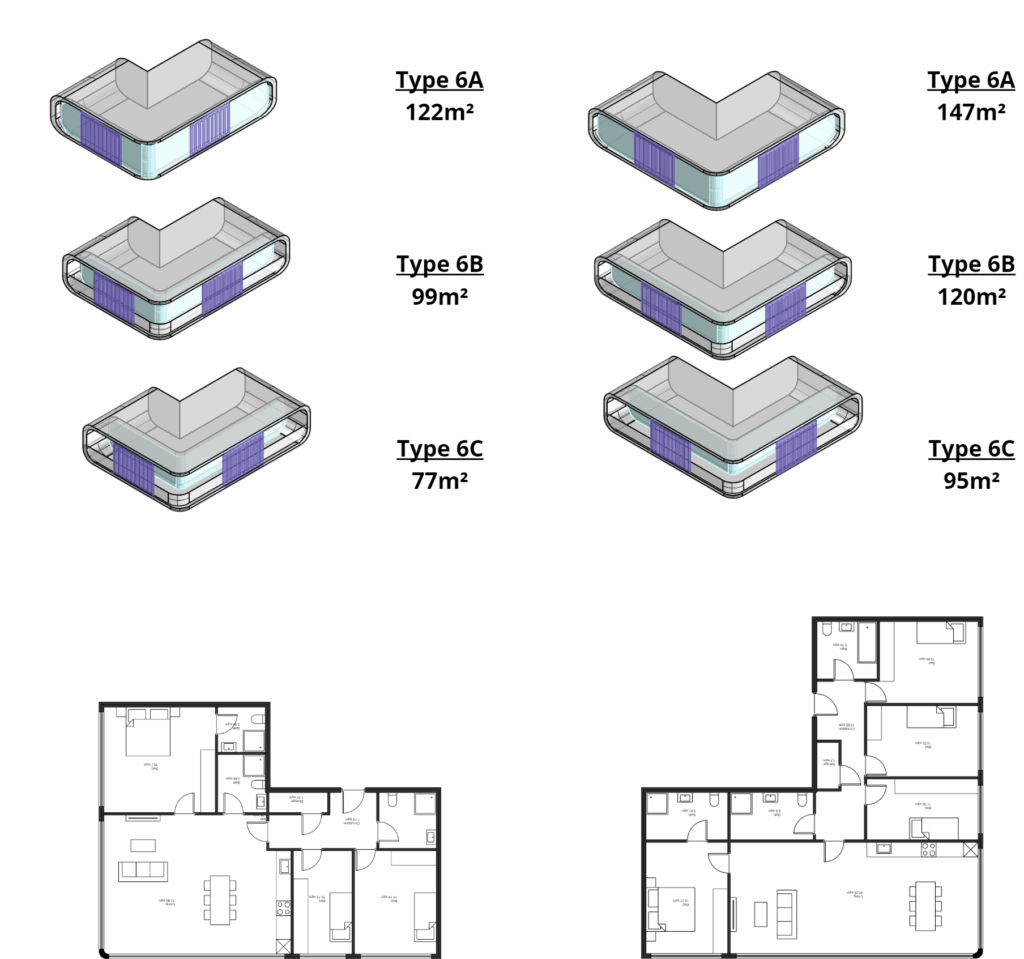
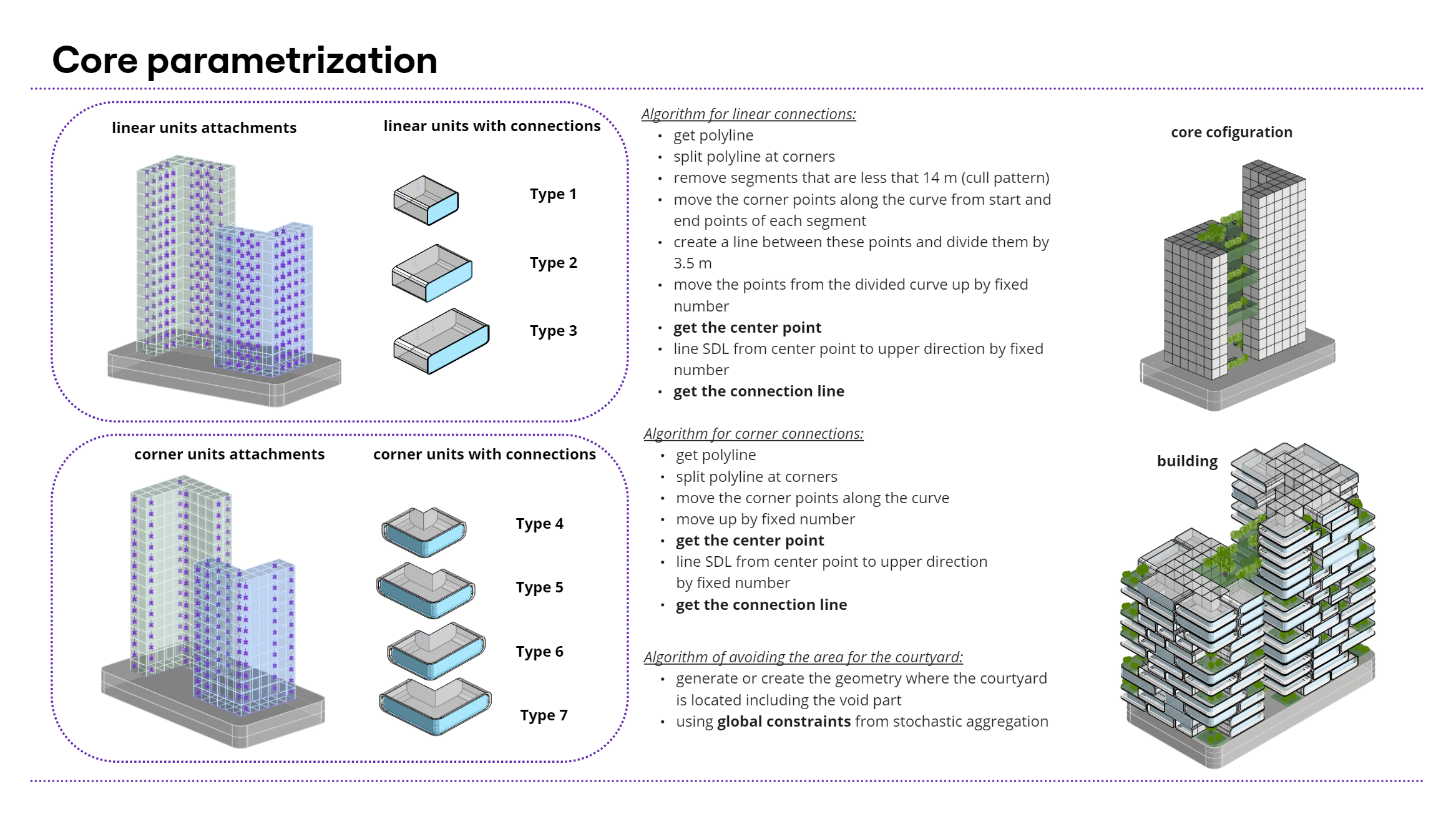
This design allows for easy customization and future updates, extending the building’s lifespan while minimizing environmental impact. Our approach combines the visionary ideas of Metabolist architecture with contemporary sustainable building practices. It’s easily customizable and adaptive to any rectangular shape.
We developed a parametric core model and attached the module using Wasp algorithm in Grasshopper, that is adaptive to any rectangular core and floor number. There are 7 main types of modules: corner and linear ones, made from lightweight GFRP material. Each module is attached to the core with the possibility to replace it in the future. Additionally, we have 3.5 m gaps between some modules that formed naturally according our generation algorithm. These gaps allow the crane attach the concrete core for the extension and maintenance works.
The structural model
Our basic model consists of 2 modules: core and modules structure.
The core structure:
- foundation
- super structure columns
- transfer slab
- core and floors
The modules structure:
- horizontal columns (B)
- vertical columns (C)
- horizontal bracings (D)
- vertical bracings (D)
All columns and transfer slab were went through cross section optimization to ensure the maximum stability with the lowest materials used.
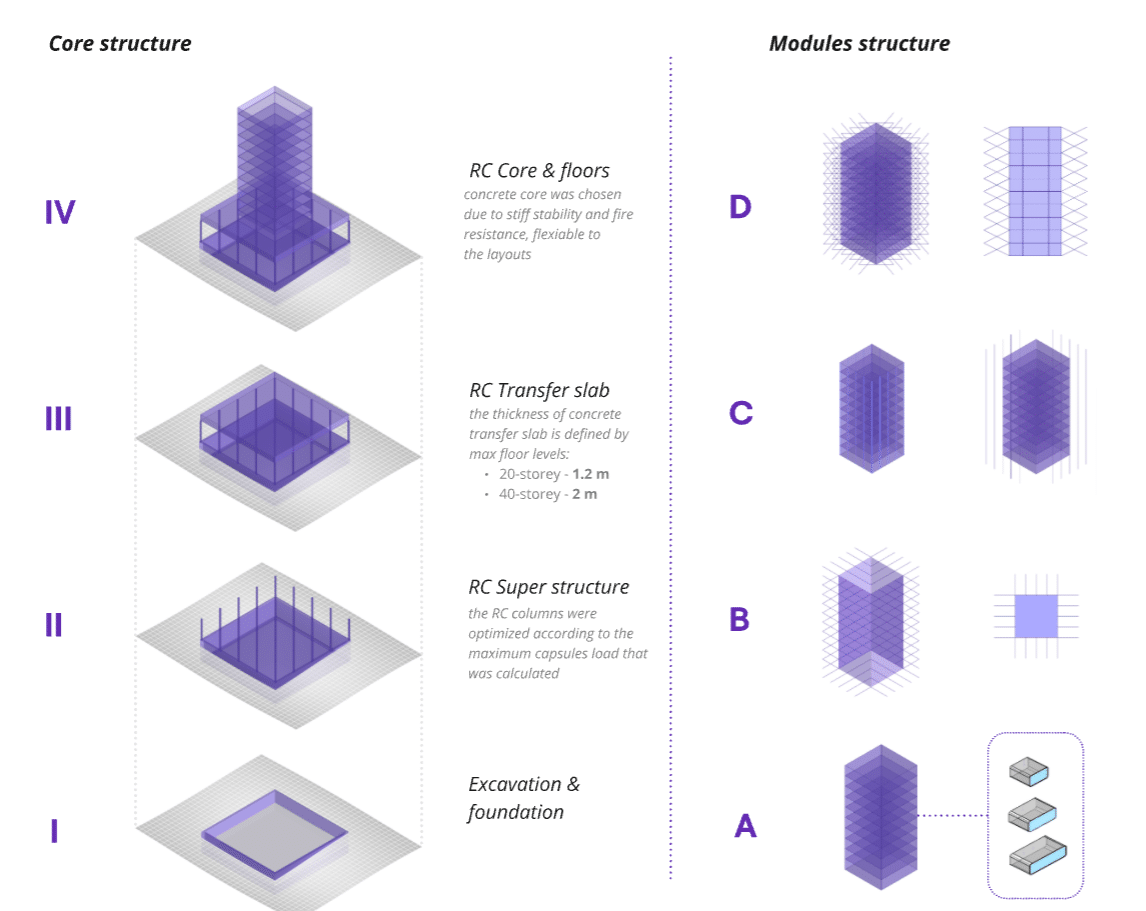
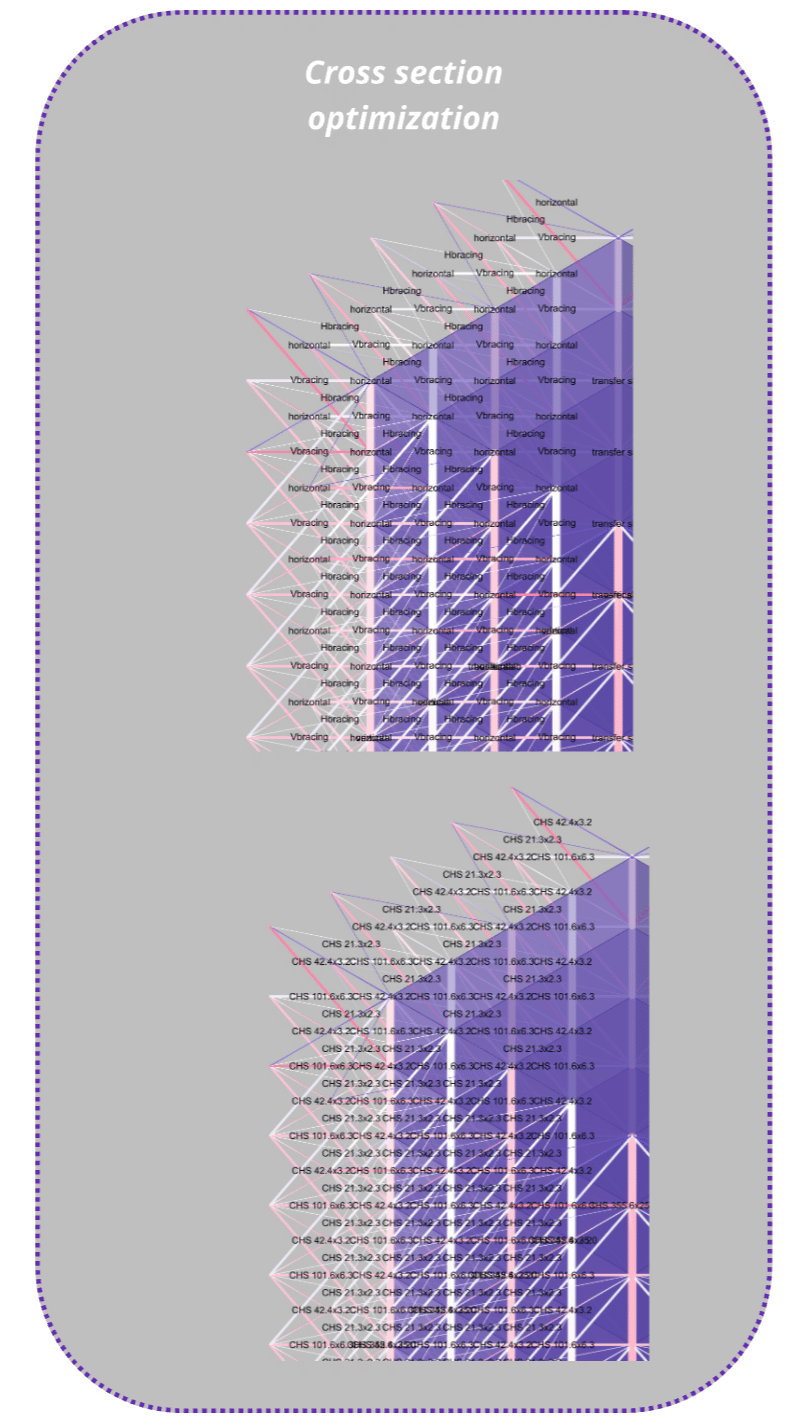
Loads
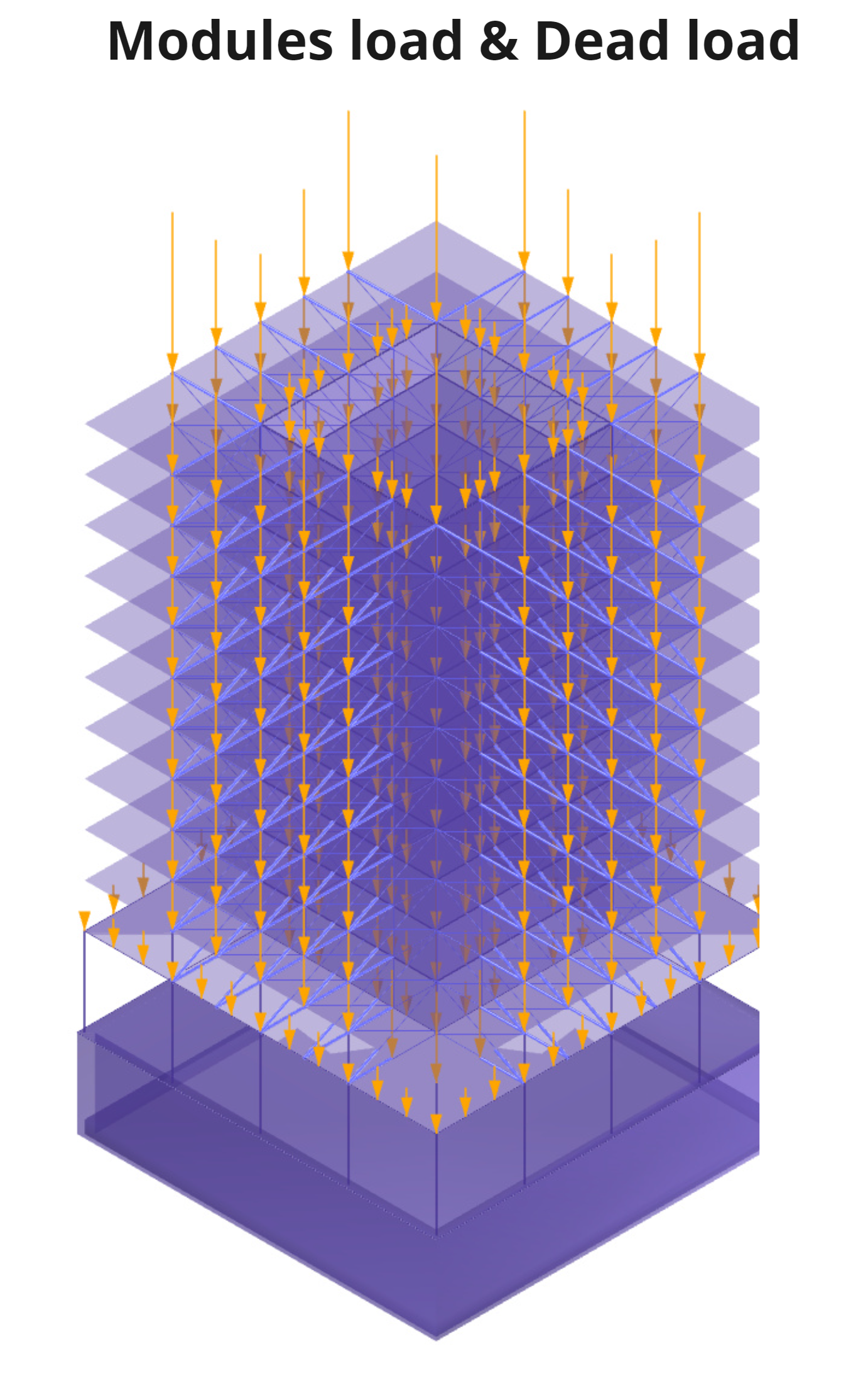
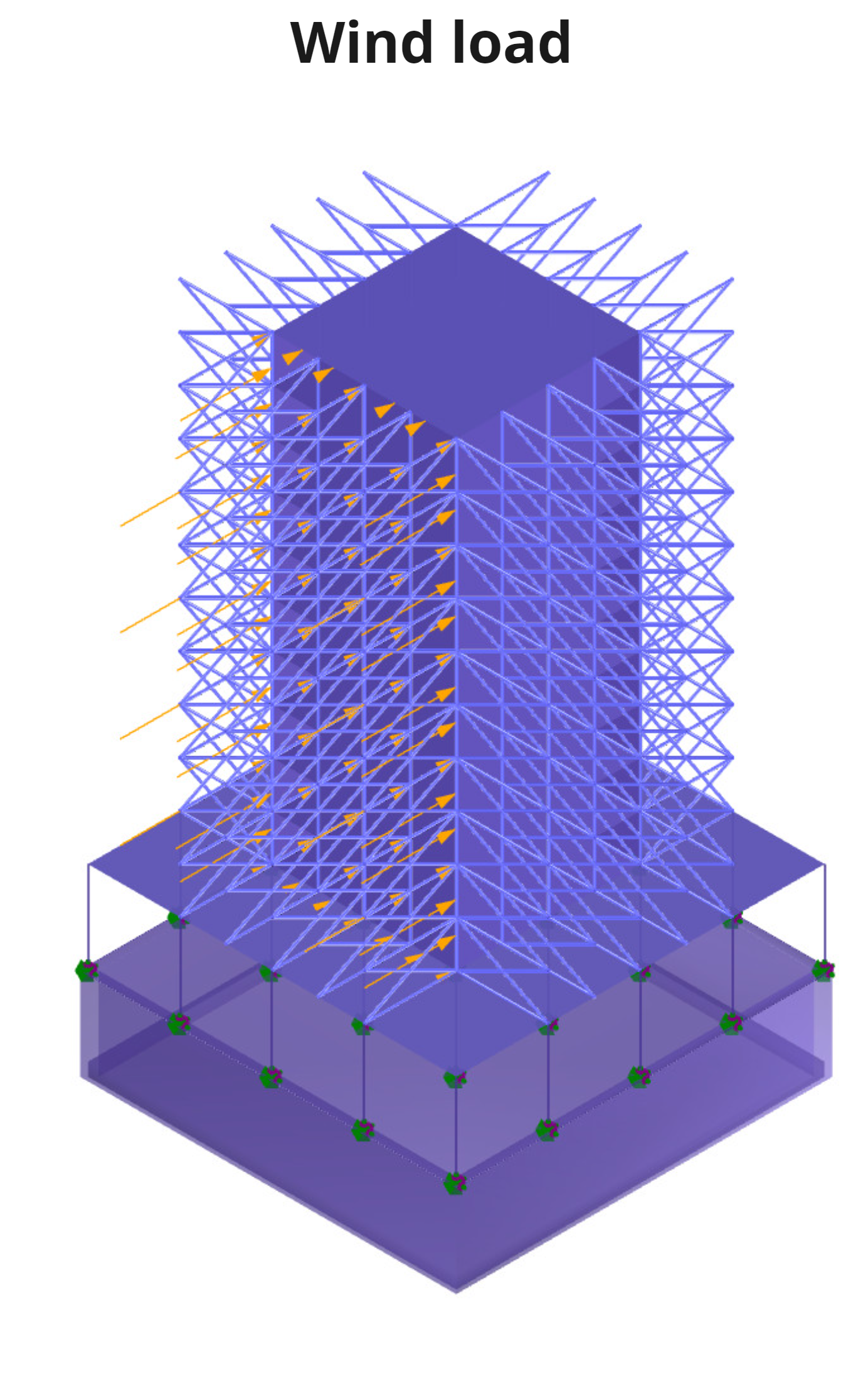
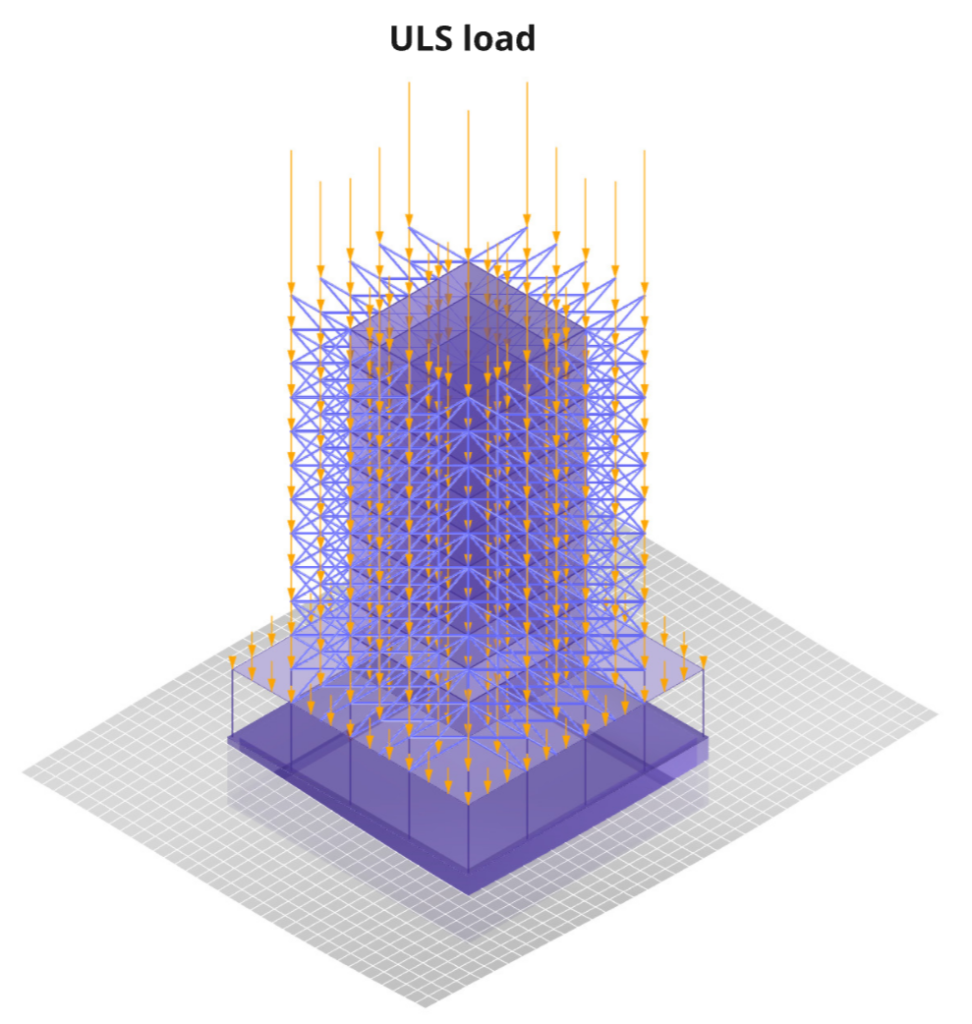
The loads applied to our structural building model:
- Gravity (g)
- Modules load (gm) 5 kN/sq.m.
- Dead load (gq) 2 kN/sq.m.
- Wind load (qw) 1 kN/sq.m.
- ULS = 1.35 (g + gm + gq) + 1.5qw
- 1.35x for dead loads
- 1.5x for live loads
We have create sets of 4 element sets in Karamba, such as vertical columns, horizontal columns, vertical bracings and horizontal bracing and run a cross section optimization for each group with 100% ULS as maximum utilization.
Design exploration & optimization
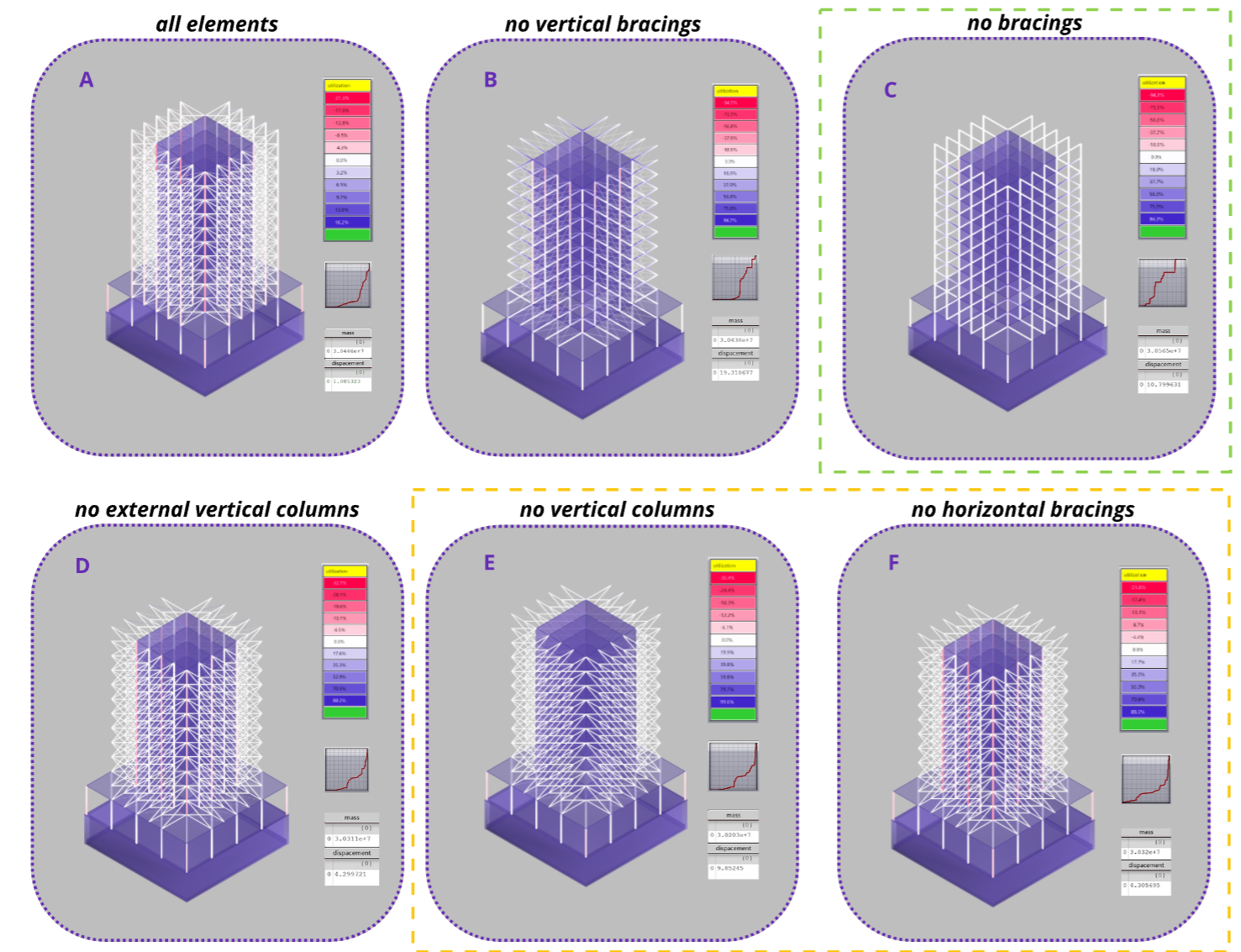
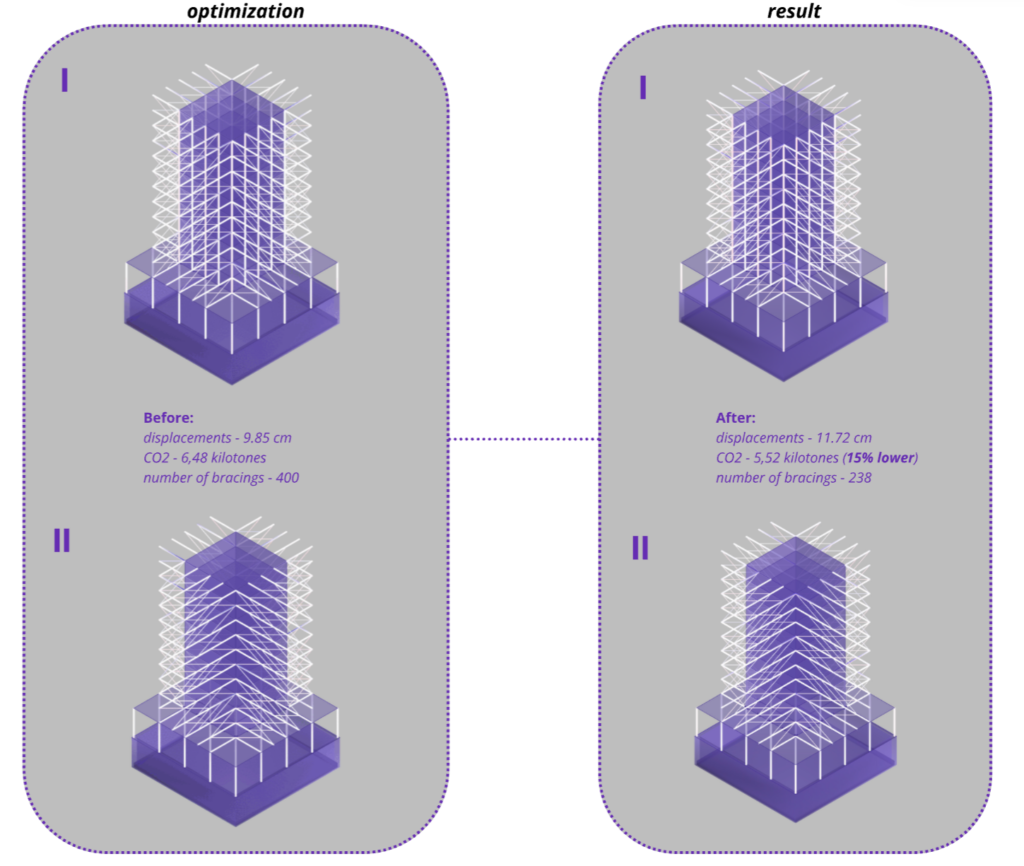
We explored some structural design options and were searching for the solution that would have the lowest mass and displacement and the maximum utilization of the elements. The displacement is measured in cm, and the mass – in kg. The element utilization graph was created for USL as load case.
Option C where, for modules structure, we used no bracings, vertical and horizontal columns only, showed the maximum structural element utilization. However, the mass value was also the highest in our research.
The bracing elements seem to be more effective: even though the number of elements is in greater quantity, they have smaller cross sections after optimization and keep the displacement smaller which makes the overall structure lighter and CO2 footprint smaller. Options E & F were chosen for further optimization.
We opted for optimizing the steel structure of the modules and were thinking of how we can optimize it by using less steel and still keeping the displacement at the lowest level.
In total, we have 400 vertical bracing elements and were thinking of reducing that number twice. So, cull 200 random index elements using gene pool that was our genom were work on with.
For optimization, we used multi-objective Wallacei solver. Our goals were:
- displacement – minimize
- amount of CO2 – minimize
- number of bracing elements – minimize
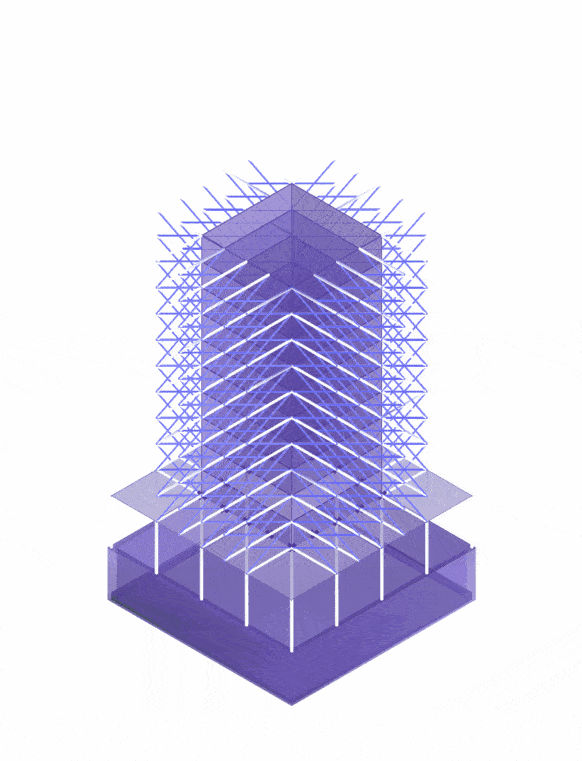
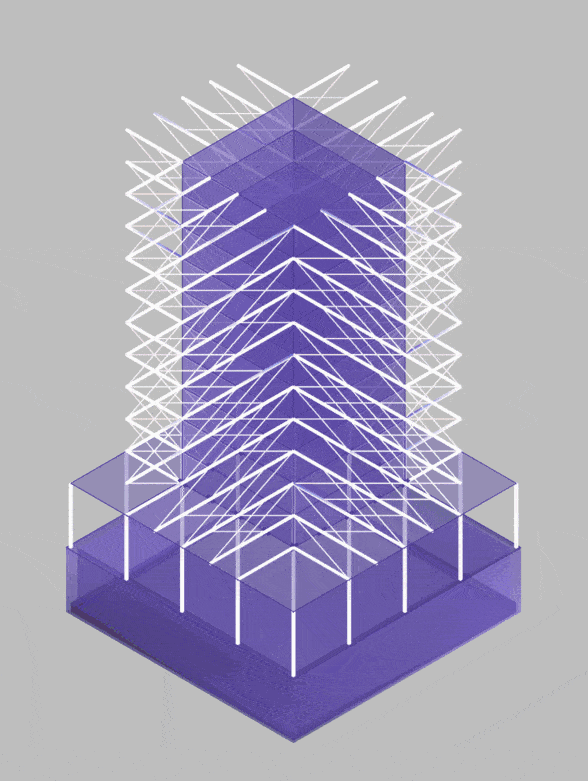
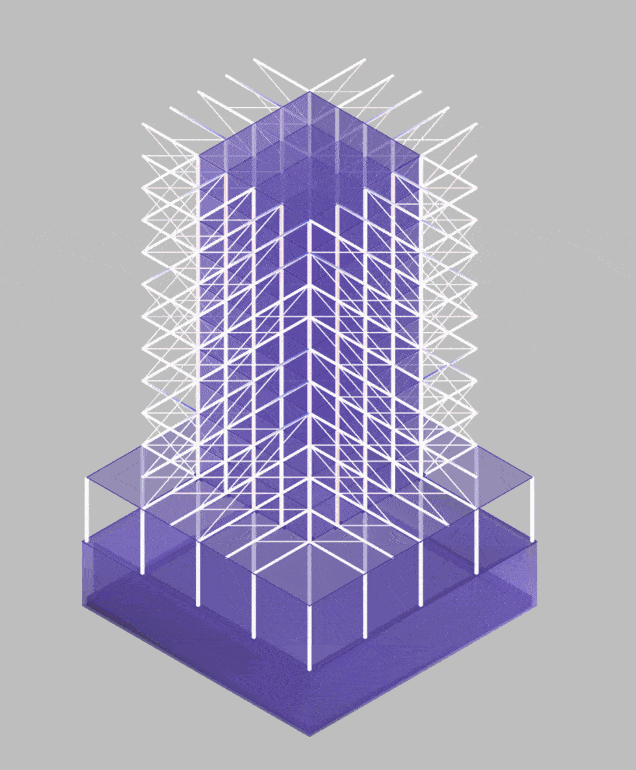
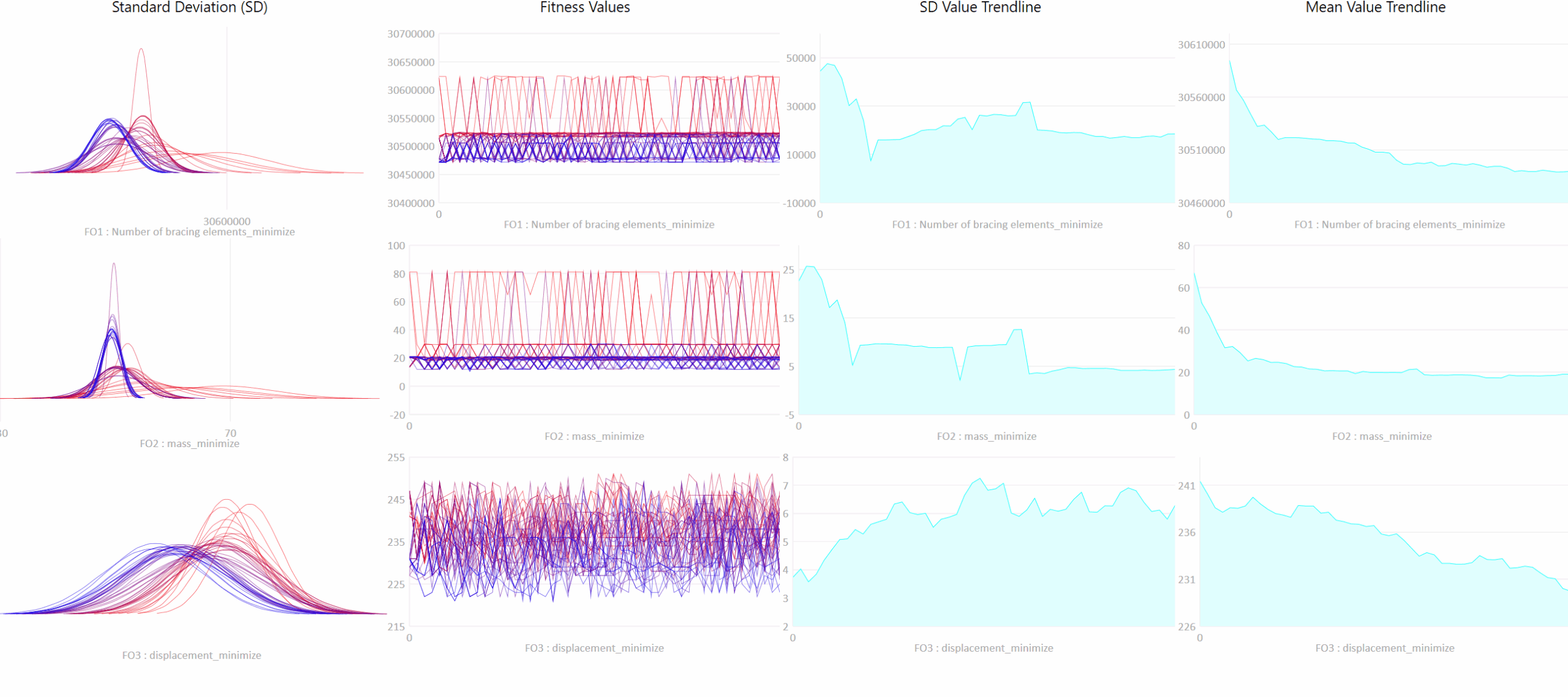
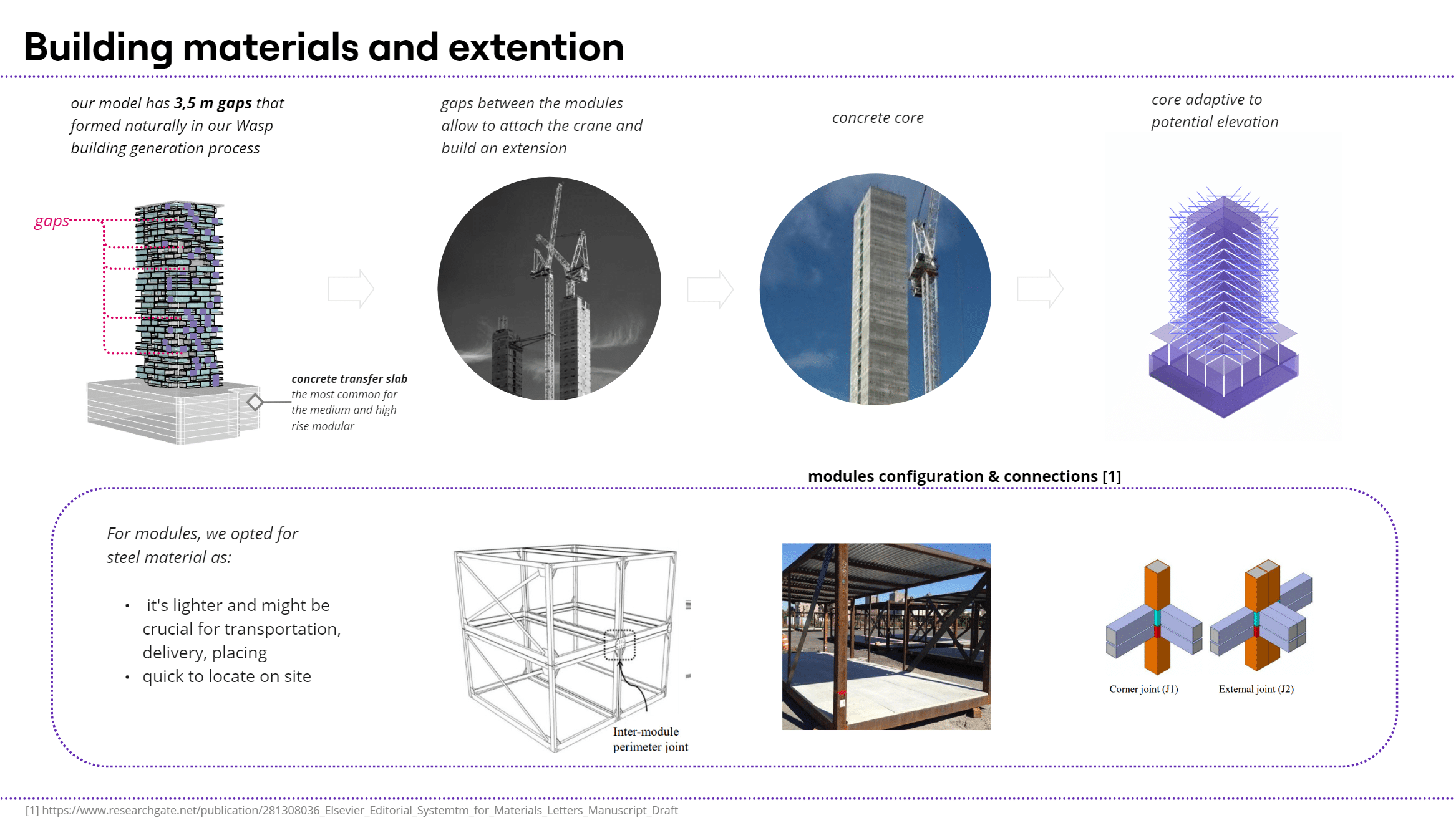
Results & further development
As a result, we have created a parametric Karamba model that is adaptive to different shapes, such as L, U or O-shaped cores and any floor number.
Depending on any specific task, this model can be adapted and used for further development and improvement of structural design.
For some high-rise options, other elements might need to be integrated. For example, for two cores near each other – steel connections between two cores can be implemented (creating some common green spaces between). Additionally, for better stiffness and stability, floor diaphragms every 10-20 floors may be included in structural design.
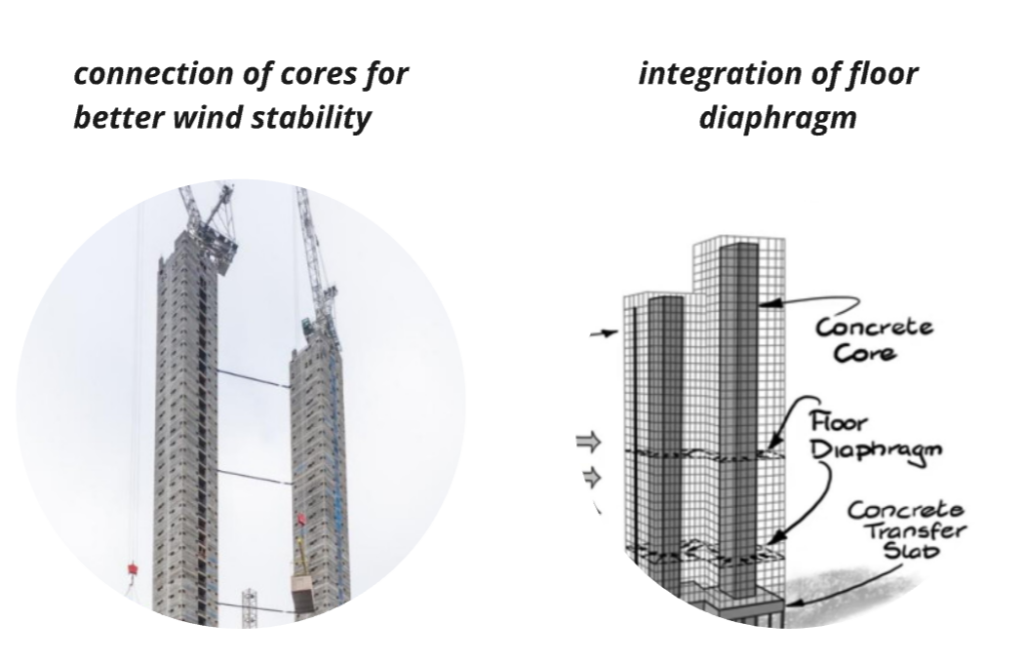
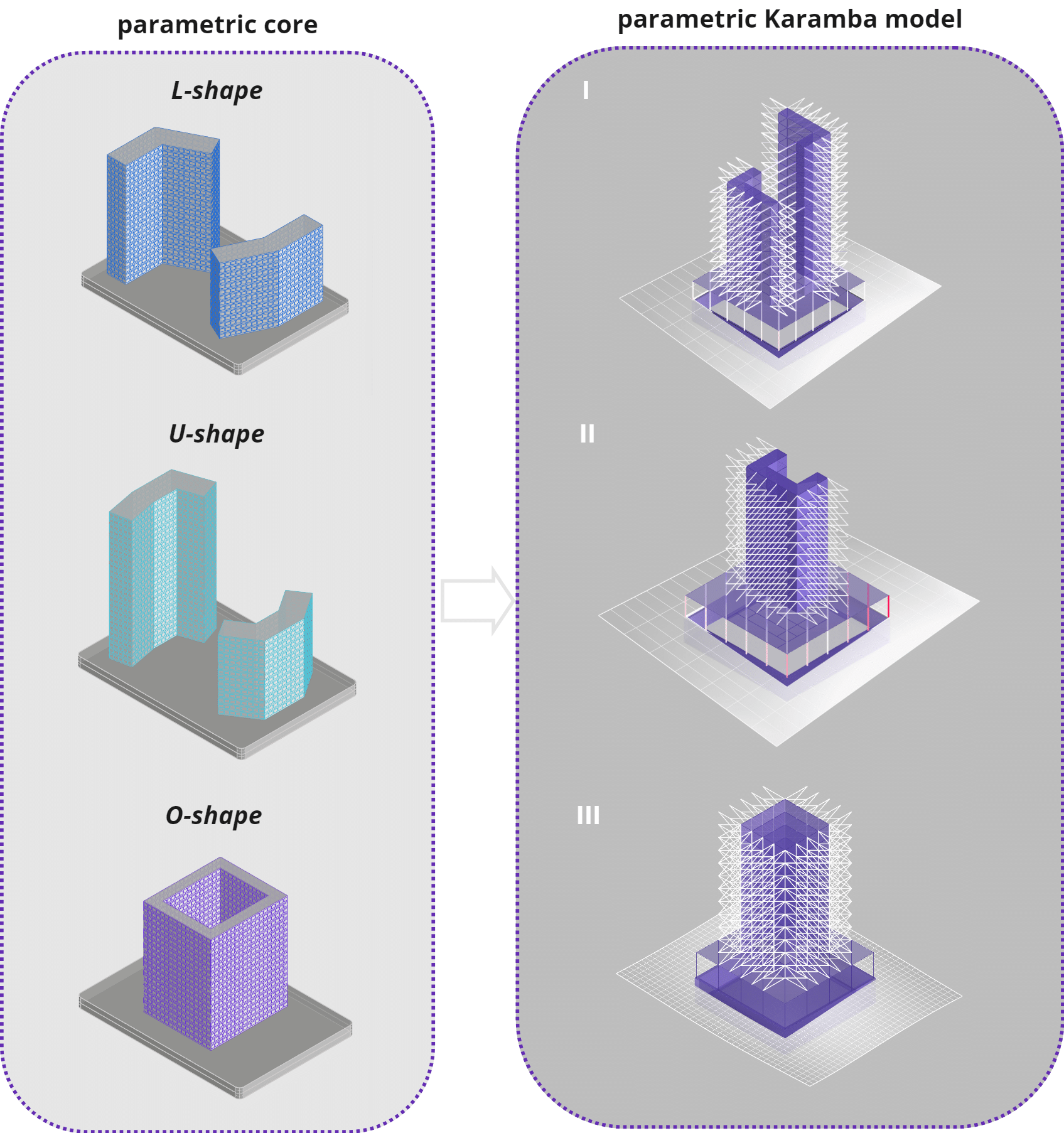