Structural Design Essentials Workshop
Introduction
The primary objective of the workshop was to explore innovative ideas in structural engineering by experimenting with materials and their compositions to create components. Specifically, the aim was to engineer a structural beam designed for integration into the case study structure, the Aravena Building, and to evaluate its structural strength under various forces acting on the building
Alternative design proposal for the Aravena Building – Design process
As a team, we leveraged our design expertise to reimagine the structural design of the existing Aravena Building. Our proposal introduced modifications to enhance the building’s structural adaptability, ensuring its capacity to accommodate future growth while providing additional space for habitation.
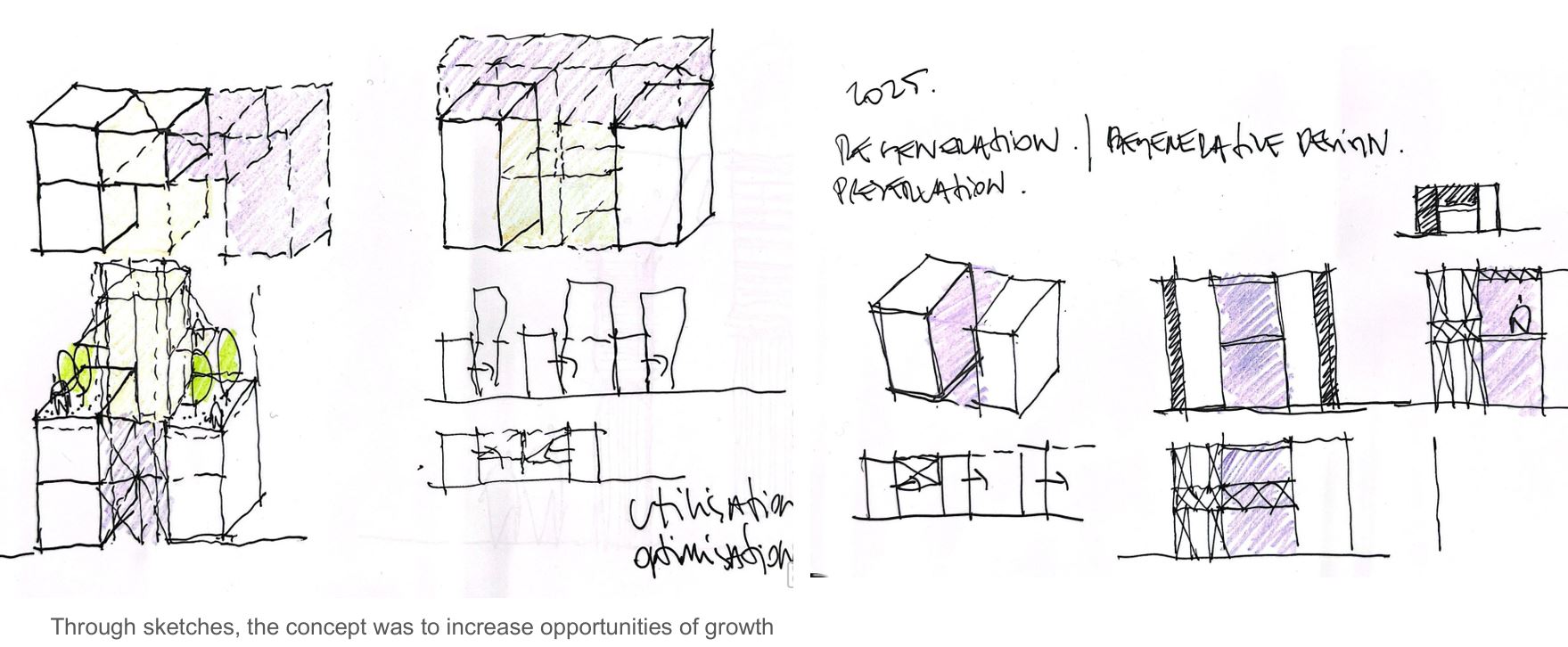
Using the original building as a case study, we collaboratively developed an approach to propose an alternative structural design. The goal was to create additional space while minimizing the use of construction materials and components, ensuring a waste-free solution.
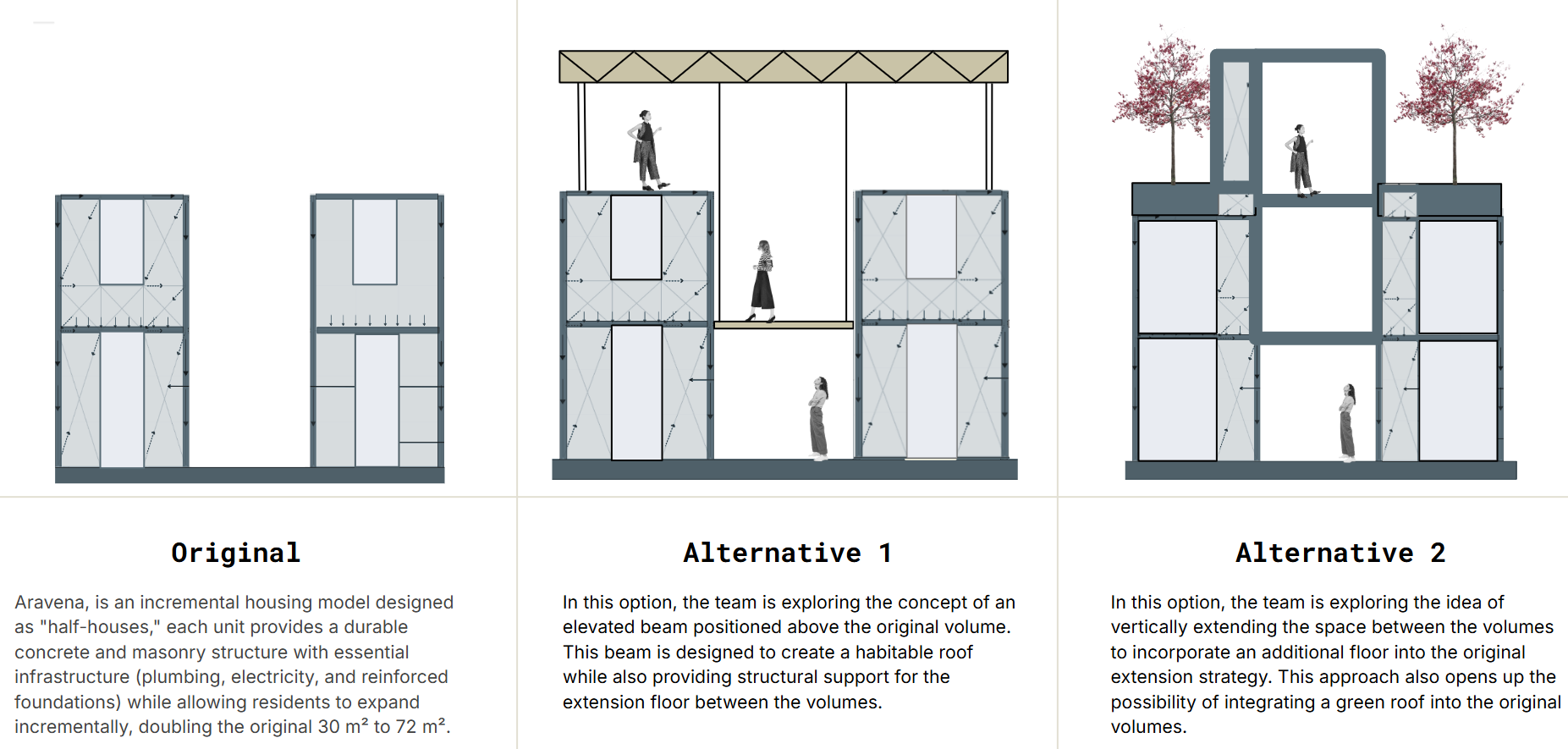
Alternative design proposal for the Aravena Building – Engineering analysis
Continuing the structural analysis using Karamba 3D, a plugin for Grasshopper 3D in Rhino 3D, we modeled the structural elevation of the original building as well as the two proposed structural alternatives. The material utilized for this project was recycled plywood timber. The Grasshopper script included linear elements, cross-section data, material properties, and the types of loads applied to specific building elements. The analysis was subsequently conducted, with the results examined through parameters such as load distribution and building reactions
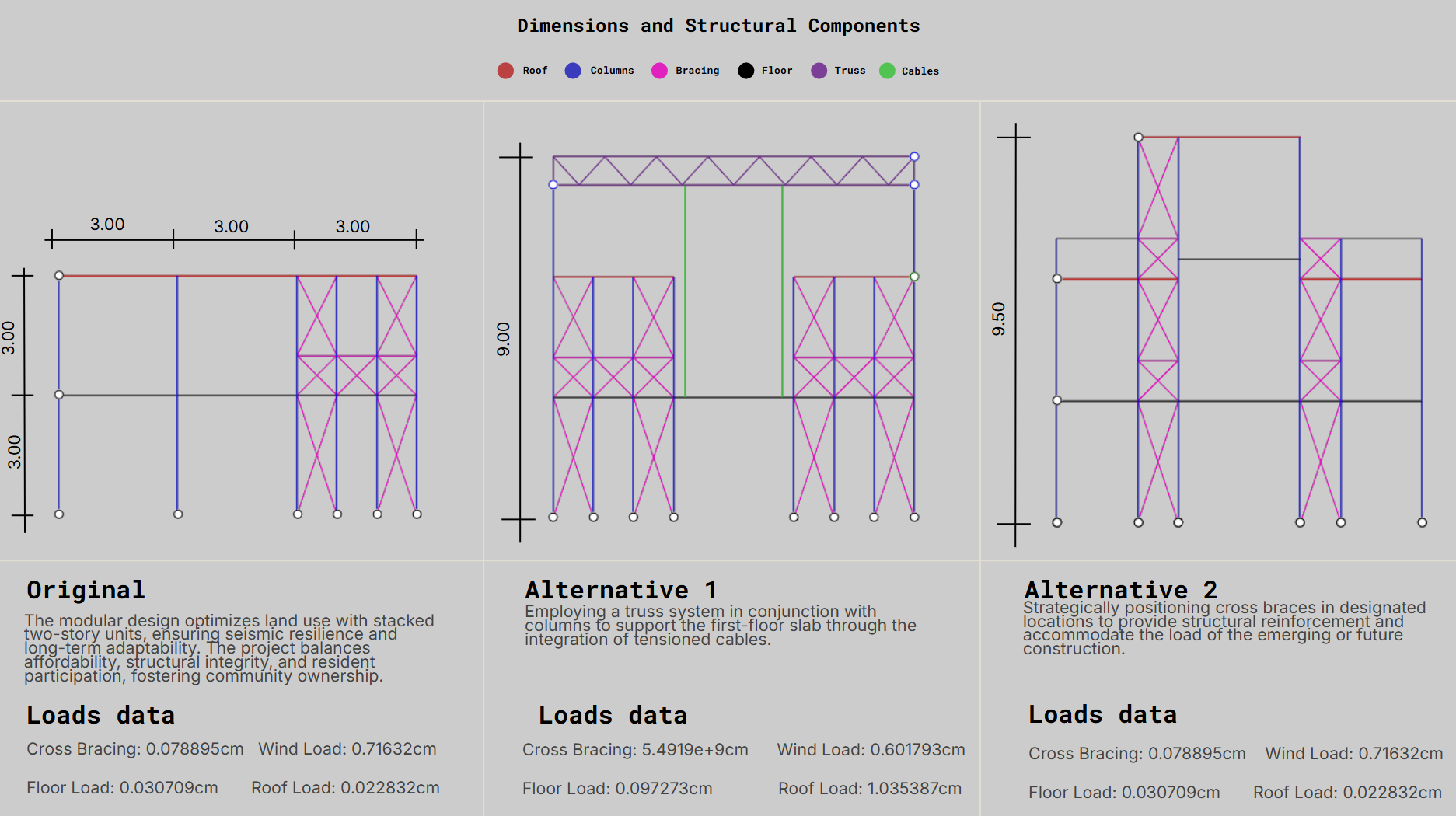
Each load or external force applied on the structures were analyzed and noted down using the following loads ; Gravitational load, wind load, floor load and roof load.
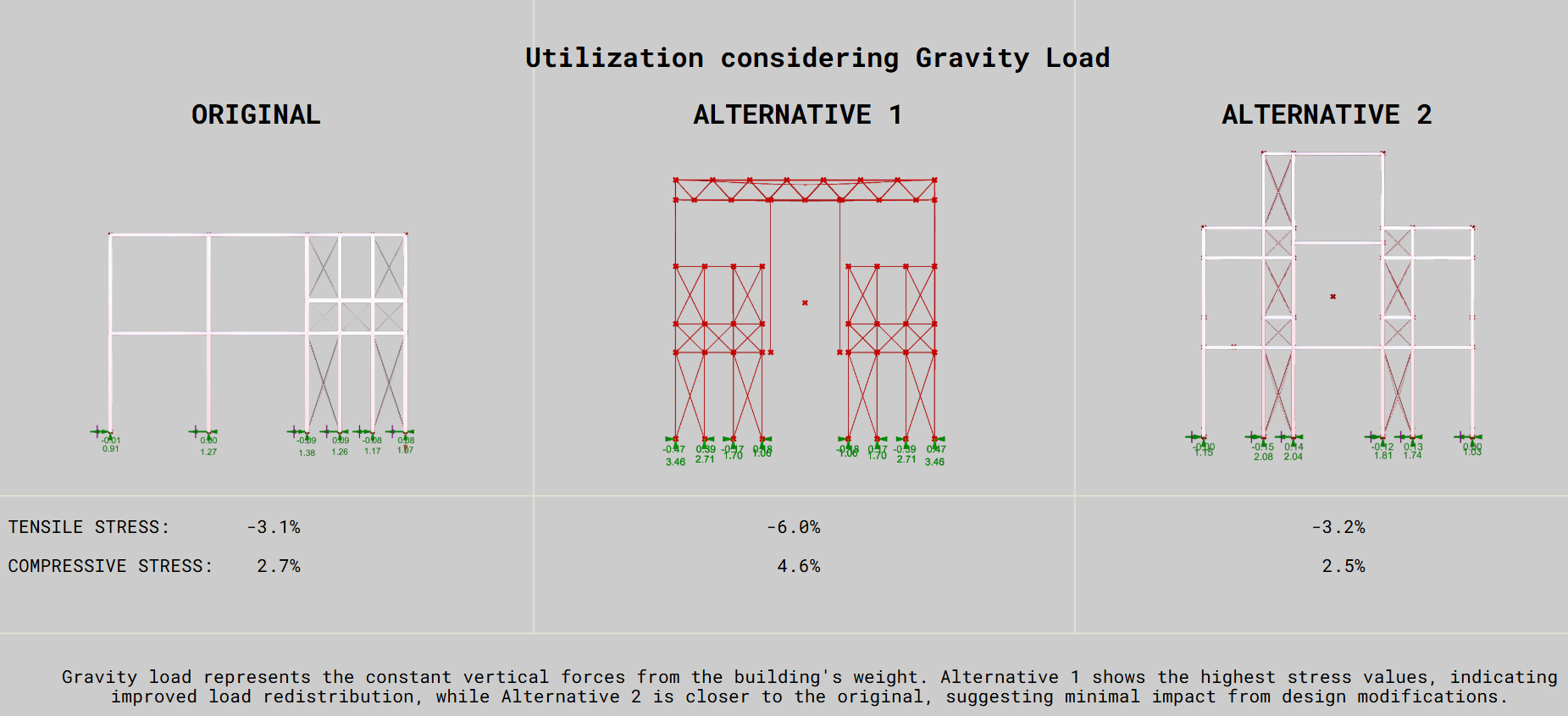
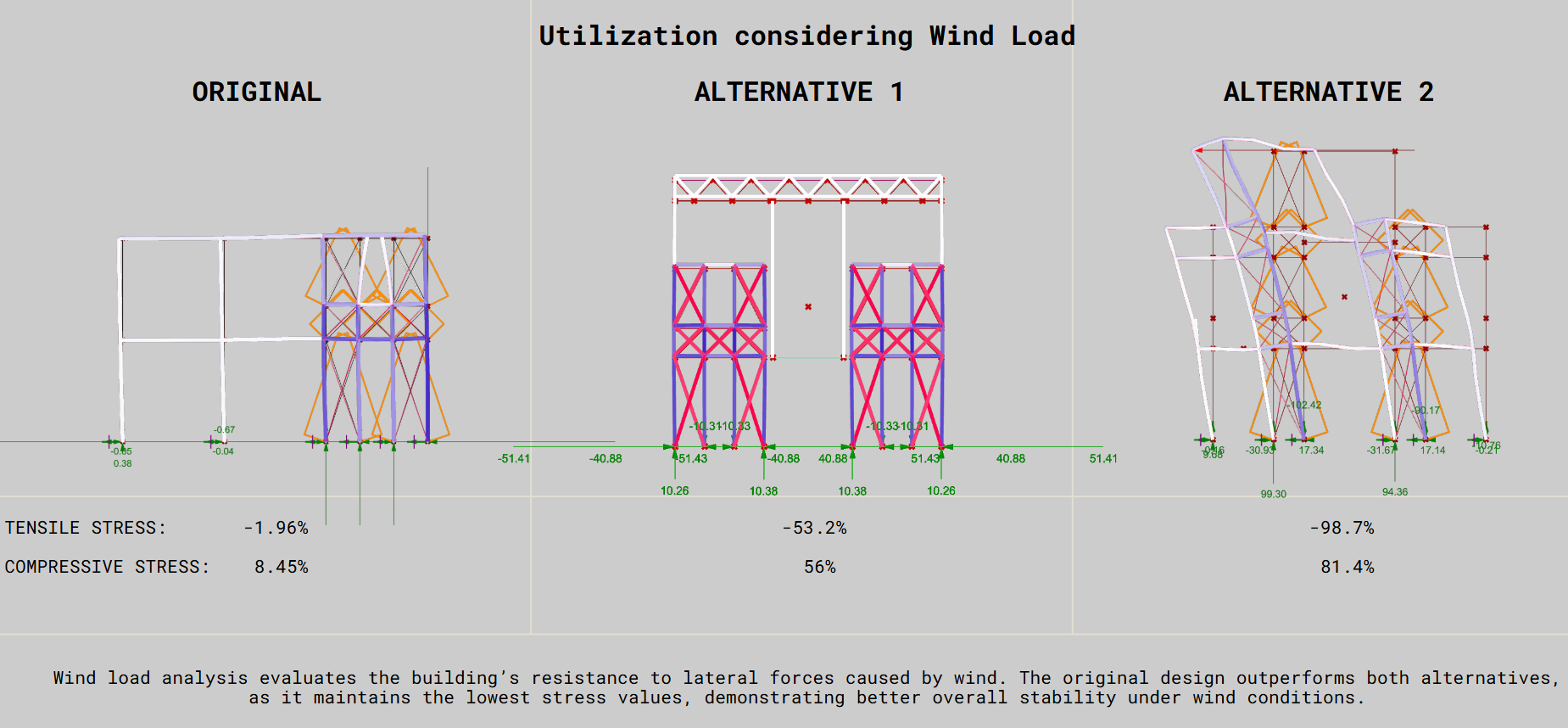
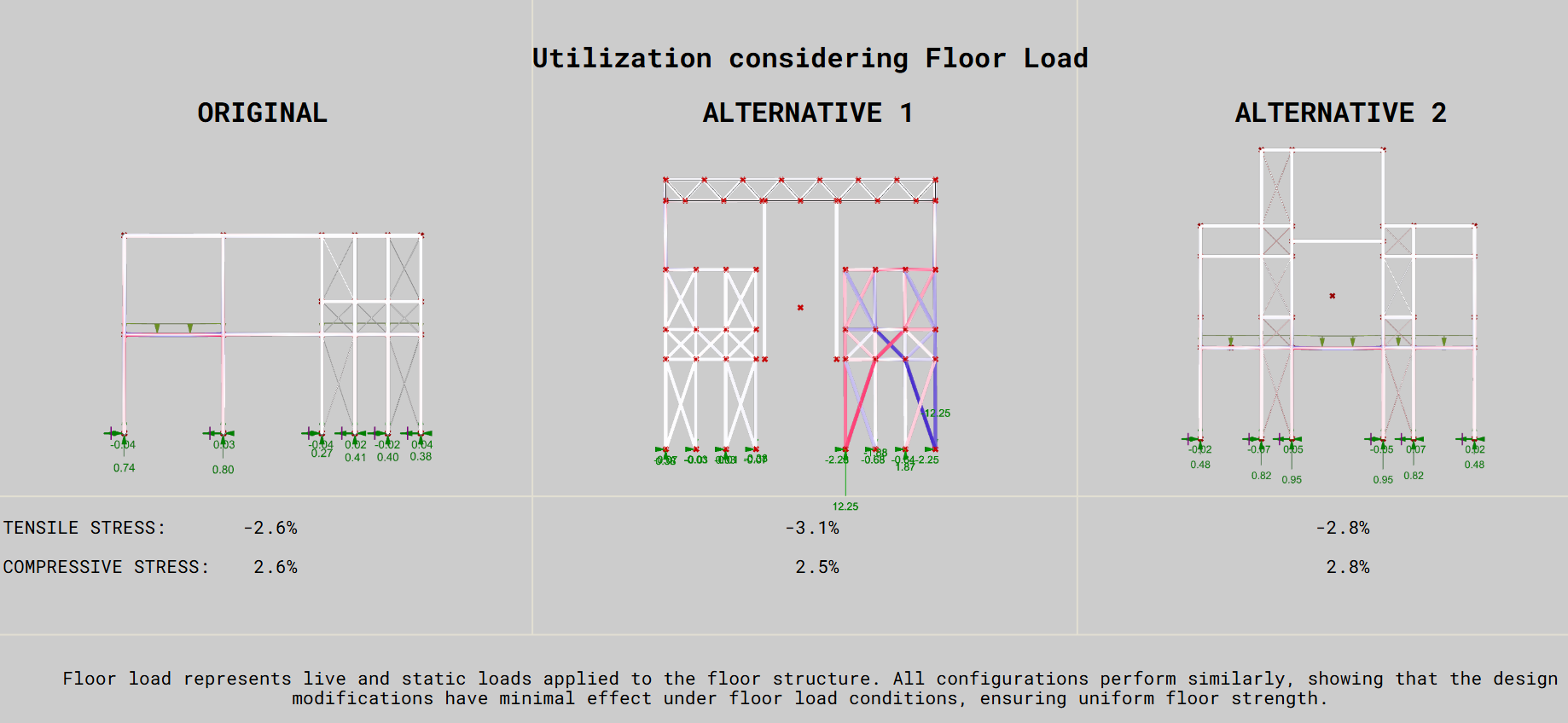
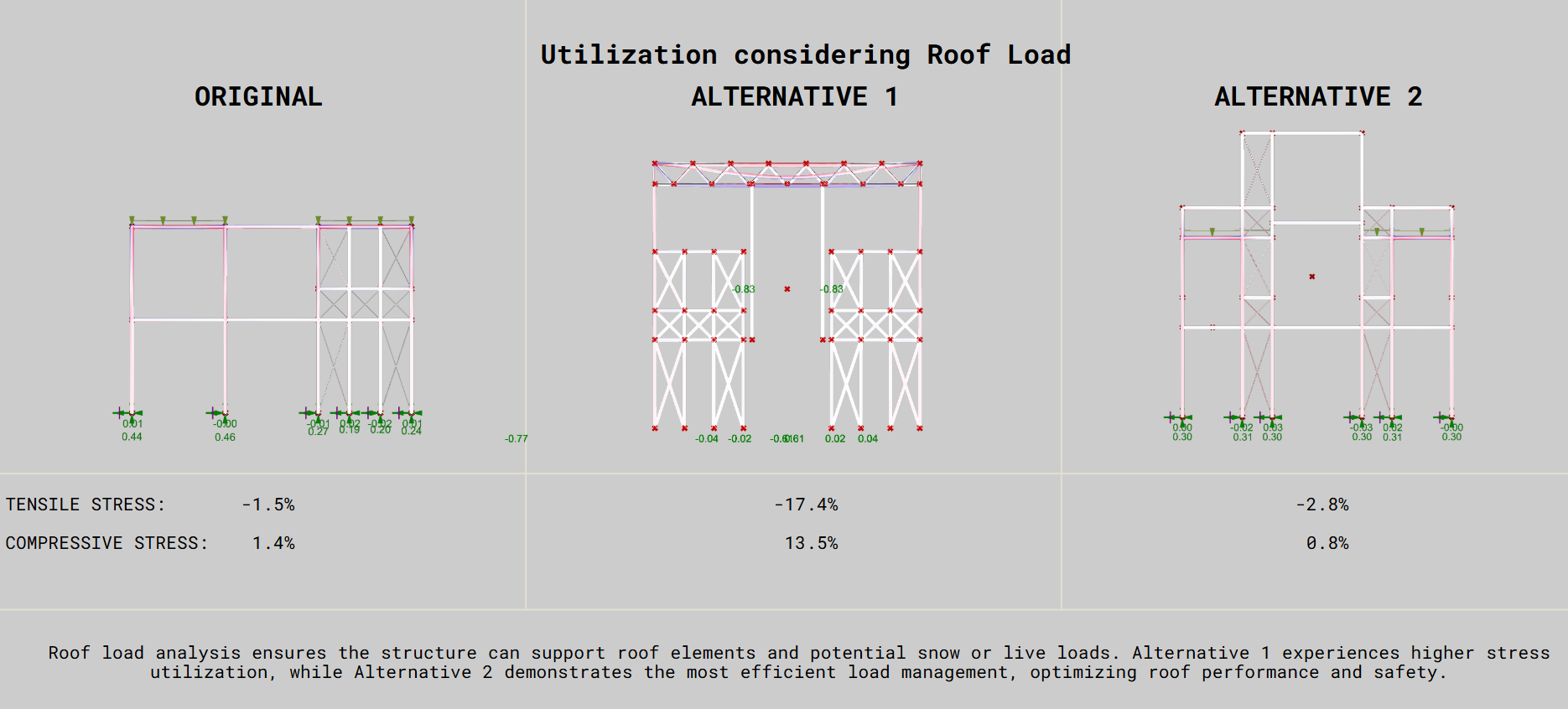
Concept of the Beam
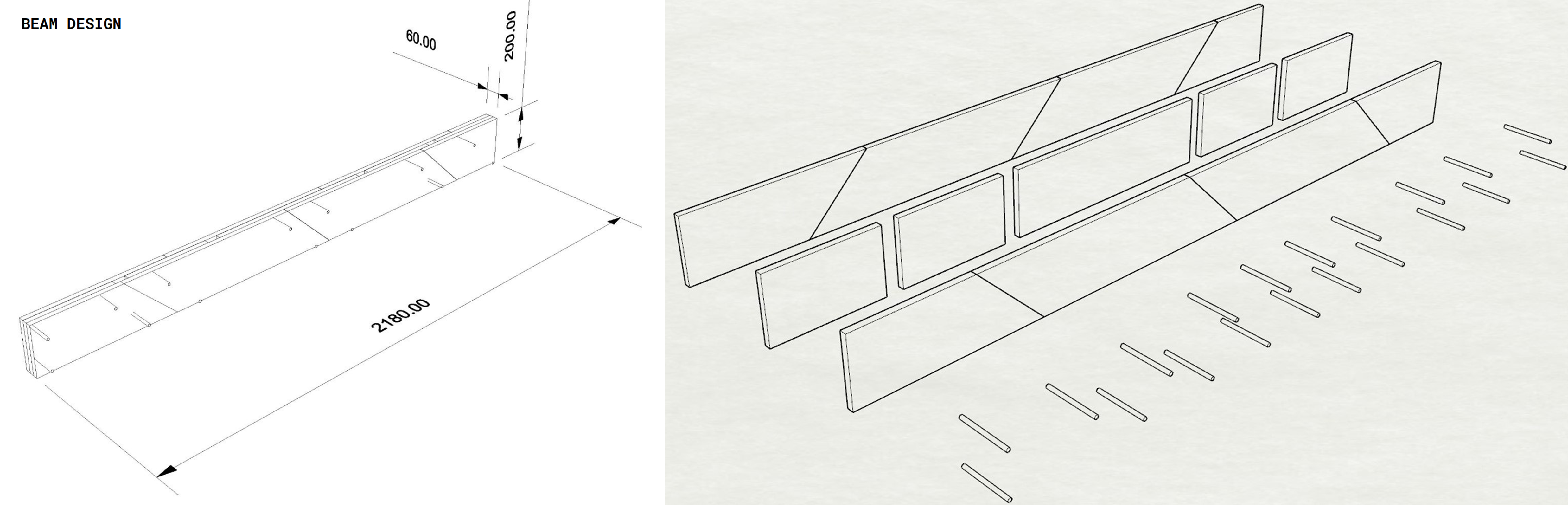
The concept involved repurposing discarded timber plywood construction materials to engineer a beam composed of three layers. The inner layer was constructed using simple 90-degree rectangular planks, with side beam planks measuring 708mm x 200mm x 18mm and a center beam plank measuring 684mm x 200mm x 18mm. The outer layers, on both the front and back, featured beam planks with 45-degree angled side cuts. The center plank measured 900mm x 200mm x 15mm, flanked by planks measuring 750mm x 200mm x 15mm.
The components of all three layers were arranged to ensure their edges overlapped with adjacent surfaces and were then secured using wooden dowels. The design concept relied on the stiffness of the layered beam to withstand external forces, ensuring structural stability and compatibility with the Aravena Building’s design. The image below illustrates an exploded diagram of the beam’s layered composition and the placement of dowels used to connect the layers.
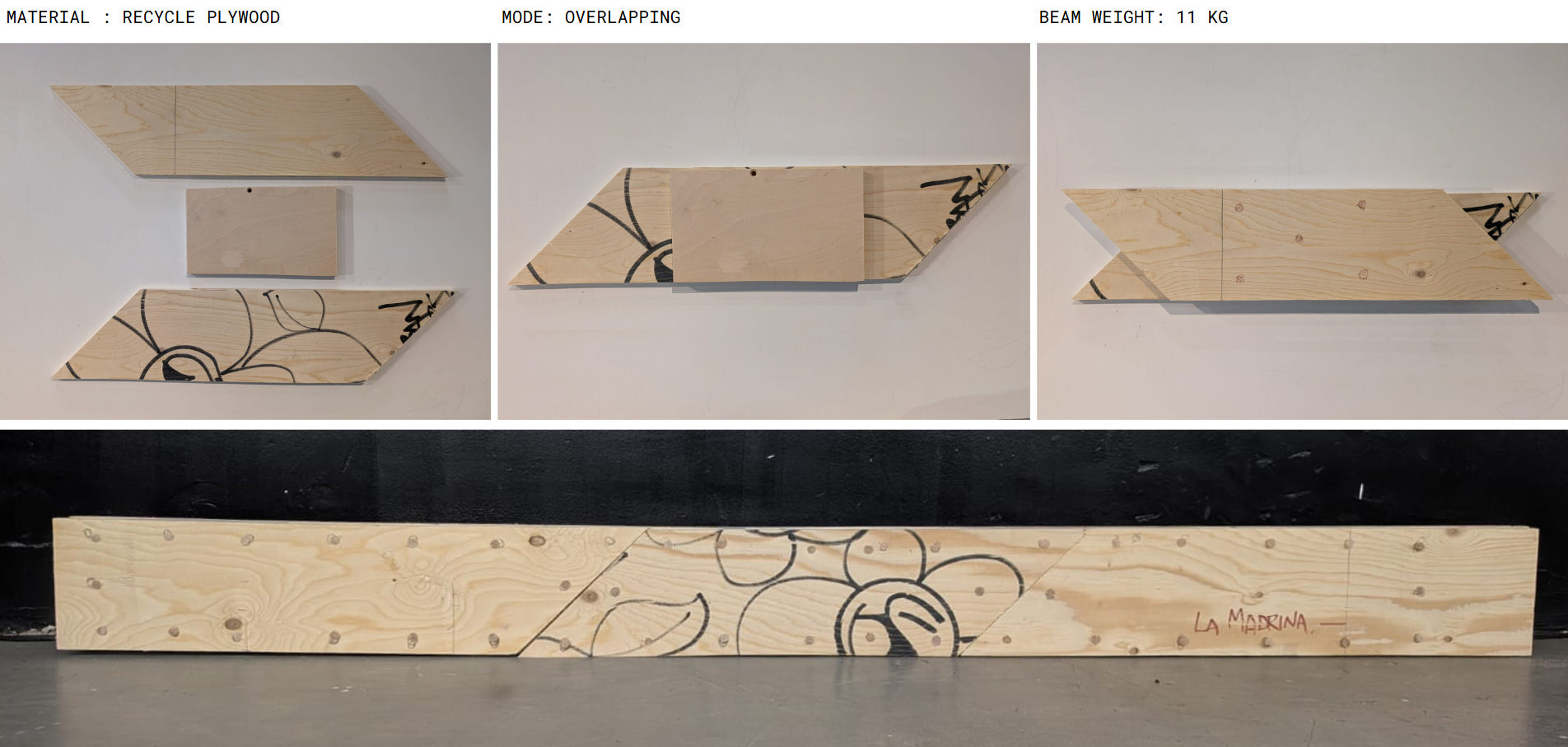

Engineering Analysis of the Beam – Physical testing
Other than Karamba3d analysis, a physical test on the prototype was performed using a machine to apply load on the Timber beam. The results varied compared to the karamba 3d analysis.
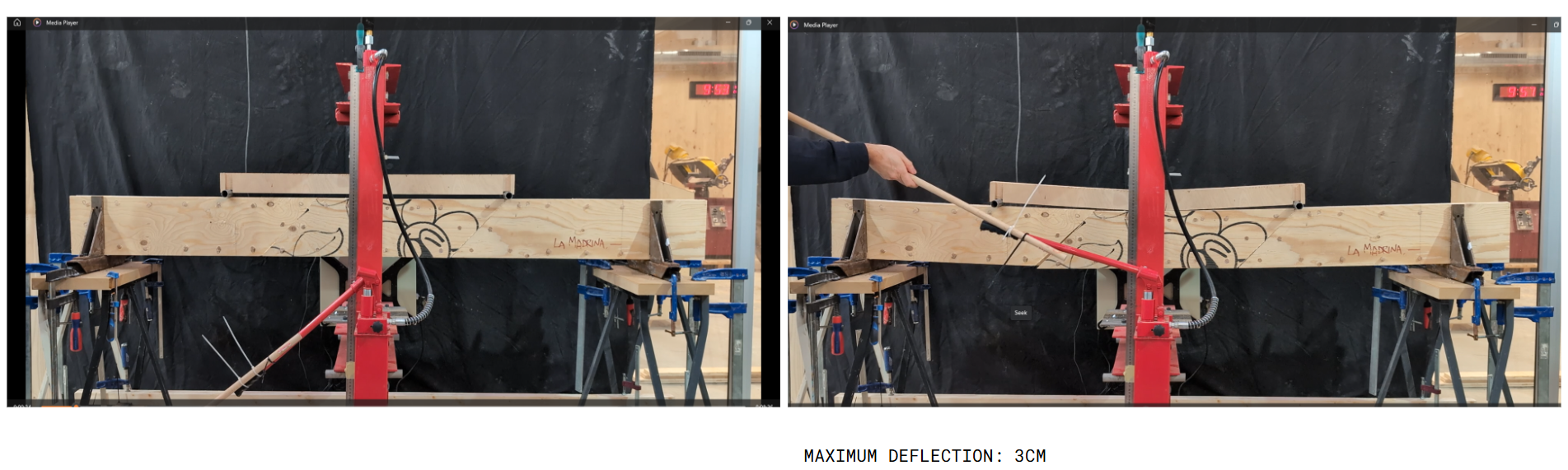
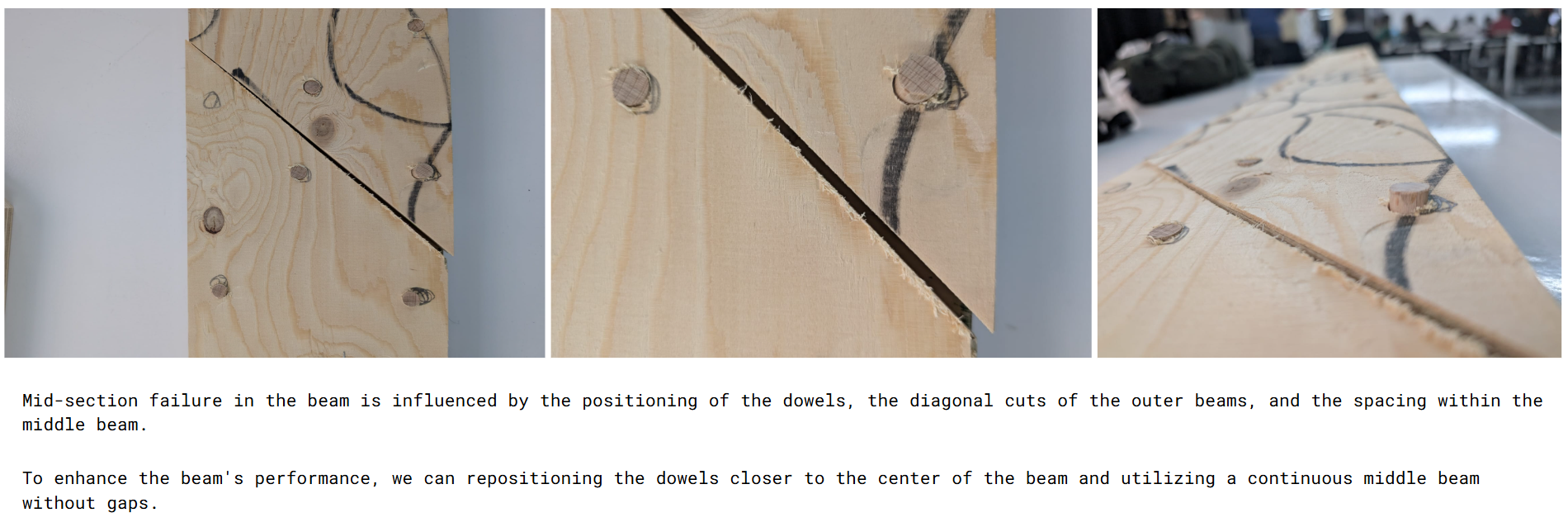
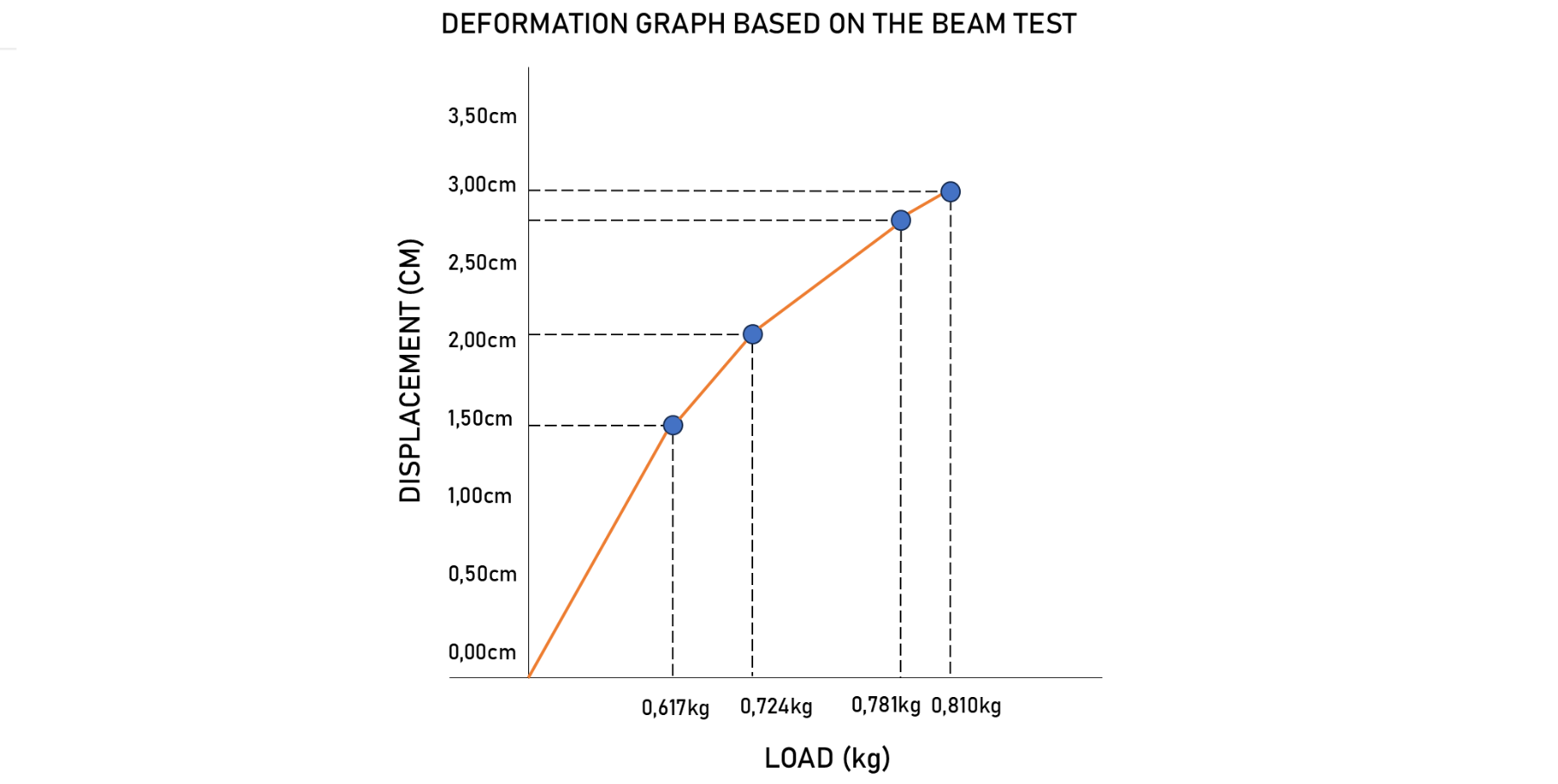
Engineering Analysis of the Beam – Karamba Analysis
The beam was modelled in form of a plan and an elevation. The script was set up with certain parameters involving loads acting on the beam. We experimented with two options, one with the center layer having no gaps and the other having center layer of two gaps of 50mm.
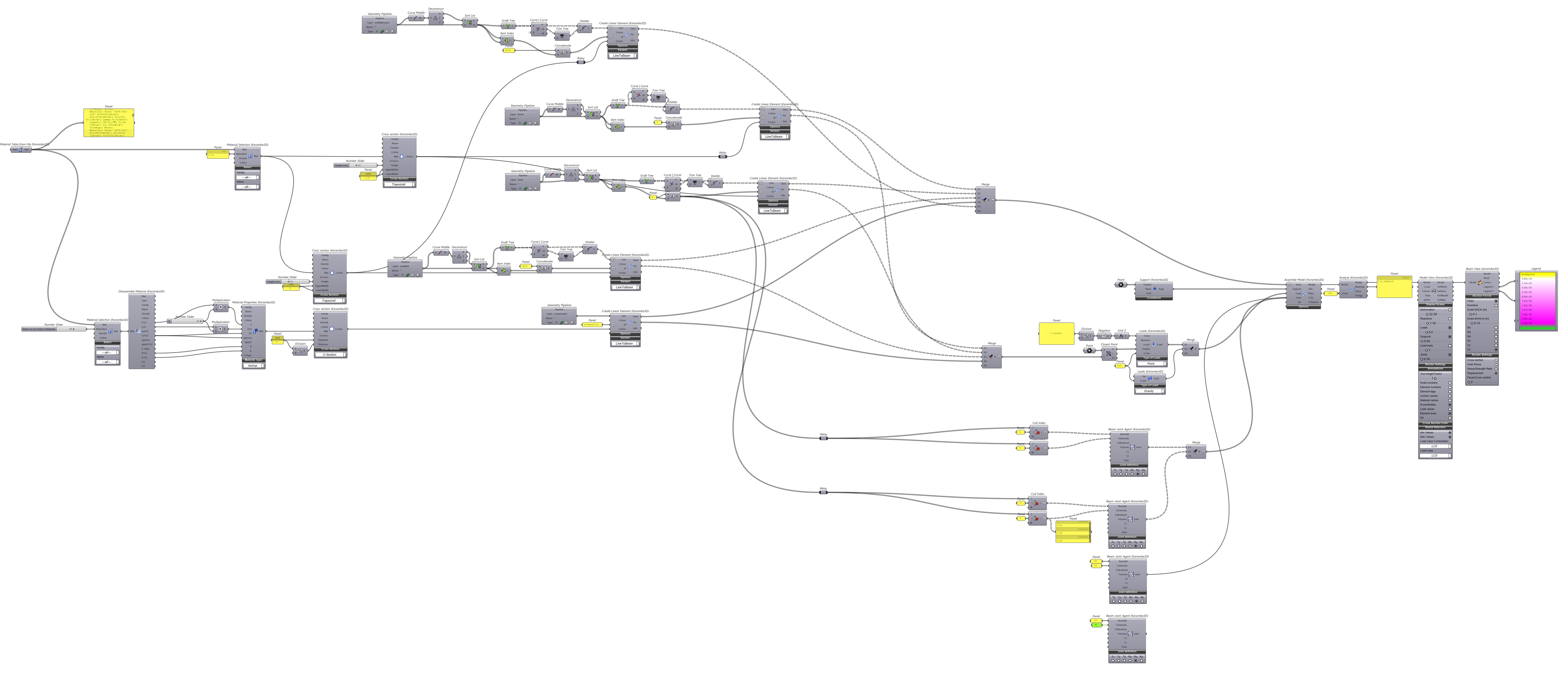
Results of the no gap timber beam using Karamba 3D analysis.
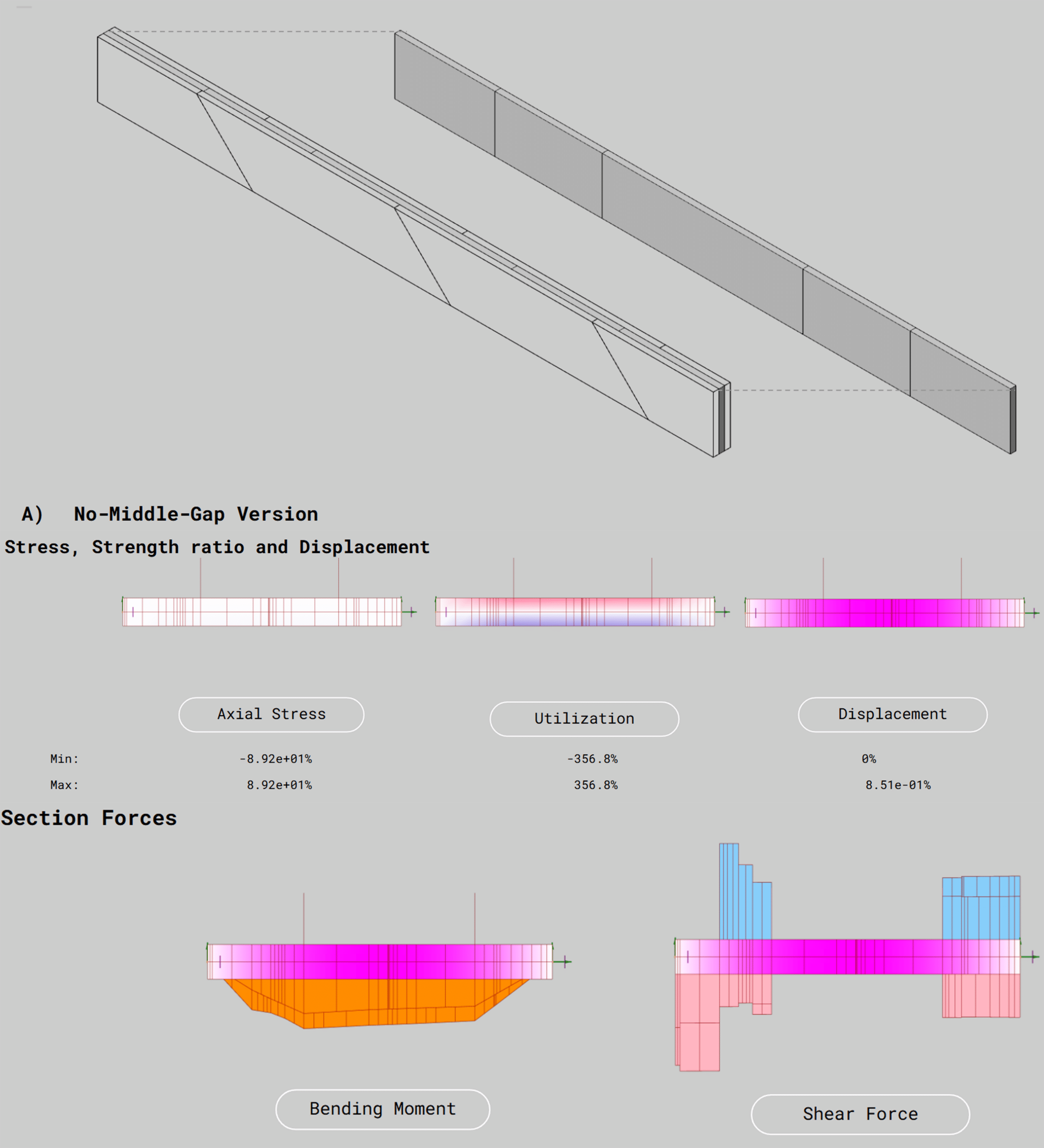
In the second beam, the center layer of timber plywood, there’s a 50mm gap between the 18mm thick beam. Using Karamba3D analysis we received results.
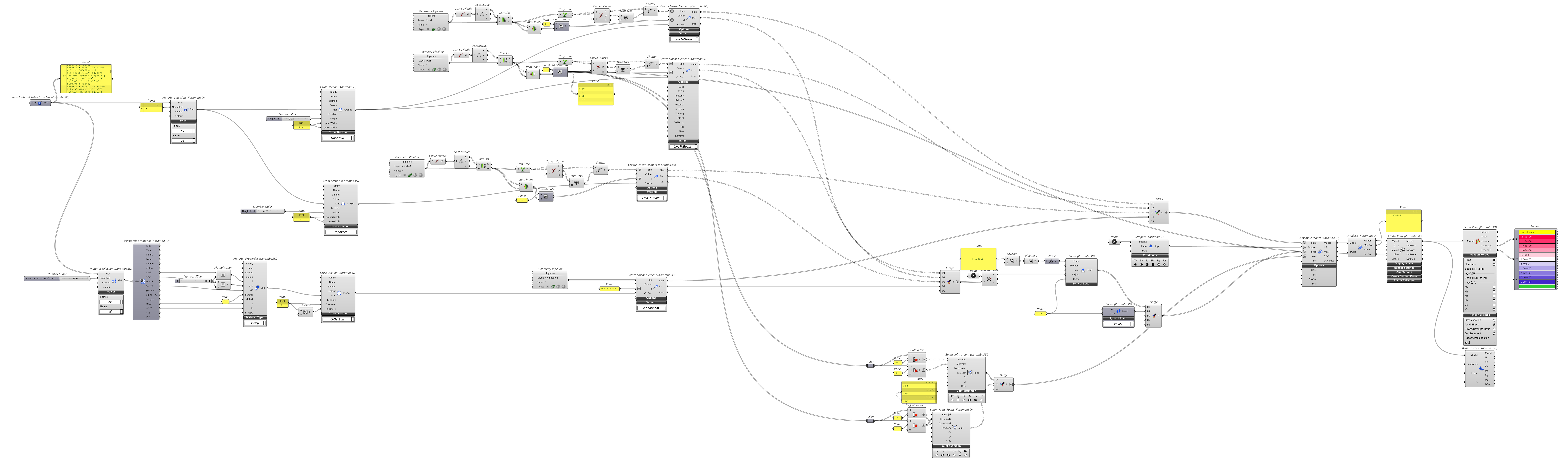
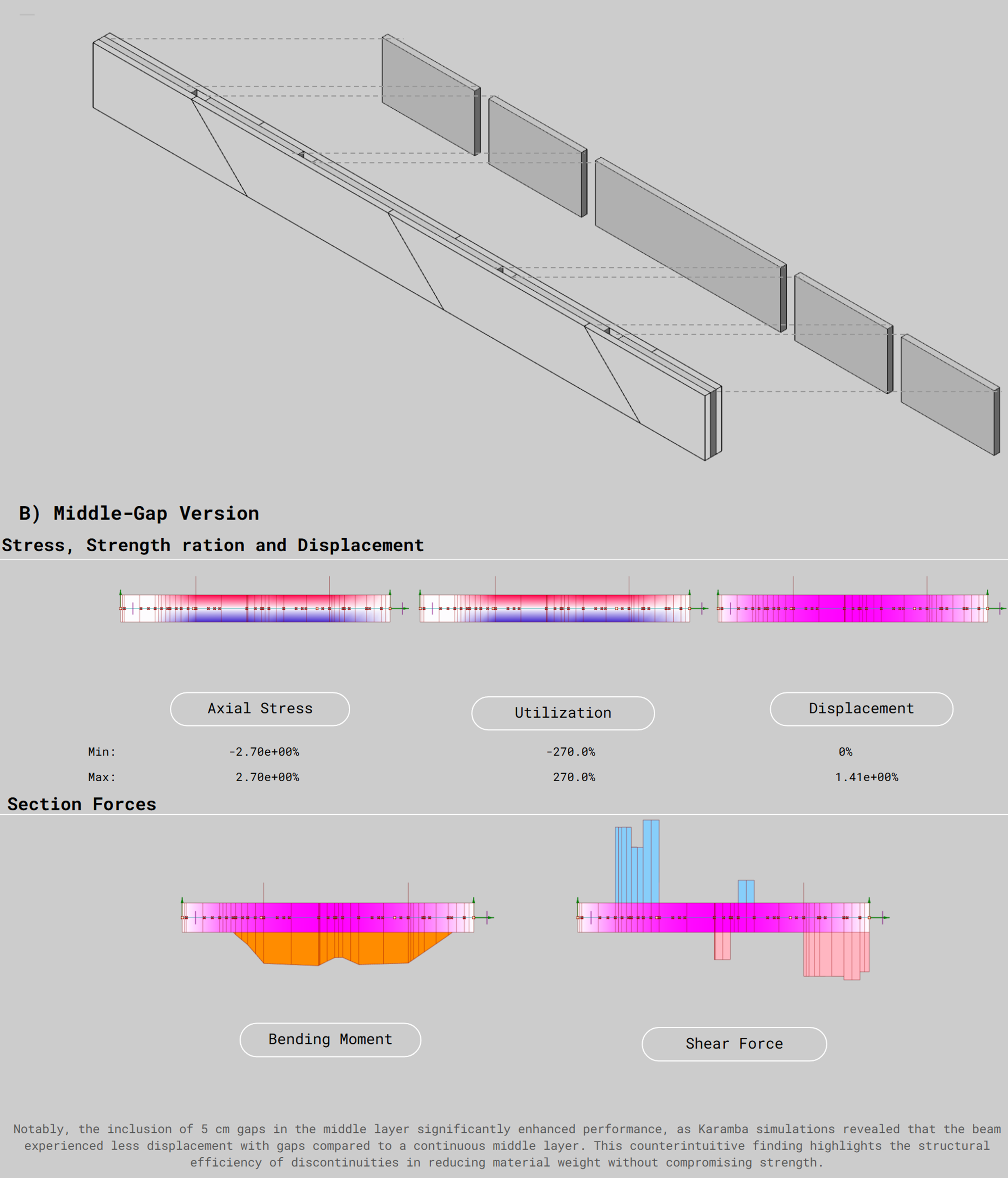
The dowels in the beam were also attentively tested using Karamba3d scripting as it too would take in the stress from the external forces. During the simulation of the external force being applied on the beam. Individually, the dowels experienced compression and tension force within. Karamba3D tests were tested using lower number of dowels and higher number of dowels.
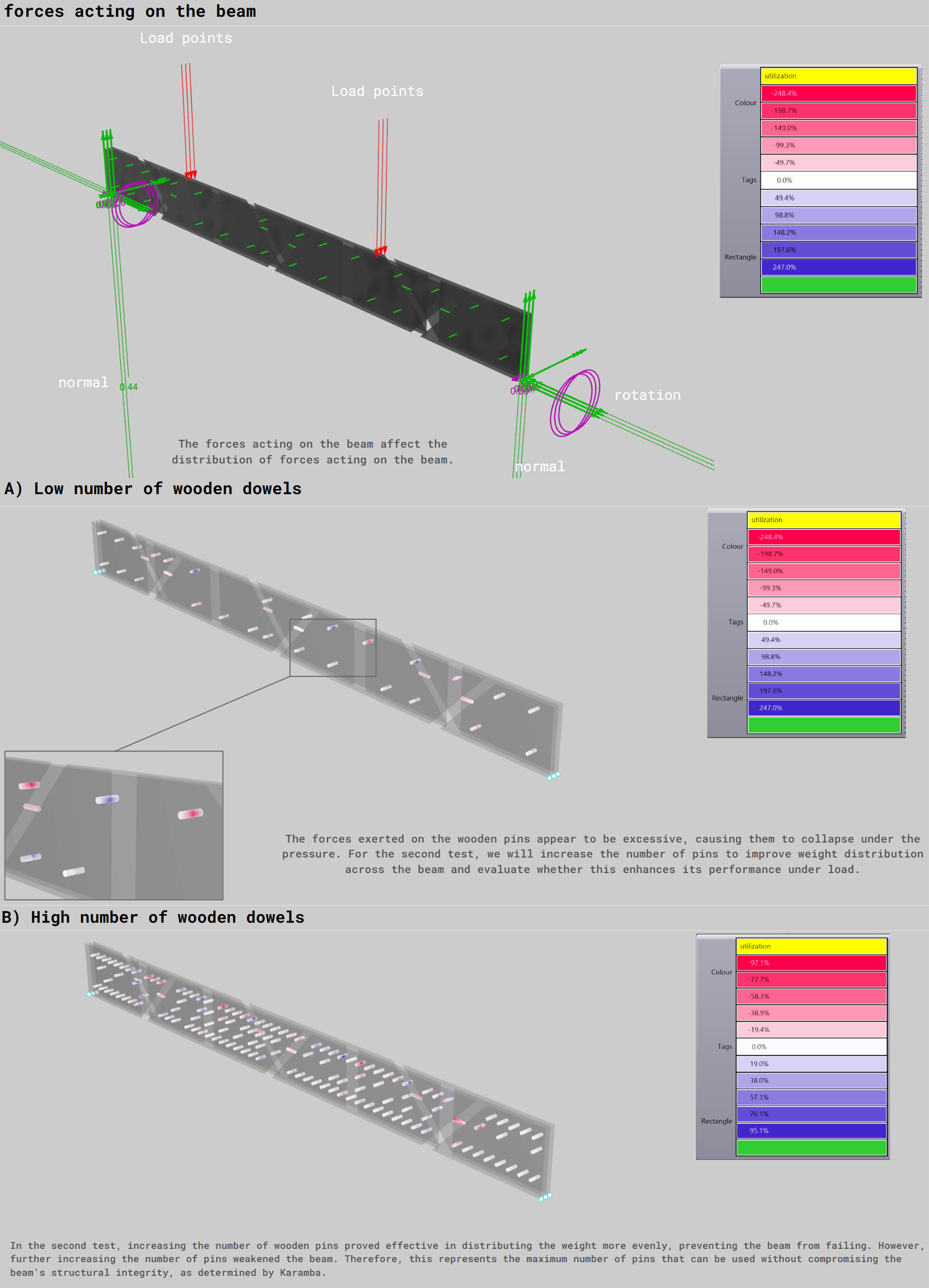
Engineering Analysis of the Beam – The difference between Physical test and Karamba3D
Other than Karamba3d analysis, a physical test on the prototype was performed using a machine to apply load on the Timber beam. The results varied compared to the karamba 3d analysis.
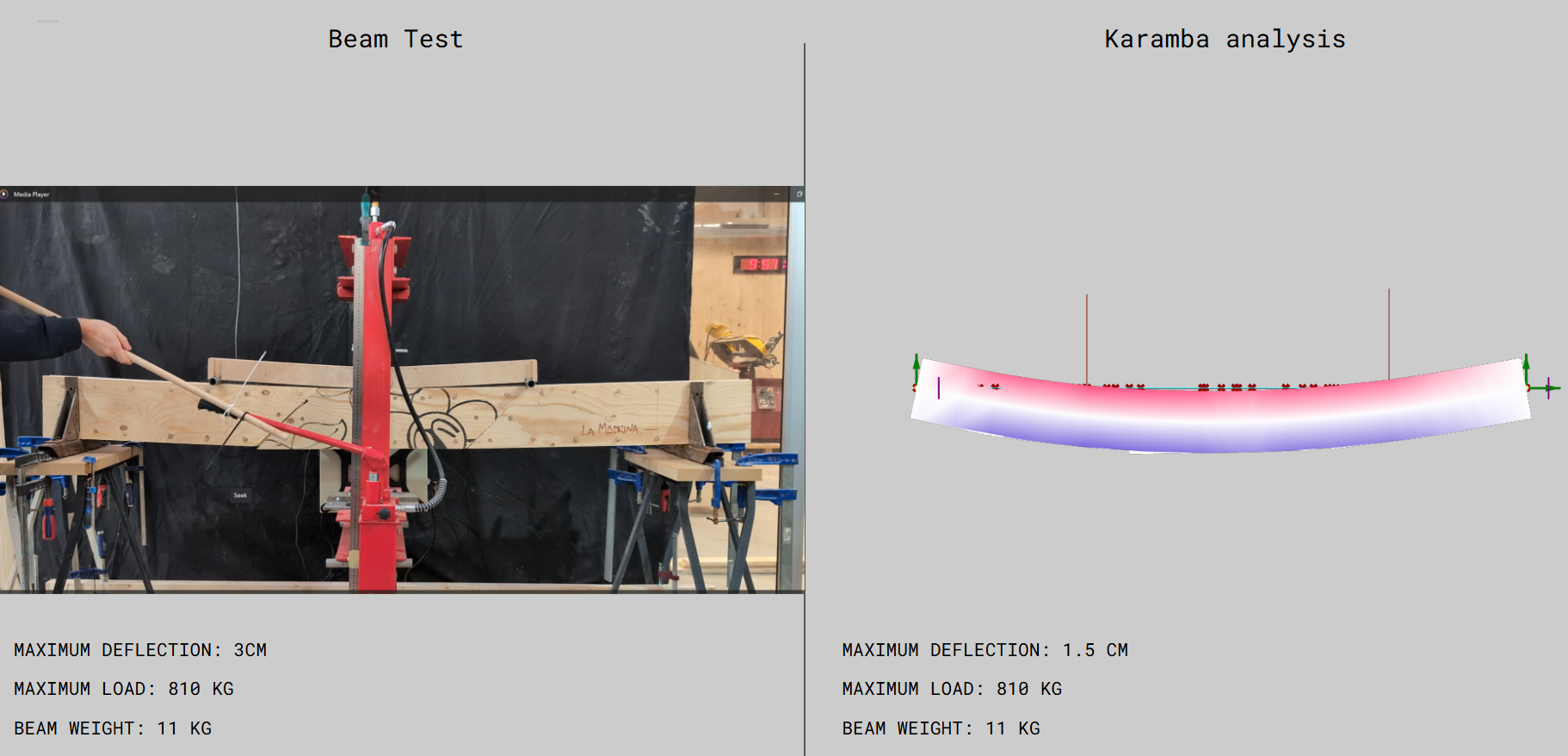
The difference between the physical testing and the karamba3D analysis was the maximum deflection of the beam. It can take maximum load of 810 kg, 73.63 times its own weight.
Engineering Analysis of the Beam – Embodied Carbon of the Beam
By utilizing recycled timber sourced independently, we effectively eliminated two significant contributors to embodied carbon: transportation and manufacturing. This allowed us to focus solely on calculating the embodied carbon of the beam based on the carbon content stored in the chosen material. Timber, known for its low embodied carbon value of 0.2589 CO₂ per kilogram, was used in this analysis. By multiplying this value by the weight of the beam, we determined an equivalent embodied carbon value of 0.236 CO2Kg/eq per Kg, as derived from the Karamba analysis
Weight of Carbon Timber CO2KG/eq x Weight of prototype beam = Embodied Carbon for the beam
0.236 kgC02E x 11 kg = 2.596 kgC02
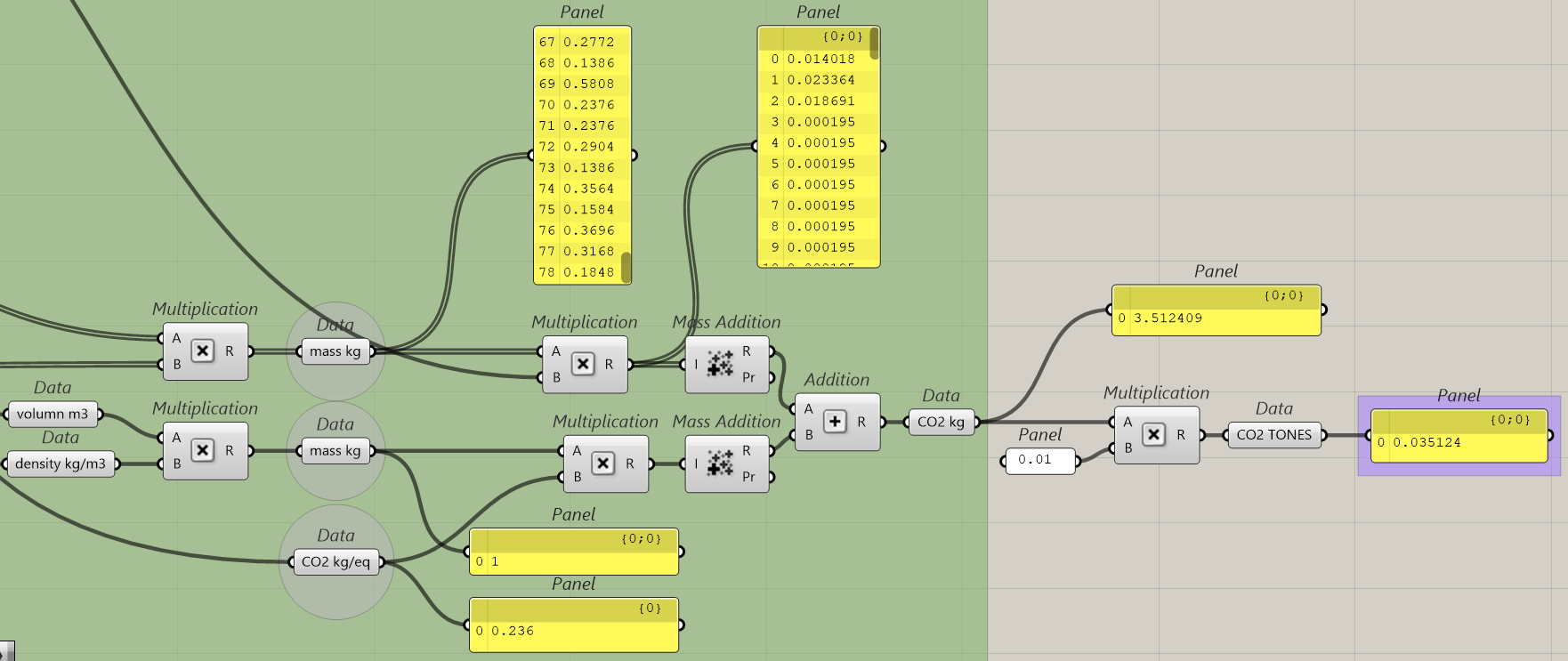
Conclusion
The design and testing of the 2.20-meter-long, three-layer plywood beam have yielded valuable insights into structural optimization and weight reduction. The beam, featuring diagonal outer layers (1.5 cm) and a thicker middle layer (2 cm), was engineered for strength under a two-point press test, with the longest panels strategically placed at the center.
Notably, the inclusion of 5 cm gaps in the middle layer significantly enhanced performance, as Karamba simulations revealed that the beam experienced less displacement with gaps compared to a continuous middle layer. This counterintuitive finding highlights the structural efficiency of discontinuities in reducing material weight without compromising strength.
The beam demonstrated impressive load resistance, withstanding 810 kg during physical testing, despite the failure of one dowel from the initial configuration of 44 dowels. Computational analysis suggested that increasing the dowel count to 120 would further enhance the beam’s structural integrity by improving stress distribution and minimizing localized weaknesses. However, at 11 kg, the beam’s weight presents a critical area for improvement, particularly for applications in weight-sensitive projects like the expansion of the Aravena initiative, where structural components must remain lightweight to align with existing constraints. Future iterations should focus on optimizing material usage and connection strategies to reduce weight while maintaining or enhancing strength.This study exemplifies the potential of integrating physical testing with parametric analysis tools like Karamba to achieve advanced, data-driven design improvements. By balancing strength, weight, and material efficiency, this approach offers a robust framework for refining structural components in resource-sensitive projects.