Funicular canopy
The aim pf the project is to design a funicular canopy on the IAAC rooftop using computational design tools.
State of the art
BUGA WOOD PAVILLION
ICD/ITKE
UNIVERSITY OF STUTTGART
The BUGA Wood Pavilion celebrates a new approach to digital timber construction. Its segmented wood shell is based on biological principles found in the plate skeleton of sea urchins, which have been studied by the Institute for Computational Design and Construction (ICD) and the Institute for Building Structures and Structural Design (ITKE) at the University of Stuttgart for almost a decade.
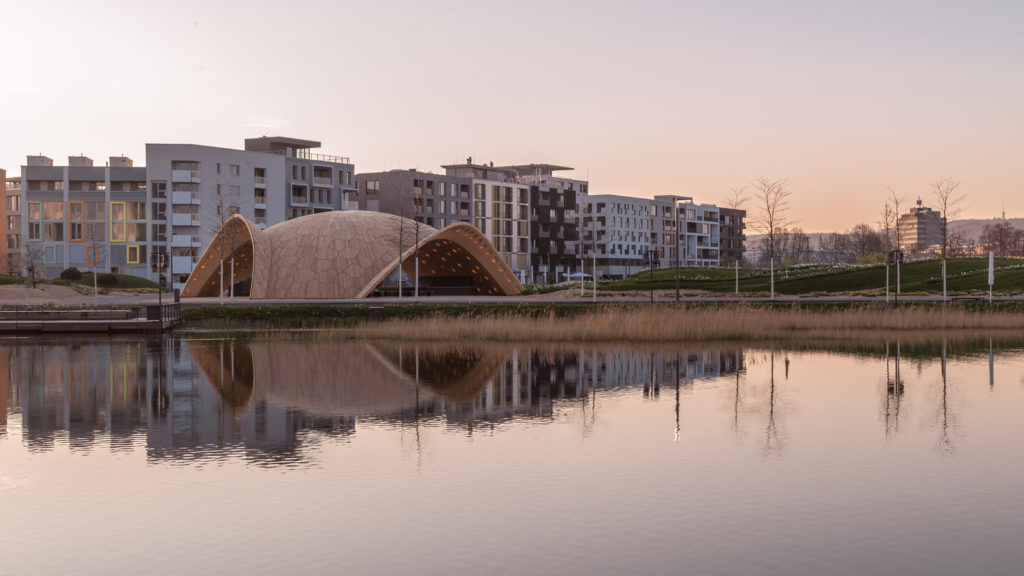
https://www.archdaily.com/916758/buga-wood-pavilion-icd-itke-university-of-stuttgart?ad_medium=gallery
The pavilion builds on the biomimetic principle of using “less material” by having “more form”, both on the level of the overall shell and its individual segments. In order to minimize material consumption and weight, each wood segment is built up from two thin plates that plank a ring of edge-beams on top and bottom, forming large scale hollow wooden cases with polygonal forms.
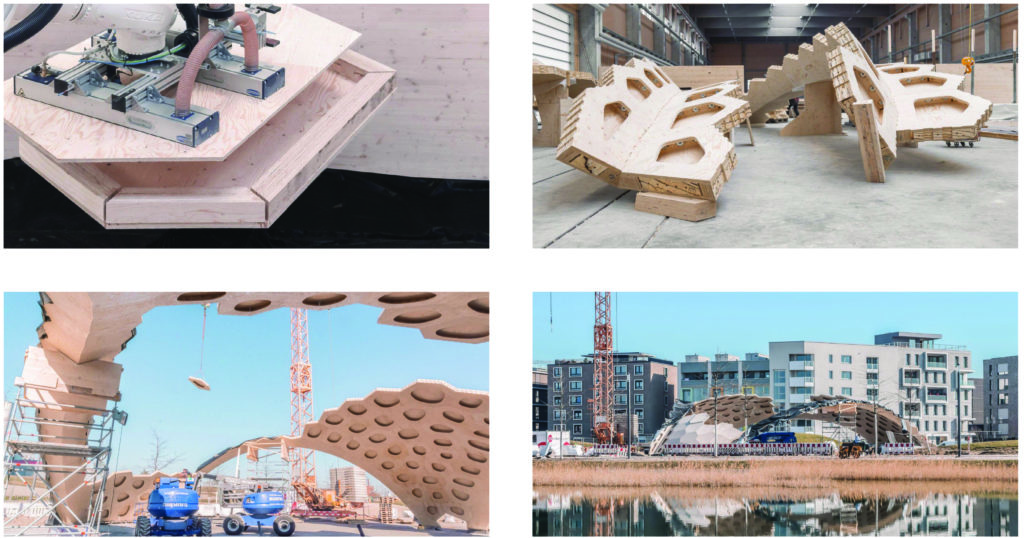
https://www.archdaily.com/916758/buga-wood-pavilion-icd-itke-university-of-stuttgart?ad_medium=gallery
Project
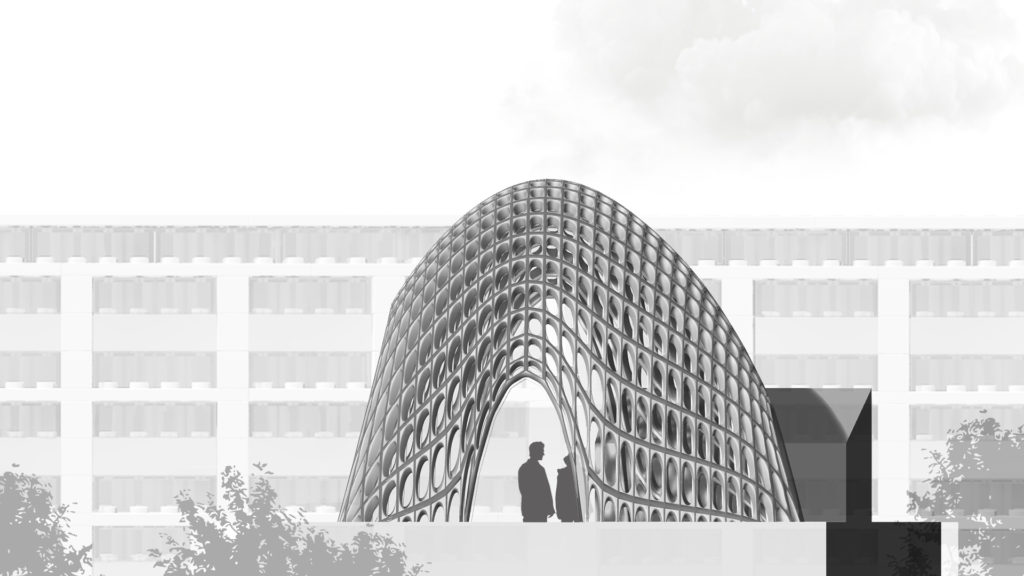
DEVELOPMENT PROCESS
- Started with a mesh plane of size 100 units x 75 units and sub-divisions of 20 and 30 to create a base mesh
- Define anchor points
- The mesh geometry is further transformed using weavebird’s picture frame, mesh thickness and stellate /cumulation to modify the geometry according to the design
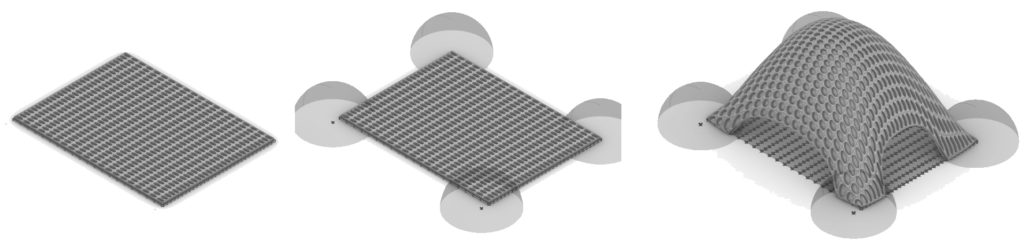
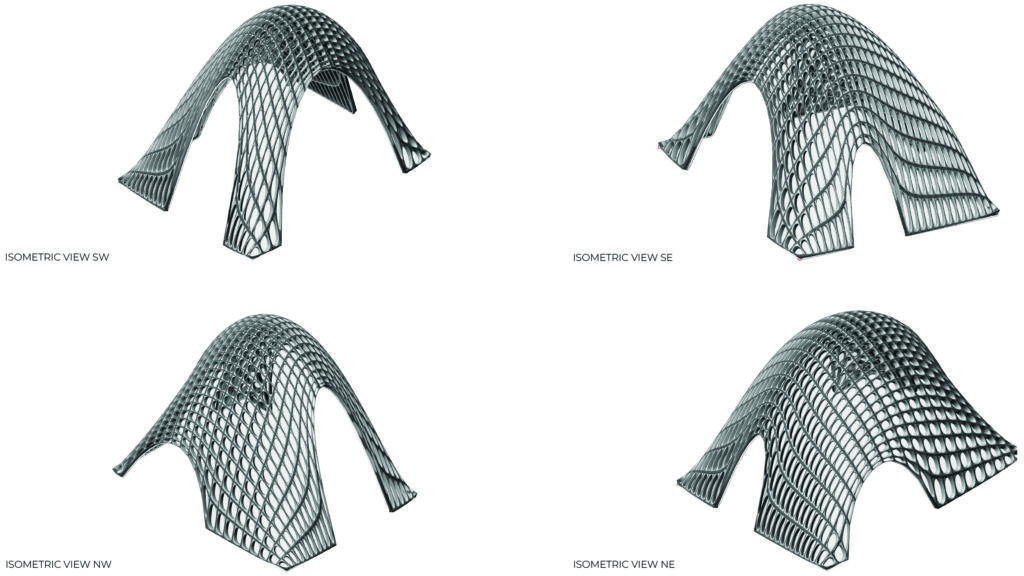
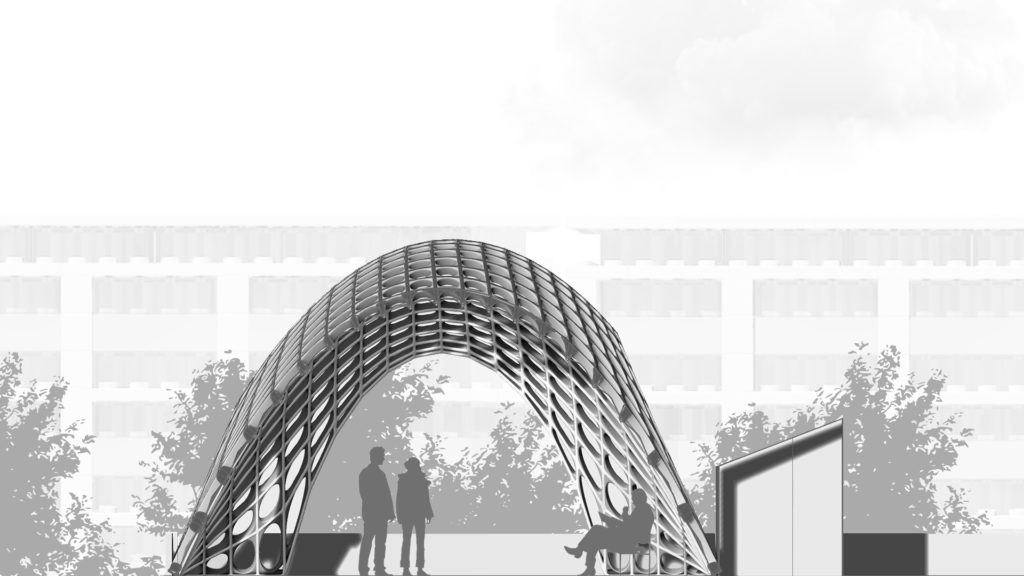
Pseudo code
- Started with a mesh plane of size 100 units x 75 units and sub-divisions of 20 and 30 to create a base mesh
- The next step is to assign goals beginning with the show, edge length, and load goals.
- Connect the base mesh to show and edge length goals keeping the length factor between 0 to 1
- By deconstructing the base mesh, we take the vertices and connect them to load goals to set the force vector at the z-axis so that the load goal will pull the mesh in the z-direction and the edge length function keeps the mesh edges from expanding indefinitely
- Define anchor point
- To identify the anchor points, we draw the points in the rhino viewport and reference them in grasshopper making sure they are being assigned near the naked edges
- Used these points to make spheres of radius 17 units. This radius value will control the number of points assigned as anchors
- Using the naked vertices component to identify naked points
- Connected the naked points and spheres to Breps component to dispatch the list of naked points into two lists in which list A contains naked points that are within the spheres which act as anchor points using the anchor goal
- Using the anchor XYZ goal and connect it with dispatch list B that are the naked points which are not anchored and provide it with boolean inputs as true towards x and y direction and merge it with the bouncy solver to control the mesh geometry.
- After defining all the goals, merge all goals and connect the output to the bouncy solver
- Reset and enable the solver#
- Used list item to extract the mesh vault geometry
- After all, the mesh geometry is further transformed using weavebird’s picture frame, mesh thickness and stellate /cumulation to modify the geometry according to the design
- To avoid the mesh edges leaning inwards, we assign movement-based constraint goals
- Later, we used mesh boundary and multi-pipe components to get the mesh vertices and edges to give a structural framework
Constructive system
FUNICULAR STRUCTURES USING TOPOLOGICAL ASSEMBLIES
The structural system is dry construction for funicular forms using topological assemblies. It is self-supporting system and it uses minimum scaffolding for erection.
The modules can be assembled and dismantled as required and transported to various locations. Moreover, the modules can be reused, following the principle of design for disassembly.
Cost of such constructions and the time are optimized by customization, minimizing on scaffolding and avoiding layers of construction as compared with the Catalan tile vaulting.

https://www.semanticscholar.org/paper/Funicular-Shell-Design-Exploration-Rippmann-Block/bc92b1137d68e105189cc901ad79b9334ec58fe3
Fabrication protocol
The idea for the fabrication and assembly is excerpted from the State Of the Art, BUGA pavilion.
Using the computational tools, puzzle shaped segments would be 3D printed using the recycled plastics.
Robotic manufacturing platform would automatically assemble 3D printed segments. This fabrication process ensures that all segments fit together with sub-millimeter precision like a big, three-dimensional puzzle.
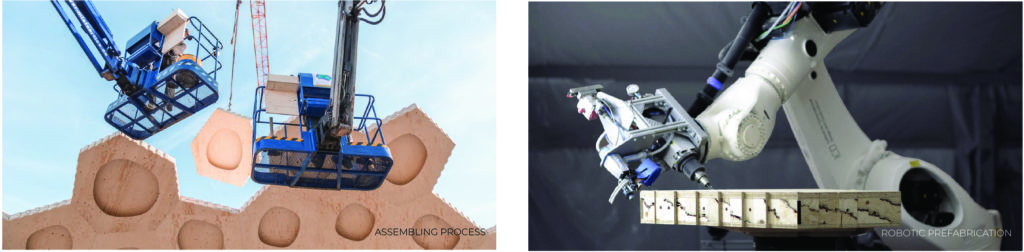
https://www.archdaily.com/916758/buga-wood-pavilion-icd-itke-university-of-stuttgart?ad_medium=gallery
Project vision
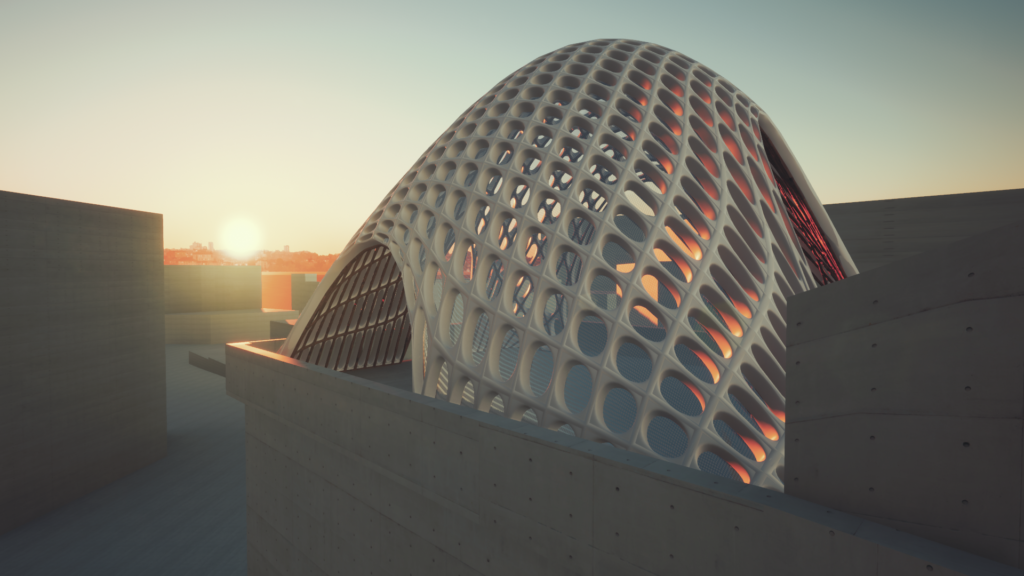
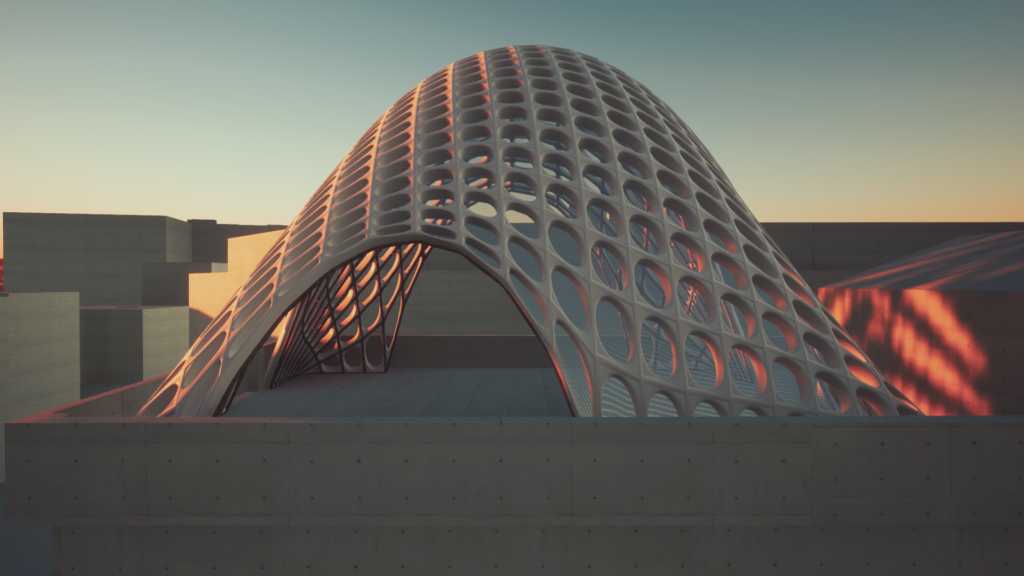
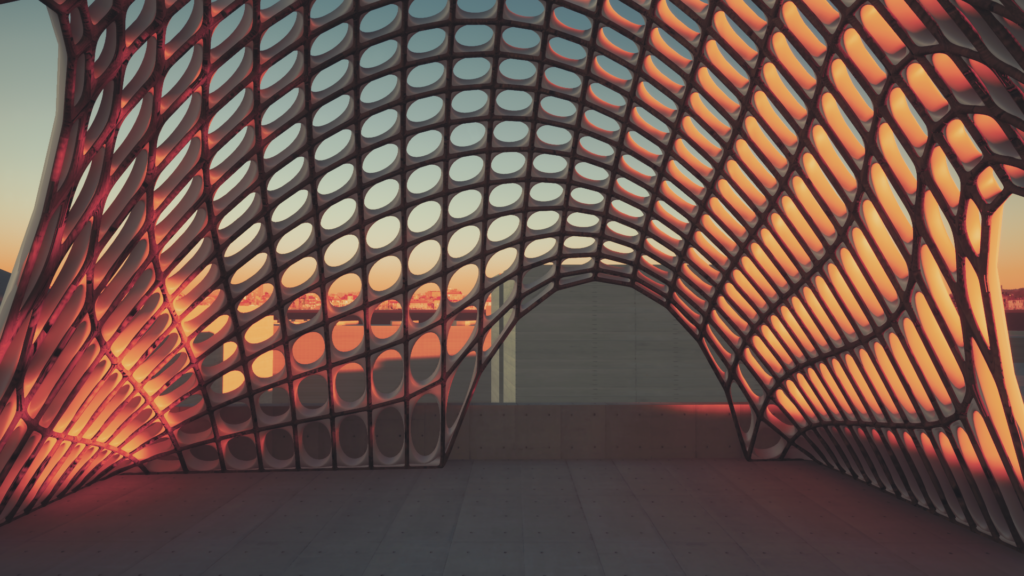
Video