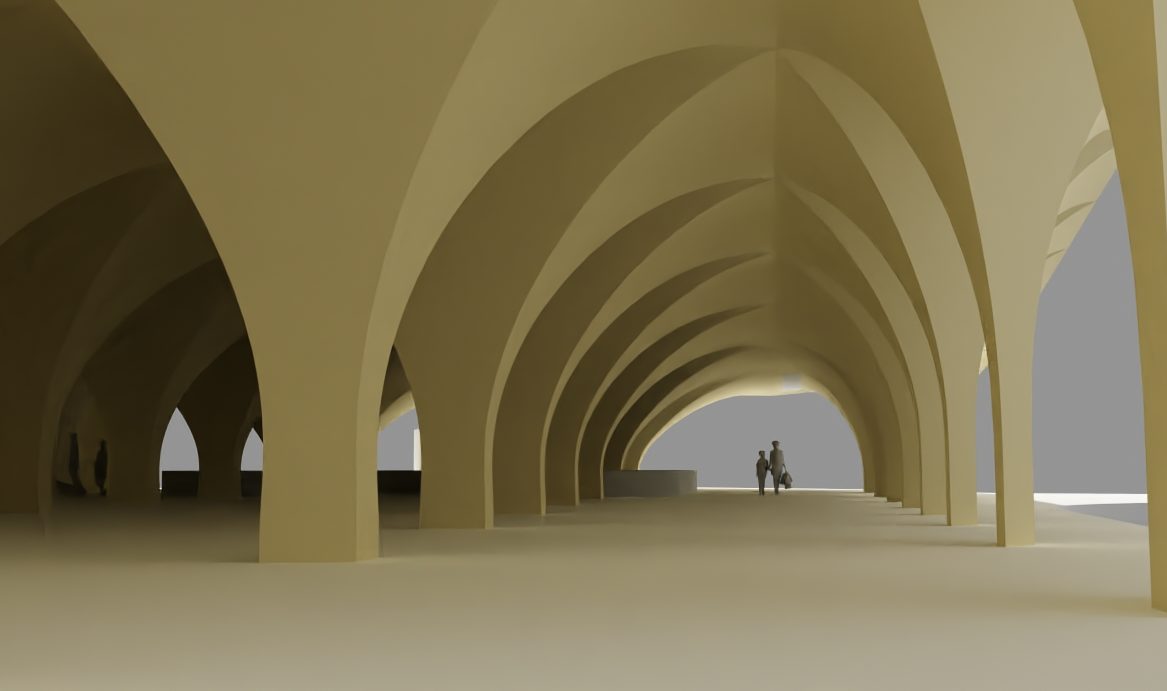
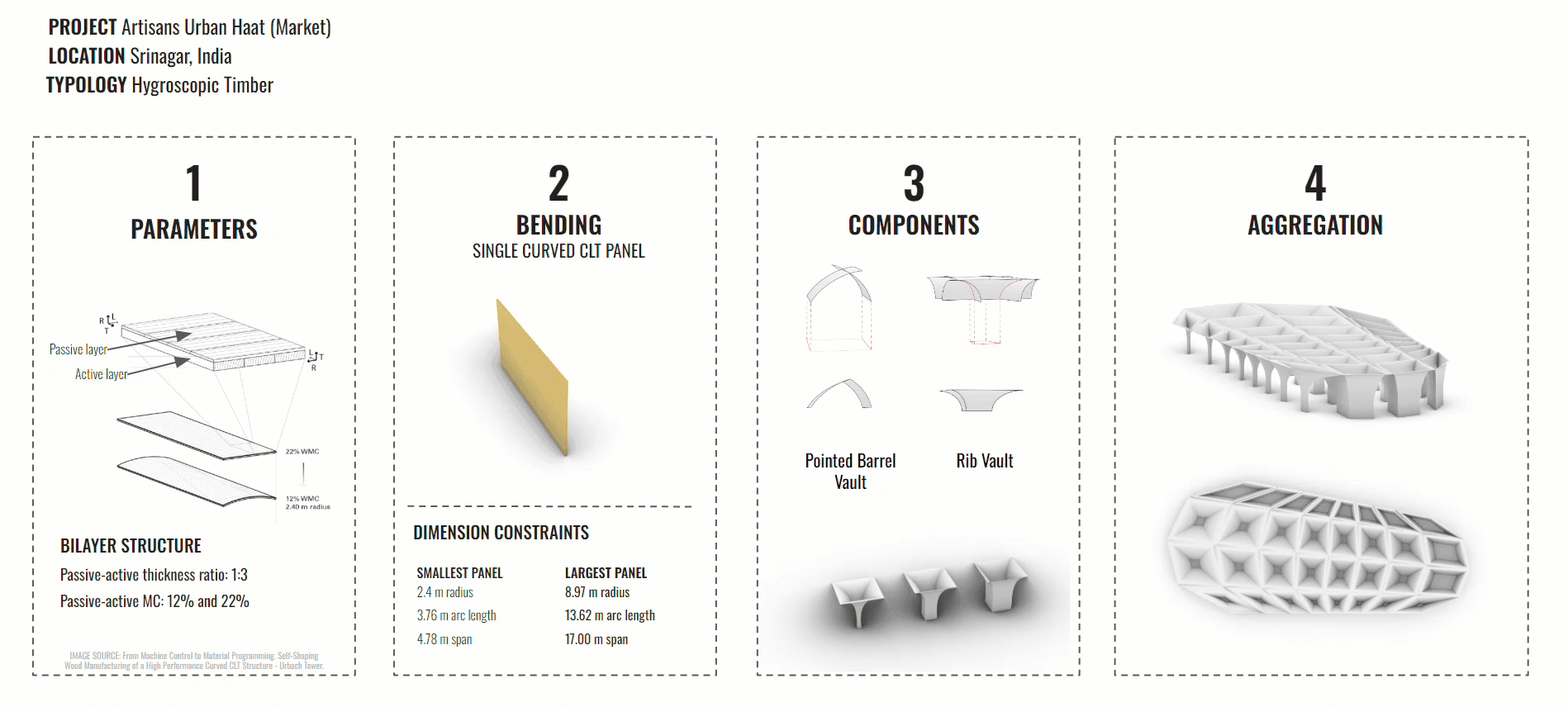
Our project is an artisan market within a cultural centre in Srinagar, India.
In our initial analysis of hygroscopic timber, we identified key factors influencing its behaviour. The bilayer structure, consisting of an active and a passive layer, allows panels to deform in response to moisture content changes. We also found a third locking layer that prevents bending back. However, we observed a limitation: we can only use single-curved panels.
To address this limitation, we developed components of multiple single-curved panels. This modular approach enables us to adjust panel curvature and covered areas based on program requirements.
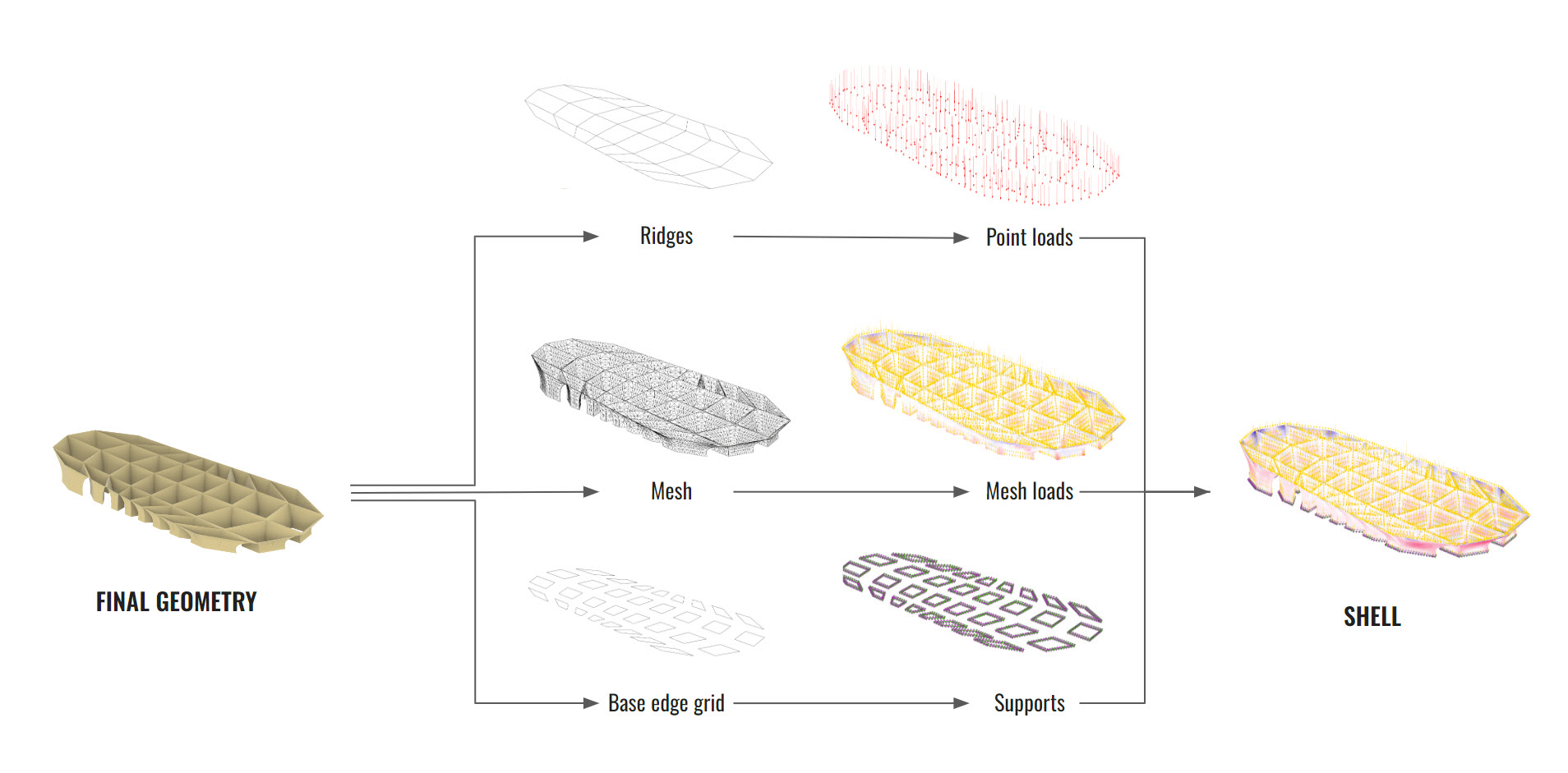
We used the final architectural program’s geometry to create the Finite Element (FE) model. We transformed single-curved panels into meshes to calculate and apply point loads for the roof on mesh ridges. The base edges of each panel were segmented into discrete support points.
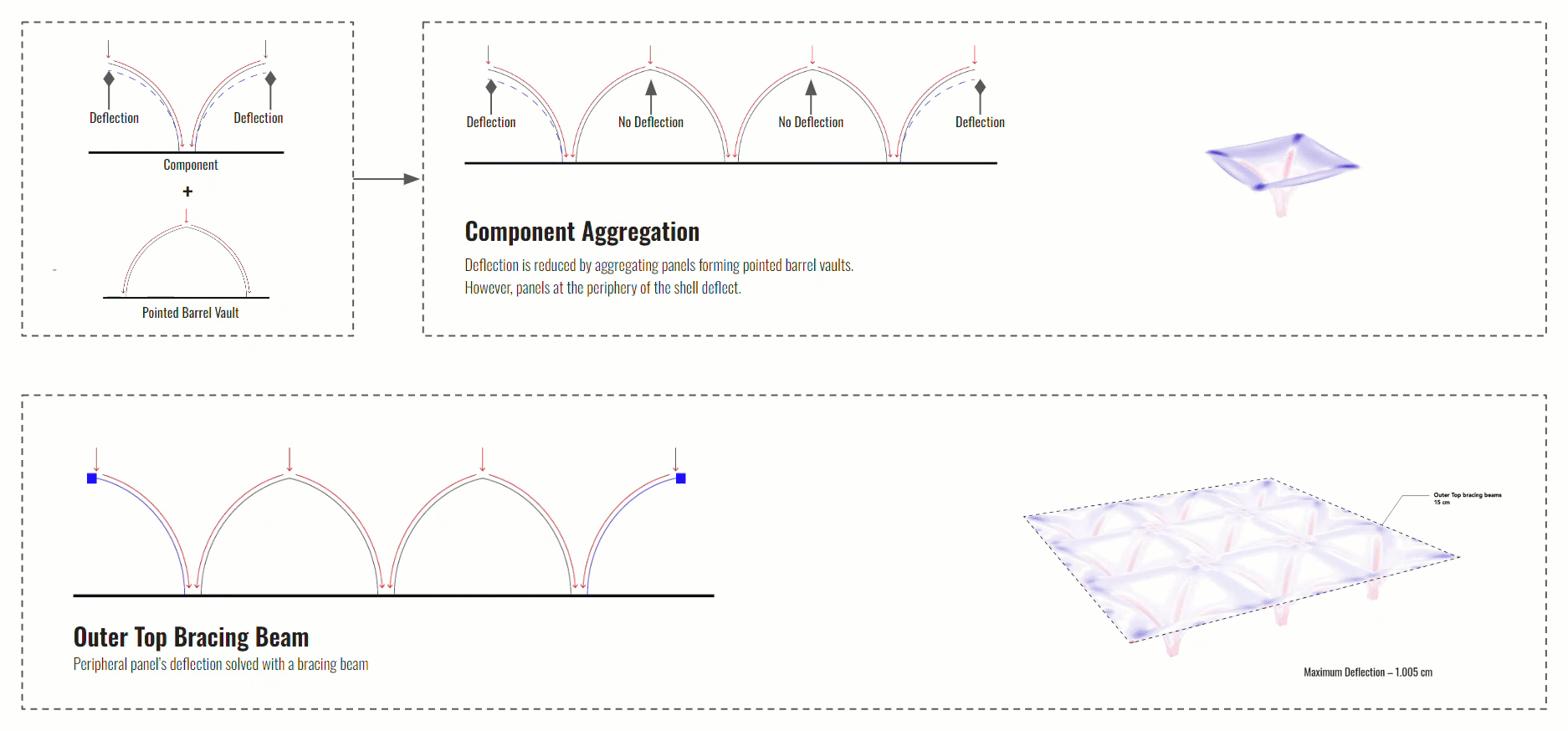
Our analysis observed that the single elements fail at the top free edges under load conditions. We applied the pointed-barrel vault load transfer principle to mitigate this, reducing internal edge deflection. However, the outer free edge still posed a challenge, leading us to introduce bracing beams for structural stability.
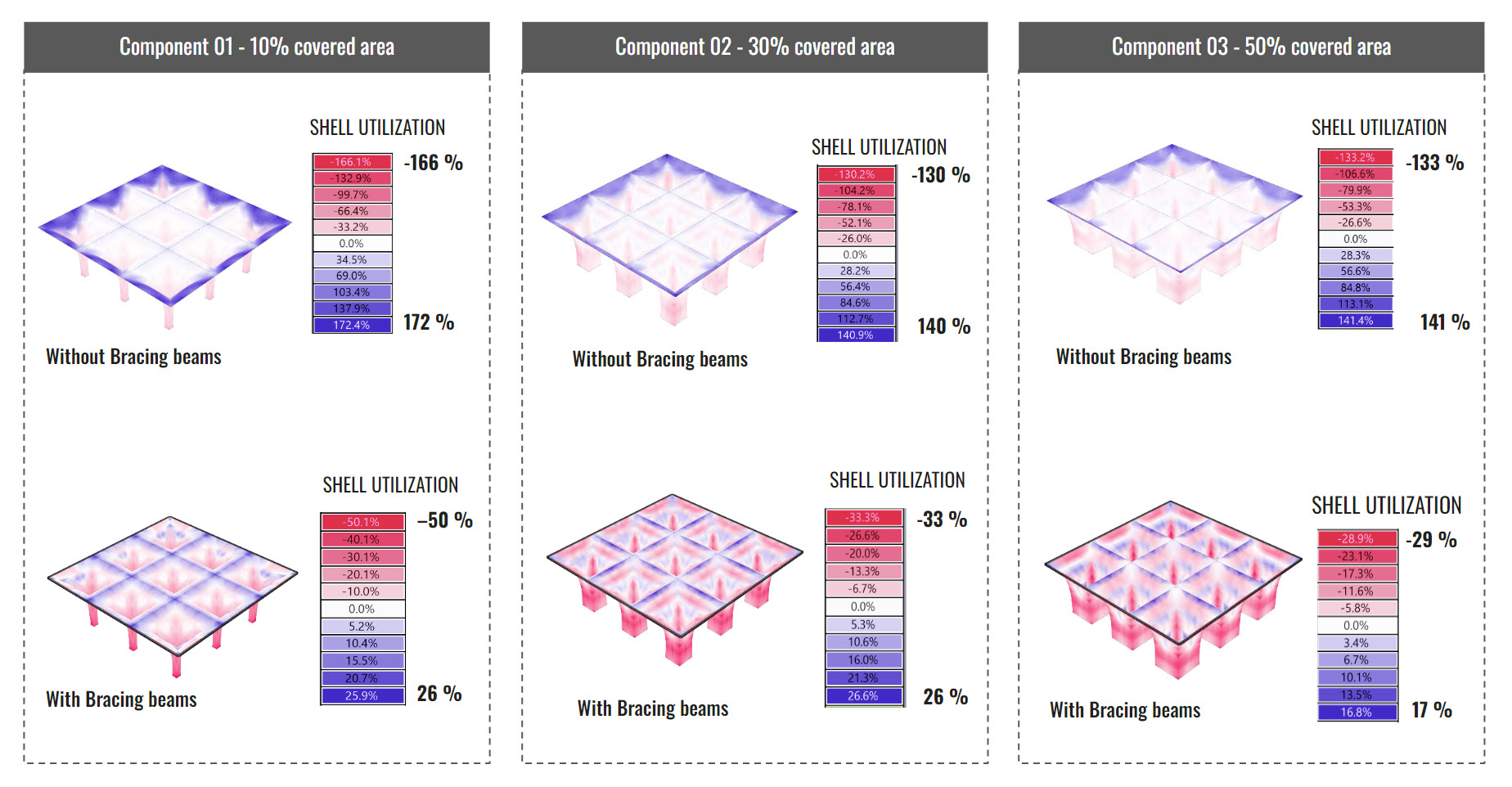
Architecturally, we required three spaces: open views, circulation areas, and enclosed spaces. We designed three prototypes using 9 rectangular components, each with a 1cm cross-section. Utilization exceeded 100% for all prototypes, with the top free edges most affected. The addition of bracing beams improved edge utilization.
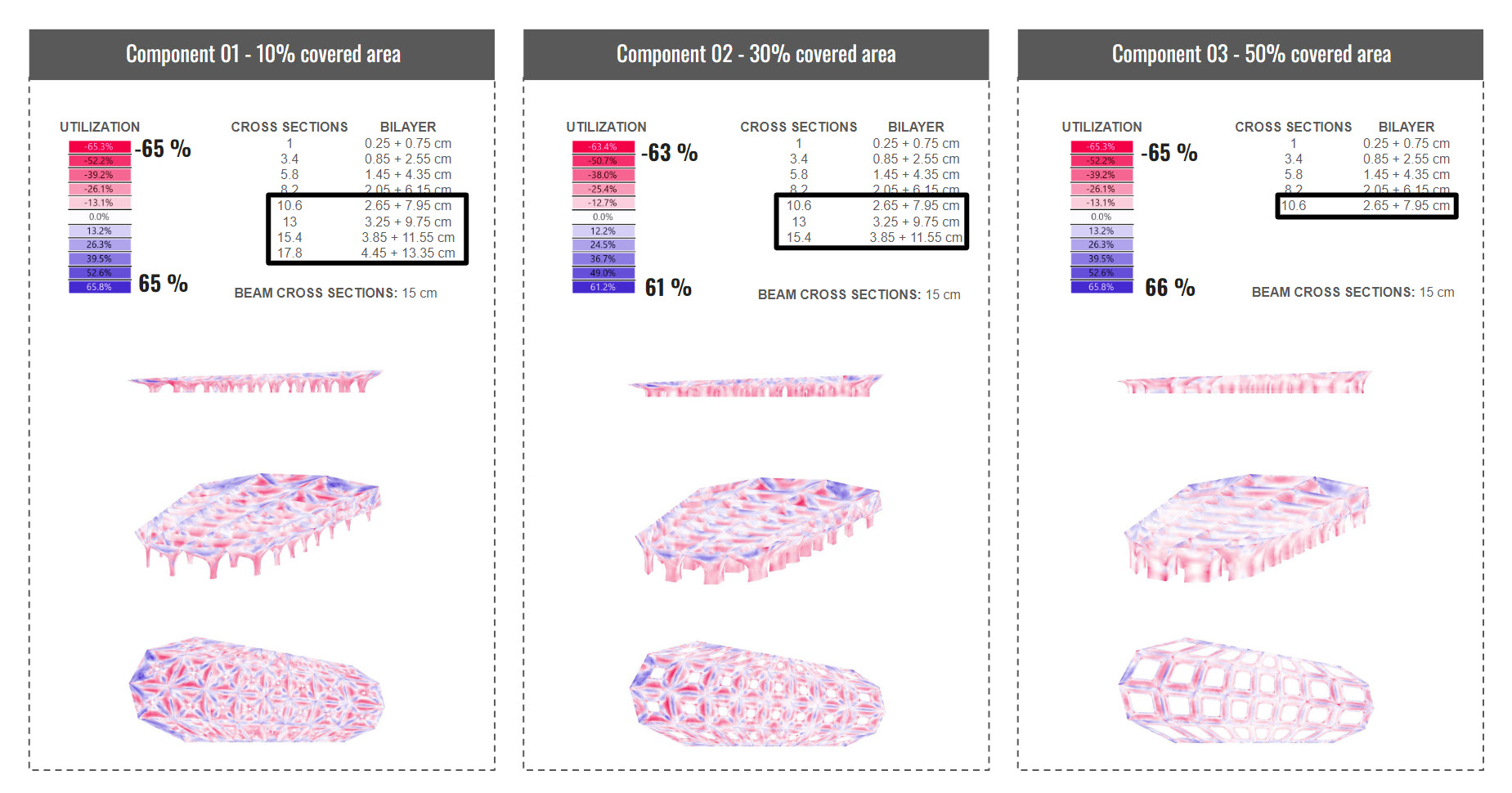
In the second stage, we used Karamba to optimize the cross-sections of the panels composing the components. While vault barrel strength allowed for sections as thin as 1cm, practical considerations limited us to sections thicker than 2cm. Bracing top beams had a 15 cm thick cross-section in the optimized designs.
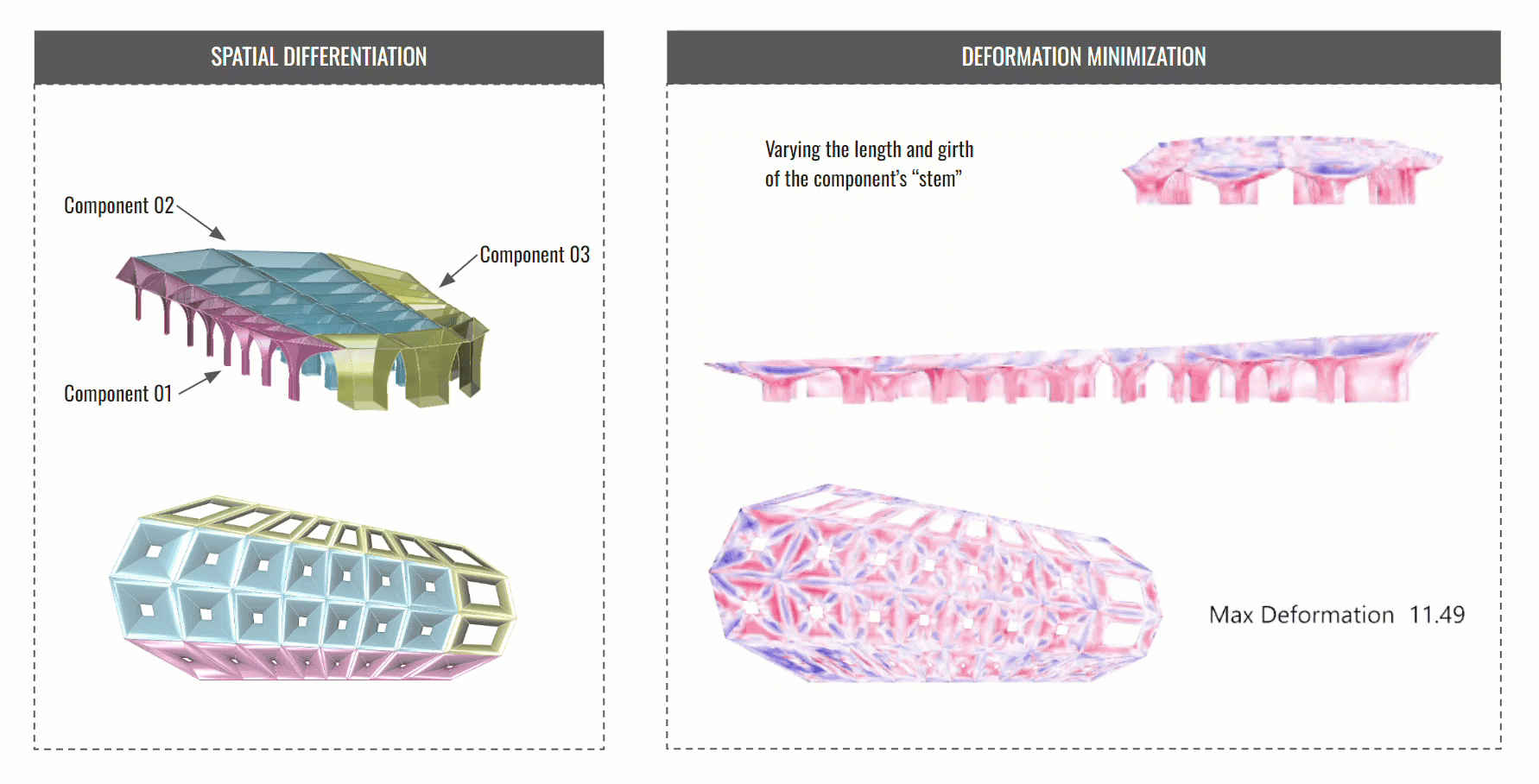
In the next phase, we used the genetic algorithm Galapagos to minimize general deformation by varying the length and girth of the component’s “stems.” We achieved a maximum deformation value of 5.54, and buckling was the next focus.
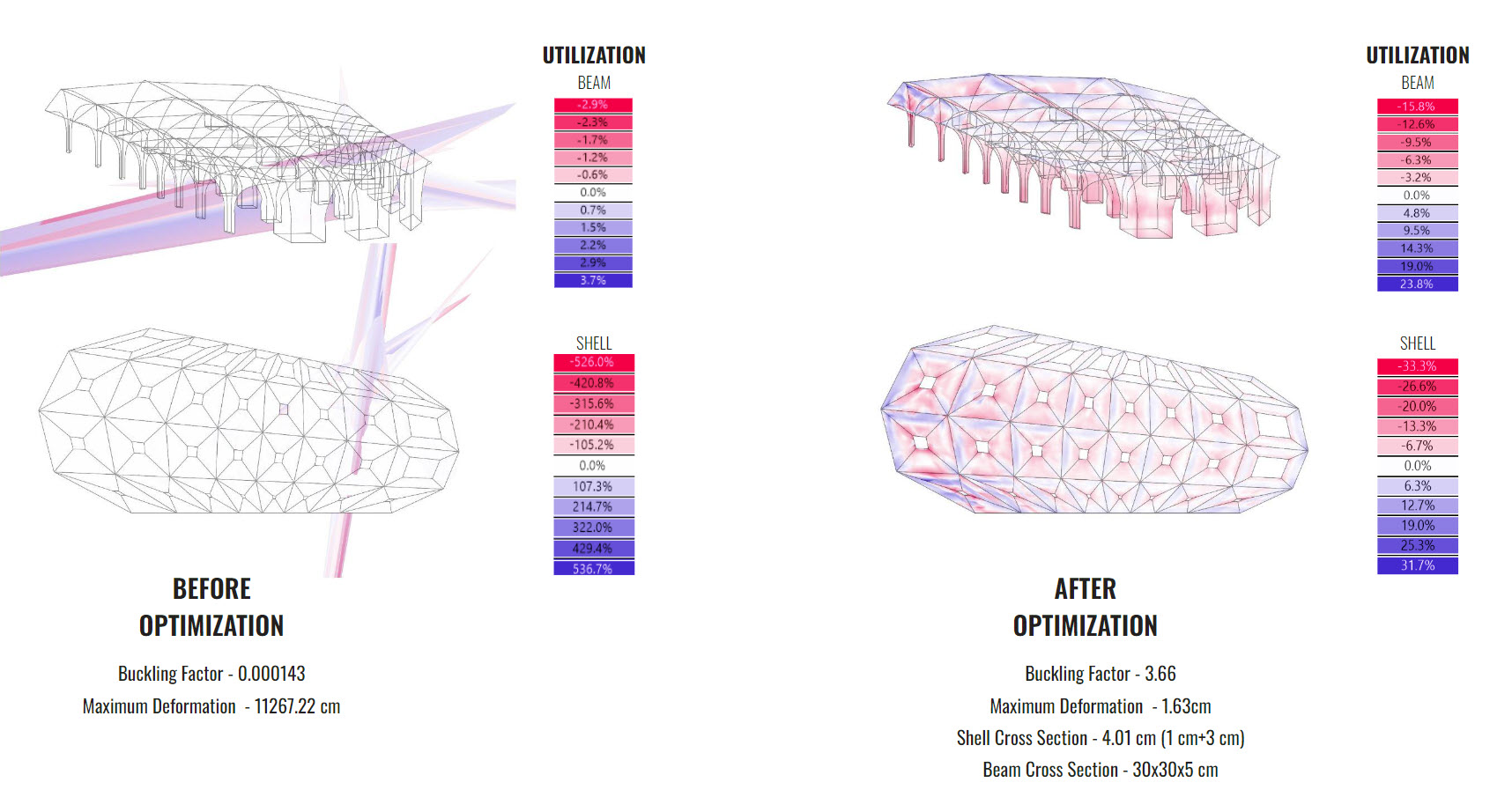
Initially, our model experienced buckling issues with a maximum deformation of 1.1m. We optimized the buckling factor to 3.66, reducing deformation to 1.63cm, resulting in a stable structure. The optimized structure featured a shell cross-section with a thickness of 4.01cm, including a 1.00cm thick passive layer and a 3.01cm thick active layer.
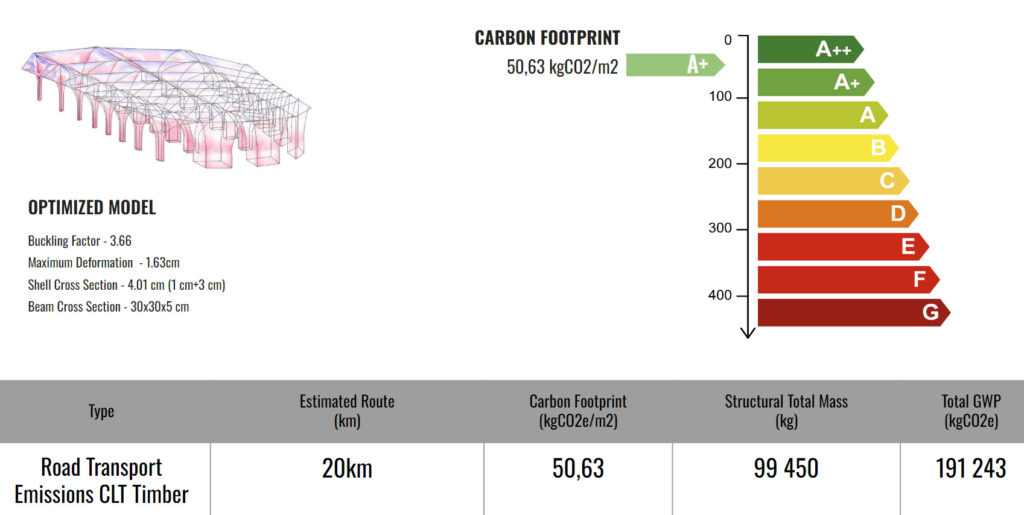
Finally, we calculated the CO2 footprint of our structure, which amounted to 50 kgCO2e/m2, falling between an A++ and A+ rating.