TECHNE: W3 – STRUCTURE workshop asks students to examine the structural behaviors inherent in 3D printing with clay and earth. Our goal for this week’s workshop was to print the tallest single and double surface structure that will be assessed against performance metrics such as toolpath length, print volume, print time, weight, collapse height, and an overall performance score.
As a class we embraced a process of rapidly prototyping structurally performative single surface geometries, that will provide us with a foundation of knowledge for structural concepts such as local and global mass, inertia, center of gravity (COG), and Finite Element Method (FEM).
Alongside this the class was introduced to structural simulation tools such as Karamba and IAAC’s 3DPA toolkit to provide an indication of how a geometry will perform during the printing process.
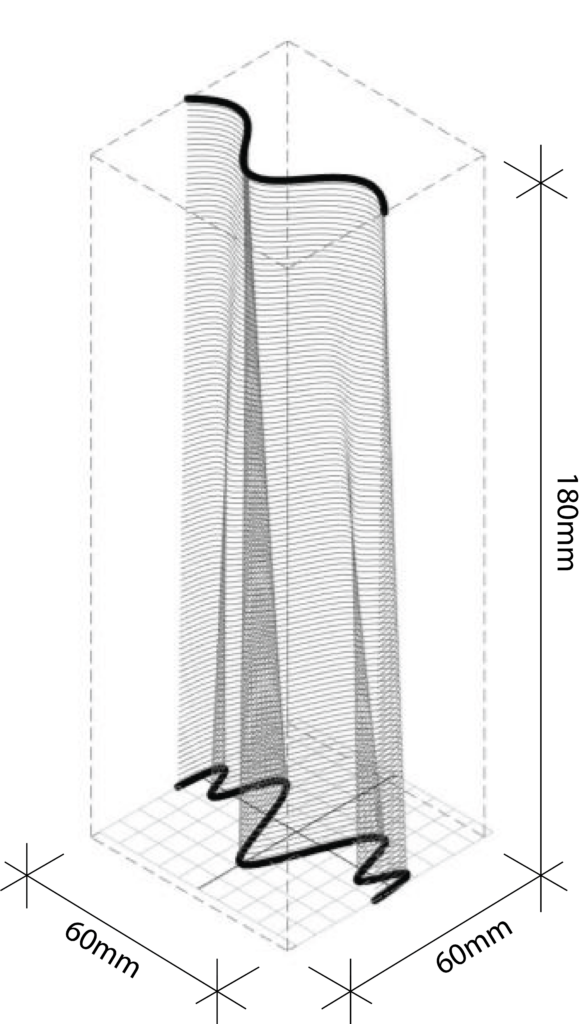
Simulation toolkit
While developing single surface geometries we had a toolkit that would would give us an indication of the geometries structural behavior.
Below are some of the simulation tools that were implemented throughout the week:
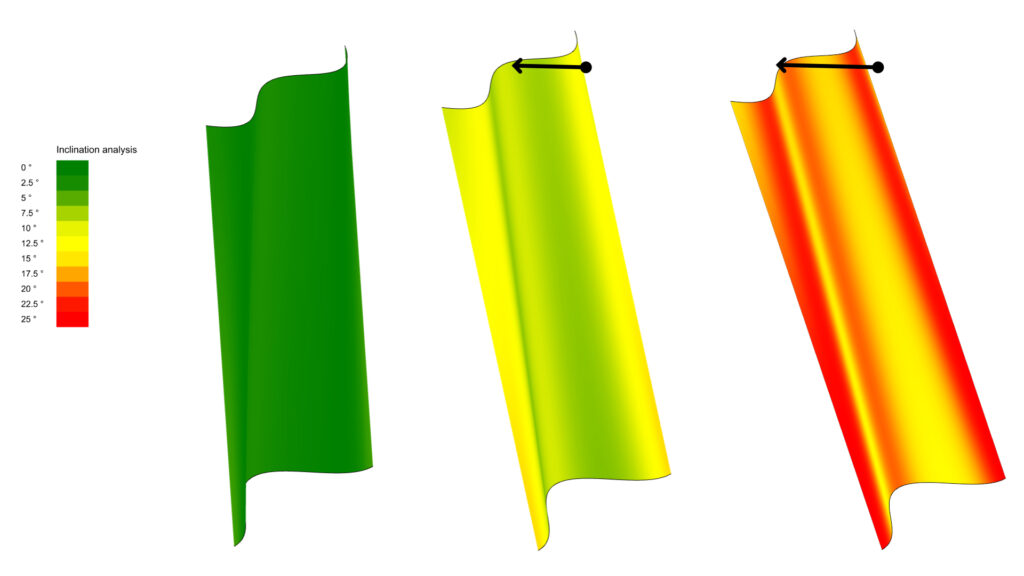
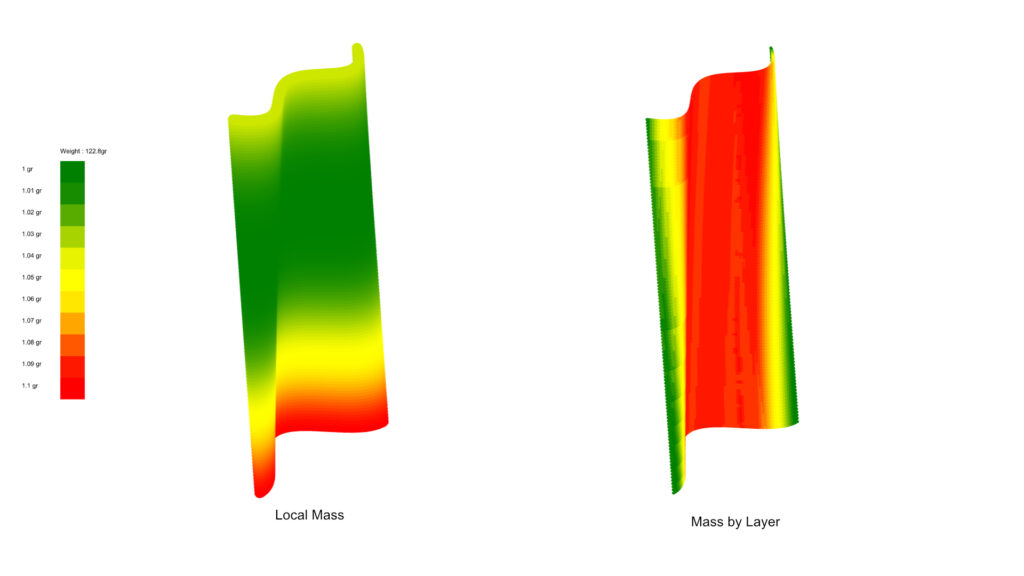
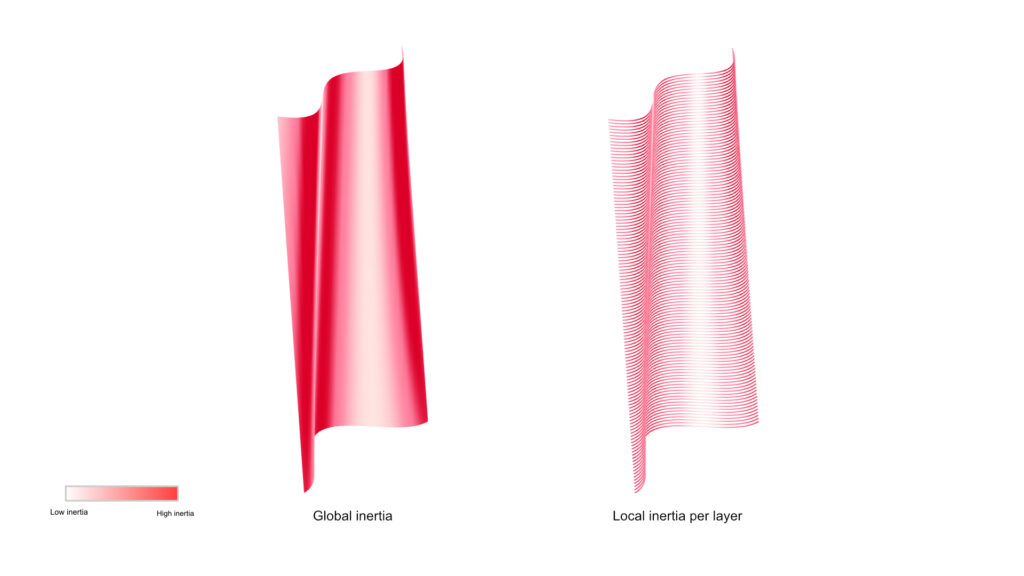
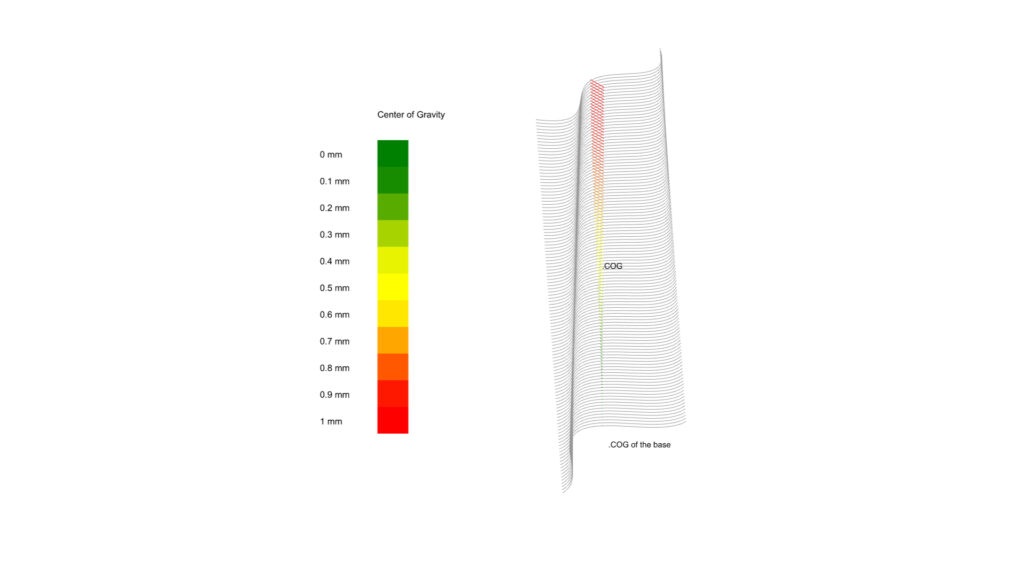
Karamba analysis
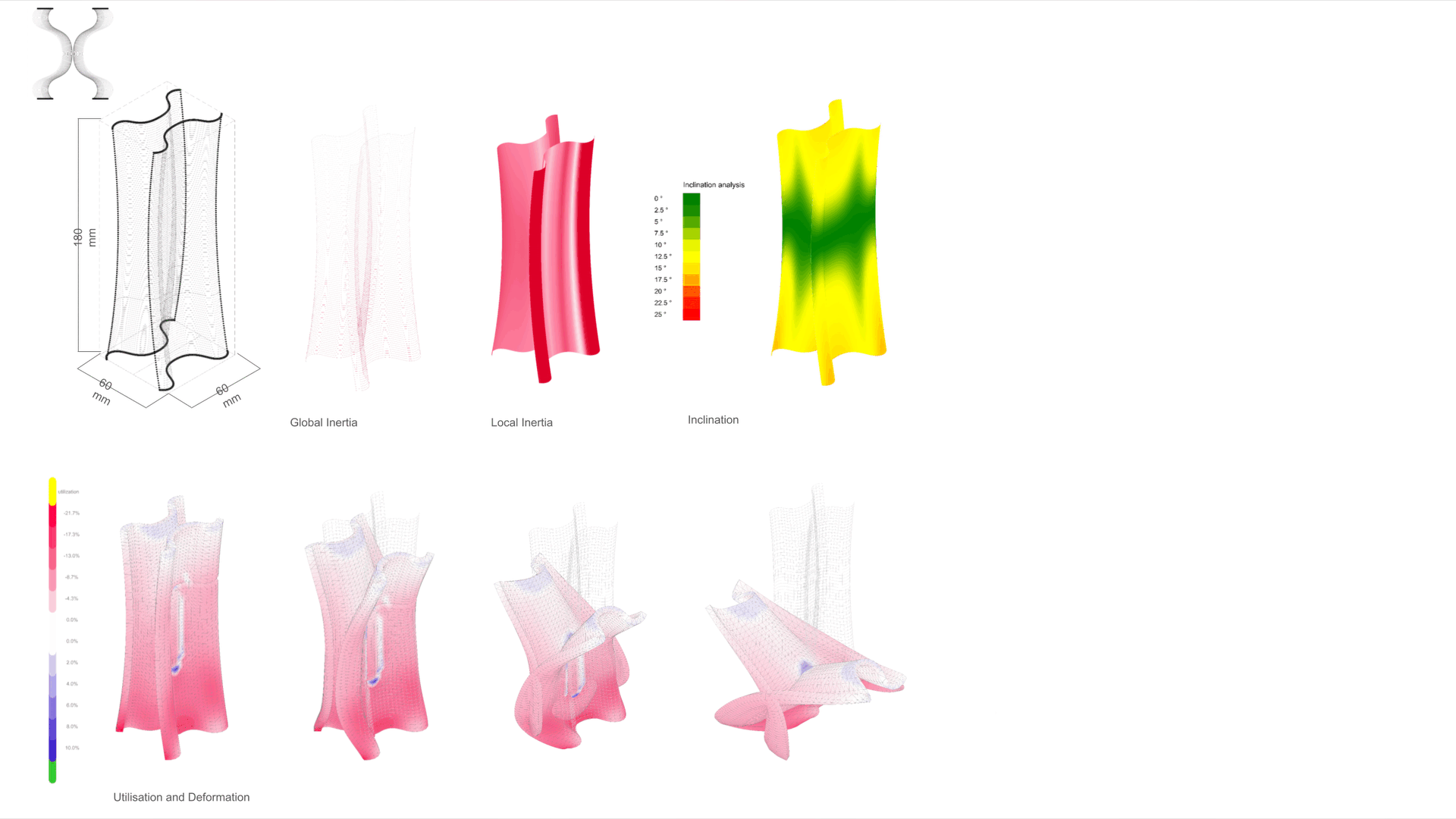
We found that to achieve best results a good balance of inertia throughout the surface was needed as this would work well with geometries that have a moderate angel or center of gravity
Results
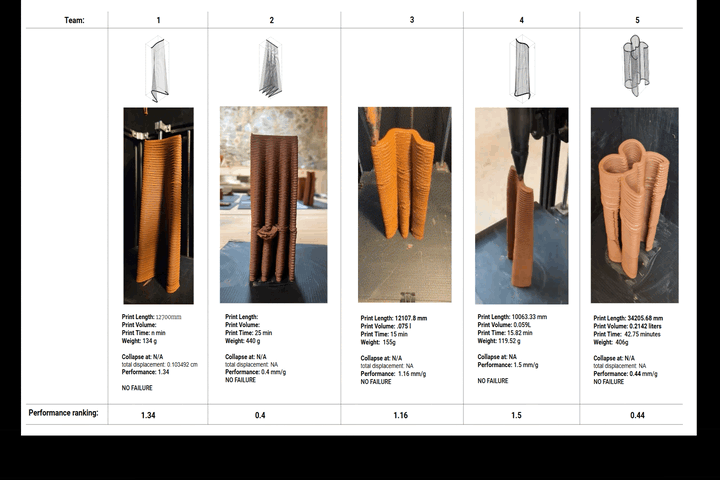
At the end of the week each group displayed their best performing print. to have a metric to compare what is the best surface printed we calculated the the height / total weight.
Scaling up to 1:1
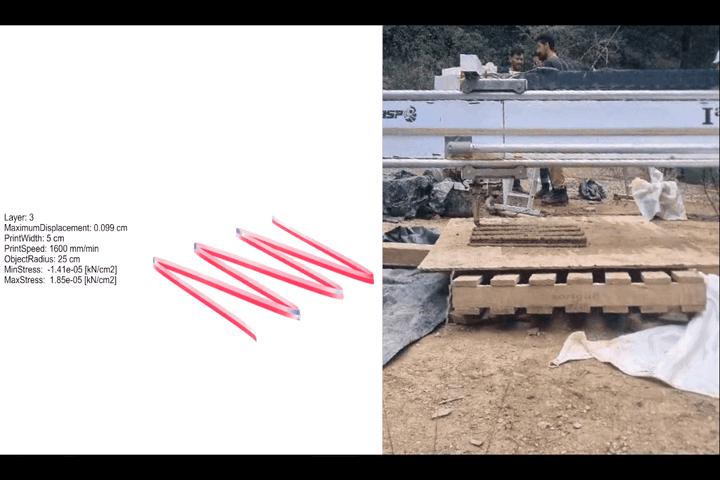
Although we might spend hours refining a geometry at 1:10 scale once we increased the scale to 1:1 on the large format printer a lot of the structural detailing was lost.
Conclusion
To optimize structural stability in 3D-printed designs, key factors include maintaining low COG variance, using wide base curves for increased surface area, and larger edge radii for higher inertia. A wider base and central COG improve balance and global inertia.
Adding perpendicular support at areas of greater displacement reduces buckling, which is crucial as straight walls without support are prone to failure. While vertically distributing inertia from large to small (bottom to top) stabilizes at smaller scales, it can cause issues at full scale due to increased mass.
Geometry plays a significant role; material placement away from the COG can enhance stability, emphasizing that mass distribution is essential beyond merely aligning with the COG.
Below are some visual summaries from the presentation:
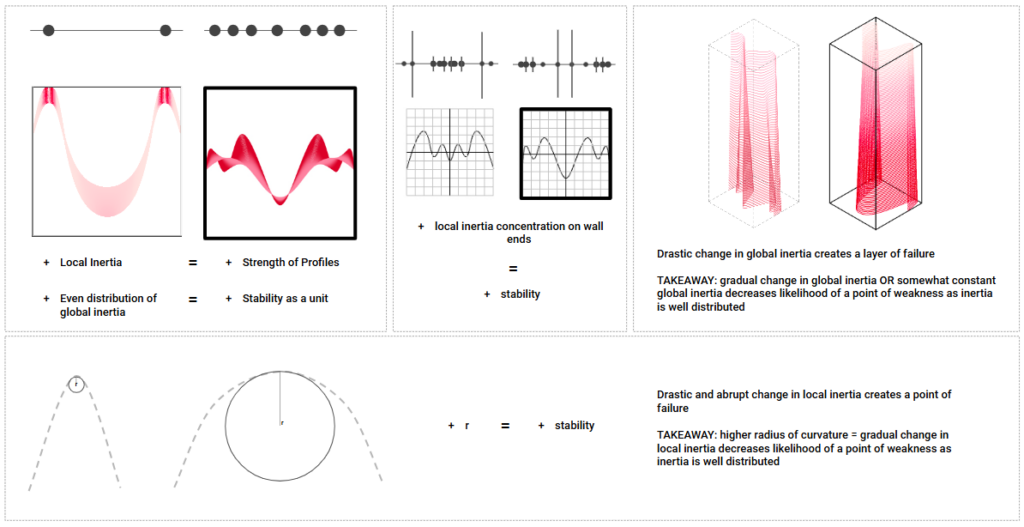
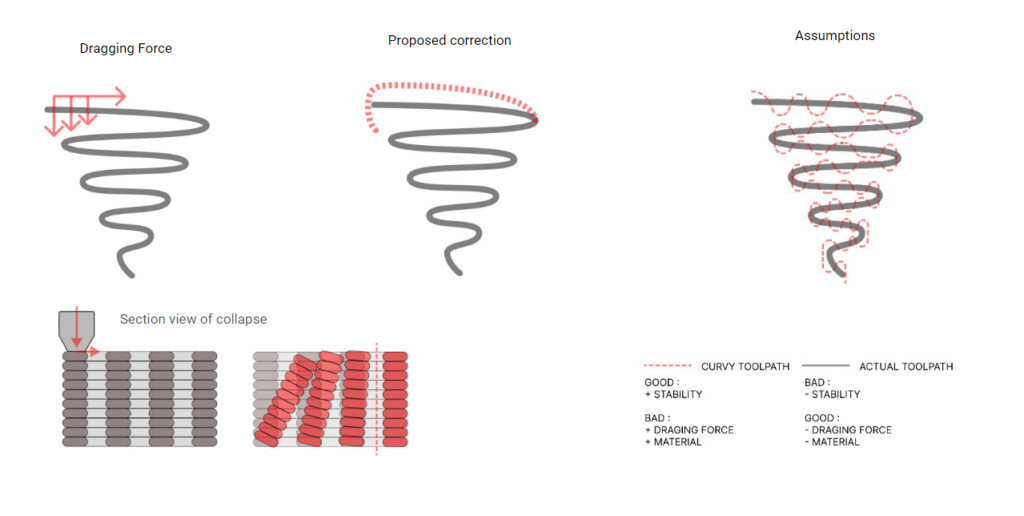