Structural analysis and optimisation
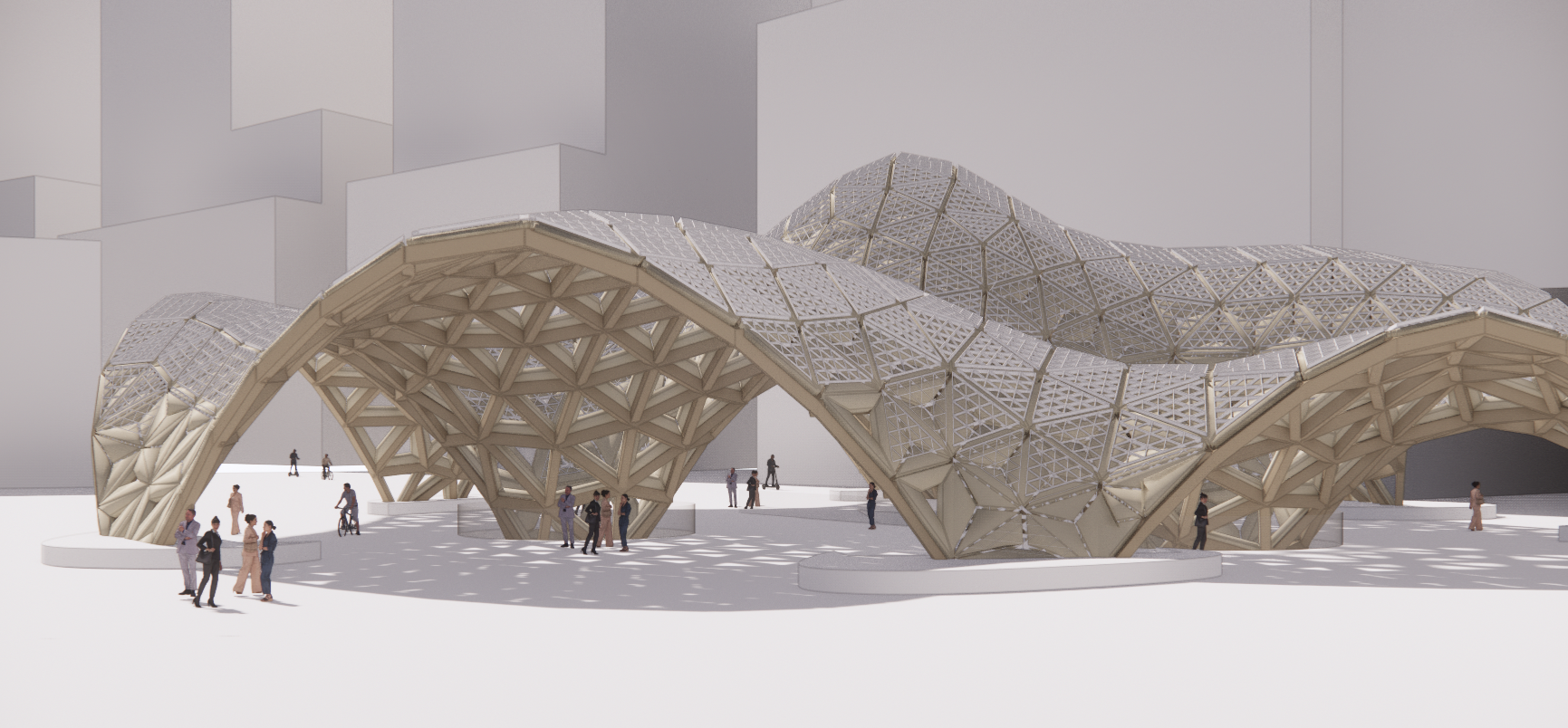
Our project is a timber grid shell which forms a roof canopy covering an underground train station in Sydney, Australia. The shell acts as a climatic roof providing shade and creating a cool public square below.
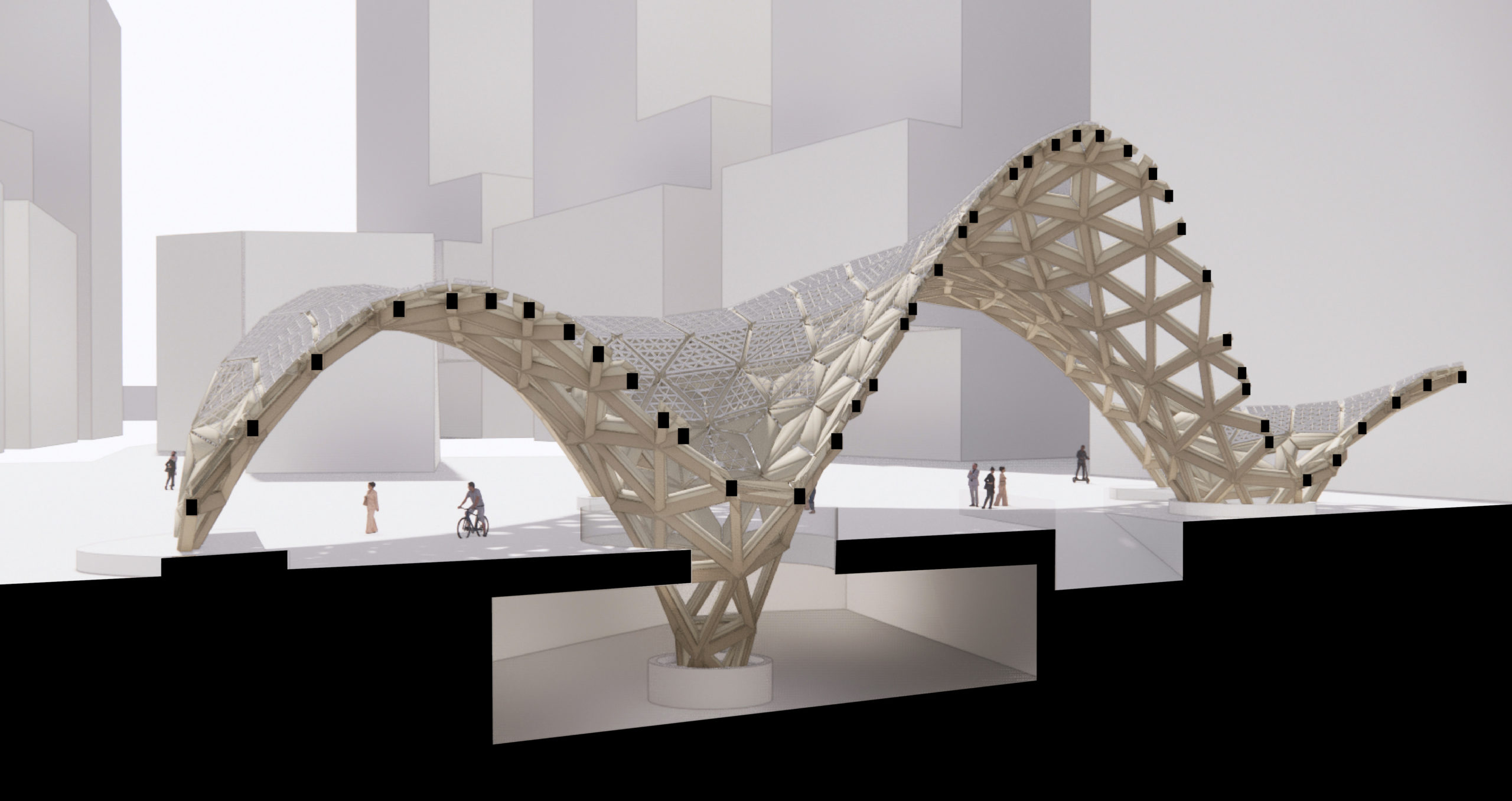
The timber shell forms funnel columns that land in the station below the public square, bringing daylight and fresh air to the underground space below.
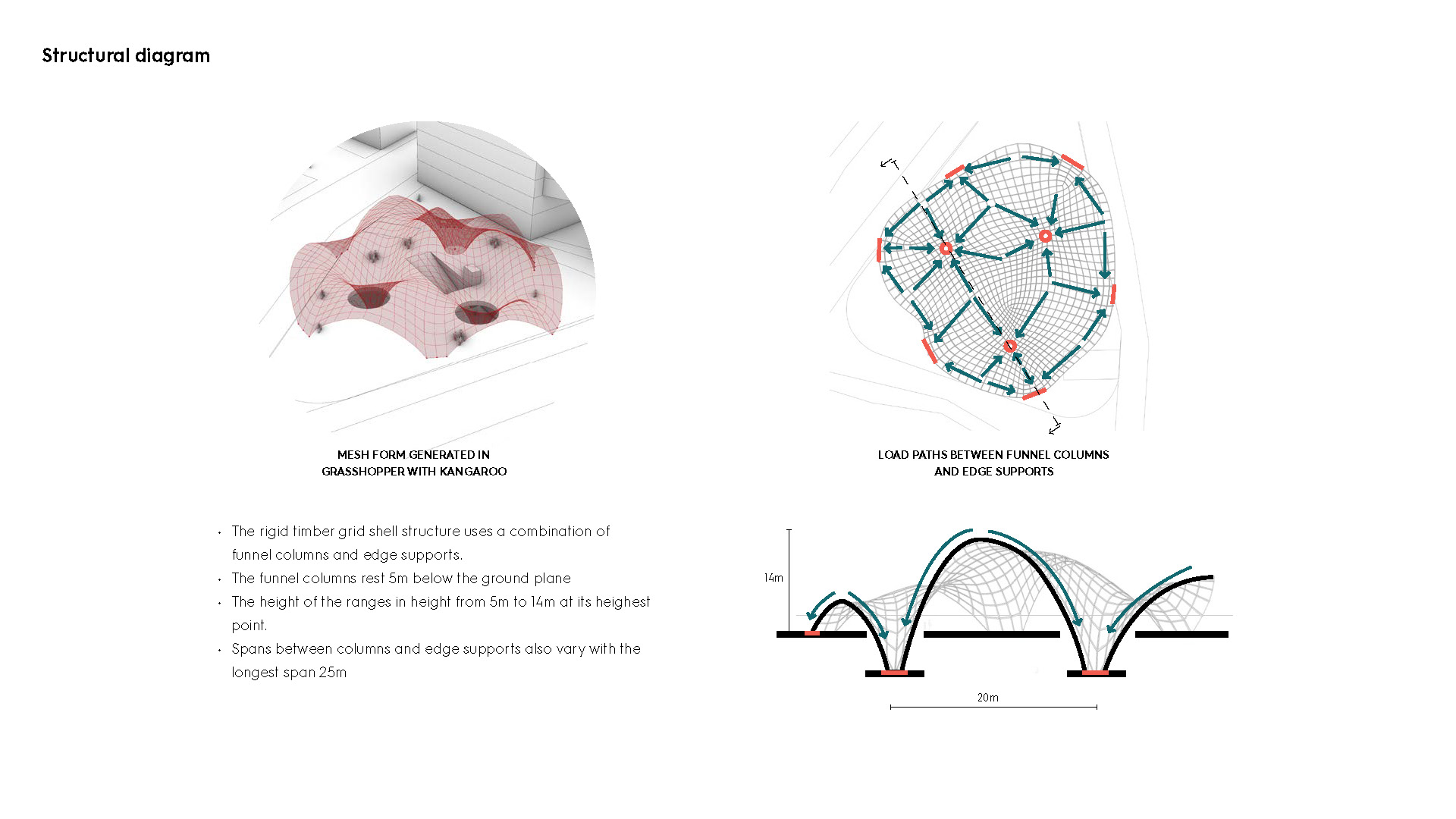
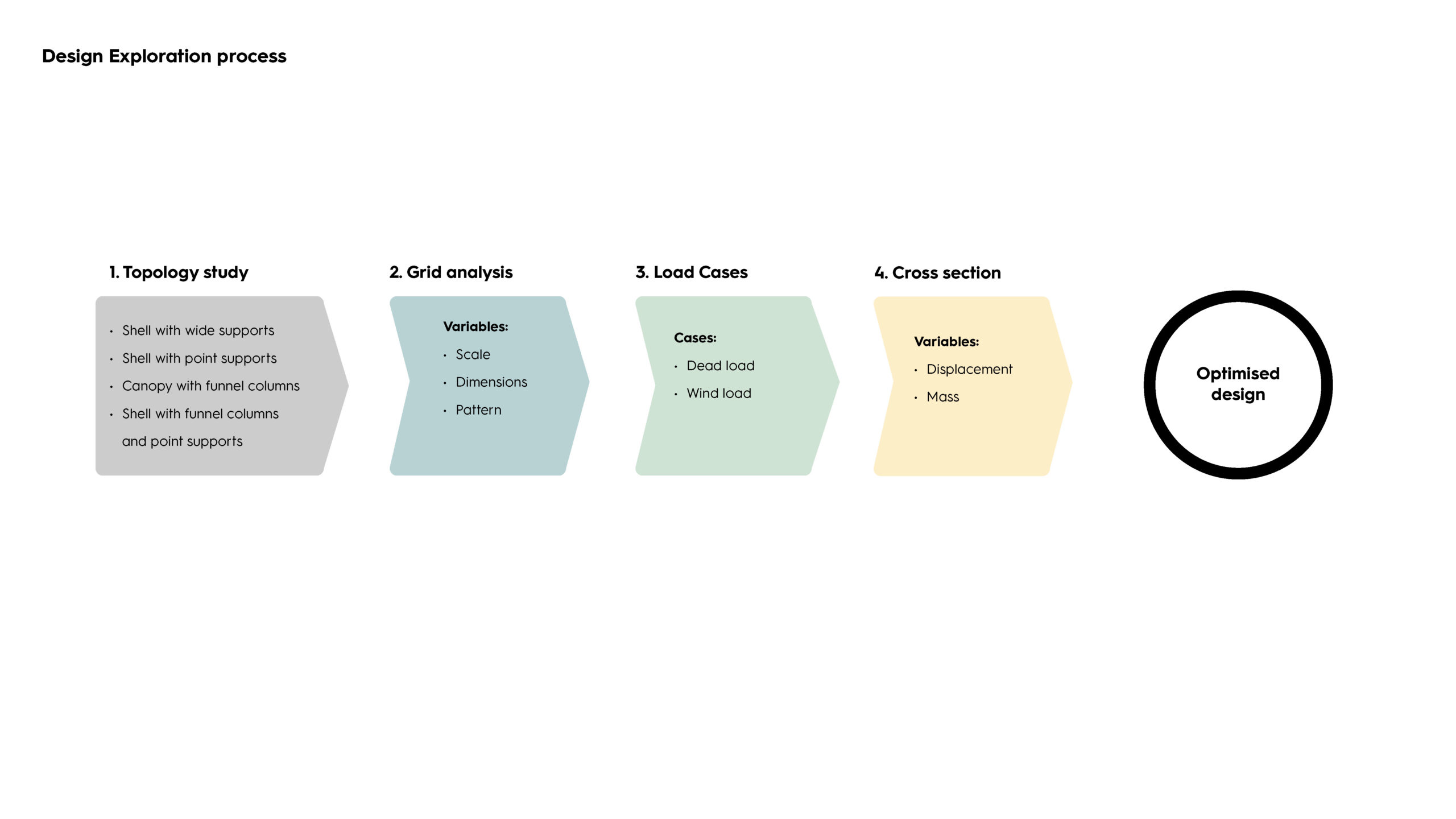
Initially the site dictated some parameters that required supports to be fixed, such as the funnel columns and some opening margins. These where determined from pedestrian flow simulations of the surrounding urban context. This animation illustrated a form-finding procedure for the placement of support for minimal structural deformation. The process used a physics engine to generate the mesh shell and a genetic algorithm to optimise support placement.
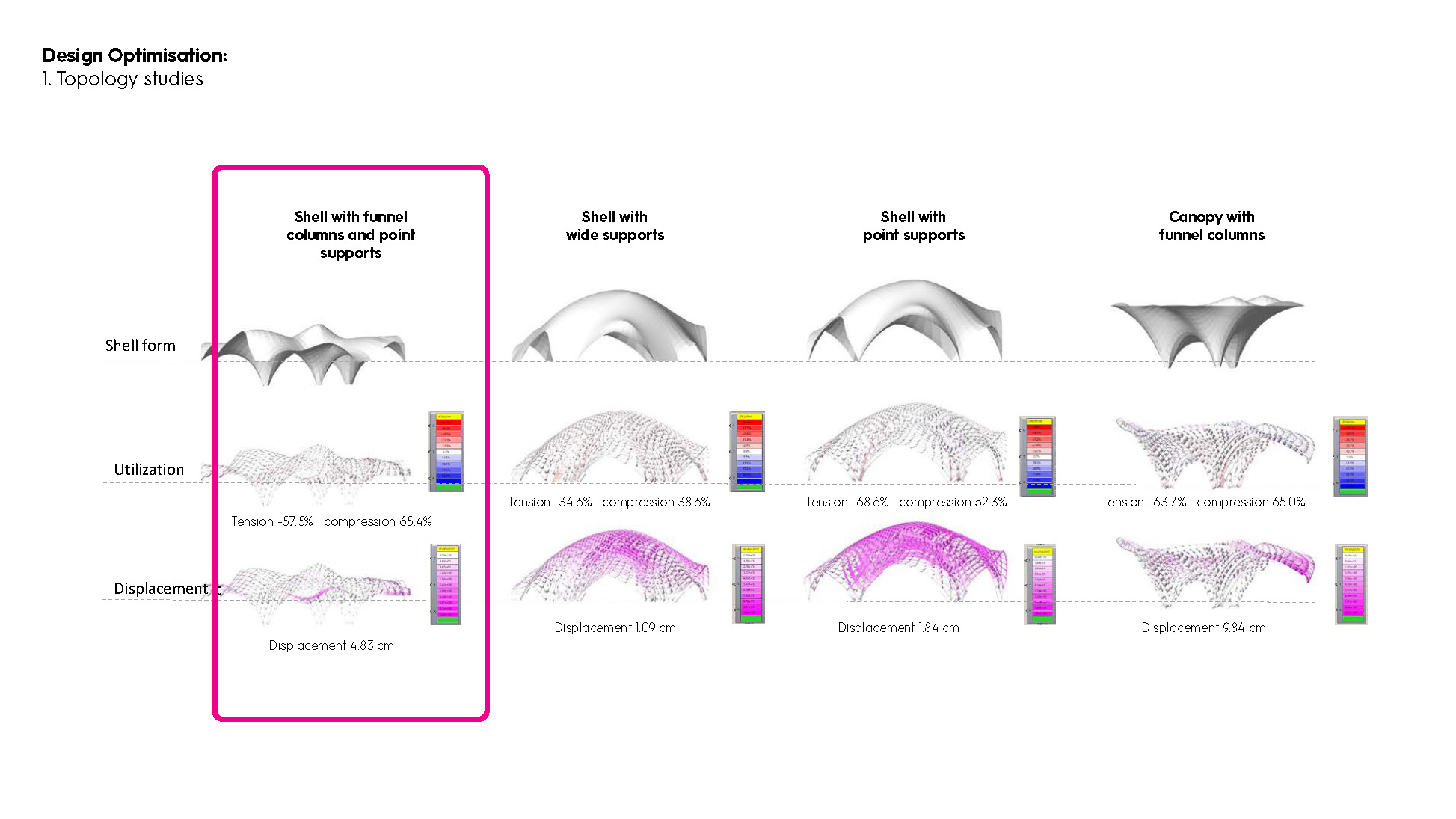
After evaluating the spatial and architectural qualities in relation to the program requirements, option 01- “shell with funnel columns and support points” has best overall
form and structural performance.
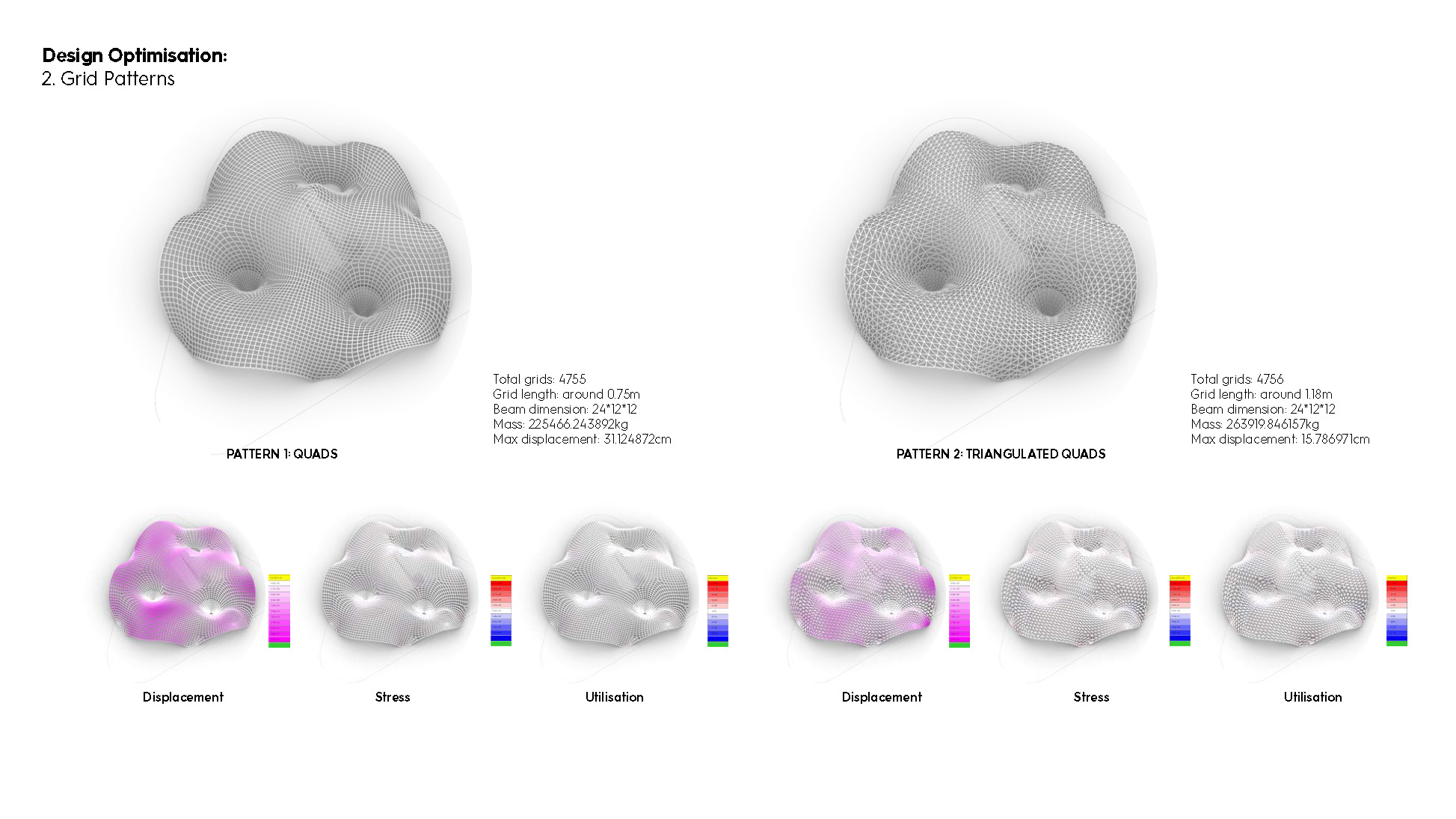
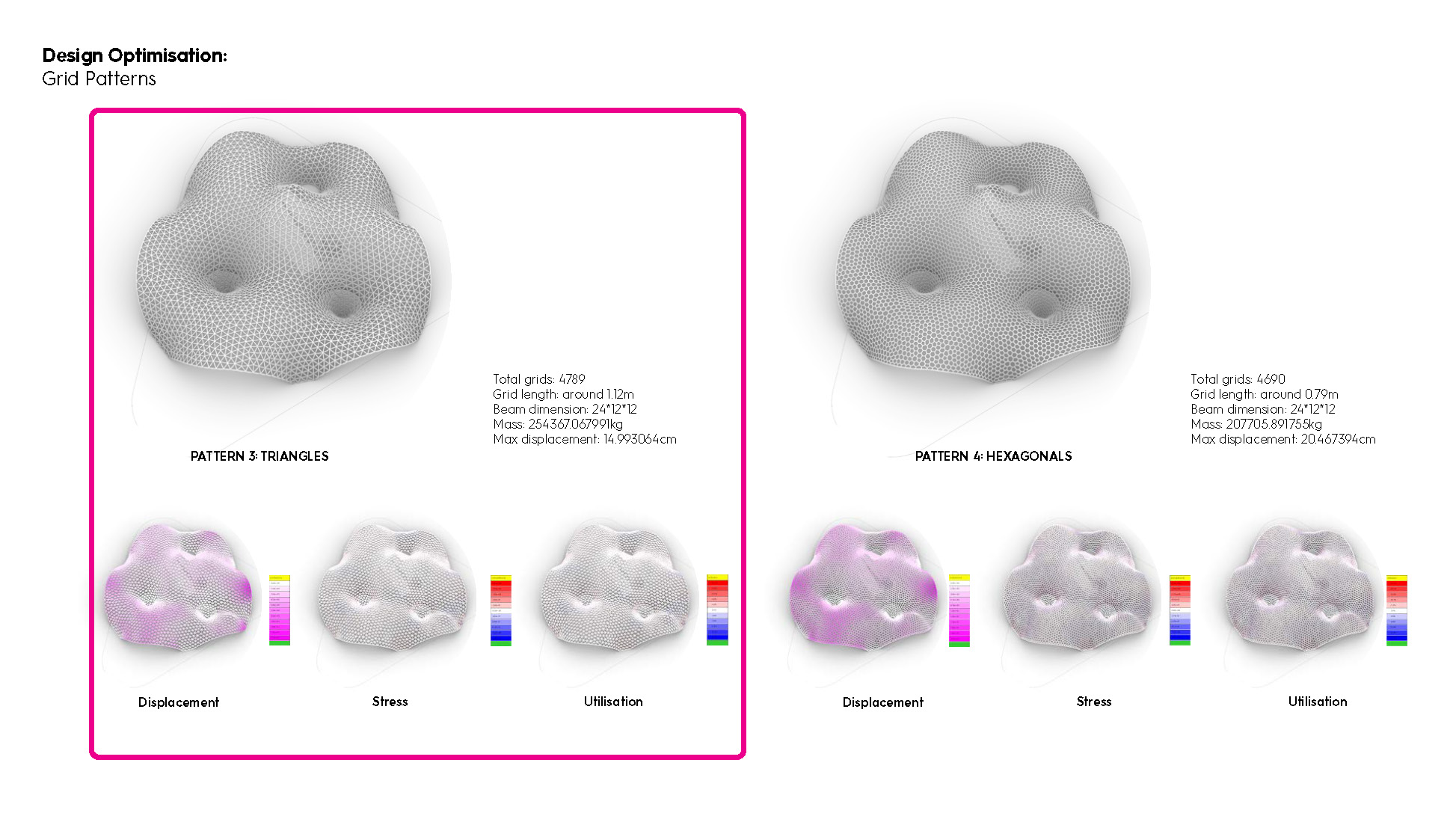
After the form finding process, the mesh was then evaluated. Four different structural patterns were tested, including a quad, triangulated quad, triangle and hexagonal mesh pattern. In order to compare them better, the same grid pattern density and cross-sectional beam dimensions were assigned. The results presented differences in total weight of the structure and the in maximum displacement. The goal was to choose a structure pattern that was most stable and had the least material usage. After observation and comparison, it was determined the triangle pattern performed better than others.
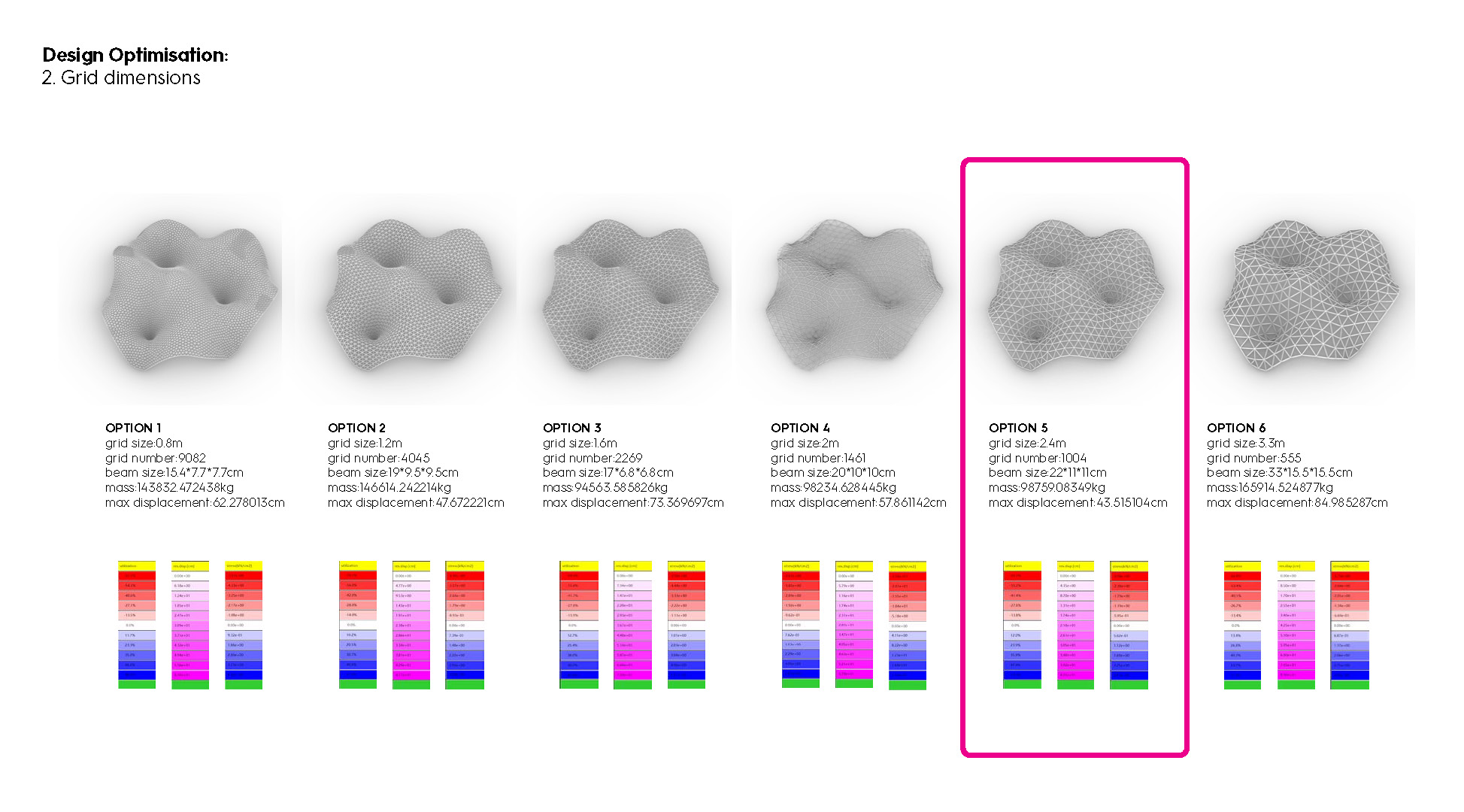
The triangle structure pattern was then tested further. Six structural grids of various size and structural skeletons ranging from dense to sparse were chosen. As a result, the cross-sectional dimensions of their beams would adjust accordingly and gradually increase as the grid became larger.
Material usage material and structural stability were simulated and compared separately. Utilization of each case was controlled to no more than 70%, and the beam cross-sectional size and maximum displacement required for them to meet the critical conditions was observed. Through comparison, it was concluded that option 5 performed better than others and was chosen for further analysis.
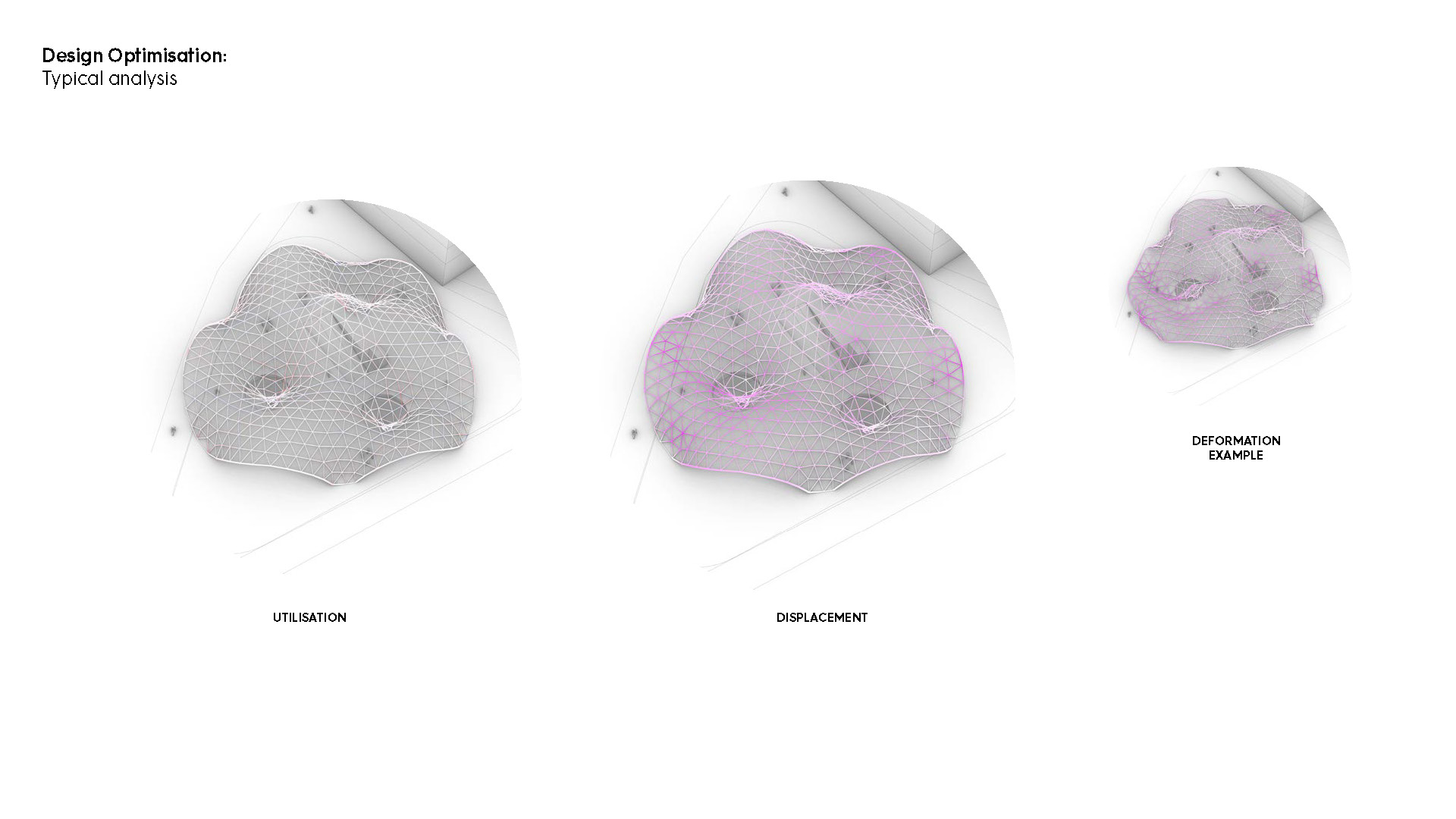
Structural analysis the shell required to be checked into three load cases:
Load Case A: gravitational + mesh + panel load
Load Case B: gravitational + mesh + panel load+dominant wind load (NW),
Load Case C: gravitational + mesh + panel load + local wind load.
Wind loads have a differentiation in the points of the abnormal shell shape that they affect and it’s crucial to test if horizontal bracing is required before everything.
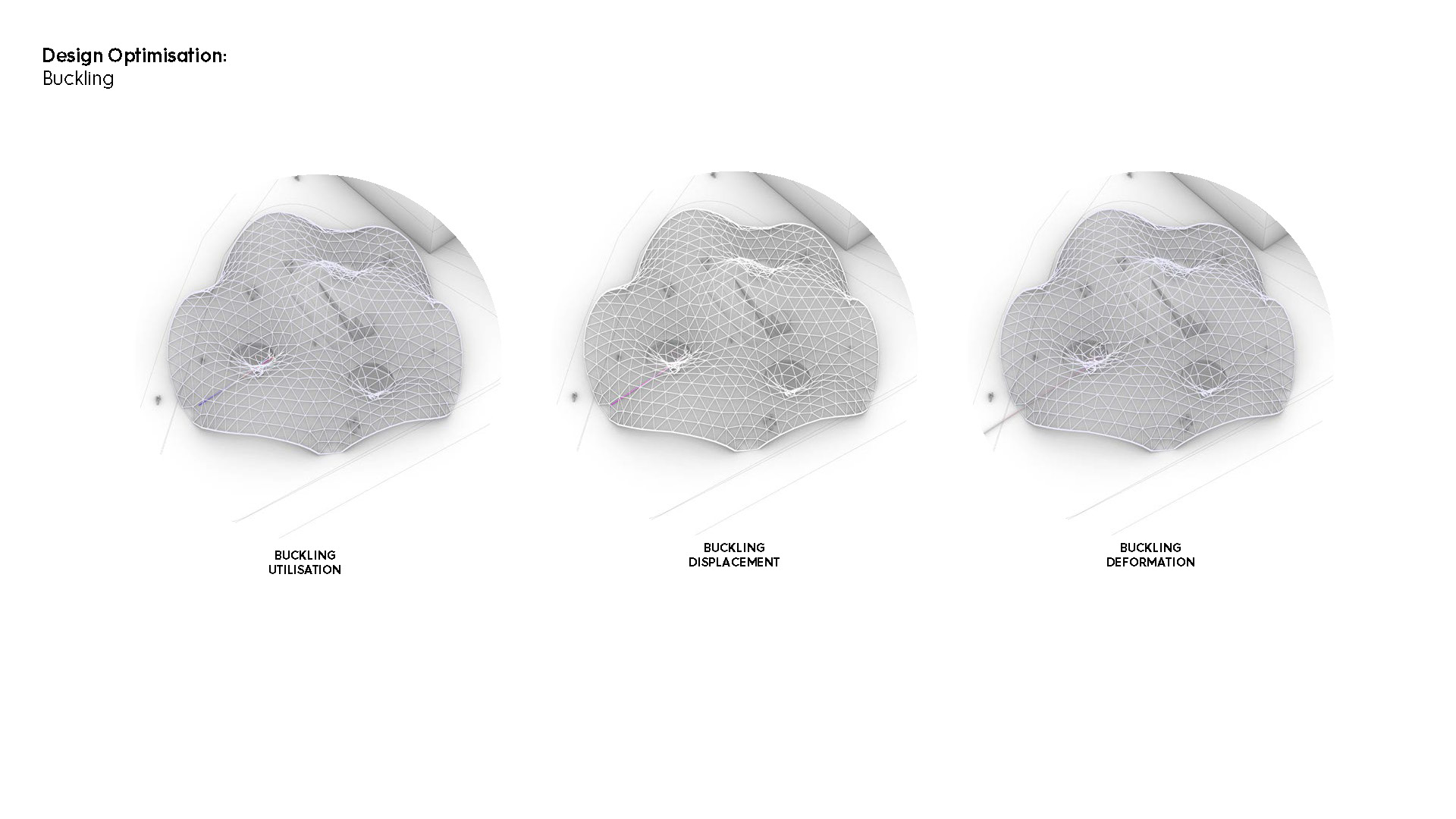
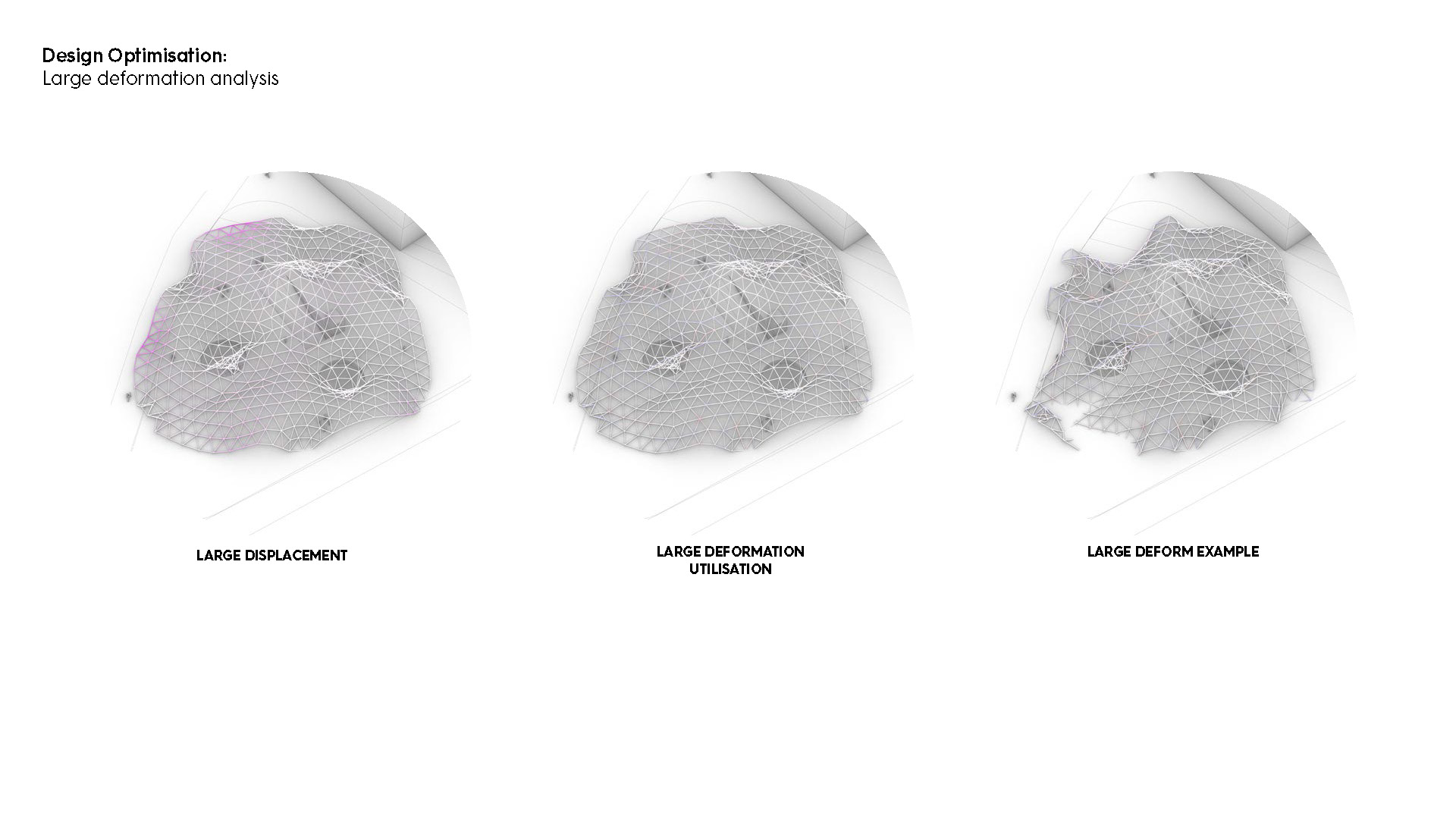
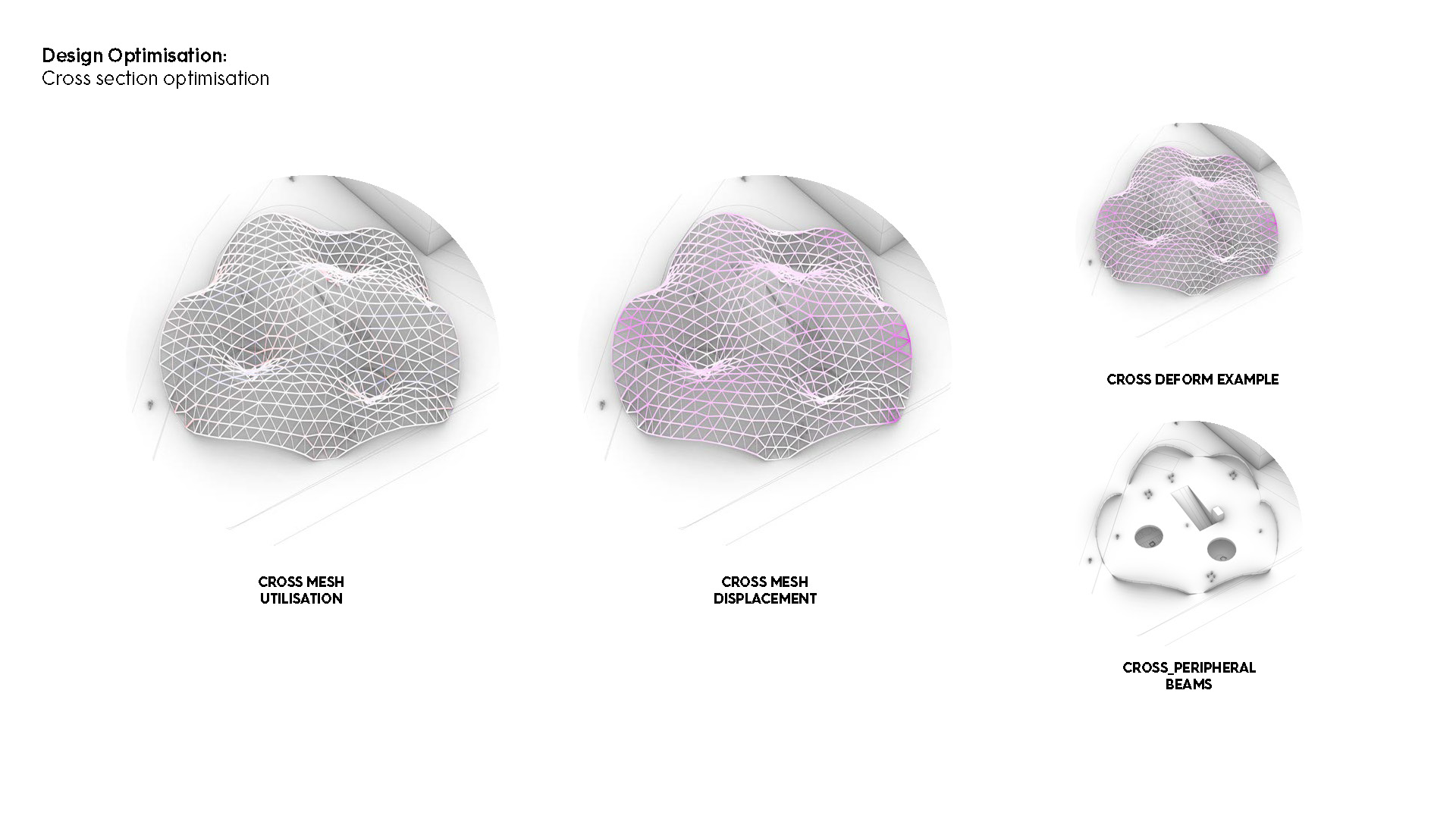
Each load case was tested in utilization and deformation in the categories of traditional structural mechanics. Large deformations analysis was also tested since nonlinearities might occur in a thin-structured shell system, which is made of sub-parts such as steel nodes and fasteners that might be low in integrity and robustness. Further in the process a cross sectional optimization was utilized in order to minimize the potential deformation value. This also helped to create a catalog for the timber member cross sectional range that the shell requires for a realistic design.
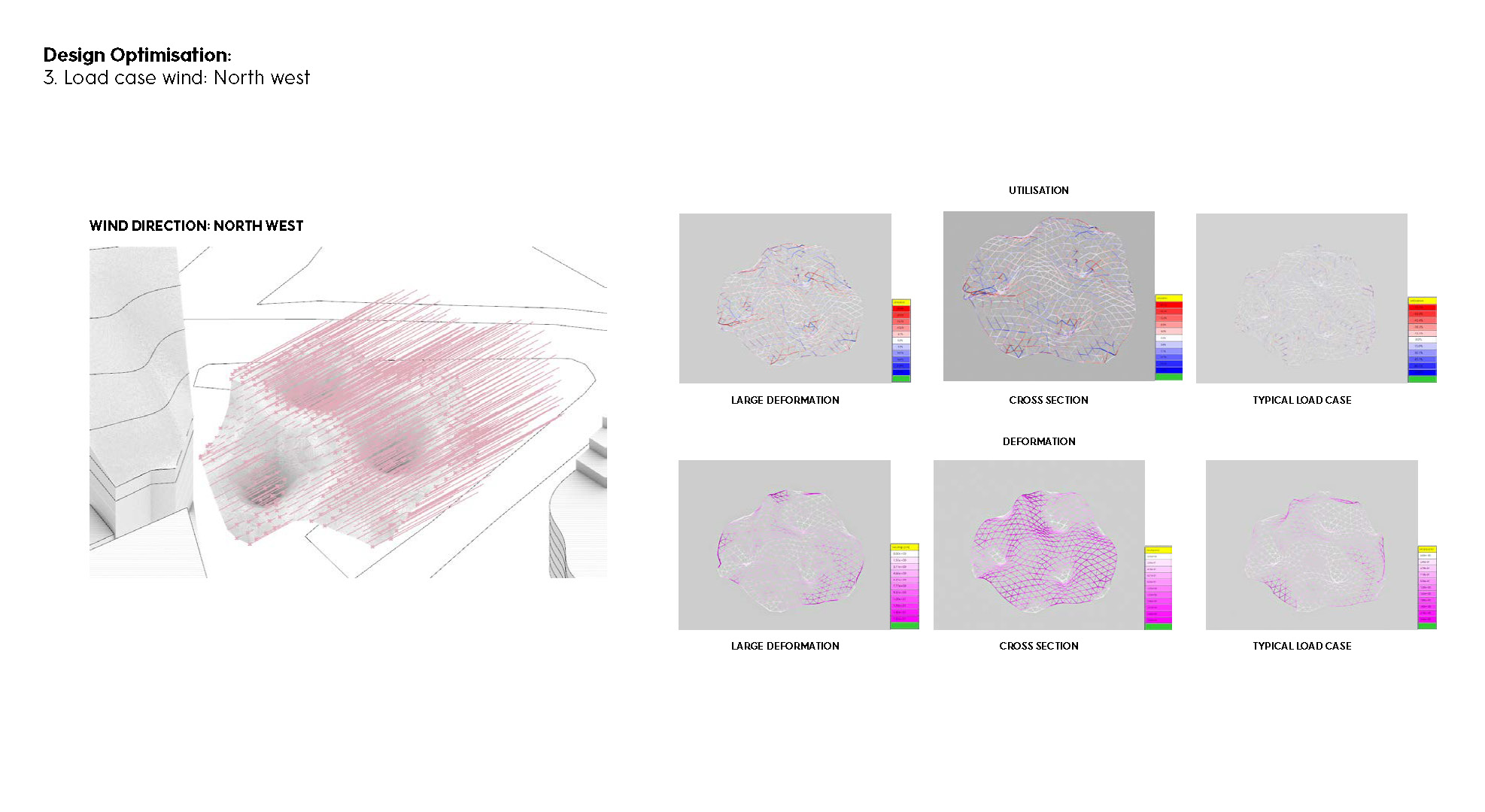
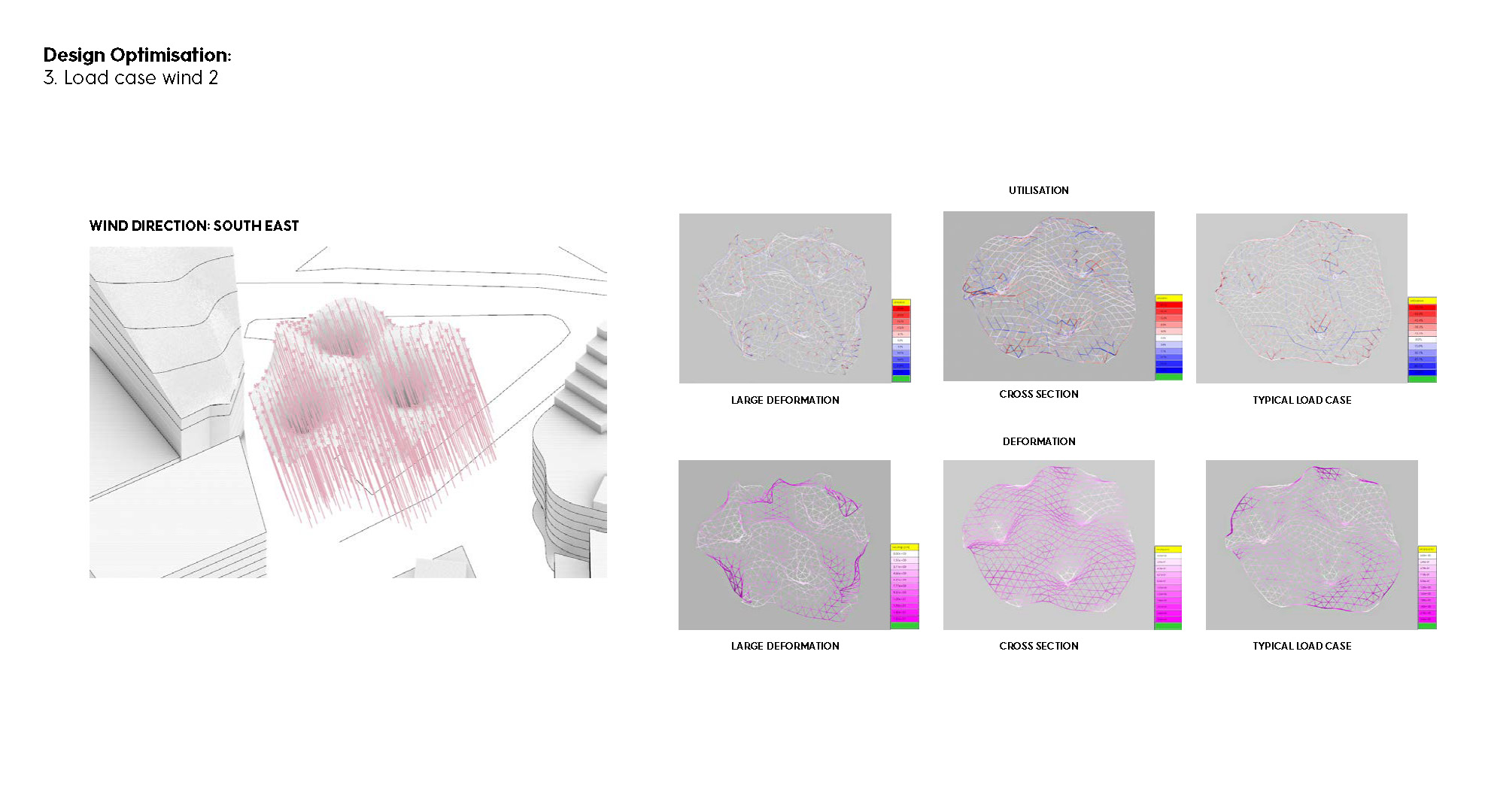
In addition to the aforementioned, buckling tests were continuously performed while on one local support on a dominant load case a profound value surpassed the limitation value that enumerated from Karamba and resulted in local buckling.
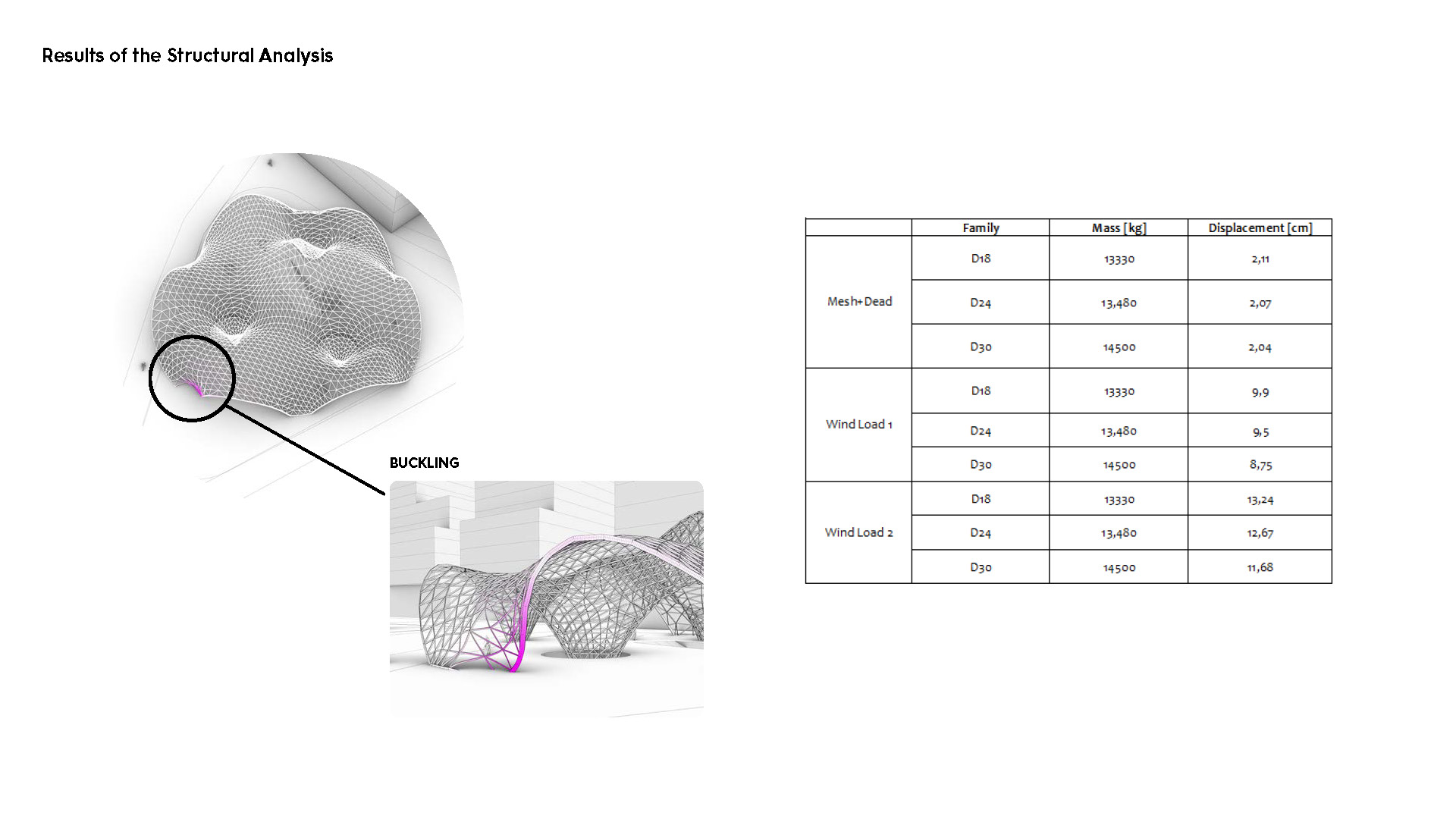
Buckling is failure based on high compressive stresses, that causes structural deflection sideways. The position of deflection is consistent with the localised displacement
from preliminary study. The above comparison table between of 3 load cases in wood and hardwood, been D30 the hardwood, shows that mass difference doesn’t have expressive variation in each load case and material application, on the other hand the displacement has significant changes. The hardwood the best performance in all cases.
The results of analysis and optimisation of the grid shell lead to a relative behavioural stability where the wind factor has significant importance since Sydney can be subject to severe thunderstorms with winds up to 27m/s in some cases, leading to triangulation for rigid and stable distribution of forces. Cross section optimization plays a crucial role in mass distribution, material utilization and displacement, stating its importance as a key point of rationalization of material usage and minimizing the embodied C0², avoiding unnecessary axial stress.
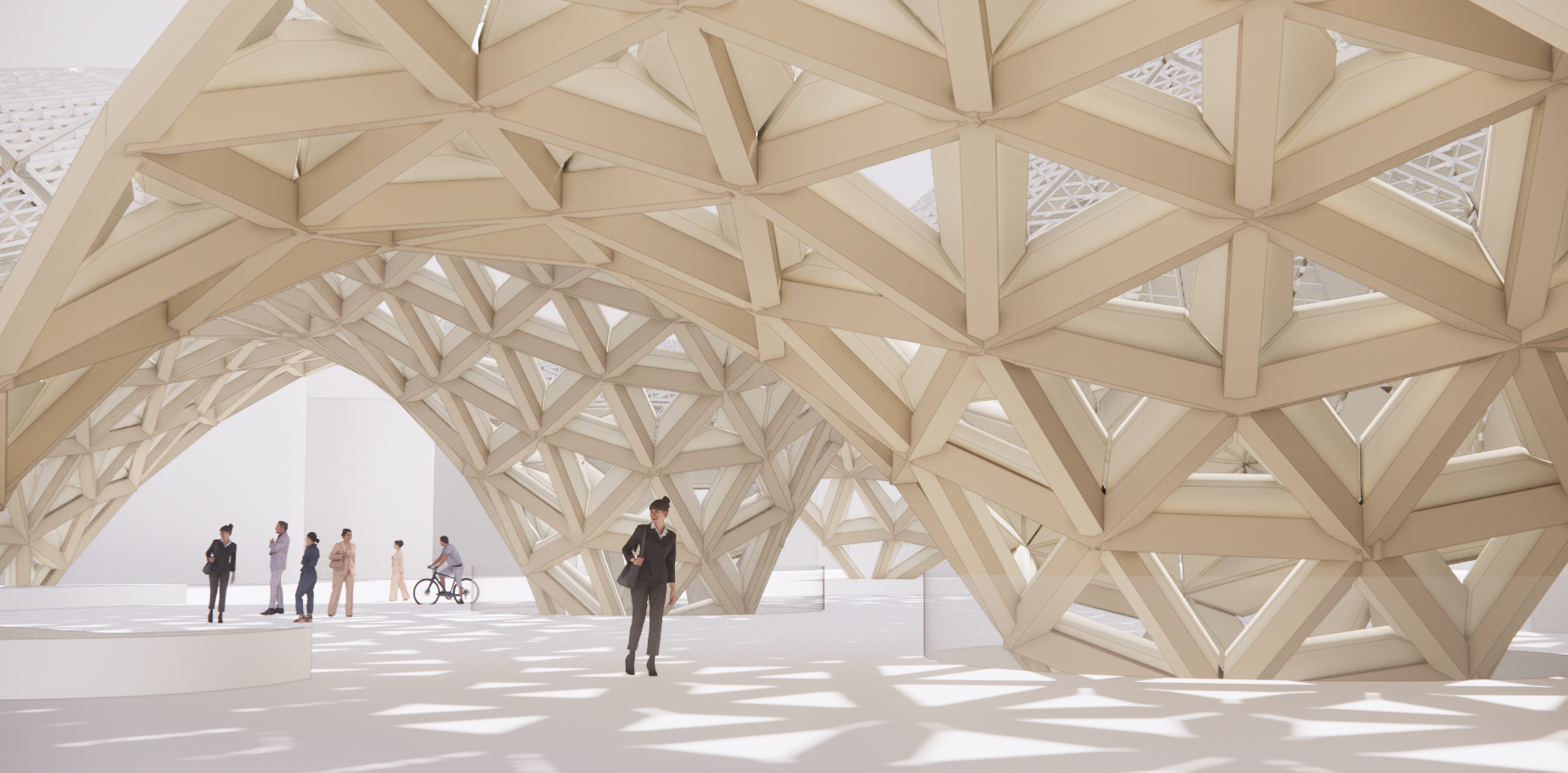