Brasil is the seventh biggest productor of Cacao worldwide and 60% of its production is from family agriculture located in the states of Pará and South of Bahia. The Chocolate Supply Chain produces substantial amounts of waste, specifically the Cacao Pod Husk and the Cacao Seed Shell. The process of producing the Chocolate goes from cropping the Cacau from the Cabruca, breaking it in a logistic location, fermenting on specific deposits, named “Cocho”, drying 4-5 days, transporting to the Chocolate Factory, Roasting, grinding, refining and conching. Between these process we have two residues, the Pod Husk and the Seed Shell.
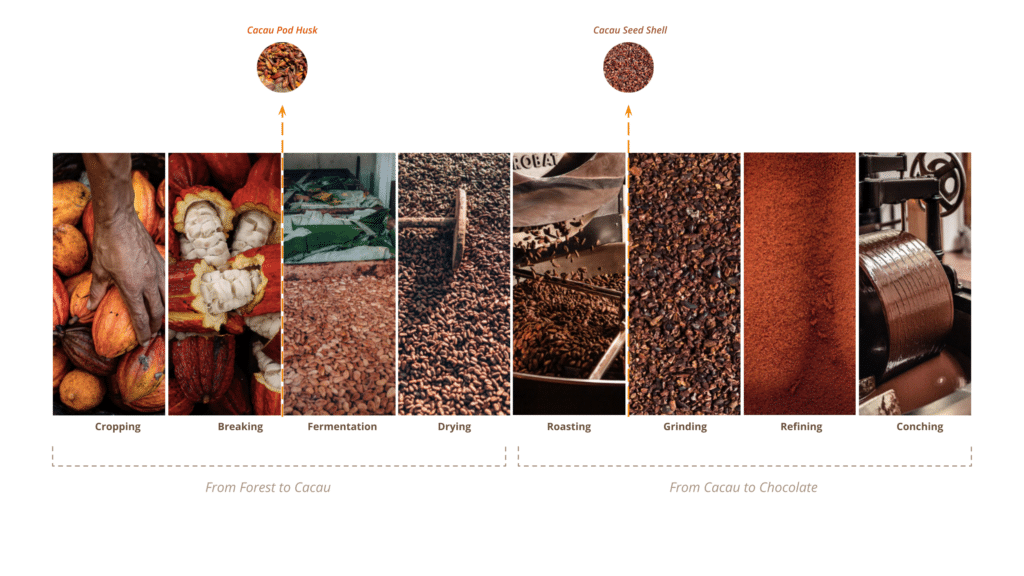
According to the Geography and Statistics Institute of Brasil, it is estimated that it is produced 2.83 million tons of Cacao Pod Husk annually. Cacao Pod Husk is mainly used as a natural fertilizer for the Cacao Crops; however, to be suitable as a natural fertilizer for the Cabruca crop it needs to be passed through thermophilic composting, a process that not every farmer has access to. Therefore, most of the Cacao Pod Husk is thrown as non-treated fertilizer in the Cabruca crop generating 57% of total crop loss due to spread of Cacao Disease, reflecting on a commercial loss.
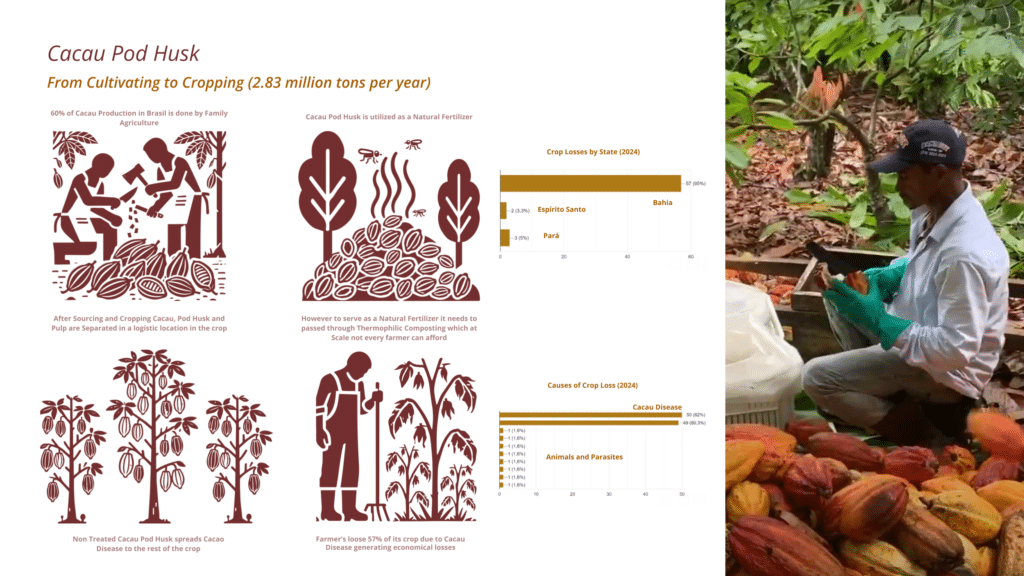
On the part of the Chocolate production, we have the Cacao Seed Shell that once is extracted from the Cacao Nibs. It is estimated that inside a chocolate company it is produced 275 kg of Cacao Seed Shell per day. This residue is outsourced, and turned into cattle feed or tea leaves. Nevertheless, on the national scenario and the growing stage of the production of Chocolate not every Cacao Seed Shell is able to be absorbed by other industries, thus portions of it are destined to landfills.
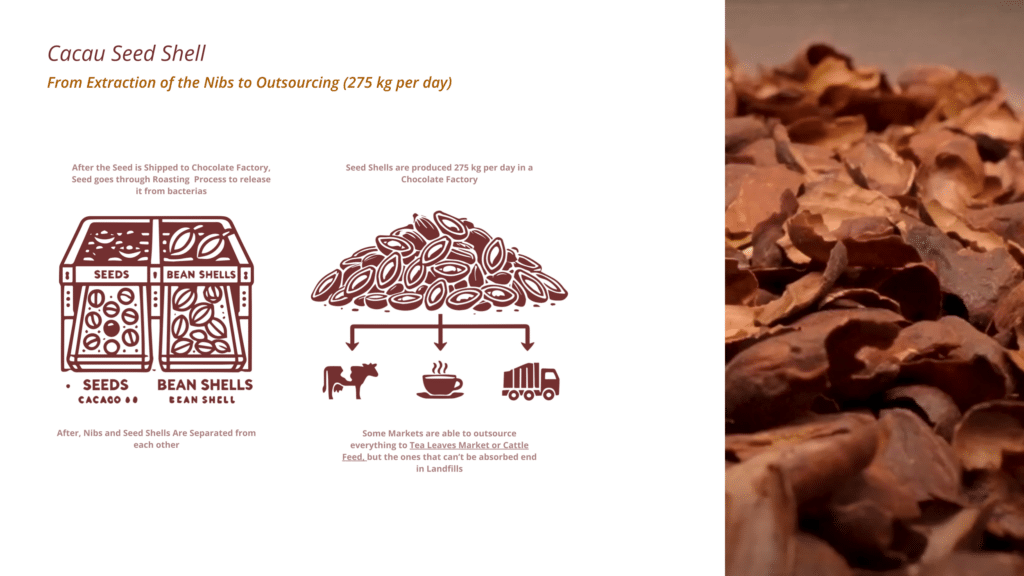
Both Residues are high in Cellulose and Lignin, presenting good properties in tensile and compression strenght. The Seed Shell being high in antioxidants and having more resistance to higher temperatures (Decomposition Temperatures between (230C – 250C).
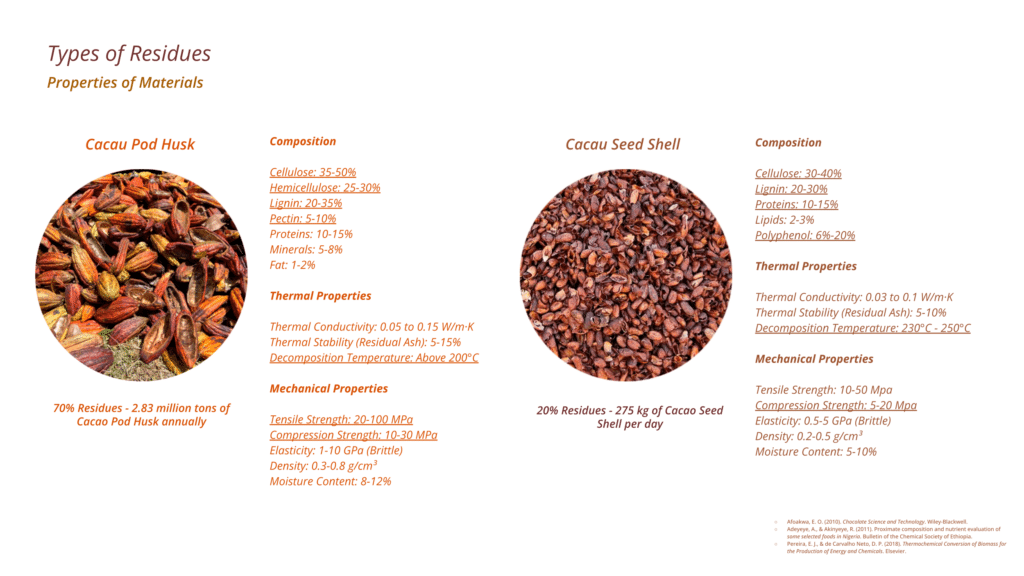
The scope of the research is focused on the development of biocomposites that utilizes renewables and biodegradable polymers as a matrix and adding both the Cocoa Pod Husk and the Cocoa Seed Shell as additives that can improve the performance of the polymer matrix and give a second life to the residues.
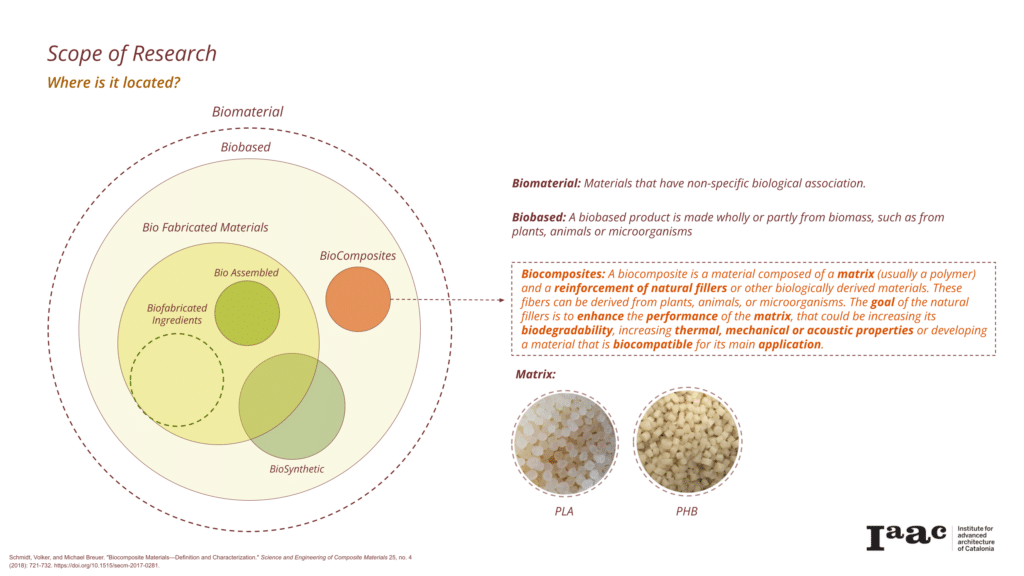
To asses this new biocomposite and its manufacturing process, circular economy parameters are used as evaluation criteria to determine if the generated product is adding value commercially and ending energy loops. According to the Ellen MacArthur Foundation, circular economy aims to minimizes resource use and waste by closing material and energy loops through design, maintenance, reuse, and recycling. The parameters used to evaluate this new biocomposite and its manufacturing process are: mechanical resistance, biodegradability/compostability, maximum usage of residue, cost of production and reduce its carbon footprint. It is important to mention that other parameters would be necessary to evalutate this new biocomposite and the products made from it utilizing additive manufacturing, so the full product would be considered fully circular, like reprintability, thermal resistance, ageing, and production of microplastic. However, due to the time constraint of the research we are focusing only on the five highlighted before.
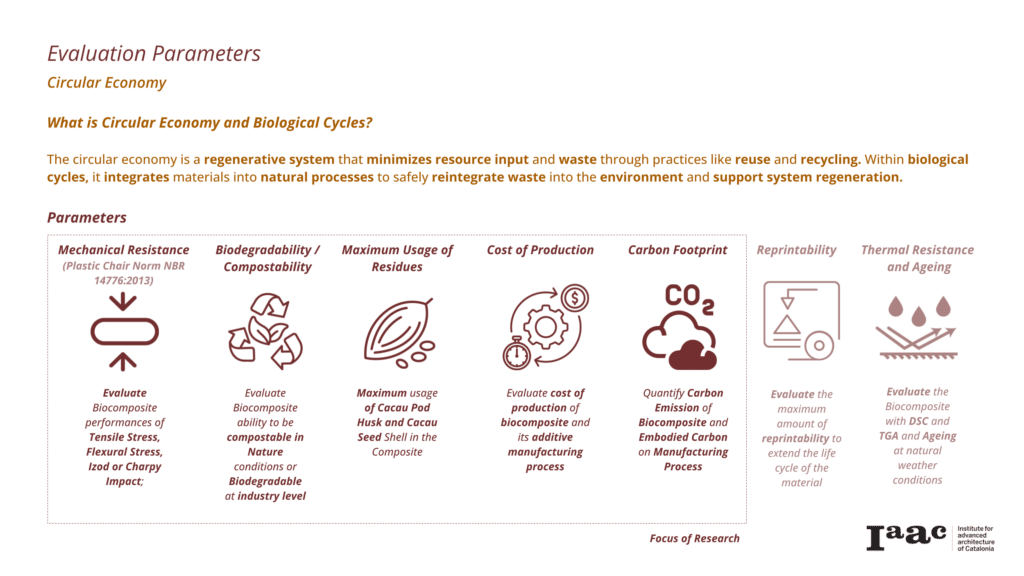
Robotic Additive Manufacturing offers several advantages on product design and manufacturing such as, customization, on-demand production, fabrication with varied materials, large scale fabrication with an emphasis on waste minimization. According to the Grand View Research report of 2023, the 3D printing market was valued at USD 20.37 billion in that year with an expected CAGR of 23.5% between 2024 to 2030. During 2022, the building segment (commercial, residential, industrial) and infrastructure, such as furniture and bridges had a total value of USD 18.2 million, on this segment materials like metal, concrete and plastic are being highly prototyped and tested. Consequently, the manufacturing of furniture and interior objects with additive manufacturing offers a viable financial scenario for experimenting with biocomposites.
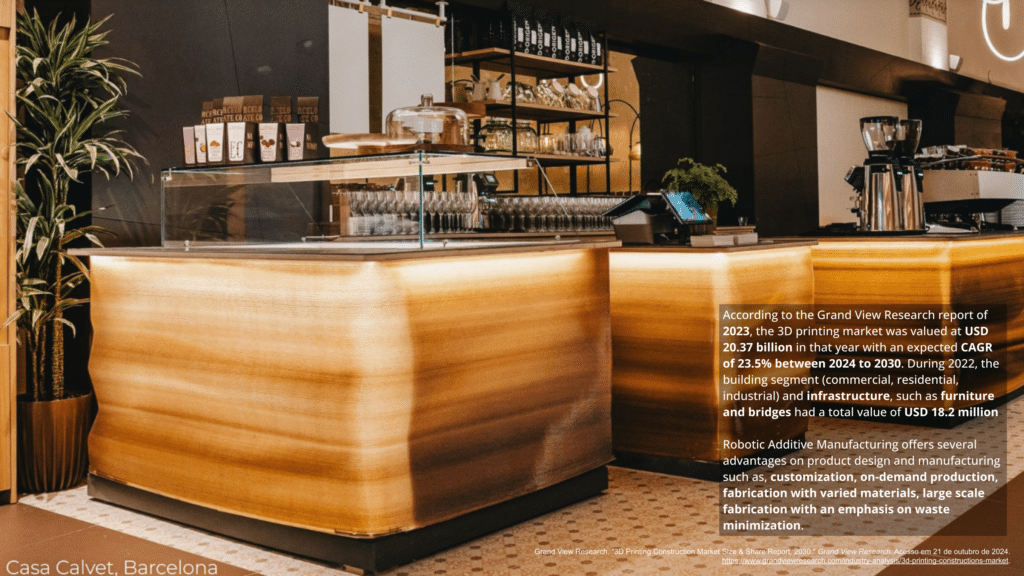
By Analizing what has been produced by the industry in terms of biocomposites and furniture with large additive manufacturing methods we can evaluate that there is scarce date on how the biocomposite is adding to the printed objects in terms of mechanical strenght, increased time of biodegradability or compostability, if it is using maximum usage of residues to reflect in considerable amounts to solve supply chains, cost of production or how much the addition of this residues are influecing the cost of the final piece of manufacturing or if the carbon emitted by the new biocomposite and the embedded carbon throughout the sourcing of the residue to the final object printing is generating more carbon or reducing it. Therefore the added value of this research is not only producing a new biocomposite and learning how to print with the material, but also to generate data on this manufacturing process and how can we more transparent and critical about generating products with organic residues for additive manufacturing.
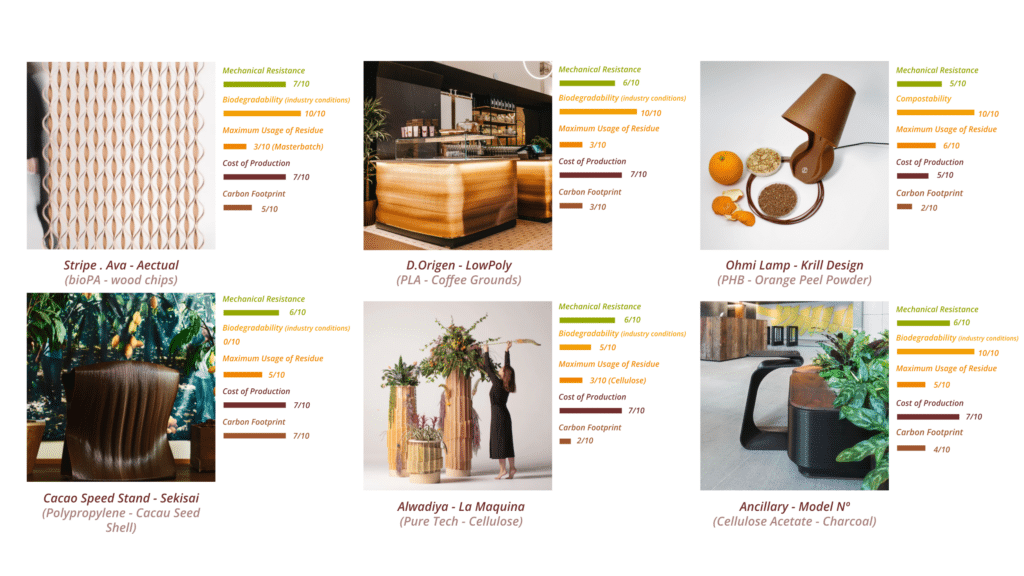
This research started three months before the initial oficial timeframe for second year researchers, all of this to understand the supply chain in Brasil (on site on where is produced the resides in the Cacau Farms and in the Chocolate Factories) and what is the best method to develop a durable, compostable/biodegradable biocomposite. The exploration started by mixing it with organic polymers, such as agar agar, corn starch, gelatin and alginate. All of these produced mold in 2-3 days of curing the material, this is due to high humidity in a tropical place and the diversity of fungus and bacterias in Brasil, coming to the conclusion that Liquid Deposition Material was not the best method to create durable products with it.
The second hypothesis was mixing different proportions with a renewable resin of Polyurethane made out of Castor Oil. It is biodegradable at industry level and with this new composite it is possible to reach 50% of addition of Cacao Pod Husk and Cacau Seed Shell by weight of the base matrix. Polyurethane is a bicomponent resin that during its curing time it inflates 20%-50% its size. What was observed was the more the addition of Cacau Residues the less the cured objected was prone to inflate . However resin can not be printed and it relies on casting and mold as manufacturing. Therefore to this robotically would not allow for mass customization since casting it is a process to mass production.
The third hypothesis, and the selected one, was mixing it with PLA and different proportions of Cacao Residues in fine powder and printing it utilizing Fused Granulated Fabrication where we could test the increasing of the Cacau Residue in the matrix and at the same time relying on the mass customization of large scale additive manufacturing to produce the objects and the data to evaluate the material and the process.
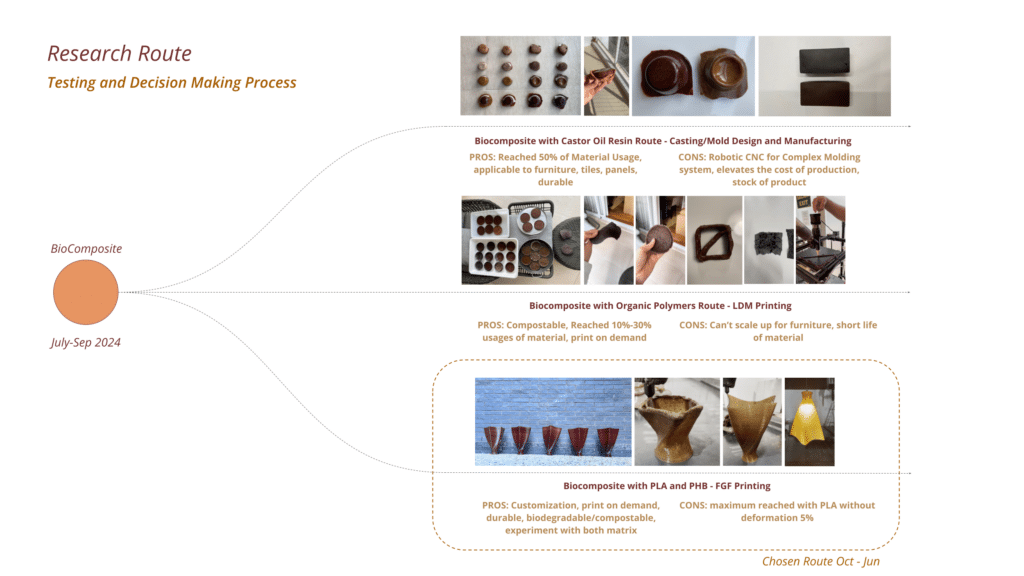
The methodology of the research relies on three systems being material, fabrication and design. All of these three systems being evaluated by circular economy principles and parameters. For the material we have the experiments that evaluates this system as mechanical resistance, compostability/biodegradability, cost of production of composite and emitted carbon of material. The material system informs the fabrication system and vice versa. For the Fabrication with FGF we are evaluating the calibration of the extruding screw, toolpath, printing time per layer, velocity of printing, size nozzle, temperature and limitations that can present by printing this noval biocomposite. Cost of production and embedded carbon throughout the whole process are going to be quantified as well. The design system embeddeds the results from Material System and Fabrication and it is a synthesis of the explorations of the two systems mentioned before.
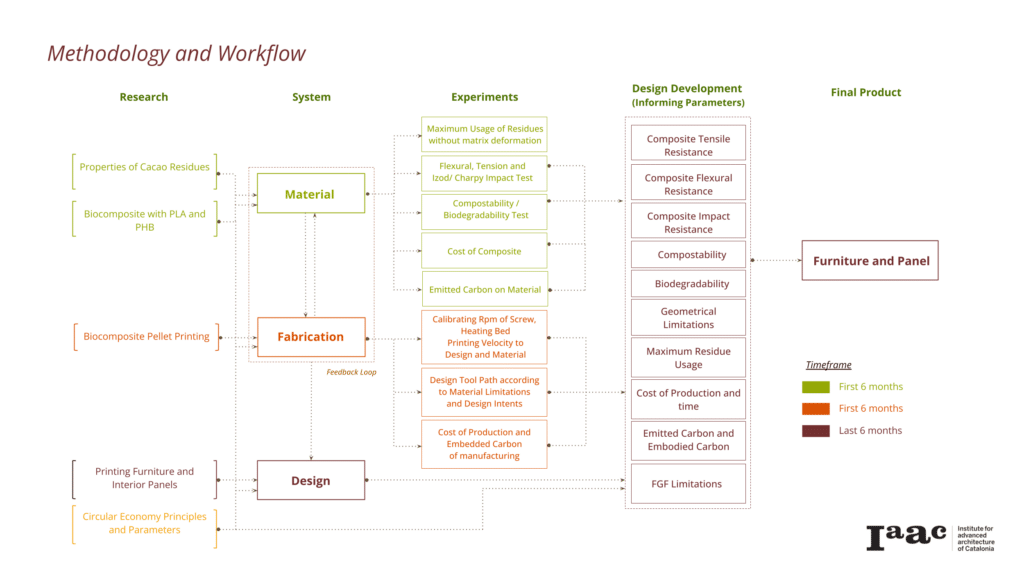
There is a pre-preparation phase prior to mixing and producing the biocomposite that relies on sourcing the waste material, drying it, transporting and grinding it. For the Pod Husk it is imperative that the material need to be dryed in well conditions without any moisture, otherwise during the trasportations it is prone to molding and infecting the biocomposite. After drying it needs to be grinded in a grinder of 20-3000 mesh that can guarantee 50 mícrons of the particles. For the Seed Shell it is only sourcing the material, separating nibs from seed shell and grinding it. Both materials need to be stored. The whole process is faster for the Seed Shell where the Pod Husk relies on trasportation and availability on cropping seasons and transportation.

For the first Experiment the base questions was “Can we bound the residues and the PLA and print at the same time?”. Based on an article by the University of Medelling and University of Rio the maximum it was reached with a single screw extruder was the range of 2%-5% of organic fillers. Following this data the experiment had a given design, the quantity of PLA was measured by the weight of the piece and it was mixed with rations of 2%-5% of Cacau Fillers by weight of the PLA pellets. Than it was dried together in a industrial pellet dryer and poured in a Pellet Extruder with the entrance temperatures and the heat bed as shown in the following diagram.
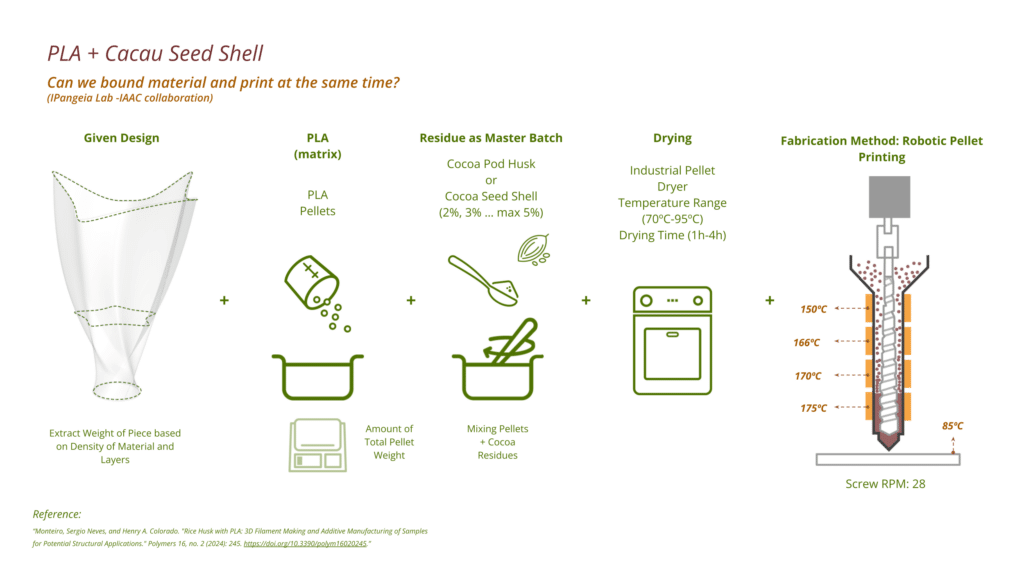
What was observed is that with 2% Cacau Fillers and the drying time of 2h and 70ºC there were no deformations of the matrix involved, however once increased to 3% the matrix started to deform and generate bubbles. Learning with that the experiments with 4% and 5% have increased drying time of 4h and 95ºC and what is observed is that the 4% had no deformations but the 5% had a lot of deformations of the first time of the printing.

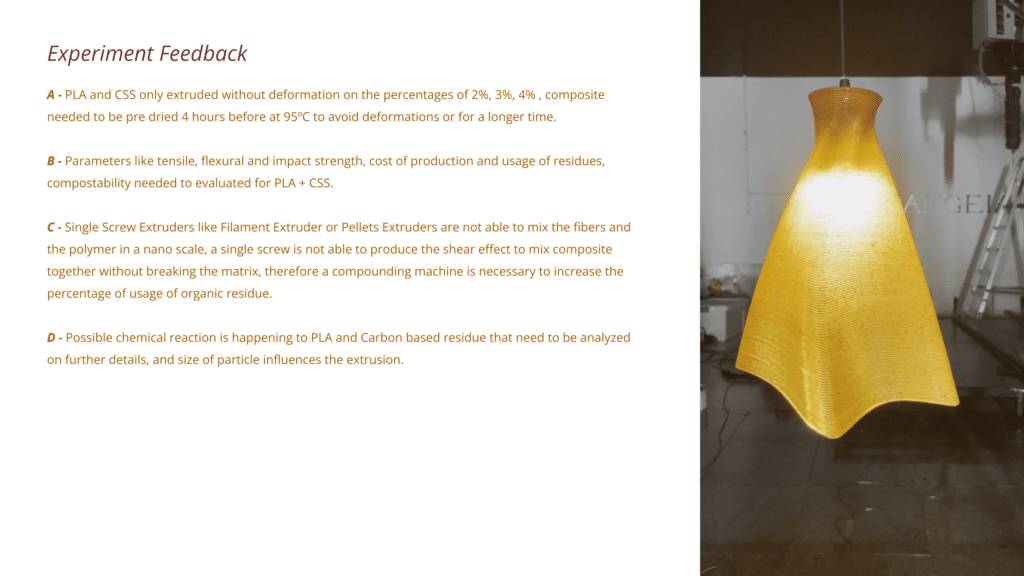
By understanding the feedback of the first experiment the second experiment aimed to answer the question of “What is causing the bounding problem?” utilizing a single screw fillament extruder and evaluating by the lenses of a microscope to discard possible chemical reactions. 200g of PLA were added to the hopper along with 1%-5% Cacau Fillers by the weight of PLA. They were dried prior to the extrusion of 6h and 70ºC.
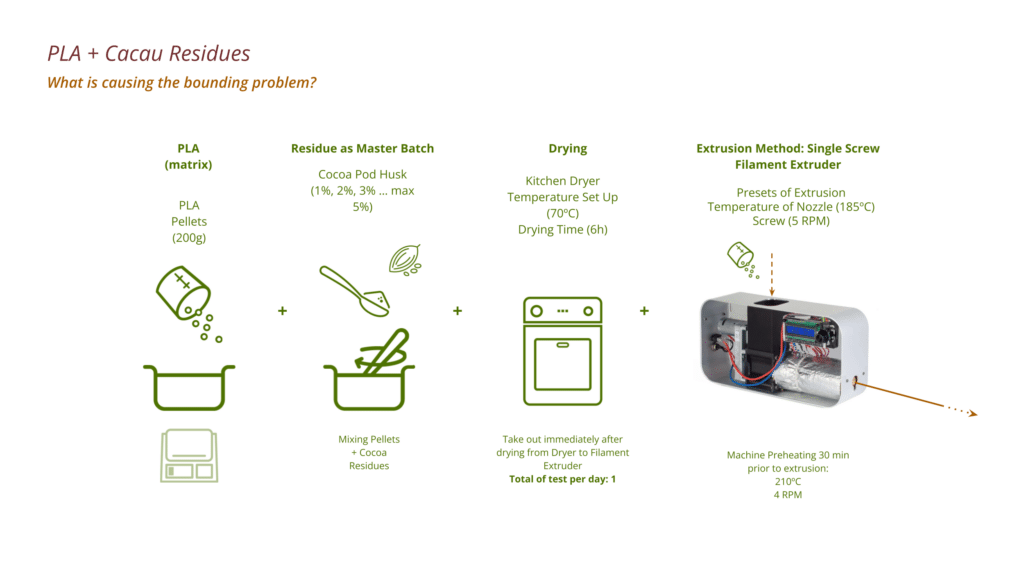

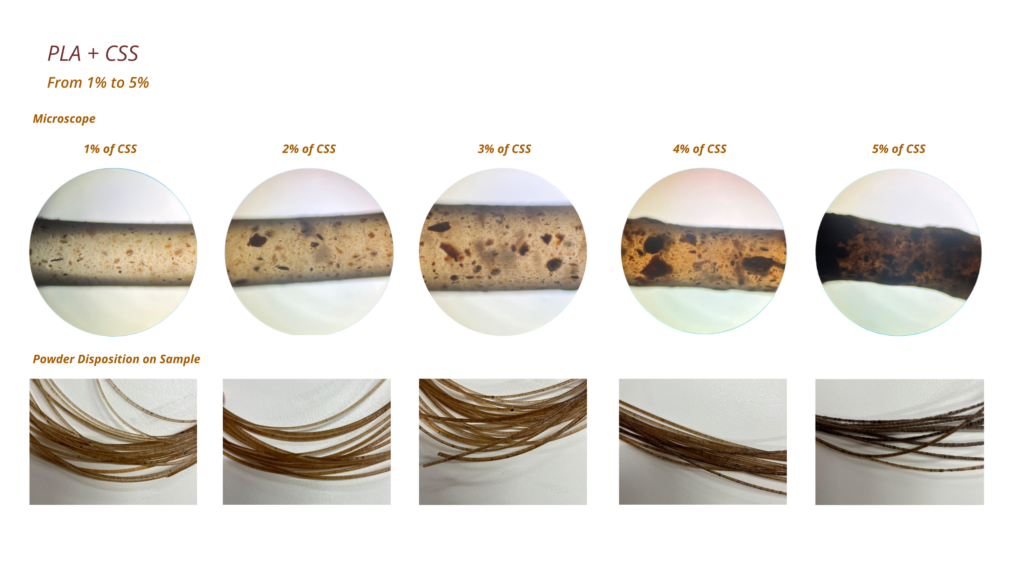
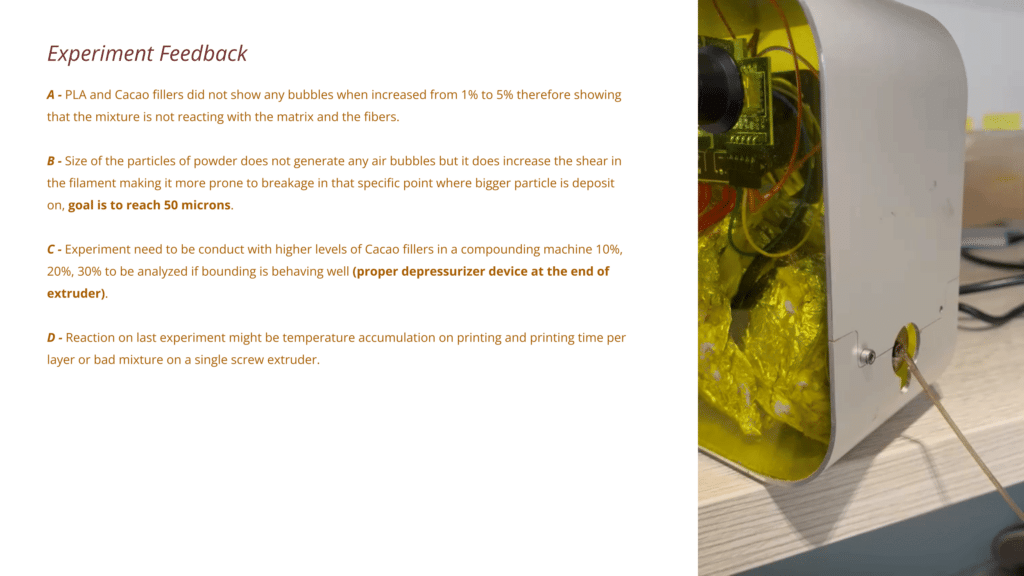
Based of the last experiment and the no apperance of a chemical reaction to the bounding of the filler + matrix, it was observed that a single screw extruder is not enought to bound the fine powder filler and the plastic matrix at a nano level, because it does not allow for shear stress to happen for the bound to be completed, also a degassing chamber is essential to this process due to the characteristic of the polylactic acid of PLA. In this new experiment an industrial compounder was utilized and the question was “With and Industrial Compouder can we increase the fillers in the matrix without deforming it?”. Percentages of 10%, 20%, 30% were tested and on the preparation of the Filler a sifting process was added to guarantee the 50 mícrons sizes of the particle.
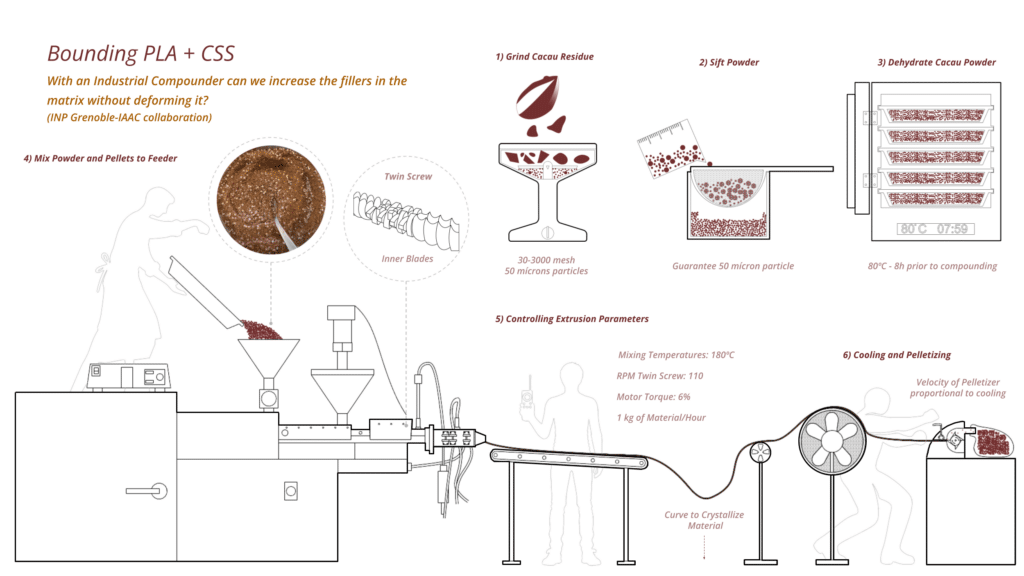
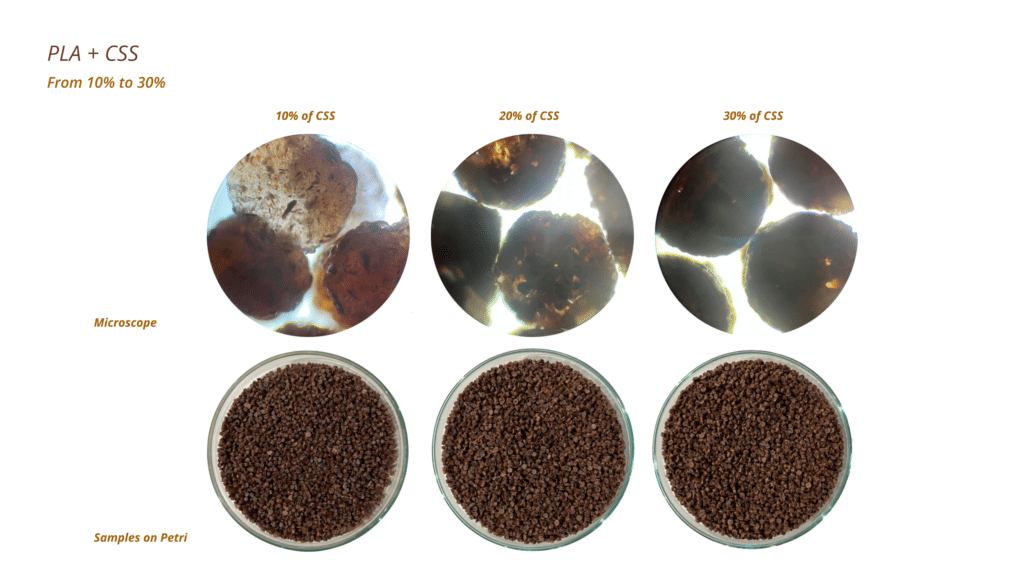
With an industrial compounder 1kg of material was extruded by 1 hour, with the mixing temperatures being 180ºC, rpm of the screw 110 and motor toque of 6%. the material needs time to crystalize before pelletizing. With the microscope lenses we can see the addesion of Cacau Fillers more distributed than the single screw that the particle size was prone to crack the location of particle, whereas the use of a compounder transform the material to be more distributed and homogeneous along the pellet. By printing it in a industrial 3D printed (WASP Delta). It was observed that the material started to show not only a opaque colour, but to behave different than regular PLA that behaves like a crystalized plastic and it begins to embedded porosity on the material (sounds like wood, presence of air).
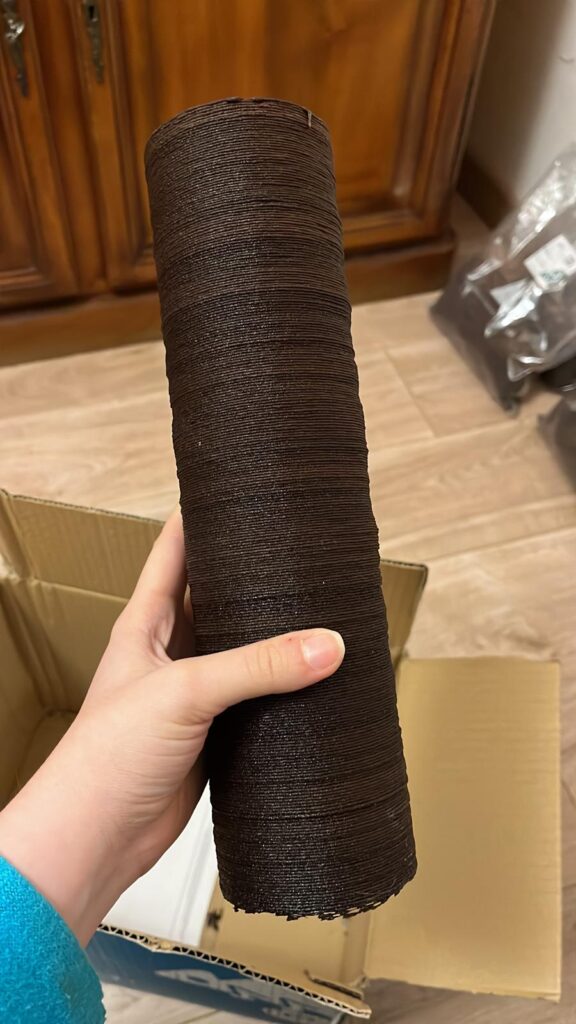
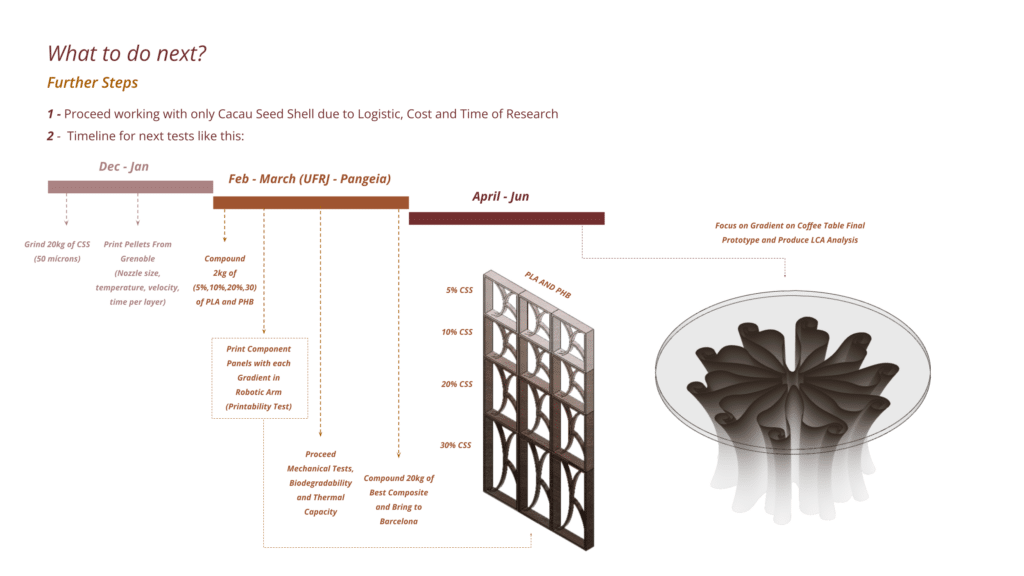