can robots and humans work hand in (hand) to create beautiful architecture?
KOMA is a contemplative space, designed to be set in the landscape and allow for peaceful viewing, the form of KOMA is parametric and is able to sway with the wind through the use of tensile cables. The vertical timber elements were placed using a robotic pick-and-place process, where the robot picked components from a gravity feeder and positioned them onto a defined base. The elements were then manually screwed together to form nine panels. Later, these panels were assembled into a 3×3 grid, creating the final pavilion structure. Tension cables were added to enhance stability and allow for movement.
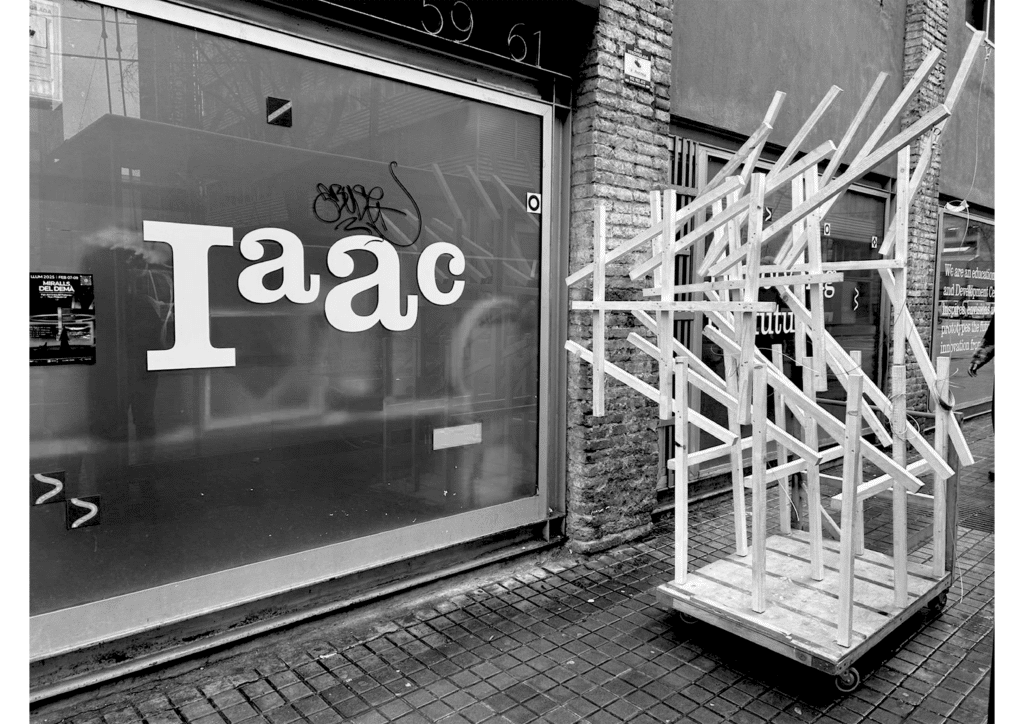
state of the art
searching for inspiration, some of the examples we came across led us to contemplate how robotic fabrication can play a role in advancing complex timber constructions. specifically kengo kuma’s intricate lattice facade in tokyo’s minami-aoyama area brought up the question of whether robotics could facilitate a speedier, more precise construction?
furthermore, theo jansen’s strandbeest, with its kinetic adaptability to natural forces, inspired this projects dynamic structure, although coma is static when placed in site, it has the possibility to change its angles according to a different setting it might be placed.
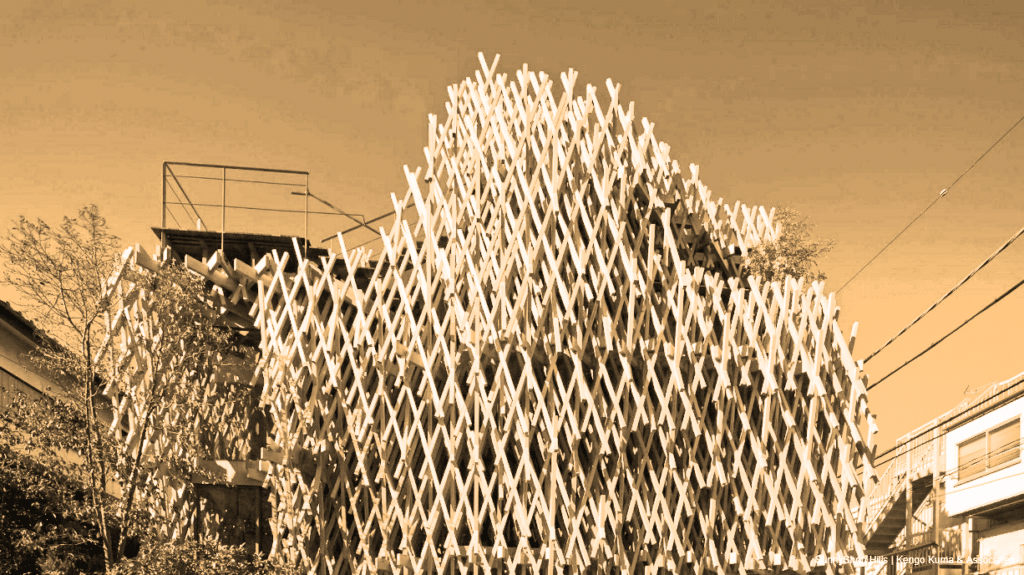
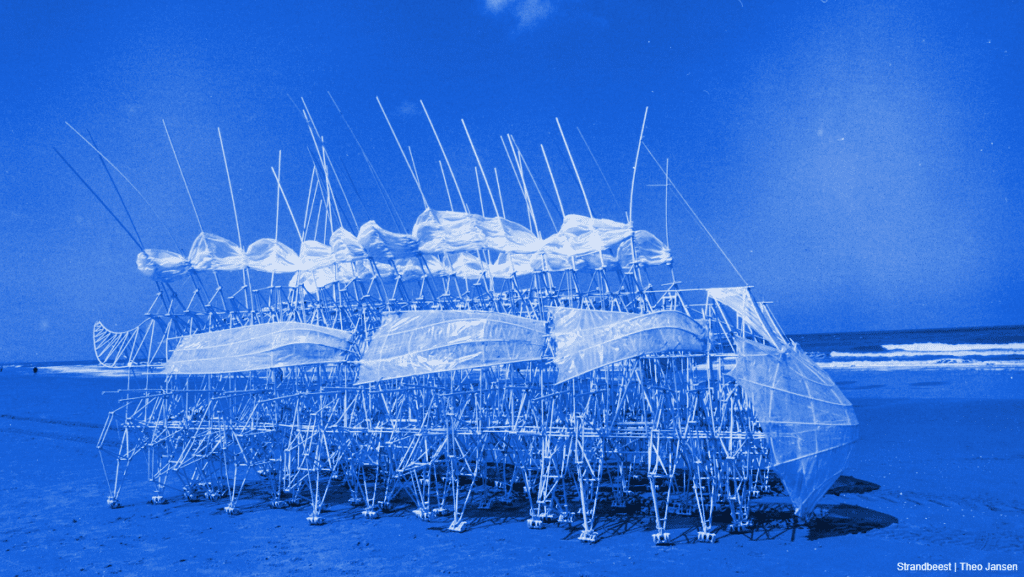
components
given the available materials, 38mm x 38mm x 2000mm sticks. We chose to explore methods of robotic assembly that would take uniform pieces and create patterns that are not complex on their own, but start to develop a language of repeated patterns that change ever so slightly.
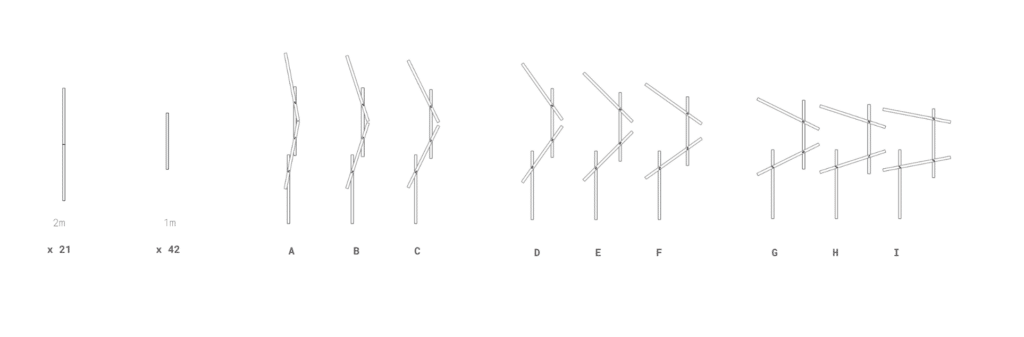
pick + place / assembly(1)
the assembly method assigned was pick and place. for the pick component a gravity feeder was designed according to the stick sizes of the design. for the place movement the robot cell was not large enough in length and width therefore we had to place the base diagonally to avoid any collisions.
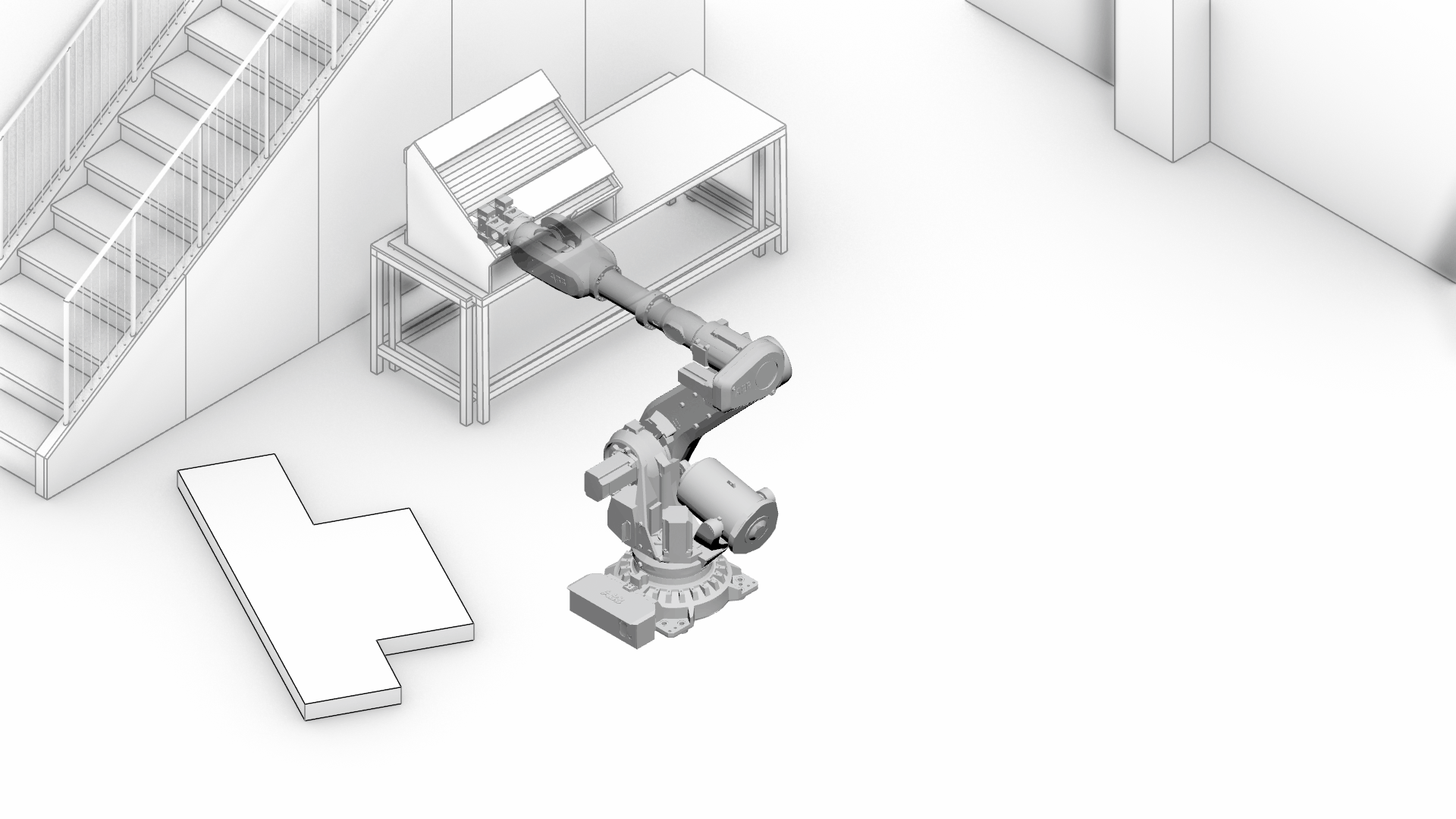
pick + place / assembly(2)
a speculative assembly method: instead of placing each stick horizontally on the base, the robot would place bottom most sticks in a pre-cut base – reducing the manual fabrication part of the fabrication.
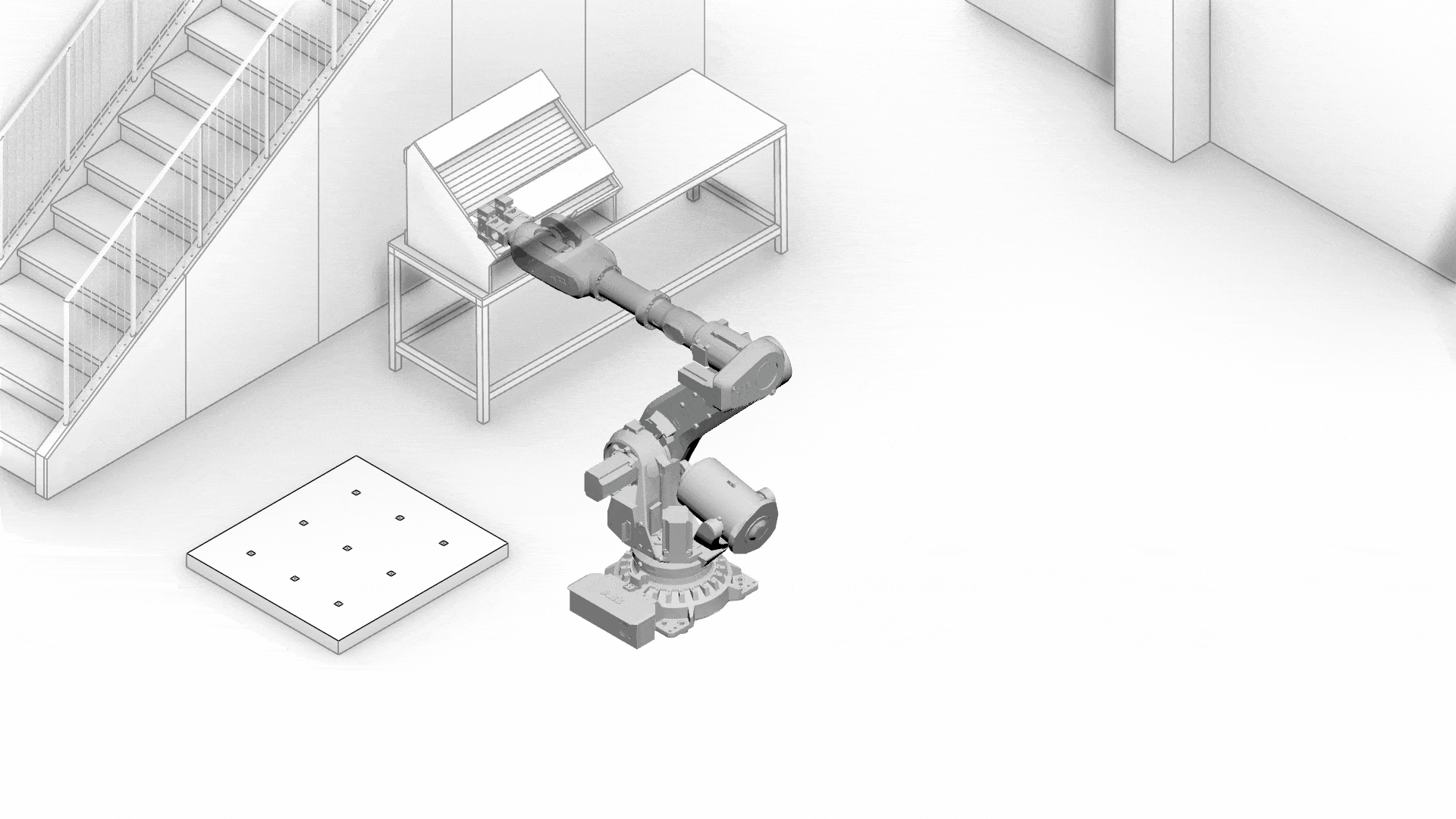
structure
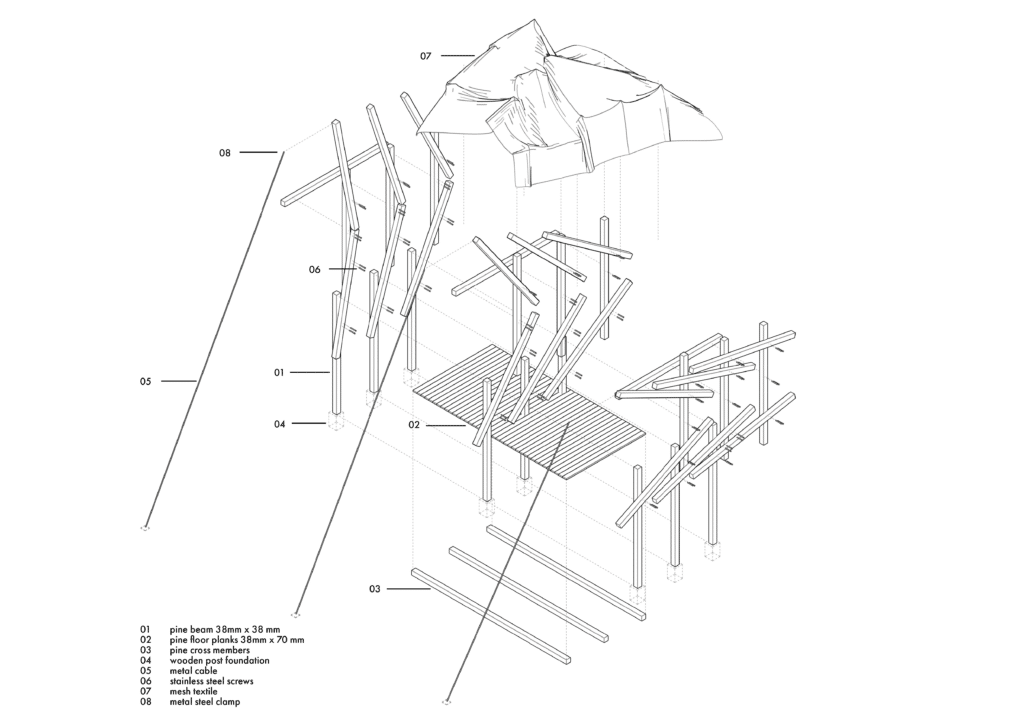
connection details
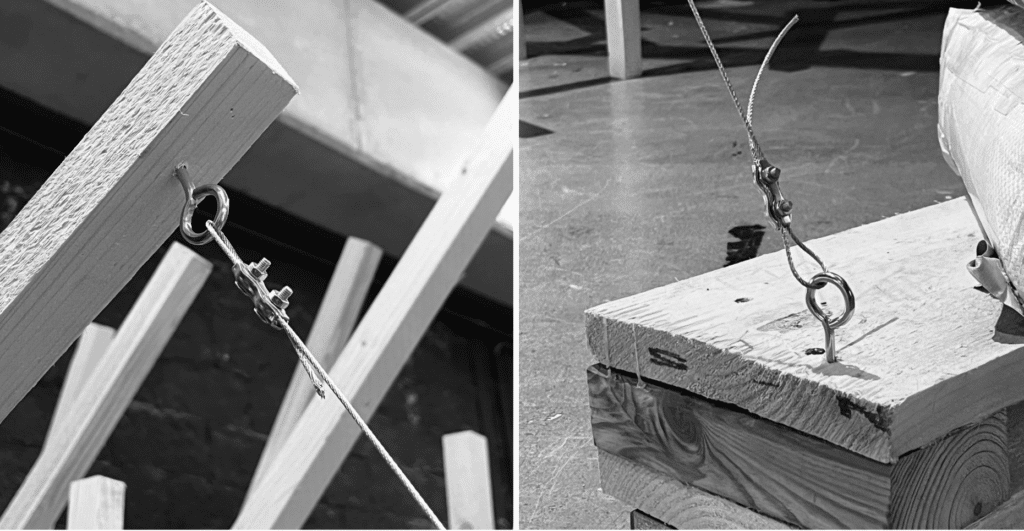
drawings & renders
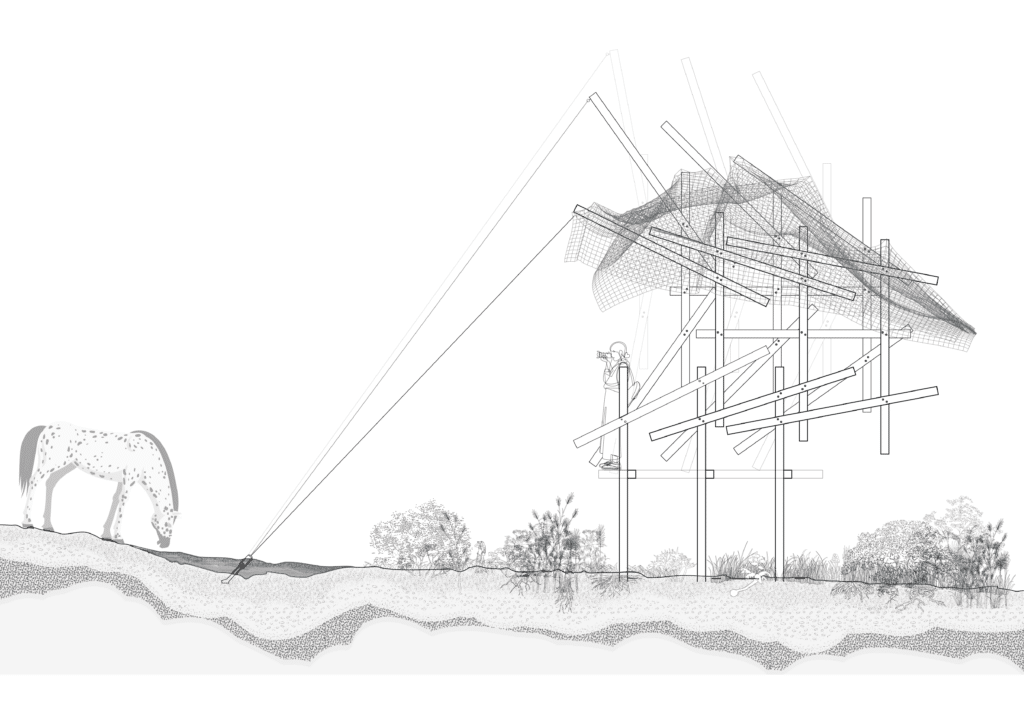
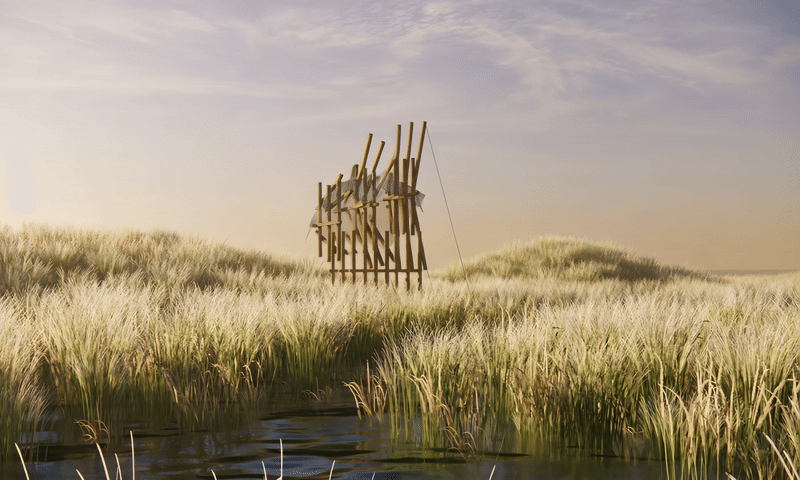
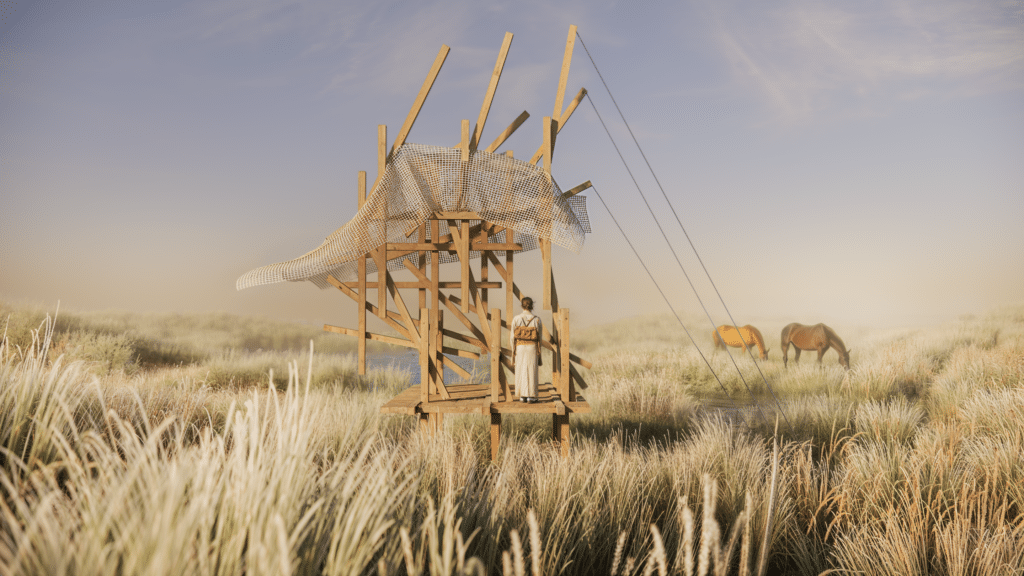
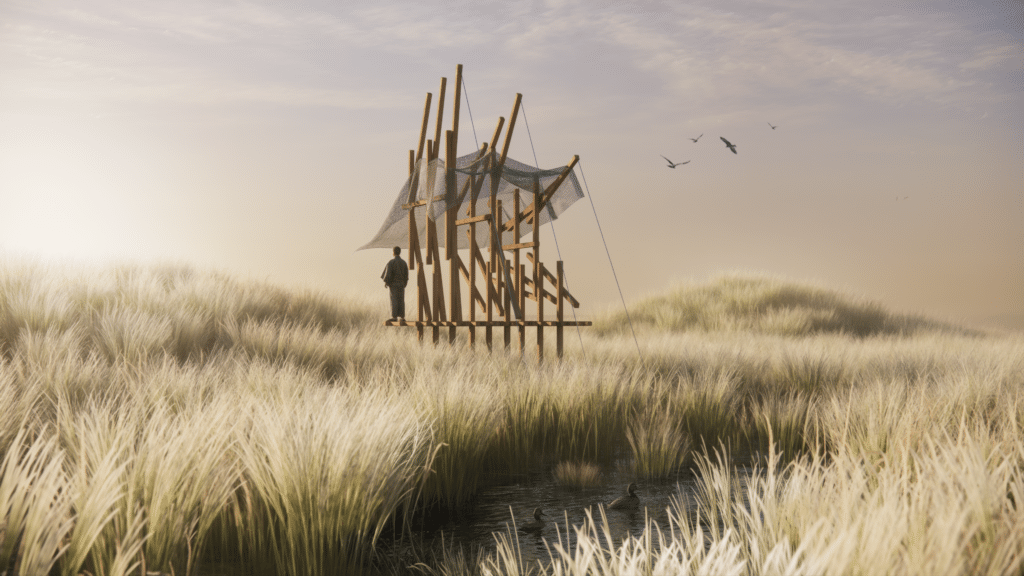
prototype
the first prototype displayed at IAAC Atelier.
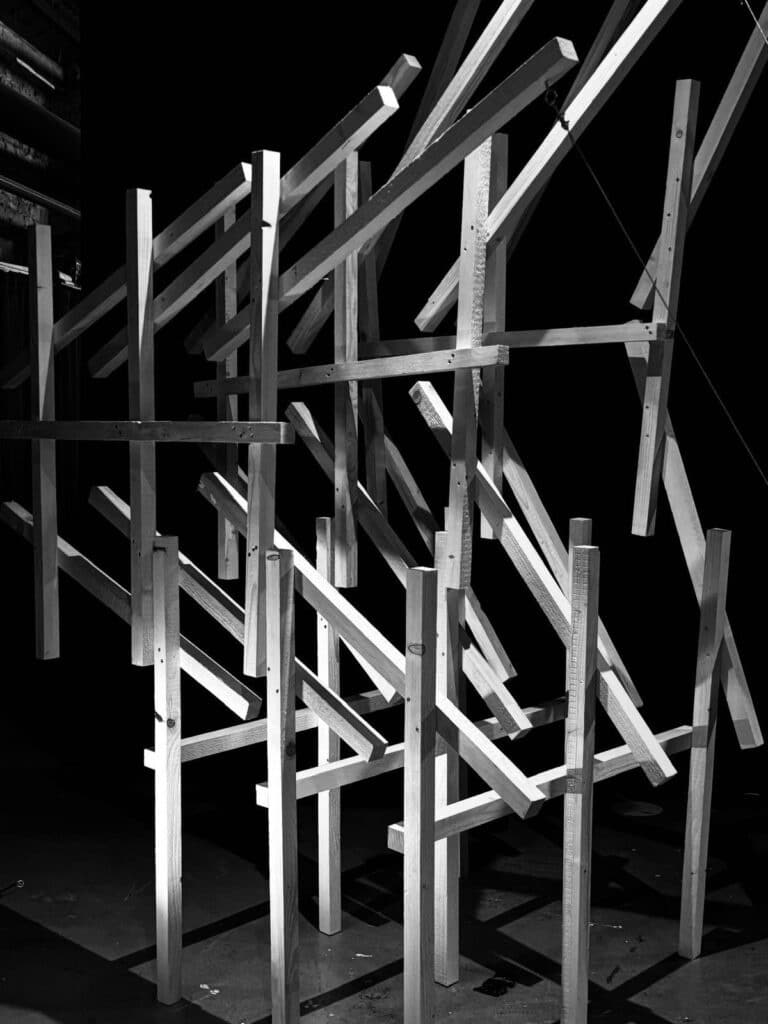
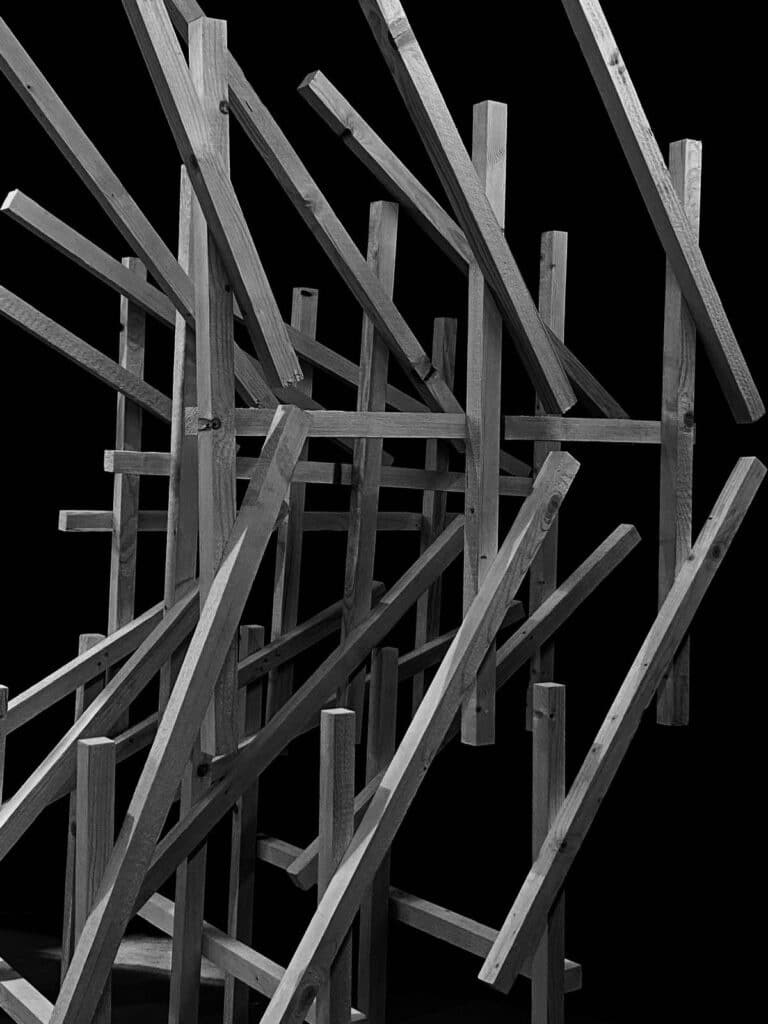
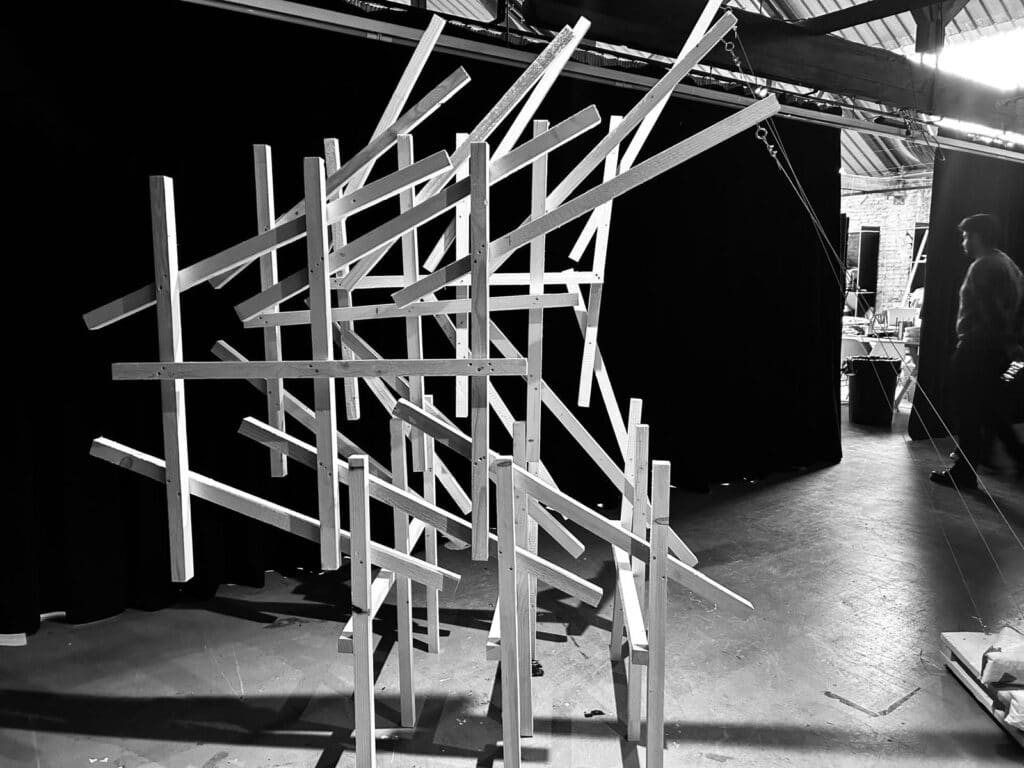
caught in transit
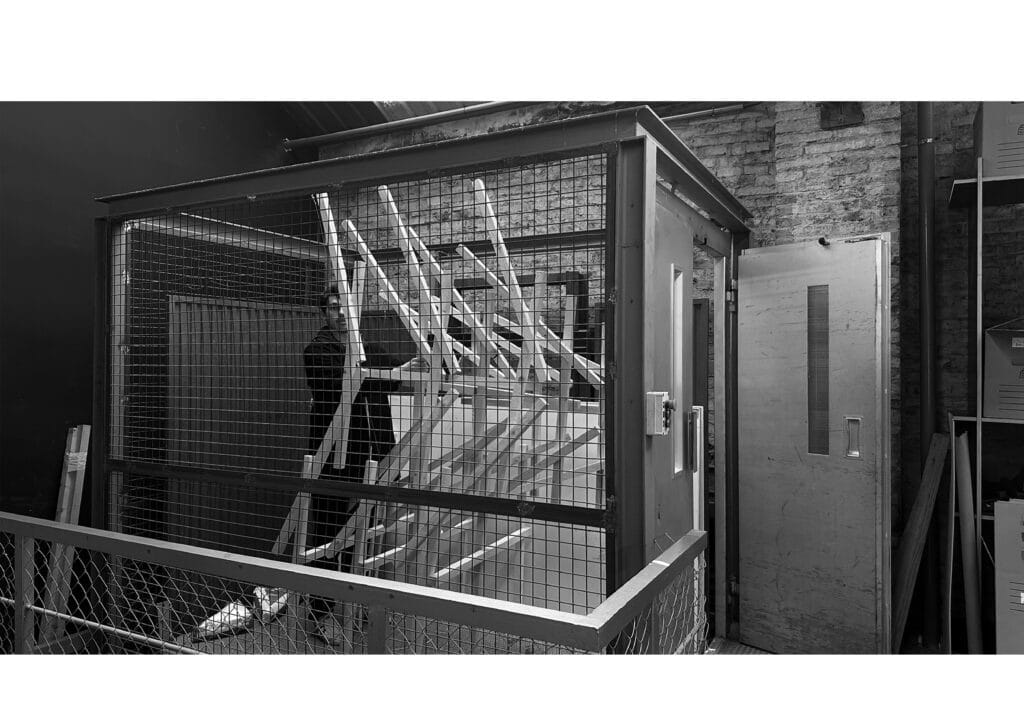
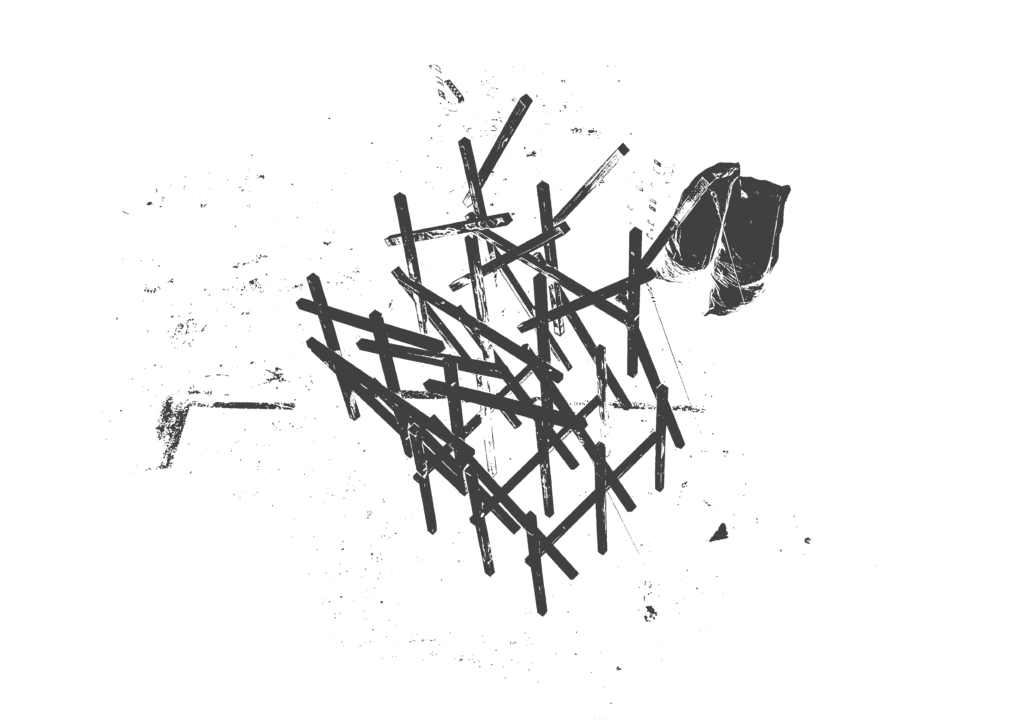