Hybrid Timber and Stone Constrcuction System Utilisng 6-axis Robotic Fabriction
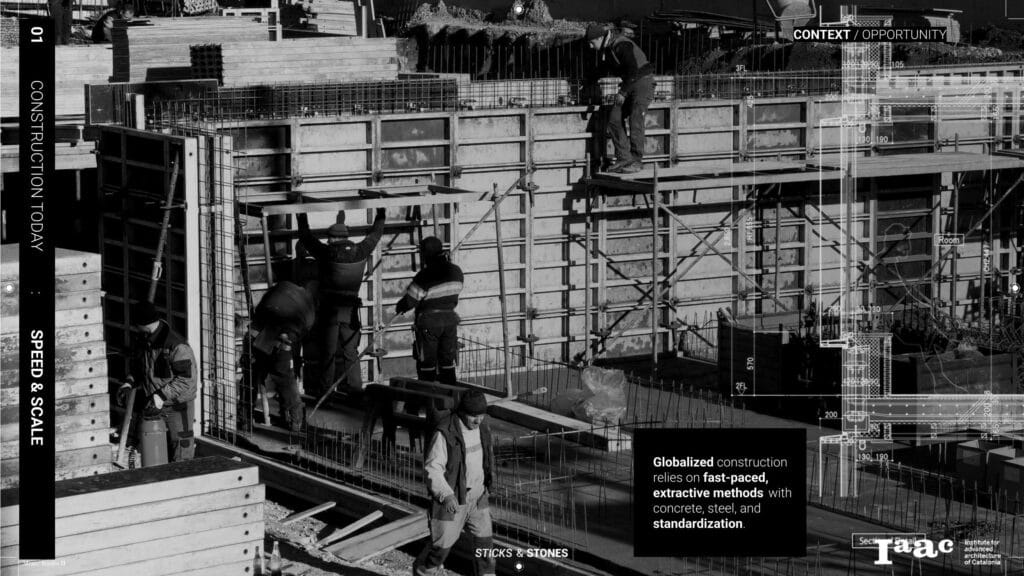
Our research begins with a critique of how we build today. Technological advancements have enabled rapid, standardized, and seemingly affordable construction. But these efficiencies hide deeper costs. In reality, we’re paying through the loss of cultural specificity, environmental integrity, and material identity. What emerges is not a low-cost system, but a hidden-cost system—one that obscures its impacts in the name of progress. The global construction industry has achieved speed and scale, but it has done so by flattening diversity, replacing nuance with repetition, and detaching buildings from place and meaning.
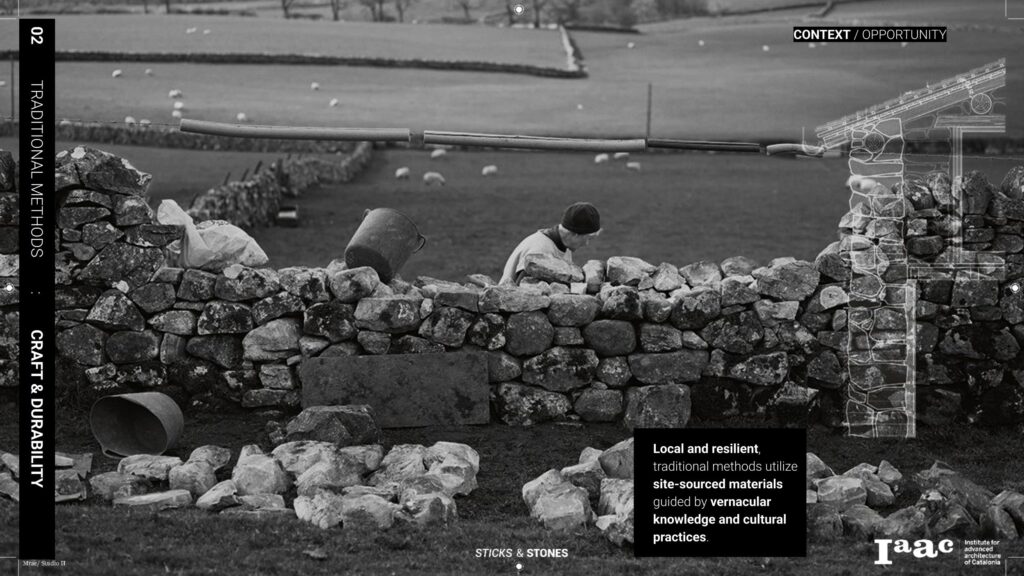
So perhaps we look backward—not out of nostalgia, but to recall a different architectural logic. Historically, construction was rooted in place. It emerged through generational adaptation, shaped by cultural memory and material availability. Buildings were slow but meaningful—they reflected people and environment in dialogue. Yet these ancient modes can no longer respond to the urgency of the global housing crisis. They are too time-intensive, too costly. Our challenge is to extract the intelligence of these systems—without replicating their limitations. Can we retain their sensitivity while meeting today’s demands?
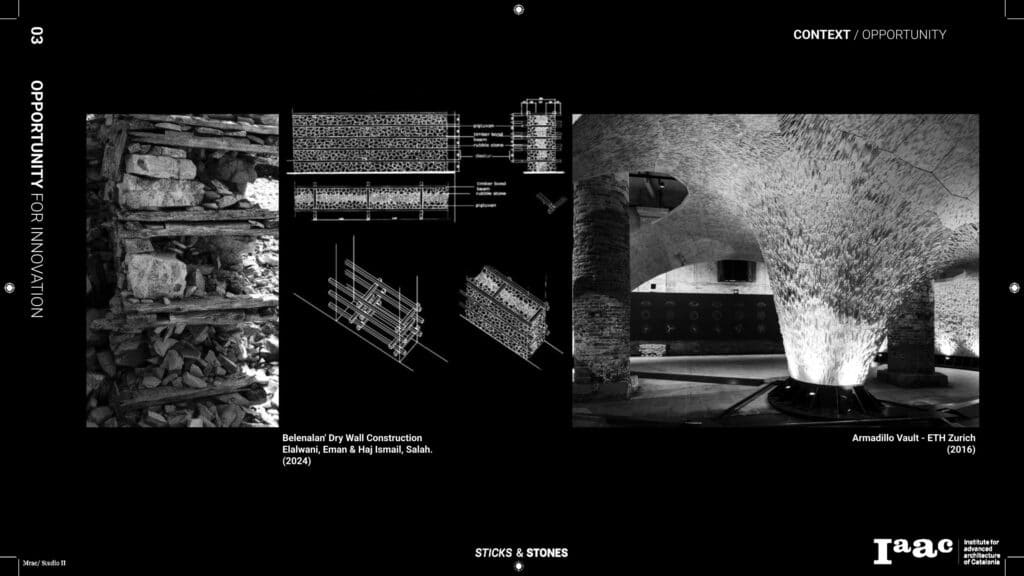
Two materials drew our attention: timber and stone. Both rich in tradition, both widely available. In Turkey’s Anatolian region, belenan drywall construction used interleaved stone and timber layers for seismic resistance—deliberately allowing movement. Today, precision fabrication is reinterpreting these materials with new accuracy. The Armadillo Vault at the 2016 Venice Biennale demonstrates how traditional logic and robotic precision can converge. Stone and timber are no longer primitive—they are programmable. Their structural capacities can be enhanced, not replaced, through digital methods. That’s where our investigation begins.
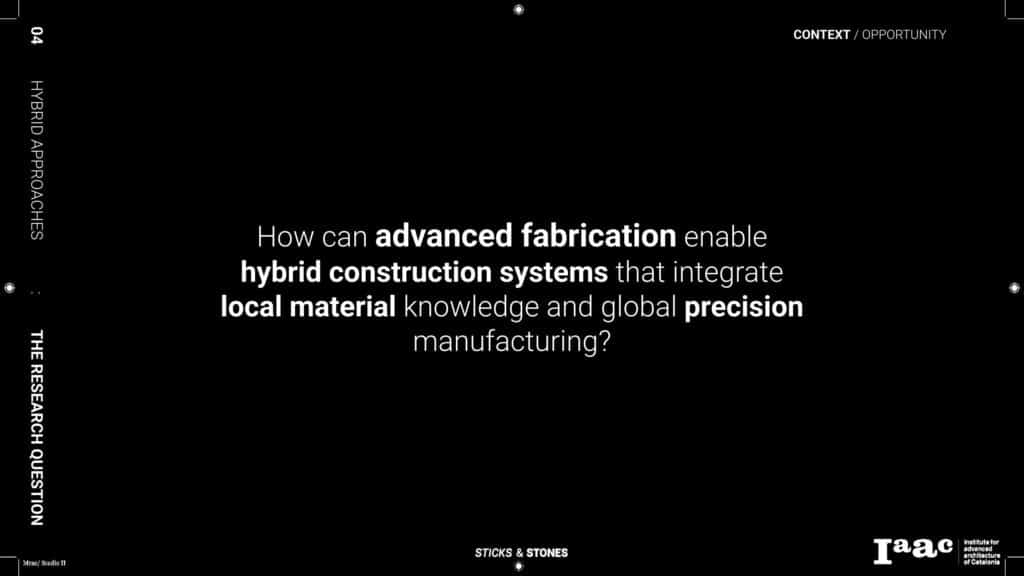
Our research asks: How can advanced fabrication enable hybrid construction systems that integrate local material knowledge and global precision manufacturing? The question challenges us to rethink what “advanced” means. Can digital tools make traditional materials viable again—not just in form, but in performance? We aim to explore whether stone and timber, when restructured through computational design and fabrication, can become the basis of a new architectural system. One that is competitive, robust, and adaptive—drawing from the past while engaging the present.
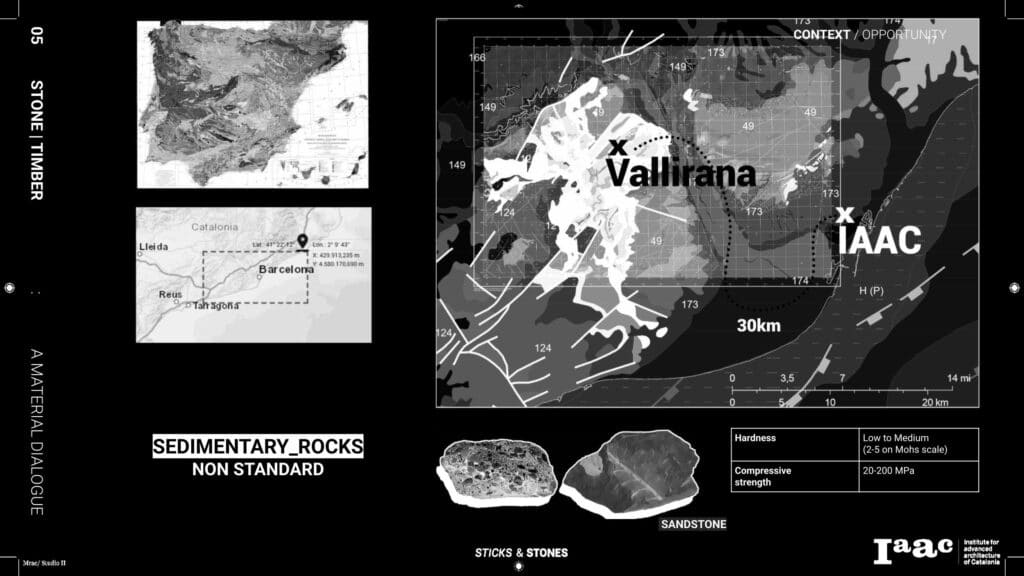
To stay grounded, we restricted ourselves to local materials from the Catalonia region. For stone, we searched for something homogenous, naturally boulder-forming, and soft enough to process. We became, for a time, stone hunters. Vallirana sandstone, with its warm tones and workable grain, proved ideal. For timber, we used standard engineered pine profiles—aiming for wood sourced as locally as possible. Catalonia has vast forests and abundant pine, making it a logical partner. This approach was about more than logistics—it was about grounding our system in place.
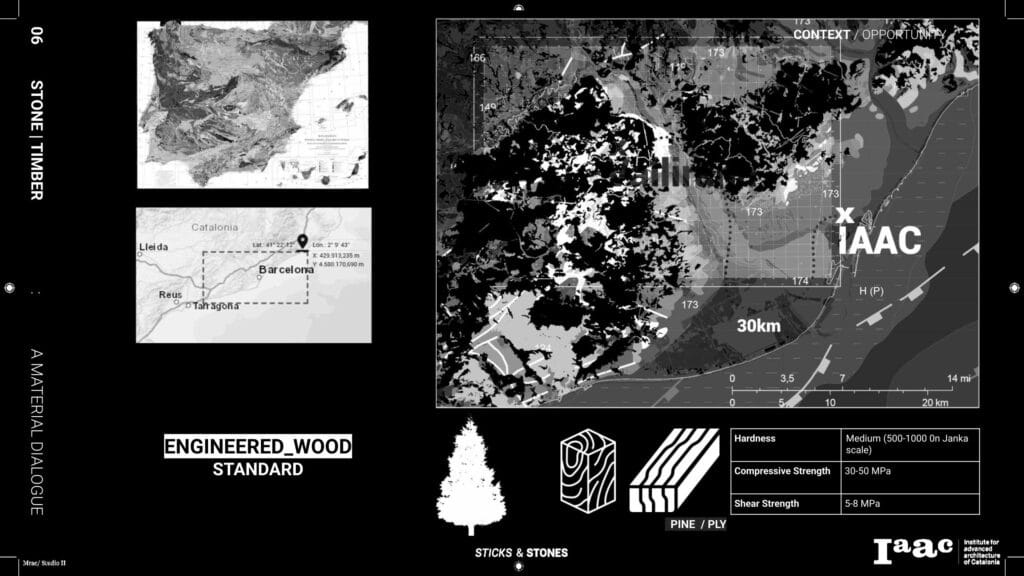
Understanding the materials was crucial. Stone is hard, dense, and performs exceptionally in compression. But it’s brittle, heavy, and nearly useless in tension. Timber, by contrast, is light, flexible, renewable, and strong in tension—but comparatively weak in compression. These two materials, seemingly at odds, are in fact perfectly complementary. Our goal was not to overcome their limitations individually, but to design a system where each material could compensate for the other. A dual-material strategy that activates their natural strengths.
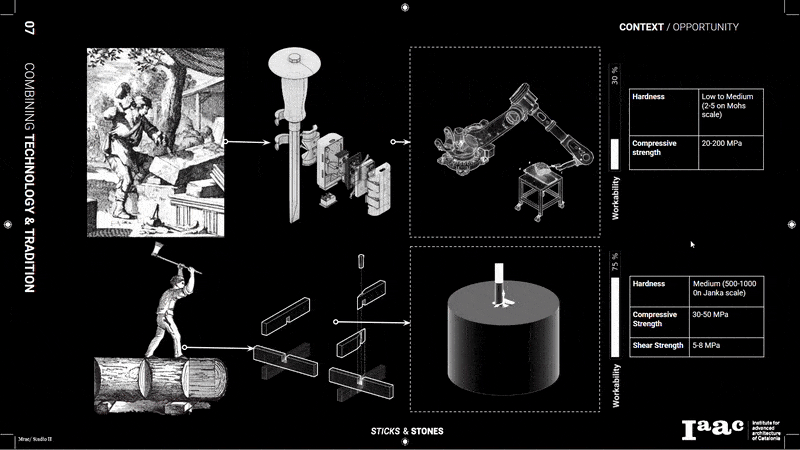
Technology allows us to reframe tradition. Our hybrid system is built on the premise that each material should only do what it does best. To that end, we studied historical techniques—Japanese tsugite joinery for timber, and traditional stone chiseling practices—to inform digital fabrication workflows. Robotic tools didn’t replace these traditions; they extended them. By translating analog logic into digital precision, we created joinery that’s both rooted in craft and enhanced by computation.
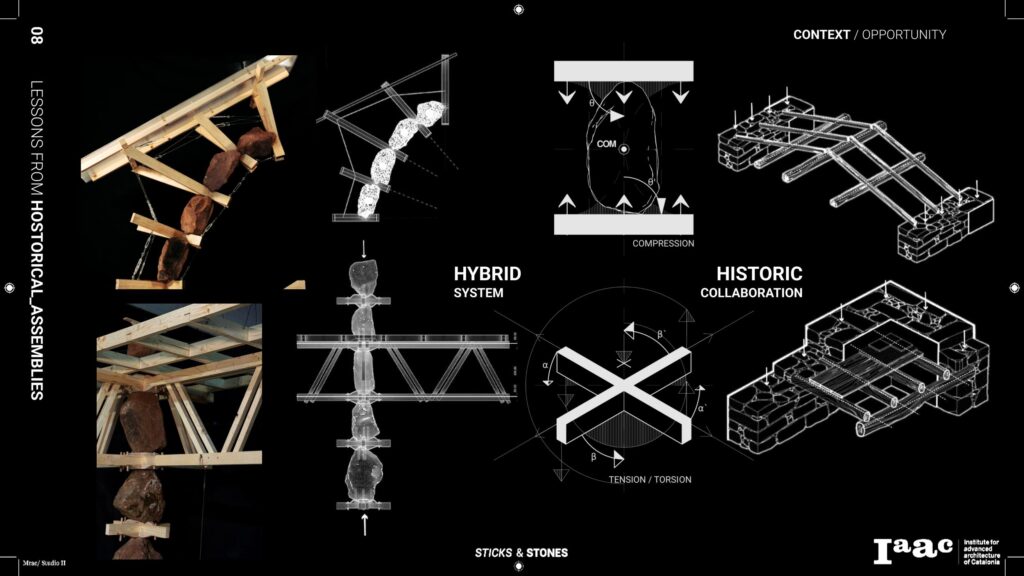
The system we propose creates digitally calibrated joints between stone and timber. Stone becomes the primary load-bearing member, transferring vertical loads into the ground through compression. Timber acts as the flexible connector, forming soft-tolerant joints and bridging elements. Together, they form a hybrid frame where each material lifts the other. Processing is minimal. Waste is reduced. Assembly is intuitive. This isn’t about reinventing materials—but about revealing the logic that emerges when they work in dialogue.
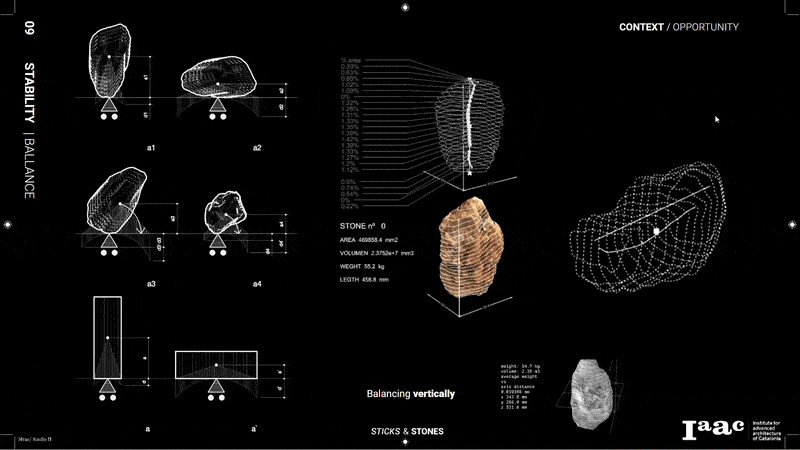
Our design method is rooted in balance—literally. Since we do not process the stones, each one arrives with a unique geometry. Stability becomes a geometric question: where is the center of mass? What’s the axis of maximum inertia? Using machine learning, we developed an algorithm to detect optimal balance points for each stone. These points guide the placement of joints, load transfers, and alignment. This allows us to assemble irregular forms into structurally coherent systems—without forcing uniformity.
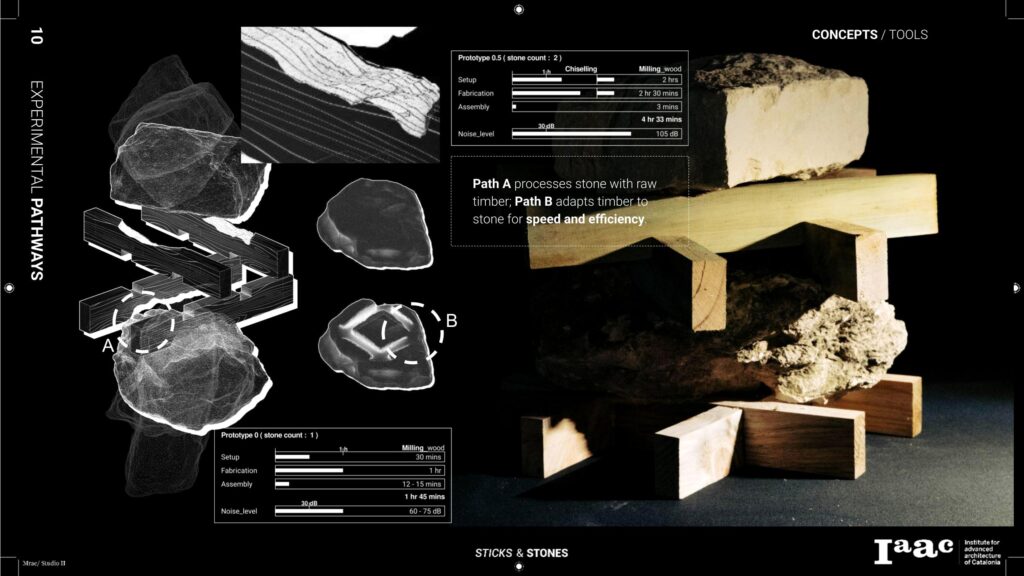
To connect stone and timber, we explored two distinct strategies. The first avoided processing the stone entirely. Instead, we CNC-milled the timber to match the negative imprint of the stone’s surface. The second involved robotic chiseling—cutting precision sockets directly into the stone for timber insertion. The imprint joint was easy to manufacture but harder to assemble and lacked rigidity. The chiseled joint was robust and intuitive during assembly, but significantly more time- and labor-intensive to fabricate. Each approach offered trade-offs.
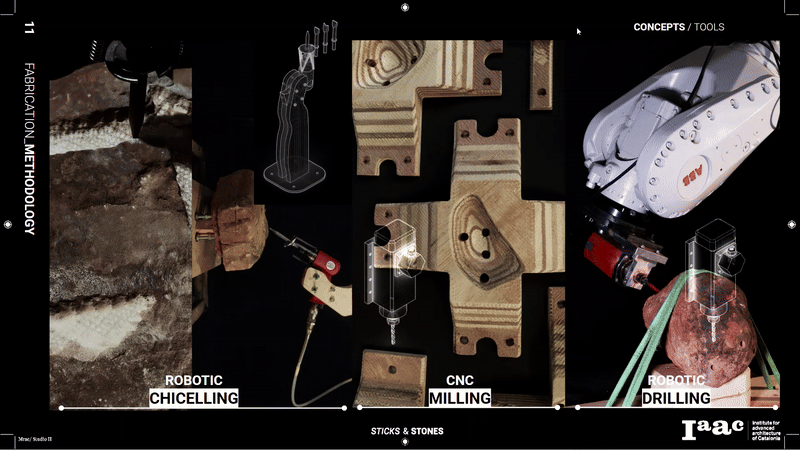
Our fabrication system combines three digital methods:
6-axis robotic chiseling, to carve joints directly into stone.
6-axis robotic drilling, for precise dowel placement and alignment.
3-axis CNC milling, to shape timber elements and embed joinery.
This combination gave us a flexible toolkit for experimenting with geometry, connection logic, and structural behavior. It also allowed us to compare levels of precision, tolerance, and efficiency across material workflows.
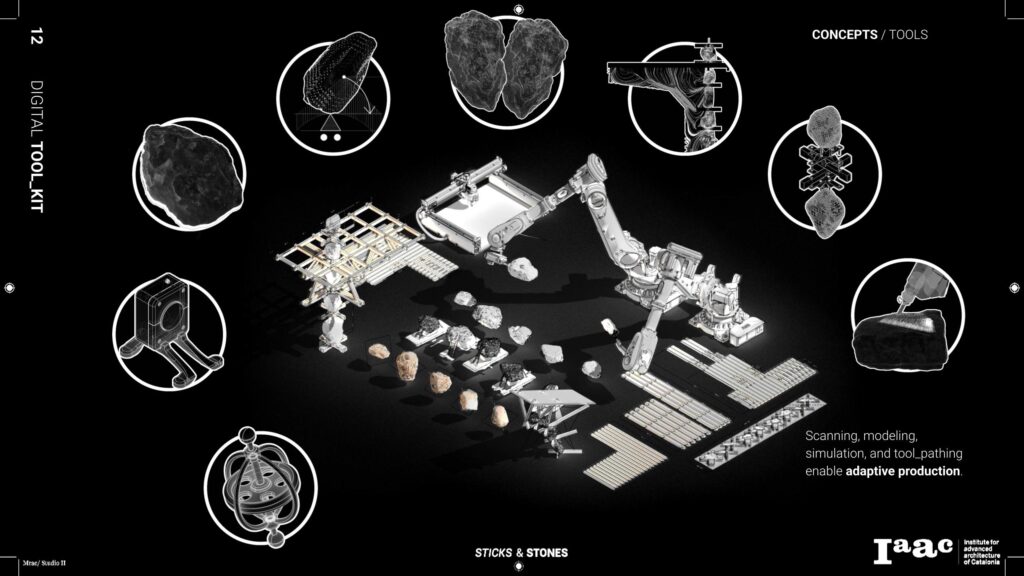
A key challenge was maintaining coherence between the physical and digital. Scanning was central to this. We created digital twins of every stone, forming a geometry library. These models were used for joint design, motion tracking, and simulation. Algorithmic joinery generation allowed us to adapt to each stone’s unique form. Structural analysis guided decision-making. Toolpaths were not fixed—they responded to site conditions. The system remained adaptive throughout, treating fabrication as an open dialogue rather than a fixed process.
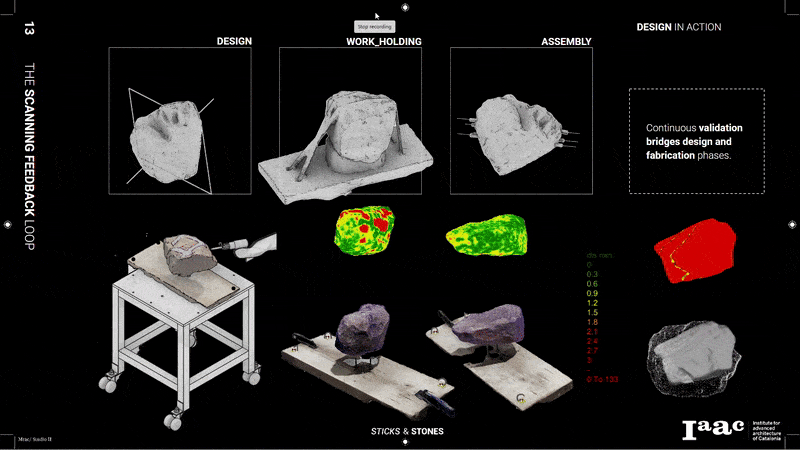
Scanning occurred in three phases. First, an initial scan captured the geometry for design and library entry. Second, during fabrication, we aligned the digital model to the real-world stone using pose-matching algorithms—critical for precision jointing. Finally, post-fabrication verification ensured the finished component matched our design intent. This allowed for final tweaks, tolerance compensation, and iterative adjustments. Scanning was the linchpin—bridging design and reality, enabling accuracy without sacrificing adaptability.
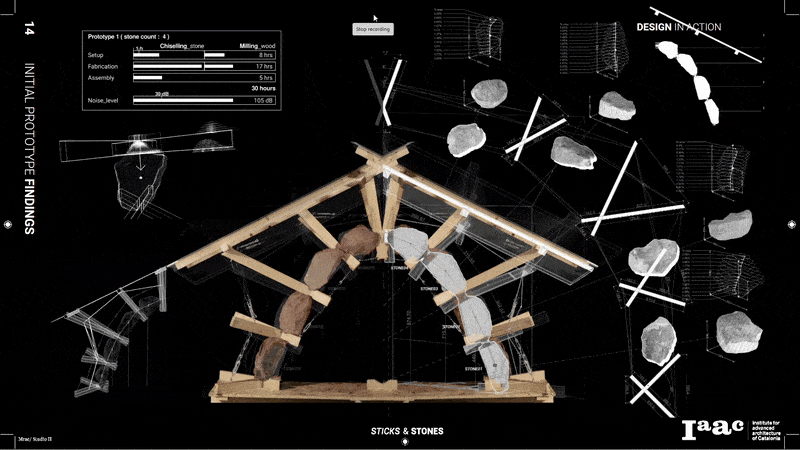
Prototype I explored chiseling as the primary fabrication technique. Timber crosses acted as structural keys, locking each stone in place. Each cross was fabricated at a unique angle, responding to the geometry and centerline of its corresponding stone. This prototype showcased the geometric precision achievable through robotic carving. Since we only completed half the arch, we used cables to stabilize the structure through tensegrity. It took five days to complete—from scanning through to assembly.
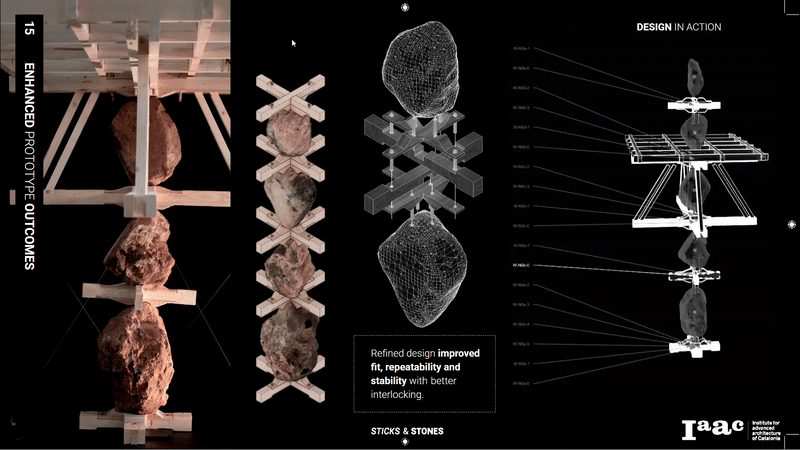
Prototype II was a response to time constraints—and to noise complaints. Chiseling, it turns out, is loud. So we shifted to a faster workflow: robotic drilling combined with CNC-milled timber. Timber pieces were shaped with stone imprint joints, while dowels enabled precise alignment. This process was far quieter and faster—under three days to fabricate, a few hours to assemble. The result was efficient and clean, albeit less structurally expressive than the chiseled counterpart.
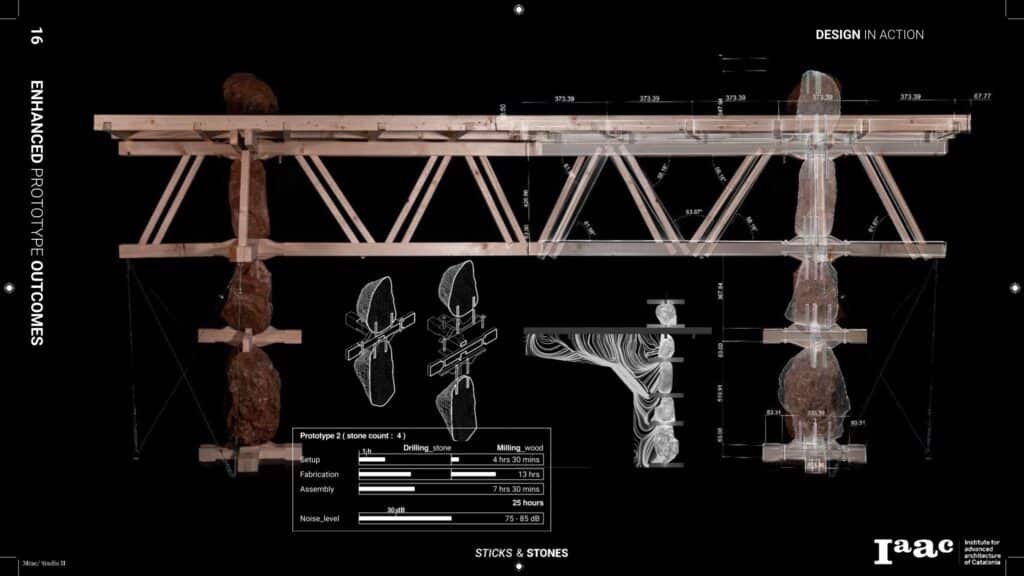
What surprised me about Prototype II was how smoothly everything came together. Like flat-pack furniture, every part just slotted in. It wasn’t a compromise or a refinement of Prototype I—it was a completely different strategy. Much faster, much easier to assemble, and far more efficient. But also, far less robust. The chiseled joints in Prototype I are stronger and allow for future stone-on-stone contact—important when timber eventually decays. I see both strategies as valid. Chiseled joints for permanence; drilled imprint joints for fast, scalable deployment.

To evaluate feasibility, we deployed our system in a proposed architectural context: IAAC’s future campus at Avilla, a former fridge factory. We integrated sticks-and-stones columns into the atrium of the proposed building design. This allowed us to test scale, integration, and realism. More than a prototype, this was a case study in how our hybrid system might function structurally and spatially—demonstrating its ability to act both as primary structure and connective skeleton.
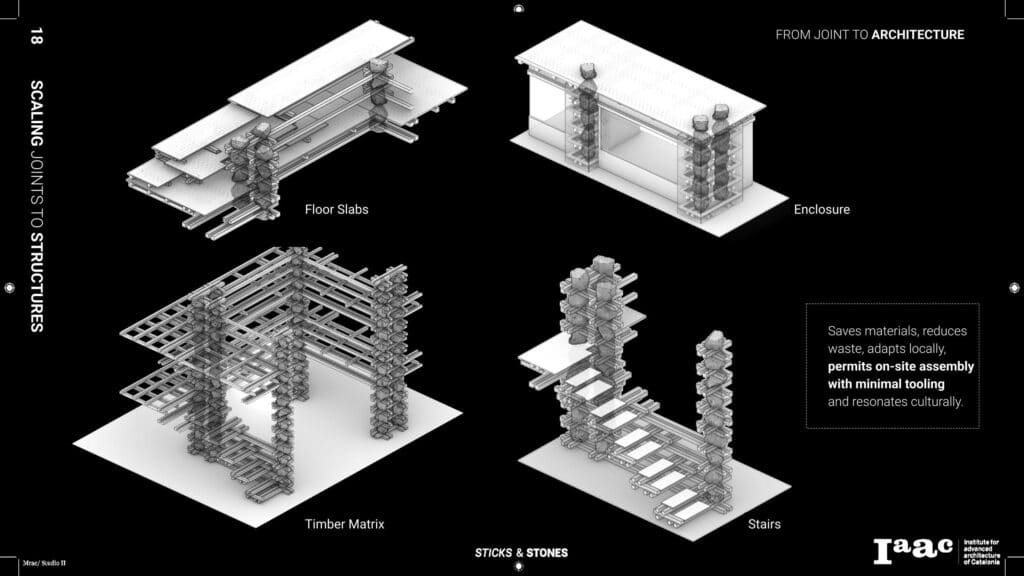
The system’s strength lies in its adaptability. It transitions fluidly between functions—becoming stairs, mezzanines, structural cores. The joinery logic easily integrates into a broader timber matrix, allowing connections to floor slabs and enclosures. We also showed how interior partitions can be made using the same principles, enabling complete spatial divisions. This isn’t just a method for isolated joints—it’s a construction logic that can scale into architecture. It creates structure, connection, and space in one cohesive strategy.
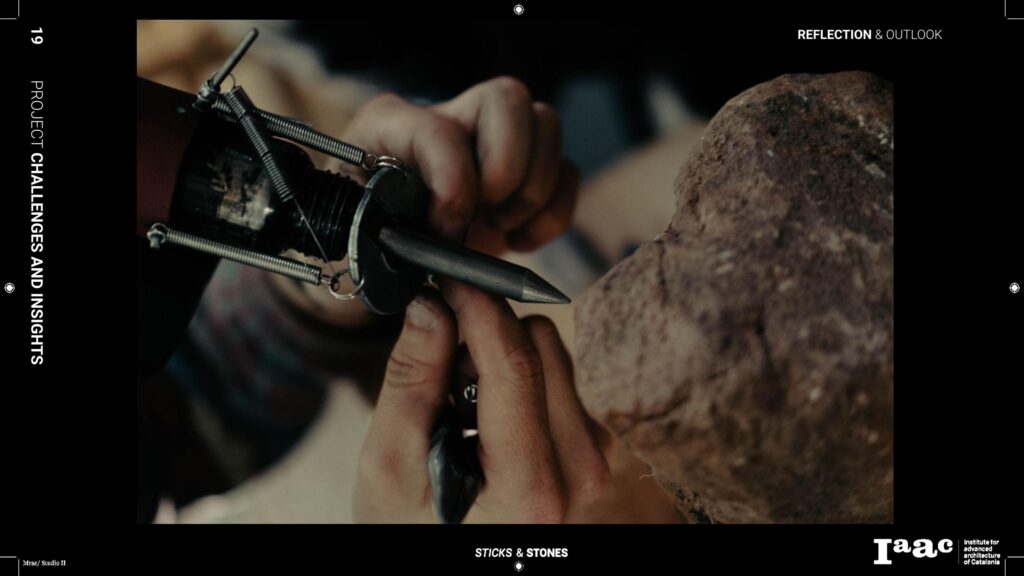
Of course, limitations remain. We’ve only demonstrated linear assemblies. We haven’t yet proven how this system becomes planar or volumetric. Robotic fabrication times—especially for chiseling—remain a bottleneck. And while our assembly process works, it still demands precision labor. In the context of European construction trends—where low-labor systems are gaining traction—we need to improve both automation and on-site tolerances. These aren’t dead ends, but known challenges for future iterations.
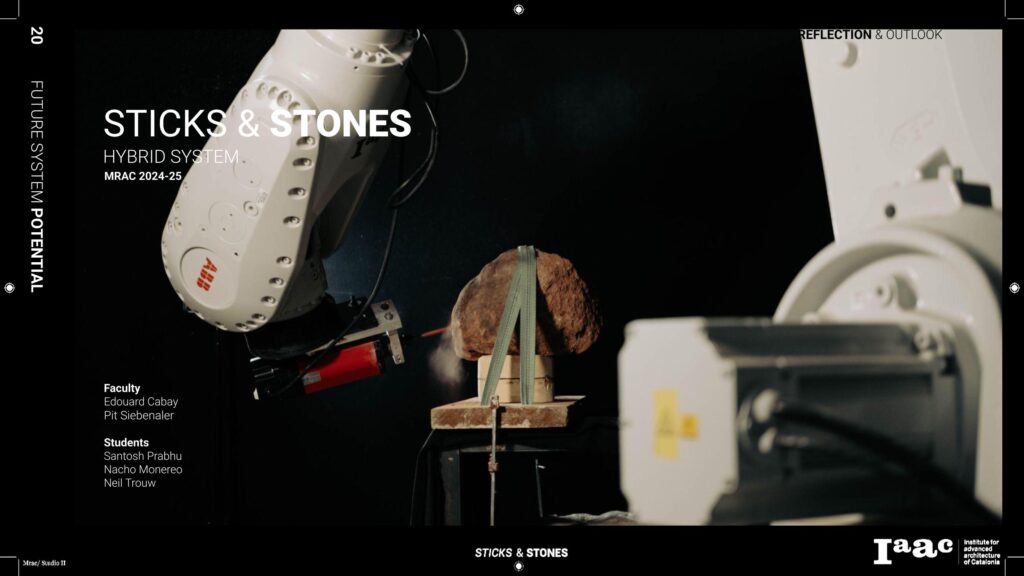
Even so, we’re proud of what we’ve achieved. We’ve demonstrated that timber and stone—when digitally coordinated—can form a hybrid, high-performance construction system. With more time, better tooling, and refined workflows, this joinery logic can evolve into something architectural at scale. These prototypes are just the beginning. Perhaps in the future, all you’ll need are some sticks, some stones, and a robot—and from that, architecture can emerge. That’s the dream we hope to share with you.