State of the Art and Minimum Value Proposition
There is an overstocking of small to medium trees over Europe due to poor firing and soil cultivation conditions, most of this trees have the diameter of 10-25 cm and depending on the species and cultivation conditions some of then are crooked and can’t be used by the wood industry. Some european countries, like Switzerland, rely mostly on importation of straight trees and less on locally sourced wood.
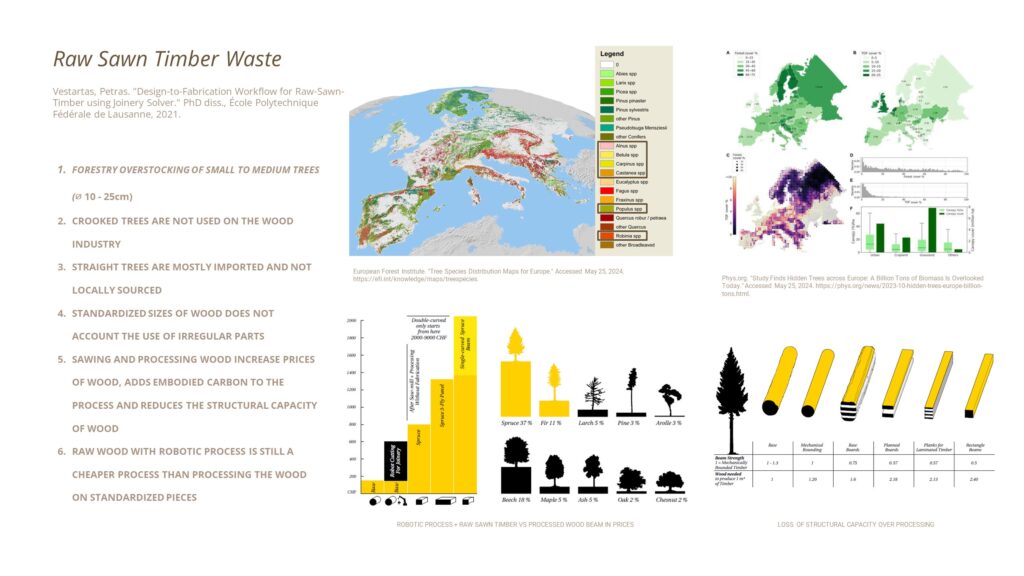
Standardized pieces of wood does not account for the use of irregular parts, because of the sawning process. Processing the wood and transforming it in regular industry sizes not only increases the embodied carbon but also the price of the final product and it reduces the structural capacity of the wood. The use of robotic fabrication and raw wood process is stilla cheaper process than processing wood to standardized pieces.
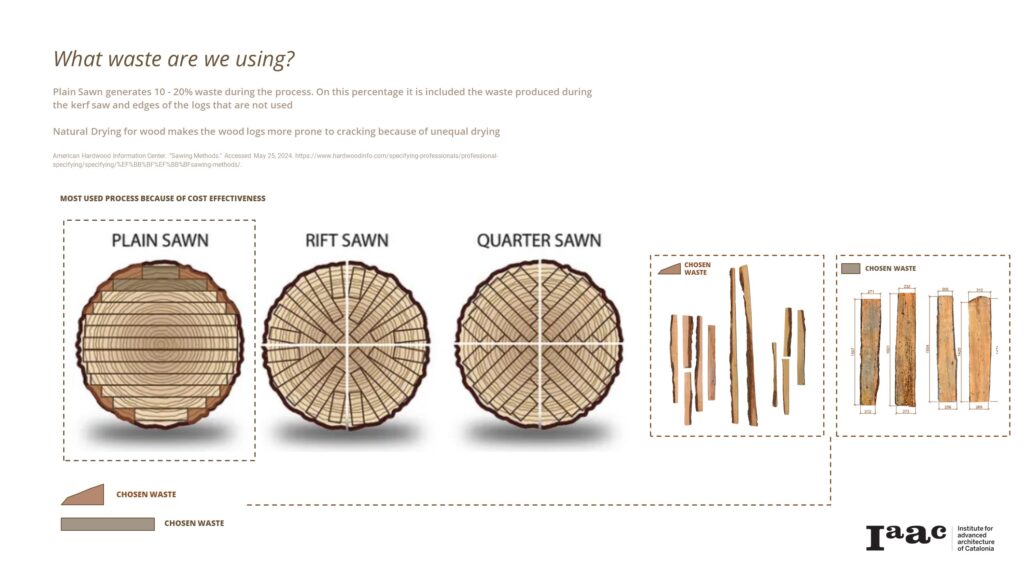
In this project we have decided to work with two types of waste that comes in the plain sawn process, the rounded sticks living edges that are discarded and the slabwoods that have been passed on poorly drying conditions. During the plain sawn process 10-20% of waste is generated during the process, and this waste is divided between wood chips from the kerf dawn and edge logs that are not used.
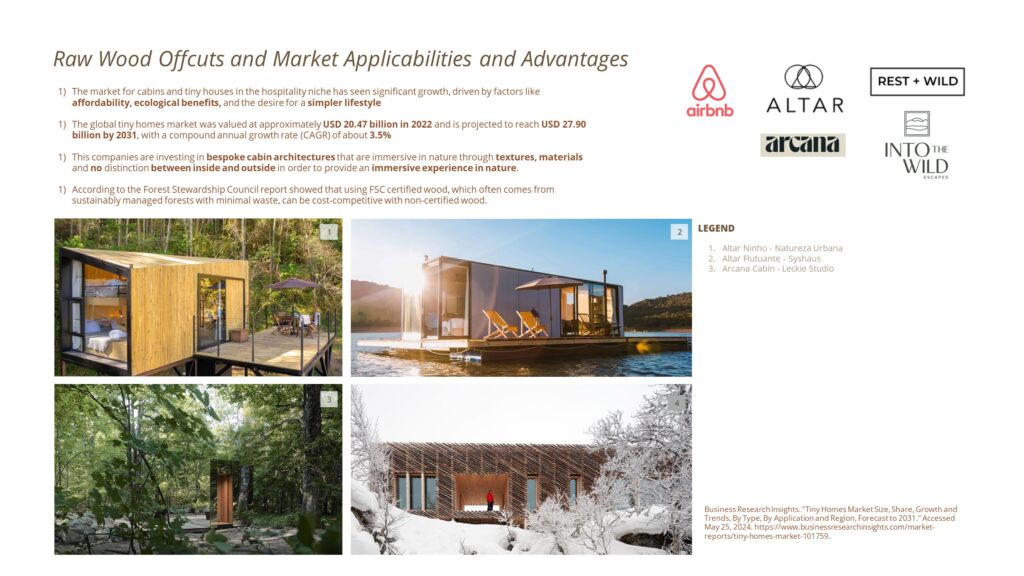
According to the Forest Stewardship Council report showed that using FSC certified wood, which often comes from sustainably managed forests with minimal waste, can be cost-competitive with non-certified wood. This opens and opportunity to work with raw edge logs offcuts and to find possible applicabilities for this material in the construction and architecture industry. he market for cabins and tiny houses in the hospitality niche has seen significant growth, driven by factors like affordability, ecological benefits, and the desire for a simpler lifestyle. The global tiny homes market was valued at approximately USD 20.47 billion in 2022 and is projected to reach USD 27.90 billion by 2031, with a compound annual growth rate (CAGR) of about 3.5%. This companies are investing in bespoke cabin architectures that are immersive in nature through textures, materials and no distinction between inside and outside in order to provide an immersive experience in nature. Therefore opening the opportunity to apply these type of waste as facade coverage for this market niche.
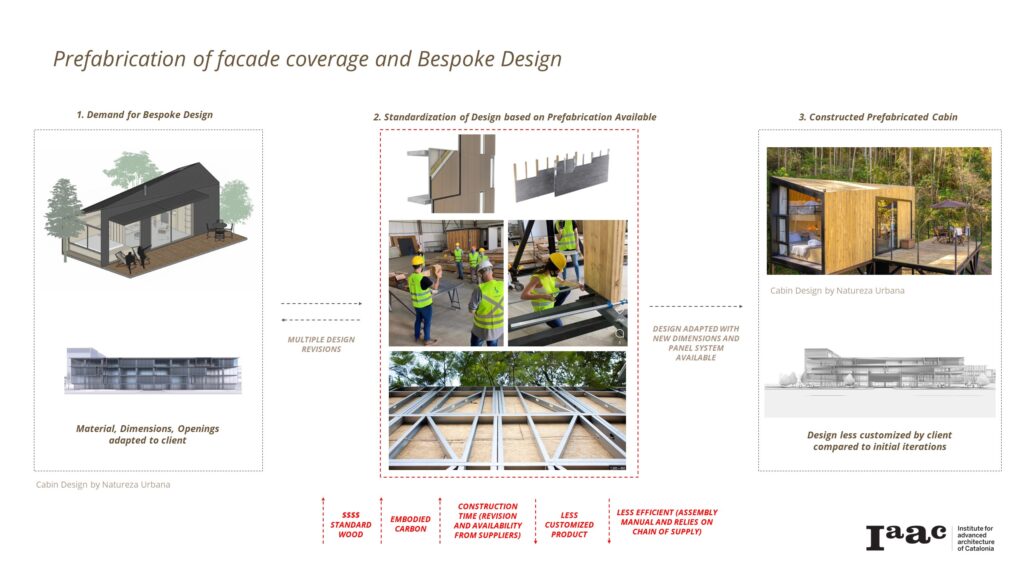
Analyzing the current market for prefabricated wood system there is a discrepancy between the design proposed by architects and final built architecture. This is explained by multiple reasons like: dependency on importation prices of material, standard sizes of construction industry that can’t be mass customized, increases of embodied carbon due process wood and waste on fabrication, construction time and multiple revisions between project and manufacturing process and dependency on manual labour for measuring and assembly. All of this contribute to a more expensive product, less customized by the user and client and with a considerable amount of time of manufacturing.
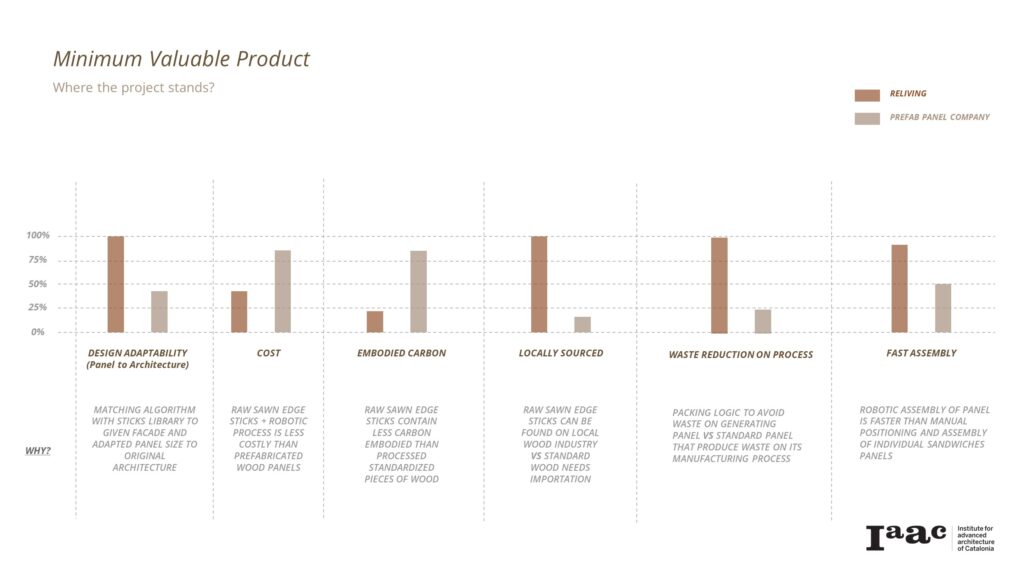
Considering all of this points this research is focusing on how we can deliver a system that includes high design adaptability (system to architecture), low cost production (robotic manufacturing + waste material), less embodied carbon to the process, waste reduction on fabrication and fast assembly.
Aim
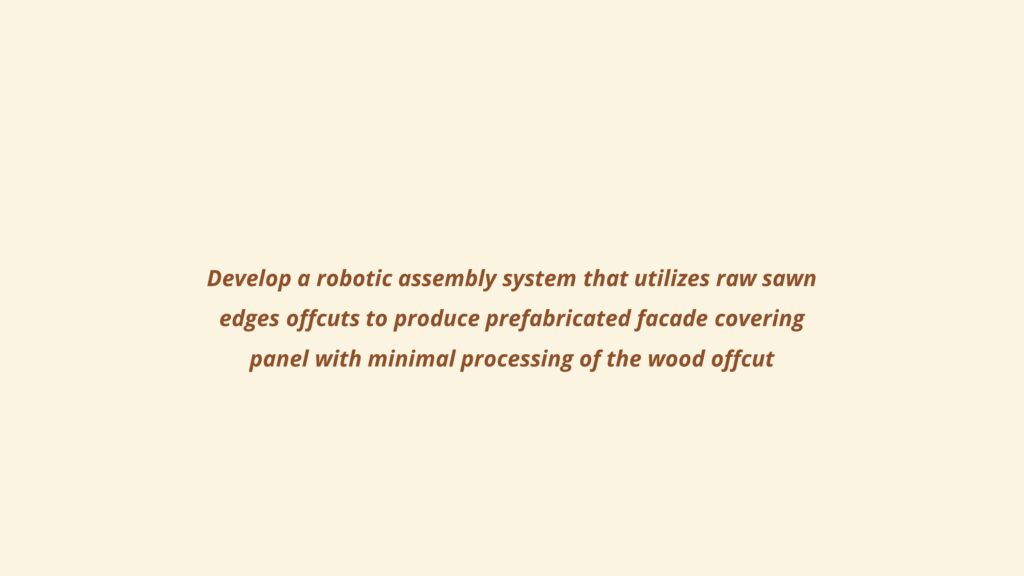
Workflow
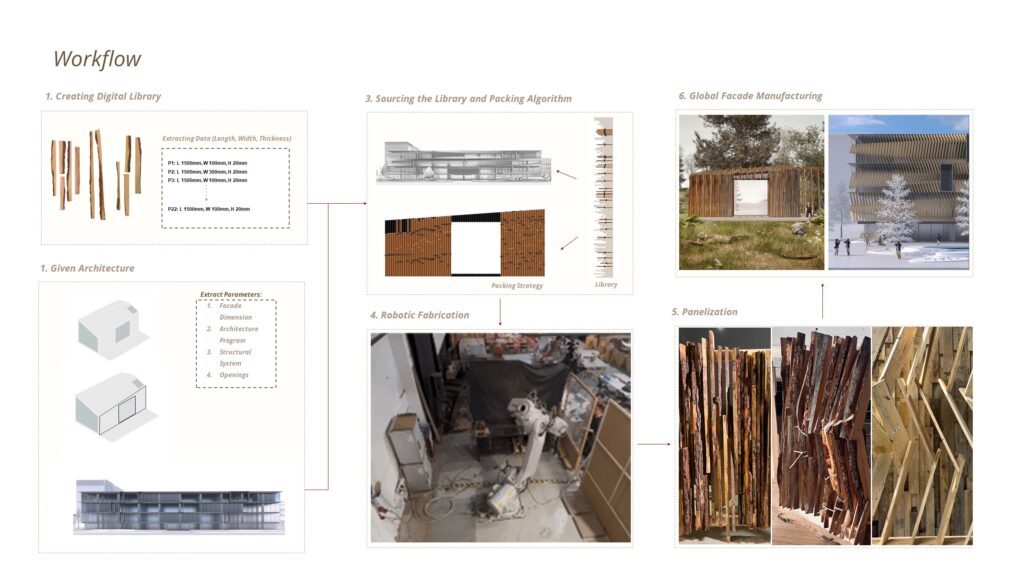
Design
A data extraction phase was developed to create a digital library with the raw edge sticks and the slab woods. Utilizing a photo,the boundary curve and the curve of the top part of the stick were extracted to CAD and then extruded into a brep in order to generate the library.
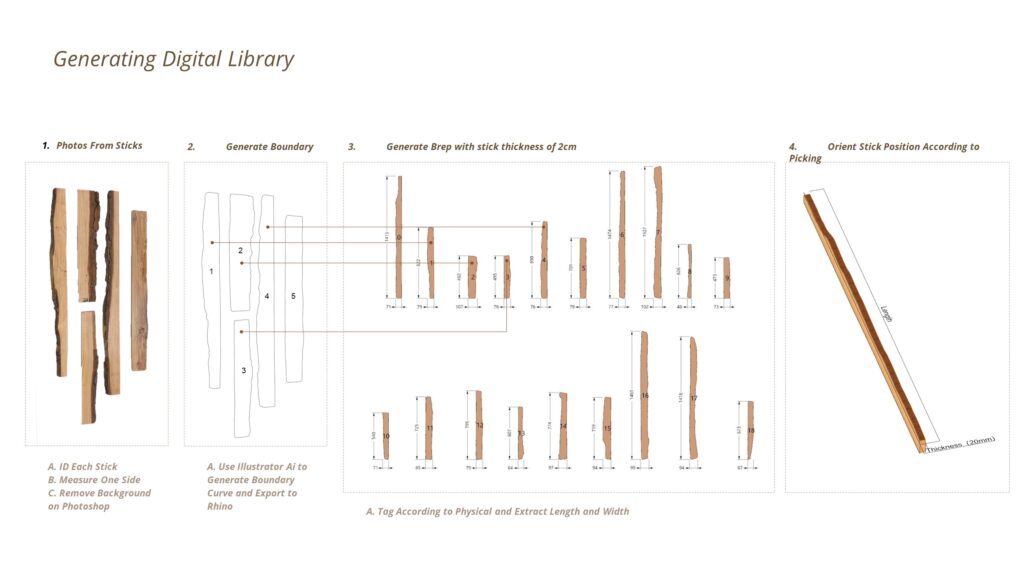
A sorting phase of this library is then generated in order to catalogue and put certain raw sticks in groups by lenght, widtdh, colour and applicabilities so it proper raw edge sticks are assigned to different design.
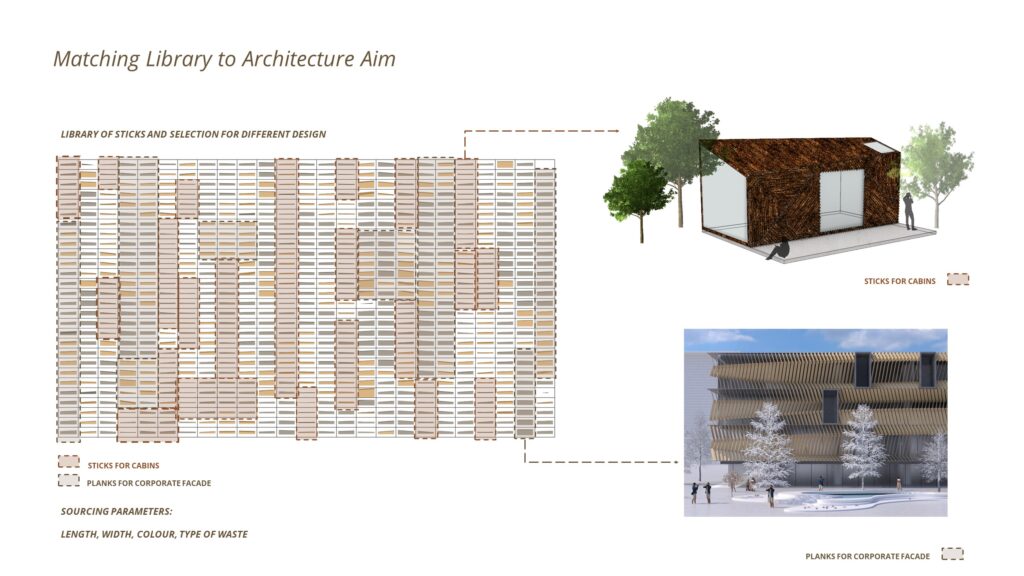
A design set up for a cabin is then designed as a possible given architecture to investigate proper scenarios where the system could be applied for facade coverage and raw edge sticks, generating a catalogue of options that could be guided by programmatic performance, gradient of transparency or customizide by user needs.
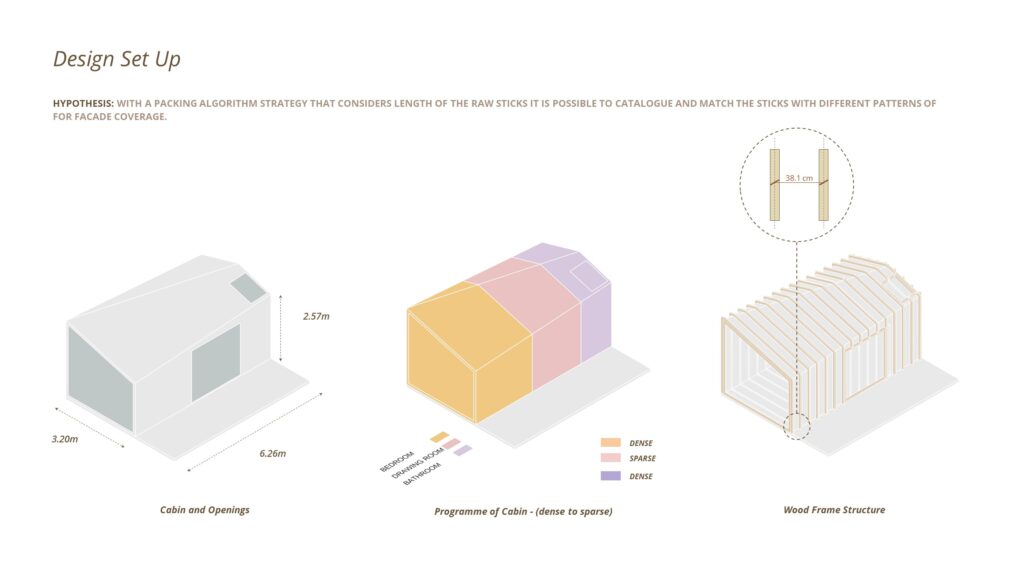
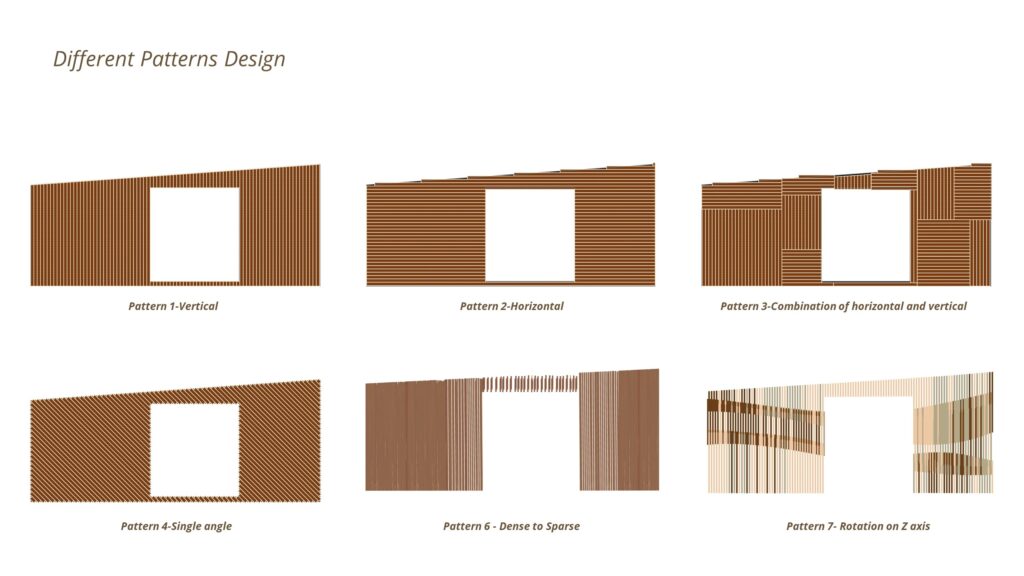
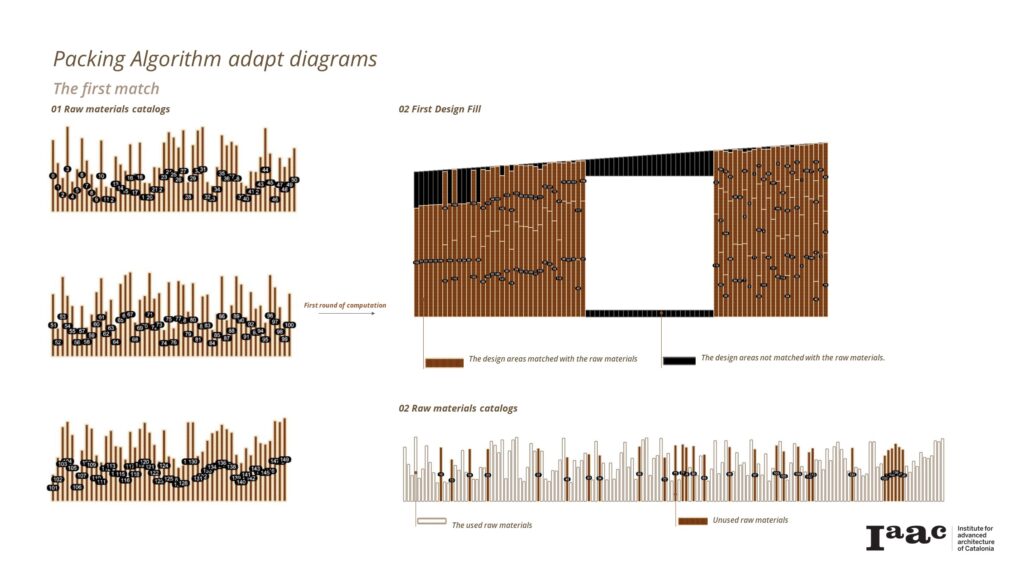
Next, a packing algorithm compares dimensions from the digital library and assigns the correct offcut to the matching design position with minimal cutting. This algorithm can adapt to any configuration and pattern, allowing customization with minimal wood waste processing. Through this process and the built prototype, it was observed that from the original library of seventeen sticks, only four needed cutting, demonstrating that the packing algorithm matched 77% of the library without additional processing.
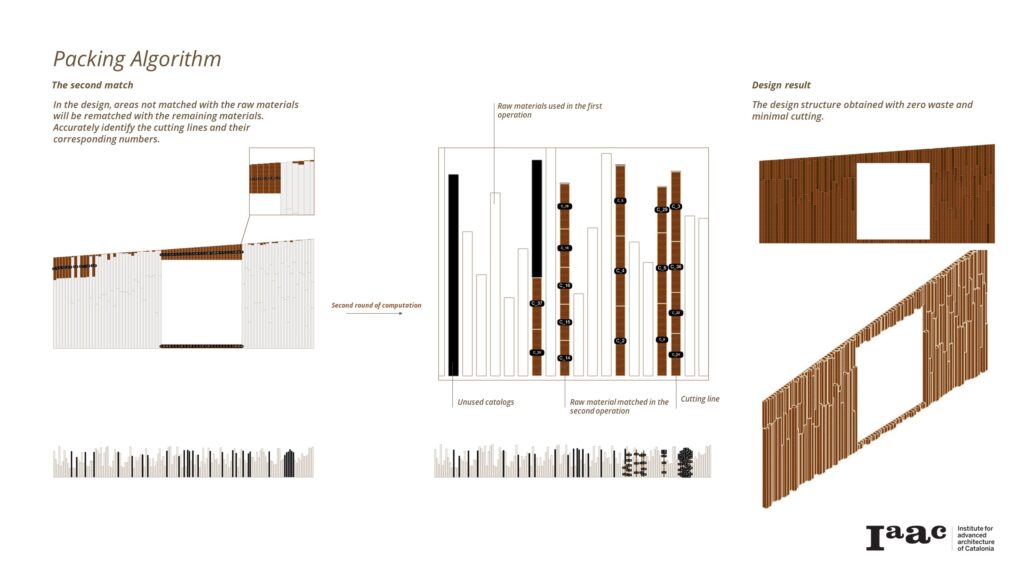
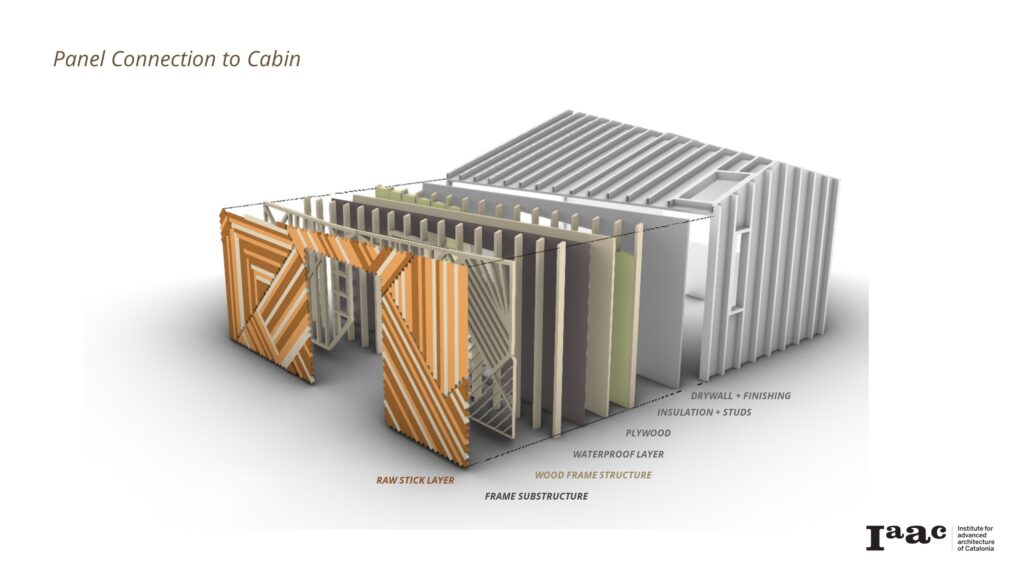
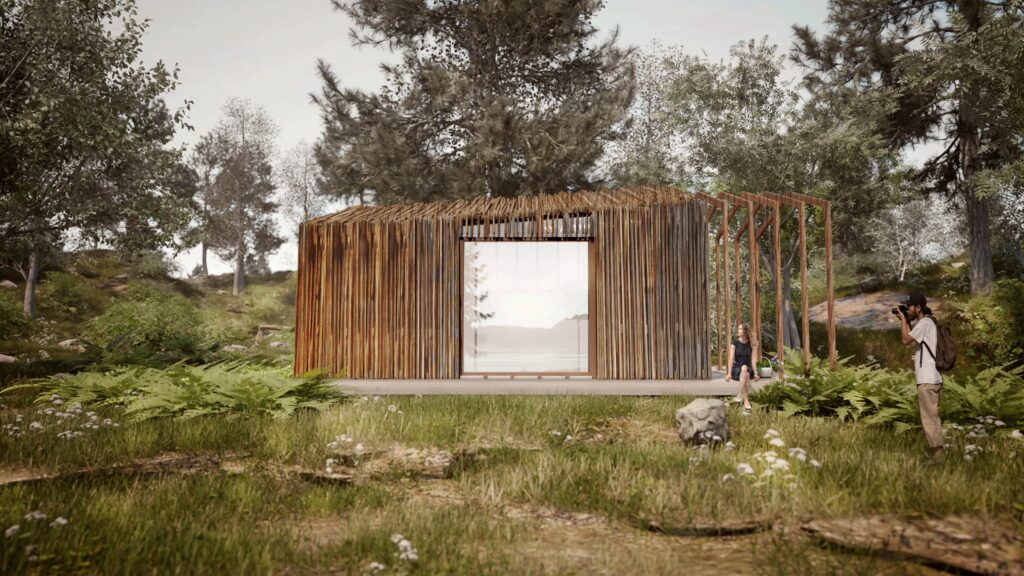
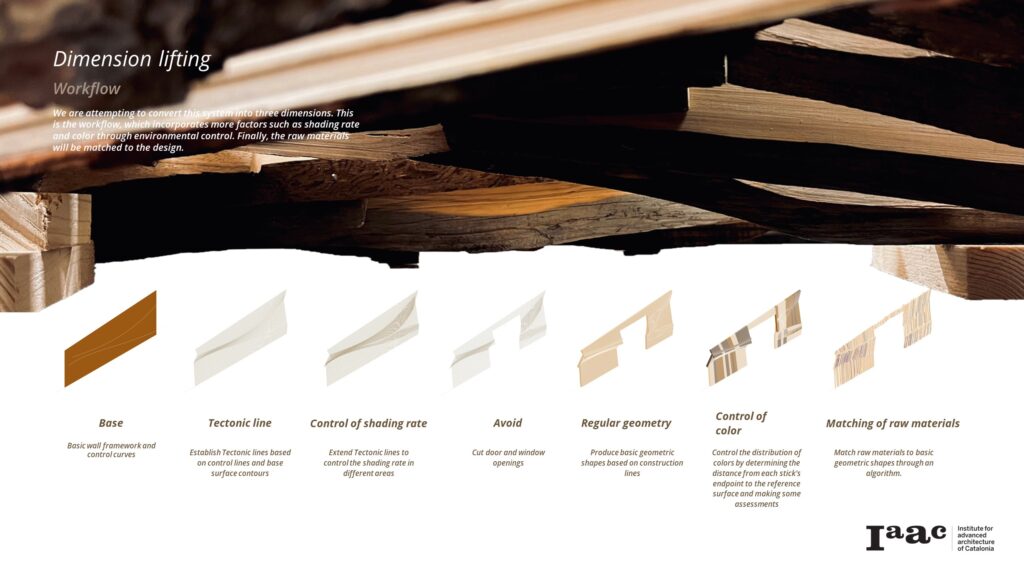
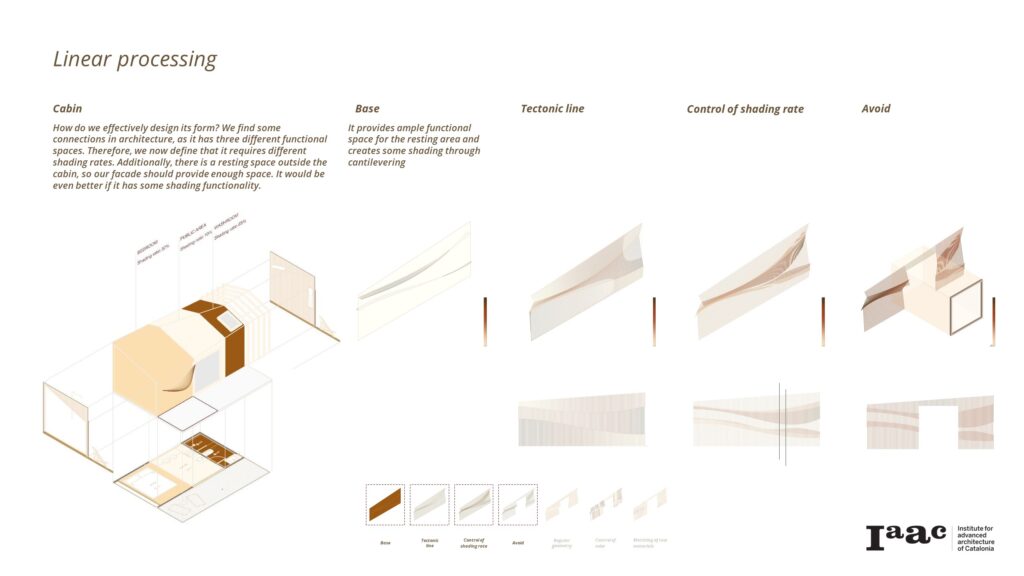
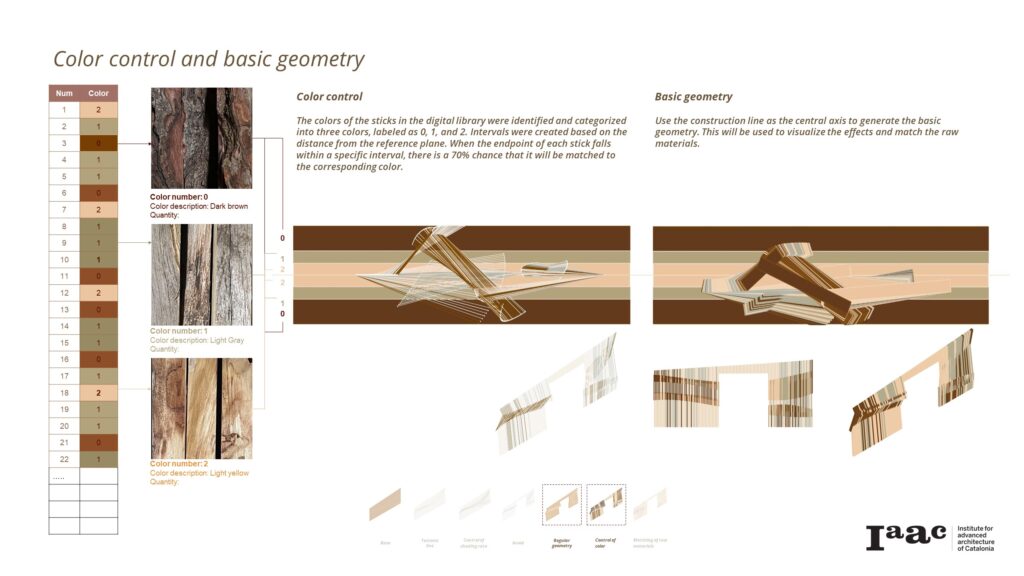
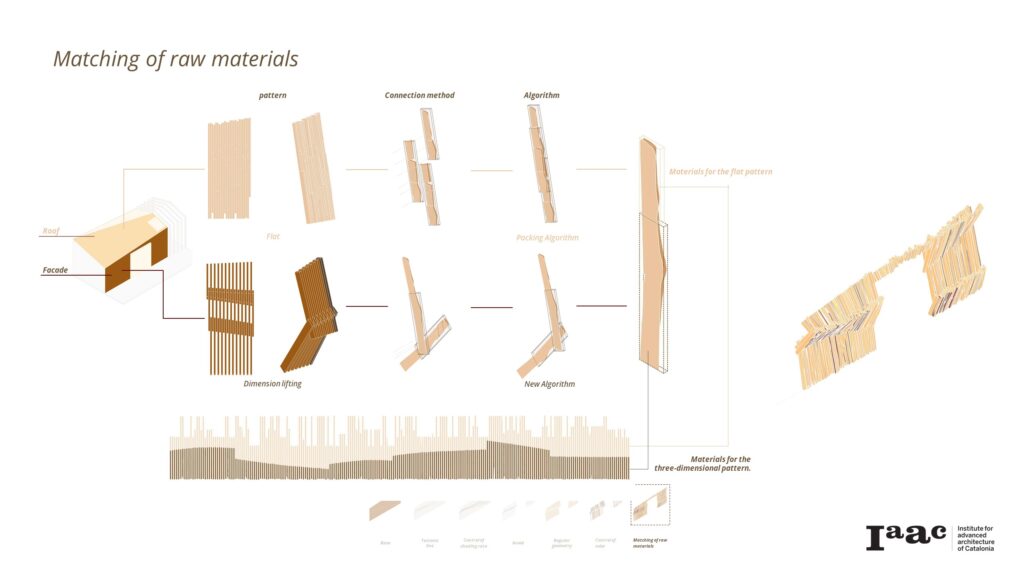
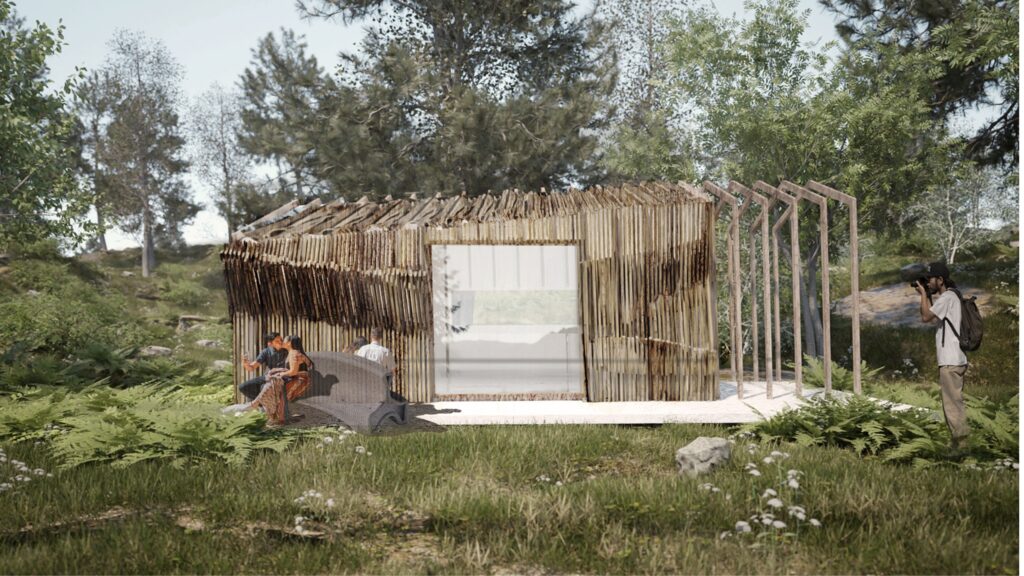
Another design exploration using waste slabwoods was developed exploring the control of transparency and selfshade for buildings aiming to explore cost effectivess and easy assembly and disasembly.
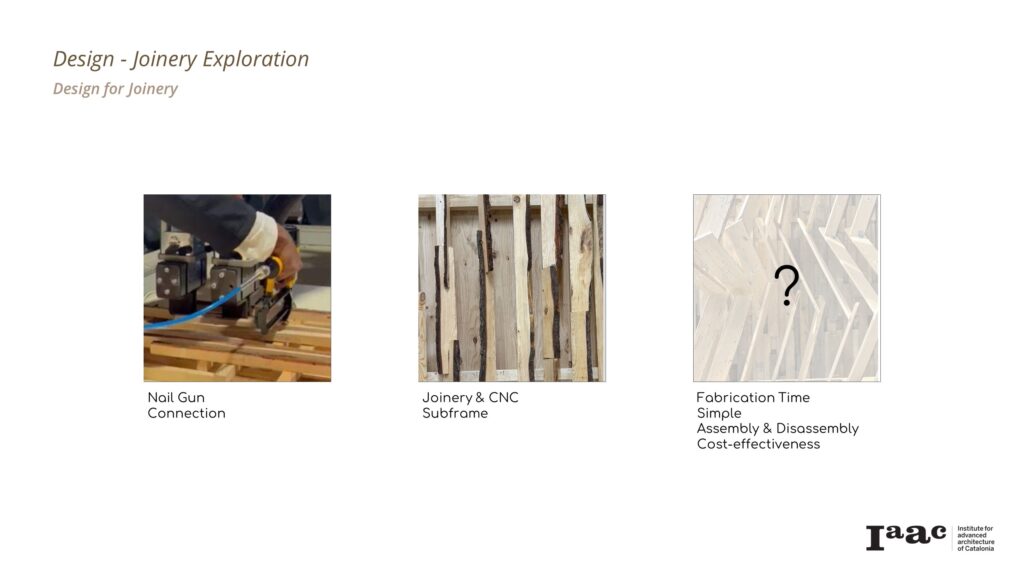
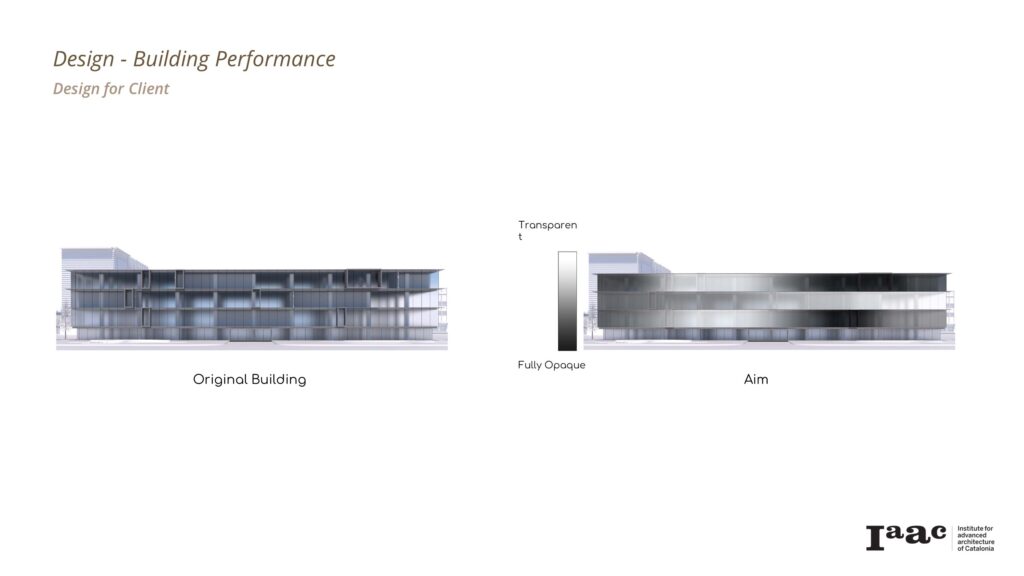
A level of transparency and opaqueness is then extracted from the desired building according to programmatic perfomance and shading analysis.
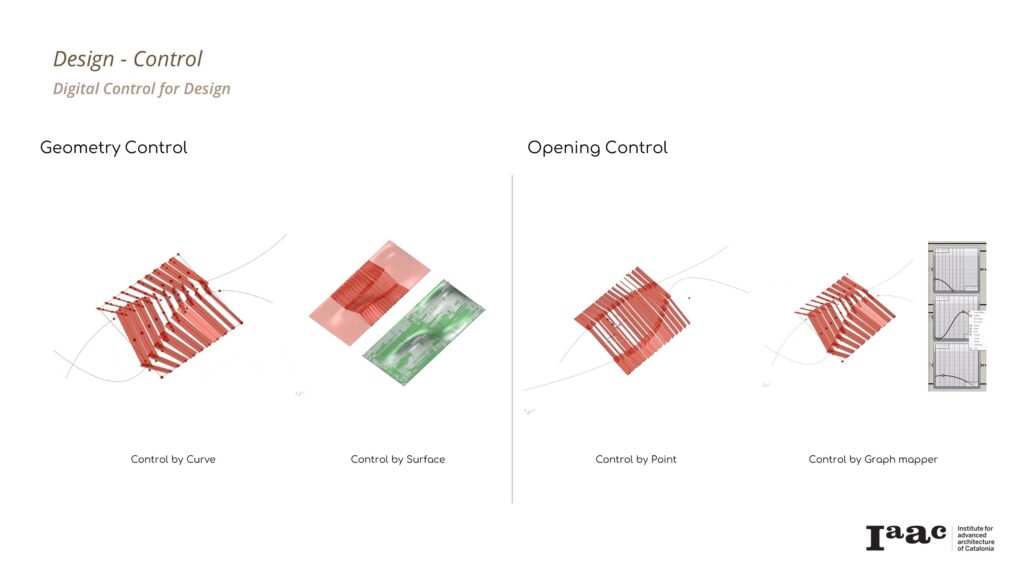
To generate the component base and the regional geometry two curves are controlled to determine the amount of rotation of the 3 raw slab woods and it also controls the excess limit of rotation to make the joinery and fabrication feasible.
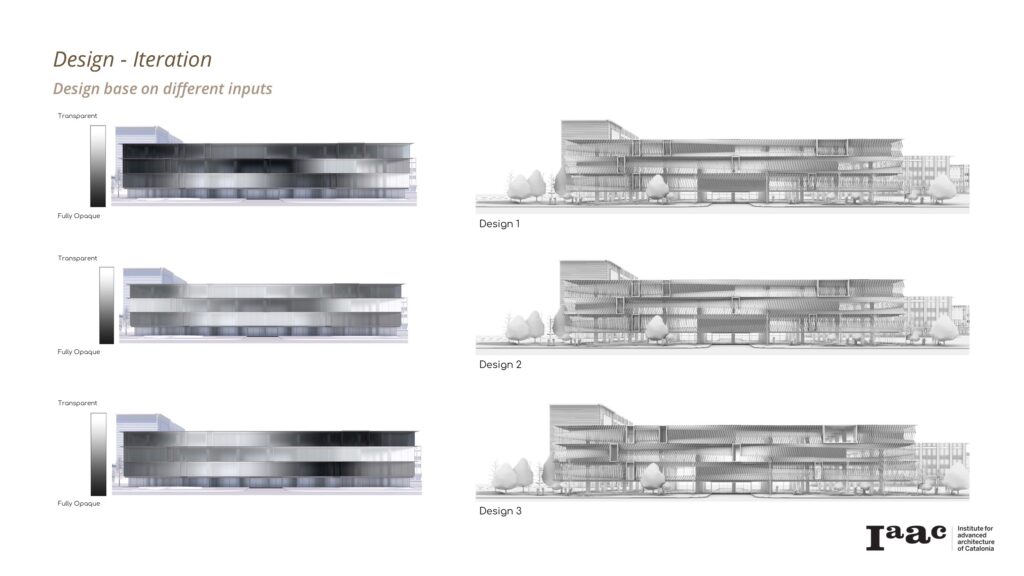
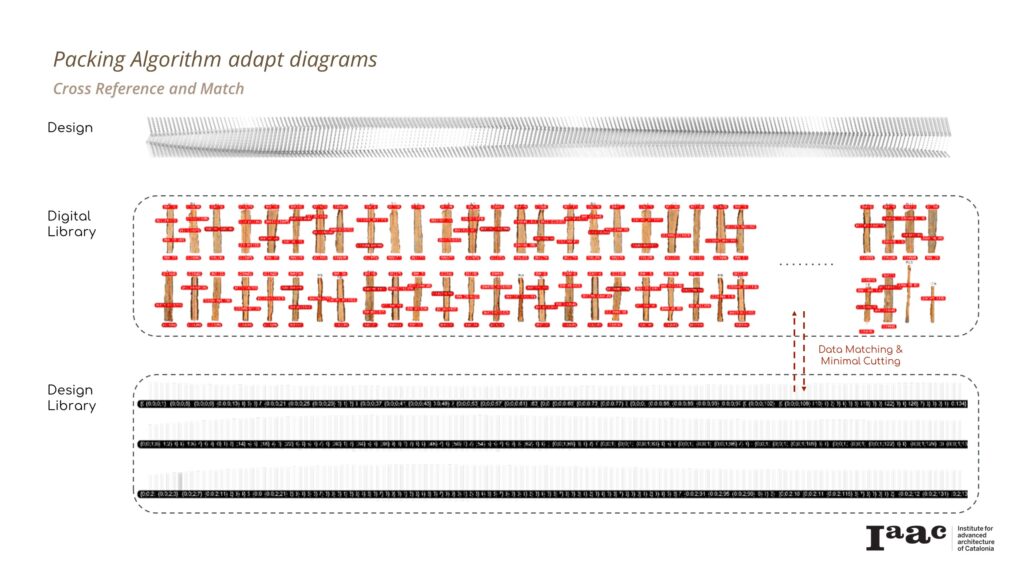
The packing algorithm was also utilized to match the raw slabwood with minimal cutting and assign to its matched location, this not only assigns the best match for the three geometries in the component but also inform the position for cutting in the robotic cell.
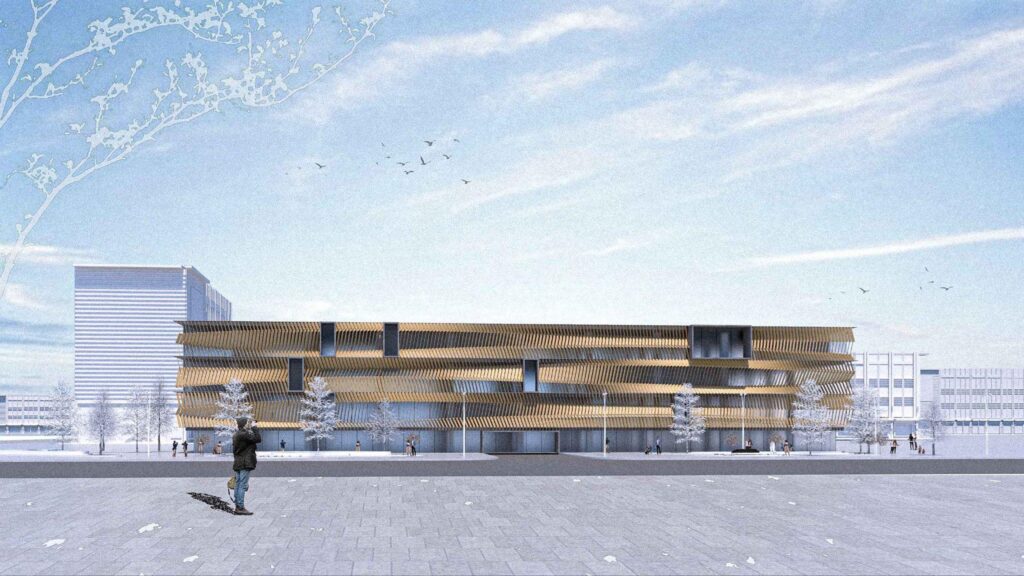
Fabrication
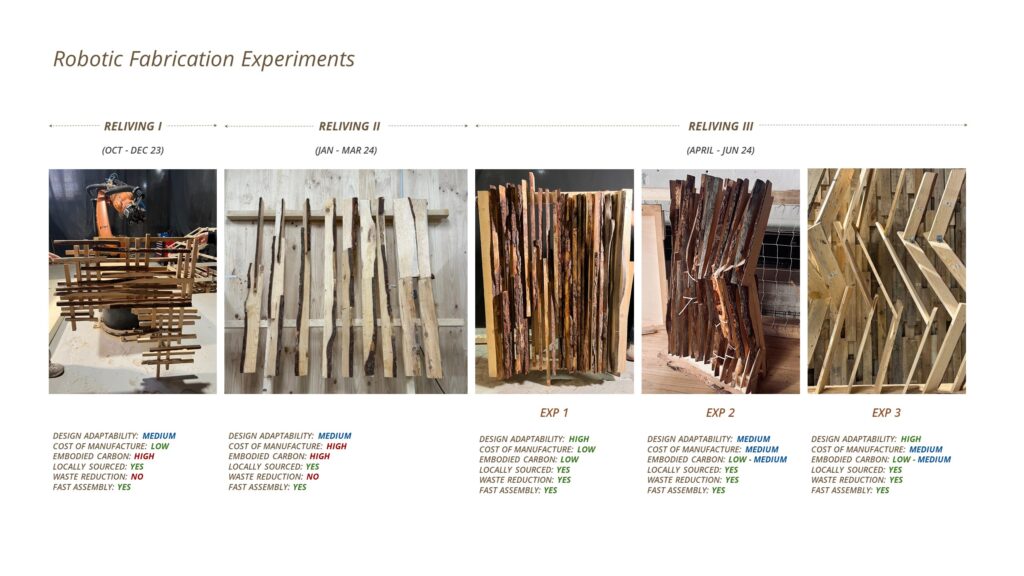
Throughout the nine months of research we have learned that some of the iterations needed to be more thought off in terms of the parameters we set in the research like design adaptability, cost of manufacturing, waste reduction and embodied carbon. With the experiences learned through the first two terms we have developed the packing algorithm and the sorting logic to address the waste reduction and the embodied carbon for cost of manufacturing some strategies were developed in robotic fabrication to measure the amount of cost of manufacturing. First prototype with only pick and placing, second prototype with pre CNC pieces and pick and place and last prototype with robotic cutting, drilling and assembly. A scenario with augmented reality was also explored to understand the cost of manufacturing and fast assembly but further experiments need to further tested to measure the time effiency of augmented reality/human powered versus robotic assembly. A full automation scenario was also developed to understand how this production would be from sourcing, sorting, data extraction and robotic fabrication could be explored further on.
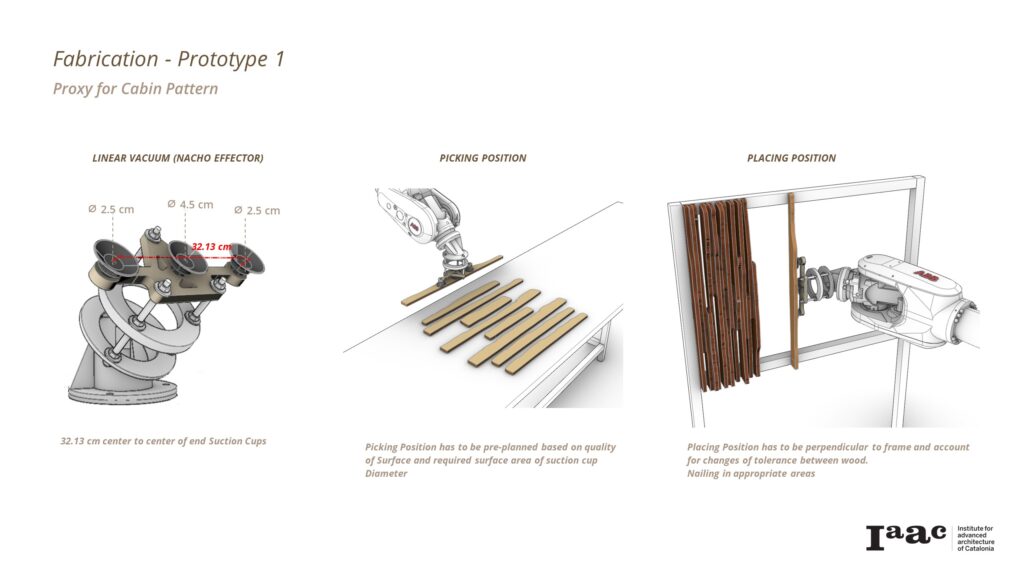
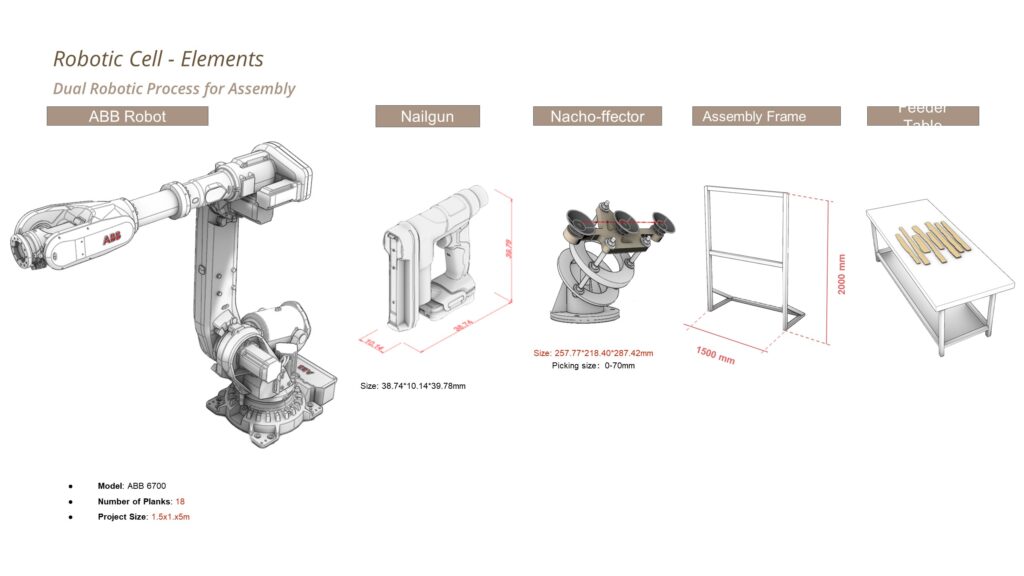
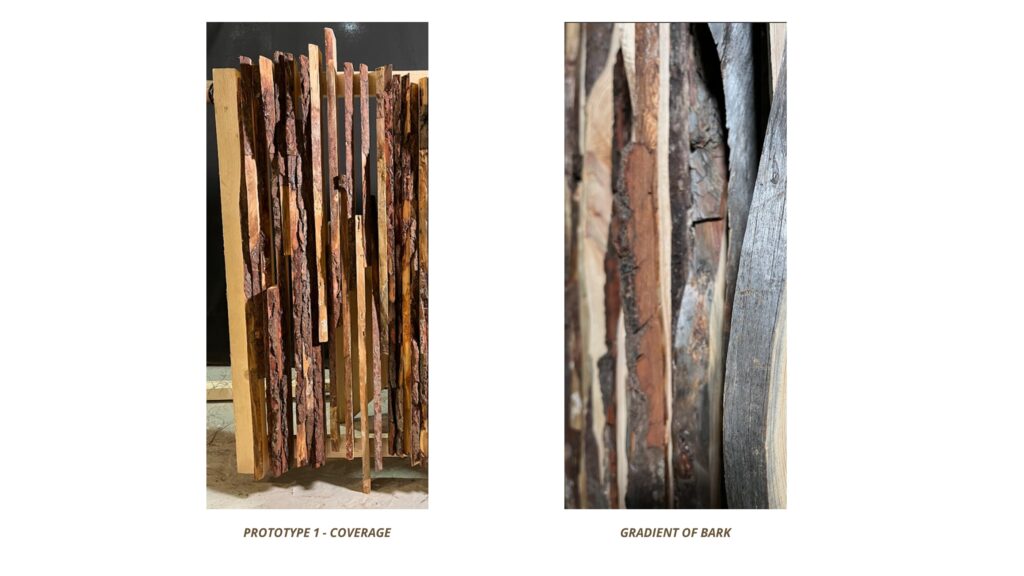
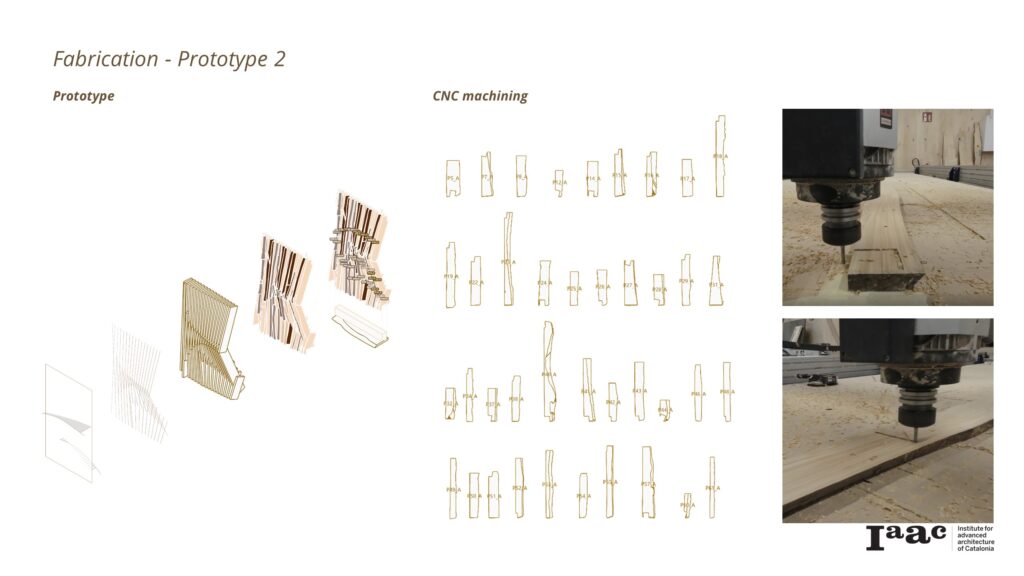
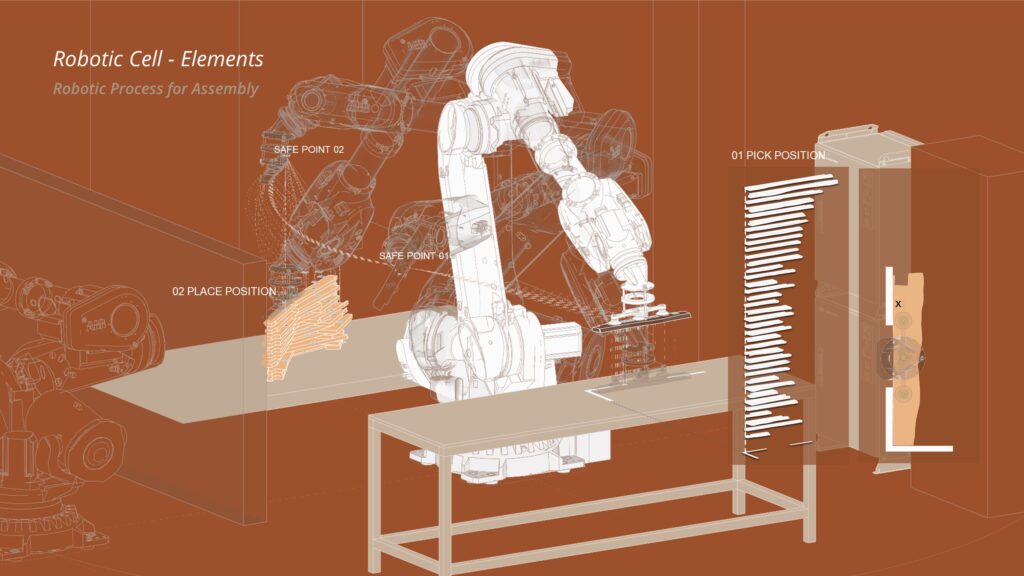
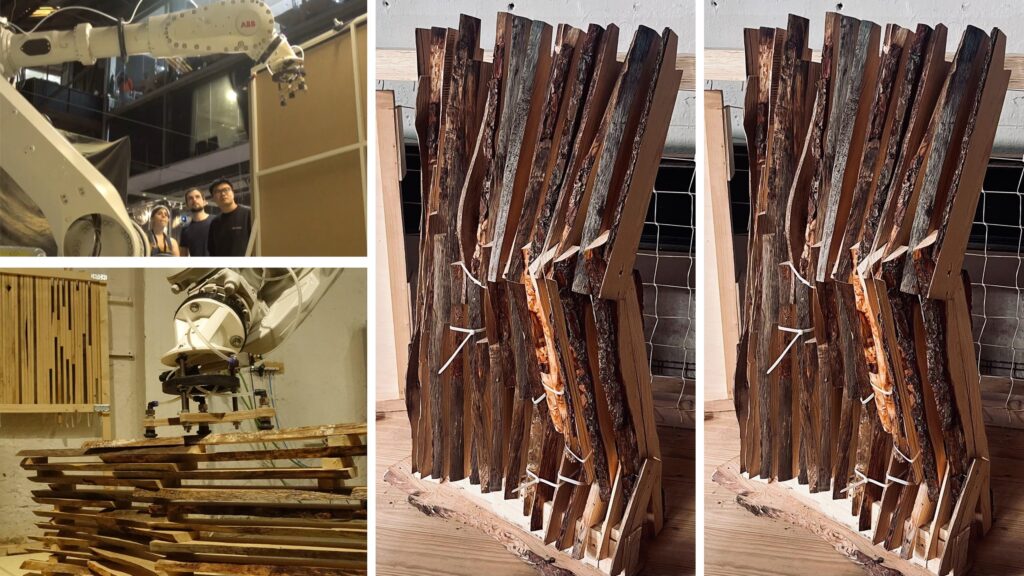
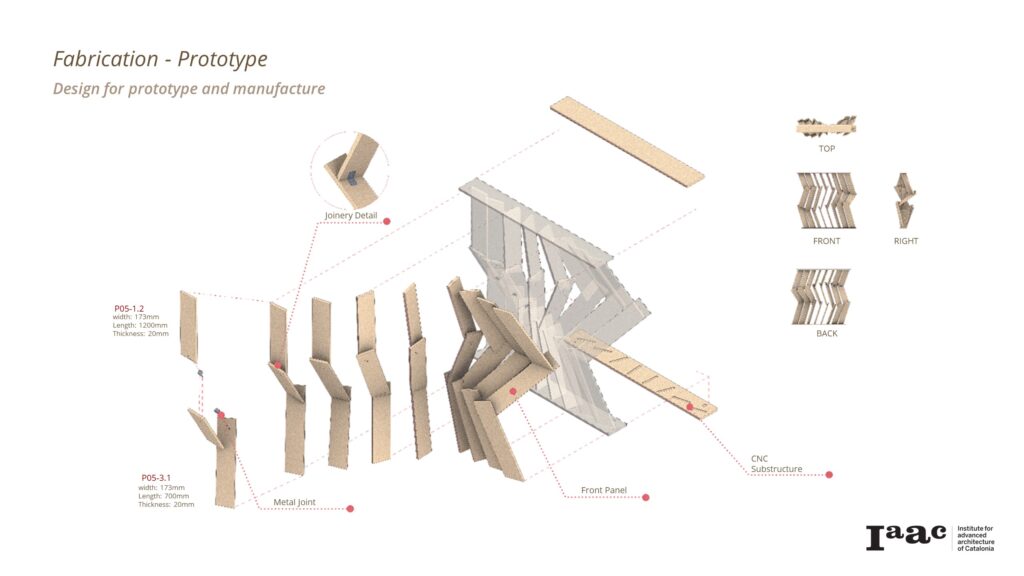
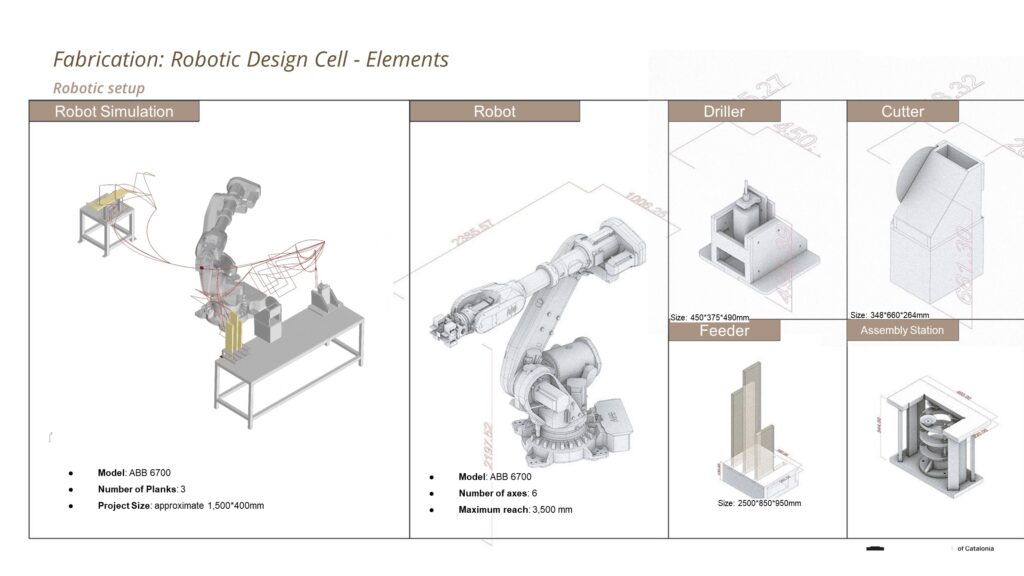
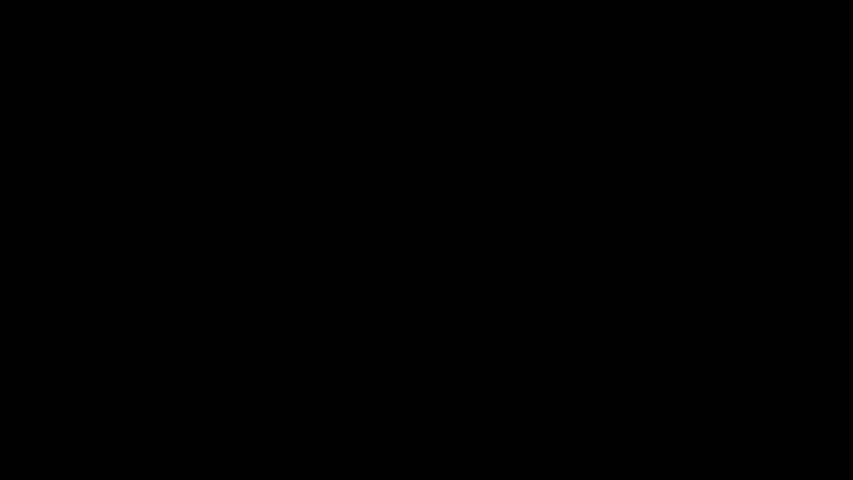
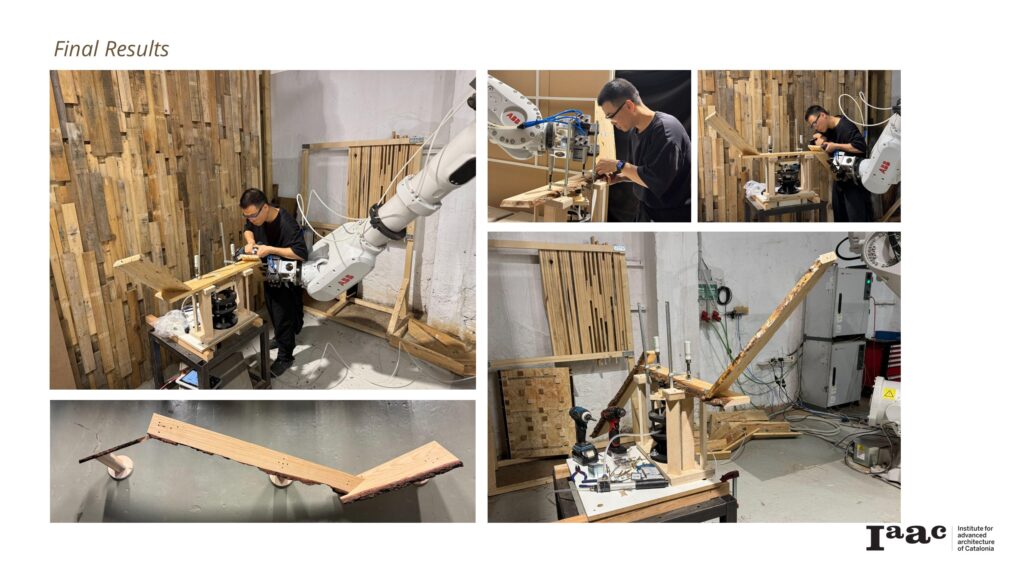
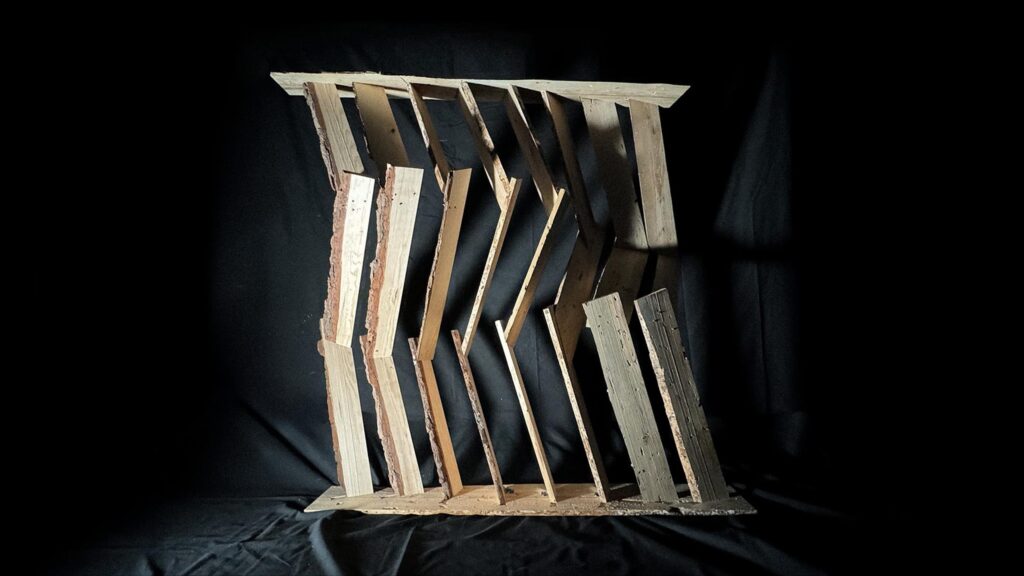
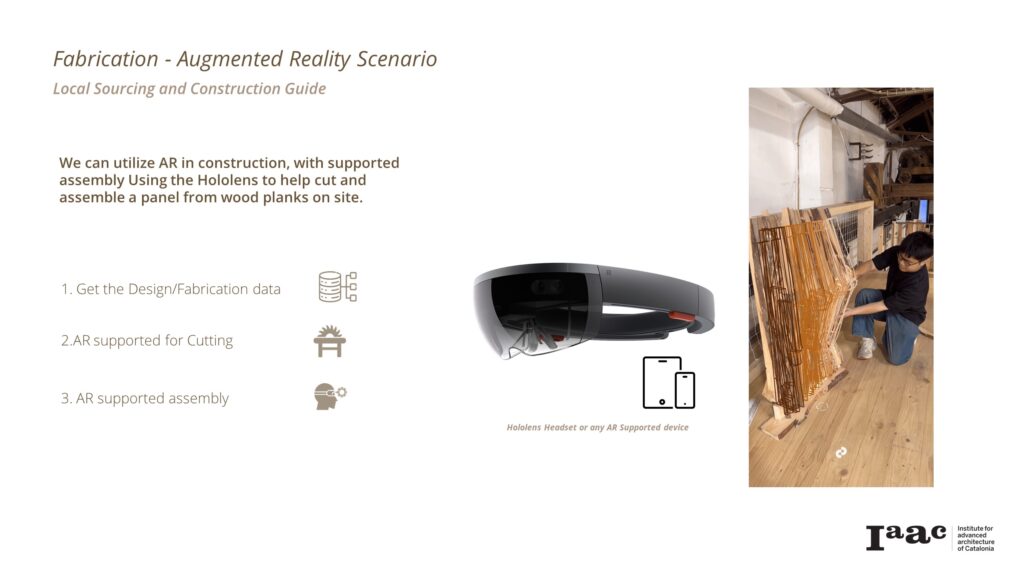
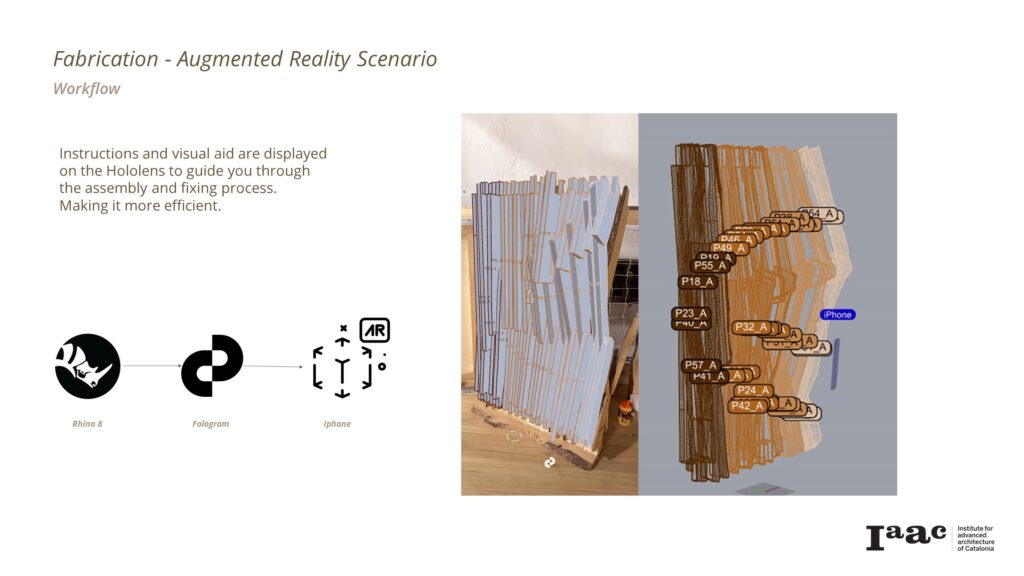
Conclusions
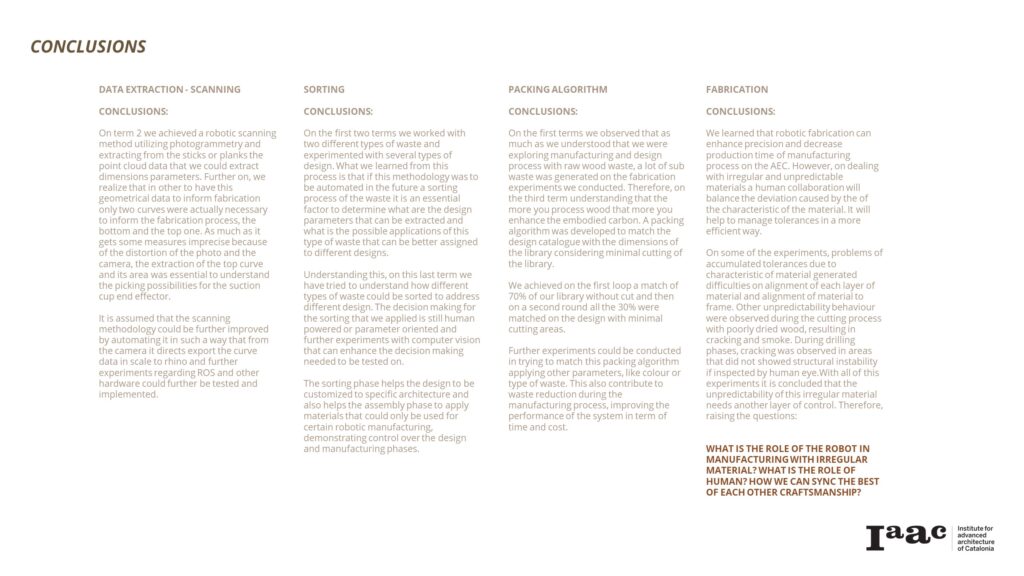