Drawing inspiration from the Central American term “colocho” meaning curl or loop, we developed a robotic printed clay column, while experimenting with non-uniform extrusions. In this seminar we explored the geometric possibilities that can be created with the incorporation of non-uniform rotations and movements in the robot while printing with clay. At the same time, we begin developing potential architectural applications of the geometries and system from the components we designed.
State of the Art

Physical Exploration
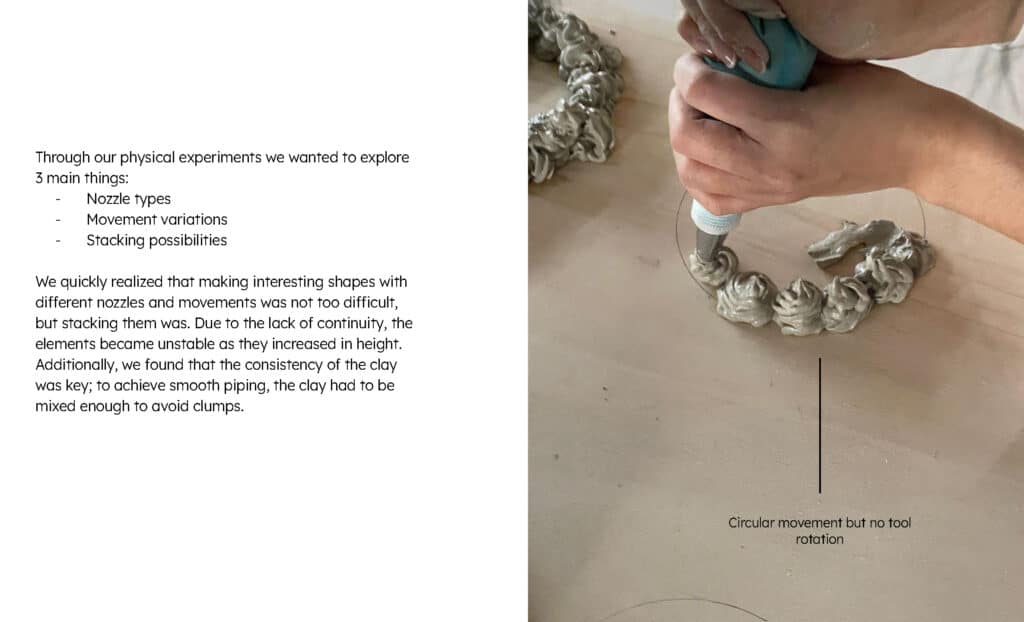
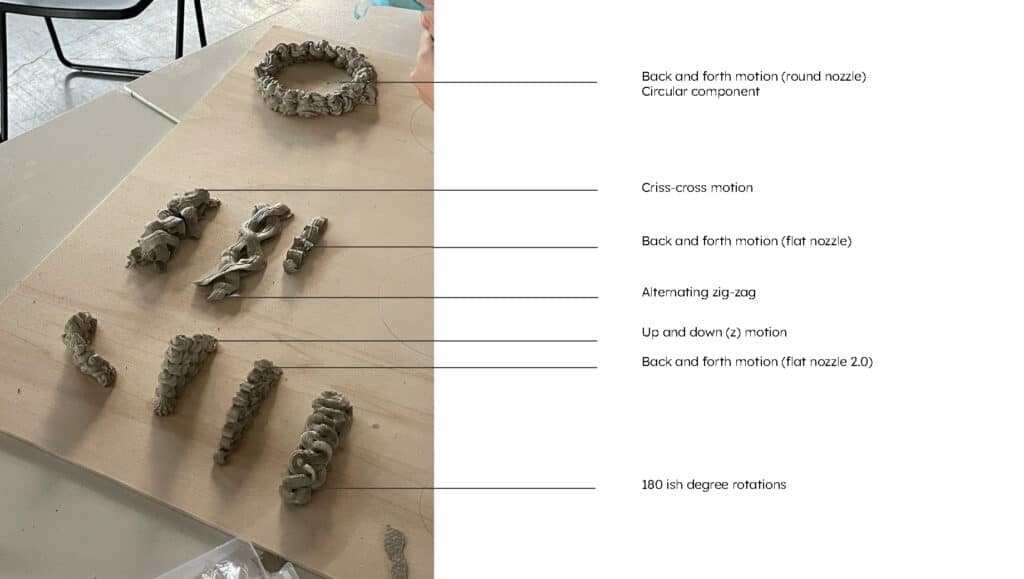
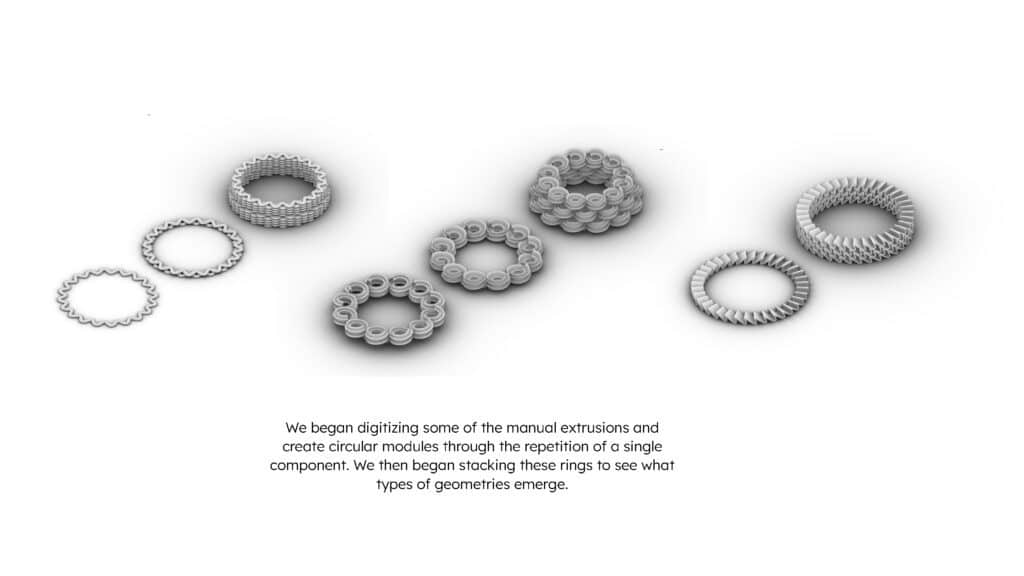
Fabrication Methodology
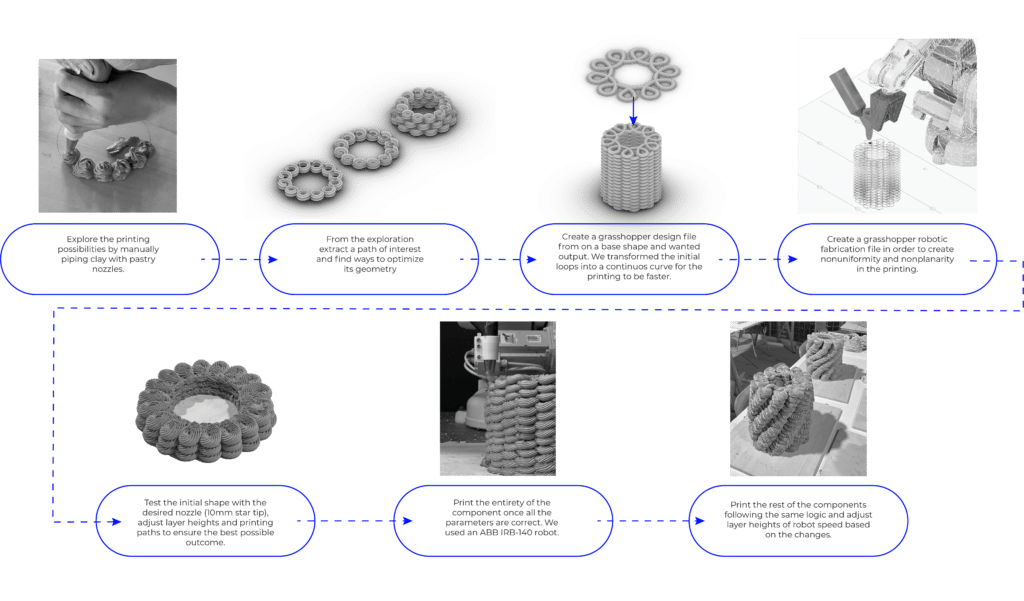
Testing
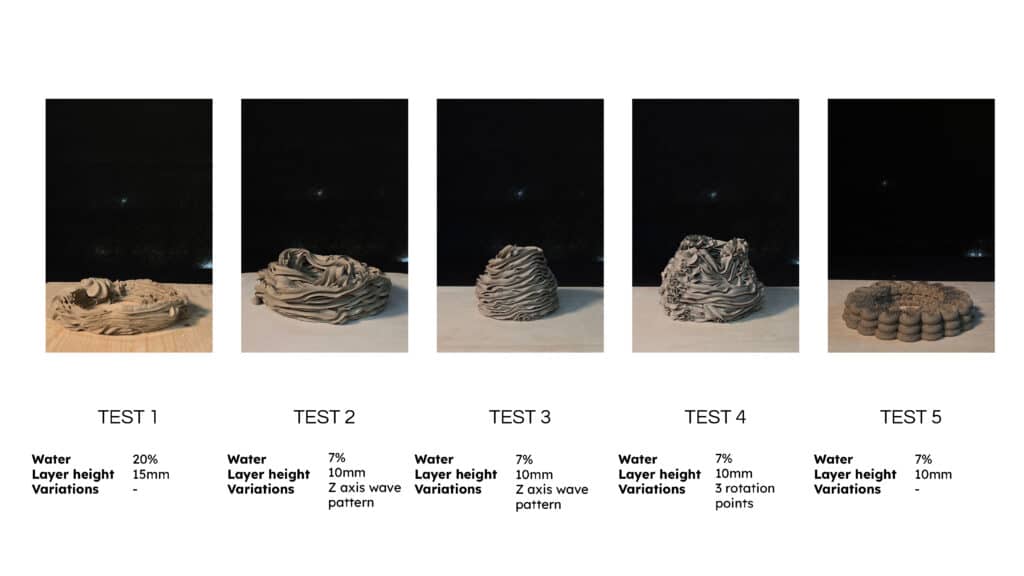
During our testing period, we played with different clay recipes, by altering the water content and noticed a distinct difference between the water required when manually extruding the clay and the water content needed for the clay in the robot. Given the significant change in extrusion pressure and strength, adding less water to the robotic printing cartridges added stability to the clay helping reduce the risk of collapsing. Another important parameter we tested was the layer height in the components. Ultimately it depended a lot on the printing path; a planar print with no rotations deposited less clay than those with non-planar paths and rotations, which allowed for smaller layer heights for a cleaner-looking print. Our non-uniform prints that had multiple rotations in the printing path deposited more clay in the process, which we found showed better results when increasing the layer height enough to account for the extra material collected every layer. Given that we were aiming for a continuous print, it is important to note that the rotations were added in our printing code to account for the robot’s axis limitations and prevent collisions.
Design Modules Catalogue
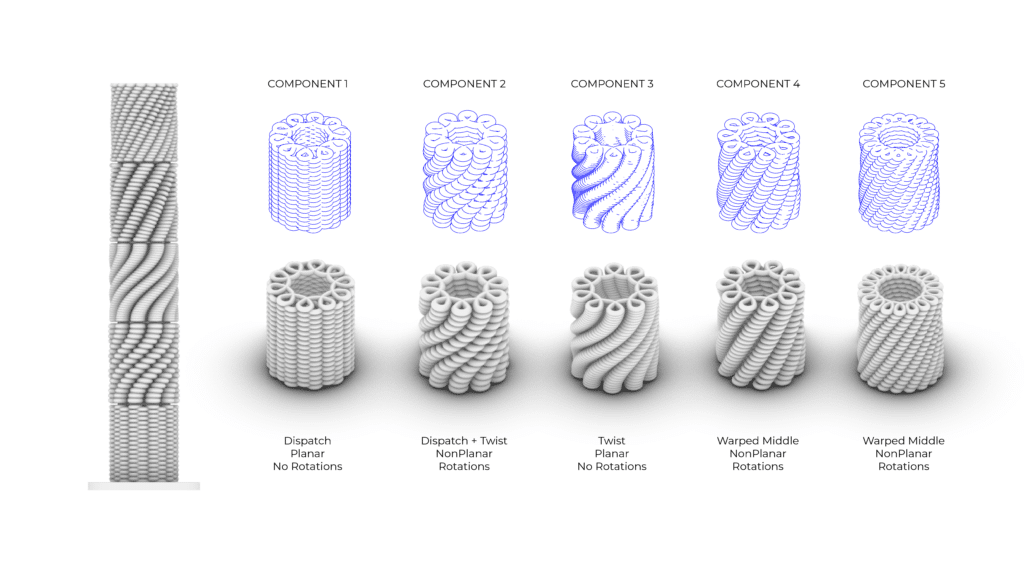
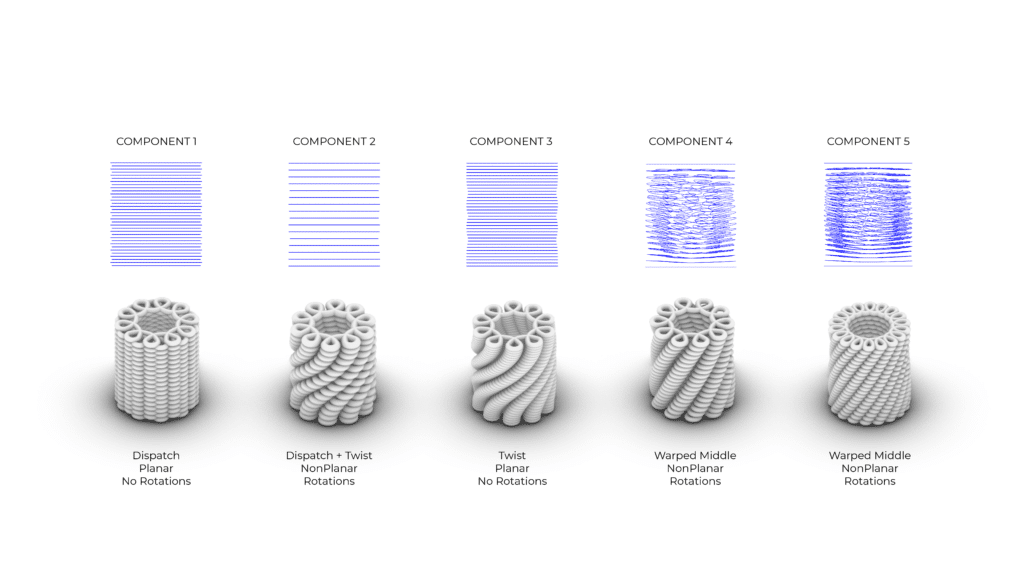
Our final modules were all developed from the same base curve, with variations generated in the Grasshopper script. As part of our robotic fabrication exploration, we developed both planar and non-planar components to compare the results and be able to see what non-uniformity has to offer.
Performance-based System
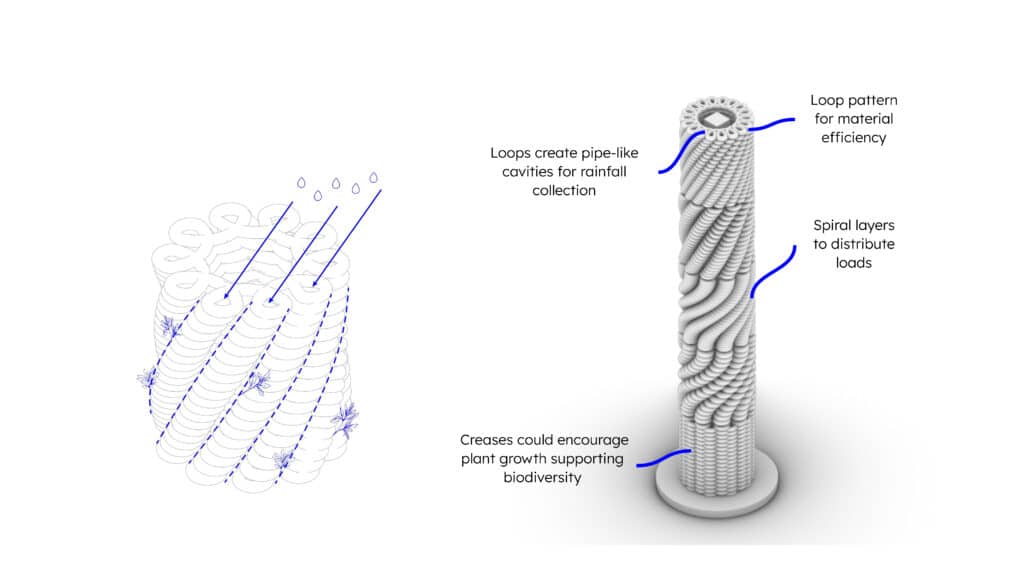
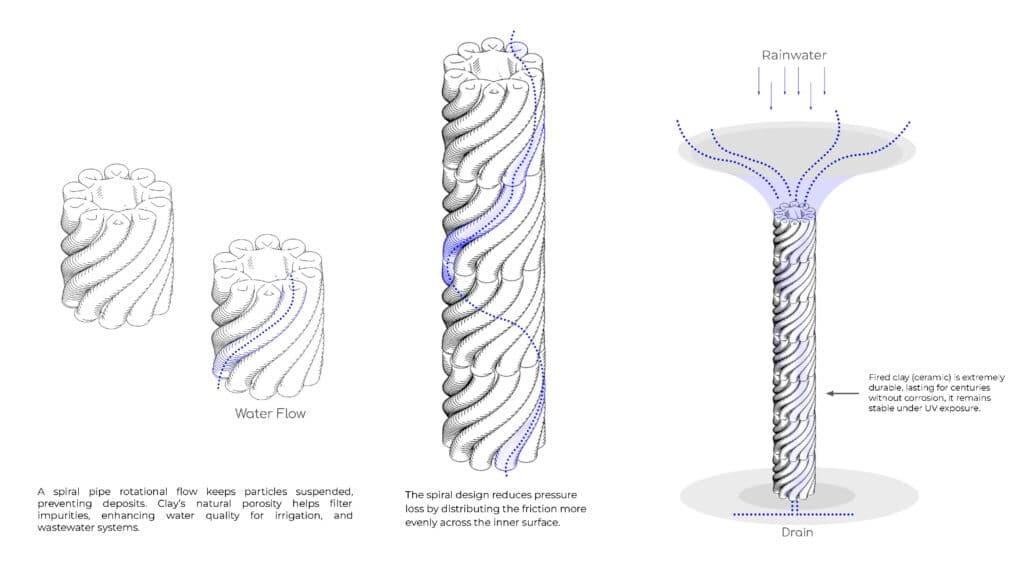
Design Analysis
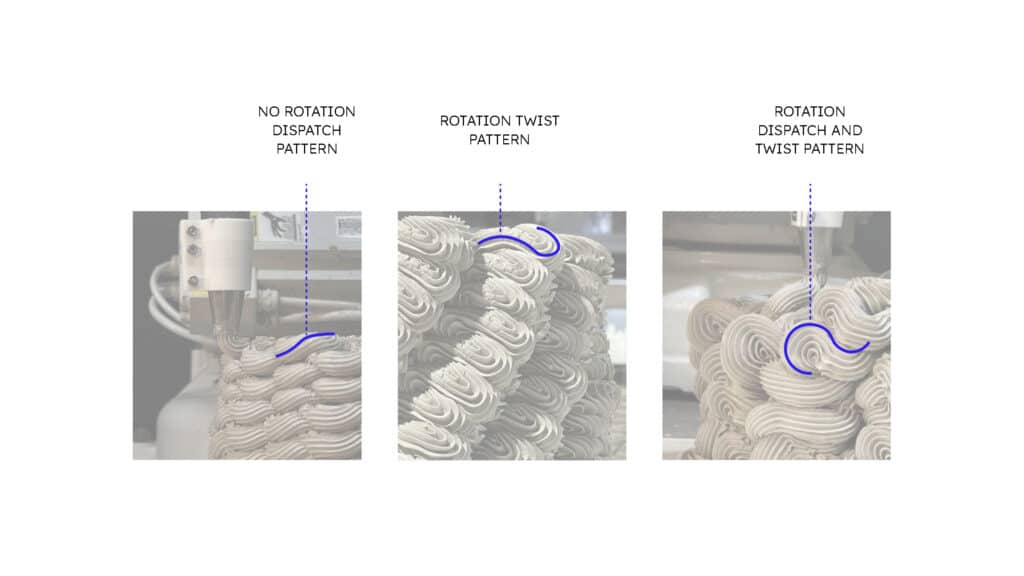
In the process of printing our final prototypes, we discovered a variety of textures that were created merely from the use of a star-shaped nozzle combined with rotations in the robotic printing path.
Prototypes
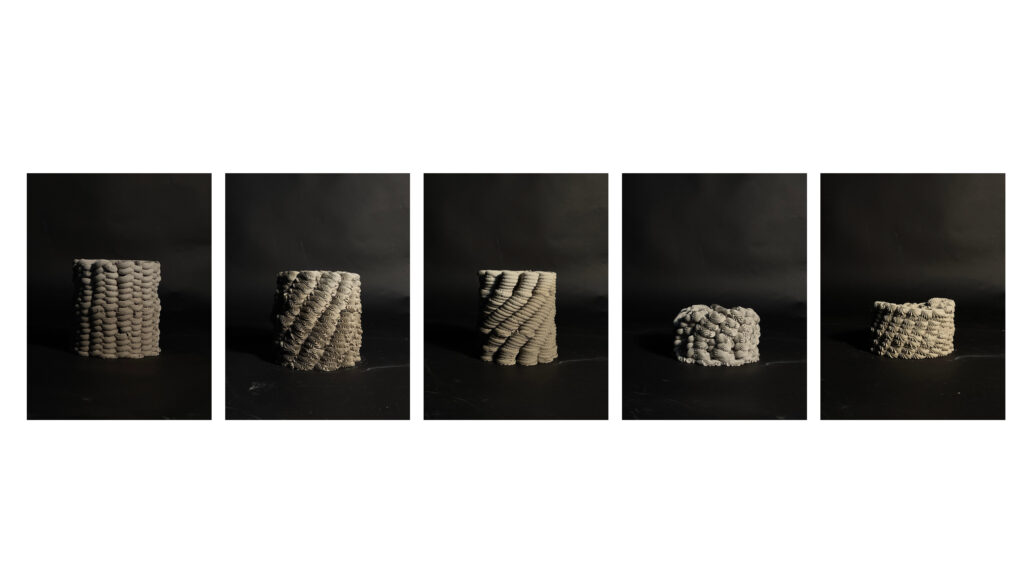
Production Calculations
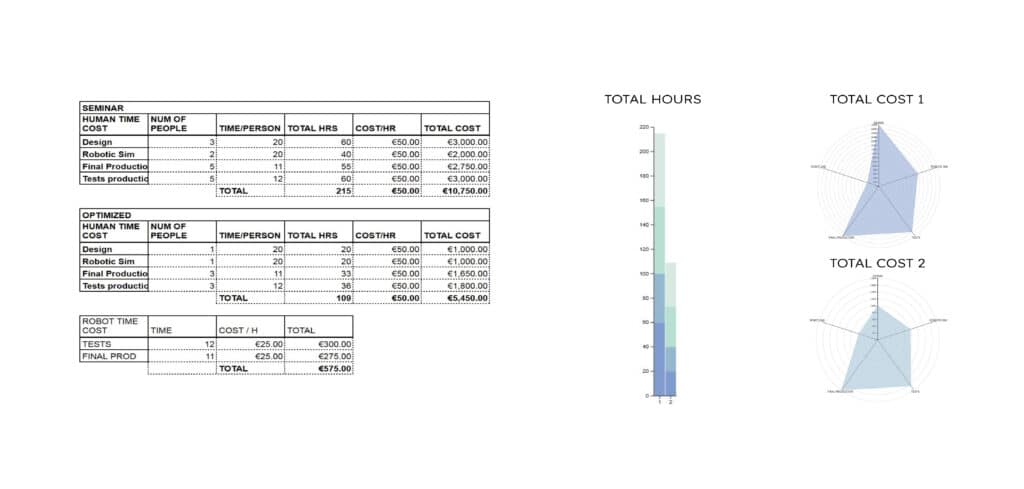
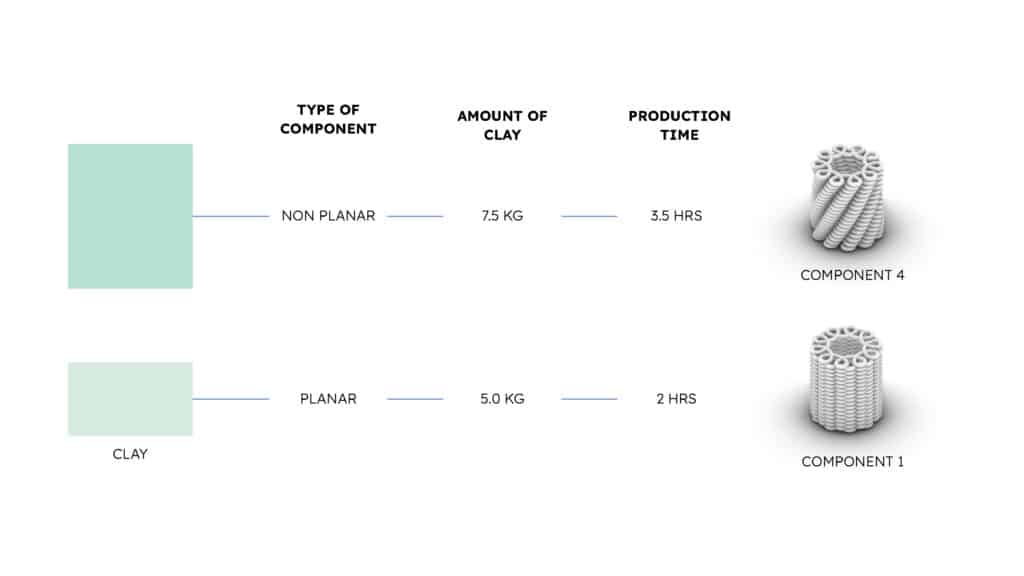
In addition to the design fabrication process, we also began understanding the costs and material required to fabricate our pieces in a manufacturing context.
Future Material Applications
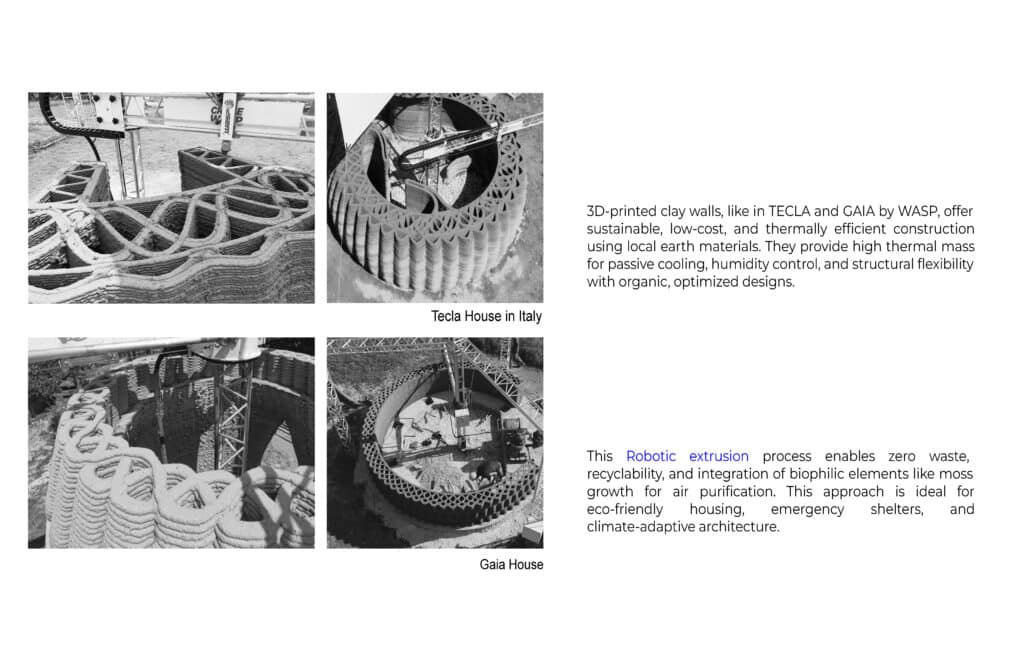
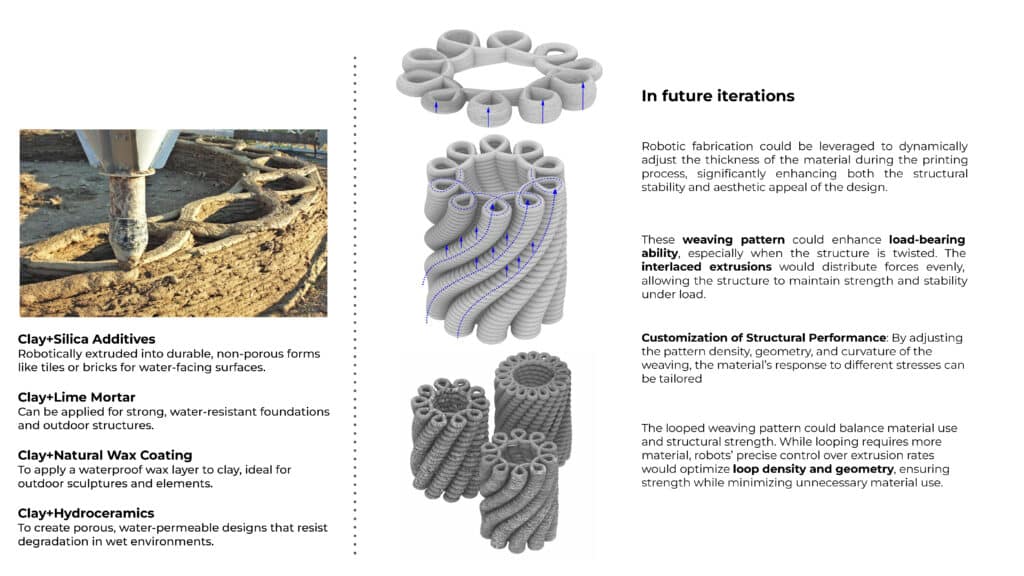
Architectural Application
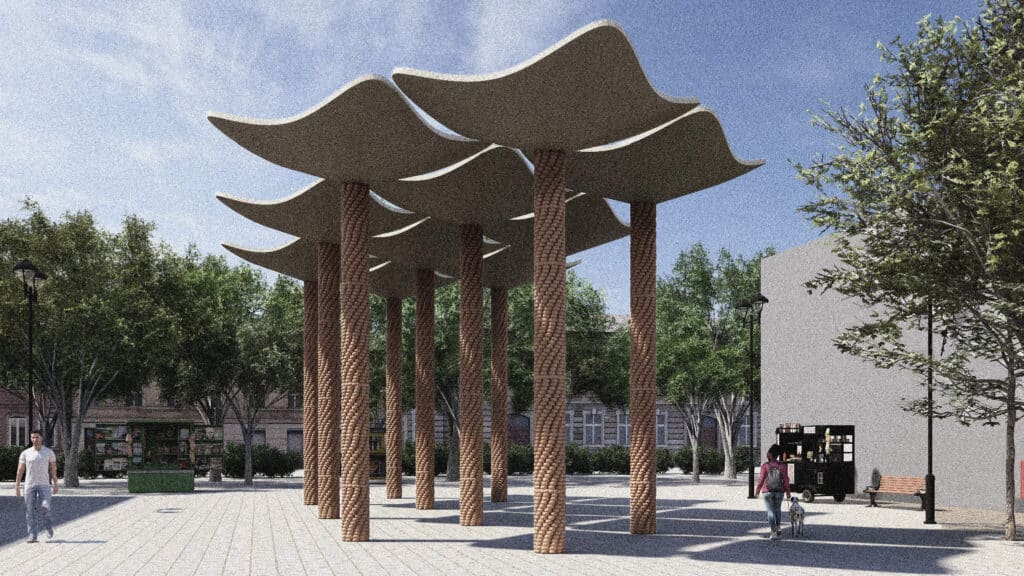
Render Made with Rhino & Lumion

Final Components Photograph

Assembled Column Photograph