This research thesis seeks for an opportunity to introduce specific human actions in the additive manufacturing robotic process to generate custom and adaptive fabrication flows based on local needs and conditions and set in a cyber-physical working environment that will scan and verify the results before and after every intervention.
1. Framework
According to UN, how AM tackled and got involved in many SDG on many sectors at many levels.

1.1. Additive Manufacturing market
The Global market in AM reached USD 15.2 Bn on 2021, predicting an annual growth of 20% every year.
However, the construction sector is still under very low digitalization and development on this field, becoming less than 0.1% of the general AM market.
Also other predictions say that by 2050:
– AM could save up to 90% of the raw material needed for manufacturing (EC, 2022)
– Cut manufacturing energy use in half (USDE, 2017)
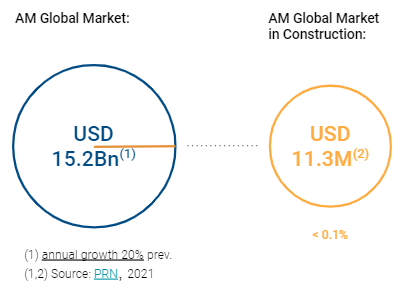
According to the policies presented by the EC and US Gov, there are several plans to increase the technology level, competitivity, flexibility in techniques and HRI programs.
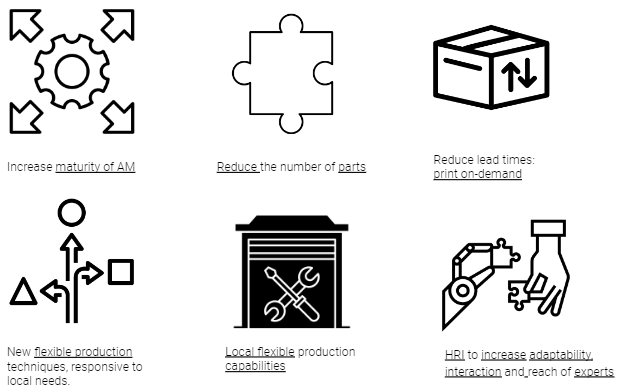
1.2. Issues in big scale printing and construction sector
there are still several challenges for the construction industry specially to update and increase its competitiveness.
Challenges in big scale or construction field:
– High costs in logistics and transportation
– Assembly – joinery design plan
– Post-processing demand
– Skilled labor for operation
– Proof-of-concept, experimental applications, not suitable for large-scale projects
Potential applications: Novel Forms, topology optimization, customized parts, in situ repair, tolerance matching (F. Craveiro, 2019).
1.3. Interactive AM
There are still, some ways to interfere in the processes to gain some flexibility in the system.
In some situations of uncertainty, humans can become inputs in the process of adaptation.
To scan, measure and calibrate the work with a bigger range of interventions or specific data collection.
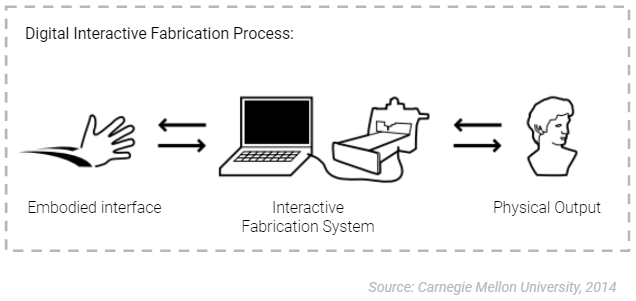
This diagram shows how on every phase of a fabrication process, there can be a potential feedback iteration between the virtual and the physical world. In this case, every result can work as a conclusion that becomes a new input on the next phase.
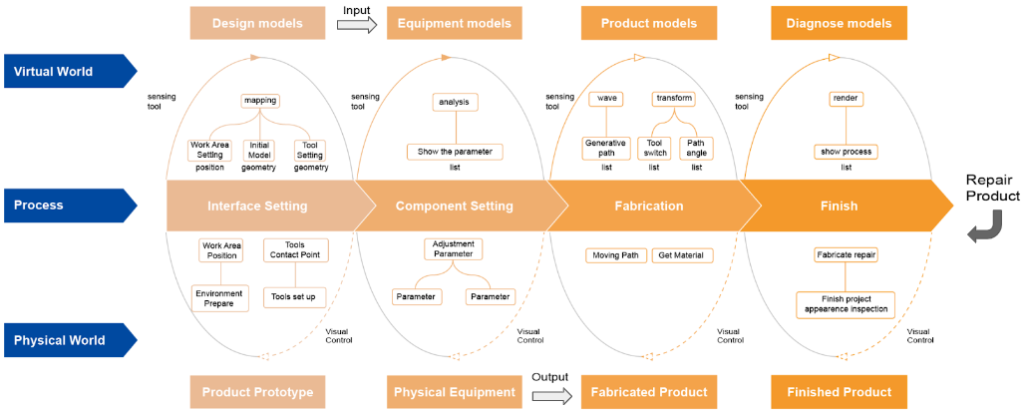
Interactivity linked to AM is usually more common in craft or artistic sectors as well as on workshops or research projects as shown below:
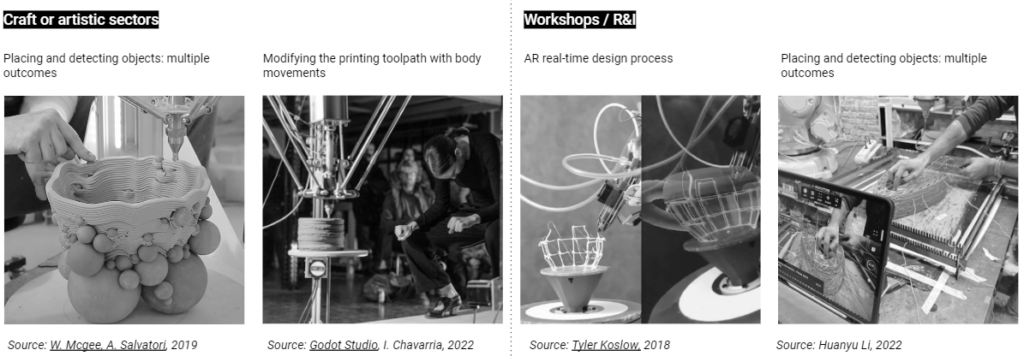
1.4. State of the Art
State of the Art #1: AM in construction: in situ retrofitting using AM with mobile robots. | Source: Advance AEC, 2022
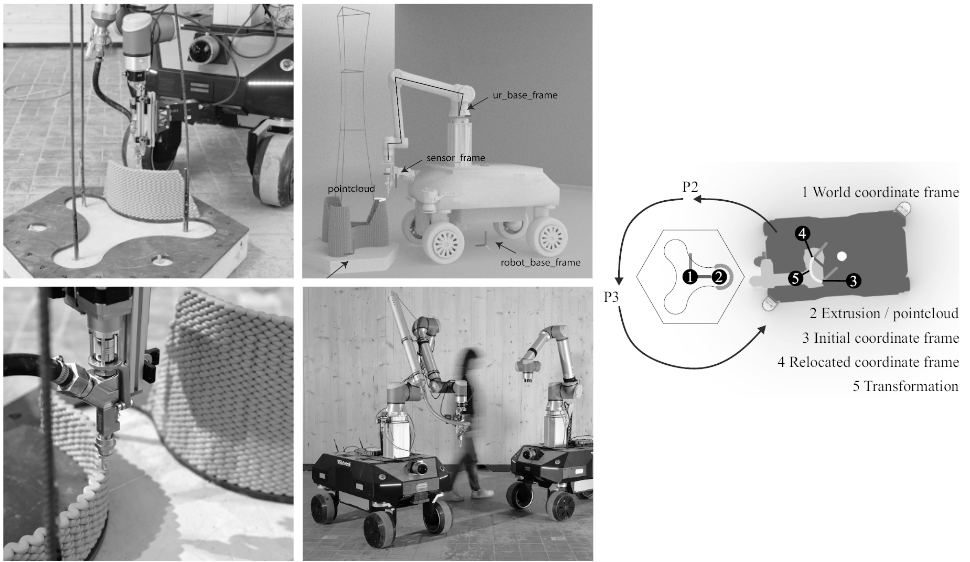
State of the Art #2: AM in construction: in situ retrofitting using AM with mobile robots. | Source: TUM-AEC Workshop, 2021
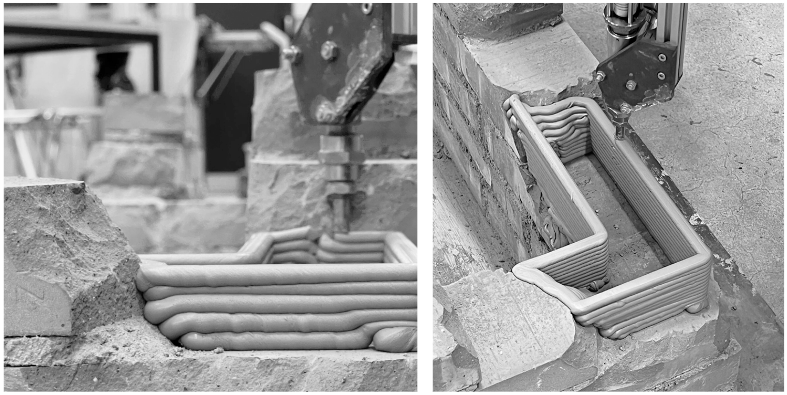
State of the Art #3: Robotic Hybrid Manufacturing | Source: S. Prajapat, 2019
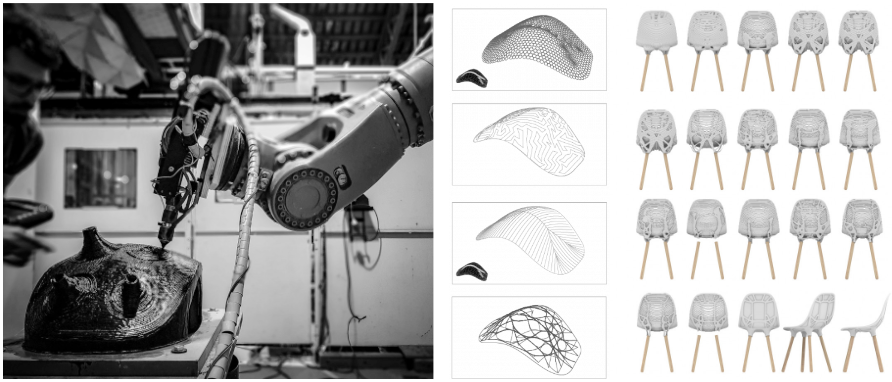
1.6. State of the Art: Conclusions
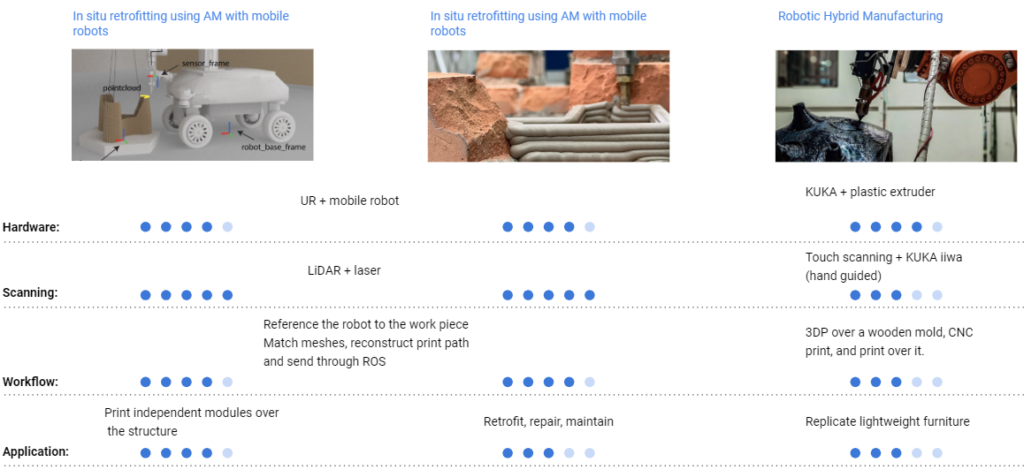
2. Research Contribution
2.1. Research Gap
A context aware AM system built on a cyber-physical online setup that aims for the adaptability and customization of modular designs based on local needs and conditions.
2.2. Hypothesis
Can HRI increase the flexibility or customization levels in projects based on big scale AM or construction sectors?
3. Proposal
Set a fixed workspace to print modular pieces that will adapt to objects embedded by a human and scanned by robot.
3.1. Methodology
Cyber-physical System
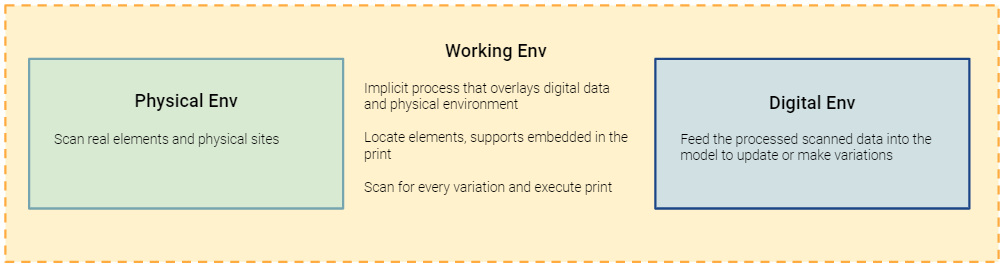
Set-up
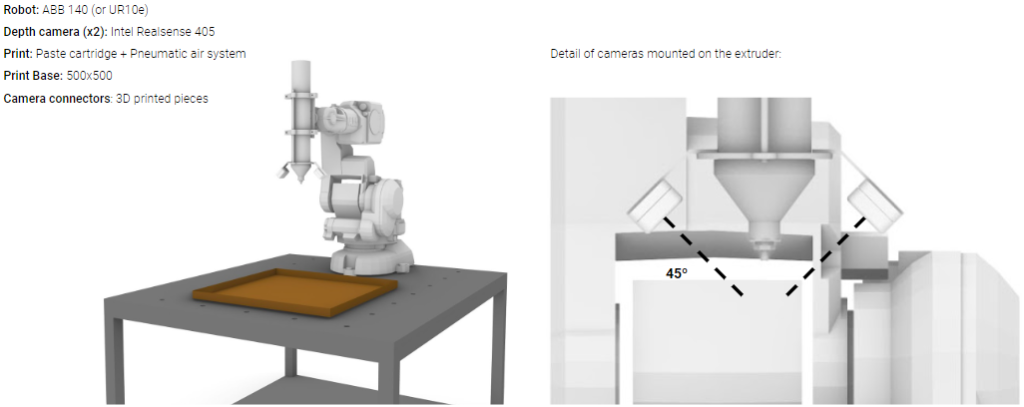
Workflow
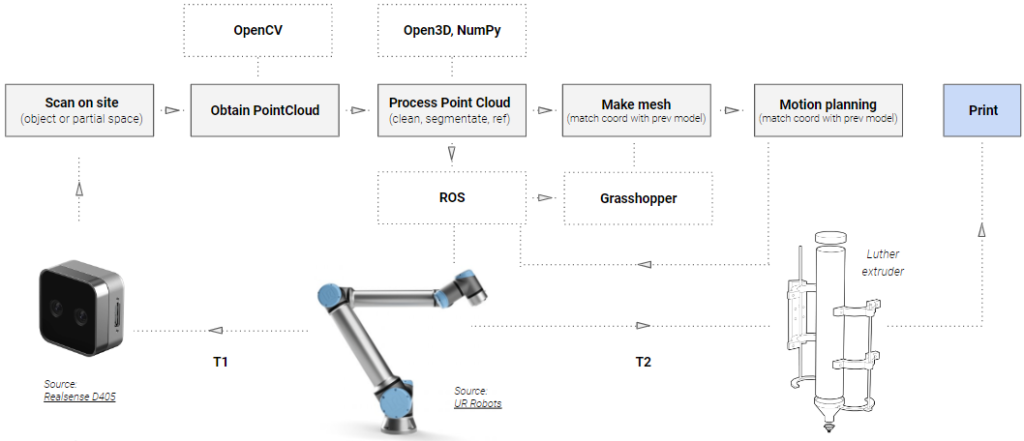
Adaptive Design
The printing tool path itself could become an adaptive design strategy that can grow or embed the elements input on the process working even as an infill.
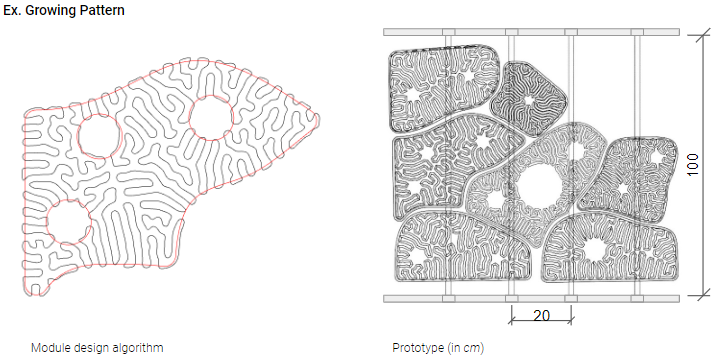
3.2. Case Study
On the next experiment, I checked the adaptive result on printing a cylinder in clay that would be interrupted in half of the way by placing 2 PVC pipes on it, and follow the adapted path avoiding the objects and finishing the original geometry.
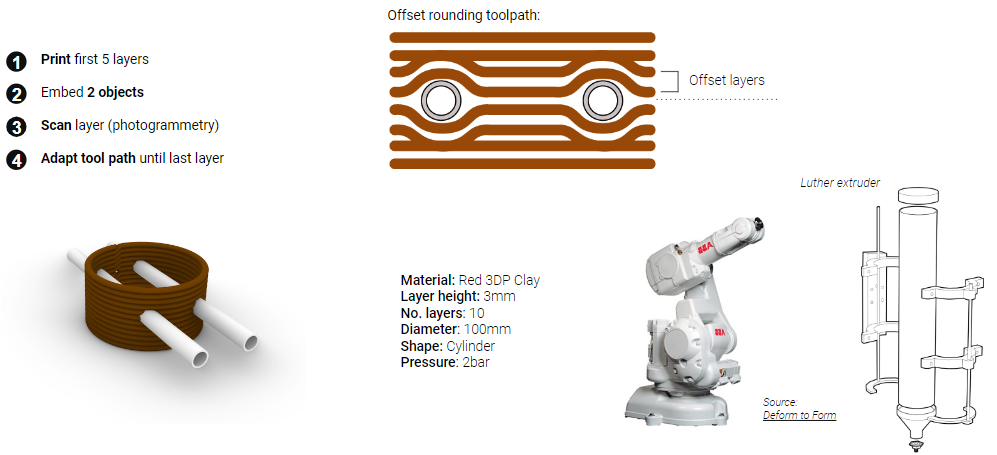
Case Study: Results
The results of the experiment are visually clear:
- Misalignment of object position
- Plane alignment to surface: not perpendicular to object surface
- Reconstruction of top part almost fine
- Middle layers separated due to shrinkage
3.3. Further steps
Scanning
- Input the real scanned data into the tool path
- Select points and reorient meshes
- Create a library with scanned elements
- Test scanning on ABB 140
Printing
- Change pneumatic pressured by screw extruder
- Test different infills or generative designs
- Test printing on UR
3.4. Research Plan
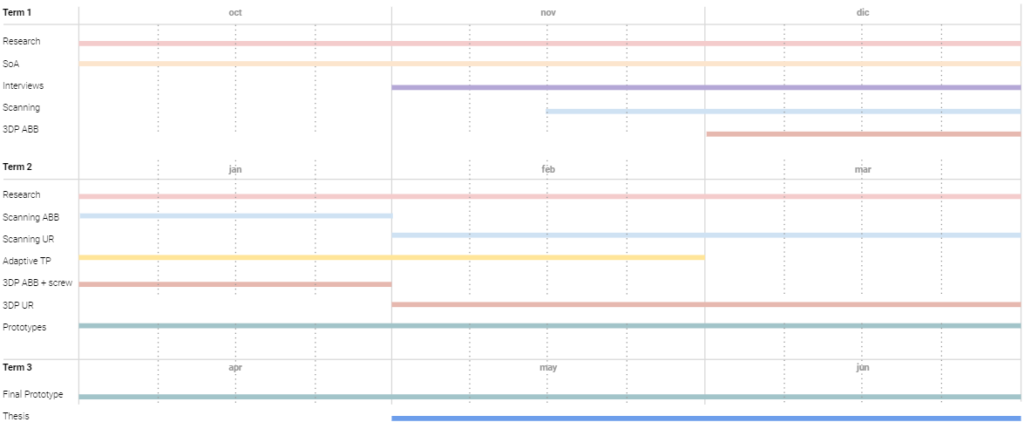