This term, the exploration of three fabrication techniques—Laser Cutting, 3D Printing, and CNC Milling—led to the creation of three vertical facade prototypes. Drawing inspiration from organic movements and waves, our laser-cut design explores the interlocking techniques with Polypropylene and acrylic.
The 3D printed geometry also explores the interlocking, this time as a mobility tool, creating a piece that is flexible and adaptable. The CNC milled prototype consist in a parametric pattern of spheres placed in a distorted surface showcasing the possibility of achieving organicity from a static material.
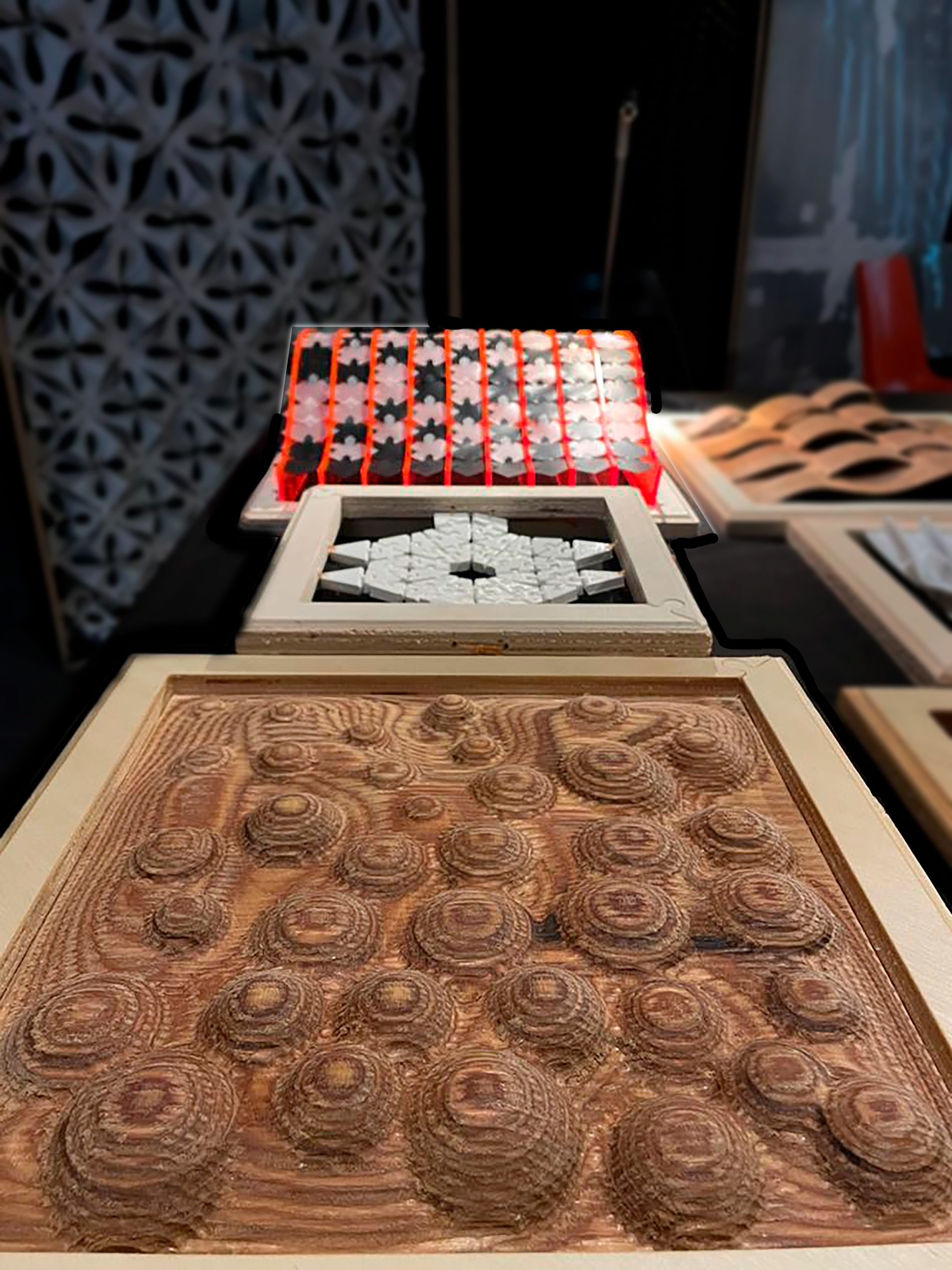
Laser Cutting – Interlocking Panels
In the exercise for laser cutting the team created a rigid interlocking system that uses a strategy of press fit diamonds into a slat structure. By experimenting with the ideal tolerances, the team was able to successfully create a structure that was extremely resilient to downward forces. The interlocking technique was used to creat the acrylic base structure, conformed buy a wave shaped sections and in the “diamonds shaped skin” that flows in the organic movement.
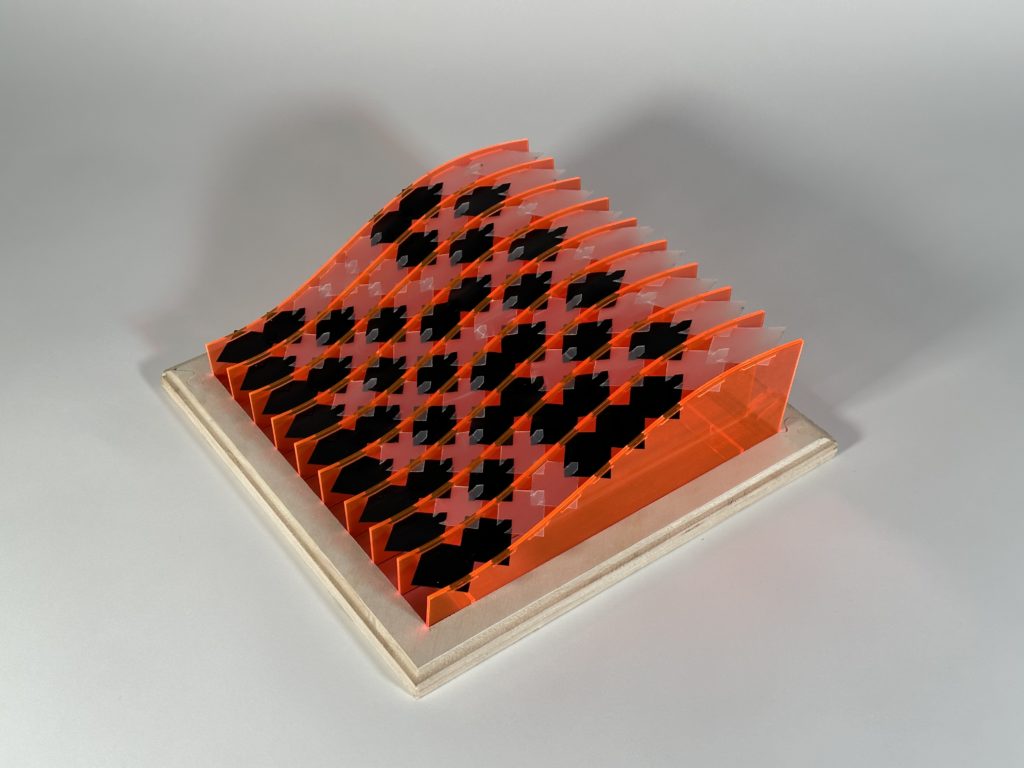
Concept – animal skin and waves movement
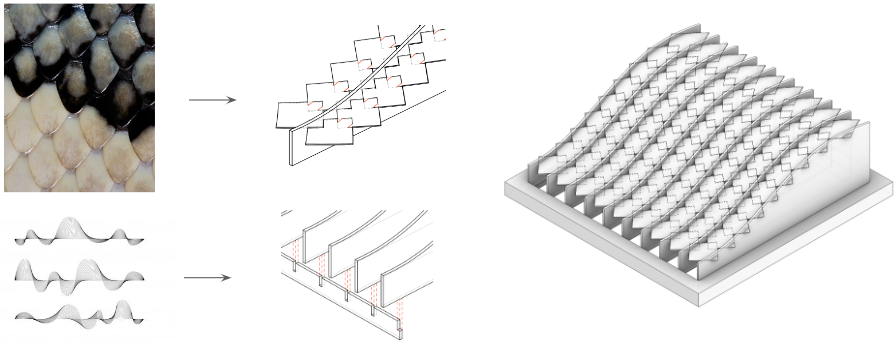
Production Process
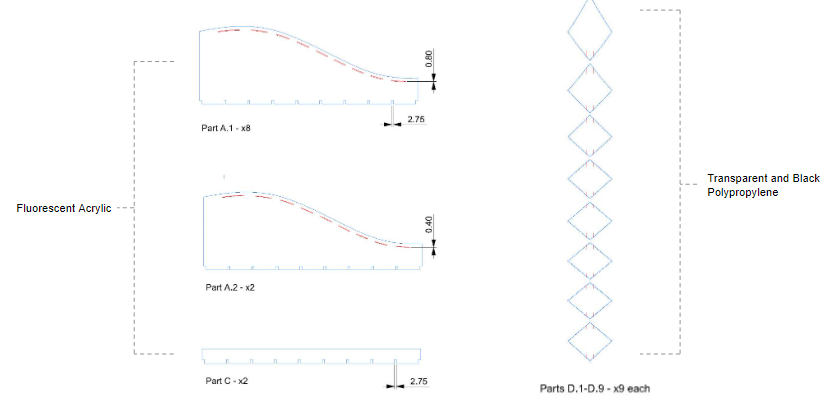
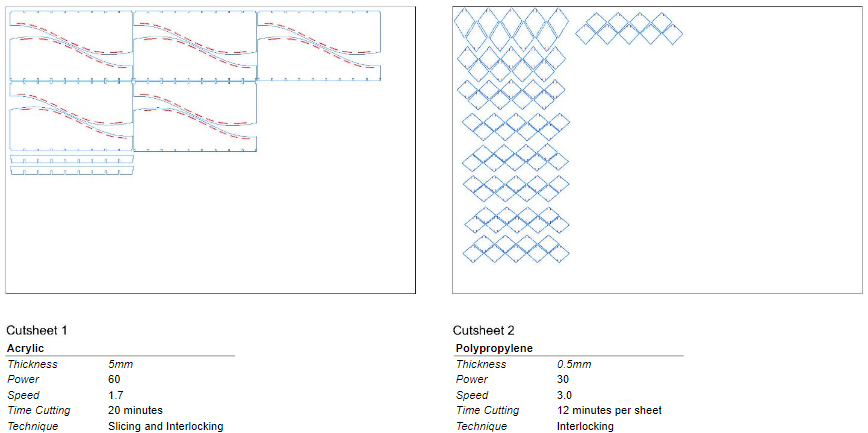
Prototyping and Fabrication Process
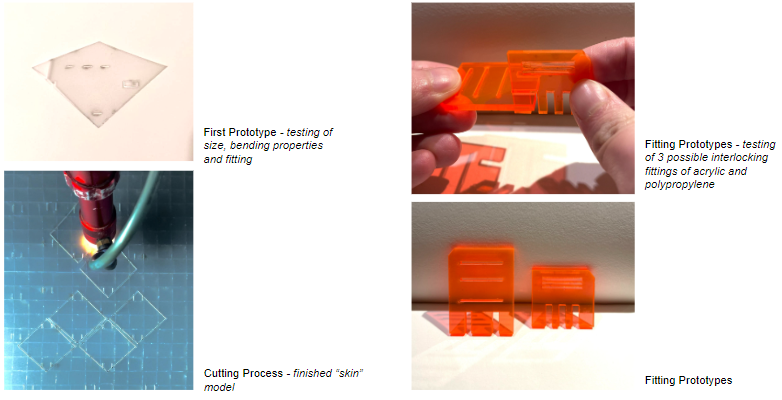
Final Model
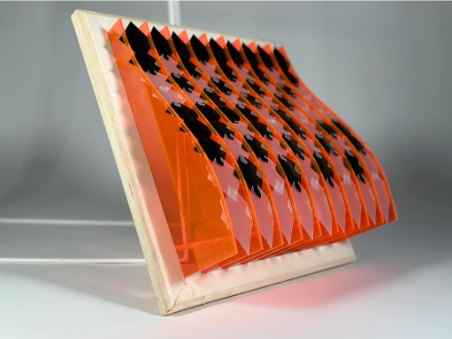
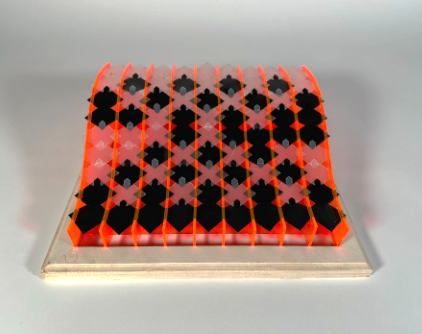
Application in Architecture
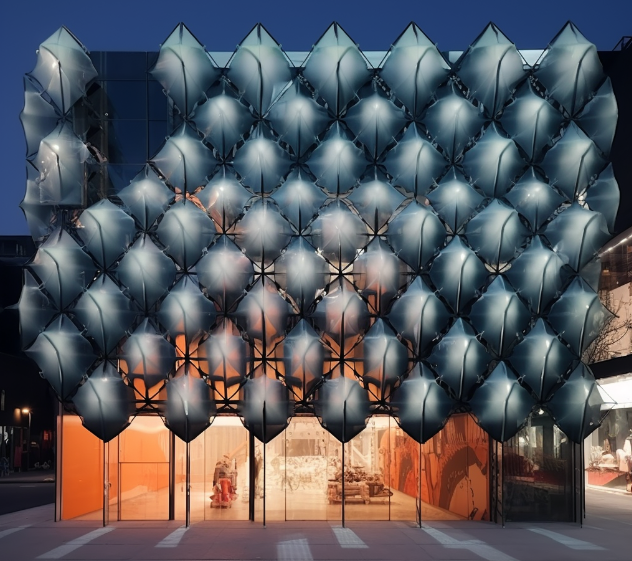
3D Printing – Interlocking Modules
This concept was developed as an exploration into the possibilities of 3D printing dynamic objects that finish in one fully connected assembly. Through prototyping a connection method, the team was able to create a strategy that could be applied to virtually any shape. The final product was a flexible yet durable material that could fold in on itself with ease and fluidity. To highlight these key attributes of the model, the final piece was mounted to the frame using rubber bands so that it could be pushed and pulled.
Concept – Fabric malleability and movement
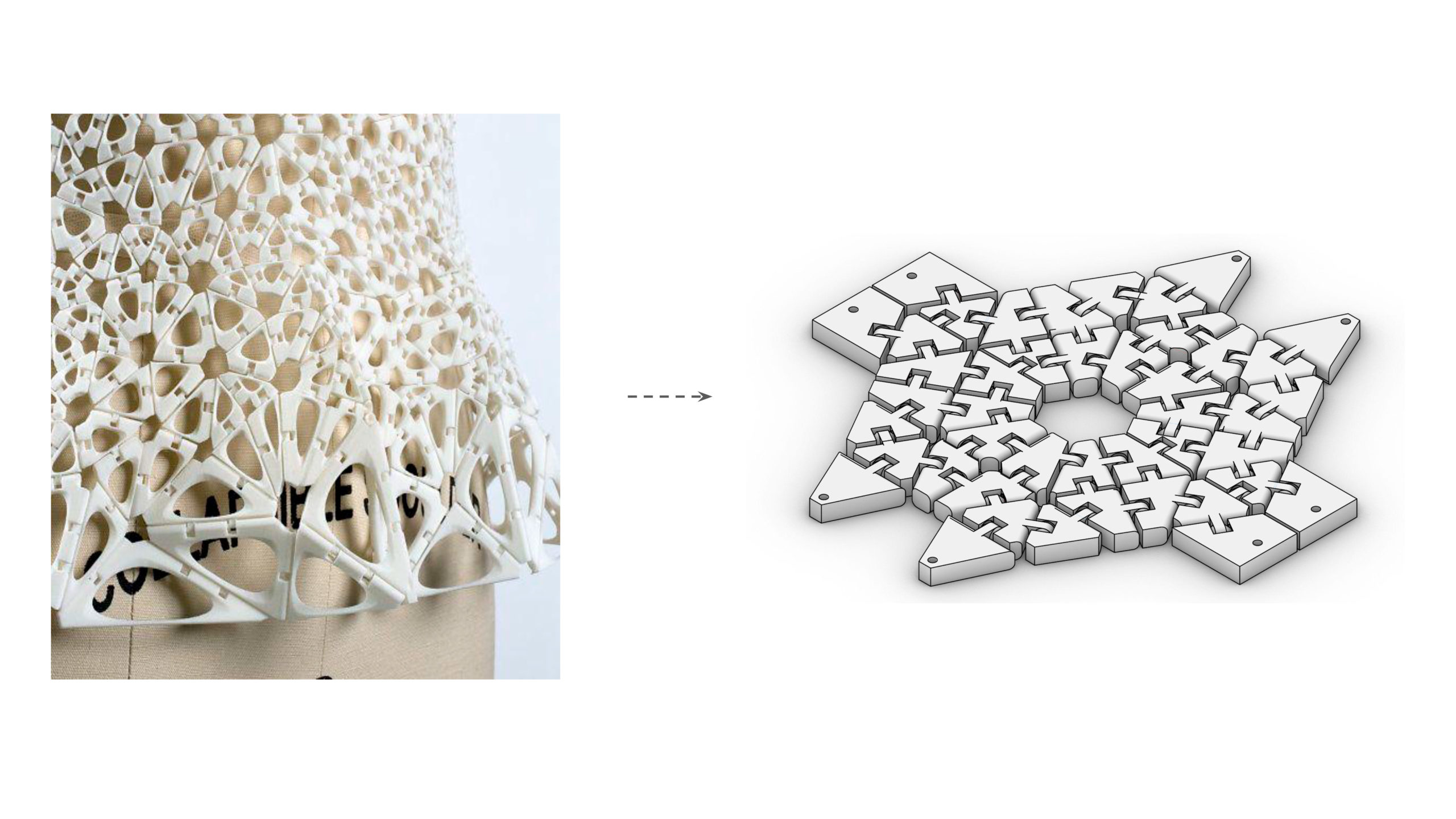
Production Process – Modeling in Rhino
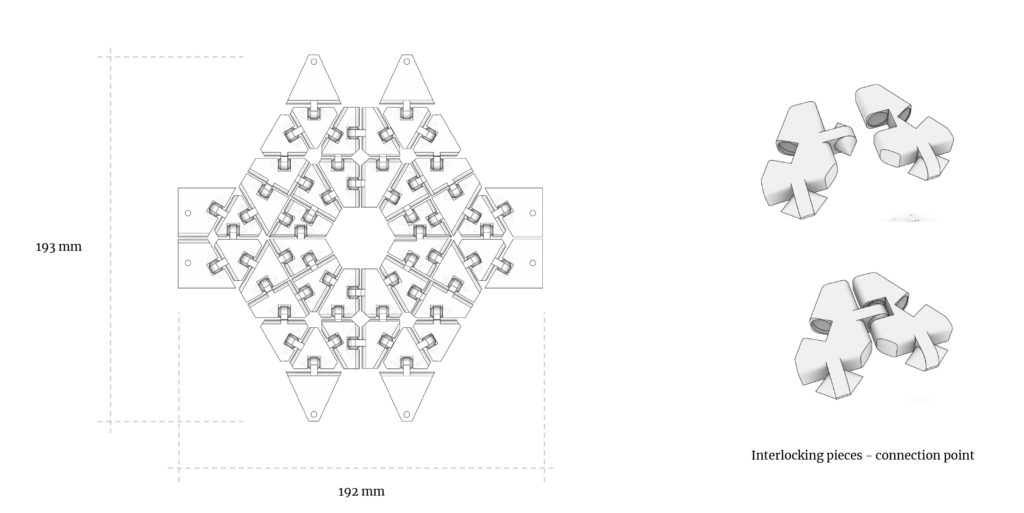
Prototyping – Test of the interlocking system
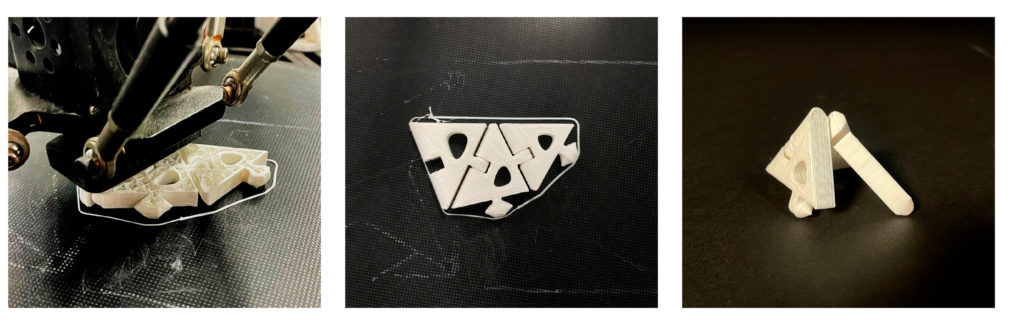
Production Process – Slicer settings for 3d printing
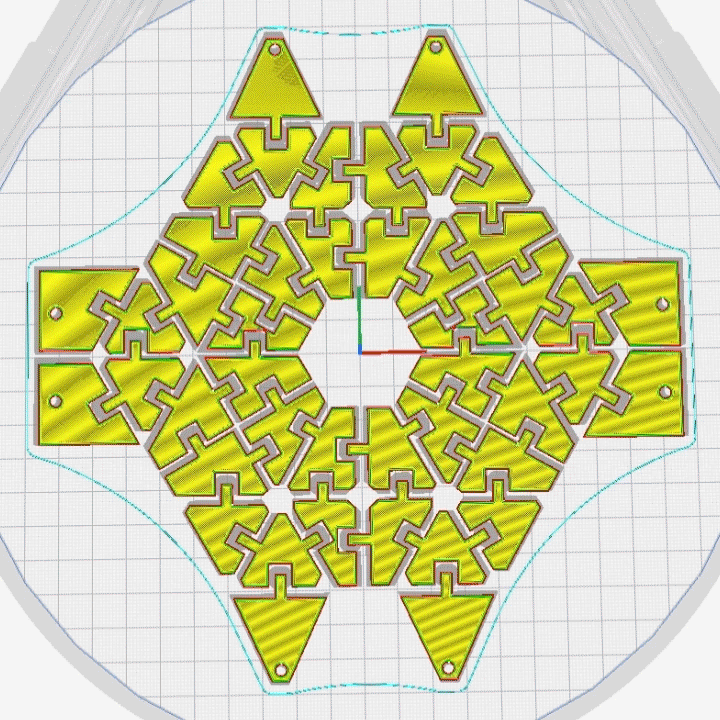
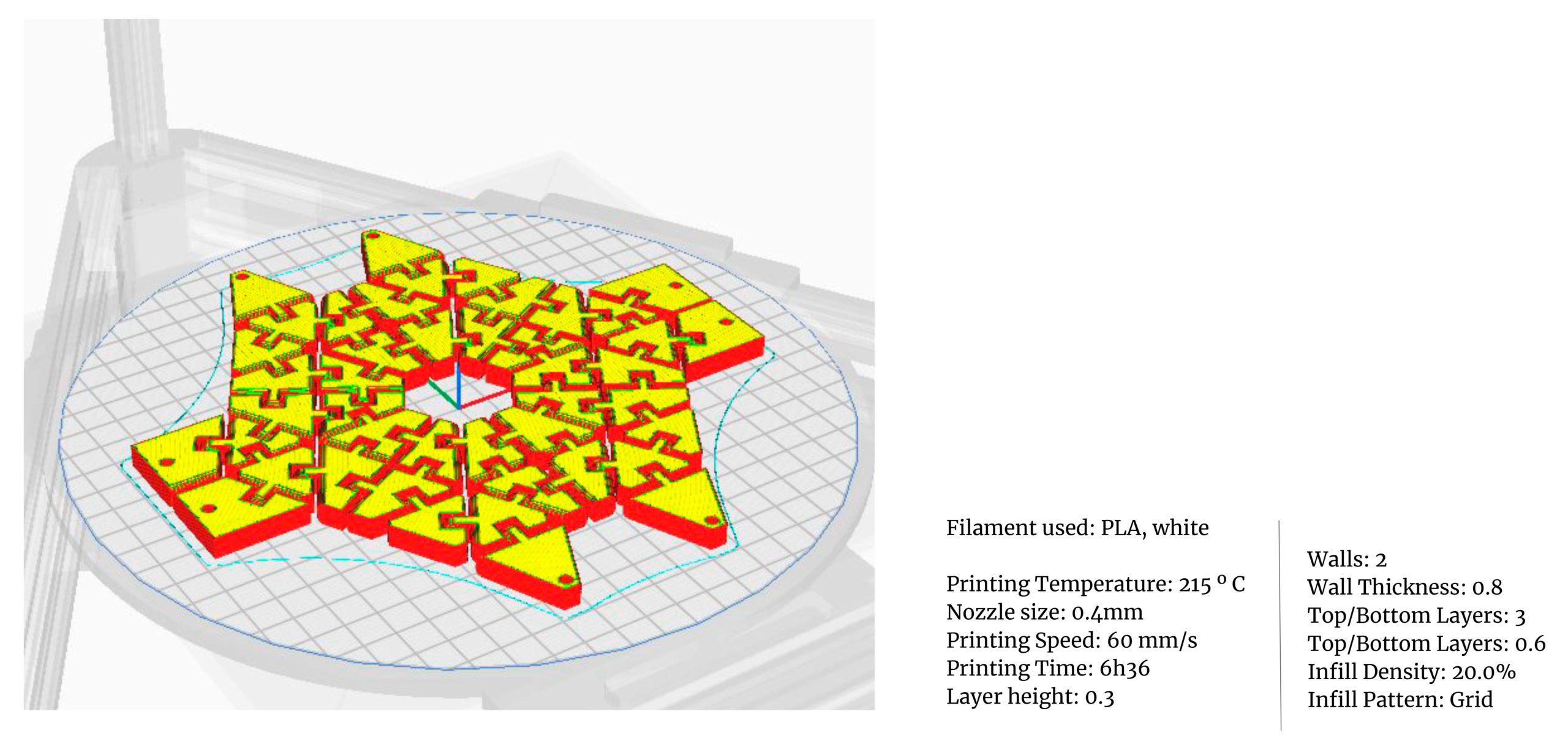
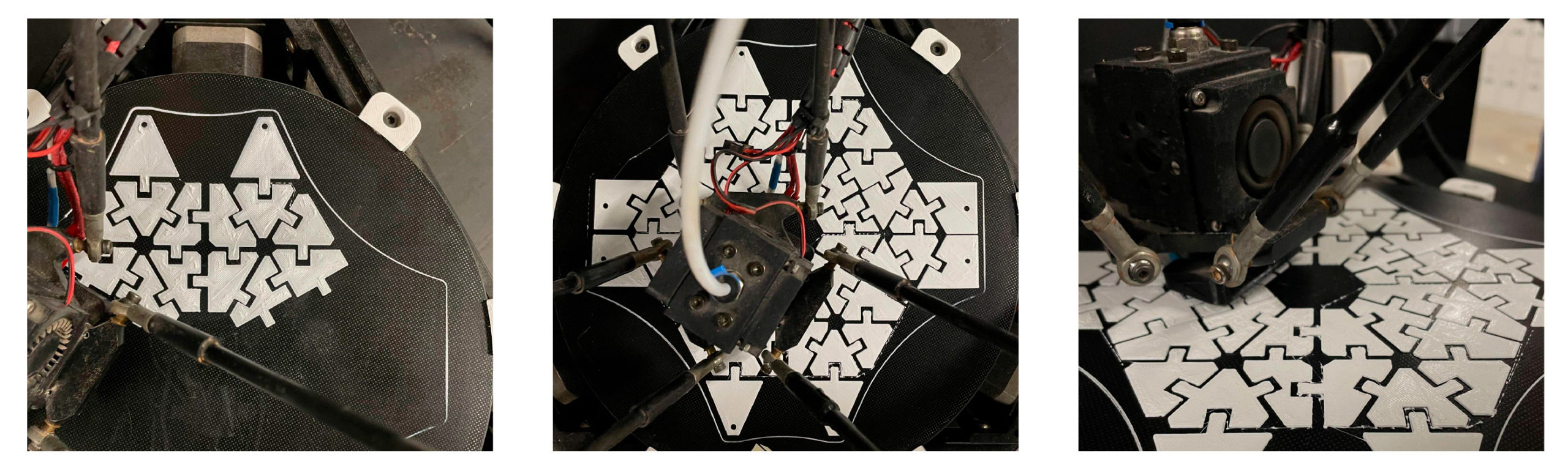
Final Model
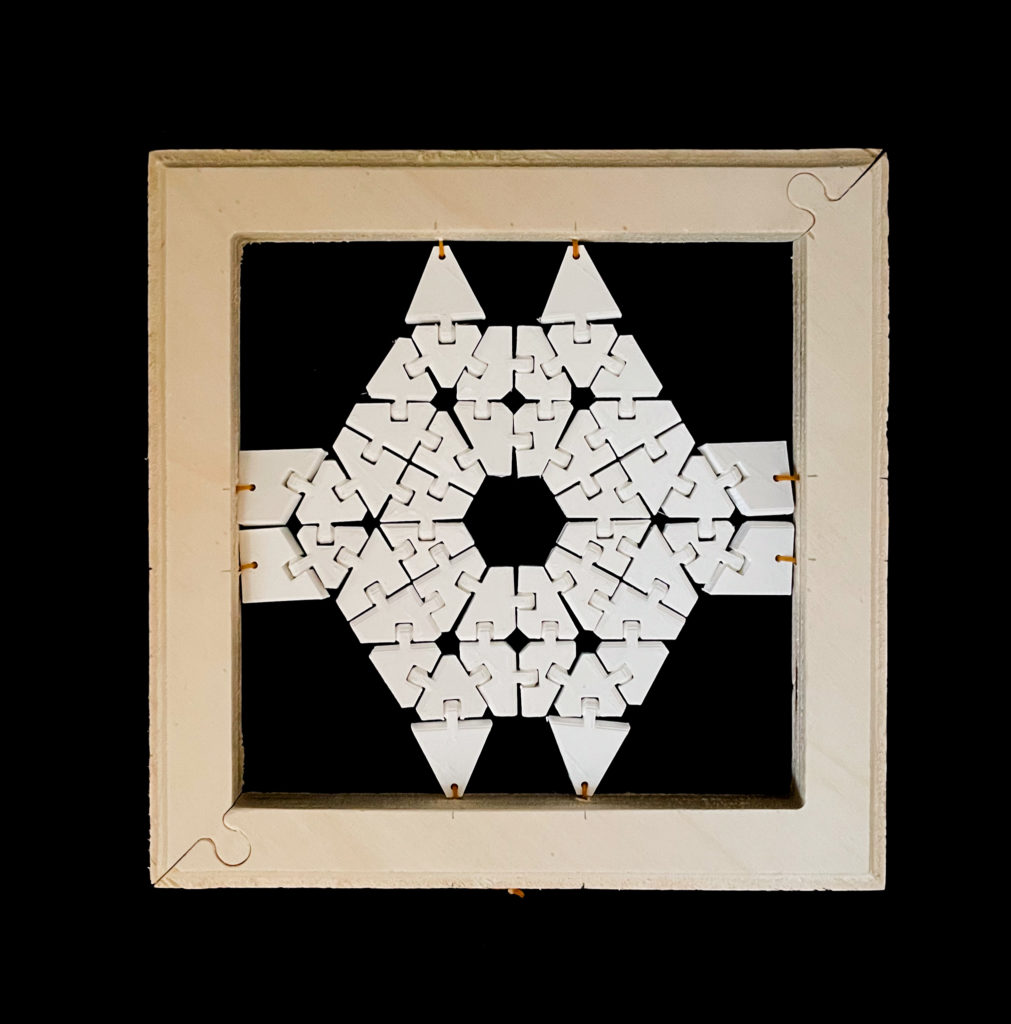
Application in architecture
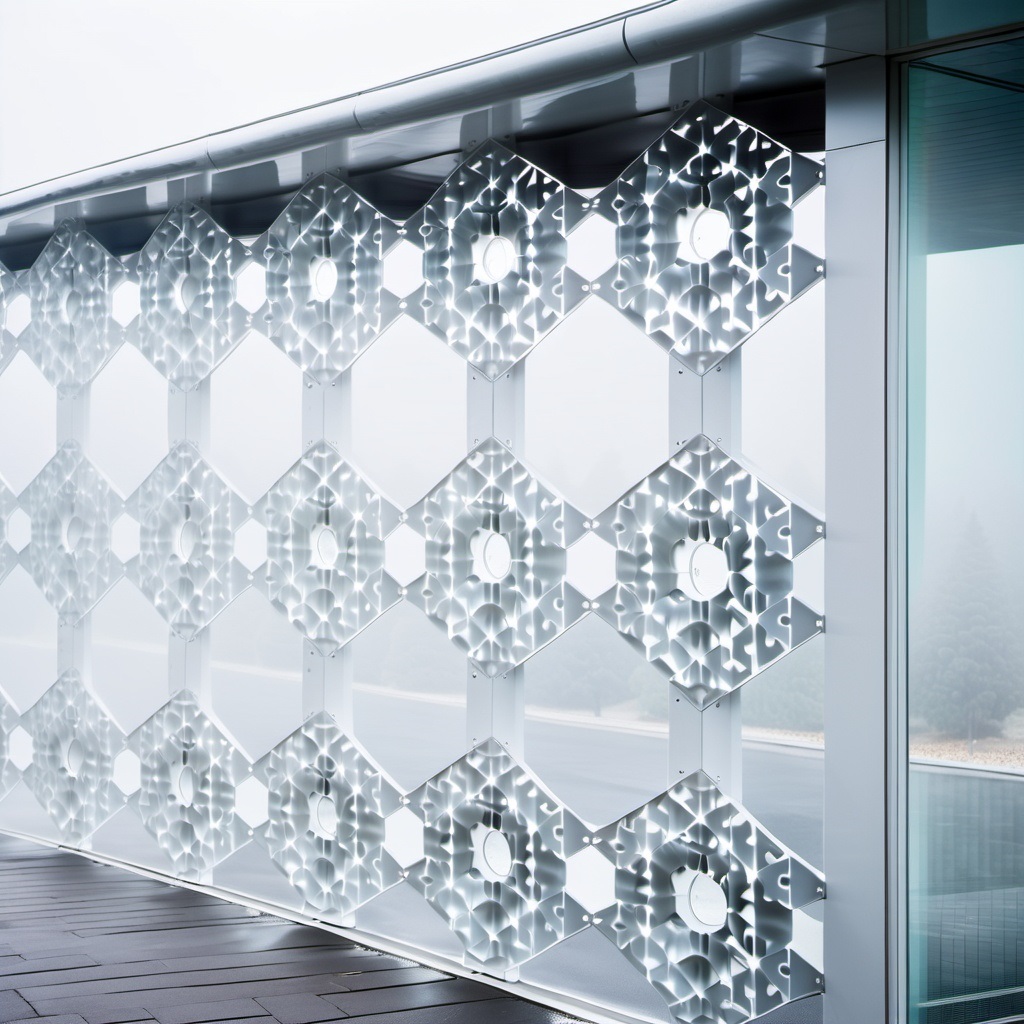
CNC Milling – Cascade
Concept and Inspiration
This vertical element was inspired by natural flows through arbitrary movement. By integrating spheres at random throughout an already undulating surface, the design could direct elements such as water and vegetation growth much like a river. Additionally, the spherical elements highlight the plywood striations creating a unique aesthetic.
Modeling Process – Rhino/Grasshopper
Production Process – RhinoCam Parameters
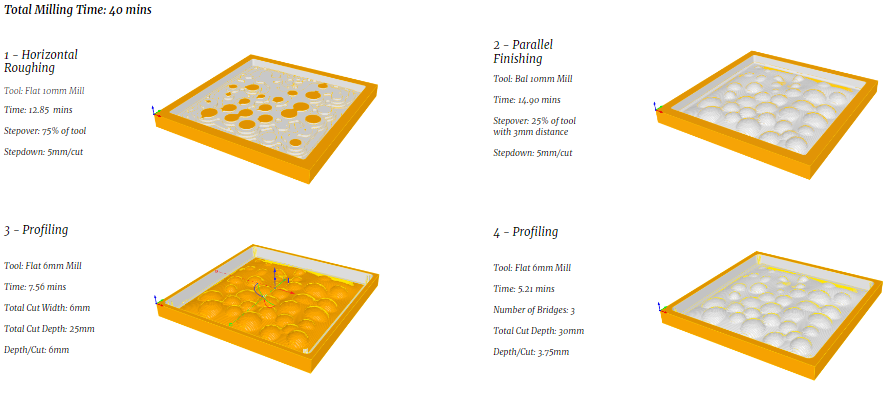
Fabrication Process – Milling in Playwood
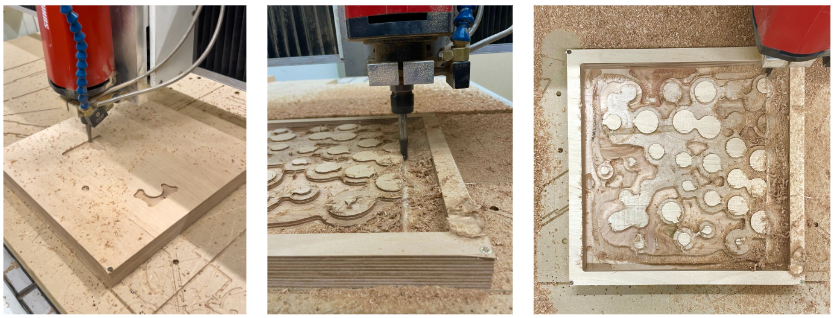
Final Model
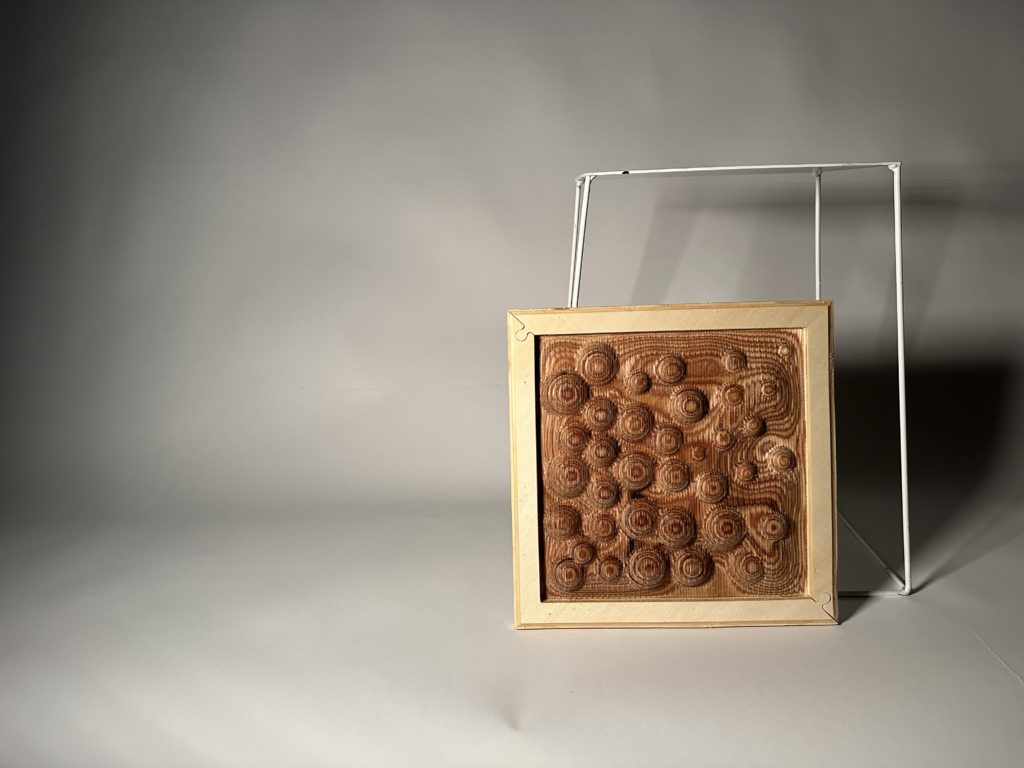
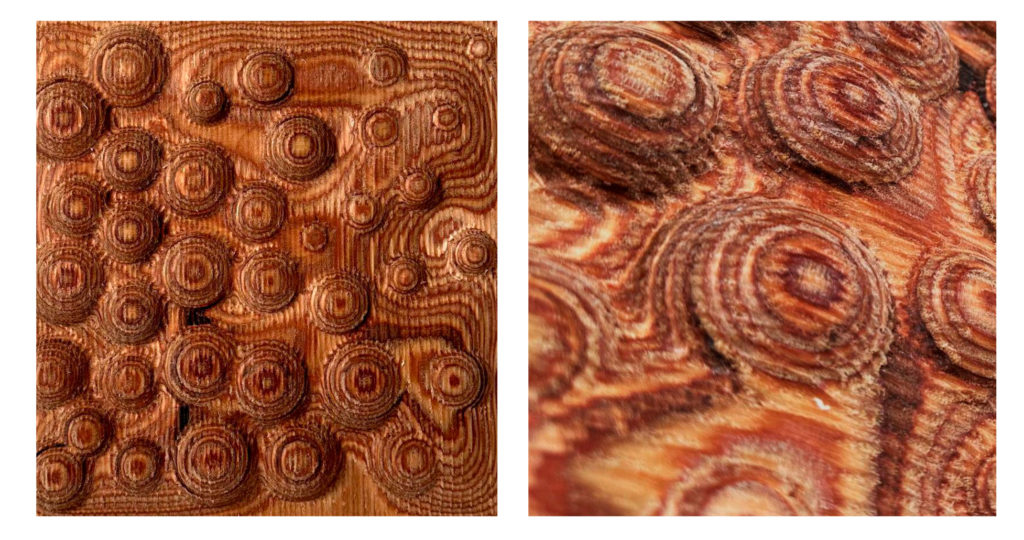
Application in Architecture
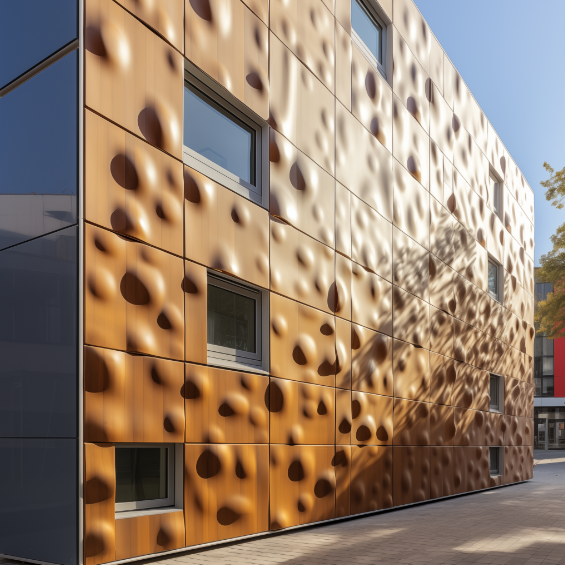